
Методическое пособие 467
.pdf
для массового производства |
|
Нвыр = Тсм / tш , |
(11.6) |
где Тсм - продолжительность смены, мин. |
|
11.3 Методы установления норм времени
Технически обоснованные нормы времени устанавливают на основе тщательного анализа и выявления всех производственных возможностей каждого цеха, участка, рабочего места и исследования составных частей данной операции.
Основными методами установления технически обоснованных норм времени, базирующимися на анализе процесса, являются:
расчет норм времени на основе изучения затрат рабочего времени наблюдением (аналитически-исследовательский метод);
расчет норм времени по нормативам (аналитически-расчетный метод);
расчет норм времени по типовым нормам (расчетно-сравнительный метод).
Аналитически-исследовательский метод основан на исследовании опера-
ции в производственных условиях и изучении затрат рабочего времени на ее выполнение с помощью хронометража и фотографии рабочего дня. Этот метод приобретает особое значение при изучении и обобщении передовых приемов труда, при разработке нормативов для установления технически обоснованных норм расчетным путем.
При аналитически-расчетном методе длительность нормируемой операции находят расчетным путем, используя нормативы для определения затрат времени на отдельные ее элементы. При этом используют действующие дифференцированные нормативы для различных видов обработки по типам производства, укрупненные нормативы, номограммы, таблицы.
При расчетно-сравнителъном методе нормы устанавливают на основе сопоставления и расчета типовых операций, типовых технологических процессов, типовой организации труда и рабочих мест. Такие нормы времени, хотя и предусматривают поэлементный расчет, будут более укрупненными и менее точными, чем при расчете по описанным ранее методам.
Вусловиях массового производства изучаются и формируются приемы труда операторов и наладчиков, сборщиков и других рабочих и технически обоснованные нормы отличаются чрезвычайно точными расчетами и анализом.
Вусловиях массового производства требуется высокая точность устанавливаемых норм времени на ручные работы. Заданную точность норм обеспечивает применение метода нормирования по микроэлементам.
Основы микроэлементного нормирования создали независимо друг от друга американский инженер Ф. Гилбрет и советский ученый В. М. Иоффе.
Сущность микроэлементного нормирования и проектирования трудовых
141
процессов заключается в следующем:
1)все разновидности трудовых движений сводятся к конечному количеству стандартных движений (у В. М. Иоффе их два с различными прибавками, у Ф. Гилбрета - 18);
2)для проектирования трудового процесса необходимо расчленить его на микроэлементы, составить карту выполнения трудового процесса и проанализировать рациональность сочетания и последовательность отдельных микродвижений. На основе такого анализа делается описание рационального способа выполнения трудового процесса;
3)норма времени на проектируемый трудовой процесс определяется суммированием нормативов по всем микроэлементам.
Метод микроэлементного нормирования ручных работ, предложенный В. М. Иоффе, заключается в том, что все многообразие трудовых движений сводится
кдвум «стандартам»: а) взять (схватить, взяться), б) переместить (вставить, переместить, сдвинуть). Каждый из этих микроэлементов может быть «решительным» (коротким, выполняемым бесконтрольно, не требуя внимания или аккуратности) или «приноровительным» (продолжительным, осуществляемым под контролем и замедленным настолько, чтобы в конце движения рука или предмет заняли исходное положение).
Достоинством метода В. М. Иоффе является относительная простота расчета норм, однако в этом заключается и основной недостаток метода, так как малое число выделенных микроэлементов не позволяет проводить глубокого анализа трудового процесса при установлении нормы времени.
В последние годы советскими учеными разработаны методы микроэлементного нормирования и проектирования рационального состава трудовых процессов с помощью ЭВМ. В память машины заносятся нормативы на микроэлементы и рациональная последовательность их выполнения. Исходная информация подвергается анализу в ЭВМ, на основе специальной программы. Результаты выдаются в виде нормы времени и карты рационального трудового процесса.
11.4 Методы изучения времени наблюдением
К основным способам изучения затрат времени методом наблюдения относятся хронометраж и фотография рабочего дня.
Хронометраж операции - способ изучения затрат времени на выполнение циклически повторяющихся ручных и машинно-ручных элементов операции. Он применяется для проектирования рациональных состава и структуры операции, установления их нормальной продолжительности и разработки на этой основе нормативов, используемых при определении технически обоснованных норм времени расчетным путем. Хронометраж применяется также для проверки норм, установленных расчетным путем, преимущественно в массовом и крупносерийном производстве. Кроме того, хронометражем пользуются при изучении передовых методов
142
работы с целью их распространения.
Процесс хронометража включает: расчленение исследуемой операции на составляющие ее элементы; измерение этих элементов во времени в порядке их выполнения; анализ результатов наблюдений и отбор элементов для включения в рациональный состав операций; определение нормальной продолжительности выполнения каждого элемента.
Хронометраж может быть сплошным и выборочным. При сплошном непрерывно измеряют все приемы операции в их технологической последовательности; при выборочном - за время выполнения операции измеряют лишь отдельные приемы независимо от их последовательности, но так, чтобы в конечном счете была определена продолжительность всех приемов операции.
Хронометраж состоит из следующих этапов: подготовка к наблюдению, наблюдение, обработка хронометражных наблюдений, анализ результатов, выводы, установление норм и проектирование нормативов оперативного времени.
Подготовка к проведению хронометражного наблюдения заключается в расчленении операции на комплексы приемов, приемы или движения (в зависимости от цели хронометрирования), проектировании рациональной структуры операции, ознакомлении с оборудованием, условиями работы, тарификацией работы и соответствием ее квалификации рабочего.
В порядке подготовки к наблюдению заполняется лицевая сторона хроно- метражно-наблюдательного листа, где записываются следующие исходные данные: наименование и характеристика изготовляемого изделия; название наблюдаемой операции; количество изделий в партии; разряд работы; сведения о материале, оборудовании, инструменте, приспособлениях; сведения о рабочем (фамилия, квалификация, стаж, производственная характеристика). Здесь же вычерчивается эскиз изделия и приводятся другие сведения, полностью характеризующие данную операцию.
Наблюдатель должен проследить, чтобы администрация цеха, где производится наблюдение, устранила все замеченные неполадки, обеспечив необходимый темп и бесперебойный ход работы. Кроме того, он должен определить наиболее рациональное расчленение операции на составные элементы, устранив излишние движения. Установление рационального состава и структуры операции производится наблюдателем как на основе личного опыта, так и (главным образом) с помощью изучения приемов работы новаторов на аналогичных операциях.
Для проведения хронометража выбирается рабочий или группа рабочих, хорошо знающих механизм, инструмент и приспособления, применяемые на данной операции, умеющие рационально организовать свой рабочий день, соответствующие по своей квалификации выполняемой работе, имеющие производственный опыт и навыки в работе.
Обычно хронометражные наблюдения проводятся за работой передовых рабочих, выполняющих и перевыполняющих плановые задания и обеспечивающих
143
высокий уровень производительности труда. Эти рабочие должны быть предупреждены о проводимых наблюдениях, их цели и проинструктированы так, чтобы работа шла по запроектированному оптимальному режиму.
Подготовка к наблюдению заканчивается занесением в наблюдательный лист элементов изучаемой операции в их технологической последовательности и установлением фиксажных точек. Под фиксажной точкой подразумевается момент, в котором совпадают окончание последнего движения предыдущего приема (комплекса) с началом первого движения последующего приема операции. Установление фиксажных точек необходимо для правильного измерения продолжительности приемов. Кроме того, в процессе подготовки к наблюдению заполняется графа «Техническая характеристика», где приводятся показатели, характеризующие технические условия выполнения изучаемой операции.
В процессе наблюдения измеряют и фиксируют продолжительность каждого нормируемого элемента операции (движения, приема или комплекса приемов). Для измерения продолжительности применяют секундомеры, хронометры и специальные регистраторы времени (многоциферблатные стрелочные и цифровые приборы), устройства нанесения информации на специальные бланки или перфоленту и киноаппаратуру. Длительность элементов операции определяют по текущему времени или по отдельным отсчетам.
При записи по текущему времени в наблюдательный лист заносят данные, фиксирующие момент окончания первого и начала последующих элементов операции без остановки хронометра или секундомера. Продолжительность элементов операции, необходимую для получения хронометражных рядов, выявляют позднее, в процессе обработки данных хронометражного наблюдения.
При выборочном хронометрировании за время выполнения операции фиксируют продолжительность только отдельных нормируемых элементов. При этом секундомер или хронометр пускают в ход с началом данного элемента операции и выключают одновременно с его окончанием.
Первый способ (определение по текущему времени) более удобен. Хронометражные наблюдения следует начинать при установившемся рациональном темпе работы, когда соблюдены все предусмотренные условия и освоены приемы труда. Наблюдатель фиксирует продолжительность нормируемых элементов операции, а также в особой графе хронокарты отмечает длительность перерывов и различных отклонений, имевших место во время хронометрирования. В результате хронометражных наблюдений по каждому элементу операции накапливаются многократно зафиксированные данные о длительности его выполнения, образующие хронометражный ряд. Каждому элементу операции соответствует один хронометражный ряд. Число членов этого ряда равно количеству проделанных замеров времени. При хронометраже особое внимание уделяется ручным и машинно-ручным приемам операции, машинные приемы определяют расчетом.
Количество замеров, составляющих хроноряд, должно быть достаточным
144
для получения достоверного норматива. Минимально необходимое число замеров рекомендуется выбирать по табл. 11.2.
Таблица 11.2
Необходимое число наблюдений при хронометраже и допустимые коэффициенты устойчивости хронометражных рядов
|
|
Допустимый коэф- |
Количество наблюдений |
||||||||
|
|
фициент устойчи- |
|
|
|
|
|
|
|||
|
Продолжи- |
для машин- |
для ручных |
||||||||
Тип производст- |
вости |
ных работ |
|
работ |
|
||||||
тельность |
|
|
|||||||||
ва |
|
|
|
|
|
|
|
|
|
|
|
машин- |
|
|
при точности |
|
|||||||
элемента, с |
ручные |
|
|
||||||||
|
ные рабо- |
|
наблюдений, % |
|
|||||||
|
|
|
|
||||||||
|
|
работы |
|
|
|||||||
|
|
ты |
5 |
10 |
20 |
5 |
|
10 |
|
20 |
|
|
|
|
|
|
|||||||
|
|
|
|
|
|
|
|
|
|
|
|
Массовое |
До 10 |
1,2 |
2,0 |
7 |
4 |
- |
45 |
|
14 |
|
6 |
Св. 10 |
1,1 |
1,3 |
4 |
3 |
- |
10 |
|
15 |
|
- |
|
|
|
|
|||||||||
|
|
|
|
|
|
|
|
|
|
|
|
Крупносерийное |
До 10 |
1,2 |
2,3 |
7 |
4 |
- |
63 |
|
19 |
|
7 |
Св. 10 |
1,1 |
1,7 |
4 |
3 |
- |
27 |
|
10 |
|
5 |
|
|
|
|
|||||||||
|
|
|
|
|
|
|
|
|
|
|
|
Серийное |
До 10 |
1,2 |
2,5 |
7 |
4 |
- |
75 |
|
21 |
|
8 |
Св. 10 |
1,1 |
2,3 |
4 |
3 |
- |
63 |
|
19 |
|
7 |
|
|
|
|
|||||||||
|
|
|
|
|
|
|
|
|
|
|
|
Мелкосерийное |
>> 10 |
1,2 |
3,0 |
7 |
4 |
- |
- |
|
25 |
|
10 |
|
|
|
|
|
|
|
|
|
|
|
|
|
|
|
|
|
|
|
|
|
|
|
|
Полученные в процессе наблюдений хронометражные ряды анализируют и подвергают статистической обработке. Анализ и обработку хронометражных рядов выполняют в следующем порядке: а) составляют ряды с достаточным числом замеров; б) устанавливают степень устойчивости ряда; в) исчисляют нормативную продолжительность каждого элемента; г) выявляют возможности совмещения элементов операции; д) устанавливают норму оперативного времени.
В практике нормирования степень устойчивости ряда принято измерять коэффициентом устойчивости kу, т. е. отношением максимального значения хронометражного ряда tmax к минимальному tmin:
kу = tmax / tmin . (11.7)
Чем ближе к единице значение коэффициента, тем устойчивее ряд. Практикой технического нормирования для различных типов производства выработаны допустимые коэффициенты устойчивости хронометражных рядов. При устойчивом хронометражном ряде норматив времени на каждый элемент операции определяется как средняя арифметическая величина всех замеров хронометражного ряда.
После установления нормальной продолжительности отдельных элементов операции проводится анализ полученных результатов, данные которого используются в виде нормы времени или первичного материала для разработки нормативов времени на вспомогательную и основную работы.
145
Результаты наблюдения анализируются с точки зрения рационализации операции и уменьшения времени на отдельные элементы операции.
Данные хронометража используются для: разработки нормативов времени на элементы ручной и машинно-ручной работы; установления норм времени на отдельные операции, главным образом, в условиях массового и крупносерийного производства, проверки и уточнения норм времени, установленных способом технического расчета по нормативам; изучения методов и приемов работы передовых рабочих с целью их широкого распространения.
Фотографией рабочего времени называется способ исследования трудового процесса с целью выявления затрат рабочего времени в течение изучаемого периода (как правило, на протяжении одной или нескольких смен). При этом способе главное внимание уделяется выявлению потерь рабочего времени, а также изучению затрат подготовительно-заключительного времени, времени обслуживания рабочего места и времени, необходимого на отдых. В этом и состоит основное отличие фотографии рабочего дня от хронометража операции, задачей которого является изучение элементов времени оперативной работы.
Фотография рабочего дня проводится с целью:
составления фактического баланса рабочего времени смены путем выявления всех его затрат за этот период, группировки их по категориям времени (подготовительно-заключительное, основное, вспомогательное, время перерывов и т. д.);
выявления причин потерь и непроизводительных затрат времени с последующей разработкой мероприятий по их устранению;
проектирования нормального баланса рабочего времени, предусматривающего улучшение использования рабочего времени путем ликвидации потерь;
получения данных, необходимых для нормирования подготовительнозаключительного времени, времени обслуживания рабочего места и перерывов, для составления нормативных таблиц по этим категориям времени;
определения числа рабочих, необходимых для обслуживания отдельных агрегатов, либо числа единиц оборудования, обслуживаемого одним рабочим.
При проведении фотографии рабочего дня производится наблюдение за работой механизмов и обслуживающих их рабочих с соответствующими отметками в наблюдательном листе фотографии рабочего дня с точностью до 1 мин. По окончании наблюдения полученные данные обрабатывают: составляют сводку времени по категориям затрат рабочего времени; разрабатывают организационнотехнические мероприятия; проектируют нормальный баланс рабочего времени; систематизируют данные, необходимые для составления нормативов подготови- тельно-заключительного времени, времени на обслуживание рабочего места, времени на отдых.
Степень детализации записей зависит от цели проведения фотографии и от
146
типа производства. В условиях единичного и мелкосерийного производства допускается меньшая детализация, чем в крупносерийном и массовом производстве, где необходим более точный анализ затрат времени, но всегда подробно фиксируют все перерывы в работе с указанием их причин. Результаты фотографии рабочего дня для целей анализа группируют по категориям рабочего времени.
Для облегчения обработки результатов наблюдения используют условные обозначения категорий времени - индексы, разработанные в соответствии с классификацией затрат времени.
Различают следующие виды фотографии рабочего дня: индивидуальную, когда объектом наблюдения служит один рабочий; групповую, когда объектом наблюдения является группа рабочих, исполняющих одинаковые или различные операции независимо друг от друга; бригадную, когда объектом наблюдения служит группа рабочих, связанных между собой единством производственного задания.
Фотография рабочего дня проводится в следующем порядке: подготовка к наблюдению, заключающаяся в подробном изучении и описании объекта наблюдения и производственной обстановки; непосредственная фотография рабочего времени путем регистрации всех без исключения элементов затрат времени; обработка полученных данных. Обработка включает: определение продолжительности отдельных видов затрат времени; составление фактического баланса рабочего дня путем разноски затрат времени по группам; анализ затрат времени и проектирование нового, нормального баланса рабочего дня. При проектировании нормального баланса предусматривается возможность совмещения отдельных элементов во времени, исключение излишних элементов, ликвидация нерегламентированных перерывов, проведение организационно-технических мероприятий, обеспечивающих устранение неполадок. В результате увеличивается норма выработки за счет уплотнения рабочего дня.
По технике проведения наблюдения фотография рабочего дня может быть: непрерывной, когда замеры времени ведутся в течение всего периода наблюдения непрерывно, и прерывной (маршрутной), при которой замеры времени производят через определенные, сравнительно небольшие промежутки времени; такая фотография рабочего дня применяется для рабочих (или бригад), не имеющих постоянных рабочих мест, например для транспортных бригад и др.
Различают два вида записи данных фотографий рабочего дня в наблюдательный лист: цифровой, когда данные наблюдений фиксируются только в цифрах; графический, когда продолжительность наблюдаемых действий графически (в масштабе) отмечается в строках соответствующих категорий (по индексам) времени.
Фотография рабочего дня - процесс трудоемкий, требующий привлечения большого числа нормировщиков для объективного суждения о резервах времени по всем участкам производства. Потери рабочего времени полнее и проще могут быть выявлены самофотографией рабочего дня. Она получила в последние годы
147

широкое распространение, но только как способ анализа потерь рабочего времени, а не нормирования операции.
Термин «самофотография» говорит о том, что все записи производятся непосредственно самим исполнителем, который регистрирует только причины и продолжительность потерь времени. Устанавливая потери во времени и причины их возникновения, рабочий вносит конкретные предложения для их устранения, а также рационализаторские предложения по улучшению организации производства.
12 Организационное обеспечение качества продукции
12.1 Понятие о качестве продукции
Качество продукции относится к числу важнейших показателей производ- ственно-хозяйственной деятельности предприятий и объединений машиностроения. В ГОСТ 15.467 - 70 «Качество продукции. Термины» указывается, что под ка-
чеством продукции понимается совокупность свойств изделия, обусловливающих ее пригодность удовлетворять определенные потребности в соответствии с ее назначением. Качество продукции характеризуется системой показателей. При этом выделяется две группы показателей: эксплуатационные и производственнотехнологические.
Эксплуатационные показатели отражают те свойства качества продукции, которые связаны с удовлетворением определенных потребностей в соответствии с назначением изделий. К числу показателей такого рода следует отнести быстродействие, надежность, долговечность приборов, их устойчивость к воздействию окружающей среды и т. д.
Производственно-технологические показатели характеризуют прибор как объект производства в условиях приборостроительного предприятия-изготовителя. Они показывают соответствие качества изготовленных изделий требованиям утвержденных стандартов или технических условий. К ним относятся коэффициент выхода годных приборов и деталей, степень конструктивной унификации, трудоемкость и себестоимость изделий в производстве и т. д.
Для получения общего представления об уровне качества того или иного изделия применяется комплексный, или интегральный, показатель качества. Методы его определения основаны на сведении воедино отдельных показателей качества изделия с помощью коэффициентов весомости каждого показателя. Для расчетов рекомендуются следующая формула для определения комплексного показателя качества:
KK b1 kK1 b2 kK 2 ... bi kK i ... bn kK n . |
(12.1) |
где КК - комплексный показатель качества;
bi - коэффициенты весомости отдельных показателей качества; kкi, kкn - единичные (частные) показатели качества.
148
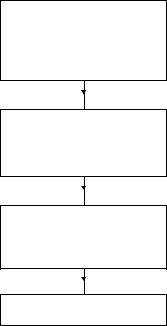
Нахождение комплексного показателя качества требует тщательного анализа всех свойств изделия, определения значимости; каждого из них, использования экспертных методов. Алгоритм расчета комплексного показателя качества приводится на рис. 12.1.
Выбор шкалы размерностец комплексной оценки Кк (для приведения единицы измерения к одному виду)
Определение способа нахождения весомостей b, приемлемого для оценки Кк
Выбор метода сведения воедино оценок отдельных свойств Кк для оценки Кк
Вычисление Кк
Рисунок 12.1 – Алгоритм расчета комплексного показателя качества.
Основные показатели качества изделий отражаются в государственных стандартах (ГОСТ) или технических условиях (ТУ). Эти документы устанавливают единые правила к техническим параметрам и другим качественным показателям изделий, требования к приемке и испытаниям приборов, их транспортировке и хранению.
12.2 Управление качеством продукции
Качество продукции зависит от многих факторов: технических, организационных, экономических, правовых, социально-психологических и др. Поэтому проблема качества не может быть решена путем проведения отдельных, разрозненных мероприятий, а требует применения системных методов управления каче-
ством. Управление качеством продукции - это установление и поддержание необходимого уровня качества при разработке, производстве и эксплуатации про-
мышленной продукции. Управление при этом осуществляется путем систематического контроля качества и целенаправленного воздействия на условия и факторы, определяющие тот или иной, уровень качества.
Требование комплексного подхода к организации управления, качеством предполагает создание и реализацию комплексной системы управления качеством продукции. Основным звеном этой системы является объединение или предприятие.
149
Комплексная система управления качеством продукции представляет собой функционирующую в рамках самостоятельной организационной структуры совокупность средств и методов воздействия на условия и факторы, участвующие в процессе формирования и реализации оптимального уровня качества продукции при ее разработке, производстве, эксплуатации (или потреблении).
Комплексная система управления качеством предусматривает осуществление воздействий на формируемый уровень качества продукции при ее разработке производстве и эксплуатации.
В период разработки нового изделия управления качеством находит выражение в планировании уровня качества, который формулируется в техническом задании; в мероприятиях по достижению зафиксированных в техническом задании параметров; в постоянном контроле за уровнем качества в процессе разработки изделия и изготовления опытных образцов и серий.
Важным звеном в единой системе управления качеством является реализация функций управления в процессе производства. В этом случае планирование состоит в определении критериев качества как изделия в целом, так и его отдельных составных частей. Контроль качества распространяется на применяемые материалы, технологические процессы, оборудование и готовые изделия. На основе анализа информации, полученной при контроле, предпринимаются меры по обеспечению надлежащего качества путем управления технологическими процессами, корректировки режимов, повышения точности оборудования и т. д.
Сложным и ответственным этапом системы является управление качеством при эксплуатации изделий. Его осуществление предполагает оптимизацию условий применения, отработку условий эксплуатации, контроль качества в период эксплуатации и т. д. Информация о поведении изделий в эксплуатации играет важную роль в разработке мероприятий по повышению качества продукции при ее проектировании и производстве.
Стандартизация - основа управления качеством. Рациональное управле-
ние качеством продукции основано на применении системы стандартов. Стандарты являются документами, регулирующими деятельность каждого
предприятия. В них отражаются как требования государственных и отраслевых стандартов, так и особенности выпускаемой продукции и организационнотехнический уровень предприятий. Сейчас в стране значительно возрастает роль этих стандартов, они становятся базой для совершенствования организации всей работы по управлению производством и качеством продукции. Стандарты предприятия охватывают все стадии цикла: от научных исследований до проектирования, от производства до эксплуатации изделий электронной техники.
Объектами стандартов предприятия могут быть детали, сборочные единицы; нормы, требования и методы в области разработки и организации производства изделия; технологические процессы, нормы, требования к ним; ограничения по
150