
Химическая технология неорганических веществ
..pdf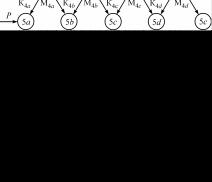
Существует несколько схем |
|
процесса. Одна из них (тре- |
|
угольная) показана на рис. 61. |
|
Исходная смесь F подается на |
|
первую стадию кристаллизации, |
|
где она растворяется в чистом |
|
растворителе Р. После охлажде- |
|
ния раствора получаются кри- |
|
сталлическая фаза К1 и маточник |
|
М1. Кристаллы К1 передаются на |
|
стадию 2а, а маточник М1 час- |
Рис. 61. Схема дробной перекристал- |
тично упаривается и подается на |
|
стадию 2b. |
лизации из раствора |
|
На стадии 2а производится перекристаллизация К1 в чистом растворителе с получением кристаллов К2а и маточника М2а. При кристаллизации маточника М1 на стадии 2b соответственно получаются кристаллы К2b и маточник М2b. Кристаллы К2а передаются на стадию 3а. Маточник М2а объединяют с кристаллами К2b и подают на стадию 3b, а маточник М2b – на стадию 3с. Далее процесс продолжается аналогичным образом до тех пор, пока не будет достигнута требуемая степень разделения.
При разделении двух компонентов по данной схеме перекристаллизации компонент, менее растворимый в используемом растворителе, концентрируется в левой части схемы, а компонент с более высокой растворимостью – в ее правой части. Если в разделяемой смеси содержатся и другие компоненты с промежуточной растворимостью, то они концентрируются в центральной части схемы.
Массовая фракционная кристаллизация в аппаратах с внешними охлаждающими поверхностями широко применяется для разделения и очистки различных веществ в лабораторной практике и в промышленности. Для ее осуществления применяют различные аппараты, с охлаждающими рубашками или с погружными элементами (змеевиками, трубчатками, дисками и т.п.). Охлаждающими агентами служат различные жидкости, сохраняющие агрегатные состояния
241
(вода, рассолы, органические вещества с низкой температурой затвердевания и др.), а также испаряющиеся жидкости (аммиак, фреоны, пропан, этан и др.). Последние используют чаще всего при фракционировании низкоплавких смесей.
Рассматриваемый процесс может осуществляться как в периодическом, так и в непрерывном режиме. В первом случае охлаждающий агент поступает в кристаллизатор с постоянной начальной температурой, либо температуру хладагента в процессе кристаллизации изменяют по определенной программе. Как правило, при программном охлаждении получают более крупные, хорошо сформировавшиеся кристаллы, что повышает эффективность процесса разделения.
Метод фракционной кристаллизации при непосредственном контакте разделяемой смеси с хладагентами имеет следующие преимущества (по сравнению с массовой фракционной кристаллизацией
сотводом тепла через теплопередающие поверхности):
–высокая интенсивность тепло- и массообмена, обусловленная развитой межфазной поверхностью и интенсивным перемешиванием;
–возможность кристаллизации при незначительной разности температур между кристаллизующейся смесью и хладагентом (по-
рядка 0,5–2,0 °С);
–отсутствие в кристаллизаторах теплообменных поверхностей, что исключает их инкрустацию и существенно упрощает конструкцию аппаратов;
–возможность изготовления аппаратов из конструкционных материалов с низкой теплопроводностью (полимеры, стекло, керамика и т.д.), а также их защиты различными антикоррозионными покрытиями (эмаль, резина, лаки, полимерные и другие мастики).
Рассматриваемому процессу присущи и недостатки: возможность загрязнения продуктов разделения хладагентом; дополнительная стадия отделения отработанного хладагента от кристаллизата, сопряженная с установкой дополнительного оборудования.
В качестве хладагентов используют охлажденные жидкости и газы, сжиженные газы, которые при контакте с кристаллизующейся
242

смесью переходят в газообразное состояние, а также твердые вещества, расплавляющиеся в процессе контактной кристаллизации. К контактной кристаллизации также следует, видимо, отнести процесс фракционной кристаллизации при смешении исходной смеси с сильно переохлажденным растворителем.
Примером применения метода кристаллизации непосрественным контактом с хладагентом является опреснение морской воды. Опреснение морской воды производят с использованием испаряющегося хладагента (например, бутана). Исходную воду F первоначально подают в поверхностный теплообменник Т1, где ее частично охлаждают сбрасываемым маточником М и опресненной водой Во (рис. 62). Затем воду вместе с рециркулирующим маточником Мр подают на стадию кристаллизации Кр, где ее непосредственно смешивают с жидким хладагентом X. В результате контактного теплообмена происходит испарение хладагента и частичная кристаллизация воды. Образующуюся суспензию подают на стадию сепарации Ф, где происходит отделение кристаллов льда К от маточника (рассола) M∑, обогащенного солями.
Рис. 62. Принципиальная схема опреснения морской воды
243
Часть маточника М пропускают через теплообменник Т1 и сбрасывают, а другую его часть Мр направляют на рециркуляцию. Пары хладагента из кристаллизатора Кр отсасывают, сжимают компрессором К1 и подают в плавитель Пл, где в результате непосредственного контакта с расплавляющимся льдом они конденсируются. Однако изза потерь холода в окружающую среду на стадиях Кр, Ф, Пл, К1, а также в трубопроводах при расплавлении льда не удается полностью сконденсировать весь поток хладагента X. Поэтому часть паров Х1 отсасывают из плавителя, сжимают компрессором К2, конденсируют в поверхностном теплообменнике Т2 и возвращают в плавитель Пл. Охлаждение потока Х1 в теплообменнике обычно производят морской водой.
Из плавителя жидкий хладагент и воду направляют на стадию декантации, где в результате расслаивания происходит отделение хладагента X от воды В. Хладагент возвращают на стадию кристаллизации. Часть полученной опресненной воды Вп отбирают для промывки кристаллов льда от захваченного маточника, а основную часть Во передают потребителям.
Рециркуляция маточника благоприятно отражается на процессе опреснения; при увеличении потока Мр, как правило, наблюдается рост размеров кристаллов льда, что снижает захват солей кристаллической фазой и облегчает процесс последующего разделения суспензии. Однако сильное увеличение потока Мр требует больших рабочих объемов кристаллизаторов, возрастают объемы перекачиваемой жидкости. В результате удельные затраты на процесс могут резко возрасти. Выбор оптимального значения Мр может быть сделан на основании технико-экономического анализа работы всей установки. Стадию кристаллизации в промышленных установках проводят в горизонтальных или вертикальных кристаллизаторах непрерывного действия. Разделение суспензии и промывку кристаллов льда осуществляют чаще всего с использованием промывных колонн. Степень извлечения опресненной воды зависит от содержания соли в исходной воде и режимов процесса разделения. Она обычно составляет 0,5–0,8. Производительность промышленных установок по опрес-
244
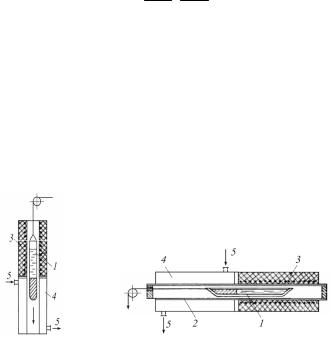
ненной воде достигает 1000 м3 в сутки и более, а удельные затраты энергии составляют 4–7 кВт·ч/м3 .
Для глубокой очистки веществ чаще используют кристаллизацию из расплава.
Составы равновесных жидкой и твердой фаз определяются диаграммами плавкости.
В реальных системах при небольшом содержании примеси состав системы можно описать диаграммой с непрерывным рядом твердых растворов.
Коэффициент разделения в кристаллизационных методах
α = 1−x x : 1–y y ,
где x – мольная доля примеси в твердой фазе; y – мольная доля примеси в жидкой фазе.
Если x << 1 и y << 1, то α = x/y. Эту величину часто называют коэффициентом распределения примеси. Коэффициент распределения можно оценить расчетным путем либо найти по диаграмме плавкости (приближенно).
Направленная кристаллизация
Схематично метод направленной кристаллизации представлен на рис. 63.
а |
б |
Рис. 63. Схемы установок для направленной кристаллизации с использованием вертикального (а) и горизонтального (б) контейнеров: 1 – контейнер; 2 – стеклянная труба; 3 – нагревающая секция; 4 – охлаждающая секция; 5 – охлаждающий агент
245
Направленную кристаллизацию можно проводить в горизонтальных, вертикальных и наклонных контейнерах. В горизонтальных установках (см. рис. 63) используют открытые или закрытые контейнеры в форме «лодочек». При очистке веществ, имеющих не очень высокую температуру плавления, контейнер 1 с разделяемой смесью помещают в стеклянную или кварцевую трубу 2, которая проходит через нагревательную и охлаждающую секции. Конструкции этих секций весьма разнообразны.
Нагревательная секция 3 чаще всего представляет собой трубчатую электропечь, с помощью которой поддерживают определенный градиент температур в расплаве. Иногда нагревательную секцию выполняют в виде обогревающей рубашки, через которую пропускают жидкий теплоноситель, в ряде случаев – в виде обогреваемого металлического блока. Охлаждающая секция 4, с помощью которой отводят тепло при кристаллизации, может быть выполнена в виде рубашки. В некоторых случаях охлаждение осуществляют путем обдува контейнера холодным воздухом, или же кристаллизация происходит вследствие потерь тепла в окружающую среду.
В установках вертикального типа (рис. 63, б) контейнер с разделяемой смесью обычно спускают вниз, и кристаллизация начинается
внижней части контейнера, который в данном случае чаще всего имеет цилиндрическую форму. Для создания градиента температур
вобеих фазах иногда применяют две несмешивающиеся жидкости, причем верхняя нагрета, а нижняя охлаждена. Поскольку конвекция происходит главным образом внутри каждой жидкости, а не через поверхность расслаивания, то температуры этих жидкостей могут различаться на несколько десятков градусов.
При α > 1 твердая фаза имеет более высокую концентрацию примеси, чем жидкая, при α < 1 твердая фаза имеет меньшую концентрацию примеси, чем жидкая.
Обозначим Nо – общее количество вещества в исходном расплаве; Nт – количество вещества, закристаллизовавшегося к некоторому времени; n = Nт/Nо. Тогда из материального баланса
246
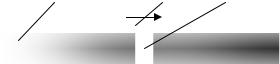
∂ [y(No – Nm)] = x∂(No – Nm)
при α = const. Тогда y = yo (1 – n)α–1 и x = xoα(1 – n)α–1.
В среднем степень очистки за однократную операцию составля-
ет 0,7–0,8.
С целью повышения глубины очистки применяют многократную направленную кристаллизацию с отбрасыванием в конце каждого цикла некоторой части расплава, в которой концентрируется примесь.
Зонная перекристаллизация (плавка)
Схематически зонная |
перекристаллизация изображена на |
|||||||
рис. 64. |
|
|
|
|
|
|
|
|
1 |
2 |
3 |
|
|||||
|
|
|
|
|
|
|
|
|
|
|
|
|
|
|
|
|
|
|
|
|
|
|
|
|
|
|
|
|
|
|
|
|
|
|
|
Рис. 64. Схема устройства для зонной перекристаллизации: 1 – очищаемый материал; 2 – нагреватель; 3 – зона расплавления
Вдоль слитка 1, изготовленного из материала, подвергаемого очистке, медленно перемещается мощный нагреватель 2, который обеспечивает расплавление материала в узкой зоне 3. По мере передвижения нагревателя зона расплавления перемещается с одного конца слитка к другому. При этом если жидкая фаза обогащена примесью (α < 1), то зона, обогащенная примесью, медленно перемещается в направлении движения нагревателя. После одного прохода нагревателя участок слитка, обогащенный примесью, удаляют и процесс повторяют снова.
Если x0 – начальное количество примеси в твердой фазе, то x/х0 = 1 – (1 – α)·ехр(–αu); u = Nт/G, G – количество молей жидкой фазы. Глубина очистки слитка за один проход составляет 70–80 %.
247
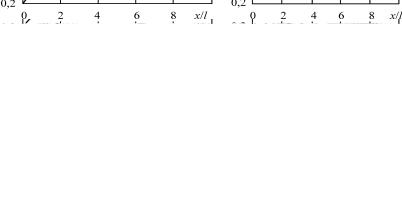
В зависимости от значения коэффициента распределения возможны два варианта перераспределения примеси по длине образца. Если примесь понижает температуру плавления образца, она концентрируется преимущественно в расплавленной зоне, передвигаясь с ней (рис. 65, а). Такая картина наблюдается в случаях, когда растворимость примеси в жидком состоянии больше, чем в твердом, т.е. при а < 1. В результате перехода примеси в жидкую фазу ее концентрация в твердой фазе, образующейся после прохода расплавленной зоны, понижается. При этом наибольшая степень очистки достигается в начале образца, где концентрация примеси в расплавленной зоне наименьшая. При продвижении зоны вдоль образца происходит постепенное накапливание примеси в ней; соответственно фазовому равновесию повышается также ее концентрация в твердой фазе. Наступает момент, когда концентрация примеси в твердой фазе достигает ее исходного значения в образце. При дальнейшем движении зоны обычно концентрации примеси в образующейся кристаллической фазе и в зоне некоторое время остаются неизменными. При этом СК = СF, а концентрация в зоне равна СF/α.
|
|
|
|
|
|
|
|
|
|
|
|
|
|
|
|
|
|
а |
б |
Рис. 65. Распределение примеси по длине образца: а – после одного прохода; б – при различном числе проходов и α = 0,9
248
На конце образца, равном длине зоны, происходит затвердевание материала по законам направленной кристаллизации, сопровождающееся быстрым возрастанием концентрации примеси.
В общем случае кривая распределения примеси после одного прохода зоны состоит из трех участков: очищенного вещества, однородного состава (горизонтальный участок) и повышенной концентрации примеси. Поскольку общее содержание примеси в образце остается неизменным, площадь, ограниченная начальным участком кривой распределения и горизонталью С = CF, равна площади, ограниченной конечным участком кривой распределения и горизонталью C = CF. Длина участка с постоянной концентрацией примеси зависит от ее растворимости в твердом и жидком состояниях, т.е. от коэффициента распределения. С увеличением последнего протяженность горизонтального участка уменьшается; при приближении коэффициента распределения к единице этот участок может вообще исчезнуть
(см. рис. 65, а).
Если содержание примеси в исходном образце повышает температуру плавления последнего (α > 1), то при движении расплавленной зоны концентрация примеси в ней понижается. Подобная картина наблюдается в случаях, когда растворимость примеси в твердом состоянии выше, чем в жидком. Тогда наибольшая концентрация примеси создается в начале образца, а наименьшая – в конце его.
Один из важных факторов, определяющих эффективность процесса очистки, – скорость движения зон. Она сильно зависит от коэффициента диффузии примеси в расплавленной зоне, который обычно очень мал, особенно для веществ с большой вязкостью расплава. При низком коэффициенте диффузии возможно образование непосредственно перед движущимся фронтом кристаллизации слоя с повышенным содержанием примеси, что, естественно, приводит к снижению степени разделения. С увеличением скорости движения зон вероятность появления такого слоя возрастает. На практике скорости движения расплавленных зон колеблются в широких пределах – от 0,5 до 20 см/ч.
Используют также зонное замораживание (обратный процесс).
249
Недостатки указанных кристаллизационных методов – малый выход продукта и большая длительность процесса. В этом отношении большими возможностями обладает метод противоточной кристаллизации. Осуществляется он в кристаллизационных колоннах, в которых создается противоток кристаллов и расплава. Наиболее эффективны колонны, в которых кристаллы транспортируются шнеком.
7. РАСЧЕТЫ В ТЕХНОЛОГИИ НЕОРГАНИЧЕСКИХ ВЕЩЕСТВ
7.1. Материальный баланс печи обжига флотационного колчедана
Баланс рассчитывается на 1 т сухого флотационного колчедана.
Исходные данные:
Массовое содержание серы в колчедане СSк = 45 %, в огарке СSог = 1,5 %. Содержание SO2 в сухом обжиговом газе СSO2 = = 14 мол. %. Влажность флотационного колчедана w = 0,04 кг/кг, воздуха v = 0,01 кг/кг. Мольные объемы при нормальных условиях кислорода и азота vO2 = 22,4 и vN2 = 22,4 кмоль/м3, SO2 – vSO2 =
=21,9 кмоль/м3.
Врасчете принято, что сера в колчедане содержится в виде пирита FeS2. Кроме пирита в колчедане содержится инертная порода.
Впроцессе обжига протекают реакции:
FeS2 = FeS + S, |
(1) |
4FeS + 7O2 = 2Fe2O3 +4SO2, |
(2) |
S + O2 = SO2. |
(3) |
Реакции (1) и (3) протекают полностью, реакция (2) протекает не до конца с учетом, что в твердом продукте обжига – огарке – сера содержится в виде FeS.
Подаваемый на обжиг воздух содержит кислорода 21 и азота 79 мол. %. Вся вода, приходящая с колчеданом и воздухом, при обжиге переходит в обжиговый газ.
250