
Учебное пособие 2180
.pdf
Р/ρг и D. Через эту точку проводят горизонталь до пересечения с кривой, соответствующей принятому типу циклона (точка Б на кривой ЦН-15). Перпендикуляр, опущенный из точки Б на абсциссу, укажет производительность циклона VЦ (точка А).
Рассмотренная номограмма устанавливает связь между типом циклона НИИОгаз, его диаметром D, производительностью Vц, сопротивлением Ри удельным весом газа ρг.
Чтобы найти один из пяти параметров, нужно знать четыре из них. Пример. Производительность циклона 3600 м3/ч газа удельного веса рг =
6,9 Н/м3. Допускаемое сопротивление циклона Р = 40 мм вод. ст. Определить диаметр циклона D для заданной производительности, если тип циклона ЦН-15.
Прежде всего находим Р/ρг = 40/0,69 = 58 м. Далее на оси абсцисс находим точку А, соответствующую производительности циклона VЦ = 3600 м3/ч. Из точки А восстанавливаем перпендикуляр до пересечения с кривой ЦН – 15 в точке Б. Из точки Б проводим горизонталь до пересечения с радиальной прямой Р/ρг–58 м в точке В. Дуга, проходящая через эту точку, укажет диаметр D= 625 мм. Таким же путем решаются другие аналогичные задачи по расчету циклонов НИИОгаз.
Для диаметра (в м) циклонов ЦККБ рекомендуется зависимость:
Dцикл V / 222 ц |
(3.59) |
где V – производительность циклона, м3/ч;
υц – скорость пылегазовой смеси на входе в циклон, принимаемая в пределах 18
– 22 м/с.
Зернистые фильтры
Зернистые фильтры являются перспективными аппаратами для очистки горячих, запыленных абразивными частиками газов. Газ пропускается сквозь движущийся слой зернистого материала, и в нем оседают частицы пыли под действием сил инерции, диффузии, статического электричества и непосредственного зацепления с зернами.
На рис. 3.18. показана схема комбинированного зернистого фильтра, разработанного сотрудниками БТИСМа.
Запыленный газ одновременно подается по патрубкам 2 и 7 в полость А между корпусом 1 и цилиндром 3 под некоторым углом к горизонтали и по касательной к окружности корпуса. Газ в полости А движется по спиральной траектории: из патрубка 2 по спирали вниз, а из патрубка 7 – вверх.
111

Рис. 3.18. Схема зернистого фильтра:
А– нижняя часть полости; Б – полость; В – отверстия;
1– корпус; 2 – патрубок; 3 – цилиндр; 4 – стенка цилиндра; 5 – стенка цилиндра; 6 – труба; 7 – патрубок
Во встречных потоках возникает значительная турбулентность, что способствует смещению частиц пыли с линий тока и их осаждении. При вращательном движении газа более крупные частицы под действием центробежных сил прижимаются к внешнему корпусу, теряют скорость и под действием сил тяжести опускаются в нижнюю часть полости А. Патрубок 2 имеет больший диаметр и больший угол наклона к горизонту, чем патрубок 7, что обеспечивает итоговое движение газа сверху вниз. При дальнейшем движении газ, содержащий более мелкие частицы, поступает в полость Б, проходит через перфорированные стенки цилиндров 4 и 5 и слои движущегося сверху вниз зернистого материала дополнительно очищаются и через отверстия В поступают в трубу 6, по которой выводятся из фильтра.
Фильтрующим слоем может служить материал, поступающий в мельницу на помол, после которого производится обеспыливание отходящих газов. Таким образом, в этом аппарате газ проходит две ступени очистки: первая (зона А) является циклоном, вторая – фильтром. В зернистых фильтрах можно очищать горячие (до 450° С) газы с запыленностью до 70 г/м3 при эффективности очистки до 99,8%. В зависимости от размеров и конструкции производительность по газу таких фильтров составляет от 20 до 150 м3/с. На второй ступени очистки отходящих газов применяют электрофильтры, которые обеспечивают степень очистки до 99% при начальной запыленности газа до 50 г/м3. Эти аппараты используют обычно на крупныхпредприятиях, например цементных заводах.
112
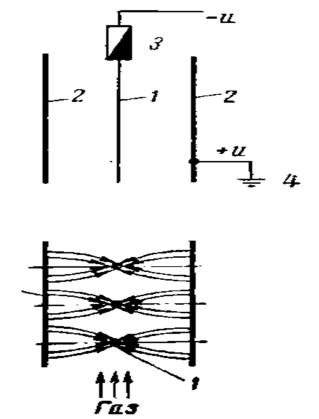
Электрофильтры
Электрический метод очистки является наиболее совершенным. Степень очистки газов в электрофильтрах доходит до 99 – 99,5%. Расход мощности в электрофильтрах составляет 0,15 – 1,1 л.с. на 100 м3 газа. Потеря напора не превышает 30 мм вод. ст. В них можно очищать химические агрессивные газы и газы с относительной температурой.
Электрофильтры делятся на две группы: трубчатые и пластинчатые. Последние могут быть вертикальными и горизонтальными.
Принцип действия электрофильтров. Если пропускать воздух (газ) со взвешенными в нем частицами пыли через электрическое поле, созданное двумя электродами, то происходит его ионизация. Взвешенные частицы получают при этом электрический заряд, за счет которого они с определенной скоростью перемещаются по направлению к электроду, заряд которого имеет противоположный знак.
Под ионизацией понимается процесс распада электрически нейтральной молекулы на положительно и отрицательно заряженные частицы (ионы). Электрическое поле может быть создано между электродами в виде двух концентрических цилиндров (полый цилиндр и стержень – проволока внутри него) или в виде плоскости и цилиндров (стержни или проволока и плоская пластинка между ними).
Рис. 3.19. Схема электрофильтра: 1 – проволока (стержень); 2 – электрод осадительный; 3 – изолятор проходной; 4 – заземление
113
При появлении ионного разряда вокруг поверхности проволоки (стержня) 1 (рис. 3.19) возникает слабое голубоватое свечение, показывающее зону образования положительно и отрицательно заряженных ионов. Это свечение называется «короной», а соответствующий ионный заряд – «коронным разрядом». Провод, вокруг которого образовалась корона, носит название коронирующего электрода. Электрофильтры питаются постоянным током. Осадительный электрод 2 присоединяется к положительному полюсу, а к коронирующему электроду через проходной изолятор 3 подводится постоянный ток отрицательного знака, потому что отрицательно заряженные ионы, например, воздуха, движутся со скоростью в 1,37 раза больше, чем положительные. Опыт показывает, что при этом улучшаются условия для выделения из газа пыли и степень очистки может достигать 99 – 99,5%. Положительно заряженные электроды имеют заземление 4. При подводе к коронирующему электроду постоянного тока положительного знака степень очистки составляет 99%, а при подводе переменноготока – всего 71 – 72%.
Объем сечения камеры электрофильтра определяется исходя из следующего. Практически время пребывания газа в камере принимают равным 2 – 3,5 сек. Такая продолжительность считается достаточной для осаждения пыли на осадительном электроде. Это означает, что частицы пыли, получив заряд, достигают осадительного электрода и, отдав ему свой заряд, оседают на нем.
Втак называемых пластинчатых электрофильтрах осадительные электроды имеют вид пластин, между которыми размещаются коронирующие электроды. В зависимости от направления движения газов пластинчатые электрофильтры бывают горизонтальные и вертикальные.
Винституте «Гипрогазоочистки» для очистки дымовых газов разработаны горизонтальные трех- и четырехпольные электрофильтры типов ПГД и ПГДС.
Вэлектрофильтрах ПГД применяют осадительные электроды в виде пластин, составленных из наклонно расположенных желобов (под углом 83° к направлению движения газов) W-образной формы. В электрофильтрах ПГДС применяют С-образные односторонние и двусторонние осадительные электроды в паре с коронирующими электродами штыкового сечения или игольчатого типа.
На рис. 3.20 представлен четырехпольный горизонтальный электрофильтр для очистки от пыли газов, отходящих от вращающейся печи.
Фильтр имеет четыре поля (электрических). Электрофильтр состоит из стального корпуса, внутри которого установлены осадительные 1 и коронирующие 2 электроды. Запыленные газы поступают в дымовую камеру 3 вращающейся печи. В камере происходит частичное осаждение пыли. Газы из камеры направляются в корпус электрофильтра, где происходит выделение пыли, собирающейся в бункерах 4. Пыль из бункеров при помощи шнека 5, а также частично из дымовой камеры направляется к загрузочному устройству печи. Очищенные от пыли газы при помощи дымососа 6 поступают в дымовую трубу.
114
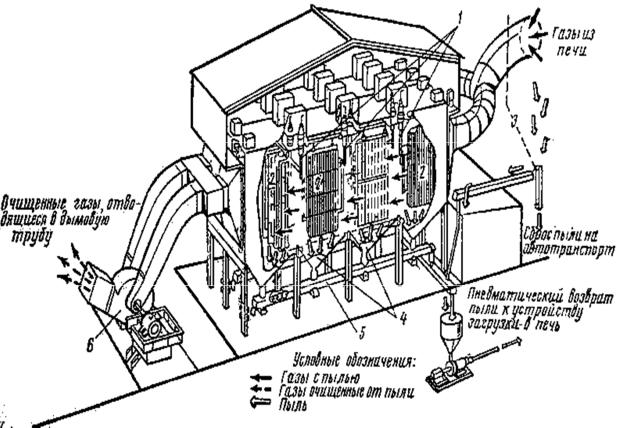
Рис. 3.20. Вертикальный пластинчатый электрофильтр 1 – электрод осадительный; 2 – электрод коронирующий; 3 – камера дымовая; 4 – бункеры; 5 – шнек; 6 – дымосос
По направлению движения газов электрофильтры подразделяются на вертикальные и горизонтальные. Новейшие мощные электрофильтры выпускаются обычно горизонтальными.
Скорость движения газов в новейших конструкциях доходит до 2–2,2 м/сек.
Матерчатые фильтры
Тканевые матерчатые фильтры применяют для очистки воздуха до санитарных норм при работе дробилок, мельниц и в системах пневмотранспорта.
В матерчатых фильтрах пылевоздушная смесь пропускается через перегородки, изготовляемые из толстых тканей (шерстянки, миткали, муслина, бумазеи, байки и т.п.). Производительность матерчатых фильтров составляет 2– 5м3/мин с м2 поверхности ткани (по воздуху).
Коэффициент качества очистки в, матерчатых фильтрах достигает 98 – 99% при запыленности смеси 110 – 450 г/м3. Общее сопротивление фильтра со-
ставляет 70 –120мм вод. cm.
Сопротивление фильтрующих тканей определяется по формуле
p kтvn |
(3.60) |
115 |
|
где kт – коэффициент, зависящий от сорта ткани, для муслина при длительном пользовании он равен 24, для бумазеи – 7,6;
v – средняя скорость прохождения воздуха (газа) через ткань;
n –показатель степени, зависящий от сорта ткани, для муслина п=1,46, для бумазеи п=1,83.
Для очистки газов, разъедающих ткань и имеющих температуру выше 100°, необходимо использовать специальные ткани (стеклянные, перхлорвиниловые и т.д.).
Различают матерчатые фильтры рамного или рукавного типа. В рамных фильтрах материя натягивается на рамки, и газовый поток, содержащий пыль, проходит через фильтрующую ткань. Более совершенны по конструкции и надежны в работе фильтры рукавного типа. Газ пропускают через ткань, сшитую в виде рукава, один конец которого открыт (для входа газов), а другой закрыт.
Схема рукавного фильтра представлена на рис. 3.21. В закрытом металлическом корпусе 1 подвешиваются матерчатые рукава 2 цилиндрической формы. Рукава (по 8–12 шт.) собраны в секции. Секции разделены перегородками на отдельные камеры. Нижние концы рукавов открыты для входа газов. Запыленный паз по трубопроводу 3 подводится в нижнюю часть 4 фильтра, откуда направляется в нижние открытые отверстия рукавов. Проходя через поры ткани, газ очищается, оставляя пыль на внутренних стенках рукавов. Очищенный газ собирается в верхней части металлического кожуха, затем отводится через трубу 5 в общий трубопровод 6. Через матерчатые фильтры газ просачивается при помощи вентиляторов, которые могут нагнетать их в фильтр или отсасывать через последний. В первом случае установка работает под давлением, во втором – под разрежением. Фильтр, представленный на рис. 3.21, работает под разрежением.
Во избежание загрязнения ткани частицами пыли, оседающими на внутренней поверхности рукавов, их периодически встряхивают. Пыль при этом падает в нижнюю часть кожуха, из которого отводится винтовым транспортером 7. Рукава каждой секции подвешены к планке 8, которая соединена со встряхивающим механизмом 9, работающим от электродвигателя. В. момент встряхивания рукавов камера отсоединяется от сборного трубопровода 6 заслонкой 10 (в отдельных конструкциях вместо заслонки применяют клапан, действующий от механизма встряхивания). Для лучшей очистки от пыли ткань продувают воздухом в направлении обратном основному движению газов. Рукава каждой камеры встряхивают в течение 18 – 20сек, затем клапаны продувочного воздуха закрывают, а заслонку 10 открывают, и секция вновь включается в работу. Диаметр рукавов обычно равен 180 – 210мм, длина 2 – 3,5м. Степень очистки газа 97 – 99%. Сопротивление фильтра в среднем равно 25 – 35мм вод. ст. Однако при увеличении остаточной запыленности ткани сопротивление может возрасти в 2 – 3 раза.
116

Рис. 3.21. Схема рукавного фильтра:
1 – корпус; 2 – рукав матерчатый; 3 – трубопровод; 4 – фильтр; 5 – труба; 6 – трубопровод общий; 7 – транспортер винтовой; 8 – планка;
9 – механизм встряхивающий; 10 – заслонка
Рукавные фильтры имеют следующие основные недостатки. В них невозможно без замены обычных тканей специальными очищать газы, температура которых выше 100°. При очистке влажных газов на фильтрующей ткани конденсируются пары воды, и ткань поэтому замазывается. Кроме того, при встряхивании из фильтра удаляется не вся пыль, вследствие чего рукава необходимо очищать каждые три месяца. Рукава фильтров работают до 3000 ч. Для предупреждения конденсации на ткани паров воды фильтры необходимо устанавливать в отапливаемых помещениях и изолировать их вместе с трубопроводом. В зимние месяцы следует продувать камеры фильтра подогретым воздухом. Для наблюдения за работой фильтров рекомендуются устанавливать V- образные манометры и термометры. По показаниям манометров можно судить о работе фильтра: повышение сопротивления свидетельствует о том, что фильтрующая ткань начала замазываться, а понижение – о разрыве ткани.
Более перспективными являются пневматические механизмы встряхивания рукавов, обеспечивающие более полную очистку ткани
Наиболее эффективной является регенерация рукавов при помощи обратного пульсирующего потока воздуха, особенно при использовании рукавов из
117

стеклоткани, не допускающих встряхивания, так как при этом происходит механическое повреждение ткани.
На рис. 3.22 показана принципиальная схема рукавного фильтра с воздушной регенерацией фильтрующей ткани. В металлическом корпусе 2, разделенном вертикальной перегородкой 10 на две одинаковые камеры, установлены группы рукавов 4. Каждый рукав выполнен из коаксиально расположенных внешней и внутренней оболочек ткани. Во внешнюю оболочку для придания устойчивости вставлен спиральный проволочный каркас 5. Снизу, между оболочками, установлена дистанционная втулка. Наружная оболочка при помощи переходной втулки жестко прикреплена к диафрагме отводящего коллектора, а внутренняя присоединена к корпусу при помощи пружинной подвески 6, что обеспечивает необходимое натяжение рукава.
Рис. 3.22. Схема рукавного фильтра:
1 – входной патрубок; 2 – корпус; 3 –продувочный клапан; 4 –рукава; 5 – каркас; 6 – пружинная подвеска; 7 –труба; 8 – клапан; 9 – плоский клапан; 10 – вертикальная перегородка; 11 – бункер; 12 – затвор
В режиме очистки воздуха изображена левая половина фильтра. Запыленный воздух поступает по входному патрубку 1 в межрукавное пространство, проходит сквозь ткань в кольцевую полость между оболочками рукавов и удаляется в атмосферу по трубе 7. Ткань очищается от слоя осевшей пыли (в этом режиме изображена правая половина фильтра) при помощи сжатого воздуха, подаваемого от компрессора через продувочный клапан 3 и соответствующий клапан 8. Сжатый воздух, заполняя надрукавную камеру, закрывает плоский
118
клапан 9, создает противодавление в кольцевых полостях рукавов и, несколько деформируя ткань, сбрасывает осевшую пыль в бункер 11, оборудованный затвором 12.
Включение соответствующей группы рукавов на регенерацию производится автоматически по заданной программе. Продувочный клапан 3 работает в импульсном режиме. Пульсирующий поток воздуха вызывает многократную деформацию стенок рукавов, что обеспечивает высокую степень их очистки от пыли.
Основной характеристикой матерчатых фильтров является площадь общей фильтрующей поверхности рукавов. Расчетная площадь фильтрующей поверхности при механическом встряхивании рукавов (м2),
S Vг / qг |
δVг / qn , |
(3.61) |
где Vг – расход запыленного газа, поступающего в фильтр, м3/с;
qг – допускаемая удельная нагрузка на ткань фильтра по газу, (м3/с)/м2, qг
=(0,01…0,02) (м3/с)/м2;
δ– концентрация пыли в газе, г/м3 δ = (40…50) г/м3;
qп – допускаемая интенсивность запыления ткани, (г/с)/м2, qп = (0,2…0,3) (г/с)/м2.
В фильтрах с пневматической обратной продувкой часть рукавов периодически отключается на регенерацию ткани. Для таких фильтров расчетная площадь фильтрующей поверхности
Sn ST /(T tn ) |
(3.62) |
где T – период цикла регенерации, с;
T tp tn , |
(3.63) |
где tp – время работы рукава при очистке газа (между операциями регенерации), с;
tп – время регенерации,с.
Техническая характеристика рукавных фильтров приведена в табл.3.11.
Таблица 3.11
Техническая характеристика рукавных фильтров для цементной промышленности
Параметр |
ФР |
ФР |
ФР- |
ФР- |
ФР- |
ФР- |
ФР- |
ФР- |
|
-10 |
-30 |
60 |
|
90 |
112 |
160 |
224 |
280 |
|
|
|
||||||||
Площадь фильтру- |
|
|
|
|
|
|
|
|
280 |
ющей поверхности, |
10 |
30 |
60 |
|
90 |
112 |
160 |
224 |
|
м2 |
|
|
|
|
|
|
|
|
|
Число секций |
1 |
2 |
4 |
|
6 |
6 |
6 |
8 |
10 |
|
|
|
119 |
|
|
|
|
|
Окончание табл. 3.11
Параметр |
ФР |
ФР |
|
ФР- |
ФР- |
ФР- |
ФР- |
|
ФР- |
ФР- |
|
-10 |
-30 |
|
60 |
90 |
112 |
160 |
|
224 |
280 |
Общее число рука- |
18 |
136 |
|
172 |
104 |
56 |
84 |
|
112 |
140 |
вов |
|
|
|
|
|
|
|
|
|
|
Диаметр рукава, мм |
|
|
|
135 |
|
|
220 |
|
|
|
Производитель- |
|
|
|
|
|
|
|
|
|
|
ность м3/ч (при |
–30 |
–45 |
|
–90 |
130– |
–150 |
– |
|
– |
– |
нии ткани 1 – 1,5 |
|
|
||||||||
удельном натяже- |
|
|
|
|
|
|
|
|
|
|
м3/м2 и сопротивле- |
20 |
40 |
|
60 |
90 |
120 |
|
|
|
|
нии фильтра 800 – |
|
|
|
|
|
|
|
|
|
|
1000 H/м2) |
|
|
|
|
|
|
|
|
|
|
Масса, т |
0,3 |
1,0 |
|
1,7 |
2,3 |
9,4 |
12,0 |
|
14,7 |
15,2 |
|
3 |
6 |
|
|
|
|
|
|
|
|
Габаритные разме- |
|
|
|
|
|
|
|
|
|
|
ры, м |
|
|
|
|
|
|
|
|
|
|
Длина |
1,2 |
1,7 |
|
2,8 |
3,8 |
3,8 |
5,3 |
|
6,8 |
6,8 |
Ширина |
0,7 |
1,6 |
|
1,7 |
1,7 |
8,6 |
8,6 |
|
8,6 |
8,6 |
|
5 |
|
|
|
|
|
|
|
|
|
Высота |
1,9 |
3,9 |
|
3,9 |
3,9 |
2,25 |
2,25 |
|
1,25 |
2,25 |
9 |
|
|
120