
Проектирование передач и механизмов. Кирпичев Ю.В., Кирпичев И.Ю
.pdfМИНИСТЕРСТВО ОБРАЗОВАНИЯ И НАУКИ РОССИЙСКОЙ ФЕДЕРАЦИИ
Воронежский государственный технический университет
Ю.В. Кирпичев И.Ю. Кирпичев М.Г. Поташников
ПРОЕКТИРОВАНИЕ ПЕРЕДАЧ И МЕХАНИЗМОВ
Утверждено Редакционно-издательским советом университета в качестве учебного пособия
Воронеж 2005
УДК 531.8 - 621.01
Кирпичев Ю.В., Кирпичев И.Ю., Поташников М.Г. Проектирование передач и механизмов: Учеб. пособие. Воронеж: Воронеж. гос. техн. ун-т,
2005. 90 с.
Учебное пособие содержит основные сведения о расчете и конструировании зубчатых и червячных передач. Учебное пособие предназначено в основном для выполнения курсовых проектов по проектированию приводов машин. С этой целью в него включено достаточно большое количество справочного материала и примеров расчета, необходимого при выполнении расчетов и чертежей.
Учебное пособие предназначено для студентов третьего курса очной формы обучения.
Издание соответствует требованиям Государственного образовательного стандарта высшего профессионального образования по направлению 150200 ‖Машиностроительные технологии и оборудование‖, специальности 150202 ―Оборудование и технология сварочного производства‖, дисциплине ―Детали машин‖.
Учебное пособие подготовлено на магнитном носителе в текстовом редакторе MS WORD и содержится в файле ―Передачи.doc‖.
Табл. 15. Ил. 20. Библиогр.: 8 назв.
Научный редактор д-р техн. наук, проф. Д.В. Хван
Рецензенты: кафедра ―Транспортные машины‖ Воронежского государственного архитектурно-строительного университета (зав. кафедрой д-р техн. наук, проф. Ю.Ф. Устинов); канд. техн. наук, доц. Ю.И. Калинин
©Кирпичев Ю.В., Кирпичев И.Ю., Поташников М.Г., 2005
©Оформление. Воронежский государственный технический университет, 2005
ВВЕДЕНИЕ
В современном машиностроении прослеживаются тенденции повышения мощности и быстроходности двигателей, равномерности хода машин, автоматизации процессов, увеличение длительности и безотказности работы, удобства и безопасности обслуживания, экономичности при изготовлении и эксплуатации, снижения массы и стоимости конструирования, изготовления и эксплуатации машин.
Проектирование передач и их узлов – творческий процесс, усовершенствуемый по мере приобретения опыта работы. Студенты при изучении курса ―Детали машин‖ постигают азы основ конструирования и расчета деталей, механических передач и машины в целом.
Учебное пособие предназначено в основном для выполнения курсовых проектов по проектированию приводов машин. С этой целью в него включено достаточно большое количество справочного материала и примеров расчета, необходимого при выполнении расчетов и чертежей.
Учебное пособие содержит основные сведения о расчете и конструировании зубчатых и червячных передач. Приведено много примеров расчета и справочного материала.
3
1.ВЫБОР МАТЕРИАЛОВ И ТЕРМООБРАБОТКИ
1.1.Цилиндрические и конические передачи
Впроизводственных условиях при проектировании и изготовлении редукторов выбор материалов и назначение термической обработки осуществляют на базе опыта конструкторов и технологов.
Вкурсовом проектировании при выборе марок сталей и термической обработки для шестерен и колес можно руководствоваться данными таблиц
иприведенными ниже рекомендациями.
Взависимости от твердости, обусловленной термической обработкой, стальные зубчатые колеса делят на две основные группы: твердостью НВ<350 (нормализация, улучшение) и твердостью НВ>350 (объемная закалка, поверхностная закалка с нагревом ТВЧ, цементация, азотирование). Колеса первой группы изготовляют из качественных углеродистых сталей 40, 45, 50, 50Г и легированных сталей 35Х, 40Х, 45Х, 40ХН и др. Их применяют в мало- и средненагруженных передачах.
Нормализованные зубчатые колеса небольших размеров изготовляют из углеродистых сталей обыкновенного качества Ст5, Ст6 и качественных углеродистых сталей 35, 40, 45, 50, а больших размеров — из стального литья 35Л, 40Л, 45Л, 50Л, 55Л (при работе на окружных скоростях до 5 м/с) или отливок из легированных сталей 40ХНТЛ, 35ГЛ, 35ХГСЛ (при скоростях более 5 м/с).
Материал твердостью НВ< 350 допускает нарезку зубьев после термообработки, благодаря чему исключаются дорогие отделочные операции (шлифовка, притирка и др.). При этом обеспечиваются хорошая приработка и отсутствие хрупкого разрушения при динамических нагрузках.
Колеса второй группы применяют в тяжелонагруженных передачах и в передачах, к которым предъявляют повышенные требования по массе и размерам. Высокая твердость активных поверхностей зубьев порядка HRC50...60, достигаемая объемной и поверхностной закалкой, азотированием, цементацией, цианированием, позволяет увеличить допустимые напряжения примерно в 2 раза.
Зубья с большой твердостью активной поверхности плохо прирабатываются и нуждаются в высокой точности изготовления. Применение термической обработки после механической приводит к короблению зубьев
ивызывает необходимость дополнительных отбелочных операций: шлифовки, притирки, обкатки и др.
Закаленные зубчатые колеса изготовляют из сталей 45, 35Х, 40Х, 40ХН, 30ХНЗА, 40ХН2МА и др., цементированные — из сталей 15, 20, 15Х, 20Х, 12ХНЗА, 15ХФ, 18ХГТ, 18Х2Н4А, азотированные – из сталей 38X210,
38Х2МЮА.
Материал и термообработку можно выбирать по таблице 1.
4

Таблица 1 Рекомендуемые стали и термообработка для зубчатых колес
[заготовка-поковка (штамповка, прокат)]
|
Размер сечения, мм не более |
|
Термообработка |
||
Марка стали |
Твердость |
|
|
||
|
|
||||
поверхности |
Вид |
Ориентировочный |
|||
|
режим |
||||
|
|
||||
|
|
|
|||
|
|
|
|
|
|
|
|
|
|
Закалка в воде |
|
40 |
60 |
НВ 192...228 |
Улучшение |
(840...860 °С), |
|
|
|
|
|
отпуск (550...620 °С) |
|
|
80 |
НВ 170...217 |
Нормализация |
Нормализация |
|
|
(850...870 °С) |
||||
|
|
|
|
Закалка в воде |
|
45 |
100 |
НВ 192...240 |
Улучшение |
(820...840 °С), |
|
|
|
|
отпуск (560...60 °С) |
||
|
|
|
|
||
|
|
|
|
Закалка в воде |
|
|
60 |
НВ 241...285 |
Улучшение |
(820...840 °С), |
|
|
|
|
|
отпуск (520...530 °С) |
|
|
|
|
|
|
|
|
80 |
НВ 179...228 |
Нормализация |
Нормализация |
|
50 |
(840...860 °С) |
||||
80 |
НВ 228.. .255 |
Улучшение |
Закалка (820...840 °С), |
||
|
|||||
|
отпуск (560...620 °С) |
||||
|
|
|
|
||
|
|
|
|
|
|
|
100 |
НВ 230...260 |
Улучшение |
Закалка (830...850 °С), |
|
|
отпуск (540…580 0С) |
||||
40Х |
60 |
НВ 260...280 |
Улучшение |
Закалка (830...850°С), |
|
отпуск (500 °С) |
|||||
|
|
|
|
||
|
60 |
HRC 50...59 |
Азотирование |
То же, с последующим |
|
|
мягким азотированием |
||||
|
|
|
|
||
|
|
|
|
Закалка в масле |
|
|
100 |
HВ 230...280 |
Улучшение |
(840...860 °С), |
|
45Х |
|
|
|
отпуск (580...640 °С) |
|
100...300 |
НВ 163...269 |
Улучшение |
Тоже |
||
|
|||||
|
|
|
|
|
|
|
300...500 |
НВ 163...269 |
Улучшение |
Тоже |
|
|
|
||||
|
|
|
|
|
|
|
|
|
|
Закалка в масле |
|
|
100 |
НВ 230.. .300 |
Улучшение |
(820...840 °С), |
|
40ХН |
|
|
|
отпуск (560...600°С) |
|
|
|
|
|
|
|
|
100...300 |
НВ >=241 |
Улучшение |
Тоже |
|
|
|
|
|
|
5
|
|
|
|
Закалка в масле |
|
40 |
HRC 48...54 |
Закалка |
(820...840 °С), |
|
|
|
|
отпуск (180…200 0С) |
|
|
|
|
Закалка в масле |
|
100 |
HВ 241 |
Улучшение |
(850...870 °C), |
|
|
|
|
отпуск (600...650 °С) |
35ХМ |
|
|
|
|
50 |
НВ 269 |
Улучшение |
Тоже |
|
|
|
|
|
|
|
|
|
|
Закалка в масле |
|
40 |
HRC 45...53 |
Закалка |
(850...870°С), |
|
|
|
|
отпуск (180…200 0С) |
|
|
|
|
Закалка в масле |
|
80 |
НВ>=302 |
Улучшение |
(830...850 °С), |
40ХНМА |
|
|
|
отпуск (600...620 °С) |
|
|
|
|
|
|
300 |
НВ >=217 |
Улучшение |
Тоже |
|
|
|
|
|
|
|
|
|
Закалка в масле |
|
150 |
НВ 235 |
Улучшение |
(850...880 °С), |
|
|
|
|
отпуск (640...660 °С) |
|
|
|
|
|
|
|
|
|
Закалка в масле |
|
60 |
НВ 270 |
Улучшение |
(850...880 °С), |
35ХГСА |
|
|
|
отпуск (500 °С) |
|
|
|
|
|
|
|
|
|
|
|
40 |
НВ 310 |
Улучшение |
Тоже |
|
|
|
|
|
|
|
|
|
Закалка в масле |
|
30 |
HRC 46...53 |
Закалка |
(860...880 °С), |
|
|
|
|
отпуск (200...250 °С) |
|
|
|
|
|
20Х |
60 |
HRC 56...63 |
Цементация |
Закалка, отпуск |
|
|
|
|
|
12ХНЗА |
60 |
HRC 56...63 |
Цементация |
Закалка, отпуск |
|
|
|
|
|
25ХГТ |
— |
HRC 58...63 |
Цементация |
Закалка, отпуск |
|
|
|
|
|
38ХМЮА |
— |
HRC 57...67 |
Азотирование |
Заготовка-улучшение |
|
|
|
|
|
Для лучшей приработки зубьев твердость шестерни рекомендуется назначать больше твердости колеса для прямозубых передач на 10...15
единиц по шкале НВ, имея в виду, что 1 HRC = 10 НВ: |
|
HB1 = HB2 + 10... 15. |
(1) |
Для косозубых передач твердость шестерни должна быть еще больше |
|
(для улучшения несущей способности передачи). Рекомендуется: |
|
НВ1 = НВ2 + 50...70. |
(2) |
6
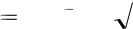
Чугун используется для изготовления зубчатых колес крупногабаритных тихоходных передач и колес открытых передач. Зубья из чугуна хорошо прирабатываются и противостоят усталостному выкрашиванию и заеданию при плохом смазывании, но имеют малую прочность при изгибе, особенно при ударных нагрузках. Рекомендуются чугуны: серый СЧ21 и СЧ24, модифицированный СЧ25, СЧ3О и СЧ35, высокопрочный всех марок, а для неответственных зубчатых колес СЧ15 и СЧ18.
Пластмассы применяют для изготовления колес малонагруженных передач (привод распределительного вала двигателей грузовых автомобилей) для уменьшения шума при работе. Главным образом используют текстолит, лигнофоль, капролон, полиформальдегид.
Практикуется покрытие зубьев металлических колес тонким слоем нейлона (0,05...0,5 мм).
1.2. Червячные передачи
Червяки для силовых передач изготовляют из сталей 15Х, 20Х, 12ХН2, 18ХГТ, 20ХФ, подвергнутых цементации и закалке до твердости HRC 58...63, или сталей 40, 45, 40Х, 40ХН с закалкой до HRC 45...55. Последние применяют в тихоходных и малонагруженных передачах.
Червячные колеса изготовляют преимущественно из бронзы, причем в целях экономии из нее изготовляют лишь зубчатый венец. При скорости скольжения 6...30 м/с применяют более дорогие бронзы БрОФ10-1, БрОНФ с высокими антифрикционными и пртивозадирными свойствами, при скорости менее 6 м/ч — менее дорогие безоловянистые бронзы БрАЖ9-4Л, БрАЖН10- 4-4Л. При этом твердость червяка должна быть HRC45 (не менее).
Если скорость скольжения менее 2 м/с, то червячные колеса из экономических соображений изготовляют целиком из чугуна марок СЧ15, СЧ18 и СЧ20.
Скорость скольжения (м/с) при проектном расчете приближенно определяют по формуле:
Vсс 4,5 |
4 n 3 |
T |
(3) |
|
1 |
2 |
где n1 — частота вращения червяка,
T2 – вращающий момент на валу червячного колеса Н • м.
7
ПРИМЕР 1
Выбрать материал и назначить термообработку для шестерен и колес цилиндрического двухступенчатого редуктора. Редуктор работает в течение смены с полной нагрузкой. Целесообразно получение малой массы редуктора.
По рекомендациям (см. табл. 1.) принимаем сравнительно недорогую легированную сталь 20Х цементированную с закалкой в масле и отпуском до твердости HRC 58, что соответствует для шестерен HВ 578. Принимаем быстроходную пару косозубую, тихоходную - прямозубую.
Твердость зубьев колеса быстроходной пары [формула (2)] : HB2б = НВ1 - 68 = 578 - 68 = 510,
что соответствует HRC 52.
Твердость зубьев колеса тихоходной пары [формула (1)]: HB2т = HB1 = HB1 - 13 = 578-13 = 565.
Это соответствует HRC 51.
8

ПРИМЕР 2
Выбрать материал и назначить термообработку червячной пары одноступенчатого червячного редуктора. Передаваемый червячным колесом вращающий момент Т2 = 1000 Н • м, частота вращения червяка n1 = 800 мин-1, передача средненагруженная.
По рекомендациям (см. табл. 1.1) принимаем для червяка сталь 40Х с закалкой в масле до HRC 45.
Материал колеса выбираем после определения скорости скольжения по формуле (3):
Vсс 4,5 4 *8003 100 3,6м / с
Принимаем менее дорогую бронзу БрАЖ9-4Л, из которой должен быть изготовлен венец червячного колеса.
9

2. ОПРЕДЕЛЕНИЕ ДОПУСТИМЫХ НАПРЯЖЕНИЙ ПРИ РАСЧЁТЕ НА УСТАЛОСТЬ
Допустимые контактные напряжения при расчѐте на усталость выбирают по кривым усталости.
Рис. 1. Кривая усталости
До базового числа циклов напряжений NH0 (рис. 1) допустимое напряжение может быть взято больше, за счет чего уменьшаются габаритные размеры передачи (меньше межосевое расстояние при тех же параметрах
нагружения). При числе циклов больше базового NH0 величину H lim b (это предел контактной выносливости при нулевом цикле) считают постоянной.
2.1. Допустимые контактные напряжения при расчёте на усталость зубчатых передач
[ H ] |
H limb K HL |
|
|
(4) |
|
|
S H |
В этой формуле отсутствуют коэффициенты по ГОСТ 21354—75, учитывающие влияние шероховатости, смазочного материала, скорости и размеров колес, которые для распространенных на практике показателей близки к единице.
Предел контактной выносливости поверхностей зубьев зависит от твердости поверхности. Его можно выбирать по таблице 2.
10