
Пайка металлов
..pdfСборка нагревается до температуры насыщенного пара (рис. 26, г), после чего нагрев прекращается независимо от того, сколько времени сборка проведет в паровой зоне. Время достижения температуры пайки обычно от 5–6 до 50 с для больших сборок. Происходит непосредственный процесс пайки.
После выхода сборки из паровой области на ней еще остается сконденсировавшаяся жидкость. Благодаря остающейся внутренней теплоте сборки она испаряется, и сухая плата покидает рабочую зону (рис. 26, д). Остатков жидкости на плате не образуется.
Рекомендуемые установки температуры: для эвтектических припоев – 200 °С, для бессвинцовых (как, например, SnAg3,5 с точкой плавления 221 °C) – 230 °С.
Пайка ненасыщенным паром. Горизонтальные системы.
Технология применения ненасыщенного пара основана на принципе инжекции.
Сборка перемещается с помощью горизонтального конвейера в рабочую камеру, которая затем герметизируется. Нижняя и боковые стенки камеры содержат нагревательные элементы, температура нагрева которых может быть задана программно. Далее происходит впрыск заданного объема рабочей жидкости в рабочую камеру. При контакте жидкости с поверхностью стенок камеры, жидкость вскипает и образует паровое облако (рис. 26, 27).
Скорость нагрева для каждой конкретной сборки может контролироваться и изменяться в зависимости от объема впрыскиваемой жидкости. Откачанный после окончания процесса пайки пар реконденсируется, очищается с целью удаления из него флюса и возвращается в бак-хранилище. Время цикла процесса пайки в горизонтальной системе сходно с таковым для пайки оплавлением в конвекционной печи.
Как было отмечено выше, количество образующегося пара, а следовательно, и его теплоемкость может управляться изменением количества впрыскиваемой рабочей жидкости. Для горизонтальных систем на характер термопрофиля оказывают воздействие несколько
131
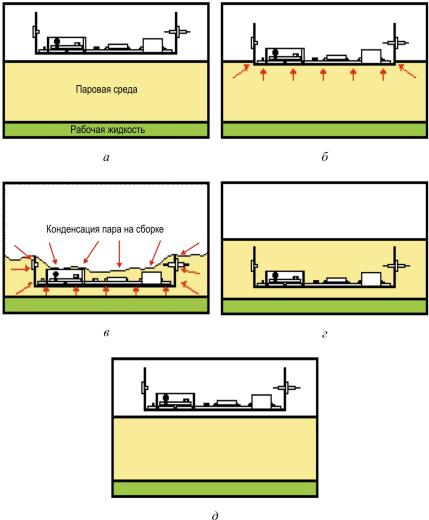
Рис. 26. Последовательность выполнения операции пайки насыщенным паром (вертикальные системы)
132
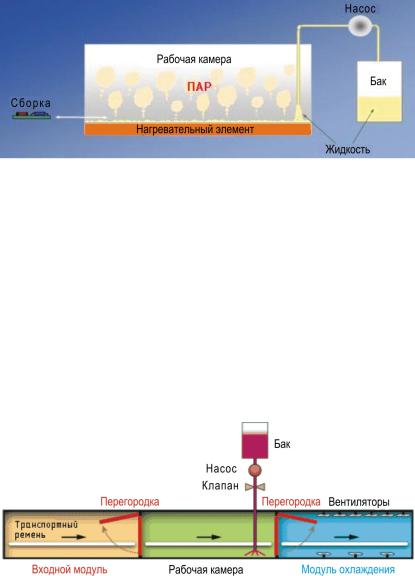
Рис. 27. Схема процесса пайки в паровой фазе с применением инжекции
параметров, среди которых можно выделить основные: количество впрыскиваемой жидкости; время выдержки после впрыска; степень откачки пара; охлаждение.
Процесс пайки включает несколько стадий впрыска/откачки, связанные с необходимостью предварительного нагрева сборки. Для систем пайки выделяют 3 стадии процесса: впрыск – выдержка – откачка.
Система может быть легко интегрирована в автоматизированную линию и, таким образом, адаптирована для больших объемов производства. Сборка, перемещающаяся по конвейеру, проходит три зоны: входную, рабочую и зону охлаждения (рис. 28).
Рис. 28. Конвейерная схема горизонтальной системы пайки в паровой фазе
133
Одной из основных трудностей пайки в паровой фазе является сложность управления скоростью подъема температуры в момент конденсации пара на поверхности сборки, так как процесс этот происходит очень быстро. Данный механизм передачи тепла характеризуется очень высокой эффективностью – коэффициент теплопередачи для него составляет ≈300 Вт/(м²·K), в то время как для принудительной конвекции (в воздушной или инертной атмосфере) его значение на порядок меньше.
Вследствие этого значения скорости подъема температуры при пайке в паровой фазе могут достигать 25–40 °С/с (большие́ значения характерны для небольших по размерам компонентов), что потенциально может вызвать появление таких дефектов, как растрескивание керамических чип-компонентов, смещение компонентов, эффект «надгробного камня», капиллярное затекание припоя. С развитием технологии пайки в паровой фазе появился ряд способов, позволяющих установить контроль над этой скоростью.
Предварительный нагрев сборок помогает обеспечить более плавный переход к температуре оплавления. В установках пайки в паровой фазе применяются как традиционные методы предварительного нагрева (ИК-нагрев, естественная и принудительная конвекция), так инагрев средствами самойпаровойфазы.
Так, компания R&D Technical Services, Inc. применяет в ряде своих систем нагрев с помощью принудительной конвекции (4 зоны нагрева).
В ряде вертикальных систем управление скоростью нагрева идет за счет последовательного погружения сборки в паровую среду, чем регулируетсяобъем конденсирующегосянасборке пара(рис. 29).
Системы оплавления, построенные по таким технологиям, включают дополнительные зоны предварительного инфракрасного либо конвекционного нагрева непосредственно перед рабочим резервуаром пайкивпаровойфазе. Примервертикальной системы, встроеннойвавтоматизированную линию и оснащенной устройствами загрузки/выгрузки, конвейером для транспортировки сборок, камерами предварительного нагреваиохлаждения, представленнарис. 30.
134
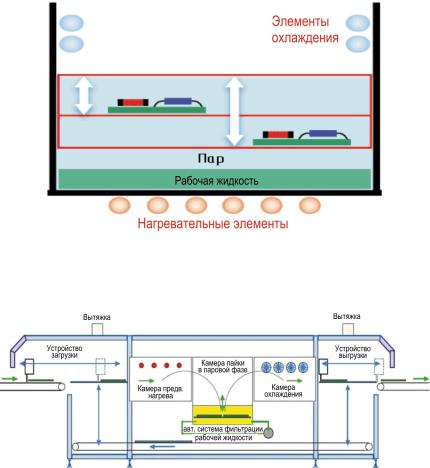
Рис. 29. Схема предварительного нагрева вертикальной системы пайки в паровой фазе. Стрелками очерчен доступный объем пара для каждой глубины погружения сборки
Рис. 30. Вертикальная система, встроенная в автоматизированную линию и оснащенная камерой предварительного нагрева
Таким образом, термопрофилирование при пайке в паровой фазе включает установку параметров предварительного нагрева, скорости движения конвейера, времени выдержки в рабочей зоне. Как и для традиционных печей оплавления, пайка в паровой фазе требует индивидуального профиля оплавления для каждой новой
135
сборки, однако термопрофилирование значительно упрощается, так как максимальная температура рабочей жидкости жестко фиксирована. Все требования, относящиеся к обеспечению предварительного нагрева в ИК-системах, справедливы и для соответствующих зон пайки в паровой фазе.
Основные достоинства пайки в паровой фазе:
1.Невозможен перегрев сборки свыше заранее известной температуры конденсации пара.
2.Относительно простой процесс термопрофилирования. Метод особенно пригоден для многономенклатурного мелкосерийного производства, так как не требуется трудоемкий подбор профилей в зависимостиотконструкциисборки.
3.Равномерное распределение температур по поверхности сборки и быстрый нагрев даже при большой разнице в теплоемкости различных компонентов и областей ПП. Нет необходимости в выдержке для обеспечения равномерного нагрева. Особенно пригоден для больших и массивных сборок, а также для изделий, включающих компоненты сложной формы.
4.Химические основы процесса обеспечивают 100 % инертную атмосферу при пайке. Отсутствие окисления при предварительном нагреве (средствами паровой фазы) и пайке. Применяемый флюс, таким образом, можетобладатьумереннойактивностью.
5.Дружественность процесса по отношению к окружающей среде– менееагрессивныепарыфлюса, чемвдругихтехпроцессах.
6.Низкие затраты на операцию, малое энергопотребление (обычно 5–12 кВт).
Оборудование для пайки в паровой фазе. Существует широкий спектр моделей как одиночных, для единичного и мелкосерийного производства (рис. 31), так и встраиваемых в линию систем пайки, для большихобъемоввыпуска(рис. 32).
Во многих моделях оборудования возможно непосредственно наблюдать за процессом пайки через смотровое окно.
136

Рис. 31. Одиночная система пайки в паровой фазе для единичного и мелкосерийного производства. Модель VP-500 Gold
Рис. 32. Автоматизированная встраиваемая в линию система пайки в паровой фазе для больших объемов выпуска. Модель VP 2000.
ФотоASSCON Systemtechnik-Elektronik GmbH
Применение вакуума при пайке. Многие производители обо-
рудования представили технологии пайки в паровой фазе, обеспечивающие применение вакуума для удаления пустот из паяных соединений, проблема образования которых стала особенно актуальной в условиях продолжающегося внедрения бессвинцовых паяльных
137

материалов и расширения номенклатуры изделий. Также отсутствие пустот важно для мощных сборок, где критичной является хорошая теплопередача от компонентов к плате.
Результаты влияния вакуума на устранение пустот приведены на рис. 33 (данные компании rehm Anlagenbau GmbH; площадь контакта паяной поверхности увеличилась при применении вакуума с <68 до >98 %) и рис. 34 (данные компании ASSCON
Systemtechnik-Elektronik GmbH).
Рис. 33. Результаты традиционного процесса оплавления (а) и процесса с применением вакуума (б)
Рис. 34. Фиксирование пустот на поверхности контакта при традиционном процессе оплавления (а) и процессе с применением вакуума (б)
138

13.4. Пайка при нагреве ИК-излучением
Инфракрасное (ИК) излучение применяют для бесконтактного нагрева деталей в различных средах: на воздухе, в контролируемой атмосфере, в вакууме.
Инфракрасное тепловое излучение находится в диапазоне длин волн 0,76–1000 мкм, однако наибольшая эффективность (75 %) приходится на коротковолновый поддиапазон 0,75–3,0 мкм. Падающее на паяемую поверхность ИК-излучение вследствие поглощения незначительно проникает вглубь металла, частично отражаясь от его поверхности. Отражательная способность гладких поверхностей чистых металлов зависит от их удельного электрического сопротивления
итемпературы поверхности:
ε= 1 + 0,1 ρ T .
Для полированных поверхностей из серебра, алюминия коэффициент отражения составляет 95 %, поэтому они используются для изготовления рефлекторов ИК-установок. Неотраженная часть излучения поглощается рефлектором, и в установках предусматривают его водяное или воздушное охлаждение (рис. 35).
Рис. 35. Схема ИК-нагрева: 1 – рефлектор;
2– ИК-лампа; 3 – маска; 4 – деталь
Вкачестве источников ИК-энергии используются галогенные кварцевые лампы мощностью 500–2000 Вт. Галогенные (йодные,
139

галоидные) лампы изготавливаются из кварцевого стекла и имеют вольфрамовую спираль с рабочей температурой порядка 3000 °С
исроком службы 2000–5000 ч. В процессах пайки широкое применение получили два вида ИК-нагрева: локальный сфокусированный
ипрецизионный рассеянный.
Для локального нагрева целесообразны отражатели эллиптической формы, фокусирующие излучение источника, помещенного в ближнем фокусе рефлектора, на объект нагрева в дальнем фокусе (рис. 36, а). Для прецизионного нагрева используют параболические (рис. 36, б) либо овально-цилиндрические с сопловыми насадками рефлекторы (рис. 36, в).
Рис. 36. Типы отражателей ИК-излучения:
а– отражатели эллиптической формы,
б– параболические отражатели,
б– овально-цилиндрические отражатели
Кдостоинствам пайки ИК-излучением следует отнести: бесконтактный подвод энергии к паяемым деталям, точную регулировку времени и температуры нагрева, локальность нагрева в зоне пайки. Недостатки процесса – затруднение при флюсовой пайке, так как испаряющийся флюс загрязняет лампы и рефлекторы, отсутствие серийно выпускаемого оборудования.
140