
Пайка металлов
..pdf12.10. Ультразвуковая пайка керамики
Ультразвуковое удаление оксидных пленок основано на введении упругих механических колебаний частотой 18–45 кГц в расплавленный припой и создании в нем кавитации, а также ряда сопутствующих явлений: звукового давления, микро- и макропотоков. Кавитацией называется явление возникновения, развития и захлопывания газовых полостей в жидкой среде. Реальные жидкости и расплавы содержат нерастворимые примеси, на поверхности которых в трещинах и углублениях могут находиться нерастворенные пузырьки газа размером 10–6–10–7 м. При введении в расплав УЗ-колебаний интенсивностью 104 Вт/м2 эти зародыши кавитации начинают пульсировать с частотой колебаний. Их количество увеличивается за счет образования разрывов в жидкой среде при интенсивностях ультразвука более 2·104 Вт/м2.
При захлопывании пузырька сконцентрированная в ничтожно малом объеме кинетическая энергия трансформируется частично в силовой импульс и частично в тепловую энергию. Из центра захлопнувшегося пузырька распространяется ударная сферическая волна, давление в которой на расстоянии, равном 10R0 (по расчетным данным), составляет 150 Па, а температура – 1000 °С и выше. Захлопывание кавитационных полостей и создание микропотоков в расплавленном припое приводят к удалению оксидных пленок с поверхности металла, что позволяет осуществлять пайку и лужение труднопаяемых металлов: алюминия, магния и никеля, тугоплавких металлов и сплавов на их основе.
Генерация упругих механических колебаний УЗ-частоты осуществляется магнитострикционными и пьезоэлектрическими преобразователями с частотой колебаний 22 и 44 кГц и амплитудой колебаний 10–25 мкм. Преобразователи встраиваются в ванны и паяльники, излучающие поверхности которых изготавливаются из кавитационно-стойких материалов (нержавеющие стали, титановые сплавы). Электрическая мощность установок для УЗ-пайки не превышает 0,4–2,5 кВт. Время пайки или лужения составляет 5–10 с,
121
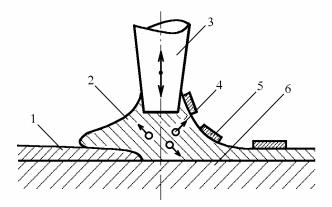
скорость перемещения излучателя паяльника (0,8–1,6) ·10–2 м/с, а оптимальный зазор между торцом излучателя и паяемой поверхностью
0,2–3,0 мм (рис. 25).
Рис. 25. Схема ультразвуковой пайки: 1 – окисел; 2 – припой; 3 – излучатель паяльника; 4 – кавитационный
пузырек; 5 – шлак; 6 – металл
С помощью УЗ-металлизации удается соединять непаяемые материалы – керамику, стекло, ферриты и др. Однако это требует специальных припоев, объективного контроля режимов процесса (амплитуды и частоты колебаний), а также специальных мер против повышенного окисления припоя.
ГЛАВА 13. СПЕЦИАЛЬНЫЕ СПОСОБЫ ПАЙКИ
13.1. Пайка печатных узлов при производстве радиоэлектронной аппаратуры (РЭА)
Пайка волной припоя
Пайка волной припоя появилась в 60-е годы и сегодня достаточно хорошо освоена. Она применяется для пайки компонентов в отверстиях плат (традиционная технология DIP-монтажа). С ее помощью можно производить пайку поверхностно-монтируемых компонентов с несложной конструкцией корпусов, устанавливаемых на одной изсторонкоммутационнойплаты.
Платы, установленные на транспортере, подвергаются предварительному нагреву, исключающему тепловой удар на этапе пайки. Затем плата проходит над волной припоя. Сама волна, ее форма и динамические характеристики являются наиболее важными параметрами оборудования для пайки. Изменяя характеристики сопла можно менять форму волны. В наиболее простых установках для пайки применяется симметричная волна, однако лучшее качество пайки получается при использовании несимметричной формы волны (в виде греческой буквы «омега», Z-образную, Т-образную и др.). Направление и скорость движения потока припоя, достигающего платы, также могут варьироваться, но они должны быть одинаковы по всей ширине волны. Угол наклона транспортера для плат тоже регулируется. Некоторые установки для пайки оборудуются дешунтирующим воздушным «ножом», который обеспечивает уменьшение количества перемычек припоя. «Нож» располагается сразу же за участком прохождения волны припоя и включается в работу, когда припой находится еще в расплавленном состоянии на коммутационной плате. Узкий поток нагретого воздуха, движущийся с высокой скоростью, уносит с собой излишки припоя, тем самым разрушая перемычки и способствуя удалению остатков припоя.
123
Пайка двойной волной припоя
Впечатном узле (ПУ) с комбинированным монтажом, где с одной стороны устанавливаются изделия электронной техники (ИЭТ),
ас обратной стороны поверхностно-монтируемые (ПМ) ИЭТ, пайка волной припоя создает множество проблем, связанных как с конструкцией плат, так и с особенностями процесса пайки:
– непропаи и отсутствие галтелей припоя из-за эффекта затенения выводов элемента другими компонентами, преграждающими доступ волны припоя к соответствующим контактным площадкам;
– наличие полостей с захваченными газообразными продуктами разложения флюса, мешающих дозировке припоя.
Вэтом случае применяют технологический процесс пайки двойной волной припоя. Первая волна делается турбулентной и узкой.
Она исходит из сопла под большим давлением. Турбулентность и высокое давление потока припоя исключает формирование полостей с газообразными продуктами разложения флюса. Однако турбулентная волна все же образует перемычки припоя, которые разрушаются второй, более пологой ламинарной волной с малой скоростью истечения. Вторая волна обладает очищающей способностью и устраняет перемычки припоя, а также завершает формирование галтелей. Для обеспечения эффективности пайки все параметры каждой волны должны быть регулируемыми. Поэтому установки для пайки двойной волной имеют отдельные насосы, сопла и блоки управления для каждой волны. В установках для пайки двойной волной припоя возможно применение дешунтирующего «ножа», служащего для разрушения перемычек припоя.
Пайка двойной волной припоя применяется в основном для одного типа ПУ: с традиционными компонентами на лицевой стороне и монтируемыми на поверхность простыми компонентами (чипами и транзисторами) на обратной. Некоторые ПМ ИЭТ (даже пассивные) могут быть повреждены при погружении в припой во время пайки. Поэтому важно учитывать их термостойкость. Если пайка двойной волной применяется для монтажа плат с установлен-
124
ными на их поверхности ПМ ИЭТ сложной структуры, необходимы некоторые предосторожности:
–применять поверхностно-монтируемые ИС, не чувствительные к тепловому воздействию;
–снизить скорость транспортера;
–проектировать коммутационную плату таким образом, чтобы исключить эффект затенения.
Хорошо разнесенные, не загораживающие друг друга компоненты способствуют попаданию припоя на каждый требуемый участок платы, но при этом снижается плотность монтажа. При высокой плотности монтажа, которую позволяет реализовать технология монтажа на поверхность, с помощью данного метода практически невозможно пропаять поверхностно-монтируемые компоненты с четырехсторонней разводкой выводов (например, кристаллоносители с выводами). Чтобы уменьшить эффект затенения, прямоугольные чипы следует размещатьперпендикулярно направлениюдвиженияволны.
Пайка печатных узлов в паровой фазе
Процесс пайки в паровой фазе начинается с нанесения способом трафаретной печати припойной пасты на контактные площадки ПП. Затем на поверхность платы устанавливаются ПМ ИЭТ.
В ряде случаев припойную пасту после нанесения просушивают с целью удаления из ее состава летучих ингредиентов или предотвращения смещения компонентов непосредственно перед пайкой. После этого плата нагревается до температуры расплава припойной пасты. В результате образуется паяное соединение между контактной площадкой платы и выводом ПМ ИЭТ.
Метод пайки в паровой фазе является разновидностью пайки расплавом дозированного припоя, в ходе которой пары специальной жидкости конденсируются на коммутационной плате, отдавая скрытую теплоту парообразования открытым участкам ПУ. При этом припойная паста расплавляется и образует галтель между выводом компонента и контактной площадкой платы. Когда температура платы достигает температуры жидкости, процесс конденсации прекращается,
125
тем самым заканчивается и нагрев пасты. Повышение температуры платы, от ее начальной температуры (например, окружающей среды перед пайкой) до температуры расплавленного припоя, осуществляется очень быстро и не поддается регулированию. Поэтому необходим предварительный подогрев платы с компонентами для уменьшения термических напряжений в компонентах и местах их контактов с платой. Температура расплава припоя также не регулируется и равна температуре кипения используемойприпайкежидкости.
Пайка расплавом дозированного припоя инфракрасным нагревом
Процесс пайки ПМ ИЭТ, собранных на коммутационной плате, с помощью ИК-нагрева аналогичен пайке в паровой фазе, за исключением того, что нагрев платы с компонентами производится не парами жидкости, а ИК-излучением.
Основным механизмом передачи тепла, используемым в установках пайки с ИК-нагревом, является излучение. Передача тепла излучением имеет большое преимущество перед теплопередачей за счет теплопроводности и конвекции. Это единственный из механизмов теплопередачи, обеспечивающий передачу тепловой энергии по всему объему монтируемого устройства. Остальные механизмы теплопередачи обеспечивают передачу тепловой энергии только поверхности монтируемого изделия.
В процессе пайки ИК-излучением скорость нагрева регулируется изменением мощности каждого излучателя и скорости движения транспортера с ПП. Поэтому термические напряжения в компонентах и платах могут быть снижены посредством постепенного нагрева элементов. Основным недостатком пайки с ИК-нагревом является то, что количество энергии излучения, поглощаемой компонентами и платами, зависит от поглощающей способности материалов, из которых они изготовлены. Поэтому в пределах монтируемого устройства нагрев осуществляется неравномерно. Пайка кристаллоносителей без выводов или с J-образными выводами мо-
126
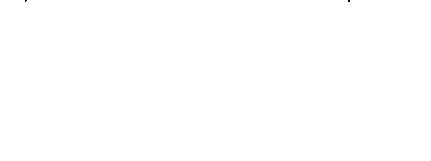
жет оказаться невозможной в установках с ИК-нагревом, если компонент непрозрачен для ИК-излучения.
В качестве источников ИК-излучения применяются ИК-лампы или панельные излучающие системы (ТЭНы).
Каждый из этих источников имеет свои достоинства и недостатки. ТЭНы более инерционны, чем лампы, что, в свою очередь, увеличивает инерционность всей установки пайки. ИК-лампы имеют большую неравномерность ИК-излучения по длине лампы. При определенной конструкции ТЭНов равномерность излучения по ширине транспортера, т.е. по всей ширине ПП, может быть повышена. В обоих случаях тепло ПП и компонентам передается как за счет излучения (50¼70 %), так и конвекцией (50¼30 %).
ЗАО ЦНИТИ «Техномаш-Трасса» совместно с предприятием S.M.D. (г. Рига, Латвия) поставляется установка ИК-пайки печатных узлов SMD-TRASSA-5609. Основные параметры установки приведены в табл. 2.
Таблица 2
Основные параметры установки ИК-пайки печатных узлов SMD-TRASSA-5609
№ |
Параметр установки |
Значение |
|
п/п |
параметра |
||
|
|||
1 |
Температура в зоне предварительного нагрева, °С |
100...270 |
|
2 |
Температура в зоне оплавления, °С |
100...300 |
|
3 |
Время достижения рабочей температуры, мин, не более |
20 |
|
4 |
Ширина конвейера, мм |
250 |
|
5 |
Скорость движения конвейера, мм/мин |
100...300 |
|
6 |
Напряжение питания, В (ГЦ) |
220 (50) |
|
|
Потребляемая мощность, кВ А |
|
|
7 |
1,5 |
||
8 |
Габаритные размеры, мм |
1630× 465× 180 |
|
9 |
Масса, кг, не более |
40 |
Установка предназначена для пайки печатных узлов, выполненных по технологии монтажа на поверхность. Установка имеет пять зон нагрева. В зонах предварительного нагрева осуществляется двустороннийнагревсвозможностьюотключения нижнихнагревателей.
127
Установка снабжена микропроцессорной системой управления, позволяющей поддерживать заданные режимы пайки, сохранять в памяти до десяти температурных профилей. Имеется возможность подключения внешнего термометра для измерения температуры на поверхности паяемого изделия и подключения компьютера для отображениятемпературныхпрофилейнамониторе.
Установка снабжена конвейером из стальных пружинных тросиков с регулируемой скоростью движения. Значения всех параметров отображаются на жидкокристаллическом индикаторе. Предусмотрена возможностьподключениявытяжнойвентиляции.
13.2. Вакуумно-компрессионные агрегаты
При пайке деталей сложной конфигурации, в частности деталей и узлов жидкостных ракетных двигателей, необходимо не только равномерно нагреть паяемое изделие, но и обеспечить зазоры под пайку за счет прилагаемого давления. Для обеспечения заданных механических свойств металла изделия иногда требуется отрегулировать скорость его охлаждения после пайки. Для этого разработаны вакуумно-компрессионные агрегаты типа ВКА-750П0, ВКА-200ПО, представляющие собой горизонтальные, герметичные, цилиндрические сосуды со сферическими крышками, по стенкам которых размещается индуктор. Внутри индуктора устанавливается цилиндрический кожух (экран) из жаропрочной стали ЭИ-435. Кожух нагревается за счет индуцируемых в нем токов от индуктора. От нагретых стенок кожуха тепло излучением передается на паяемое изделие. Корпус печи по всей поверхности охлаждается водой. Передняя крышка печи устанавливается на передвижной манипулятор, на котором монтируется паяемое изделие.
Манипулятор имеет систему для откачки воздуха из внутренних полостей изделия и механизмы для его вращения и перемещения. Крышка печи герметично закрывается специальным байонетным затвором и уплотняется кольцевым шланговым уплотнителем. В кожух
128
печи вварены патрубки для откачки воздуха с целью создания вакуума или наполнения ее контролируемой атмосферой. Управление вентилями и шиберами печи дистанционное с щита управления.
Для шахтной пайки разработаны вертикальные индукционные печи типа ВИП-2, состоящие из металлического кожуха, футерованного огнеупорным ультралегкого веса кирпичом. Внутри корпуса смонтирован индуктор. В печь опускается контейнер с паяемыми деталями. Стенки контейнера из стали ЭИ-435 нагреваются от индуктора, и излучением нагрев передается на паяемой детали. Пайка деталей производится в контролируемой атмосфере.
Индукционные печи по сравнению с печами сопротивления имеют ряд преимуществ: значительно экономится электроэнергия, так как печь включается только на цикл пайки; за счет малой инерционности печей более гибким становится процесс управления циклом пайки; улучшаются условия труда паяльщиков, так как печь во время загрузки и выгрузки деталей находится в холодном состоянии.
13.3. Пайка в паровой фазе
Основа процесса пайки в паровой фазе – конденсация паров специальной нагретой жидкости на печатной плате, в результате которой энергия, выделяемая при фазовом переходе, передается открытым участкам сборки. При этом происходит оплавление припойной пасты и образование паяных соединений. Температура кипения жидкости – равновесная (она же максимальная) температура, обеспечиваемая данным видом пайки. Выбирается жидкость с известной точкой кипения, равной требуемой температуре пайки, после нее конденсация пара на сборке прекращается и дальнейший рост температуры физически невозможен. Вследствие этого устраняется необходимость точного подбора и строгого контроля максимальной температуры и становится принципиально невозможным перегрев сборки.
В качестве рабочей жидкости используются химически инертные, некоррозионные составы на основе фтороуглерода (преимуще-
129
ственно применяются перфторполиэфирные (PFPE, Perfluoropolyether) жидкости GALDEN), имеющие различные точки кипения; для пайки электронных модулей применяются жидкости с типичным диапазоном точек кипения от 200 до 260 °С и выше (вплоть до 320 °С). Жидкости не содержат фреон и не наносят ущерба окружающей среде.
Впроцессе развития технологии сформировались два варианта
еереализации: пайка насыщенным и ненасыщенным паром. Первый вариант находит применение в так называемых вертикальных системах с резервуаром (vertical tank) и вертикальным движением сборки при пайке, второй – в горизонтальных, оснащенных рабочей камерой (vapor chamber) и горизонтальным движением сборки. Ряд производителей работает с насыщенным паром (ASSCON SystemtechnikElektronik GmbH), другие– с ненасыщенным (rehm Anlagenbau GmbH).
Ниже рассмотрены особенности реализации каждого варианта, их достоинства и недостатки.
Пайка насыщенным паром. Вертикальные системы. Метод основан на передаче тепла сборке от сконденсированной на ней жидкости. Типичная последовательность выполнения операции пайки при этом следующая (рис. 26).
Сборка (рис. 26, а) перемещается в резервуар и располагается над зоной пара (рис. 26, б), образующегося над нагретой до точки кипения рабочей жидкостью. Осуществляется предварительный нагрев сборки (ИК-нагревом, предварительным погружением в паровую среду и прочими методами). Методы предварительного нагрева подробно рассмотрены ниже.
Сборка погружается в паровую среду и нагревается. Воздух вытесняется инертным фторуглеродным паром, так как вес паров жидкости высок, и дальнейшие процессы происходят в полностью инертной среде. Паровойзащитныйпокровполностьюнакрывает сборку.
Пар конденсируется на поверхности сборки и передает ей свою энергию (рис. 26, в). Образуется защитная инертная атмосфера без необходимости использования азота.
130