
Роторные дробилки. Конструкции и расчеты. Шарипов Л.Х
.pdfМинистерство образования и науки Российской Федерации
Федеральное государственное бюджетное образовательное учреждение высшего образования
«Воронежский государственный технический университет»
Л.Х. Шарипов
РОТОРНЫЕ ДРОБИЛКИ. КОНСТРУКЦИИ И РАСЧЕТЫ
Учебное пособие
для студентов специальности 23.05.01 «Наземные транспортнотехнологические средства», направления подготовки 23.03.02 «Наземные транспортно-технологические комплексы»
Воронеж 2017
УДК 621.879.3(072) ББК 33.4я37
Ш259
Шарипов, Л.Х.
Роторные дробилки. Конструкции и расчеты : учебное пособие для стуШ259 дентов специальности 23.05.01 «Наземные транспортно-технологичес-
кие средства», направления подготовки 23.03.02 «Наземные транс - портно-технологические комплексы» / Л.Х. Шарипов. – Воронеж : ВГТУ, 2017. - 82 с.
Рассматриваются конструкции роторных дробилок, приведена методика расчёта технологических и конструктивных параметров и другие сведения, необходимые для выполнения курсовых и дипломных проектов.
Учебное пособие составлено в соответствии с Федеральным государственным образовательным стандартом высшего образования по дисциплине «Строительные машины и оборудование».
Ил. 37. Табл. 5. Библиогр.: 4 назв.
УДК 621.879.3(072) ББК 33.4я37
Рецензенты:
кафедра промышленного транспорта, строительства и геодезии ВГЛТУ им. Г.Ф. Морозова (зав. каф., д.т.н., профессор С.И. Сушков); В.В. Кандалинцев, директор Воронежского филиала АП ЦНИИОМТП
Печатается по решению учебно-методического совета ВГТУ
© Шарипов Л.Х., 2017 © ФГБОУ ВО «Воронежский
государственный технический университет», 2017
ВВЕДЕНИЕ
Дробление гонных пород является основным технологическим процессом при производстве нерудных строительных материалов, которые используюутся в огромных количествах в различных отраслях строительства.
Техника дробления и обогащения материалов требует решения таких задач, как повышение производительности дробилок, сокращение числа стадий переработки, повышение качества и увеличение выхода требуемых фракций в готовом продукте дробления, снижение удельной энергоёмкости и др.
Щековые, конусные и волковые дробилки, работающие по принципу раздавливания, во многих случаях не могут в полной мере удовлетворить современные требования.
Роторные дробилки, реализующие принцип ударного разрушения, давая более высокие производительность и степень измельчения при улучшенном качестве продукта, меньшей металлоемкости , удельном расходе энергии и других положительных показателях позволяют более эффективно решать поставленные задачи в области дробильно-обогательной техники.
Благодаря малой металлоёмкости роторные дробилки широко используются на передвижных дробильно-сортировочных установках, так как они наиболее экономичны. Они используются на различных стадиях дробления в качестве основных машин, принимающих куски до 2 м3, также используются на последующих стадиях дробления до получения продукта содержащего около 90% зерен класса - 2 мм.
В различных областях использования роторных дробилок предъявляются специальные требования для данного производства: минимальное содержание мелких фракций, наибольшая степень уменьшения при отсутствии кусков, превышающих данный размер; ограничение выхода лещадных и иглообразных зерён; максимальная разница в степени уменьшения двух компонентов дробящихся совместно; минимальный скос рабочих органов. Выполнение этих требований часто является решающим фактором при выборе конструкций и режима роторных дробилок. Определение основных параметров роторных дробилок с учетом выполнения слоев различных требований представляет особые трудности, обусловленные значительным разнообразием и непостоянством свойств дробимого материала, недостаточной их измельченностью, а так же сложность характера разрушения и движения материала при ударе, что требует знания теоретичесикх основ этих процессов. Поэтому учебное пособие предназначенное для студентов, изучающих машины для измельчения нерудных строительных материалов в рамках дисциплины «Строительные машины и оборудование», будет полезным, так как в нём изложены материалы, позволяющие понять физическую сущность явлений, происходящих в роторных дробилках, и оценить точность применяемых формул, практическое изложение которых использовано в примере расчёта.
3
1. ОБЩИЕ СВЕДЕНИЯ
Роторные дробилки применяют для дробления осадочных и изверженных горных пород в промышленности нерудных строительных материалов при производстве щебня, в цементной и известковой промышленности для измельчения клинкера и сырьевых материалов. В угольной промышленности роторные дробилки широко используются для измельчения вскрышных пород в открытых карьерах. В мировой практике они применяются в рудной промышленности для дробления железных, марганцовистых, свинцовых, оловянных, медных, сурьмяных, а также бокситовых, серных, фосфорных руд и ангидрида.
Вследствие малой металлоемкости роторных дробилок они успешно применяются на передвижных дробильно-сортировочных установках. Роторные дробилки, как экономичные машины, устанавливаются на различных стадиях дробления – на первой, промежуточной и последней, на которой может быть получен продукт, содержащий 90% зерен класса 2 мм.
Решающим фактором при выборе роторных дробилок является выполнение следующих требований: максимальная степень измельчения при минимальном содержании переизмельченного материала и отсутствии кусков, превышающих заданный размер; ограничение выхода лещадных и иглообразных зерен; минимальный износ рабочих органов.
Для роторных дробилок характерно конструктивное разнообразие, которое объясняется отсутствием удовлетворительной методики расчета основных параметров – производительности, качества продукта дробления, расчета расходуемой энергии, ударных нагрузок, сроков службы рабочих органов и др. – с учетом выполнения указанных требований. Трудности расчета обусловлены значительным разнообразием и непостоянством свойств дробимого материала, недостаточной их изученностью, а также сложностью характера разрушения и движения материала при ударе.
Роторные дробилки – сравнительно новый вид оборудования. Первый патент на роторную дробилку был выдан в США в 1842 г. на шестнадцать лет раньше, чем на щековую. Промышленное производство роторных дробилок начато в 1939 г. в США, но только с 1946 г. они получили широкое распространение благодаря работам фирмы Хацемаг (ФРГ), которая за короткий срок выпустила несколько тысяч дробилок, продав лицензии на их производство многим странам. В нашей стране роторные дробилки стали выпускаться с 1956 г.
2. КЛАССИФИКАЦИЯ РОТОРНЫХ ДРОБИЛОК
Роторные дробилки классифицируют по технологическому назначению и конструктивному исполнению. К технологическим признакам, определяющим тип дробилки, относятся: крупность исходного продукта(Dmax) и его физикомеханические свойства и требования, предъявляемые к готовому продукту.
4
По крупности исходного продукта дробилки разделяются на три класса:
–крупного дробления (ДРК) с размером исходного материала (Dmax) более 0,3 диаметра ротора (Dр);
–среднего дробления (ДРС) с Dmax = (0,1 ÷ 0,3) Dр;
–мелкого дробления с Dmax < 0,1Dр (их также обозначают ДРС).
Дробилки крупного дробления предназначены главным образом для работы на первой стадии дробления, дробилки среднего и мелкого дробления для работы на последующих стадиях дробления.
По свойствам исходного материала и требованиям к качеству получаемого продукта различают машины для дробления: пород малой и средней абразивности (известняков, доломитов, сланцев, мрамора песчаника и других материалов, но не более 7-й категории абразивности), высокопрочных и абразивных пород (гранитов, базальтов, диабазов, диоритов, кварца, кварцитов и других материалов более 7-й категории абразивности); с одновременной промывкой от пылевидных частиц и глинистых загрязнений; с одновременной подсушкой горячими газами, пропускаемыми через дробилку; с ограниченным выходом зерен максимальной крупности в готовый продукт.
По конструктивным признакам роторные дробилки классифицируются:
–по числу роторов: – однороторные, представляющие многочисленный класс и наиболее широко распространенные, многороторные – двухроторные и трехроторные;
–по способу разгрузки готового продукта: со свободной разгрузкой, с разгрузкой через контрольную колосниковую решетку, которая охватывает всю нижнюю полуокружность ротора полностью, комбинированные, т.е. с разгрузкой через контрольную колосниковую решетку, которая охватывает часть нижней полуокружности ротора;
–по характеру исполнения отражательных органов: с отражательными плитами; – с отражательными колосниковыми решетками, с комбинированными отражательными органами (с плитами и колосниковыми решетками). По числу камер дробления: однокамерные, многокамерные (двух-, трех-, и т.д. камерные);
–по способу подвески отражательных плит: с жесткой подвеской, с шарнирной подвеской, с комбинированной подвеской (обычно первые отражатель-
ные плиты имеют жесткую подвеску, последующие − шарнирную);
–по реверсированию вращения ротора: реверсивные, нереверсивные;
–по форме линии профиля отражательной плиты: с криволинейными поверхностями, с поверхностями, выполненными по ломаной линии.
Многороторные дробилки разделяются по числу ступеней дробления:
–одноступенчатые, в которых поток материала поступает одновременно на все роторы;
–многоступенчатые, в которых поток дробимого материала поступает последовательно от одного ротора к другому или от одной группы роторов к другой (двух-, трехступенчатые и т.д.).
5
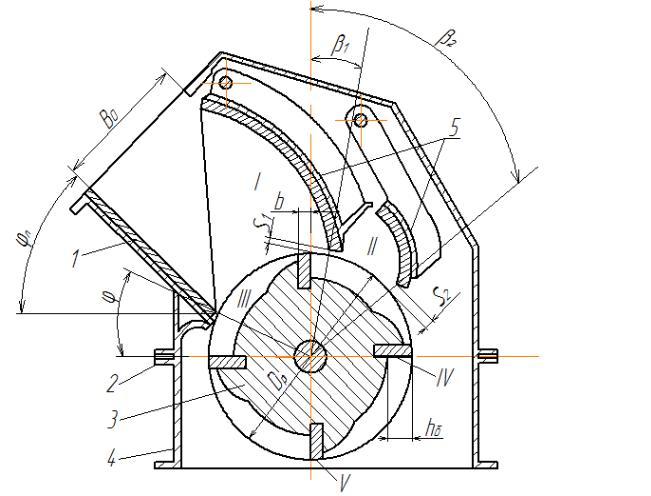
–по наличию торцовый дисков: с торцовыми дисками и обычные (без торцовых дисков);
–по способу защиты внешней поверхности от износа: открытые - незащищённые, с износостойком наплавкой и со сменной футеровкой.
Дробилки с колосниковыми решетками по расположению колосников различают с вертикальными и горизонтальными колосниками.
На рис. 2.1 представлена типовая схема роторной дробилки с указанием основных геометрических параметров и взаимным расположением рабочих органов,
ана рис. 2.2 − основные конструктивные схемы.
Рис. 2.1. Типовая схема роторной дробилки:
1 – приемный лоток; 2 – корпус дробилки; 3 – ротор; 4 – станина; 5 – отражательная плита (отражательная колосниковая решетка); I,II – камеры дробления; III – рабочая зона ротора; IV – рабочая поверхность; V – внешняя поверхность била; φ – угол установки приемного лотка; φл – угол наклона приемного лотка; В0 – поперечный размер приемного отверстия; S1, S2 – ширина наклонной щели; β1, β 2 – углы установки отражательной плиты (колосниковой решетки); b – ширина внешней поверхности била; Dp – диаметр ротора; hб – рабочая высота била
6
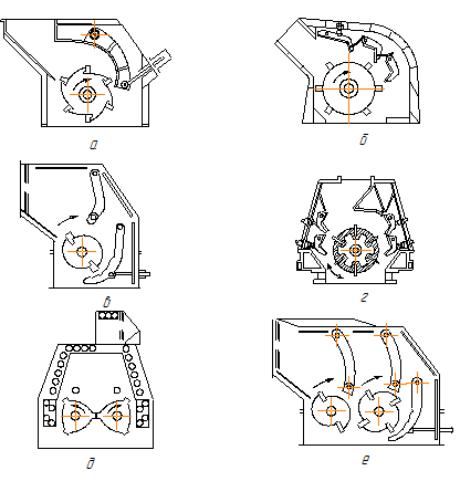
Рис. 2.2. Конструктивные схемы роторных дробилок:
а– однороторная однокамерная с отражательной плитой; б – однороторная трехкамерная
сотражательными плитами; в – однороторная двухкамерная с колосниковыми решетками;
г– реверсивная; д – двухроторная одноступенчатого дробления; е – двухроторная
двухступенчатого дробления
3.КОНСТРУКЦИИ И РАБОТА РОТОРНЫХ ДРОБИЛОК
3.1.Конструктивные особенности главных узлов роторных дробилок
Основными узлами дробилки являются ротор, корпус дробилки, отражательные устройства (плиты, колосниковые решетки) и привод.
Ротор дробилки (рис. 3.1) представляет собой вращающийся рабочий орган, включающий била с деталями, их крепления, корпус с валом и является основным и наиболее ответственным узлом, служащим для нанесения удара по дробимому материалу. Диаметр и длина ротора являются основными параметрами.
Диаметр роторов на промышленных образцах бывает 400 − 2000 мм, а длина роторов 400 − 2500 мм.
7
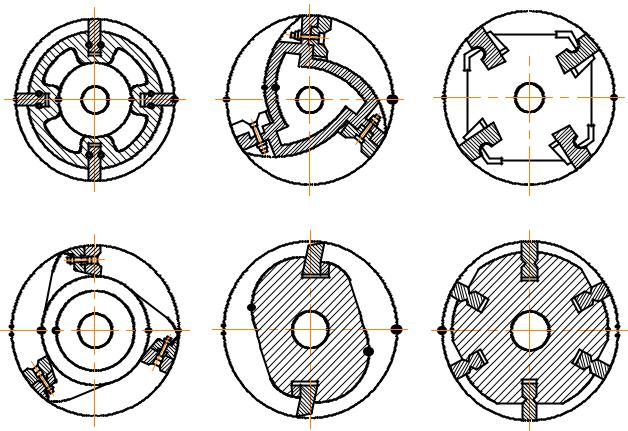
Соотношение длины ротора и его диаметра колеблется от 0.5 до 2.0, чаще это соотношение бывает в пределах 0.8 − 1.0. Масса ротора крупных дробилок достигает 25 т.
а |
б |
в |
г |
д |
е |
Рис. 3.1. Конструкции корпусов роторов:
а– закрытый с очертанием внешней поверхности по окружности; б – закрытый с очертанием внешней поверхности по спирали; в – корпус из дисков с внешней поверхностью в виде многогранника; г – закрытый с очертанием внешней поверхности по окружности
свыступами; д – закрытый монолитный овальный корпус; е – закрытый монолитный цилиндрический корпус со срезанными предбильными частями
Эффективная конструкция ротора является главным условием надежности работы всей дробилки, поэтому интенсивный поиск рациональных конструкций, максимально удовлетворяющих всем требованиям, способствовал появлению множества конструктивных решений, нашедших промышленное применение.
Рассмотрим несколько конструкций ротора, предварительно определив принятую терминологию.
Цилиндрическую поверхность корпуса ротора между билами, образующая которой параллельна оси вращения, называют внешней поверхностью ротора. Поверхности, ограничивающие ротор по длине и перпендикулярные его оси вращения, называют торцовыми.
8
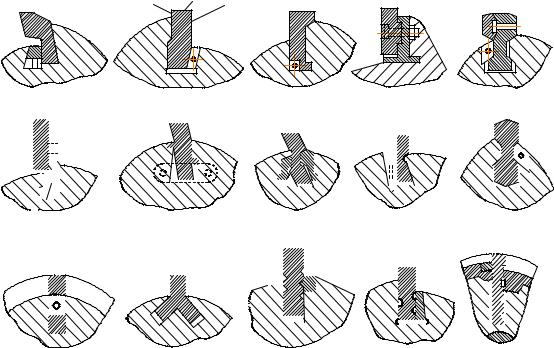
Окружность, описываемая наиболее удаленной от оси вращения точкой била, называют окружностью ротора (рис. 3.1). Билом называют деталь ротора, непосредственно наносящую удар по дробимому материалу.
Числом бил ротора считается число бил в поперечном сечении ротора. Поверхность A била (рис. 3.2), наносящую удар по дробимому материалу, называют рабочей поверхностью, противоположную ей поверхность Б, прилегающую к корпусу ротора – опорной поверхностью, а наиболее удаленную от оси вращения ротора поверхность В – внешней поверхностью била.
Б В А
|
|
а |
|
|
|
|
|
|
|
|
|
|
|
|
|
б |
|
|
|
|
|
в |
|
|
|
|
г |
д |
|
|||||||||||||||||||
|
|
|
|
|
|
|
|
|
|
|
|
|
|
|
|
|
|
|
|
|
|
|
|
|
|
|
|
|
|
|
|
|
|
|
|
|
|
|
|
|
|
|
|
|
|
|
|
|
|
|
|
|
|
|
|
|
|
|
|
|
|
|
|
|
|
|
|
|
|
|
|
|
|
|
|
|
|
|
|
|
|
|
|
|
|
|
|
|
|
|
|
|
|
|
|
|
|
|
|
|
|
|
|
|
|
|
|
|
|
|
|
|
|
|
|
|
|
|
|
|
|
|
|
|
|
|
|
|
|
|
|
|
|
|
|
|
|
|
|
|
|
|
|
|
|
|
|
|
|
|
|
|
|
|
|
|
|
|
|
|
|
|
|
|
|
|
|
|
|
|
|
|
|
|
|
|
|
|
|
|
|
|
|
|
|
|
|
|
|
|
|
|
|
|
|
|
|
|
|
|
|
|
|
|
|
|
|
|
|
|
|
|
|
|
|
|
|
|
|
|
|
|
|
|
|
|
|
|
|
|
|
|
|
|
|
|
|
|
|
|
|
|
|
|
|
|
|
|
|
|
|
|
|
|
|
|
|
|
|
|
|
|
|
|
|
|
|
|
|
|
|
|
|
|
|
|
|
|
|
|
|
|
|
|
|
|
|
|
|
|
|
|
|
|
|
|
|
|
|
|
|
|
|
|
|
|
|
|
|
|
|
|
|
|
|
|
|
|
|
|
|
|
|
|
|
|
|
|
|
|
|
|
|
|
|
|
|
|
|
|
|
|
|
|
|
|
|
|
|
|
|
|
|
|
|
|
|
|
|
|
|
|
|
|
|
|
|
|
|
|
|
|
|
|
|
|
|
|
|
|
|
|
|
|
|
|
|
|
|
|
|
|
|
|
|
|
|
|
|
|
|
|
|
|
|
|
|
|
|
|
|
|
|
|
|
|
|
|
|
|
|
|
|
|
|
|
|
|
|
|
|
|
|
|
|
|
|
|
|
|
|
|
|
|
|
|
|
|
|
|
|
|
|
|
|
|
|
|
|
|
|
|
|
|
|
|
|
|
|
|
|
|
|
|
|
|
|
|
|
|
|
|
|
|
|
|
|
|
|
е |
ж |
|
|
|
|
з |
|
и |
|
|
|
|
|
|
к |
||||||||||
|
|
|
|
|
|
|
|
|
|
|
|
|
|
|
|
|
|
|
|
|
|
|
|
|
|
|
|
|
|
|
|
|
|
|
|
|
|
|
|
|
|
|
|
|
|
|
|
|
|
|
|
|
|
|
|
|
|
|
|
|
|
|
|
|
|
|
|
|
|
|
|
|
|
|
|
|
|
|
|
|
|
|
|
|
|
|
|
|
|
|
|
|
|
|
|
|
|
|
|
|
|
|
|
|
|
|
|
|
|
|
|
|
|
|
|
|
|
|
|
|
|
|
|
|
|
|
|
|
|
|
|
|
|
|
|
|
|
|
|
|
|
|
|
|
|
|
|
|
|
|
|
|
|
|
|
|
|
|
|
|
|
|
|
|
|
|
|
|
|
|
|
|
|
|
|
|
|
|
|
|
|
|
|
|
|
|
|
|
|
|
|
|
|
|
|
|
|
|
|
|
|
|
|
|
|
|
|
|
|
|
|
|
|
|
|
|
|
|
|
|
|
|
|
|
|
|
|
|
|
|
|
|
|
л |
м |
н |
о |
п |
Рис. 3.2. Виды бил роторной дробилки
Кольцевое пространство, образуемое вращением рабочей поверхности била, называют рабочей зоной ротора, так как попавший в нее кусок дробимого материала неизбежно подвергается удару билом.
Для эффективного разрушения дробимого материала окружные скорости бил достигают 20 − 80 м/с. Такие высокие окружные скорости создают центробежные силы в сотни килоньютонов, действующие на било, а при соударении возникают ударные усилия, превышающие их в сотни раз.
Роторы классифицируются по наиболее существенным признакам: по числу бил ротора – 2 – 12; по монолитности корпуса ротора – монолитные (закрытые) и пустотелые (в виде дисков); по наличию торцовых дисков – с торцовыми дисками и без них.
При выборе числа бил руководствуются следующим: чем больше число бил, тем меньше промежуток времени между двумя проходами двух соседних
9
бил и меньше глубина проникновения кусков в рабочую зону, а следовательно, и меньше размер части куска, которая может быть отколота и выброшена в выходную щель. В тоже время при большей глубине проникновения куска и надлежащей скорости удара получается более эффективный удар по куску, повышается производительность. Отсюда следует, что чем больше диаметр и чем мельче желают получать продукт дробления, тем больше число бил должен иметь ротор и наоборот. Наиболее удобны как при изготовлении, так и при эксплуатации роторы с четным числом бил (два, четыре и шесть), так как для балансировки требуется подобрать равные по весу диаметральнопротивоположные била. Однако изготавливают и трехбильные роторы и еще реже пятибильные. Подобрать пять бил, равных по весу сложнее, поэтому с нечетным числом бил (более пяти) роторы не изготавливают. Роторы с 8 − 12 билами встречаются на дробилках мелкого дробления.
При большом многообразии конструктивных решений роторов следует выделить две их разновидности (рис. 3.1): монолитные или закрытые (а, б, д, е) и пустотелые в виде дисков – открытые (в, г). Закрытый ротор (рис. 3.1) представляет собой цилиндр с круглым (а), овальным (д), квадратным или другой формы сечением, на внешней поверхности которого предусмотрены продольные пазы для установки бил. Цилиндр (рис. 3.1) может быть монолитный (д) или полый внутри (б). Конструкция таких роторов обладает большим моментом инерции, что позволяет эффективно использовать их на дробилках крупного дробления. Используют такие роторы и на дробилках среднего и мелкого дробления.
Роторы, как отмечалось ранее, выпускаются двух типов – с торцовыми дисками и без них. В дробилках с роторами без торцовых дисков куски дробимой породы заклиниваются между торцом била и боковой стенкой дробилки, вызывая интенсивное изнашивание боковой стенки в зоне ротора. Для защиты от изнашивания боковую стенку покрывают специальной футеровкой. Срок службы футеровки в этих условиях невелик, что вызывает необходимость частого профилактического ремонта дробилок.
Для уменьшения количества материала, попадающего между торцами бил и боковой стенкой, приемный лоток выполняют уже длины ротора или ему придают форму, ограничивающую поступление камней на края ротора. С целью уменьшения износа корпуса ротора его длину делают меньше длины бил. Это обеспечивает больший зазор между корпусом ротора и стенкой, чем между торцом била и стенкой.
В конструкциях дробилок с роторами, имеющими торцовые диски, проникновение части дробимого материала между боковой стенкой и корпусом ротора сведено до минимума.
Торцовые диски роторов располагаются в нишах боковых стенок корпуса дробилки так, что внутренние их плоскости совпадают с внутренней плоскостью боковых футеровок. Зазор между футеровкой и торцовым диском в радиальном направлении намного меньше, чем в осевом. Поэтому куски, прошед-
10