
Методическое пособие 502
.pdf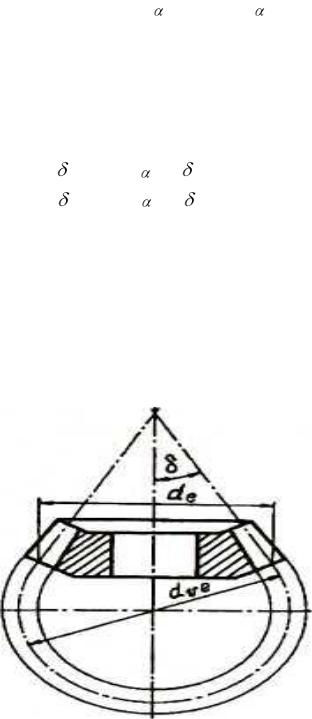
Нормальную силу давления Fn одного зуба на другой и ее состав-
ляющие Ft (окружная, тангенциальная) и F 'r силы определяют по формулам:
Ft = 2 T/d; Fn = Ft /cos ; F 'r =Ft tg , |
(57) |
где Т — вращающий момент, Н*мм;
— угол зацепления, град.
При этом для шестерни указывают индекс 1, а для колеса — 2.
Силу Fr' для шестерни можно разложить на радиальную Fr1 и осевую Fal силы, связанные зависимостями:
F |
rl |
= |
F ' cos |
1 |
= F |
|
*tg |
cos |
1 |
; |
|
|
r |
tl |
|
|
|
||||
F |
al |
= |
F ' cos |
1 |
= F |
tl |
*tg |
cos |
1 |
; |
|
|
r |
|
|
|
|
Рассматривая зацепление зубьев колеса и шестерни, можно записать:
Ft1 = Ft2; Frl = Fa2; Fal = Fr2. |
(58) |
Прямозубые конические колесо и шестерня (как и косозубые цилиндрические) приводят к эквивалентному колесу (шестерне), используя это в дальнейшем при прочностных расчетах.
Рис. 8. Схема для приведения прямозубого конического колеса (шестерни) к эквивалентному
31

Диаметры эквивалентных колеса и шестерни (рис. 8) определяют по формулам:
dve1 = de1/cos 1 ; dve2 = de2/cos 2 |
(59) |
Приведенные (фиктивные) числа зубьев определяют точно так же, как и для косозубой цилиндрической передачи:
z v1 = z1 /cos 1 ; z v2 = z2 /cos 2 |
(60) |
Взависимости от взаимного расположения шестерни и колеса нагрузка от одного зуба к другому может передаваться по-разному. Оптимальным является случай, когда нагрузка передается по всей линии контакта, т. е. по всей длине зуба.
Впроизводственных условиях это достигается регулировкой конической прямозубой передачи по пятну контакта. Перед регулировкой зубья шестерни и колеса устанавливают визуально так, что бы они находились в зацеплении на всю длину, и устраняют зазор в конических роликовых подшипниках. На поверхность 5 зубьев шестерни наносят краску
ипроворачивают вал шестерни на угол, соответствующий выходу зубьев из зацепления. После этого на зубьях колеса видны пятна контакта. Можно также использовать тонкую: фольгу (кальку), пропускаемую через зубья, находящиеся в зацеплении.
При правильной регулировке пятно контакта должно располагаться, как показано на рисунке 9а,б. Без нагрузки и при малой Нагрузке пятно контакта располагается со стороны малого торца (см. рис. 9, а), при полной нагрузке — по всей длине середины зуба (см. рис. 9, б).
Рис. 9. Варианты расположения пятна контакта зубьев в прямозубой конической передачи
32
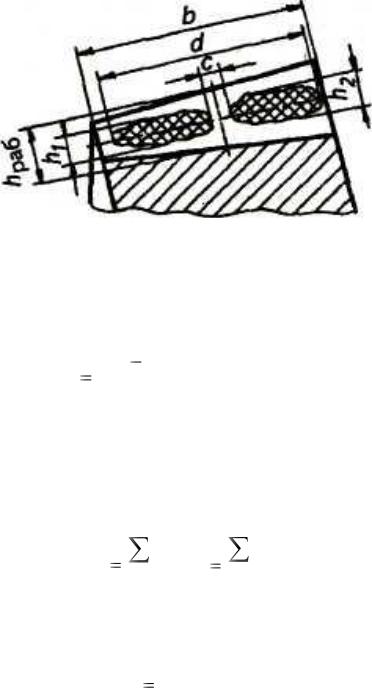
Если пятно контакта расположено на вершине зуба (рис. 9, в), то шестерню необходимо придвинуть к колесу (рис. 9, ж), если у основания зуба (рис. 9, г), то ее нужно отодвинуть от колеса. В случае расположения пятна контакта на узком конце зуба (рис. 9, д) колесо следует отодвинуть от шестерни, а на широком конце зуба (рис. 9, е) — придвинуть к шестерне.
Пятно контакта замеряют по длине и высоте зуба (рис. 10).
Рис. 10. Размеры пятна контакта прямозубой конической передачи
Пятно контакта по длине зуба — это отношение расстояния, между крайними точками следов прилегания за вычетом разрывов, превосходящих значение модуля, к полной высоте зуба, т. е.:
Kl |
dср |
|
cср |
|
|
|
|
|
, |
(61) |
|
|
b |
|
|||
|
|
|
|
|
где dср — среднее расстояние между крайними точками пятна контакта для пяти зубьев, мм;
сср — средний разрыв между пятнами контакта для пяти зубьев, мм; b — длина зуба, мм.
Средние значения замеров на 5 зубьях:
d |
|
|
|
d |
; cср |
c |
|
|||
ср |
|
|
|
|
|
|
(62) |
|||
|
|
5 |
|
5 |
|
|||||
|
|
|
|
|
|
|
|
|
||
Пятно контакта по высоте зуба — это отношение высоты пятна |
||||||||||
контакта на всей длине к рабочей высоте зуба в среднем сечении: |
|
|||||||||
|
|
K h |
|
|
hср |
*100 , |
(62) |
|||
|
|
|
|
|
||||||
|
|
|
|
|
hраб |
|
|
|
где hср = (h1 + h2)/2 — средняя высота пятна контакта, мм; hраб — рабочая высота зуба в среднем сечении, мм.
33
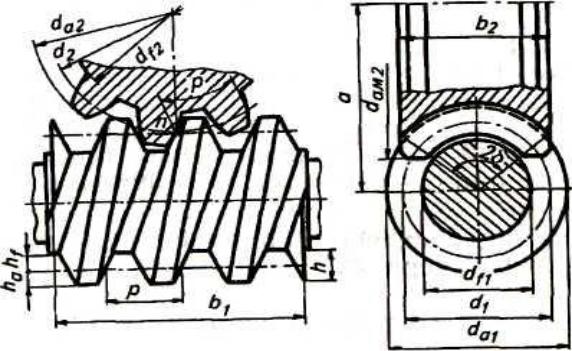
Средние значения замеров на 5 зубьях: |
|
hср = ∑h/10 |
(64) |
Если разрывов в пятне контакта нет (с = 0), то в знаменателе формулы (64) вместо 10 нужно ставить число зубьев 5.
Сборку и регулировку считают удовлетворительной, если размеры пятен контакта по высоте зуба:
не менее 40% — для 5...8 квалитетов (1-й и 2-й классы точности); 30% —для 8, 9 квалитетов (3-й класс точности); 20% — для 11 квалитета (4-й класс точности).
По длине зуба:
не менее: 65% — для 5...8 квалитетов; 50% — для 8...11 квалитетов.
3.4.Червячная передача
Вчервячных передачах угол между осями червяка и колеса обычно составляет 90°. По форме червяки изготовляют цилиндрическими и глобоидными (в рулевом управлении тракторов и автомобилей), а по профилю зуба в осевом сечении — прямолинейными (архимедов червяк) и эвольвентными. Конволютные червяки имеют прямолинейный профиль зуба
внормальном к виткам червяка сечении. Профиль зубьев колеса с архимедовыми, эвольвентными и конволютными червяками эвольвентный.
Рис. 11. Геометрия червячной передачи
34
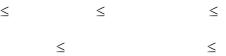
Для червячной передачи без смещения (рис. 11) характерны
следующие геометрические зависимости. |
|
Межосевое расстояние: |
|
а = (d1 + d2)/2, |
(65) |
где d1 — диаметр начальной окружности червяка, мм;
d2 — диаметр начальной окружности колеса по среднему сечению, мм.
Модуль червячной передачи: |
|
m=d2/z2=p/П, |
(66) |
где z2 — число зубьев колеса; р — шаг зацепления, мм.
Чтобы исключить подрезание зубьев, z2 должно быть больше или равно
28.
Для червяка введено понятие коэффициента диаметра червяка,
который показывает число модулей в делительной окружности: |
|
q =d1 /m. |
(67) |
Значение q стандартизировано (ГОСТ 19672-74). Рекомендуемое число заходов червяка:
z1 = 1 при передаточном числе u 30; z1 = 2 при u = 15...30;
z1 = 4 при u = 8...15.
Высота зубьев колеса и витков червяка: |
|
h = 2,2m; ha = m; hf = 1,2/m |
(68) |
Диаметры выступов и впадин червяка: |
|
da1 = d1 + 2m; df1 = d1 – 2,4m |
(69) |
Диаметры выступов и впадин колеса: |
|
da2 = d2 + 2m; df2 = d2 – 2,4m |
(70) |
У колеса кроме диаметров в среднем сечении рассматривают наружный диаметр daM2, который так же, как и идейна колеса b2, зависит от числа заходов червяка. При угле обхвата червяка колесом 25 = 100° (в силовых передачах) b2 и daM1 выбирают из соотношений:
z1 |
1 |
2 |
4 |
daM2 |
da2 +2m |
da2+ 1,5m |
da2 +m |
b2 |
0,75da1 |
0,67da1 |
|
|
|
35 |
|
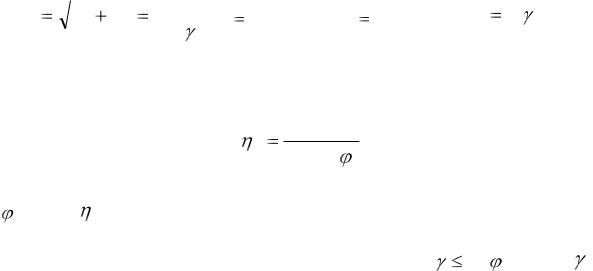
Длина нарезанной части червяка (мм):
при z1 = 1 и z1 = 2 b1= (11 + 0,06z2)m; при z1 = 4 b1 = (12,5 + 0,09z2)m.
Передаточное число червячной передачи определяют в зависимость от числа заходов червяка:
u = z2/z1 или i = n1/n2. |
(71) |
В силовых передачах u = 10...80.
Скорость скольжения VCK, направленную по касательной к винтовой линии червяка, и окружные скорости V1 червяка и V2 колеса (рис. 4.12) рассчитывают по формулам:
|
|
|
|
v1 |
|
Пd n |
|
Пd |
|
n |
|
|
||
|
2 |
2 |
|
|
2 |
2 |
|
|||||||
vcк |
v1 |
v2 |
|
|
; v1 |
1 |
1 |
|
; v2 |
|
|
; |
||
|
cos |
|
|
|
|
|
|
|
||||||
|
60 *1000 |
60 *1000 |
||||||||||||
|
|
|
|
|
|
|
где — угол подъема винтовой линии червяка, град.
Коэффициент полезного действия червячной передачи: tg
ч tg( )
С увеличением числа заходов z1 увеличиваются угол
v1 |
tg |
(72) |
|
v2 |
|||
|
|||
|
|
(73)
и КПД. При
имеем ч =0, т. е. передача движения от колеса к червяку невозможна. Это явление используется в талях с червячным редуктором или ручных талях
без тормозных механизмов. При этом рекомендуется |
0,5 . Угол |
практически всегда менее 30°. |
|
На рисунке 12 показано взаимное положение вектора скорости vCK и контактных линий. На входе червяка в зацепление с зубьями колеса контактные линии и вектор vCK почти совпадают, и условия смазки здесь затруднены. На выходе из зацепления эти линии почти перпендикулярны, поэтому смазочный материал хорошо затягивается между зубьями. Опыты показали, что если часть зубьев колеса со стороны входа червяка в зацепление срезать резцом, то склонность передачи к заеданию уменьшается. На практике это не применяют, так как при реверсировании получается обратная картина.
Из схемы на рисунке 12 видно соотношение сил в червячной передаче:
Ft1 = Fa2 = 2T1/d1; Ft2 = Fa1 = 2T2/d2; Frl = Fr2, |
(74) |
где Ft, Fa, Fr — соответственно окружные, осевые и радиальные силы, Н.
Червячная передача по своим конструктивным особенностям весьма чувствительна к неточностям изготовления и сборки. Неправильная сборка может резко ухудшить нормальную работу передачи, в результате чего по-
36
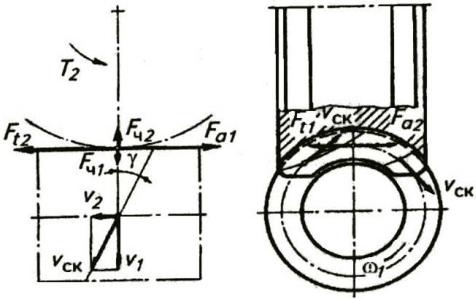
вышаются нагрев и интенсивность изнашивания деталей, снижается КПД. Поэтому сборку червячной передачи надо выполнять особенно тщательно.
Рис. 12. Скорости и силы зацепления
Нормальная работа передачи обеспечивается при соблюдении следующих условий:
1)заданного расположения осей червяка и червячного колеса (межосевое расстояние, возможный перекос валов);
2)требуемого бокового зазора между витками червяка и зубьями червячного колеса;
3)надлежащего контакта прилегающих профилей;
4)легкости хода передачи (свободное вращение).
5)заданного расположения осей червяка и червячного колеса (межосевое расстояние, возможный перекос валов);
6)требуемого бокового зазора между витками червяка и зубьями червячного колеса;
7)надлежащего контакта прилегающих профилей;
8)легкости хода передачи (свободное вращение).
37
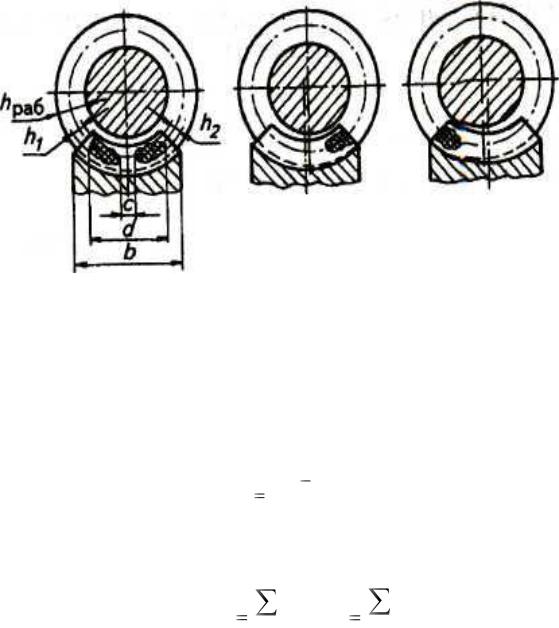
Первые два условия соблюдают при проектировании и изготовлении передачи, задавая допуски на межосевое расстояние, перекосы валов и другие параметры с таким расчетом, чтобы боковой зазор между витками червяка и зубьями червячного колеса был в допустимых пределах в зависимости от заданного квалитета.
Вторые два условия зависят от точности монтажа и существенно влияют на равномерность изнашивания зубьев колеса и легкость хода. Надлежащий контакт прилегающих поверхностей витков червяка и зубьев колеса проверяют по отпечатку краски на рабочей поверхности зубьев колеса и по расположению отпечатков оценивают правильность сборки передачи.
Рис. 13. Расположение пятна контактов зуба
Исходя из геометрии зацепления червячной передачи осевая линия, проходящая через центр червяка, должна совпадать с впадинами зубьев колеса (рис. 13, а). Если колесо при монтаже смещено влево (рис. 13, б) или вправо (рис. 13, в), то пятно контакта располагается с одной стороны зубьев. Его замеряют по длине и высоте зуба. Пятно контакта по длине зуба [см. формулу (61)]:
Kl |
dср |
cср |
*100 |
|
b |
||
|
|
|
В практических условиях замеры выполняют не менее чем на 5 зубьях. Тогда средние значения замеров (мм):
d |
|
d |
|
cср |
c |
|
ср |
|
; |
|
|||
5 |
5 |
|||||
|
|
|
|
Для приработанной передачи с = 0.
38
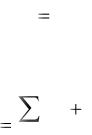
Пятно контакта по высоте зуба [см. формулу (63)]:
K h |
hcp |
||
|
|
*100 |
|
h |
|
||
|
раб |
Среднее значение (мм):
hcp |
(h1 |
h2 ) |
|
|
|
(75) |
|
10 |
|
||
|
|
|
Рабочая высота зуба:
hраб = 2m,
где m — модуль, мм.
Если в пятне контакта разрывов нет (с = 0), то h1 = h2 = hmax и в формуле (75) вместо 10 ставят цифру 5. Положение червячного колеса регулируют
прокладками между крышками конических подшипников.
Сборку и регулировку считают удовлетворительной, если размеры пятен контакта по высоте зубьев не менее 50 %, а по длине зубьев не менее:
75 % — для 5 квалитета (1-й класс точности); 65% — для 6 и 7 квалитетов (2-й класс точности); 50% — для 8 и 9 квалитетов (3-й класс точности); 35 % — для 11 квалитета (4-й класс точности).
39
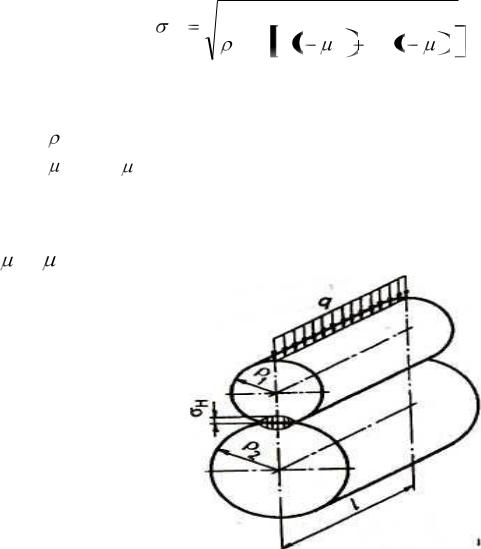
4.РАСЧЕТ ПЕРЕДАЧ НА КОНТАКТНУЮ ПРОЧНОСТЬ
Взубчатых передачах (цилиндрических прямозубых и косозубых, червячных) между зубьями, находящимися в зацеплении, возникает контактное напряжение. В общем случае напряжение представляет собой силу, деленную на площадь. Теоретически на поверхности зубьев, контактирующих между собой по линии, напряжение должно быть бесконечно велико. Но практически материал зубьев под давлением деформируется и вместо линии получается площадь.
Основоположником теории контактных напряжений является Герц (Herz, 1881), поэтому буквенным обозначениям контактных напряжений приписывают индекс Н. Формула Герца для определения контактных напряжений между двумя сжатыми цилиндрами (рис. 14) имеет вид:
|
|
|
|
qE1 E2 |
|
|
(77) |
H |
П E1 |
1 |
2 |
E2 1 |
2 |
||
|
пр |
2 |
|
|
где q — удельная нагрузка, Н/мм;
Е1 и Е2 — модули упругости материалов цилиндров соответственно меньшегo и большего диаметров, МПа;
пр — приведенный радиус кривизны цилиндров, мм;
1 и |
2 — коэффициенты Пуассона материала цилиндров |
соответственно меньшего и большего диаметров.
Коэффициент Пуассона для стали 0,25...0,35; для бронзы 0,32...0,35; для чугуна 0,23...0,27, поэтому без существенной погрешности принимают
1 |
= |
2 |
= 0,3. |
Рис. 14. Схема сжатия двух цилиндров
40