
Методическое пособие 760
.pdf
Концентрация нагрузки по длине зуба в основном вызывается деформациями червяка, вала колеса и др.
Теоретический коэффициент Kβ выражается следующей зависимостью в условиях отсутствия приработки
3
K 1 Z2 ,
где: θ – коэффициент деформации червяка зависящий от Зубья червячного колеса способны прирабатываться. При
постоянной нагрузке наблюдаются полная приработка и концентрация напряжений отсутствует. При переменной нагрузке частичная приработка и зубья получают бочкообразность. Тогда коэффициент К определится:
3
K 1 Z2 1 x ,
|
M |
ср |
|
M n |
|
x |
|
|
|
i iоо |
, |
|
|
|
|||
|
M max |
|
M max N |
N Tu nu ; nuоо Tu nu ,
где Mu, Tu, u – соответственно: крутящий момент, время работы в часах и частота вращения (об/мин) при режиме "u".
Mmax – максимальный длительно действующий момент. При постоянной нагрузке x = 1 и Kβ = 1, коэффициент KV
определяется качеством изготовления и скоростью вращения. При точном изготовлении и V ≤ 3 м/c принимают КV = 1. Обычно Kβ = 1 … 1,3.
Допускаемые номинальные напряжения изгиба для бронзовых червячных колес при работе зубьев одной стороны (нереверсивная передача) определяется зависимостью:
|
|
106 |
, |
|
u |
n |
|
NE |
|
|
|
|
|
где: [ζ]u – исходные допускаемые напряжения при 106 или 107 циклов нагружений:
179

0 |
0,25 T 0,08 B , |
u |
здесь: ζТ и ζВ – расчетные пределы текучести и прочности бронзы при растяжении.
Например, для Бр ОФ 10-1 при отливе в песок ζТ = 120
МПа и ζВ = 200 МПа.
NE – эквивалентное число циклов нагружений:
|
M i |
9 |
|
NE 60 |
niTi , |
||
M max |
|||
|
|
здесь: Mu, nu, Tu – момент, частота вращения колеса в мин. и время работы в часах при режиме “u”.
Mmax – максимально длительно действующий момент, по которому ведется расчет.
При реверсивной передаче, когда зубья работают обеими сторонами, формула принимает вид:
|
0 |
9 |
106 |
, |
Rn |
Rn |
|
NE |
|
|
|
|
|
где: [ζ]Rn = 1,6 ζb.
Допускаемые контактные напряжения для червячных колес из бронз средней прочности выбирают из условия сопротивления материала поверхностной усталости.
|
|
|
|
|
|
0 |
8 |
107 |
, |
|
|
|
|
|
H |
|
H |
NE |
|||
|
|
|
|
|
|
|
||||
|
|
|
|
|
|
|
|
|
|
|
где: |
0 |
0,75...0,9 |
b – допускаемое исходное напряжение |
|||||||
H |
||||||||||
при 107 циклов нагружения; |
|
|
|
|
|
|||||
|
- эквивалентное число циклов нагружений: |
|||||||||
|
|
|
|
|
|
4 |
|
|
|
|
|
|
|
|
|
|
Mu |
|
|
7 |
|
|
|
N |
E |
60 |
|
|
|
n T |
25 10 . |
|
|
|
|
|
|
||||||
|
|
|
|
M max |
u u |
|
||||
|
|
|
|
|
|
|
|
|||
|
|
|
|
|
|
180 |
|
|
|

18.8. Тепловой расчет червячных передач
Червячные передачи работают с большим тепловыделением. Если масло нагреется до температуры, превышающей допустимую [t]max ≈ 95°, то оно теряет защитную способность и приводит к опасности заеданий в передаче. Расчет проводят на основе теплового баланса, т.е. приравнивают тепловыделения теплоотдаче.
Количество тепла (ккал/час), выделяющееся в непрерывно работающей червячной передаче равно:
|
Q |
|
860 1 |
N1 . |
|
|||
Максимальное количество тепла, отводимое корпусом |
||||||||
передачи находится из соотношения: |
|
|
|
|||||
Q |
K |
T |
[ t ] |
max |
t |
0 |
S 1 |
, |
1max |
|
|
|
|
|
где: η – КПД червячной передачи,
N1 – передаваемая мощность, KBт, KT – коэффициент теплоотдачи
KT = 10 …16 ккал/м2
t0 – температура окружающего воздуха, °С,
S – свободная поверхность охлаждения корпуса передачи (плюс 50 % поверхности ребер), м2.
ψ – коэффициент, учитывающий теплоотвод в фундаментную плиту или раму ψ ≈ 0,3.
Приравнивая левые части уравнений /на основе теплового баланса: Q = Q1max, после преобразований можно получить рабочую температуру масла или мощность, длительно передаваемую передачей при условии, что температура масла в редукторе не превышает допустимой:
t t |
|
860 1 N1 |
, |
||
0 |
KT |
1 |
|||
|
|
||||
|
|
|
или:
181

N1 |
KT t max |
t0 |
1 |
. |
860 1 |
|
|
||
|
|
|
|
Если t > [t]max, т.е. Q > Qmax, то должен быть предусмотрен отвод избыточного тепла Q – Q1max. Это достигается оребрением редуктора, искусственной вентиляцией, змеевиками с охлаждающей жидкостью в масляной ванне и др. охлаждающими устройствами.
Если передача работает с перерывами и время непрерывной работы и паузы малы по сравнению с временем разогрева передачи до установившейся температуры, то расчет можно вести по тем же зависимостям, что и при постоянном режиме, но по среднему количеству тепла, выделяющемуся за единицу времени, тогда, в формулы вместо Q подставляют
Q Tp ,
Tобщ
где: ТР – время работы, Тобщ – общее время: время работы (Тр) плюс время пауз за
один цикл работы передачи или, например, за 1 час.
Для передач, работающих с длительными остановками, во время которых они успеют остыть, расчетом определяют время "Т" непрерывной работы до приобретения маслом предельно допустимой температуры.
19.ПОНЯТИЕ О СИСТЕМЕ ДОПУСКОВ И ПОСАДОК
19.1.Понятие о взаимозаменяемости
При производстве, эксплуатации и ремонте изделий особое значение имеет принцип взаимозаменяемости. Взаимозаменяемость – это свойство конструкции, составной части изделия, обеспечивающее возможность ее применения вместо другой без дополнительной доработки… Патроны, болты, чайки – примеры полной взаимозаменяемости.
182
Имеет место также групповая взаимозаменяемость. При групповой взаимозаменяемости изготовленные детали сортируют по размерам на несколько групп (допуски деталей в каждой группе уменьшаются). Затем производят сборку изделия из деталей в пределах одной группы. Такая групповая взаимозаменяемость (селективная сборка) широко применяется в шарикоподшипниковой промышленности. При сборке изделий высокой точности этот метод является единственно экономически целесообразным методом обеспечения требуемой точности.
Метод регулирования предполагает сборку с регулирование положения или размеров определенной детали, называемой компенсатором.
Взаимозаменяемость базируется на стандартизации. Допуски и посадки нормируются стандартом ЕСДП – «Единая система допусков и посадок» (ГОСТ 25346-82). Допуски и посадки указывают на чертежах. На их основе разрабатывают технологические процессы изготовления и контроля.
19.2. Допуски размеров, посадок
На рабочем чертеже в первую очередь проставляют габаритные, присоединительные, посадочные, номинальные размеры, предельные отклонения размеров, условные обозначения полей допусков и квалитеты.
Номинальный размер определяет конструктор расчетным или конструктивным путем и назначает из нормального ряда линейных размеров (ГОСТ 6636-69), который ограничивает число применяемых размеров (качество режущего и мерительного инструмента), удешевляя производство.
Обработать деталь точно по номинальному размеру невозможно из-за многочисленных погрешностей, влияющих на процесс обработки. Размеры обработанной детали всегда отличаются от номинального, по этому их ограничивают двумя предельными размерами: на и большим Dmax (отв); dmax (вал) и наименьшим Dmin; dmin (вал). Деталь является годной, если ее
действительный размер:
183

dmin d dmax
На чертеже вместо предельных размеров указывают номинал и два предельных отклонения
d |
0 ,021 |
мм. |
D |
0 ,02 |
0 ,002 |
0 ,005 |
Отклонение – это алгебраическая разность между размером (действительным, предельным) и номиналом.
Одно из предельных отклонений называют верхним ЕS (es), второе – нижним EI(ei) [отв. (вал)].
0 |
TD |
|
|
|
|
|
|
|
TD |
|
|
|
|
|
|
|
|
|
|
|
|
|
|
|
|
|
|
|
|
||||
|
|
|
|
|
|
|
|
|
|
|
|
|
|
|||
|
|
|
|
|
|
|
|
|
|
|
|
|
||||
|
|
|
|
|
|
|
|
|
|
|
|
|
|
|
|
|
|
|
|
|
|
ES |
|
|
|
|
|
|
|
|
TD |
|
|
|
|
|
|
|
|
|
|
|
|
|
|
|||||
|
min |
|
max |
|
|
) |
EI |
|
|
|
|
|
|
|
|
|
|
|
|
|
|
|
|
|
|
|
|
|
|
||||
|
|
|
|
|
|
|
|
|
|
|
|
|
|
|||
|
|
|
|
|
|
|
|
|
|
|
|
|
|
|||
|
|
|
|
|
|
min |
|
|
|
max |
|
|||||
|
|
|
|
|
|
|
|
|
|
|||||||
|
|
|
|
|
|
|
|
|
|
|||||||
|
D |
|
D |
|
D |
|
номинал |
D |
|
|
D |
|
||||
|
|
|
|
|
|
|
( |
|
|
|
|
|
|
|
|
|
|
|
|
|
|
|
|
|
|
|
|
|
|
|
|
|
|
|
|
|
|
|
|
|
|
|
|
|
|
|
|
|
|
|
|
|
|
|
|
|
|
|
|
|
|
|
|
|
|
|
|
ES |
TD |
|
|
EI
Нулевая линия
Рис. 19.1. Расположение полей допусков отверстия (в обозначении вала используются строчные буквы)
Зону ограниченную верхним и нижним предельными отклонениями называют полем допуска. Поле допуска характеризуется не только величиной, но и положением относительно номинального размера (нулевой линии). Поле допуска детали может располагаться выше, ниже, симметрично и не симметрично относительно нулевой линии.
Характер соединения деталей определяется взаимным расположением полей допусков деталей и называется посад-
184

кой. Различают посадки трех типов: с зазором, с натягом и переходные.
|
|
TD |
|
|
|
|
|
|
||
|
|
|
|
|
|
|
|
|
|
|
|
|
EI=0 |
|
|
|
|
ES |
|
|
|
0 |
|
|
|
|
|
|
0 |
|
||
|
|
|
|
|
|
|
|
|
||
|
|
|
|
es |
|
|
|
|
||
|
|
|
|
|
|
|
ei |
max |
|
|
|
D(d) |
|
|
|
|
|
S |
|
||
|
|
|
|
|
|
|
||||
|
|
Td |
min |
|
|
|||||
|
|
S |
|
|
||||||
|
|
|
|
|
Td |
|
|
|
|
|
es
0
D(d)
min |
|
max |
N |
ei |
N |
TD
Рис. 19.2. Соединение деталей с зазором (а), с натягом (б)
Зазор S – разность размеров отверстия и вала до сборки, когда размер отверстия больше размера вала.
Посадка с зазором обеспечивает гарантированный зазор в соединении (подшипники скольжения), когда поле допуска отверстия расположено над (выше) поля допуска вала. Посадка характеризуется наибольшим Smax и наименьшим Smin зазорами.
Натяг N – разность размеров вала и отверстия, когда вал больше отверстия. При посадке с гарантированным натягом поле допуска отверстия расположено под полем допуска вала (со-
185

единения с натягом, запрессовка и температурная сборка) – характеризуется максимальным Nmax минимальным натягом Nmin.
Переходная посадка возникает, когда поля допусков перекрываются частично или полностью. В этом случае в соединении возможны как зазоры, так и натяги.
Чем меньше поля допусков и колебания зазоров и натягов, тем выше точность посадки.
Td
0
D(d) |
|
TD |
|
max |
|
|
|||
|
|
N |
||
|
|
|
||
|
|
|
|
|
Smax
Рис. 19.3. Соединение деталей по переходной посадке
19.3. Квалитеты
Класс (уровень) точности в ЕСДП называется квалитетом. Всего стандартом установлено 19 квалитетов.
01, 0,1 – предусмотрены для оценки точности плоскопараллельных концевых мер длины;
2, 3, 4 – для оценки гладких калибров – пробок и калибров – скоб;
5,6 – высокоточные соединения (авиация, вертолеты, прецизионные станки);
7,8 – наиболее распространены в машиностроении; 9 – детали ПТЧ, с/х машины, текстильные; 10-12 – соединение литых деталей; 13-17 – для свободных размеров.
IT6 – допуск квалитетов.
186
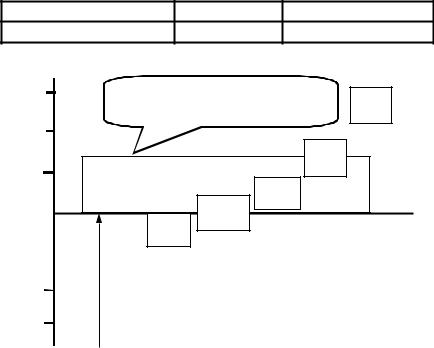
19.4. Система отверстия и система вала
Посадки в системе отверстия – получают с одним основным отверстием, поле допуска которого (для данного квалитета) постоянно для всей совокупности посадок.
Таблица 19.1 Наименование полей допусков валов в системе отверстия
a b c cd d e ef f fg |
h js k m n |
|
p r s t u v x y z |
|
Посадки с зазором |
Переходные |
Посадки с натягом |
||
Поле допуска основного отверстия H. |
|
|||
мкм |
|
|
|
|
+30 |
Основное отверстие, |
s6 |
||
|
|
поле допуска |
|
|
|
|
|
|
|
+20 |
|
|
|
|
+10 |
|
|
|
n6 |
|
|
|
19.1. ES |
|
|
H |
|
|
|
|
k6 |
|
=+15 |
|
|
|
|
||
0 |
|
js6 |
|
|
|
h6 |
|
|
-10 |
|
D(d)=10 |
|
|
|
||
|
|
f6 |
|
|
|
|
|
-20 |
|
|
|
|
|
|
|
-30 |
|
|
|
Рис. 19.4. Образование посадок в системе отверстия Отверстие – основной элемент системы.
1)Посадки получают соединением различных валов с ос-
новным отверстием.
2)Поле допуска основной детали соединения всегда на-
правлено «в тело» этой детали.
В практике машиностроения предпочтение (размеры более 1 мм) отдается системе отверстия, поскольку его точно изготовить и изменить значительно труднее и дороже, чем вал того же размера.
187

В тех случаях, когда посадку экономически выгоднее получить за счет различных размеров отверстия при постоянном поле допуска вала, применяют систему вала.
–подшипники качения в корпус (стандартные детали)
–шпонки призматические и сегментные (шпонка одна, а посадки на вал и втулку разные за счет полей допусков вала и втулки).
мкм
+30
+20
+10
0
-10 -20 -30
D(d)=10
F7
|
|
|
H7 |
|
|
|
|
|
|
|
|
|
|
|
|
|
|
|
|
|
|
|
|
|
|
|
|
|
|
|
|
|
|
|
|
|
|
|
|
|
|
|
|
|
|
|
|
|
|
es =0 |
|
h6 |
|
|
|
Js7 |
|
|
|
|
|
|
|
|
|
||
|
|
|
|
|
|
|
|
|
|
|
|
|
|
|||
|
|
|
|
|
|
|
|
M7 |
|
|
|
|
|
ei = -9 |
||
|
|
|
|
|
|
|
|
|
|
|
||||||
|
|
|
|
|
|
|
|
|
|
|
|
|
|
|||
|
|
|
|
|
|
|
|
|
|
|
|
|
|
|
||
|
|
|
|
|
|
|
|
|
|
|
N7 |
|
|
|
|
|
|
|
|
|
|
|
|
|
|
|
|
|
|
|
|
|
|
|
|
|
Основной вал, |
|
|
|
S7 |
|
||||||||
|
|
|
|
поле допуска |
|
|
|
|
|
|||||||
|
|
|
|
|
|
|
||||||||||
|
|
|
|
|
|
|
|
|
|
|
|
|||||
|
|
|
|
|
|
|
|
|
|
|
|
|
|
|
|
|
|
Рис. 19.5. Образование посадок в системе вала |
– |
для отверстий малого диаметра (d 1 мм), когда вал |
точно обработать труднее, чем отверстие |
|
– |
для длинных валов, особенно, когда на отдельных |
участках вала одного номинального размера необходимо поместить несколько деталей с разными посадками.
Таблица 19.2 Наименование полей допусков отверстий в системе вала
A B C C D D E F G H Js K M N P R S T U V X Y Z
Посадки с зазором Переходные Посадки с натягом
188