
Шестак Вакуумная техника. Концепция разреженного газа 2012
.pdf4.На основании чего можно частично пренебречь отдельными признаками, рассматриваемыми при проектировании, для снижения затратной составляющей проекта?
5.Чем отличаются схемотехническое решение вакуумной системы и ее принципиальная схема?
6.Почему при проектировании вакуумной системы резонно говорить о составлении «бизнесплана»?
7.Что такое компоновка вакуумной системы, какие возможности при ее рассмотрении можно использовать?
8.Почему при проектировании вакуумных систем в части выбора компонентов естественным представляется использование SWOT-анализа, применяемого в бизнесе?
9.Какой основной критерий используется при составлении рейтинга источников газовой нагрузки в вакуумных системах?
10.Почему изменяется рейтинг различных компонентов газовой нагрузки при различных стадиях откачки вакуумной системы?
11.Почему в практике вакуумной техники принято считать, что каждая течь в высоковакуумной
системе пропускает поток газа не менее 10−12 Вт?
12.Что такое «карта газовой нагрузки», и для чего она составляется?
13.В каких случаях достаточно иметь линейную карту газовой нагрузки, а в каких необходима объемная карта?
14.Для чего определяются суммарные пропускные способности элементов вакуумных систем при их расчете?
15.В каких случаях необходимо знание спектра масс остаточного газа в вакуумной системе?
16.Почему при расчете низковакуумной системы необходимо знать рекомендуемый объем откачиваемого сосуда?
17.Какое время происходит низковакуумная откачка правильно рассчитанной вакуумной сис-
темы?
18.Как определяется требуемая быстрота действия вспомогательного насоса для высоковакуумных насосов объемного действия?
19.Что достигается при перемещении насосов относительно их положения, определенного при первичной компоновке?
20.Почему размещение манометров может зависеть от «векторных» характеристик источников газовой нагрузки?
21.Изобразите примерный продольный профиль молекулярной концентрации в длинном трубопроводе, считая, что насос установлен на одном из его концов, периметр трубопровода не изменяется, а поток газовой нагрузки постоянен по длине.
22.Почему в вакуумной технике для расчета пропускных способностей элементов системы широко применяется метод численного статистического моделирования, иначе – метод Монте-Карло?
23.Что в вакуумной технике называется «индикатрисами»? Для каких целей можно использовать знание о них? Каким образом можно их измерить?
161

ГЛАВА 3. ТЕХНИКА И ТЕХНОЛОГИИ НИЗКОГО ВАКУУМА
Изучение этого модуля позволит вам:
освоить концепции получения низкого вакуума, реализованные в современных насосах;
провести позиционирование так называемых сухих насосов в процессах получения низкого вакуума;
освоить выбор насосов низкого вакуума под имеющуюся физическую задачу по разрежению газа с использованием их рабочих характеристик;
выбирать средства диагностики, адекватные процессам разрежения газа;
понять, в чем состоит проблема метрологического обеспечения вакуумных систем и в чем заключается ее специфика;
проводить выбор материалов и компонентов низковакуумных систем.
3.1. Насосы низкого вакуума
При получении низкого вакуума важнейшее значение для пользователя вакуумной техники имеют следующие вопросы:
•каков объем откачиваемой вакуумной системы?
•какова величина требуемого остаточного давления в вакуумной системе?
•за какое время можно получить требуемое остаточное давление?
Для ответа на эти вопросы нужен системный подход, который заложен в алгоритм проектирования вакуумной системы (см. рис. 2.3.1).
На рис. 3.1.1 изображена общая схема получения разрежения в вакуумной системе с помощью объемных вакуумных насосов, то есть насосов, которые извлекают молекулы из вакуумных систем и отправляют их в атмосферу240. Вакуумная часть (Вакуум) отделена от атмосферной части (Атм) рядом насосов или рядом ступеней откачки одного насоса, каждый (каждая) из которых обладает способностью реализовать распределение давления газа, подобное изображенному на рис. 2.1.2, обеспечить диффузионный захват свободных молекул в вакуумируемой части системы и не допустить излишне большого обратного потока молекул со стороны высокого давления.
Каждый насос (или ступень) откачки представляет собой «специальную зону», разделяющую вакуум и область с повышенным давлением и характеризующуюся коэффициентом компрессии кк = = рвып /рвп. Установленные друг за другом насосы образуют либо откачной агрегат, в котором все насосы, кроме первого, обращенного в вакуум, являются вспомогательными, либо многоступенчатый насос.
Рис. 3.1.1. Общая схема получения разрежения в вакуумной системе
Суммарный коэффициент компрессии241 kк∑ определяется как произведение коэффициентов компрессии отдельных насосов или ступеней откачки: kк∑= ∏ кi , где i – число насосов или ступеней откачки.
240Как следует из рис. 1.2.4, вопрос уменьшения количества свободных молекул в вакуумной системе может быть решен за счет сорбционной откачки – либо путем «вымораживания молекул» при криогенных темпе-
ратурах (менее 77 К), либо за счет их абсорбционного связывания на сильно развитых поверхностях, в первую очередь, на цеолитах.
241Рекордным является значение kк = 109 по азоту, достигнутое в современных турбомолекулярных насо-
сах.
162

Выбор насоса определяется родом и количеством откачиваемых насосом газов, а также диапазоном рабочих давлений. Рабочей характеристикой насоса называется зависимость быстроты откачки насоса Sнас от величины рабочего или впускного давления ркам.
Типовые рабочие характеристики вакуумных насосов приведены на рис. 3.1.2. Они же могут рассматриваться как рабочие характеристики отдельных ступеней. В этом случае давления, указанные на оси абсцисс слева, определяются соответственно величине предельного давления данной ступени (например, для низковакуумного многоступенчатого насоса вместо 10−7 следует записать 1 или
10 Па).
Рис. 3.1.2. Типовые рабочие характеристики вакуумных насосов
(аппроксимация соответствует «правилу крокодила», см. раздел 2.2)
Спад характеристик при разных давлениях для каждого насоса обусловлен разными причинами: спад быстроты откачки слева на характеристике – удельным ростом паразитных потоков и достижением предельного давления для данного насоса, спад справа – физическими принципами работы насосов – насос просто перестает работать!
Типичная кривая откачки вакуумной системы для насосов низкого вакуума изображена на рис. 3.1.3.
Рис. 3.1.3. Типичная кривая откачки для насосов низкого вакуума
Наклон прямой 1 соответствует величине постоянной времени откачки τ = V/S, где V – объем системы; S – быстрота откачки. Величина получаемого соответствует р∞1 паспортным данным насоса по предельному остаточному давлению с учетом пропускной способности тракта откачки.
Кривая 2 соответствует режиму откачки при подаче балластного газа или при наличии грубой течи в вакуумной системе (напомним, что р∞ = Σ , где р∞ – предельное остаточное давление, полу-
чаемое при откачке; Σ |
суммарная газовая нагрузка вакуумной системы; |
скорость ее откачки |
Получаемое предельное |
–остаточное давление в этом режиме откачки р∞2 существенно выше давле-. |
ния р∞1.
163

Цель демонстрации приведенных на рис. 3.1.3 кривых откачки состоит в том, чтобы показать, что время откачки в правильно спроектированной и правильно собранной вакуумной системе до разрежений, соответствующих низкому вакууму, очень мало и не превышает десятка минут.
На рис. 3.1.4242 рассмотрена морфология принципов низковакуумной откачки, для которой не-
обходим действующий насос, удаляющий тем или иным способом молекулы из вакуумной системы вопреки огромному «желанию» молекул атмосферного воздуха «прорваться» за счет градиента давлений243 в систему.
Рис. 3.1.4. Морфология принципов (механизмов) низковакуумной откачки
Варианты механизмов откачки, определяющих тип вакуумного насоса, разнесены по четырем группам:
первую группу составляет самый простой и традиционный для вакуумной техники компрессион- но-поршневой клапанный (см. рис. 3.1.4, а) механизм откачки, в котором величина предельного дав-
ления не зависит от величины обратного потока Qобр, а определяетсяпаразитным потоком Qпаразит изза несовершенства конструкции, а также давлением паров используемого масла;
вторая группа (см. рис. 3.1.4, б), использующая «механизм откачки по Аристотелю», очень интересна, так как в ней собраны насосы, не имеющие выпускного клапана и не использующие компрессию. В этих насосах допускается существование обратного потока газа со стороны выпуска,
правда, с условием, что Qотк >> Qобр;
в третьей группе (см. рис. 3.1.4, в) представлены самые современные разработки, к которым отнесен шнековый механизм откачки, не только сохраняющий все достоинства второй группы, но и дополнительно обеспечивающий непрерывную откачку;
242Восприятие состава и содержания окружающего мира, его первичная идентификация, а значит, и достаточно яркие, надолго запоминающиеся впечатления, как правило, определяются внешним видом наблюдаемого объекта или субъекта. Именно это первое образное впечатление, во многом влияющее на последующее отношение к изучаемому, становится исходным началом организации любого исследования, получившим название
морфология.
243Следует помнить, что на практике всегда ратм >> ркам.
164

четвертая группа (см. рис. 3.1.4,г) – насосы, использующие сорбционный механизм откачки, основным достоинством которого является отсутствие связи с окружающим вакуумную систему атмосферным воздухом.
Низковакуумные насосы в XVII – XIX вв. работали с применением воды или ртути, и, следовательно, в вакуумных камерах были пары воды или ртути; в XX в. стали использовать масло, и в вакуумных камерах появились его пары – углеводороды, летящие из насоса в вакуумные системы и загрязняющие их.
XXI в. потребовал простых и прагматичных решений по обеспечению вакуума, в котором отсутствуют углеводороды. Были изобретены насосы, обеспечивающие вакуум без углеводородов244, которые называются сухими (группы насосов б, в и г). Сухие насосы обеспечивают вакуум без паров мас-
ла (dry vacuum pump: oil free vacuum pump or oil free vacuum).
Справедливости ради следует заметить, что подобные насосы, а точнее сказать, воздуходувки Рутса, были изобретены братьями Фрэнсисом и Филандером Рутс еще в 1859 г. для сжатия и подачи воздуха и других газов. Конструктивная простота сделала эти устройства основой целого ряда нагнетателей воздуха, получивших название роторные воздуходувки.
На современном рынке низковакуумных насосов (форвакуумных) можно приобрести следующие варианты:
•пластинчато-роторные вакуумные насосы с рециркуляционной смазкой или, как они назывались в недавнем прошлом, механические вакуумные насосы с масляным уплотнением (ММН);
•пластинчато-роторные сухие вакуумные насосы;
•двухроторные вакуумные насосы;
•кулачковые (когтевые) вакуумные насосы;
•спиральные вакуумные насосы;
•мембранные вакуумные насосы;
•поршневые вакуумные насосы.
По сути, воплощение основных концепций теории разреженного газа в конкретных устройствах (в нашем случае в насосах) является верификацией этих концепций и подтверждает их научность.
Верификация (от лат. verus – истинный, facere – делать) – это подтверждение соответствия конечного продукта предопределённым эталонным требованиям
Несмотря на явный технологический прогресс по разработке новых бесконтактных сухих насосов, во всем мире продолжается использование и классических ММН, для чего применяются различные фильтры, ловушки масляных паров, новые сорта масел и т.п. Полный переход на сухие средства откачки сдерживает, как правило, только их более высокая стоимость.
3.1.1. Механические масляные насосы
Исторически в течение 100 лет существования вакуумной техники главным средством получения низкого вакуума являлись механические вакуумные насосы с масляным уплотнением – механические масляные насосы (ММН). ММН относятся к первой группе (см. рис. 3.1.4, а). ММН используют для работы в области давлений от 105 до 1 Па, они входят в состав практически всех вакуумных систем. По принципу действия ММН относятся к насосам объемного типа. ММН – вращательные насо-
сы дискретного принципа действия.
Предложено большое количество различных конструкций подобных насосов. Схема пластинча- то-роторного механического насоса с масляным уплотнением приведена на рис. 3.1.5. Через впускной патрубок 1 газ поступает в рабочую камеру, которая полностью (уровень масла 2) погружена в резер-
244 В масс-спектре сухого вакуума не должно быть газов с массовыми числами более 44.
165

вуар с маслом. При вращении ротора 3 в статоре 4 заполнившая рабочий объем насоса порция газа 5 в определенный момент времени отсекается от вакуумной системы пластиной 6 (выдвигаются из ротора пружиной две пластины). Далее используется «механизм Аристотеля», где роль камня выполняет пластина справа, отсеченная порция газа переносится на сторону выпуска, одновременно сжимаясь второй пластиной (слева) до величины атмосферного давления, после чего сжатая порция газа 7 выбрасывается в атмосферу через выпускной клапан 8 (на рис. 3.1.5 – шарик).
|
Величина предельного давления, |
|
|
обеспечиваемого ММН, определяет- |
|
|
ся паразитными потоками откачи- |
|
|
ваемого газа в точках соприкоснове- |
|
|
ния вращающихся и трущихся частей |
|
|
этих насосов (на рис. 3.1.5 показаны |
|
|
тремя треугольниками). Для сведе- |
|
|
ния этих потоков к минимуму ис- |
|
|
пользуется масло из резервуара, ко- |
|
|
торое, попадая в ничтожном количе- |
|
Рис. 3.1.5. Схема устройства пластинчато-роторного |
стве внутрь насоса, уплотняет |
|
механического насоса с масляным уплотнением (а) |
имеющиеся зазоры, заполняет так |
|
и его условное обозначение (б): |
называемые вредные пространства, |
|
1 – впускной патрубок; 2 – уровень масла; 3 – ротор; 4 – статор; |
обеспечивает смазку и частичное ох- |
|
5 – отсеченная порция газа; 6 – рабочие пластины; |
лаждение механизма насоса. |
|
7 – сжимаемый газ; 8 – шарик на выпускном патрубке |
||
Уровень масла, заливаемого в |
||
|
||
|
бак насоса, имеет прямое отношение |
к достигаемому предельному давлению, так как масло должно покрывать выпускной клапан, чтобы предотвратить попадание атмосферного воздуха в рабочий объем насоса при выбросе из насоса сжатого газа. ММН обеспечивают остаточное давление менее 1 Па (без газобалласта). Шумность насоса на уровне 60 дБ определяется не только вращением массивного ротора, но и пробулькиванием сжатого газа через масло (см. подробнее в кн.: Глазков А.А., Милованова Р.А. Учебная лаборатория вакуумной техники: Учебное пособие для вузов. М.: Атомиздат, 1971, с. 174 – 178).
Как вы помните, для откачки конденсирующихся газов и паров Вольфгангом Геде в 1935 г. была изобретена так называемая газобалластная откачка, смысл которой сводится к тому, что суммарное давление в выпускной камере насоса над клапаном складывается из давления конденсирующегося пара рпар и давления воздуха (сухого азота) рбг, впущенного через специальный дополнительный регулируемый клапан: рΣ = рбг + рпар.
Если суммарное давление рΣ увеличивается до уровня рвып, когда парциальное давление пара рпар еще не достигает критической величины конденсации пара ркрит, то мы сможем откачать некоторую часть конденсирующегося пара. Естественно, что при этом достигаемая величина р∞ ухудшается почти на порядок, что и показано на рис. 3.1.3.
Схема ММН, работающего с газобалластом, изображена на рис. 3.1.6. Насос подключают к вакуумной камере, в которой есть влага (пары воды). В камеру сжатия насоса через натекатель V добавляется балластный газ «бг». Суммарное давление газа, пара и балластного газа станет достаточным для открытия выпускного клапана, начнется выпуск сжатого газа, вплоть до полного очищения вакуумной системы от
паров воды. Процесс этот длительный, поскольку мы сознательно снижаем долю откачиваемого газа в выбрасываемой порции.
Источники паразитного потока для вакуумных систем, откачиваемых ММН: пары испаряющегося масла; газ, растворенный в масле; газ, находящийся во «вредных пространствах» (к которым относятся объемы под выпускным клапаном и между клапаном и отсекающей пластиной) и возвращающийся на впускную сторону.
Следует сказать, что основным компонентом паразитного потока является сжимаемый в выпускной части насоса газ, часть которого неизбежно из-за геометрических требований размещения выпу-
166

скного патрубка и вращения ротора в статоре попадает на впускную сторону. Для того чтобы уменьшить величину этого потока, а значит, снизить величину получаемого предельного давления, разработаны конструкции двухступенчатых насосов245. Объем первой ступени V1 делается больше, чем объем второй ступени V2 для обеспечения условия неразрывности потока:
V1 p1 = V2 p2 , |
(3.1.1) |
где p1 и p2 − давления в первой и второй ступенях соответственно.
Такая конструкция ММН дает возможность уменьшить величину получаемого предельного давления на 1,5 – 2,0 порядка по сравнению с одноступенчатым ММН.
ММН, как и любой механизм, обладает конечным коэффициентом полезного действия246. Для насосов потери энергии на трение и выделение тепла при сжатии газа приводят к нежелательному разогреву. При геометрическом увеличении размеров насосов возникает проблема теплосъема, так как теплосъем растет всего лишь как квадрат линейных размеров, а выделение тепла как куб линейных размеров. Следовательно, наступает момент, когда необходимо вводить принудительное охлаждение. Для ММН эта необходимость возникает при быстроте откачки более 100 м3 · ч−1 (30 л · с–1). Заметим, что в подавляющем большинстве случаев применения ММН в электрофизике достаточно быстроты откачки низковакуумных насосов в диапазоне от 1 до 5 л · с–1.
3.1.2. Пластинчато-роторные сухие вакуумные насосы
Эти насосы, устроенные точно так же, как ММН (подобная конструкция называется «насос Геде») относятся к первой группе (см. рис. 3.1.4,а), работают полностью без масла благодаря самосмазывающимся пластинам, изготовленным из специального углеродного материала. Такие насосы идеальны для использования в технологических процессах, где недопустимо применение масла.
Они обеспечивают остаточное давление менее 50 Па, при быстроте действия в диапазоне от 1 до
200 л · c–1.
3.1.3.Мембранные насосы
Вмембранных вакуумных насосах перемещение газа происходит за счет изменения объема рабочей камеры в результате деформации упругой мембраны. Вследствие конструктивных особенностей этого вида насосов (мембраны больших размеров трудны в изготовлении и неизбежно ведут к неоправданному увеличению габаритных размеров машины), широкое применение имеют насосы малой производительности, очень малошумные и, как правило, обладающие высокой коррозионной стойкостью. Мембрана легко заменяется в процессе эксплуатации. Мембранные «сухие» насосы относятся к первой группе (см. рис. 3.1.4, а) и предназначены для «чистых» и технологических лабораторных применений, где необходимо достигать вакуум уровня не лучше 100 Па при невысокой про-
изводительности.
Мембрана из эластомера247 (см. рис. 3.1.7) перемещается вверх и вниз при вращении эксцентрика. При движении мембраны вниз всасывается газ через входной клапан (справа). При движении мембраны вверх газ сжимается а потом через выхлопной клапан (слева) газ выбрасывается за пределы головки насоса. Компрессионная камера герметично изолирована от приводного механизма посредством мембраны. Таким образом, мембранный насос перемещает, откачивает и сжимает перекачиваемую среду без использования масла и, следовательно, является «сухим».
245Идея многоступенчатости используется практически во всех объемных вакуумных насосах, так как позволяет увеличить общий коэффициент компрессии.
246В каждом механизме значительная часть мощности уходит не на полезную работу, которая для насоса состоит в количестве удаляемых молекул, а на преодоление внутреннего сопротивления (трение, перенос пленок масла и пр.). Таким образом, полезная мощность механизма всегда меньше его полной мощности, что и отражается коэффициентом полезного действия.
247Резиной или эластомером называют любой упругий материал, который может растягиваться до размеров, во много раз превышающих начальные, и, что существенно, возвращаться к исходному размеру, когда нагрузка снята.
167
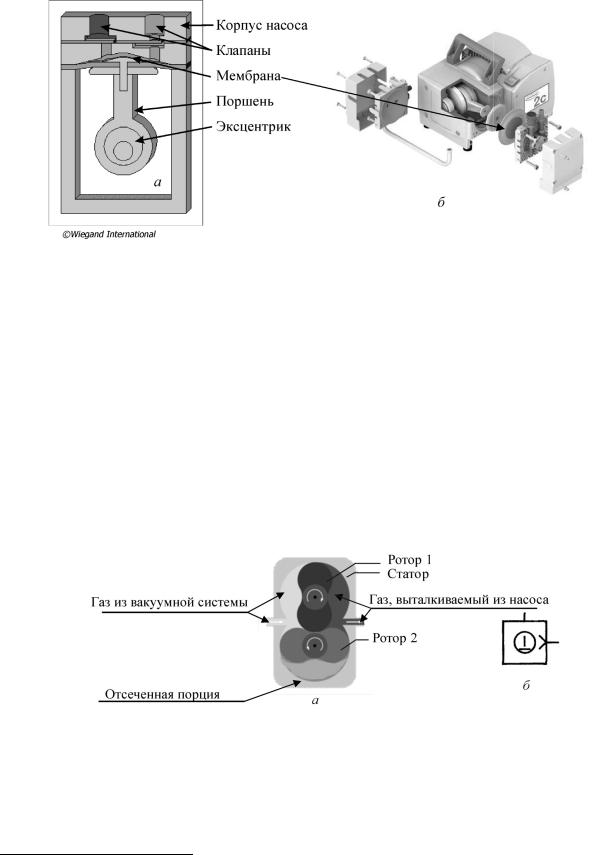
Рис. 3.1.7. Схема устройства (а) и конструкция (б) мембранного насоса
3.1.4. Двухроторные вакуумные насосы
Использование второй ступени в ММН позволяет получить выигрыш в величине предельного давления почти на порядок. Естественно возникает вопрос: не добавить ли еще третью, четвертую и т.д. ступени? Оказывается, что такое решение не приводит к уменьшению величины предельного давления, так как все последующие ступени также являются ступенями с масляным уплотнением. Ограничение в получаемой величине предельного давления связаны, во-первых, с невозможностью полного обезгаживания масла и, во-вторых, с конечной величиной давления паров масла. Следовательно, третья ступень должна работать без использования масла, обладать высокой скоростью откачки при относительно малом перепаде впускного и выпускного давлений. Коэффициент компрессии этой ступени не должен превышать 102, в этом случае, возможно получить минимальные обратные потоки откачиваемого газа. Именно такими свойствами и обладают двухроторные вакуумные насосы (ДВН). ДВН относятся ко второй группе (см. рис. 3.1.4, б).
ДВН, называемые за рубежом насосами Рутса, предназначены для работы в области давлений от 102 до 10–1 Па, где они наиболее экономичны по сравнению с другими типами насосов.
Рис. 3.1.8. Схема устройства ДВН (а) и его условное изображение (б)
На рис. 3.1.8 приведена схема, поясняющая устройство и принцип действия ДВН. В рабочей камере насоса два ротора, имеющие сечения, по форме похожие на цифру 8, вращаются навстречу друг другу в овальном статоре. Роторы синхронизированы и контуры их таковы248, что при вращении обеспечивается минимальный зазор между ними и между роторами и стенками статора. Зазоры не превышают (75 – 100) · 10–6 м, что и определяет малую пропускную способность для обратного потока газа.
248 Говорят о том, что профиль ротора – лемнискатный. Лемниската по форме напоминает восьмерку или символ бесконечности. Её название происходит от греч. λημνισχος – лента, повязка. В Древней Греции «лемнискатой» называли бантик, с помощью которого прикрепляли венок к голове победителя на спортивных играх. Швейцарский математик Якоб Бернулли в 1694 г. положил начало изучению лемнискатных кривых. В частности, лемниската Бернулли – плоская кривая, геометрическое место точек, произведение расстояний от которых до двух заданных точек (фокусов) постоянно и равно квадрату половины расстояния между фокусами.
168

Отсеченный от стороны всасывания газ при вращении роторов перемещается ими без сжатия на сторону выпуска, где он при дальнейшем вращении роторов выталкивается из насоса. При этом создается поток откачки Qотк.
Как и ММН, ДВН являются вращательными насосами дискретного типа, реализующими для откачки «механизм Аристотеля». ММН используется в качестве вспомогательного насоса для работы ДВН. Вместе они образуют вакуумный откачной агрегат (см. рис. 3.1.1).
Комбинация ДВН с ММН работает в оптимальных условиях при выполнении следующего равенства:
Sммн = (0,2 ÷ 0,1) Sдвн, |
(3.1.2) |
где Sммн и Sдвн – скорости откачки ММН и ДВН соответственно.
Основными достоинствами ДВН являются: отсутствие масла, так нет трения и необходимости в смазке; простота устройства; малая чувствительность к пыли, грязи, колебаниям величины потока откачки; устойчивость к прорывам атмосферного воздуха.
Наличие рабочих зазоров в ДВН приводит к тому, что величина впускного давления рвп всегда
является функцией величины выпускного давления рвып: |
|
рвп = F (рвып), |
(3.1.3) |
так как часть откачиваемого газа всегда образует обратный поток.
Быстрота откачки насоса зависит в первую очередь от его геометрических размеров. Известны насосы с быстротой откачки от 18 до 90 000 м3 · ч–1 (от 5 до 25 000 л · с–1). Как и в случае ММН,
принцип действия ДВН позволяет строить многоступенчатые насосы в одном корпусе, что также дает выигрыш в величине получаемого предельного давления р∞ на один порядок за счет снижения величины обратного потока.
Рис. 3.1.9. Рабочая характеристика ДВН:
1 – рабочая характеристика вспомогательного ММН, 2 – рабочая характеристика ДВН без байпасной линии предварительного разрежения, 3 – рабочая характеристика ДВН с байпасной линией предварительного разрежения, 4 – область характеристики, формируемая при использовании байпасной линии
«Проталкивания» отсеченных порций газа повторяются четыре раза за один оборот, вызывая частые колебания величины выпускного давления рвып (частота больше 200 Гц) и колебания величины потока откачки. Такой не очень эффективный способ откачки приводит к интенсивному разогреву роторов и, как следствие, к расширению деталей насоса, что очень опасно, так как для реализации принципа работы ДВН зазоры между торцами роторов и крышками статоров, между роторами и статором должны быть минимальными. Их размеры определяют величину обратного потока молекул и, следовательно, достигаемое предельное давление. Для ДВН существует понятие «безопасная длительность работы» с точки зрения разогрева роторов. Этот параметр для ДВН определяет, в частности, правую границу рабочей характеристики.
Производство ДВН, несомненно, относится к высокотехнологичным, и оно по силам не каждой компании.
Консолидированная зависимость быстроты откачки от величины впускного давления для современных ДВН, в которых с помощью байпасной линии (pressure equalization line) ММН автоматически переключается из режима работы в качестве основного, осуществляющего откачку основной массы газа в диапазоне давлений от 104 до 105 Па, в режим работы в качестве вспомогательного для ДВН, приведена на рис. 3.1.9, (2) и (3). Поскольку величина рвп является почти линейной функцией
169
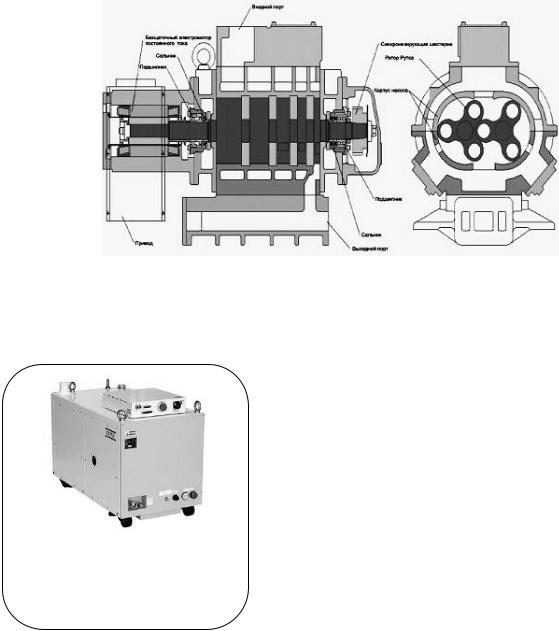
рвып, то вид и положение кривой на рис. 3.1.9 сильно зависят от выбора насоса предварительного разрежения. При уменьшении впускного давления от атмосферного до р∞двн быстрота откачки вначале плавно растет, что связано с переходом режима течения газа из вязкостного в промежуточный, а затем в молекулярный. При этом за счет уменьшения суммарной проводимости зазоров падает величина обратного потока и коэффициент компрессии достигает своего максимума. После достижения максимального значения Sдвн начинает уменьшаться за счет увеличения разности давлений на впускной и выпускной сторонах насоса.
Быстрота откачки легких газов с помощью ДВН всегда меньше, чем тяжелых. Это объясняется большей проникающей способностью легких газов через те же зазоры в насосе и, следовательно, большими величинами обратных потоков. Например, быстрота откачки водорода в максимуме на 10 % меньше быстроты откачки азота.
Остаточные газы в системе после ее откачки с помощью ДВН состоят в основном из окиси углерода, паров воды и паров углеводородов. Последний компонент возникает из-за использования ММН в качестве предварительного, а также из-за частичного просачивания паров подшипникового масла на впускную сторону.
Насосы используются в качестве форвакуумных при работе с высоковакуумными объемными насосами и широко применяются для самостоятельной откачки воздуха или неактивных газов и паров.
Рис. 3.1.10. Схема современного двухроторного пятиступенчатого насоса Рутса большой производительности (©Kashiyama, Япония)
На рис. 3.1.10 представлена схема современного двухроторного пятиступенчатого насоса Рутса
большой производительности, выпускаемого японской компанией Kahiyama, роторы которого имеют трехлопастную конструкцию.
Так выглядит современный «сухой» насос Рутса в комбинации с «сухим» низковакуумным насосом. Диапазон рабочих давлений
0,5 – 105 Па
Быстрота действия современных насосов Рутса находится в пределах от 0,3 до 28000 л · с–1. Роторы имеют дветри лопасти, как правило, прямозубые. Зазор между роторами и корпусом не превышает 0,0015 – 0,0025 наружного радиуса ротора; между роторами и торцовыми крышками зазор выполняется приблизительно в 1,5 раза больше.
Компании Kashiyama принадлежит около 20 % мирового рынка промышленных безмасляных вакуумных насосов, а в технологических производствах таких стран, как Япония и Китай, доля насосов этой компании превышает 50 %. Многоступенчатые насосы Рутса и винтовые насосы отвечают всем требованиям современных производств и технологий по созданию чистого вакуума.
Основными достоинствами ДВН являются исключительная надежность, в том числе в самых «тяжелых» приложениях при откачке агрессивных газов, высокая степень
170