
Методическое пособие 760
.pdf
4.3. Классификация способов сварки
Ручная дуговая сварка металлическим электродом осуществляется вручную посредством возбуждения дуги между свариваемыми детали и электродом.
Впервые в 1882 г. Н. И. Бенардос предложил сварку угольным электродом, а в 1888 г. Н. Г. Славянов заменил угольный электрод металлическим. Сварка, рекомендуется для индивидуального производства для соединения деталей толщиной 1…60 мм.
Автоматическая электродуговая сварка металлическим электродом под слоем флюса.
Способ разработан институтом электросварки.
АН УССР под руководством академика Е. О. Патона. Сварка осуществляется автоматически специальной установкой и под флюсом в состав его входят шлакообразующие, легирующие и раскислительные составляющие. Возможна сварка деталей толщиной 2…130 мм. Производительность и качество высокое.
Электрошлаковая сварка металлическим электродом отличается от электродуговой тем, что в ней источником нагрева тепло, выделяемое при прохождение электрического тока через шлаковую ванну от электрода к изделию. Тепло расплавляет основной и присадочный материалы. Применяется для сварки стальных деталей толщиной от 30 мм до 1…2 метров станины прокатных станков, прессов, молотов и т.п.
Электрическая монтажная сварка основана на нагреве стыковых концов торцов свариваемых деталей выделяющимся теплом при прохождении через них электрического тока. Способ наиболее рентабельный при массовом производстве.
Электрическая контактная роликовая сварка применя-
ется для получения герметических швов в тонколистовых конструкциях.
Электрическая контактная точечная сварка применяет-
ся для тонколистовых конструкций, в которых не требуется герметичность швов.
29

4.4.Классификация сварных соединений и швов
Взависимости от расположения соединяемых деталей различают следующие виды сварных соединений: стыковые,
внахлѐстку, угловые,тавровые.
Сварные швы стыковых соединений называют стыковыми. Классификация стыковых швов по форме подготовки кромок деталей представлена на рис. 4.1.
Рис. 4.1 Разделка кромок в стыковых сварных соединениях: бесскостная (а, б); V-образная (c, d, е); X-образная (f ); U-образная (g, h)
Сварные швы соединений внахлѐстку, а также угловых соединений и тавровых называют угловыми. По форме подготовки кромок угловые швы бывают: бесскосные, со скосом одной кромки, со скосом двух кромок. По характеру выполнения бывают: односторонние и двусторонние.
По форме сечения угловые швы подразделяются: нормальные, специальные, вогнутые и выпуклые.
30

По расположению шва относительно линии действия силы различают лобовые (рис. 4.2, а), фланговые (рис. 4.2, b) косые (рис. 4.2, с) и комбинированные (рис. 4.2, d).
При значительной разнице толщины соединяемых деталей (для соединений малонагруженных) применяют пробочные, прорезные и проплавные швы (рис. 4.3)
Рис. 4.2 Сварные соединения внахлестку
Рис. 4.3 Сварные швы: пробочные (а); прорезные (б); проплавные (в)
31

4.5. Расчет стыковых сварных швов
Основным требованием при проектировании сварных конструкций является обеспечение равнопрочности шва и соединяемых ими деталей.
Если сварное соединение осуществляется несколькими швами, то эти швы нужно располагать так, чтобы они были нагружены возможно равномернее.
В ряде случаев целесообразнее назначать все размеры шва, а затем выполнять проверочный расчѐт на прочность.
При расчете на прочность стыковых швов утолщение их (наплыв металла) не учитывается. Стыковые швы рассчитываются на растяжение или сжатие (рис. 4.4).
На растяжение:
|
P |
[ ' ] p |
|
P |
|
||
S |
|||
|
|
где: p’, с’, [ ’]p, [ ’]c – соответственно расчетные и допускаемые напряжения в сварном шве при растяжении и сжатии;
S – толщина более тонкой свариваемой детали; ℓ – длина сварного шва.
P |
|
|
|
|
S |
|
P |
||
|
|
|
|
|
|
|
|||
|
|
|
|
|
|
|
|
|
|
|
|
|
|
|
|
|
|
|
|
|
P |
|
P |
|
|
M |
|
M |
|
l |
|
|
|
Рис. 4.4 Схема к расчету стыкового шва
При действии на стыковой шов момента Ми в плоскости к плоскости стыка, расчет шва производят по формуле:
' |
6Ми |
|
[ |
P ] |
|
S 2 |
|||||
|
|
|
|||
|
32 |
|
|

Если же на шов действуют момент Ми и сила P, то
' |
P |
|
6 Ми |
[ |
P ] |
S |
|
S 2 |
|||
|
|
|
|
4.6. Расчет угловых сварных швов
Угловые швы рассчитываются по наименьшему сечению, расположенному в бессикторной плоскости прямого угла поперечного сечения шва.
M |
|
M |
|
|
|
Рис. 4.5 Схема к расчету угловых (валиковых) швов
Расчет угловых швов унифицирован и производится по единым формулам (рис. 4.5).
'ср |
P |
[ ' ]ср . |
|
|
|||
0,7 K |
|||
|
|
Если угловой шов нагружен моментом Ми, то:
'ср |
Ми |
[ ' ]ср . |
|
Wc |
|||
|
|
0,7 K 2
Wc 6
33
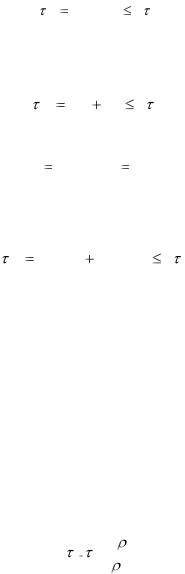
Тогда
'ср |
6 Ми |
[ ' ]cр |
|
0,7 K 2 |
|||
|
|
При нагружении простого углового шва моментом М и силой Р условие прочности имеет вид:
'cp |
M |
|
P |
[ |
' ]cp |
||
|
|
|
|||||
Wc |
|
Fc |
|||||
|
|
|
|
|
|
||
|
|
|
|
|
0,7 K 2 |
||
Fc 0,7 K; Wc |
|
|
|
, |
|||
|
|
6 |
|||||
|
|
|
|
|
|
|
где Wc – момент сопротивления опасного сечения шва. Окончательно:
'cp |
P |
|
6M |
[ ' ]cp . |
|
|
|
||
0,7 K |
|
0,7 K 2 |
||
|
|
|
При более сложных конструкциях сварных швов при их расчете необходимо правильно учесть все параметры шва и величины действующих нагрузок.
Пробочные, прорезные и проплавные швы также рассчитываются на срез.
4.7. Уточненный расчет комбинированного сварного шва
Принимают, что привариваемый элемент стремится повернуться вокруг центра тяжести (ц.т.) площади сечения шва (рис. 4.6). Тогда напряжения сдвига η в отдельных точках шва будут пропорциональны радиусам-векторам, проведенным из центра тяжести и направлены перпендикулярно этим радиусам:
max |
|
, |
|
||
|
|
|
|
max |
где ηmах – максимальное напряжение в наиболее удаленной точке с радиусом ρmах.
34

Момент, воспринимаемый сечением сварных швов (по аналогии с кручением), равен
F |
|
|
F |
|
|
|
M |
dF |
max |
|
2 dF |
max |
J |
|
|
|||||
0 |
|
max 0 |
|
max |
Jρ – полярный момент инерции шва Отсюда:
|
M |
max |
[ |
/ ] |
|
|
|
|
|||
max |
|
J |
|
|
ср |
|
|
|
|
|
Напомним, что Jρ =Jх + Jy
y |
|
|
|
τ dF |
ρ |
ρmax |
|
|
|
|
|
|
|
|
x |
|
|
h |
М |
|
|
|
|
с1 |
с2 |
к |
|
|
|
||
|
|
|
|
|
а |
|
|
Рис. 4.6 Схема к уточненному расчету комбинированного сварного шва
Таблица 4.1 Допускаемые напряжения для сварных швов
|
Допускаемые напряжения |
||
Вид сварки |
растяжение |
|
/ |
|
[σ/]p |
|
сдвиг [τ ]ср |
Автоматическая, ручная Э42А |
[σ]p |
|
0,65 [σ]p |
Э 50А, в среде защитного газа |
|
||
|
|
|
|
Ручная электродами обычного |
0,9 [σ]p |
|
0,6 [σ]p |
качества |
|
||
|
|
|
|
Ориентировочно [σ]p ≈ (0,4…0,5) σТ |
|
||
35 |
|
|
|
5. ШПОНОЧНЫЕ И ШЛИЦЕВЫЕ СОЕДИНЕНИЯ
5.1. Типы шпоночных соединений
Шпонка – деталь, устанавливаемая в пазах двух соприкасающихся деталей и препятствующая относительному повороту или сдвигу этих деталей. Шпонки служат для передачи крутящего момента от вала к ступице и наоборот. Шпонки широко применяются в машиностроении. Шпоночные соединения делятся на ненапряжѐнные и напряжѐнные.
Сборка и разработка ненапряжѐнного соединения (с призматической шпонкой) не требует приложения значительного усилия к сопрягаемым деталям. Детали, посаженные на призматическую шпонку, должны иметь крепления, предупреждающие их осевое перемещение.
Напряжѐнное состояние получается в результате предварительной затяжки клиновой шпонки при отсутствии рабочих нагрузок. Такое соединение может передавать не только крутящий момент, но и осевую силу (в одном направлении).
Шпонки всех основных типов стандартизованы и их размеры выбираются по ГОСТ 23360-78 (призматические); ГОСТ 24071-80 (сегментные); ГОСТ 24068-80 (клиновые).
Материалом для шпонок обычно являются углеродистые стали марок ст.5; ст.6; сталь 45 с пределом прочности не ниже 60 Н мм2. Легированная сталь для шпонок применяется редко. Целесообразно, чтобы материал шпонки был менее прочным, чем материал вала и ступицы.
Допускаемые напряжения для шпоночных соединений обуславливаются характером нагрузки. Причиной разрушения этих соединений чаще всего бывает деформация смятия, на которую следует обращать особое внимание при выборе допускаемых напряжений. Допускаемые напряжения принимают:
- |
при стальной ступице [ζ]см ≈ 100…120 МПа; |
- |
при чугунной ступице [ζ]см ≈ 50…60 МПа. |
|
При динамическом нагружении соединения (резкие уда- |
ры) допускаемые напряжения следует понизить на 25…40%.
36

Допускаемые напряжения среза принимают в пределах [η]ср ≈ 60…90 МПа. Более точные значения допускаемых напряжений приведены в табл. 5.1.
Таблица 5.1 Допускаемые напряжения смятия [ζ]см МПа
Тип |
Условия |
Твердость поверхности |
|
соединений |
эксплуатации |
до 350 НВ |
свыше 40 HRC, |
Неподвижное, |
а |
35-50 |
40-70 |
с осевой |
б |
60-100 |
100-140 |
фиксацией |
в |
80-120 |
120-200 |
Подвижное без |
а |
15-20 |
20-35 |
нагрузки |
б |
20-30 |
30-60 |
|
в |
25-40 |
40-70 |
Подвижное под |
а |
– |
3-10 |
нагрузкой |
б |
– |
5-15 |
|
в |
– |
10-20 |
Призматические шпонки (рис. 5.1) выполняют прямоугольного сечения с соотношением сторон h : b ≈ 1 : 1 для валов малых диаметров и 1 : 2 для больших диаметров вала.
Рис. 5.1 Соединение призматической шпонкой
37

Рабочими у призматической шпонки являются более узкие, боковые грани. Шпонка погружена в паз вала на глубину ≈ 0,6 h, а в радиальном направлении между шпонкой и ступицей предусмотрен зазор.
а) Шпонки призматические (рис. 5.2):
-обыкновенные со скруглѐнными или плоскими торцами;
-направляющие (с дополнительным креплением на валу винтами) со скруглѐнными или плоскими торцами.
б) Скользящие:
-шпонки призматические с углубленной посадкой на вал (нормаль станкостроения);
-шпонки сегментные.
Шпонки для напряжѐнных состояний: А. Шпонки клиновые (с уклоном 1: 100):
-врезные со скруглѐнными и плоскими торцами ГОСТ
8791-68;
-врезные с головкой забивные – ГОСТ 8792-68.
Б. На лыске с головкой ГОСТ 8793-68. В. Фрикционные.
Г. Тангенциальные.
Рис. 5.2 Виды наиболее часто применяемых шпонок: призматические с плоскими торцами (а) и с закругленными торцами (б), сегментные (в); цилиндрические (г)
38