
Методическое пособие 467
.pdf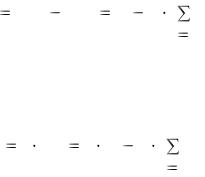
|
|
|
m |
|
tпр |
Т пос tобр |
(n 1) |
i 1ti , |
(7.6) |
а общее время пролеживания всех изделий партии, представляющее собой также обусловленную пролеживанием изделий величину связывания оборотных средств в незавершенном производстве, равно
|
|
|
m |
|
Тпр |
n tпр |
n (n 1) |
i 1ti , |
(7.7) |
Важным достоинством последовательного многооперационного цикла изготовления партии изделий является отсутствие в нем перерывов в работе рабочих и оборудования на всех операциях. Однако он имеет и существенные недостатки: вопервых, большое время пролеживания изделий и большой объем незавершенного производства; во-вторых, значительная длительность из-за отсутствия параллельности в обработке изделий. В связи с этим применять последовательный вид движения партии изделий по операциям целесообразно только в единичном и мелкосерийном производстве или при изготовлении небольших партий малотрудоемких изделий в серийном производстве.
Параллельный многооперационный цикл изготовления партии изде-
лий и его характеристики. Весьма эффективным в организации производственных процессов является использование параллельного вида движения партии изделий по операциям, при котором изделия передаются в обработку на последующую операцию поштучно или передаточными партиями сразу после окончания их обработки на предыдущей операции, не дожидаясь окончания обработки всей партии на этой операции, и обрабатываются на всех операциях без пролеживания. Этому виду движения соответствует параллельный многооперационный цикл изготовления партии изделий.
Параллельным называется такой многооперационный цикл изготовления партии изделий, при котором каждое изделие или передаточная партия изделий передается для обработки на последующую операцию сразу после окончания его (ее) обработки на предыдущей операции и обрабатывается на всех промежуточных операциях без пролеживаний.
Структура такого цикла представляет собой упорядоченную совокупность операционных циклов, в максимальной степени перекрывающихся во времени на каждой паре смежных операций (рис. 7.4). При этом партия изделий размером п разбивается на передаточные партии размером р (на рис. 7.4 n = 4 р), каждая из которых представляет собой совокупность изделий, передаваемых с одной операции на другую одновременно как единое целое. В частном случае, когда изделия передаются с операции на операцию поштучно, p = 1. Для того чтобы при движении по операциям любая передаточная партия нигде не пролеживала, необходимо найти операцию с максимальной длительностью tmax, называемую главной,
91
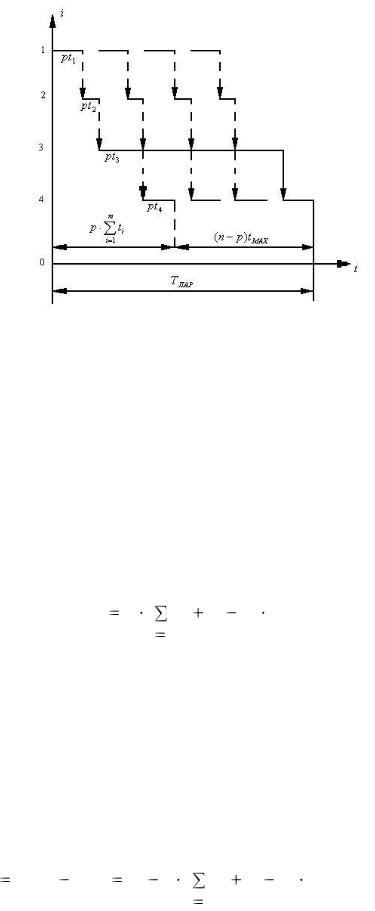
Рис. 7.4 Структура параллельного многооперационного цикла изготовления партии изделий
определить время обработки на ней передаточной партии изделий p tmax и осуществлять на всех операциях запуск в обработку передаточных партий изделий с так-
том τ, равным этому времени, т. е. τ = p tMAX.
Как видно из рис. 7.4, длительность параллельного многооперационного цикла состоит из двух частей, первая из которых представляет собой сумму времени обработки одной передаточной партии на всех операциях, а вторая равна времени обработки всей партии, за исключением одной передаточной партии, на главной операции:
|
|
m |
|
|
Тпар |
p |
i 1ti |
(n p) tmax . |
(7.8) |
Эта длительность намного меньше длительности последовательного многооперационного цикла изготовления партии изделий.
При параллельном виде движения партии изделий по операциям тоже могут иметь пролеживания, во-первых, до начала обработки на первой операции и после окончания обработки на последней операции и, во-вторых, внутри передаточной партии. При этом общее время пролеживания каждого изделия партии определяется как разность между длительностью цикла и временем обработки одного изделия на всех операциях:
|
|
|
|
m |
|
|
tпр |
Тпар |
tобр |
( p 1) |
i 1ti |
(n p) tmax , |
(7.9) |
а общее время пролеживания всех изделий партии равно
92

|
|
|
m |
|
|
Тпр |
n tпр |
n ( p 1) |
i 1ti |
n (n p) tmax . |
(7.10) |
Существенным моментом параллельного многооперационнога цикла является наличие перерывов в работе оборудования и рабочих на всех операциях, кроме главной. Число перерывов на i-й операции на единицу меньше числа передаточных партий (рис. 7.4), а продолжительность каждого перерыва равна разности между тактом запуска τ и продолжительностью обработки передаточной партии на этой операции: p ti
p
(tmax ti ) . Время перерывов в обработке всей партии
изделий на i-й операции равно произведению числа перерывов на длительность одного перерыва:
tпер |
(n / p |
1) p |
(tmax |
ti ) (n |
p) (tmax |
ti ) . |
(7.11) |
|
а общее время всех перерывов на всех операциях равно |
|
|||||||
|
Тпер |
(n |
p) |
m |
1(tmax |
ti ) . |
|
|
|
i |
|
(7.12) |
Необходимо отметить, что в чистом виде параллельный вид движения партии изделий по операциям реализуется только при поштучной передаче изделий с операции на операцию. При передаче изделий передаточными партиями в пределах каждой из них имеет место последовательный вид движения.
Достоинствами параллельного многооперационного цикла изготовления партии изделий являются его минимальная длительность, строгая ритмичность процесса производства и отсутствие пролеживания изделий на всех операциях, кроме первой и последней при поштучной передаче изделий с операции на операцию. В то же время его существенным недостатком является наличие перерывов в работе оборудования и рабочих на всех операциях, кроме главной. Исключением является случай, когда все операции цикла синхронизированы, т. е. продолжительность каждой из них равна целому числу тактов выпуска изделий, которое одновременно является числом рабочих мест на данной операции. Применяется этот цикл главным образом в поточном производстве преимущественно в процессах сборки, так как здесь сравнительно легко синхронизировать операции.
Параллельно-последовательный многооперационный цикл изготовления партии изделий и его характеристики. Стремление использовать достоинст-
ва параллельного и последовательного видов движения и одновременно избавиться от недостатков каждого из них привело к применению комбинированного, па-
раллельно-последовательного вида движения партии изделий по операциям, при котором обеспечивается непрерывная работа рабочих и оборудования на каждой операции и большая степень параллельности выполнения смежных операций. Ему соответствует параллельно-последовательный многооперационный цикл изготов-
93
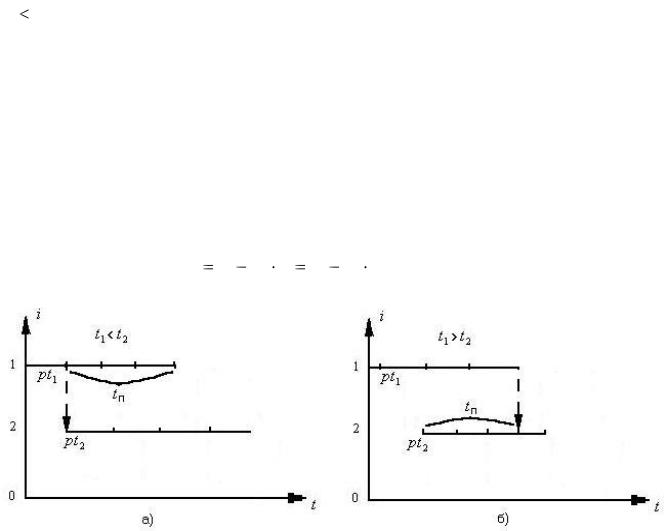
ления партии изделий.
Параллельно-последовательным называется такой многооперационный цикл изготовления партии изделий, при котором их обработка на каждой последующей операции начинается до окончания обработки всей партии изделий на предыдущей с таким расчетом, чтобы одновременно обеспечить, во-первых, непрерывную работу оборудования и рабочих на последующей операции и, вовторых, минимально возможную при этом длительность цикла выполнения данной пары смежных операций.
В структуре этого цикла существует два различных варианта сочетания операционных циклов на смежных операциях. Первый вариант соответствует случаю, когда штучное время предыдущей операции меньше, чем последующей, т. е. t1 t2 (рис. 7.5, а), и каждая передаточная партия обрабатывается на первой опе-
рации быстрее, чем на второй. При этом минимальная длительность цикла обработки партии изделий на данной паре смежных операций и непрерывная работа оборудования и рабочих на второй операции обеспечиваются лишь в том единственном случае, если обработка всей партии изделий на второй операции начинается сразу после окончания обработки первой передаточной партии на первой операции. Следовательно, сопряжение операционных циклов этих двух смежных операций должно осуществляться по моменту окончания обработки первой передаточной партии на первой операции. Время перекрытия, т. е. параллельного выполнения, этих двух операционных циклов равно
tп |
(n p) t1 |
(n p) min(t1,t2) . |
(7.13) |
Рис. 7.5 Варианты сочетания операционных циклов параллельнопоследовательного многооперационного цикла изготовления партии изделий
Второй вариант сочетания операционных циклов на смежных операциях соответствует случаю, когда штучное время предыдущей операции больше, чем
94
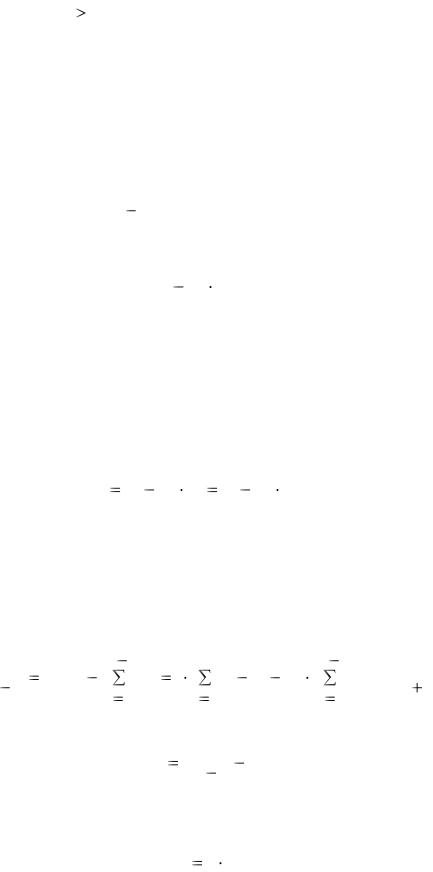
последующей, т. е. t1 t2 (рис. 7.5, б). В этом случае каждая передаточная партия
обрабатывается на второй операции быстрее, чем на первой, и непрерывность работы оборудования и рабочих на второй операции может быть достигнута только при предварительном накоплении определенного числа изделий на этой операции.
Для получения минимальной продолжительности обработки всей партии изделий на данной паре смежных операций необходимо строить обработку так, чтобы в момент окончания обработки последней передаточной партии на первой операции она немедленно поступала в обработку на второй операции. Следовательно, к этому моменту (n p) изделий партии уже должны быть обработаны на второй операции, а их обработка на этой операции должна быть начата в тот момент, когда до момента окончания обработки всей партии изделий на первой операции остается время, равное (n p) t2 . Лишь при этом условии одновременно
обеспечиваются непрерывная работа оборудования и рабочих на второй операции и минимальная длительность цикла обработки всей партии изделий на данной паре смежных операций.
Таким образом, сопряжение операционных циклов на данной паре смежных операций необходимо осуществлять по моменту окончания обработки последней передаточной партии на первой операции. Время перекрытия операционных циклов этих двух операций равно
tп |
(n p) t2 |
(n p) min(t1,t2) . |
(7.14) |
Общий принцип определения длительности параллельнопоследовательного многооперационного цикла состоит в том, что вначале определяется сумма длительностей всех операционных циклов, равная длительности последовательного многооперационного цикла, и из нее вычитается сумма времен перекрытий операционных циклов на всех парах смежных операций (рис. 7.6):
|
|
m |
1 |
|
m |
|
|
m |
1 |
|
Тп п |
Тпос |
i |
tпi |
n |
i |
ti |
(n p) |
i |
min(ti ,ti 1) . |
(7.15) |
|
|
1 |
|
1 |
|
1 |
|
|||
Время пролеживания одного изделия на всех операциях равно |
|
|||||||||
|
|
|
tпр |
|
Тп |
п |
tобр , |
|
|
(7.16) |
а общее время пролеживания всех изделий на всех операциях определяется выражением
Тпр |
n tпр . |
(7,17) |
Время перерывов в работе оборудования и рабочих на всех операциях равно
нулю.
95
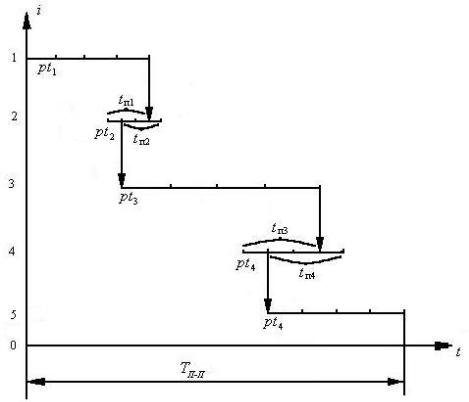
Рис. 7.6 Структура параллельно-последовательного многооперационного цикла изготовления партии изделий
В целом параллельно-последовательный многооперационный цикл изготовления партии изделий характеризуется тем, что, во-первых, его длительность меньше длительности последовательного, но больше длительности параллельного многооперационных циклов; во-вторых, в нем отсутствуют перерывы в работе оборудования и рабочих; в-третьих, в нем имеются пролеживания изделий на операциях, общее время которых, однако, много меньше, чем в последовательном многооперационном цикле. Это обусловливает его применение при больших партиях и больших трудоемкостях изделий в серийном и крупносерийном производстве.
7.6 Производственная структура предприятия Иерархия производственных систем. Каждое объединение и предприятие
характеризуется конкретным составом его подразделений, специализированных на выполнении определенных производственных функций или выпуске конкретной номенклатуры продукции и имеющих в соответствии с этим конкретную совокупность связей с другими подразделениями. По своему административнохозяйственному статусу объединения, предприятия и их подразделения образуют определенную иерархию производственных систем.
Иерархия производственных систем - это множество типов производственных систем, упорядоченное по отношению включения их друг в друга.
96
В приведенной иерархии каждый тип производственных систем принадлежит к определенному иерархическому уровню, а стрелки выражают наличие и направление отношения включения между системами соответствующих типов, показывая, что производственная система определенного типа включает производственную систему другого типа. Эта иерархия такова, что производственная система определенного иерархического уровня может непосредственно включать производственные системы не только следующего более низкого, но и еще более низких иерархических уровней.
Таким образом иерархическая производственная структура предприятия представляет собой совокупность вертикально соподчиненных его подсистем
(корпуса, цехи, отделы, участки, бюро, лаборатории, бригады, группы и элементарные производственные системы) и форм их взаимосвязей.
Корпус (отделение). На крупных предприятиях и в крупных структурных единицах выделяются административно и хозяйственно обособленные производственные системы типа корпуса (отделения), каждая из которых включает совокупность цехов (отделов), охватывает ряд технологически взаимосвязанных стадий процесса производства большего количества видов продукции или всю совокупность стадий по производству определенного вида продукции. По административ- но-хозяйственной обособленности, самостоятельности, обязанностям и ответственности корпус (отделение) значительно уступает структурной единице объединения, в частности не имеет отдельного баланса и текущего счета и не может вступать в самостоятельные хозяйственно-правовые отношения с внешними для предприятия (НИИ, КБ) системами. Тем не менее за ним закрепляются основные фонды и оборотные средства, он обладает значительными правами в области управления и организации производства и может функционировать на началах хозрасчета.
Цех (отдел). Это тип административно и хозяйственно обособленных производственных систем, каждая из которых специализирована на выполнении однородных технологических стадий процесса производства или на выпуске ограниченной номенклатуры продукции определенного вида.
Административно-хозяйственные обособленность, самостоятельность, обязанности и ответственность цеха (отдела) значительно меньше, чем у структурной единицы объединения. Цех (отдел) имеет закрепленное за ним имущество, однако он не имеет отдельного баланса и текущего счета в банке, не может вступать в хо- зяйственно-правовые отношения с внешними для структурной единицы или предприятия (НИИ, КБ) хозяйственными системами. Если цех (отдел) является непосредственной подсистемой корпуса (отделения), то его административнохозяйственная обособленность и самостоятельность также меньше, чем у последнего.
97
8 Организация поточного и автоматизированного производств
8.1 Сущность и характеристика поточного производства
Поточное производство является наиболее прогрессивной и эффективной формой организации производственного процесса. Его важнейшими признаками являются: закрепление одного или ограниченного числа наименований изделий за определенной группой рабочих мест; ритмичная повторяемость согласованных во времени технологических и вспомогательных операций; выполнение на каждом рабочем месте одной или небольшого числа операций, что обеспечивает узкую специализацию рабочих мест; расположение оборудования и рабочих мест по ходу технологического процесса с наименьшими пространственными разрывами; поштучная или небольшими транспортными партиями передача изделий с операции на операцию с минимальными перерывами во времени при помощи специальных транспортных средств.
Поточное производство обладает основными чертами передовой организации производственного процесса, поскольку в наибольшей степени реализует научные принципы организации: специализацию, параллельное выполнение работ, пропорциональность, прямоточность, непрерывность, ритмичность процесса производства.
Детальное расчленение технологического процесса, создающее предпосылки для автоматизации производства и быстрого обучения рабочих, совершенная организация труда и производства способствуют достижению в условиях поточного производства высокого уровня технико-экономических показателей и качества работы. Поточное производство обеспечивает самую высокую производительность труда, низкую себестоимость продукции, наиболее короткую продолжительность производственных циклов при высоких показателях использования производственных фондов.
Первичным звеном поточного производства является поточная линия — группа рабочих мест, на которой производственный процесс осуществляется в соответствии с характерными признаками поточного производства. Организация поточных линий предъявляет специфические требования к планировке оборудования производственных участков и цехов, к транспорту и таре, применяющимся на поточных линиях.
Планировка поточных линий должна обеспечивать наибольшую прямоточность и кратчайший маршрут движения изделия; наиболее рациональное использование производственной площади; наилучшие условия для транспортировки материалов и деталей к рабочим местам; удобство подходов для обслуживания и ремонта; достаточность площадей и устройств для хранения требуемых запасов материалов и деталей.
Пример расположения оборудования и пути движения изделия при односторонней, двусторонней и зигзагообразной расстановке оборудования приведены
98
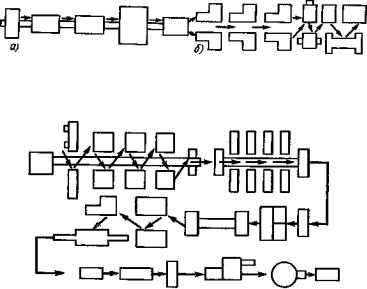
на рис. 8.1 и 8.2. В зависимости от конструкции производственного здания, вида выпускаемых изделий и используемого оборудования могут разрабатываться планировки овальных, Т-образных, П-образных, круговых поточных линий.
В поточном производстве применяются самые разнообразные транспортные средства: склизы, желоба, транспортеры (ленточные и подвесные), пневмотранспортные средства, промышленные роботы, универсальные манипуляторы с программным управлением и др. В радиопромышленности широко применяются конвейеры — транспортные средства, служащие для транспортировки изделия или транспортировки и выполнения на нем рабочих операций и регламентирующие ритм работы поточной линии, т. е. играющие организующую роль в потоке. В том случае, если конвейер служит для перемещения изделий и поддержания ритма работы линии путем
Рис. 8.1 Движение изделия на поточной линии при расположении оборудования: а — одностороннем, б — двустороннем
Рис. 8.2. Схема зигзагообразной поточной линии с односторонним и двусторонним расположением оборудования
четкого адресования изделий по рабочим местам, он называется распределительным, если же он служит и местом выполнения операции, то называется рабочим.
Конвейер может быть непрерывного действия и пульсирующим. В последнем слу-
чае конвейер, переместив изделие с предыдущей операции на последующую, останавливается на время выполнения операции и затем снова приходит в движение.
8.2 Классификация поточных линий
Все разнообразие применяемых в отрасли поточных линий можно классифицировать по ряду признаков.
По степени механизации т е х н о л о г и ч е с к и х операций поточные линии делятся на механизированные, комплексно-механизированные, полуавтоматические и автоматические.
В зависимости от количества т и п о в одновременно о б р а б а т ы в а е - м ы х и с о б и р а е м ы х изделий поточные линии подразделяются на однопред-
99
метные (их называют также однономенклатурные) и многопредметные (многономенклатурные). На однопредметной линии обрабатывается или собирается изделие одного наименования, на многопредметной — изделия нескольких наименований, их обработка или сборка ведется (последовательно или одновременно) по типовому технологическому процессу.
В зависимости от количества о д н о в р е м е н н о обрабатываемых объектов одного н а и м е н о в а н и я линии делятся на однопоточные и многопоточные. Иногда (это характерно для электронной промышленности) операции с поштучной обработкой изделий на одних операциях чередуются с обработкой изделий партиями на других операциях, что существенно усложняет расчеты и плани-
рование. |
|
В зависимости от х а р а к т е р а |
д в и ж е н и я и з д е л и й по операциям |
п р о и з в о д с т в е н н о г о п р о ц е с с а |
следует различать прерывно-поточные и |
непрерывно-поточные линии. На непрерывно-поточной — все операции равны или кратны ритму линии, т. е. синхронизированы во времени. Ритм непрерывнопоточных линий может быть принудительным (регламентированным) или свободным, поддерживаемым самими рабочими. На прерывно-поточных— операции (все или часть из них) не выровнены согласно ритму линии. Непрерывно-поточные линии применяются, главным образом, при высоком удельном весе ручных работ (конденсаторостроение, производство резисторов и др.). Преобладающим типом поточных линий в отрасли являются прерывно-поточные. Это объясняется рядом специфических особенностей производства, к числу которых можно отнести: наличие планируемых технологических потерь, объем которых является вероятностной величиной; чередование операций с поштучной и партионной обработкой изделий; необходимость длительного вылеживания отдельных групп приборов для стабилизации их параметров; наличие большого количества контрольноизмерительных операций и оборудования с непрерывным режимом работы и др. Все эти причины ведут к перерывам в ходе производственного процесса и невозможности осуществить синхронизацию технологических операций во времени. На рис. 8.3 приведена классификация поточных линий.
8.3 Расчет поточных линий
При проектировании и организации поточных линий выполняются расчеты ряда показателей, которые определяют регламент работы линии и методы выполнения технологических операций.
Под тактом поточной ланий понимается промежуток времени между выпуском отдельных изделий (деталей, сборочных единиц) с последней операции или их запуском на первую операцию поточной линии. Исходными данными для расчета такта линии является производственное задание на год (месяц или смену), плановый фонд рабочего времени за этот же период и планируемые пооперационные технологические потери.
100