
Учебники 80351
.pdf
Э = |
|
m m υ 2 |
. |
||
|
1 |
2 |
0 |
||
|
|
|
|||
р |
2 |
(m1 + m2 ) |
|
||
|
|
|
|
|
Экспериментами установлено, что при ударе по камню, сопровождаемом его разрушением, количество энергии, отдаваемое камню,
2 m12m2 |
|
Э2 = К1Э2 = 2К1υ0 (m + m )2 |
|
1 |
2 |
или учитывая, что в роторных дробилках масса ротора m1 значительно больше массы камня m2 и отношение m2 m1 можно принять равным нулю, получим
Э2 = 2K1m2υ02 ,
где K1 = 0,9 ÷ 0,95 .
Дробление материала в ударных дробилках начинается только при сообщении ему энергии определенной величины. При малой величине передаваемой энергии тело не разрушается.
Критерием оценки ударного воздействия по камню является число dϑ 2 = G . Если для данной горной породы оно меньше постоянного значения С, то камень не разрушается, если больше, то удар происходит с разрушением.
В результате исследований ударного дробления ВНИИСтройдормашем получена формула для определения критического размера куска dкр в м, т.е. ес-
ли кусок материала будет иметь размер меньше критического, то при данных условиях он не раздробится
|
|
d |
|
= 230 |
σ р |
10−5 , |
|
|
кр |
γ υ1,5 |
|||
|
|
|
|
|
||
|
|
|
|
|
|
|
|
|
|
|
|
о р |
|
где d – |
размер частицы; |
|
|
|
|
|
υ – |
скорость удара; |
|
|
|
|
|
z – |
показатель степени, равный z ≤ 2 ; |
|
||||
σ |
р |
– предел прочности материала при растяжении, Н/м2; |
||||
|
|
|
|
|
|
γ о – объемная масса дробимого материала, кг/м3;
υ p – скорость удара, принимаемая равной окружной скорости ротора, м/с.
Если же необходимо определить критическую скорость υкр для опреде-
ленного вида материала и заданной крупности продукта дробления d, то из предыдущего выражения будем иметь
υкр |
= 1,75 ×10−2 |
|
σ |
р |
2 |
3 |
|
. |
|||
|
|
||||
|
|
|
γ оd |
||
|
41 |
|
|
|
|
6. РАСЧЕТ ТЕХНОЛОГИЧЕСКИХ ПАРАМЕТРОВ
Производительность. На производительность роторных значительно влияют его конструктивные и технологические параметры такие, как параметры ротора, углы установки отражательных плит, ширина выходной щели и внешней поверхности била, размеры исходного материала и его физикомеханические свойства и др.
Производительность роторных дробилок определяется рядом последовательных операций, разрушения и перемещения материала к разгрузочному отверстию. Кроме бил ротора в этом процессе участвуют отражательные плиты и колосниковые решетки. В отражательных плитах разделяющих дробилку на отдельные камеры дробления, создаются определенные условия дробления и разгрузки материала. Чтобы исключить забивание дробилки, производительность последовательно расположенных камер дробления должна возрастать к разгрузочному отверстию. На производительность дробилки существенно влияют условия подачи исходного материала и максимальная его крупность. Наибольшая производительность достигается при таком питании дробилки, при котором над ротором постоянно поддерживается «шапка» исходного материала. Это обеспечивает большую плотность материала, взаимодействующего с билами , увеличивается масса материала, участвующая при каждом ударе ротора.
Крупность исходного материала не должна превышать значения, при которых происходит затрудненное перемещение материала в камере и возможно сводообразование и заклинивание камней. Для условий работы ротора «под шапкой» наибольшая крупность исходного материала не должна превышать
0, 2Dp .
В соответствии с перечисленными особенностями процесса дробления производительность первой камеры дробления определяют по следующей схеме. Частицы материала под действием сил тяжести опускаются на ротор со скоростью и проникают в рабочую зону ротора в период между проходами бил, а ротор подобно фрезе срезает каждым билом «стружки» объемом
V = ALph , |
(6.1) |
где A − горизонтальная проекция дуги между приемным лотком и первой отражательной плитой;
Lp − длина ротора;
h − средняя толщина стружки.
Тогда для данной модели максимальная производительность дробилки в объемных единицах
Qmax = ALphnz , |
(6.2) |
42
где n − частота вращения ротора в единицу временна; z − число бил ротора.
Как следует из формулы на максимальную производительность влияют размеры ротора, частота его вращения, число бил и параметров, определяющие глубину проникновения. Экспериментальные исследования, проведенные во ВНИИстройдормаше, показали, что на толщину влияют многие параметры, для которых зависимости установлены опытным путем.
Общее выражение для определения максимальной производительности имеет вид
|
Q |
=1390 |
Lp Dp |
K |
|
K |
|
K |
K |
, |
(6.3) |
|
ϑpm zq |
|
|
||||||||
|
max |
|
|
β |
|
D |
|
S σ |
|
|
|
где m = 0,35; |
|
|
|
|
|
|
|
|
|
|
|
q = 0,5; |
|
|
|
|
|
|
|
|
|
|
|
при 0 < β < 90o |
функция Kβ =1 - 0, 49sin β + 4,7sin2 β ; |
|
|||||||||
K D − функция, характеризующая влияние крупности кусков исходного ма- |
|||||||||||
териала, при (D / Dp ) £ 0, 2 функция KD = 1 − 3, 4D / Dp , |
при 0, 2 £ (D / Dp ) £ 0,6 |
||||||||||
(содержание максимальных кусков единичное) |
K D = 0,3 ; |
|
|||||||||
K S − функция, |
характеризующая |
влияние |
выходной |
щели, |
KS =1 +1,9(S / Dp ) =1 +1,9ε ;
Kσ − функция, характеризующая влияние физических свойств дробимого материала, Kσ =1 -σ p / ( p0 Dp × 700).
Производительность последующих камер дробления также определяют по этой формуле с учётом изменения крупности дробимого материала и параметров камеры дробления.
Мощность привода. Стоимость затрачиваемой электроэнергии составляет около 30% от общей стоимости операции дробления материалов в роторных дробилках среднего и мелкого дробления. Расход электроэнергии на дробление зависит от производительности, результатов дробления, вида перерабатываемого материала, конструкции и режима работы дробилки.
Исследованиями, приведенными во ВНИИСстройдормаше на промышленных и опытных дробилках, были получены основные зависимости расхода электроэнергии от показателей и режима работы дробилок.
Чтобы сопоставить расход энергии на процесс дробления Nдp в разных
конструкциях дробилок, чаще всего из общей мощности вычитают мощность холостого хода, подразумевая, что разность представляет собой мощность, затрачиваемую на чистое дробление. Как показали исследования, этот метод дает большую погрешность. Мощность, расходуемая на потери в меха-
43
низмах роторной дробилки и электродвигателе, при номинальной нагрузке больше мощности холостого хода в 1,1−1,7 раза.
Расход энергии на дробление зависит от многих параметров, важнейшие из которых производительность, степень дробления и вид перерабатывающего материала.
Существующие формулы и рекомендации для определения установленной мощности электродвигателя дробилки в разной степени учитывают конструктивные и технологические параметры и показатели машины. Наиболее простой способ расчета получается по формулам, выведенным в результате обработки каталожной информации.
Наибольшие и наименьшие установочные мощности, вычисленные как среднестатистические зависимости, определяются следующими выражениями:
Nmax = 100Dp Lp ; |
(6.4) |
||
Nmin = 30Dp Lp ; |
(6.5) |
||
В некоторых источниках приведены простые формулы, используемые для |
|||
расчета мощности (кВт) привода молотковых и роторных дробилок: |
|
||
n |
|
|
|
N = 7,5Dp Lp |
|
; |
(6.6) |
|
|||
60 |
|
|
|
N = 0,15Dp2 Lpn ; |
|
(6.7) |
|
N = (0,1 − 0,15)iQ ; |
|
(6.8) |
где Dp , Lp − диаметр и длина ротора, м; n − частота вращения ротора, об/мин; i − степень дробления; Q − производительность, т/ч.
Формулы (6.6) – (6.8) устанавливают зависимость мощности от размеров дробилки и частоты вращения ротора. Поэтому они удобны для расчета установочной мощности электродвигателя, режим работы которого известен или будет уточняться. Формула (6.8) устанавливает связь с технологическими показателями дробилки, однако для надежного расчета мощности технологических показателей и недостаточно.
Более полной является формула (6.9), которая учитывает основные технологические параметры, влияющие на расход энергии. Входящие в эту формулу КПД дробилки и КПД клиноременной передачи могут быть определены по графикам рис. 6.1 и 6.2 .
Для сопоставления в таблице 6.1 приведены значения мощностей подсчитанных по приведенным формулам и по ГОСТу 12375-70
44
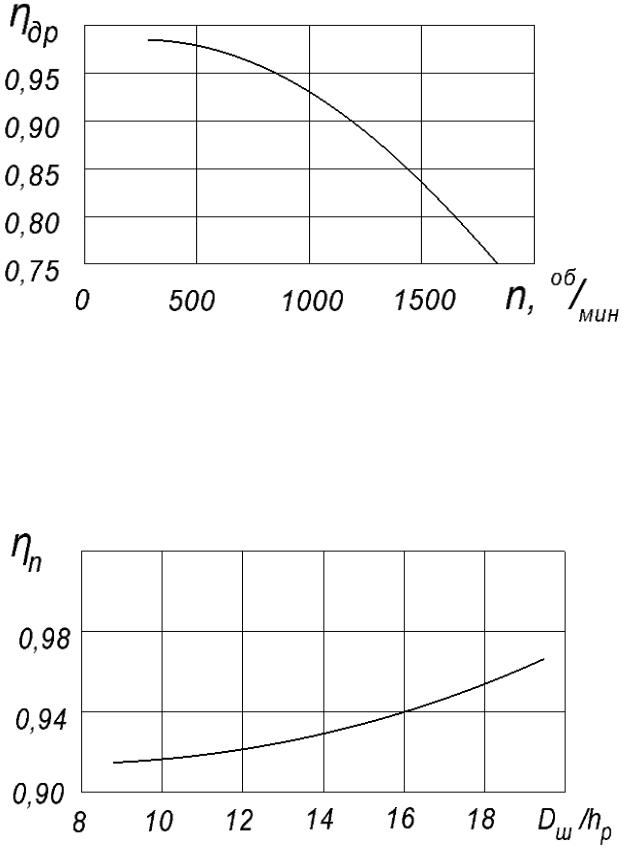
Рис. 6.1. График для определения КПД однороторных дробилок
Формулы (6.4)–(6.5) устанавливают зависимость мощности от размеров дробилки и числа оборотов. Поэтому они удобны для расчета установочной мощности электродвигателя определенного типоразмера, режим работы которого неизвестен или будет уточнен. Формула (6.8) устанавливает связь с технологическими показателями дробилки, однако для надежного расчета мощности технологических параметровi и Q недостаточно.
Рис. 6.2. График для определения КПД клиноременной передачи отечественных роторных дробилок: hр – толщина ремней в мм; Dш – диаметр меньшего шкива в мм
45
Таблица 6.1
Сравнение мощностей, определенных по разным формулам
|
|
|
|
|
Типоразмер дробилки |
|
|
|||
|
|
|
|
|
|
|
|
|
|
|
Расчетные параметры |
–5×4ДРК |
–6×5ДРК |
|
–8×6ДРК |
–10×8ДРК |
–12×10ДРК |
–16×12ДРК |
–20×16ДРК |
–25×20ДРК |
|
|
|
|
|
|
|
|
|
|
||
|
|
|
|
|
|
|
|
|
|
|
Диаметр ротора в м |
|
0,50 |
0,63 |
|
0,80 |
1,00 |
1,25 |
1,60 |
2,00 |
2,50 |
|
|
|
||||||||
Длина ротора в м |
|
0,40 |
0,50 |
|
0,63 |
0,80 |
1,00 |
1,25 |
1,60 |
2,00 |
Производительность |
в |
|
|
|
|
|
|
|
|
|
м3/ч |
|
13 |
24 |
|
47 |
68 |
125 |
200 |
370 |
560 |
Средневзвешенный |
|
|
|
|
|
|
|
|
|
|
размер исходного ма- |
|
|
|
|
|
|
|
|
|
|
териала в мм |
|
125 |
150 |
|
200 |
250 |
300 |
400 |
550 |
750 |
Степень дробления |
|
5,85 |
6,18 |
|
7,50 |
9,20 |
9,74 |
12,5 |
15,0 |
19,7 |
|
|
|
|
|
|
|
|
|
|
|
Расчетная мощность |
в |
|
|
|
|
|
|
|
|
|
кВт, вычисленная |
по |
|
|
|
|
|
|
|
|
|
формулам: |
|
|
|
|
|
|
|
|
|
|
(7.4) |
|
20 |
31 |
|
50 |
80 |
125 |
200 |
320 |
450 |
|
|
|
||||||||
(7.5) |
|
6 |
10 |
|
15 |
24 |
38 |
60 |
96 |
135 |
|
|
|
||||||||
(7.9) |
|
13,8 |
22,6 |
|
41,4 |
60,5 |
99,3 |
157 |
256 |
380 |
|
|
|
||||||||
(7.6) |
|
26 |
32 |
|
41 |
52 |
65 |
81 |
104 |
130 |
|
|
|
||||||||
(7.7) |
|
11 |
18 |
|
29 |
46 |
69 |
115 |
183 |
287 |
|
|
|
||||||||
(7.8) |
|
8 |
15 |
|
35 |
63 |
120 |
250 |
560 |
1100 |
|
|
|
||||||||
Мощность, принятая по |
|
|
|
|
|
|
|
|
|
|
ГОСТу 12375–70 |
|
10 |
22 |
|
40 |
55 |
100 |
160 |
250 |
400 |
|
|
|
|
|
|
|
|
|
|
|
|
|
|
|
46 |
|
|
|
|
|

Более точные формулы основаны на классических гипотезах дробления и энергетических показателях разрушения материалов и горных пород.
В работах ВНИИстройдормаша были проведены исследования по определению достоверности результатов расчета мощности по различным гипотезам. При этом характеристикой результатов дробления были приняты выраже-
ния (i -1)/
Dсв и lgi соответственно для гипотез Риттингера,
Бонда и Кирпичева-Кика. Наименьший разброс точек от осредняющего графика и наименьший коэффициент вариации соответствовал гипотезе Риттингера, что дало основание рекомендовать для расчетов следующую формулу:
|
N = |
ωдрQ(i -1) |
, |
(6.9) |
|
|
|||
|
|
Dсвηдрηп |
|
|
где ω |
– энергетический показатель дробилки, кВт·ч/м2; D |
– средневзвешен- |
||
др |
|
|
св |
|
ный размер исходного материала, м; ηдр – КПД дробилки; ηп – |
КПД привода. |
Энергетический показатель включает в себя все виды энергии, отдаваемой ротором при ударе, в которую входит кроме энергии, расходуемой непосредственно на разрушение камня, энергия на износ бил, футеровок и отражательных плит, на перемещение материала, на колебательные процессы в материале и дробилке от ударного воздействия, не приводящие к разрушению камня, и на другие сопутствующие явления не отделимые от ударного процесса дробления. Изменение энергетического показателя связанно с относительным перераспределением этих видов энергии. Увеличение энергетического показателя с уменьшение окружной скорости бил ротора обусловлено меньшей долей энергии, расходуемой непосредственно на разрушение материала, – степень дробления с уменьшением скорости снижается. В то же время потери энергии на непроизводственные затраты (перемещение материала, колебательные процессы и др.) снижаются в меньшей мере.
При увеличении размера выходной цели снижаются непроизводительные затраты энергии на износ бил и нижней кромки отражательной плиты. Однако при этом увеличиваются затраты на перемещение нераздробившихся кусков. Как вытекает из анализа графика, существует оптимальная ширина выходной щели, при которой сумма этих затрат принимает минимальное значение, вследствие чего ωдр имеет минимум.
Для некоторых материалов значение энергетического показателя приведено в таблице 6.2.
Значение ηдр зависит от окружной скорости ротора и может быть определено по следующим формулам:
ηдр =1 - 0,8 ×10−7 n2 ; |
(6.10) |
47 |
|
ηп = 0,76 - 0,61×10−7 n2 . |
|
(6.11) |
||
КПД клиноременной передачи принимают в пределах , ,. |
|
|||
|
|
|
|
Таблица 6.2 |
Физико-механические характеристики материалов |
|
|||
|
|
|
|
|
Материал |
ρн, г/см3 |
|
σр, МПа |
103ωдр,3 |
|
|
|
|
кВт·ч/м |
Уголь, антрацит |
0,9 |
|
2,75 |
2,5 |
Силикатный кирпич |
1,2 |
|
1,0 |
4,5 |
Известняк месторождения: |
|
|
|
|
Шуровского |
1,48 |
|
1,85 |
8,6 |
Турдейского |
1,54 |
|
12,0 |
19,0 |
Ковровского |
1,52 |
|
7,0 |
21,0 |
Гранит Клесовского месторождения |
1,52 |
|
12,7 |
15,0 |
Диорит Клесовского месторождения |
1,76 |
|
16,4 |
40,0 |
|
|
|
|
|
Следует отметить, что энергетический показатель включает в себя все виды энергии, отдаваемой ротором при ударе, в которую, кроме энергии, расходуемой непосредственно на разрушение камня, входит энергия, затрачиваемая на изнашивание бил, футеровок и отражательных плит, на перемещение материала и на колебательные процессы, происходящие в материале и дробилке. Исследования показали, что при различных режимах дробления значение энергетического показателя непостоянно. Коэффициент вариации его значения составляет около 20%. Это свидетельствует о различных соотношениях расхода энергии непосредственно на дробление и прочие потери.
Рядом исследователей предложено определить энергию, расходуемую на дробление, по выходу мелких фракций 0–0,25 , 0–03 , 0–0,7 мм. Данные предложения базируются на том, что мелкие фракции образуются в основном в зоне контакта материала с рабочим органом, а на процессы разрушении в этой зоне затрачивается до 95–97% всей энергии дробления.
Установленная мощность (кВт) электродвигателя по выходам мелких фракций:
|
|
- γ i ) + |
1.5 |
|
|
|
N = |
Q ωR (γ i |
0,0004vp |
|
, |
(6.11) |
|
|
ηдрηп |
|
|
|||
|
|
|
|
|
|
|
|
|
48 |
|
|
|
|
где ωR − энергетический показатель, кВт·ч/т; vp − окружная скорость ротора дробилок со свободной загрузкой (без колосниковых решеток), м/c; γ i ,γ i − доли фракций (0… i), мм, соответственно в продукте дробления и в исходном материале, определяемые по графикам зернового состава;ηп − КПД привода.
Выбор размера мелкой фракции определяется крупностью дробления. Для крупного дробления рекомендуется принимать размер мелкой фракции 0– 7 мм, для мелкого 0 – 0,25 мм. При этом учитывается, что определение содержания мелких фракций практически затруднено из-за их значительного распыливания.
Сложность использования в расчетах формулы заключается в том, что значения энергетических показателей обычно бывают неизвестными. С этой целью предлагают пересчетные формулы для определения энергетических показателей (кВт·ч/м2) материалов средней прочности:
ωR = 0,002σ p . |
(6.12) |
Для некоторых материалов |
значение энергетического |
показателя |
||||||||
ωR − приведено в табл. 6.3 |
|
|
|
|
|
|
|
|
|
|
Таким образом, энергетические показатели дробления состовляют: |
|
|||||||||
ω |
R |
= 22 / (V K ) кВт·ч/м2, |
(6.13) |
|||||||
|
|
|
|
|
max |
|
|
|
|
|
|
ω |
R |
= 22 /V |
кВт·ч/м2; |
(6.14) |
|||||
|
|
|
|
max |
|
|
|
|
||
где К – удельная поверхность продукта дробления фракции 0…7 |
мм, К = |
|||||||||
100÷150 см2/см3. |
|
|
|
|
|
|
|
|
|
|
|
|
|
|
|
|
|
|
|
|
Таблица 6.3 |
Физико-механические характеристики материалов |
|
|||||||||
|
|
|
|
|
|
|
|
|
|
|
Материал |
|
|
|
|
|
σр, |
|
ρ0, |
|
ωR, |
|
|
|
|
|
МПа |
|
г/см3 |
|
кВт·ч/т |
|
|
|
|
|
|
|
|
|
|
|
|
Уголь, антрацит |
|
|
|
|
|
2,1 |
|
1.8 |
|
0.5 |
|
|
|
|
|
|
|
|
|
|
|
Красный кирпич |
|
|
|
|
|
1.7 |
|
1.7 |
|
0.9 |
|
|
|
|
|
|
|
|
|
|
|
Доломит |
|
|
|
|
|
5.7 |
|
2.2 |
|
1.1 |
|
|
|
|
|
|
|
|
|
|
|
Доломит |
|
|
|
|
|
5.4 |
|
2.3 |
|
1.0 |
|
|
|
|
|
|
|
|
|
|
|
Известняк |
|
|
|
|
|
7.8 |
|
2.5 |
|
1.6 |
|
|
|
|
|
|
|
|
|
|
|
Гранит |
|
|
|
|
|
12.4 |
|
2.8 |
|
2.2 |
|
|
|
|
|
|
|
|
|
|
|
|
|
|
|
|
|
49 |
|
|
|
|
Установочную мощность двигателей дробилок можно определить и по другим формулам. Например, В. А. Олевский предлогает такую эмпирическую зависимость:
N = 9Dp2 Lpn , |
(6.15) |
где N, кВт; Dp и Lp – диаметр и длина ротора, м; n − число оборотов в секунду.
7. ПРИМЕНЕНИЕ РОТОРНЫХ ДРОБИЛОК
Роторные дробилки широко используются на стационарных и передвижных дробильно-сортировочных заводах и установках различной мощности. Применение роторных дробилок упрощает технологические схемы производства и улучшает его экономику.
Применение дробилок на стационарных дробильно-сортировочных заво-
дах. ГИПРОНИНерудом разработаны типовые схемы дробильносортировочных заводов, на которых для переработки карбонатных пород (известняков и доломитов) средней прочности, содержащих слабые разности в количестве до и глины до , используются роторные дробилки. Годовая производительность заводов составляет и ! .
Карбонатные породы по условиям образования характеризуются высокой неоднородностью при незначительной толщине различных слоев, поэтому избирательная разработка отдельных слоев в карьерах практически невозможна.
Использование избирательной способности роторных дробилок, а также применение дополнительных способов обогащения при переработке карбонатных пород позволяет получить щебень двух или трех марок прочности.
На рис. 7.2 показана типовая технологическая схема щебеночного завода для переработки горных пород с использованием метода избирательного дробления и последовательного выделения слабых разностей. Исходная горная масса крупностью до разделяется на колосниковом инерционном грохоте СМ– 690 на два потока, которые условно называют «слабый» (менее мм) и «прочный» (более мм). Каждый поток перерабатывается в дальнейшем отдельно. В слабый поток уходит значительная часть вскрышных пород и глины, поэтому после вторичного разделения на грохоте СМ– 572 и дробления в дробилке СМД– 86 предусматриваются удаление мелких фракций в отход. Третья стадия дробления производится в дробилке СМД– 75.
Первичное дробление прочного потока осуществляется в однороторной дробилке СМД– 87. Затем продукт дробления рассеивается на двух грохотах СМ– 572, из которого фракция .мм удаляется в отход, а фракция " мм имеющая значительное количество слабых пород, направляется в поток слабого материала. Материал крупностью #" мм подается на вторую стадию в
50