
Химическая технология неорганических веществ
..pdf5.Разработка способов сокращения объема дистиллерной жидкости (получение известкового молока путем репульпирования «пушонки» дистиллерной жидкости, подача сухой извести в смеситель, упаривание дистиллерной жидкости газами содовых печей).
6.Повышение степени использования тепла.
В табл. 16 приведены данные об использовании тепла в современном производстве соды.
Таблица 16 Данные об использовании тепла в отделениях производства
Отделение |
Доля общего |
Тепловой КПД |
|
потребления |
|||
|
|
||
обжига известняка |
19,9 |
72,8 |
|
кальцинации |
26,8 |
37 |
|
дистилляции |
41,7 |
25,1 |
|
карбонизации |
3,3 |
60,1 |
Общий КПД составляет 43 %. Ставится задача довести тепловой КПД до 69 %. Например, на стадии дистилляции это – применение термокомпрессоров (первый испаритель – термокомпрессор – дистилляция).
Производство «тяжелой соды»
Обычная «легкая сода» имеет насыпную плотность 500– 550 кг/м3, «тяжелая сода» – 900–1000 кг/м3.
Существует два способа производства «тяжелой соды». Первый способ основан на получении «тяжелой соды» из моногидрата Na2CO3·H2O. Соду после кальцинации увлажняют конденсатом и направляют в барабанный кристаллизатор. Затем моногидрат карбоната натрия после смешения с ретурной «тяжелой содой» подают в содовую печь. После отделения на грохотах товарная фракция отправляется на склад, а крупная – измельчается в валковой дробилке и снова подается на грохочение и выделение продукта.
101
Второй способ получения «тяжелой соды» основан на прессовании «легкой». Получаемые при прессовании пластины Na2CO3 дробят и рассеивают.
3.3.5.Комплексная переработка нефелина
ВРоссии большое значение приобретает комплексная перера-
ботка нефелина (Na, K)2O Al2O3 2SiO2. Соотношение между K2O и Na2O непостоянно и существенно меняется для нефелинов различных месторождений. Щелочные алюмосиликатные породы, содержащие значительные количества нефелина, объединены в группу пород под названием нефелиновых сиенитов. Имеются крупные запасы нефелинов на Кольском полуострове, на Кия-Шалтырском и Тежарском месторождениях.
Из апатито-нефелиновых руд Хибинского месторождения методом флотации получают апатитовый и нефелиновый концентраты. Нефелиновый концентрат имеет следующий усредненный химиче-
ский состав (мас. %): |
|
|
Al2O3…..29,2 |
Na2O…..2,1 |
Fe2O3 …..2,5 |
SiO2……43,2 |
K2O……7,1 |
FeO…….1,0 |
TiО2…......0,5 |
СаО…...1,6 |
MgО……0,5 |
Рассматриваемый комплексный способ переработки нефелина включает следующие комплексы процессов:
–производство глинозема (Al2O3) с получением в качестве отходов растворов соды и поташа, а также нефелинового шлама;
–переработка нефелинового шлама на портланд-цемент;
–переработка растворов Na2CO3 и К2СО3 на кальцинированную соду и поташ. Принципиальная схема комплексной переработки нефелина на глинозем, соду, поташ и цемент представлена на рис. 29. Схема получения глинозема при этом очень близка к процессу производства Al2O3 из бокситов методом спекания.
Нефелиновый концентрат поступает с обогатительной фабрики
ввиде порошка с размером частиц мельче 170 мкм на стадию смешения (приготовления шихты). Шихта составляется только из двух
102
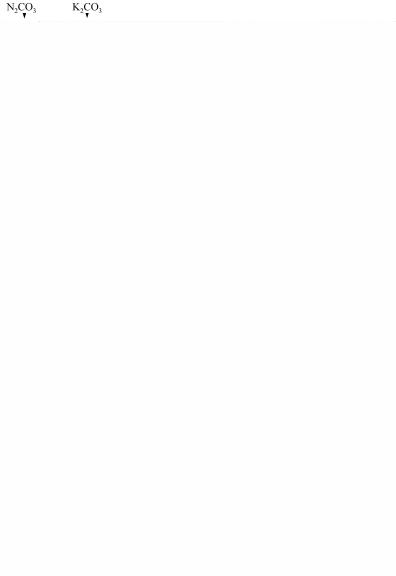
Рис. 29. Принципиальная схема производства глинозема, соды, поташа и цемента из нефелинового концентрата
103
компонентов – нефелинового концентрата и известняка, высушенного и измельченного до –170 мкм, т.к. в самом нефелине содержится такое количество оксидов щелочных элементов (Na2O + K2O), которые связывают глинозем (Al2O3) в соответствующие алюминаты.
Известняк вводится в шихту из расчета образования двухкальциевого силиката (2СаО SiO2), т.е. в соотношении 2СаО : SiO2 = = 2 ± 0,1. Чтобы выдержать это соотношение практически, на 1 т нефелинового концентрата вводят 1,6–1,7 т известняка.
После тщательного перемешивания шихта подвергается спеканию во вращающейся трубчатой печи. Температура в печи поддерживается на уровне 1300 ± 20 °С. В этих условиях взаимодействие нефелина с известняком протекает по уравнению
(Na,K)2O Al2O3 2SiO2 + 4CaCO3 =
= (Na,K)2O Al2O3 + 4CO2 + 2(2CaO SiO2).
После охлаждения спек подвергается дроблению, а затем выщелачиванию оборотным содопоташным раствором. Выщелачивание ведут одновременно с размолом спека в стержневых мельницах до размера частиц 0,25–0,15 мм. При этом алюминаты щелочных металлов и небольшое количество SiO2 в виде Na2SiO3 переходят в раствор, а 2CаO SiO2 и примеси остаются в осадке – шламе. Оптимальными условиями выщелачивания спека являются: 1) на 1 моль Al2O3 спека должно приходиться не менее 1 моля R2CO3 (т.е. Na2CO3 + K2CO3) в растворе; 2) температура раствора 70–80 °С. В результате выщелачивания получается раствор с концентрацией око-
ло 100 г/л Al2O3, 120–125г/л Na2O общ (R2O) и около 3,5 г/л SiO2.
Суспензия двухкальциевого силиката в этом растворе подвергается фильтрованию на карусельных вакуум-фильтрах (так же, как суспензия гипса в кислоте в производстве Н3РО4).
Раствор алюминатов калия и натрия идет на стадию обескремнивания, а промытый нефелиновый шлам – на стадию смешивания с молотым известняком. Для переработки нефелинового шлама, содержащего примерно 56 % СаО; 28 % SiO2, примеси (Fe2O3 4,9 %,
104
Al2O3 2,8 %, Na2O + K2O 2,2 %) и до 30 % Н2О, на портланд-цемент составляется шихта из 75 % шлама и 25 % известняка, которая подвергается мокрому помолу на шаровых мельницах. Пульпа из мельниц с содержанием влаги 36–38 % в пульверизированном состоянии обжигается во вращающейся цементной печи при температуре факела не ниже 1550 °С. Полученный клинкер после охлаждения размалывается в шаровых мельницах и транспортируется на склад готовой продукции.
Обескремнивание проводят в одну стадию и в две стадии. При двухстадийном обескремнивании первую стадию проводят в автоклавах при давлении 3,5 атм и температуре 150 °С в течение 3 ч в присутствии затравки. Процесс можно представить реакцией
2Na2SiO3 + Na2O Al2O3 + 4Н2О
Na2O Al2O3 2SiO2 2Н2О + 4NaОН.
Это значит, что процесс сопровождается потерями Na2O и Al2O3. При одностадийном обескремнивании и на второй стадии двухстадийного процесса в алюминатный раствор добавляют известковое молоко в таком количестве, чтобы силикат натрия перевести в труднорастворимый и быстро кристаллизующийся гидроалюмосиликат
кальция:
2(Na2O SiO2) + Na2O Al2O3 + Са(ОН)2 + 4Н2О = = СаО Al2O3 2SiO2 2Н2О + 6NaОН.
Процесс ведут в аппаратах с мешалками при 80–90 °С. Получившуюся суспензию разделяют на пресс-фильтрах. Осво-
божденный от кремнезема алюминатный раствор направляют на стадию карбонизации, а белый шлам промывают на фильтрах и посылают на стадии смешения или с нефелиновым концентратом (гидроалюмосиликат натрия), или с нефелиновым (красным) шламом (гидроалюмосиликат кальция).
Карбонизацию алюминатного раствора проводят в аппаратах с рамными мешалками (8 об/мин) высотой 8 м. В низ аппарата подается тщательно очищенный печной газ со стадии спекания
105
(10–14 % СО2). При этом протекает реакция карбонизации алюминатов натрия и калия:
2NaAlO2 + СО2 + 3Н2О = 2Al(OН)3 + Na2СO3.
Аналогичная реакция протекает с алюминатом калия. Из-за снижения каустического модуля раствора протекает и гидролиз алюминатов:
Na2O Al2O3 + 4Н2О 2Al(OН)3 + Na2OН.
Чтобы обеспечить выделение крупных кристаллов Al(OН)3 размером 60–80 мкм, карбонизацию ведут в присутствии затравки при повышенной температуре (70–80 °С), т.е. при минимальной степени пересыщения раствора по Al(OН)3.
После отделения от маточного раствора фильтрованием и промывки осадок гидроксида алюминия направляют на кальцинацию. Кальцинацию ведут в барабанных (трубчатых) вращающихся печах. Температура факела 1200 °С. При этом Al(OН)3 переходит в γ-Al2O3,
а часть ( 20 %) в α-Al2O3.
Отфильтрованный маточный раствор (Na2СO3 + К2СО3) в количестве 55 % идет на выщелачивание новых порций нефелинового спека, а остальные 45 % поступают на производство кальцинированной соды и поташа. Примерный (условный) состав раствора, полученного из Кольского нефелинового концентрата одностадийной карбонизацией, следующий (г/л): Na2СO3 114,1; К2СО3 62,0; K2SO4
7,7; KOН 2,7; KCl 0,6; Al2O3 0,93. Поскольку в топливе, используе-
мом для спекания, обычно содержится сера, в растворе появляется сульфат-ион, хотя в нефелиновом концентрате нет его. Кроме того, в раствор может переходить и весь содержащийся в нефелиновом сиените KCl.
Карбонатный раствор перед переработкой на соду и поташ подвергают нейтрализации. После этого растворы можно рассматривать как пятикомпонентную систему Na+, K+/ СО2–3, SO2–4, Cl– – Н2О, графическое исследование которой связано с обычными в таких случаях трудностями.
106
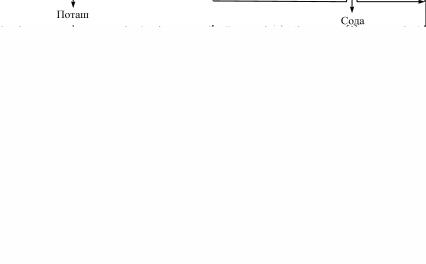
На практике соду и поташ получают методом политермического упаривания с промежуточным охлаждением. Схема процесса довольно сложна. В нее включены возвращение в начальную стадию выпарки двойной соли Na2СO3 К2СО3, выделение из раствора
втвердую фазу сульфата калия, двухстадийная кристаллизация соды и поташа, а также предварительное выделение из исходных щелоков KCl с целью получения поташа хорошего качества.
Но для стекольной промышленности, например, присутствие
всоде К2СО3 и К2SО4 является допустимым. При этом переработка карбонатных растворов упрощается. На рис. 30 представлена принципиальная схема получения соды и поташа при комплексной переработке нефелина. По этой схеме продукты получаются пониженного качества. Например, сода в среднем содержит (мас. %) Na2СO3
91,3; К2СО3 6,2; К2SО4 2,5, тогда как сода, полученная по схеме с многократным разделением солей при выпарке, содержит в сред-
нем (%) Na2СO3 95,6; К2СО3 3,3; К2SО4 1,0.
Рис. 30. Упрощенная схема получения соды и поташа при химической переработке нефелина
107
Получение поташа при комплексной переработке нефелина практически является в России единственным способом его производства. В соответствии с ГОСТ 10690–73 предусматривается выпуск карбоната калия технического (поташа) трех сортов. Он должен соответствовать (в пересчете на прокаленное при 500 °С вещество) следующим нормам:
Содержание, мас. %: |
1-й сорт |
2-й сорт |
3-й сорт |
К2СО3, не менее |
98,0 |
94,0 |
92,5 |
Na2СO3, не более |
0,6 |
3,2 |
5,0 |
Хлориды в пересчете на Cl–, |
|
|
|
не более |
0,05 |
1,0 |
2,0 |
сульфаты (SO42− ), не более |
0,4 |
0,6 |
0,9 |
алюминия (Al2O3), не более |
0,25 |
0,8 |
1,0 |
железа (Fe2O3), не более |
0,002 |
0,005 |
не норм |
п.п.п. (500 °С), не более |
|
|
|
для кальцинированного |
5,0 |
5,0 |
5,0 |
для полутораводного |
18,5 |
20,0 |
20,0 |
В результате переработки нефелина на 1 т Al2O3 получают примерно 1 т карбонатов натрия и калия, а из нефелинового шлама – около 7,5–8 т цемента. Но это расходуется 4,3 т нефелинового концентрата и 7,5 известняка. Из вышеизложенного видно, что комплексная переработка нефелина является безотходным (малоотходным) производством. Основным недостатком этого способа является образование слишком большого количества цемента.
Сульфат и хлорид калия получаются в очень малых количествах. Они представляют собой мелкокристаллические порошки светло-коричневого цвета из-за содержания значительного количества соединений железа. Хлорид калия содержит солей калия (в пересчете на K2O) не менее 62 %, карбоната калия – не более 10 % в пересчете на K2O, Na2СO3 – не более 2,0 %. Сульфат калия содержит не менее 50,0 % K2O и не более 4,0 % Na2O.
108
4.ТЕХНОЛОГИЯ КАТАЛИЗАТОРОВ
ИАДСОРБЕНТОВ
Технологии катализаторов и адсорбентов выделены в отдельную группу по той причине, что они связаны с производством специфических материалов, применение которых основано на использовании особых свойств поверхности твердых тел.
4.1.Технология катализаторов
4.1.1.Значение катализа. Важнейшие каталитические процессы и катализаторы
Катализаторы играют важнейшую роль как в живой природе, так и в промышленном производстве. Явление катализа было открыто в конце XVIII в. Однако основные понятия этого явления начали формироваться лишь в первой половине XIX в. Сначала возник термин «контактные реакции» (Е. Митчерлих), затем в 1835 г. Д. Берцелиус предложил термин «катализ» для обозначения явления влияния веществ на скорость реакций, в которых эти вещества формально не принимают участия. Из твердых катализаторов первой нашла применение платина. В 1831 г. было обнаружено, что платина резко ускоряет реакцию взаимодействия диоксида серы с кислородом.
В настоящее время известно несколько тысяч веществ, которые могут служить катализаторами. Несколько сот катализаторов находят применение в промышленности.
К наиболее крупнотоннажным промышленным каталитическим процессам относятся каталитический крекинг и каталитический риформинг. Каталитический крекинг – это термокаталитическая переработка нефтяного сырья (керосин, газойль, мазут) с целью получения продуктов меньшей молекулярной массы – компонентов высокооктановых бензинов, легкого газойля, углеводородных газов С3–С4. Катализаторы каталитического крекинга главным образом цеолитсодержащие, микросферические (12–25 мас. % цеолита марки Y с редкоземельными элементами, 35–50 % Al2O3, размеры частиц 20–100 мкм). Условия крекинга: температура 450–520 °С, давле-
109

ние 0,4 МПа. С помощью каталитического крекинга перерабатывается 10–30 % нефтепродуктов.
Каталитический риформинг – это процесс каталитической переработки бензиновых фракций нефти под давлением водорода с целью получения высокооктановых автомобильных бензинов, ароматических углеводородов и водородсодержащего газа. Применяют
восновном алюмоплатиновые катализаторы (платина 0,5–0,65 %, галоген 0,7–0,75 %, нанесенные на оксид алюминия). Параметры процесса: температура 490–530 °С, давление 2–3,5 МПа.
Наиболее важными катализаторами в технологии неорганических веществ являются: ванадиевые катализаторы, использующиеся
впроцессе окисления диоксида серы; катализаторы на основе железа для синтеза аммиака; никелевые катализаторы для процессов паровой, паровоздушной и парокислородной конверсии углеводородов; железохромовый и цинк-медный оксидные катализаторы процесса паровой конверсии монооксида углерода и многие другие.
4.1.2. Основные понятия катализа
Катализом называют увеличение скорости химических реакций или возбуждение их под влиянием веществ – катализаторов, многократно вступающих в промежуточные химические взаимодействия с участниками реакции и восстанавливающих свой состав после каждого цикла промежуточных взаимодействий.
Ускоряющее действие катализаторов специфично: многие катализаторы проявляют активность по отношению к одной реакции или к узкой их группе.
Действие катализатора очень сильно отличается по эффективности и механизму от влияния других факторов (температуры, концентрации реагентов, перемешивания) на скорость химических реакций.
Скорость химического процесса определяется выражением
±V1 ddNτi = k ∆c ,
где V – реакционный объем, Ni – молярное количество вещества i, τ – время, k – константа скорости, ∆с – движущая сила процесса.
110