

ских строительных конструкций выполняются с учетом требований и рекомендаций следующей нормативно-технической и нормативнотехнологической документации, а именно: 156, 161, 226, 227, 233, 241-243, 246-272, 273-308, 309-384.
Практическая работа № 11 ЭЛЕКТРИЧЕСКИЙ НЕРАЗРУШАЮЩИЙ КОНТРОЛЬ
Сконтролю качества определяются нормативными документами, в том числе требован ями государственного стандарта [162], правил эксплуатац [164] стандарта организации [165].
Общ е положен я, правила и контроль выполнения, а также требован я к результатам работ по электрическому неразрушающему
кающие анализе параметровбАэлектрического поля или электрического тока,
Электр ческ й неразрушающий контроль качества основан на
которые вза модействуют с контролируемыми объектами или возни- в стро тельных конструкциях, и соответственно в целом в зданиях сооружен ях, т.е. в контролируемых объектах, в результате
внешнего воздейств я.
То есть электрический метод неразрушающего контроля качества основан на регистрации параметров электрического поля (тока), взаимодействующего с контролируемыми объектами.
При этом на практике применяются следующие методы электриче-
|
Д |
||
ского неразрушающего контроля качества, которые указаны в табл. 12. |
|||
|
|
Таблица 12 |
|
Термины электрического кон- |
|
Определения электрического |
|
троля качества |
|
контроля качества |
|
1. Термоэлектрический метод |
|
И |
|
|
Метод электрического неразру- |
|
|
контроля качества представляет |
|
шающего контроля, основанный на ре- |
|
|
|
гистрации величины термо- э.д.с, воз- |
|
|
|
никающей при прямом контакте нагре- |
|
|
|
того образца известного материала с |
|
|
|
объектами контроля. |
|
2. Трибоэлектрический метод |
|
Метод электрического неразру- |
|
контроля качества представляет |
|
шающего контроля, основанный на ре- |
|
|
|
гистрации величины электрических за- |
|
|
|
рядов, возникающих в объекте контро- |
|
|
|
ля при трении разнородных материа- |
|
|
|
лов. |
|
92
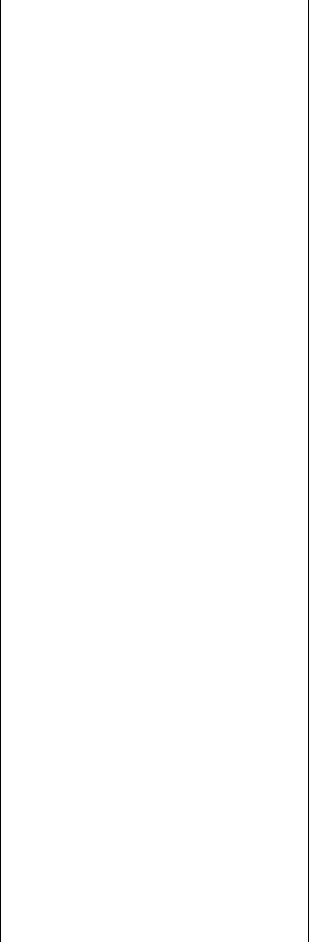
|
3. Электропотенциальный ме- |
|
Метод |
электрического |
неразру- |
|
|||
|
тод контроля качества представляет |
|
шающего контроля, основанный на ре- |
|
|||||
|
|
|
|
гистрации распределения потенциалов |
|
||||
|
|
|
|
по поверхности объектов контроля. |
|
||||
|
|
|
|
|
|
|
|||
|
4. Электроемкостный метод |
|
Метод |
электрического |
неразру- |
||||
|
контроля качества представляет |
|
шающего контроля, основанный на ре- |
|
|||||
|
|
|
|
гистрации |
емкости участка |
объекта |
|
||
|
|
|
|
контроля. |
|
|
|
|
|
|
5. Электростатический |
|
|
Метод |
электрического |
неразру- |
|
||
|
порошковый метод контроля |
|
|
шающего контроля, основанный на ре- |
|
||||
С |
|
|
гистрации |
электростатических полей |
|
||||
|
|
рассеяния с использованием в качестве |
|
||||||
|
|
индикатора |
наэлектризованного по- |
|
|||||
|
|
рошка. |
|
|
|
|
|
||
|
|
|
|
|
|
|
|
|
|
|
6. Электропараметр |
ме- |
Метод |
электрического |
неразру- |
|
|||
|
тод контроля качества представляет |
|
шающего контроля, основанный на ре- |
|
|||||
|
ческий |
гистрации |
электрических |
характери- |
|
||||
|
стик объекта контроля. |
|
|
|
|||||
|
7. Электро скровой метод кон- |
Метод электрического неразру- |
|
||||||
|
троля качества представляет |
|
|
шающего контроля, основанный на ре- |
|
||||
|
|
|
|
гистрации |
возникновения |
электриче- |
|
||
|
|
|
|
ского пробоя и (или) изменений его |
|
||||
|
|
|
|
параметров |
в окружающие |
объекты |
|
||
|
|
|
|
контроля среде или на его участке. |
|
||||
|
8. Метод реком инационного |
|
Метод |
электрического |
неразру- |
|
|||
|
излучения |
|
|
шающего контроля, основанный на ре- |
|
||||
|
|
|
|
гистрации рекомбинационного излуче- |
|
||||
|
|
|
|
ния р-n переходов в полупроводнико- |
|
||||
|
бА |
|
|
|
|||||
|
|
|
|
вых изделиях. |
|
|
|
||
|
9. Метод экзоэлектронной |
|
Метод |
электрического |
неразру- |
|
|||
|
эмиссии |
|
|
шающего контроля, основанный на ре- |
|
||||
|
|
|
|
гистрации экзоэлектронов, эмитиро- |
|
||||
|
|
|
|
ванных поверхностью контролируе- |
|
||||
|
|
|
Д |
|
|||||
|
|
|
|
мых объектов при приложении к ним |
|
||||
|
|
|
|
внешнего |
стимулирующего |
|
воздейст- |
|
|
|
|
|
|
вия. |
|
|
|
|
|
|
10. Метод контактной разности |
Метод электрического неразру- |
|
||||||
|
потенциалов |
|
|
шающего контроля, основанный на ре- |
|
||||
|
|
|
|
гистрации |
Иконтактной разности потен- |
|
|||
|
|
|
|
циалов на участках объектов контроля, |
|
||||
|
|
|
|
через которые пропускается электри- |
|
||||
|
|
|
|
ческий ток. |
|
|
|
|
|
|
|
|
|
|
|
|
|
|
|
93

|
Также применяются следующие средства электрического неразрушающе- |
|||
|
го контроля качества, а именно: |
|
|
|
|
|
|
|
|
|
1. Прибор электрического не- |
Прибор, |
предназначенный для |
|
|
разрушающего контроля качества |
выявления дефектов на объектах кон- |
||
|
|
троля, основанный на методе электри- |
||
|
|
ческого неразрушающего контроля. |
||
|
2. Термоэлектрический прибор |
Прибор |
электрического |
нераз- |
С |
рушающего контроля, основанный на |
|||
|
|
|||
|
|
термоэлектрическом методе. |
|
|
|
3. Электропотенциальный |
Устройство, состоящее из двух |
||
|
преобразователь |
или более токопроводящих и двух или |
||
|
и |
более потенциальных электродов и |
||
|
предназначенное для регистрации раз- |
|||
|
|
|||
|
|
ности потенциалов на контролируемых |
||
|
|
участках объектов контроля. |
|
|
|
4. Электр ческ й дефектоскоп |
Прибор |
электрического |
нераз- |
|
|
рушающего контроля, предназначен- |
||
|
бА |
|
||
|
|
ный для обнаружения несплошностей |
||
|
|
и неоднородностей в объектах контро- |
||
|
|
ля. |
|
|
|
5. Электр ческ й змеритель |
Прибор |
электрического |
нераз- |
|
глуб ны трещ н |
рушающего контроля, предназначен- |
||
|
|
ный для измерения глубины трещин. |
В качестве примера рассмотрим термоэлектрический дефекто- скоп-толщиномер ТЭС-364М, предназначенный для контроля структурного состояния поверхностногоДслоя сталей, слоя, связанного с химическим составом, термообработкой, толщиной поверхностноупрочненных слоев и проводящих гальванических покрытий.
Основной областью применения термоэлектрического дефекто- скопа-толщиномера ТЭС-364М является рассортировка металлов, в том числе по маркам, а также контроль Икачества поверхностноупрочненных слоев сталей, то есть задачи толщинометрии которые неудовлетворительно решаются основными методами.
Применение термоэлектрического дефектоскопа-толщиномера ТЭС-364М предоставляет возможность измерения толщины тонких проводящих покрытий и слоев на металлическом основании, в случае наличия достаточной величины термо-э.д.с. «покрытие-основание».
Основными преимуществами прибора ТЭС-364М являются:
-рассортировка металлов по маркам (по величине термо-э.д.с.), то есть на достаточно большой скорости;
-высокая локальность контроля качества структурного состояния поверхностного своя сталей, недостижимая другими методами;
94

- автоматический перевод измеренных значений термо-э.д.с. в значения контролируемых технологических параметров металла, в том числе толщин и твердости, а также марок металла;
- малая чувствительность прибора к кривизне металлических изделий, строительных конструкций, и соответственно в целом или отдельных частей зданий и сооружений (объектов контроля).
При этом интуитивно понятный русский интерфейс термоэлек-
Стрического дефектоскопа-толщиномера ТЭС-364М обеспечивает ра-
боту оператора по принципу «включай и измеряй».
Основными техн ческими характеристиками термоэлектрического дефектоскопа-толщ номера ТЭС-364М являются характеристики, которые
указаны в табл це 13.
Таблица 13
|
Характер ст ка |
|
|
Параметр |
|||
|
|
|
|||||
|
Пр веденная |
разрешешающая |
|
5 мкВ |
|||
|
способность |
определении терм-эдс: |
|
||||
|
|
|
|||||
|
при |
|
|
||||
|
Температура зоны контакта нако- |
|
|
||||
|
нечника датч ка |
|
поверхности контро- |
|
не менее 100 С |
||
|
лируемого участка: |
|
|
|
|
||
|
Локальность |
контролируемого |
|
1,5 х 1,5 мм |
|||
|
участка: |
|
|
|
|
|
|
|
|
|
|
|
|
|
|
|
Количество |
запоминаемых |
10 |
||||
|
корреляциоонных взаимосвязей: |
|
|||||
|
|
|
|
||||
|
|
|
|
|
|||
|
Пороговая сигнализация: |
|
|
есть |
|||
|
|
бА |
|||||
|
Время подготовки к работе: |
|
|
не более 2 мин |
|||
|
|
|
|
|
|
|
|
|
Питание: |
|
|
|
|
сетевое 200В или от выносного |
|
|
|
|
|
|
аккумулятора - по требованию |
||
|
|
|
|
|
|
|
|
|
|
|
|
|
|
Д |
|
|
При этом требования к контролируемым металлическим изделиям, а |
||||||
|
также к строительным конструкциям, и соответственно к объектам кон- |
||||||
|
троля, заключаются в следующем: на контролируемой поверхности объ- |
ектов контроля, а именно в области контактаИгорячего наконечника датчика с поверхностью не допускаются следы окалины, а также следы гальванических и лакокрасочных покрытий, различных загрязнений.
Комплектность поставки термоэлектрического дефектоскопатолщиномера ТЭС-364М состоит из следующего, что указано в табл. 14.
95

Таблица 14
|
Характеристика |
|
|
Параметр |
|
|
|
|
|||
|
Электронный блок дефектоскопа- |
|
1 шт. |
||
|
толщиномера |
|
|
|
|
|
|
|
|
|
|
|
Датчик |
|
|
|
1 шт. |
|
|
|
|
|
|
С |
|
|
|
1 шт. |
|
|
етевой адаптер |
|
|
||
|
Руководство по эксплуатации (со- |
|
1 шт. |
||
|
вмещено с паспортом) |
|
|
||
|
|
|
|
||
|
|
|
|
|
|
|
Образцы |
для |
контроля |
|
2 шт. (закреплены на корпусе |
|
работоспособности |
|
|
|
прибора) |
|
|
|
|
||
|
умка для переноски и хранения |
|
1 шт. |
||
|
|
|
|
|
|
В качестве дополн тельных принадлежностей в комплектность потермоэлектр ческого дефектоскопа-толщиномера входят следую-
прибора бора о дате поверки приАора.
щие пр надлежности, а менно: |
|
ставки- выносной аккумулятор для |
; |
- зарядное устройство для аккумулятора прибора; |
|
- св детельство о поверке |
или отметка в паспорте при- |
Практические ра оты с применением электрического нераз-
рушающего контроля качества предусматривают выполнение работ по данному контролю качества с орных и монолитных железобетон-
1.Сборных и монолитных железобетонныхДфундаментов, в том числе ростверков и свайных оснований.
2.Сборных и монолитных железобетонных строительных конструкций. И
3.Металлических строительных конструкций.
нормативно-технической и нормативно-технологической документа-
ции, а именно: 163, 226, 227, 233, 241-243, 246-272, 309-384.
96
Практическая работа № 12
УЛЬТРАЗВУКОВОЙ НЕРАЗРУШАЮЩИЙ КОНТРОЛЬ
Общие положения, правила и контроль выполнения, а также требования к результатам работ по ультразвуковому неразрушающему контролю качества определяются нормативными документами, в том числе требованиями государственных стандартов [167], [170],
Сний (объекты контроля) является ультразвуковая дефектоскопия.
[173], [174] и стандартов организаций [177], [179], [180].
Пр мером ультразвукового неразрушающего контроля качества строительных конструкц й, и соответственно в целом зданий и сооруже-
илиПри этом при ультразвуковой дефектоскопии решаются следующ е основные задачи на о ъектах контроля, а именно:
- обнаружен е дефектов на объектах контроля; - класс ф кац я дефектов, то есть отнесение дефектов к тому
иномубт пу, в том числе: трещины, раковины, включения, непровары т.д., при выполнении сварочных работ на объектах контроля;
- определен е координат и размеров дефектов; - определен е степени опасности дефектов на объекты контроля.
Для решения указанныхАвыше поставленных основных задач применяются следующие ультразвуковые методы неразрушающего контроля качества и нео ходимое оборудование, которое реализует эти методы, а именно:
1.Оборудование для ультразвукового контроля качества можно разделить на следующие основные типы:
а) ультразвуковые дефектоскопы с преобразователями для возбуждения и регистрации акустических волн и колебаний;
в) комплекты эталонов и тест-образцов для проверки и настройки приборов ультразвукового контроля качества;
с) диаграммы для определения размеров дефектов на объектах контроля;
д) вспомогательные приспособления для выполнения ультразвукового контроля качества.
2.Технологический процесс для ультразвукового контроля качества включает следующие последовательно выполняемые операции, а именно:
- оценка дефектоскопийности изделий, строительных конструкций, и соответственно в целом дефектоскопийности зданий и сооружений;
- подготовка объектов к контролю качества; - настройка оборудования для осуществления ультразвукового кон-
троля качества объектов контроля; - поиск и обнаружение дефектов, определение их размеров и формы;ДИ
97
-оценка качества изделий, строительных конструкций, и соответственно в целом зданий и сооружений, т.е. допустимости дефектов;
-оформление результатов ультразвукового контроля качества.
При этом рассмотрению подлежат основные этапы технологического процесса ультразвуковой дефектоскопии на примере эхо- и теневого методов контроля, в том числе рассмотрим способы ввода и приема упругих волн в объектах контроля, которые являются залогом успешного решения задач ультразвукового контроля качества по обеспечению высокой стабильности ввода в контролируемый объект и приема акустических волн, в результате анализа параметров которых делается заключение о наличии и характер ст ках обнаруженных дефектов на объектах контроля.
В современных дефектоскопах для излучения и приема ультразвуковых волн чаще всего спользуются пьезопреобразователи.
3. |
этом существует несколько способов ввода ультразвуковых |
С |
|
волн в контрол руемые о ъекты и приема сигналов, а именно: |
|
а) бесконтактный способ ввода ультразвуковых волн; |
преобразователем ный зазор толщиной неАолее определенных значений, т.е. прозрачный для
в) контактный способ ввода ультразвуковых волн; с) ммерс онный способ ввода ультразвуковых волн;
д) струйный способ ввода ультразвуковых волн. |
|
При |
|
Бесконтактный способ ввода ультразвуковых волн указывает на то, |
|
что между |
и ъектами контроля существует воздуш- |
ультразвуковых волн. Этот способ требует высокого качества поверхности объектов контроля и применяется для ввода низкочастотных волн.
Контактный способ ввода ультразвуковых волн указывает на то, что преобразователь вводят в контакт с поверхностью объектов контроля. При этом если осуществляется контрольДна низких частотах, то используют сухой контакт. При ультразвуковом контроле качества на частотах более 10 кГц, ввод ультразвуковых волн осуществляется через слой масла.
Иммерсионный способ ввода ультразвуковых волн указывает на то, что между преобразователем и изделиями, строительными конструкциями,
-высокая стабильность излучения иИвысокая стабильность приема ультразвуковых волн;
-отсутствие износа преобразователя для излучения и приема ультразвуковых волн;
-достаточно низкие требования к качеству поверхности объектов контроля.
Струйный способ ввода ультразвуковых волн указывает на то, что контакт преобразователя с объектами контроля обеспечивается непрерывной струей жидкости. При этом толщина слоя жидкости регулируется зазором между преобразователем и изделиями, строитель-
98
ными конструкциями, и соответственно в целом зданиями и сооружениями. Струйный способ ввода ультразвуковых волн применяется при контроле качества вертикальных поверхностей или поверхностей с переменной кривизной на объектах контроля.
В зависимости от способа ввода ультразвуковых колебаний используются различные типы преобразователей, которые классифицируются по следующим признакам, а именно:
а) преобразователи различаются по способу введения ультразвуковых волн, в том числе:
- контактные преобразователи; - ммерс онные преобразователи;
в) преобразователи различаются по назначению, в том числе: |
|
- нормальные (прямые) преобразователи для возбуждения про- |
|
С |
|
дольных ультразвуковых волн; |
|
- наклонные (пр зматические) преобразователи для возбужде- |
|
нормальных поперечных поверхностных ультразвуковых волн. |
|
с) |
различаются по функциональным призна- |
ния кам, в томпреобразователич сле:
- раздельные прео разователи;
- совмещенные прео разователи; А
- раздельно-совмещенные преобразователи.
При этом основными конструктивными элементами преобразователей являются:
1)пьезопластина;
2)демпфер;
3)протектор;
4)корпус;
5)призма предусмотрена в наклонных и раздельносовмещенных преобразователях.
Впреобразователях конструктивный элемент демпфер служит для ослабления свободных колебаний пьезопластины, а также для управления добротностью преобразователя и защиты пьезопластин от механических повреждений.
При этом материал и форма демпфера должна обеспечивать полное затухание и отвод колебаний, которые излучаются пьезопластиной без многократных отражений в преобразователе. В том числе ослабление колебаний пьезопластины тем сильнее, чем лучше согласованы импедансы пьезопластины и демпфера.
Вкачестве основного материала для демпфера используются
эпоксидные смолы с добавкой порошковых наполнителей, которые обладают высокой насыпной плотностью, необходимой для получе-И
99
ния требуемого характеристического импеданса (вольфрам, свинец или их соединения).
При этом для уменьшения многократного отражения демпфер выполняется в виде конуса. В некоторых случаях в виде конуса выполняется тыльная поверхность демпфера. Также в некоторых случаях в материал демпфера вводятся рассеиватели.
|
В преобразователях протектор служит для защиты пьезопластин |
|||
С |
|
|||
от механических повреждений и от воздействия иммерсионной или |
||||
контактной жидкости, а также служит для согласования импеданса |
||||
пьезопласт ны с |
|
мпедансом контролируемого объекта. |
||
|
При этом матер ал протектора должен обладать высокой изно- |
|||
ли |
||||
состойкостью |
высокой скоростью звука (кварц, сапфир, керамика, |
|||
эпоксидные смолы с порошковыми наполнителями в виде кварцевого |
||||
песка |
|
корундового порошка и др.). Толщина протектора состав- |
||
ляет 0,1…0,5 мм. |
|
|||
|
|
преобразователях |
||
|
Как прав ло, спользуются четвертьволновые протекторы, ко- |
|||
торые обеспеч вают просветление границы пьезопластина-жидкость. |
||||
|
В |
|
|
призма изготавливается из материала с не- |
большой скоростью звука (оргстекло; капролон и др.), что позволяет |
||||
при относ тельно не ольших углах падения волны получить большие |
||||
|
|
|
|
А |
углы преломления данной волны.
При этом высокое затухание ультразвука в призме обеспечивает ослабление волны, которое также увеличивается за счет многократных переотражений. Для улучшения данного эффекта в призме часто
тельным затуханием ультразвука.Д При возбуждении в объектах контроля ультразвуковых волн од-
используется ловушка, которая удлиняет путь отраженных волн, в частности, на пути волны располагаются небольшие отверстия. Также для обеспечения ослабления волны грани призмы выполняются реб-
ристыми или приклеивают к граням призмы материалы с приблизи-
тельно одинаковым характеристическим импедансом, но со значи- И
ного типа угол наклона призмы делают либо небольшим (при этом
поперечные волны практически не возбуждаются), либо выбирают угол наклона в интервале между первым и вторым критическими углами. В данном случае продольные ультразвуковые волны трансформируются в поперечные.
При этом призмы с углами 60º (оргстекло – сталь) применяются для возбуждения волн Рэлея.
Для получения произвольных углов ввода ультразвуковых волн применяются универсальные преобразователи, то есть с переменным углом ввода ультразвуковых волн.
100
В раздельно-совмещенных преобразователях излучатель и приемник ультразвуковых волн разделены акустически, но при этом объединены конструктивно в одном корпусе. Преимуществом данного преобразователя является то, что излучающий (зондирующий) импульс практически не попадает на приемник. В результате данного
преимущества |
«мертвая зона» уменьшается до 1…2 мм, вместо |
5…10 мм для прямых преобразователей. Также изменяя углы призм в |
|
С |
|
раздельно-совмещенном преобразователе можно менять глубину про- |
|
звучивания объектов контроля. |
|
При этом |
ммерс онные и щелевые преобразователи отличают- |
ся от прямых преобразователей тем, что имеют повышенный импе- |
|
данс демпфера. Для данных преобразователей протектор изготавлива- |
|
ется, как прав ло, з эпоксидной смолы толщиной равной четверти |
волны, которая о еспечивает просветление границы пьезоэлемент – г дро золяц я – иммерсионная жидкость.
торых сохраняютсябАдостоинства иммерсионного способа без приме-
Также основным достоинством иммерсионных преобразовате-
лей является ста |
льность акустического контакта. Поэтому разрабо- |
таны конструкц |
локально-иммерсионных преобразователей, в ко- |
длины |
нения громоздкой ванны для жидкости.
При этом одна из стенок корпуса локально-иммерсионных преобразователей выполняется в виде мембраны, которая препятствует вытеканию жидкости, и хорошо прилегает к неровностям поверхности объектов контроля. В данном случае мембрана выполнена из маслостойкой резины или полиуретана, характеристический импеданс которых близок к импедансу воды, поэтому ультразвуковая волна
В щелевом преобразователеДмембрана не соприкасается непосредственно с поверхностью объектов контроля. При этом между мембраной и объектами контроля имеется слойИводы. анный вариант предохраняет мембрану от износа и улучшает возможности контроля изделий, строительных конструкций, и соответственно объек-
практически от нее не отражается.
тов контроля, с грубой поверхностью.
При этом волновые сопротивления сред между мембраной и жидкостью, а также сверху и снизу от мембраны, подбираются максимально одинаковыми (приближенными), что сводит к минимуму эффект отражения ультразвуковой волны. Для устранения эхосигнала от мембраны ее располагают под углом 80…85º к акустической оси преобразователя. Небольшие размеры нижней части ванны для жидкости позволяют обеспечить требуемое заполнение ванны при небольшом расходе жидкости.
101
Основными требованиями к преобразователям, при их разработке для эхо- и теневых дефектоскопов, являются следующие:
- максимальная чувствительность, то есть максимальные значения модуля коэффициента преобразования на определенной оптимальной рабочей частоте ультразвуковой волны;
- максимальная ширина пропускания частот, которая определяется амплитудно-частотной характеристикой. При этом широкопо- Слосность преобразователя обеспечивает возможность излучения и приема коротких акустических импульсов без искажения их формы.
Данное свойство важно для достижения минимального значения «мертвой зоны» при контроле эхо-методом.
- в связи с тем, что отраженные от дефектов импульсы по ам- амплитудаплитуде всегда меньше излучаемого — зондирующего, поэтому, пока зонд рующего импульса не уменьшится в 10…102 раза,
отраженный от дефектов импульс не может быть надежно зарегистрирован;
- дост жен е максимальной стабильности акустического контакта;
-сн жен е шумов прео разователей. При этом главным источником шумов прео разователей является многократное отражение ультразвуковых волн в протекторе, демпфере и других его элементах;
-согласование (приведение в соответствие) полного электрического импеданса прео разователей с выходным импедансом генераторов и входным усилителем дефектоскопов;
-оптимизация акустического поля преобразователей.
-повышенная износостойкость преобразователей, которая зависит от сопротивления истиранию протекторов.
Практические работы с применением ультразвукового не-
разрушающего контроля качества предусматривают выполнение работ по данному контролю качества сборных и монолитных бетонных и железобетонных строительных конструкций, а также металлических строительных конструкций, а именно:
1.Сборных и монолитных бетонных и железобетонных фундаментов, в том числе ростверков и свайных оснований.
2.Сборных и монолитных бетонных и железобетонных строительных конструкций.
3.Металлических строительных конструкций.бАИ
Работы по организации ультразвукового неразрушающего контроля качества сборных и монолитных бетонных и железобетонных строительных конструкций, а также металлических строительных конструкций выполняются также с учетом требований и рекоменда-
102
ций следующей нормативно-технической и нормативнотехнологической документации, а именно: 166, 168, 169, 171, 172, 175, 176, 178, 181, 226, 227, 233, 241-243, 246-272, 309-384.
Практическая работа № 13
МОЛЕКУЛЯРНЫЙ НЕРАЗРУШАЮЩИЙ КОНТРОЛЬ
Общие положения, правила и контроль выполнения, а также требован я к результатам работ по молекулярному неразрушающему контролю качества определяются нормативными документами, в том числе требован ями государственных стандартов [182], [183] и руко-
водящего документа [184]. |
|
С |
|
Одн м |
з основных методов неразрушающего контроля качест- |
ва является молекулярный, основанный на неразрушающем контроле |
|
качества |
кающ ми веществами, то есть регистрации вещества |
|
в полости дефектов или проникающего через полости |
модейств я.
дефектов |
здел й, стро тельных конструкций, и соответственно в це- |
проникающего |
|
лом здан |
й сооружений, в результате их межмолекулярного взаи- |
|
бА |
При этом термин «проникающими веществами» может быть изменен на «капиллярный», а при выявлении сквозных дефектов на «те-
чеискание».
Молекулярный неразрушающий контроль качества имеет сле-
дующую классификацию:
- вид контроля осуществляется проникающими веществами; - по характеру взаимодействия физических полей с контроль-
ными изделиями, строительными конструкциями, и соответственно со |
|
зданиями и сооружениями данный контроль есть молекулярный; |
|
|
И |
- по первичному информационному параметру определяется как |
|
жидкостный и газовый; |
Д |
- по способу получения первичной информации определяется как яркостный (ахроматический), цветной (хроматический), люминесцентный, люминесцентно-цветной, фильтрующихся частиц, массспектрометрический, пузырьковый, манометрический и галогенный.
Суть физических явлений при молекулярном неразрушающем контроле качества заключается в следующем:
- важной характеристикой индикаторных жидкостей является их способность к смачиванию материала изделия, строительных конструкций. Смачивание вызывается взаимным притяжением атомов и молекул проникающей жидкости и твердого тела;
103
- в связи с тем, что между молекулами среды действуют силы взаимного притяжения, молекулы находящиеся внутри проникающего вещества испытывают со стороны других молекул в среднем одинаковое действие по всем направлениям., а молекулы находящиеся на поверхности подвергаются не одинаковому притяжению со стороны внутренних слоев проникающего вещества и со стороны граничащей с поверхностью среды;
Сбольше чем энерг я внутренних молекул, когда проникающая жидкость ли твердое тело находятся в газе или в вакууме, в связи с этим стремятся пр о рести форму с минимальной наружной поверхностью. Также в твердом теле этому препятствует явление упругости
- поведение системы молекул определяется условием минимума свободной энергии, т.е. той части потенциальной энергии, которая
изотерм чески может обратиться в работу. При этом свободная энергия молекул на поверхности проникающей жидкости и твердого тела
онитак , поверхности проникающей жидкости и твердого тела стремятся сократиться, и в результате чего возникает давление
формы, а прон кающая жидкость в невесомости под влиянием данного явлен я пр обретает форму шара;
поверхностного натяжения; - в капиллярном методе контроля качества главным образом,
для проявления, используют явление физической адсорбции прони- |
|
образом |
|
кающей жидкости (пенетранта) на поверхности твердого тела (частиц |
|
проявителя), данное явление также вызывает осаждение на дефекте |
|
контрастных проникающих веществ, растворенных в жидкой основе |
|
пенетранта. |
А |
|
|
Цветная дефектоскопия как дефектоскопический метод иссле- |
дования, при помощи проникающих жидкостных веществ в повреж- |
|
денные поверхности, широко используется для определения целост- |
|
|
И |
ности деталей, изделий, строительных конструкций, и соответственно |
|
в целом зданий и сооружений. |
Д |
Цветная дефектоскопия физически возможна благодаря существованию капиллярного давления, вследствие чего повышается световая и цветовая контрастность контролируемого участка. Данный метод дает возможность выявить дефекты, которые слишком малы для визуального определения и неконтрастны для луп и микроскопов.
При этом жидкий индикаторный раствор или суспензия проникают в полости и недостатки, а нецелостность деталей, изделий, строительных конструкций, и соответственно в целом зданий и сооружений можно обнаружить и зарегистрировать преобразователями.
104
Специалисты, как правило, используют 2-е разновидности молекулярного неразрушающего контроля, по способу получения первичной информации, это люминесцентную и цветную.
Люминесцентный капиллярный контроль подразумевает проведение капиллярного неразрушающего контроля качества путем регистрации контраста, который светится в УФ – лучах, на фоне базовой поверхности. При этом детали, изделия и строительные конструкции освещаются ультрафиолетовым светом в затемненном помещении, и дефекты (недостатки) хорошо определяются и зрительно видны.
Люм несцентный капиллярный контроль качества проводится при помощи спец альных проникающих жидкостей (пенетрантов), в которых пр сутствует УФ – проникающие вещества, и состоит дан-
ный метод з следующ х этапов работы, а именно: |
|
С |
|
- предвар тельно очистить поверхности деталей, изделий и |
|
конструкций водой или органическими составами для |
|
удален я масел, |
красок, ржавчины и любых других покрытий дета- |
лей, издел й |
конструкций, после чего необходимо |
строительныхтщательно высуш ть х поверхность;
- удалитьбАиз ытки проникающей жидкости (пенетранта), при этом необходимо детали, изделия и строительные конструкции про-
- нанести прон кающую жидкость (пенетрант) на поверхность деталей, здел й стро тельных конструкций распыляя, обрабатывая ее кистью или погружая в ванну с цветным или люминесцентным
раствором;
мыть водой, протереть ветошью и обработать струей воздуха; - нанести проявляющий состав, сразу после удаления избытков
проникающей жидкости (пенетранта), который растворит краситель и «вытянет» проникающую жидкость на поверхность деталей, изделий
и строительных конструкций. |
И |
При этом для исследования результатов потребуется времени |
|
около получаса. |
Д |
Пузырьковая дефектоскопия или метод контроля герметичности основан на регистрации индикаторных жидкостей и газов, которые проникают через сквозные дефекты.
Метод пузырьковой дефектоскопии или метод контроля герметичности предназначен для выявления мест локальных течей, обусловленных наличием сквозных дефектов типа трещин, непроваров, прожогов в сварных строительных изделиях, конструкциях, в листовом прокате и литых строительных изделиях, в том числе при сооружении резервуаров, кессонов, тоннелей, трубопроводов и др.
105
Метод пузырьковой дефектоскопии основан на обнаружении дефектов по образованию и увеличению размеров пузырьков пенообразующей жидкости в местах расположения несплошностей, тоесть основан на способности жидкостей и газов проникать через несплошности деталей, изделий и строительных конструкций.
Данный метод определяется в зависимости от условий эксплуатации деталей, изделий, строительных конструкций, и соответственно в целом зданий и сооружений, типа строительных конструкций и других факторов. При этом метод пузырьковой дефектоскопии осуществляется после внешнего осмотра контрольных, деталей, изделий и строительных конструкций, и соответственно в целом зданий и сооружен й. Для проведения испытаний методом пузырьковой дефек-
тоскоп |
спользуется керосин, аммиак, воздух, вода, гелий и др. |
С |
|
В ж дкостных (г дравлических) методах течеискания в качестве |
|
проникающего вещества используется жидкость, обычно вода, кото- |
рая подается под давлением с одной стороны сварных швов. Дефекты обнаруж ваются по факту появления жидкости с противоположной
Испытан я з ыточным гидравлическим давлением деталей, изделий и строительных конструкций проводятся под давлением в 1,5-2,0 раза превышающее ра очее давление. При этом детали, изделия и строительные конструкции выдерживают под таким давлением определенное время, следя за давлением по манометру, затем их обстукивают молотком, течи выявляются в виде струек и отпотевания поверхностей контролируемых деталей, изделий и строительных кон-
стороны сварных швов. |
этом применяются разные варианты гид- |
При |
|
равлического неразрушающего контроля качества. |
|
бА |
При люминисцентно-гидравлическомДметоде неразрушающего контроля качества не герметичность сварных швов определяется по течи и свечению индикаторной жидкости. ПриИнеобходимости в индикаторную жидкость добавляются радиоактивные вещества, которые дают возможность фиксировать очень мелкие дефекты с помощью
струкций, и соответственно в целом зданий и сооружений.
датчиков ионизирующего излучения. Не герметичность сварных швов проверяют, как правило, керосином используя его высокую проникающую способность, также используются другие пенетранты, например бензин или спирт.
Люминисцентно-гидравлический неразрушающий метод контроля качества состоит из следующих этапов работы:
- контролируемые сварные швы покрываются меловой краской со стороны, доступной для осмотра и устранения дефектов;
106
- затем сварные швы смачиваются керосином с другой стороны и выдерживаются необходимое время, примерно от 15 до 60 мин;
- дефекты сварных швов выявляются по ржавым полосам и пятнам на слое мела, при необходимости в проникающую жидкость добавляется краска или люминофор.
Газоаналитические методы течеискания заключаются в сле-
дующем: с одной стороны сварных швов (в замкнутом изделии,
С |
|
|
|
строительной конструкции) подается пробный газ, с другой стороны |
|||
отбирается проба газа, которая подается в анализатор течеискателя. |
|||
При этом существуют разные схемы контроля качества с помо- |
|||
щью тече скателей, а |
менно: |
|
|
зделий |
|
||
- опрессовка сосуда, когда пробный газ подается под избыточ- |
|||
ным давлен ем внутрь сосуда; |
|
||
- обдув контрол руемых сварных швов пробным газом и отбор |
|||
пробы |
з сосуда; |
|
|
- |
бА |
||
аккумул рован е, когда изделия и строительные конструкции |
|||
выдерж ваются в атмосфере про ного газа, а затем производится от- |
|||
бор пробы газа |
|
строительных конструкций. При этом |
достигается макс мальная чувствительность, но определение места течи затруднено.
Галогенными течеискателями дефекты определяются по изменению ионного тока при пропускании его через промежуток анодколлектор платинового диода газов, содержащих галоиды.
Требования к проникающим жидкостям и газам устанавли-
ваются следующие, исходя из предъявляемым к ним требованиям:
-проникающие вещества должны хорошо проникать через течи
ихорошо обнаруживаться средствами течеискания;
-проникающие вещества должны быть недорогими, не оказывать вредного действия на людей и контрольные изделия, строительные конструкции, и соответственно в целом на здания и сооружения;
-проникающее вещество должно быть подобрано в зависимости от метода испытания и величины испытательного давления, а также конструкции изделий и строительных конструкций, их назначений и нормы герметичности;
-главное требование к проникающим газам, как и ко всем пробным (проникающим) веществам, существование высокочувствительных методов их обнаружения;
-к жидким проникающим веществам, как принято, относят воду, которая применяется при гидроиспытаниях, при этом воду с лю-
минесцирующими добавками применяют для облегчения индикации течей, также применяются водные растворы бихромата калия или на-ДИ
107
трия с технологическими добавками. В некоторых случаях, в качестве проникающих веществ применяются легколетучие жидкости, а именно: этиловый спирт, ацетон, бензин и эфир. Индикаторы улавливают пары этих легколетучих жидкостей, а способы контроля качества такими легколетучими жидкостями относятся к газоаналитическим.
Практические работы с применением молекулярного неразрушающего контроля качества предусматривают выполнение работ
С |
|
|
|
|
по данному контролю качества сборных и монолитных бетонных и |
||||
железобетонных строительных конструкций, а также каменных, ар- |
||||
мокаменных металл ческих строительных конструкций, а именно: |
||||
1. |
борных |
монолитных бетонных и железобетонных фунда- |
||
зации |
|
|||
ментов, в том ч сле ростверков и свайных оснований. |
||||
2. |
борных |
монолитных бетонных и железобетонных строи- |
||
тельных конструкц й. |
|
|
||
3. |
Каменных |
армокаменных строительных конструкций. |
||
4. |
бА |
|||
Металл ческ х строительных конструкций. |
||||
Работы по орган |
|
молекулярного неразрушающего кон- |
||
троля качества с орных |
монолитных бетонных и железобетонных |
строительных конструкций, а также каменных, армокаменных и металлическ х стро тельных конструкций выполняются с учетом требований и рекомендаций следующей нормативно-технической и нор- мативно-технологической документации, а именно: 226, 227, 233, 241-243, 246-272, 273-308, 309-384.
Д Общие положения, правила и контрольИвыполнения, а также
Практическая работа № 14 ВИБРАЦИОННЫЙ НЕР ЗРУШ ЮЩИЙ КОНТРОЛЬ
требования к результатам работ по вибрационному неразрушающему контролю качества определяются нормативными документами, в том числе требованиями государственных стандартов [185], [186], [188] и
методических указаний [193].
При этом вибрация – это движение точек, оборудования, строительных конструкций, и соответственно зданий и сооружений (механическая система), при которых происходят колебания характеризующих его скалярных величин. При этом в жилых и общественных зданиях контролируется общая вибрация, которая создается внутренними и внешними источниками и передается на конструкцию пола в помещениях данных зданий.
108
Основными источниками, которые определяют возникновение общей вибрации в жилых и общественных зданиях, являются:
1. Внешние источники:
- городской рельсовый транспорт, в том числе трассы мелкого заложения и открытые линии метрополитена, трамвайные линии, железнодорожный транспорт и автотранспорт;
- промышленные предприятия и передвижные промышленные
Срудован я; 2.Внутр домовые источники вибрации:
установки, в том числе источники вибрации при эксплуатации гидравлических и механических прессов, а также при эксплуатации стро-
гальных, вырубных других металлообрабатывающих механизмов. Вибрац я при работе мощных компрессоров, бетономешалок, дроби-
лифтовоедование, а также размещаемые в зданиях предприятия торговли, общественного п тан я (холодильное оборудование) и коммунально-
лок, стро тельных маш н, в том числе дизель-молотов и другого обо-
- нженерно-техническое оборудование зданий, в том числе оборудован е, вентиляционные системы и насосное обору-
обслуж утвержденные в установленномАпорядке, которые оснащаются кор-
бытового |
ван я (котельные и т.д.). |
Средства |
змерен я ви рации должны быть стандартного типа, |
ректирующими фильтрами типа Wk, Wm, Wd и должны соответствовать требованиям [191] и [192] для 1-го класса, в части стандартных требований к октавным (треть октавным) фильтрам.
Для измерений вибрации, вДчасти уменьшения влияния внешних помех на измерение вибрации, рекомендуется использовать 1-но и 3-х координатные датчики виброускорения, со встроенными усилителями сигнала. При этом диапазон измерения виброметра с применяемым датчиком, должен включать в себя значения предельно допустимых и допустимых уровней вибрации, которые подлежатИизмерению.
Калибратор вибрации должен быть стандартного типа, утвержденный в установленном порядке, и он должен соответствовать рекомендациям изготовителя средства измерения вибрации.
Вспомогательные средства измерения вибрации применяются, в том числе в случаях, когда при проведении измерений вибрации может возникнуть необходимость фиксирования температуры воздуха в помещениях и фиксирования расстояния от точки измерения вибрации до различных ориентиров, с целью идентификации контрольной точки. Вспомогательные средства измерения вибрации должны быть стандартного типа, и утвержденные в установленном порядке.
109
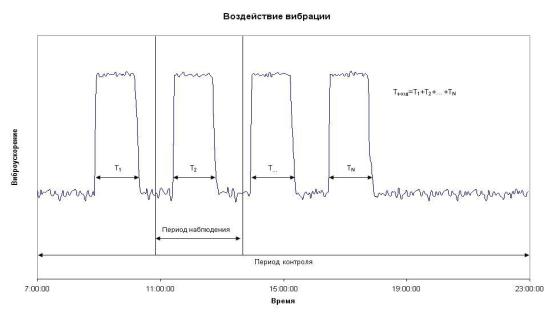
Применяется также оснащение для крепления датчиков вибрации в контрольных точках, то есть в заданных точках измерения вибрации.
При обследовании (мониторинге) оборудования, строительных конструкций, и соответственно в целом зданий и сооружений (объекты контроля), и определении измерений вибрации на объектах контроля осуществляются следующие действия:
- определяются источники вибрации, а также принимаются необходимые решения по их локализации;
- определяются временные характеристики генерации вибрации, в том ч сле характер стики генерации вибрации в течение суток;
|
- определяются способы передачи вибрации в обследуемые зда- |
ния, помещен я (объекты контроля); |
|
С |
|
|
- определяются помещения и точки в данных помещениях, в ко- |
торых необход мо проводить измерения вибрации. Также выбирают- |
|
ся |
для проведен я измерений вибрации. При этом в помещении |
ощущаетсяточкив на ольшей степени, или же точка в центре данного помещен я.
в качестве контрольной точки вы ирается точка, в которой вибрация
Во времябдневного или ночного периодов контроля вибрации, в зависимости от характера ви рации, выбирается период наблюдения (смотри рисунок 1), в течение которого проводятся измерения вибрации. При этом, если характер ви рации в ночное время такой же, как в дневное время, то измерения ви рации допускается проводить толь-
А ко в дневное время. Д
И
Рисунок 1. Период контроля и период наблюдения вибрации. Где: T1, T2, …, TN – продолжительность вибрационных событий; Твозд – общее время воздействия вибрации в период контроля
110
При этом главная задача при выборе периодов наблюдения – это необходимость для обеспечения в получении эквивалентного значения уровня вибрации, представительного для всего периода контроля.
При подготовке к проведению измерений вибрации включаются следующие работы:
- контроль условий, влияющих на точность измерений вибра-
ции;
- проверка калибровки систем измерения вибрации; - крепление датчика вибрации в заданной контрольной точке
здания, помещен я (объекта контроля); - дент ф кац я расположения контрольной точки в здании,
помещен |
(на объекте контроля); |
|
|
- установка реж ма средств измерения вибрации. |
|||
С |
выполняются в соответствии с методикой, |
||
Измерен я в |
|||
которая |
зложена в руководстве по эксплуатации средств измерения. |
||
При этом температура воздуха, в зоне проведения измерений |
|||
рации |
|
||
|
об |
||
вибрац , должна соответствовать рабочим условиям эксплуатации |
|||
средств |
змерен я в |
. |
|
Также про звод тся проверка калибровки средств измерения |
|||
вибрац |
с помощью ви рокалибратора, в соответствии с руково- |
||
|
|
А |
|
дством по эксплуатации средств измерения вибрации. |
|||
При этом со ранные данные |
условиях измерений вибрации |
вносятся в конспект ра очих записей (рабочий журнал изменений). Обработка результатов измерений вибрации заключается в оп-
ределении уровня вибрации за контролируемый период измерений (дневное или ночное время), а также:
-для постоянной вибрации определяется среднеарифметическое значение уровня вибрации в октавных полосах и корректированного уровня;
-для непостоянной вибрации определяется эквивалентное корректированное значение для контролируемого периода по результатам всех измерений. Расчет эквивалентных корректированных значений производится в соответствии с требованиями нормативных документов.
При этом протокол измерений вибрации заполняется по форме, принятой в конкретной испытательной лаборатории или испытательном центре, где отражаются следующие данные:
-дата и время измерения вибрации;
-сведения о средствах измерения вибрации, а также об основном и вспомогательных средствах измерения;ДИ
111
- сведения об объекте контроля, его назначении и источниках вибрации, а также их локализации, временных параметрах вибрации, а также способах передачи вибрации от источников в зданиях;
- сведения о помещениях, в которых производится измерение вибрации, и о контрольных точках, а также данные об идентификации контрольных точек (по расстояниям от различных ориентиров), при необходимости приводится эскиз расположения контрольных точек;
С |
|
||
- сведения об условиях проведения измерений вибрации, в том |
|||
числе о наличии помех и мерах по их устранению; |
|||
- |
результаты |
змерений вибрации, с указанием времени суток |
|
проведен я |
змерен й, характера вибрации и продолжительности из- |
||
нием |
|||
мерен й; |
|
|
|
- результаты обработки данных измерений вибрации с вычисле- |
|||
экв валентных корректированных значений (для непостоянной |
|||
вибрац |
) |
д апазона расширенной неопределенности измерений. |
|
Вибродиагностический |
|||
В протоколе |
змерения ви рации оформляется вывод по изме- |
||
рениям в брац |
том, находятся ли измеренные величины в зоне |
||
допуст |
мых значен |
, который не заменяет экспертного заключения. |
|
В брод агност ческий метод измерения вибрации является |
|||
одним |
з основных методов неразрушающего контроля качества. |
||
|
|
|
А |
|
|
|
метод контроля качества дает возмож- |
ность осуществлять |
следование (мониторинг) за состоянием обору- |
дования, строительных конструкций, и соответственно в целом зданий и сооружений (о ъект контроля), не останавливая работу объекта
оружений (объекты контроля). Д Так как любая вибрация – это колебанияИ, то она представляет
контроля и не прерывая производственный процесс.
Вибродиагностический метод контроля качества основывается на анализе вибрации, которая возникает при работе оборудования, строительных конструкций, и соответственно в целом зданий и со-
собой совокупность различных частот колебаний, которые необходимо изучать, определять амплитуды колебаний, и по этим показателям определить, в каком состоянии находится оборудование, строительные конструкции, и соответственно в целом здания и сооружения (объекты контроля). Данная информация собирается с помощью высокочувствительной аппаратуры.
Вибродиагностический метод контроля качества используется преимущественно в следующих случаях:
- при контроле работы оборудования, которое имеет в своей конструкции подшипники качения (в гидрооборудовании - это колес- но-редукторные блоки);
112
- с помощью данного метода производится диагностика цилиндров низкого давления, паровых турбин, «кручение» ригелей фундаментов турбин, а также статорных систем и т.д.
Вибродиагностика также применяется в энергодобывающих компаниях, на железнодорожном и морском транспорте и в области жилищно-коммунального хозяйства.
Метод вибродиагностики позволяет проводить вибрационный Сконтроль и обследование (мониторинг) вращающегося оборудования.
Также вибродиагностика позволяет осуществлять тестовую диагност ку центровку машин, в том числе электрических, осуществлять баланс ровку машин на месте эксплуатации, диагностику механическмашиных передач, а также выявлять дефекты подшипников скольжения и качен я, ременных и зубчатых передач, дефекты компрессоров, насосов вент ляторов. Метод вибродиагностики может также обнаружить дефекты смазки.
-измерениябАотносительного движения ротора и подшипниковой опоры. При этом используются датчики вибрации бесконтактного типа;
-измерения а солютного движения вращающихся элементов. При этом используются прижимныеДщупа с датчиком инерционного типа или посредством сочетания средств измерений.
При этом необходимо правильно подбирать соответствующие преобразователи и системы измерений вибрации, для обнаружения
неисправностей разных типов и в разных машинах. Например, от конкретного режима работы машины будет зависетьИдиапазон частот измерений вибрации и требуемое разрешение измерений вибрации по частоте.
В качестве примера можно рассмотреть состав аппаратуры вибрационного контроля качества типа ВСВ-350П, в состав которого входят:
-блок защиты аппаратуры вибрационного контроля;
-блок автоматики вибрационного контроля;
-блок скачка вибрации;
-пьезоэлектрический однокомпонентный вибродатчик (вибропреобразователь) аппаратуры вибрационного контроля;
113
-импульсный датчик применяется для измерения частоты вращения и сдвига фазы аппаратуры вибрационного контроля;
-контроллер для ПЭВМ.
Из указанного выше состава аппаратуры вибрационного контроля, в настоящее время серийно выпускаются только блоки защиты и вибродатчики (вибропреобразователи).
Повышенные требования предъявляются к надежности эксплуатации энергетических установок атомных электростанций (АЭС), а также тепловых электростанций (ТЭС), что в значительной степени определяется надежностью и рабочим ресурсом технологических трубопроводов.
При этом в брац и технологических трубопроводов наряду с |
|
корроз ей, дефектами сварочных соединений и изменением механи- |
|
С |
|
ческих свойств металла, в процессе эксплуатации, являются факто- |
|
ром, который определяет их ра очий ресурс и надежность эксплуата- |
|
ции. |
|
В брац технологических трубопроводов вызываются пульса- |
|
давлен я транспортируемого жидкостного потока, а именно |
|
циями |
|
гидрод нам ческ ми |
аэродинамическими явлениями в трубопрово- |
дах. |
|
Также |
технологических трубопроводов вызываются |
вибрации вибрациями гидравлическихАмашин и несущих строительных конст-
рукций, а также сейсмическими воздействиями.
При этом в результате повышенной вибрации в технологических трубопроводах возникают следующиеДявления:
- трещины вследствие усталости материала (металла); - саморазвинчивание арматурных деталей, изделий и строитель-
ных конструкций, а также путевых соединений и систем управления арматуры;
- разгерметизация технологических трубопроводовИ. Разгерметизация технологических трубопроводов часто сопровожда-
ется взрывом и пожаром, а на атомных электростанциях (АЭС) также загрязнением окружающей среды.
Повышенные требования к обеспечению надежности технологических трубопроводов обеспечиваются вводом в процессе их эксплуатации систем периодического контроля (мониторинга) вибраций и вибродиагностики технологических трубопроводов. Как правило, для ответственных энергетических установок вводятся и системы мониторинга вибраций технологических трубопроводов, обеспечивающие непрерывный контроль уровня вибраций.
114
Наиболее распространенными средствами вибродиагностики, которые используются на атомных электростанциях (АЭС), а также на тепловых электростанциях (ТЭС) являются:
1. Стационарная система контроля вибрации и защиты ДИАМЕХ
2000
В зависимости от типа оборудования ДИАМЕХ 2000, в значительной мере отличается и набор контролируемых величин.
При этом на быстроходных агрегатах и на подшипниках скольжения, кроме контроля абсолютной вибрации подшипниковых узлов в обязательном порядке про звод тся контроль относительной вибрации и осевого сдвига. Также на быстроходном оборудовании, на подшипниках качения (вентиляторы, насосные с стемы и т.д.) наиболее востребованным по
информации параметром является абсолютная вибрация подшипников. |
|
С |
|
тационарные с стемы ДИАМЕХ 2000, которые установлены на тур- |
|
боагрегатах |
тельно укомплектовываются датчиками линейных и |
угловых перемещен й, а также датчиками тепловых абсолютных и отно- |
|
сительных расш рен й. Кроме этого, на агрегатах могут устанавливаться |
|
|
датч ки ви рации на корпуса насосов, также может |
дополнительные |
|
контролироваться температура подшипников и рабочие параметры элек- |
тродвигателей, насосов т.д.
При диагностике тихоходного о орудования повышенные требования предъявляются к частотному диапазону датчиков, которые измеряют абсолютную вибрацию подшипников.
При диагностике многорежимных агрегатов, где в значительной сте-
ДИАМЕХ которые в максимальной степени отвечают современнымИтребованиям
пени могут отличаться условия работы (частота вращения, нагрузка и т.д.) |
|
особые требования к диагностике приобретает контроль зависимости |
|
бА |
|
вибрационных характеристик от режима работы оборудования. |
|
Для эффективного решения указанных выше требований эксплуата- |
|
ции различных типов оборудования, |
2000 разработано 4-ре |
типа стационарных систем и 1-на система |
полустационарного типа, |
производства, а именно "надежность - функциональность - стоимость". 2. Стационарная система контроля вибрации и защиты АЛМАЗ-
7010
При создании системы непрерывного контроля (мониторинга) вибрации нового поколения АЛМАЗ-7010 были положены 2-а главных принципа непрерывной работы любой системы мониторинга — это надежность и универсальность.
Система АЛМАЗ-7010 имеет ряд достоинств по сравнению с аналогичными системами непрерывного контроля вибрации, и обеспечивает независимую работу каждого измерительного канала (см. рис. 2).
115

Си
Рисунок 2. Функциональная схема сбора данных |
|
Система непрерывного мониторинга ЛМ З-7010 осуществляет кон- |
|
троль следующих параметров: |
Д |
- вибрационныхбАпараметров (абсолютные и относительные); |
|
- тепломеханических параметров (частота вращения, линейные пере- |
|
мещения, тепловые абсолютные и относительные расширения, угловые |
перемещения и температура). |
И |
При этом возможность подключения датчиков с различными выходными интерфейсами позволяет реализовывать комбинированные системы для контроля давления, сил и т.д.
К достоинствам системы непрерывного мониторинга АЛМАЗ-7010 необходимо отразить ее аппаратную и программную масштабируемость. При необходимости система АЛМАЗ-7010 может дооснащаться каналами с дополнительными и новыми датчиками, а также средствами компьютерного обеспечения и интерфейсами с внешними устройствами и сетями. Также программное обеспечение может дооснащаться дополнительными и новыми модулями балансировки, экспертных оценок и диагностики.
Отличительной особенностью системы непрерывного мониторинга АЛМАЗ-7010 является высокая надежность ее работы. В данной системе
116
каждый измерительный канал представляет собой законченную измерительную систему непрерывного мониторинга, с полным набором необходимых входов и выходов и может работать абсолютно независимо от других. Неисправность в таком канале слабо сказывается на работоспособности всей системы АЛМАЗ-7010, именно поэтому подобные системы получили широкое распространение для контроля наиболее ответственного оборудования, а именно мощных турбоагрегатов атомных и тепловых электростанций.
При этом, универсальность контрольно-измерительного модуля системы АЛМАЗ-7010 позволяет применять только один тип модулей, который настра вается на решение конкретной задачи программными
методами, а меющ еся в нем "избыточные" ресурсы позволяют исполь- |
|
зовать их для повышен я надежности работы, за счет дублирования |
|
С |
|
обработки, а также резерв ровать их для дальнейшего расширения систе- |
|
мы непрерывного мон торинга |
ез расширения аппаратных средств. |
Данное решен также м нимизирует необходимый (требуемый) объем |
|
запасных частей. |
|
Программное |
ЛМ З-7010 обеспечивает возможность |
обеспечение |
|
просмотра текущ х данных, трендов изменения параметров во времени, а |
также обеспеч бвает возможность осуществлять архивацию и хранение информации за длительный период времени. При этом универсальный программный комплекс З-МОНИТОР, который входит в состав системы непрерывного мониторинга, удовлетворяет современным требованиям и имеет также дополнительные возможности.
ставляет собой 5-ть основныхАЛМблоков:
тер неуравновешенности агрегатов, качествоДсоединения роторов, нагрузочные факторы, влияющие на изменение вибрации, а также позволяет контролировать изменение уровня вибрации во времени, на пускахостановах и на аварийных режимах агрегатов;
Универсальный программный модуль ЛМАЗ-МОНИТОР пред-
- блок вибрации подшипников позволяет определять уровень и харак-
- блок вибрации валов позволяет более эффективно определять вели-
чину и место неуравновешенности валопровода, в том числе, при отрыве |
|
лопаток, а также позволяет корректировать расцентровки по статическому |
|
положению роторов на масляном слое и оценивать качество сборки |
|
роторов; |
И |
|
|
- блок измерения механических величин (осевой, сдвиг, относитель- |
|
ное расширение и абсолютное расширение, наклоны опор, искривление, |
|
измерения положения главного сервомотора), и соответственно является |
основным блоком контроля тепломеханического состояния агрегатов. С помощью данного блока осуществляется контроль режима пуска, набора
117
мощности и работы под нагрузкой, а также процесс остановки и остывания агрегатов;
- блок архивации данных осуществляет накопление, хранение и предоставление информации. Данный блок позволяет восстановить информацию о характере протекания процессов (мониторинге), и является основой для диагностики агрегатов. Также данный блок дает возможность просмотра технического состояния агрегатов (мониторинга) в лютой времен-
СБлочное построен е позволяет максимально эффективно использовать возможности модуля АЛМАЗ-МОНИТОР, которые предоставляются с стемами, и не только в период эксплуатации оборудо-
ной, удобной для обслуживающего персонала форме;
- по уровню срабатывания помимо стандартной логики сигнализации и отключен я блок защ ты имеет широкие возможности перенастройки
системы, в зав с мости от поставленной ему задачи.
вания, но и во время проведения испытаний агрегатов и т.д.
И как результат, ольшое количество реализованных функций системы непрерывного мон тор нга АЛМАЗ-7010, а также высокая ее надеж-
ность |
помехозащ щенность, а также блочно-модульная архитектура |
|
стационарными |
||
системы и ее простая |
нтеграция гарантируют безотказную и надежную |
|
работу оборудован я атомных и тепловых электростанций и т.д. |
||
При этом система |
-7010 является системой непрерывного |
|
мониторинга, бкоторая о еспечивает непрерывный контроль вибрации |
технологического о орудованияАЛМАЗ(подшипников и валов) и контроль механических величин о орудования (осевого сдвига, относительных
личин обеспечивается также на всех Дэксплуатационных режимах турбоагрегатов. Система АЛМАЗ-7010 обеспечивает срабатывание защиты по виброскорости, относительному расширению роторовИ, осевому сдвигу и частоте вращения при выходе указанных величин за допустимые пределы. Данные измерения передаются на мониторы щита управления и в подраз-
расширений роторов высокого, среднего и низкого давления, искривления вала, абсолютных расширений цилиндров и наклонов опор).
При этом непрерывный контроль вибрационных и механических ве-
деления автоматизированной системы управления (АСУ) и заносятся в базу данных, которые отображаются на алфавитно-цифровых индикаторах модулей системы.
3. Стационарный комплекс контроля вибрации и защиты
РУБИН-М1
Комплекс применяется при оснащении паровых и газовых турбин малой мощности с функциями:
-защиты для предотвращения аварийных выходов оборудования из строя;
118
- мониторинга для отслеживания различных параметров работы оборудования во времени;
- диагностики для выявления типов неисправностей и построения прогнозов их дальнейшего развития.
При этом функции защиты, мониторинга и диагностики оборудования с использованием комплекса РУБИН-М1 обеспечивает следующие требования:
С- высокая скорость реакции на развитие дефекта, равное 0,1 сек; - автоматическое отключение аварийного оборудования;
- обнаружен е зарождающихся дефектов на ранней стадии их разви-
тия;
-вностианал з работы оборудования по сложным алгоритмам и в широком частотном д нам ческом диапазонах;
- реал зац я разл чных условий обслуживания оборудования с использованием комплекса РУБИН-М1;
- повышен е эффект производства за счет значительного снижения незаплан рованных простоев и сокращения затрат на техническое обслуж ван е ремонт о орудования;
-предотвращен е авар йных ситуаций с возможными разрушительными последств ями о орудования, строительных конструкций, и соответственно в целом зданий и сооружений;
-повышение достоверности диагностики с использованием большого количества параметрических данных непрерывного мониторинга оборудования;
-наличие полной автоматизации сбора данных по защите, мониторингу и диагностике оборудования;
-создание единого информационного пространства в рамках данной системы, и соответственно для принятия решений по защите, мониторингу и диагностике оборудования, строительных конструкций, и соответственно в целом зданий и сооружений.
Наличие дополнительных возможностей комплекса РУБ Н-М1, которые обеспечивают универсальность и гибкость применения защиты, мониторинга и диагностики паровых и газовых турбин, а также центробежных насосов, в том числе на тепловых электростанций (ТЭЦ), а именно:
-параллельные каналы защиты обеспечивают возможность обнаружения быстрого роста контролируемого параметра оборудования, в том числе вертикальной вибрации на подшипниках, т.к. серьезные поврежде-
ния подшипника сопровождаются ростом вертикальной и поперечной вибрации; бАИ
119
- последовательные диагностические каналы обеспечивают возможность контроля вибрации, а также обеспечивают подробный анализ вибрации на подшипниковых узлах, в вертикальном и в горизонтальном направлениях. Данные действия необходимы для раннего обнаружения изменений в вибрационных процессах данного технологического обору-
дования; |
|
|
|
|
|
- в комплексе РУБИН-М1 реализована возможность подключения до- |
|||
С |
|
|||
полнительных датчиков с аналоговыми и цифровыми интерфейсами, |
||||
которые позволяют контролировать температуру, а также токи, напряже- |
||||
ния, давлен е |
друг |
е параметры оборудования; |
||
|
- обеспеч вают возможность расположения измерительного блока |
|||
|
многоканальности |
|
||
вблизи контрол руемого оборудования за счет использования надежного |
||||
пыле- и влагозащ щенного корпуса, а также обеспечивает подключение |
||||
датчиков непосредственно к измерительному блоку. При этом передача |
||||
информации |
получаемой со всех датчиков осуществляется по одному |
|||
|
|
блок |
|
|
высокоскоростному стандартному каналу. |
|
|||
|
В результате од |
змерительный |
комплекса РУБИН-М1, бла- |
|
годаря |
|
может о служивать один или несколько объек- |
||
тов. |
При этом нал ч е восьми каналов защиты и четырех входов датчиков |
|||
|
||||
|
|
|
А |
оборотов позволяет, в том числе одним измерительным блоком осуществлять контроль и диагностику технического состояния четырехвального роторного агрегата, который имеет до восьми подшипников.
Также особенностью комплекса РУБИН-М1 является то, что благодаря многоканальности вся информация о указанном выше сложном объекте позволяет учесть наличие корреляционных зависимостей между всеми контролируемыми параметрами. При этом возможны различные струк-
турные сети для организации обмена данными, в том числе возможно |
|
построение отказоустойчивых сетей, которые обеспечивают сохранение |
|
|
И |
работоспособности оборудования даже при обрыве соединительного |
|
кабеля сети. |
Д |
120

С |
|
|
|
|
и |
|
|
|
бА |
||
|
Рисунок 3. Различные варианты построения функциональной схемы |
||
|
Одним из портативных приборов вибродиагностики является |
||
|
|
Д |
|
анализатор вибрации ОНИКС, который устанавливает новый стандарт |
|||
качества профессиональной аппаратуры для измерения и анализа вибра- |
|||
ции. |
При этом в виброанализаторе ОНИКС имеются следующие конструк- |
||
ционные особенности, а именно: |
|
И |
|
|
- современная аппаратная база; |
|
|
|
- максимальный набор функций; |
|
|
|
- операционная система Windows CE; |
||
|
- параллельное измерение по двум каналам; |
||
|
- цветной дисплей высокого разрешения; |
||
|
- эргономичный корпус; |
|
- сменные карты памяти SD.
Внешний вид портативного прибора вибродиагностики – анализатора вибрации смотри на рис. 4.
121

Си бАР сунок 4. Внешний вид анализатора ОНИКС
Прибор ОНИКС, являясь анализатором вибрации дает возможность в полной мере использовать последние достижения в области измерения и анализа вибрации, а также диагностики подшипников и балансировки роторов.
При этом 2-х канальный переноснойДвиброанализатор ОНИКС, который создан на базе самых современных аппаратных и программных технологий, является продолжением по разработке высокотехнологичных переносных виброанализаторов производства ИАМЕХ 2000.
Переход на принципиально новую высокотехнологичнуюИплатформу виброанализатор ОНИКС позволил не только значительно улучшить большинство технических характеристик прибора, но и реализовать ряд специальных возможностей и новых функций, значительно повышающих достоверность диагностики промышленного оборудования. В виброанализаторе ОНИКС используется новый измерительный тракт и набор специальных встроенных фильтров, которые обеспечивают максимальную метрологическую точность получаемых результатов.
Также имеются уникальные технические характеристики портативного виброанализатора ОНИКС, а именно:
-большой объем памяти;
-высокое разрешение дисплея;
122
- расширенный частотный (0,1 — 40 кГц) и динамический диапазон (>100 Дб), которые позволяют использовать его в качестве самостоятельного инструментария при мониторинге и диагностике даже без применения специального программного обеспечения.
Переносной виброанализатор ОНИКС обладает широкими возможностями, в том числе он позволяет контролировать текущее состояние агрегатов, выполнять в автоматизированном режиме глубокую поузловую
ОНИКС |
|
диагностику и балансировку в собственных подшипниках, а также опре- |
|
делять собственные частоты строительных конструкций. Также виброана- |
|
лизатор |
может быть использован как в качестве анализатора |
вибрации, так |
в качестве сбора и обработки данных в режиме работы |
маршрутной карты.
Вдатчиковвиброанал заторе ОНИКС реализован максимальный набор замеров для 1-но канального 2-х канального анализа, а также ряд исследова-
тельских функц й, которые позволяют существенно повысить информа-
ВвиброаналбАзаторе ОНИКС предусмотрена максимальная функциональность высокотехнологичных ви роанализаторов, а именно:
- кроме стандартных типовых замеров (общий уровень вибрации, амплитуда/фаза, спектр, спектр оги ающей, временной сигнал и др.);
- реализован ряд специальных исследовательских функций, направленных на повышение достоверностиДдиагностики;
- измерение дампа временного сигнала (до нескольких часов); - кепстральный анализ, а также новый метод оценки нестационарных
процессов - вайвлет-анализ, который набирает все большую популярность среди диагностов-исследователей.
Всвязи с возможности проведения синхронныхИизмерений различных параметров вибрации одновременно по двум каналам, в виброанализаторе ОНИКС реализованы крайне информативные при диагностике виды замеров, как орбиты и взаимные спектры, а также разработан алгоритм расчета взаимной фазы, позволяющей выявлять ряд дефектов роторного оборудования без использования тахометрического датчика.
Практически неограниченный объем памяти виброанализатора ОНИКС позволил создать возможность новых типов замеров, а также исследовательских функций и диагностических методик, которые могут применяться специалистами при углубленной диагностике оборудования, как непосредственно во время проведения измерений, так и во время последующего анализа.
123
Удобство и простота работы виброанализатора ОНИКС отвечает всем общемировым стандартам современного приборостроения, ориентированным на удобство конечного пользователя. При этом большой цветной дисплей высокого разрешения позволяет выполнять анализ данных в полевых условиях без использования переносного компьютера.
Эргономичное исполнение виброанализатора ОНИКС, его небольшие габариты и малый вес, а также простой интуитивно понятный пользова-
Смодульный пр нц п построения, а именно:
тельский интерфейс и процедура упрощенного ввода данных с наличием разветвленной системы помощи позволяют с максимальной эффективностью и удобством конечного пользователя, использовать многочисленные возможности пр бора при решении сложных задач диагностики.
При разработке в броанализатора ОНИКС использован следующий
- большой объем памяти не накладывает никаких ограничений на допустимый макс мальный размер встроенного программного обеспечения
обновления находятся в открытом доступеАна сайте www.diamech.ru
прибора;
- по мере разв т я платформы, виброанализатор ОНИКС будет до-
полняться |
функц ями, программными модулями и методиками |
новыми |
|
диагностики; |
|
- в отл ч от о щепринятой мировой практики все последующие |
|
программные |
и расширения предоставляются бесплатно и |
Многолетний опыт разра отки и практической апробации балансировочных программ в составе переносных виброанализаторов семейства AU, КВАРЦ и АГАТ-М, получил практическуюДреализацию в новой балансировочной программе виброанализатора ОНИКС.
При этом удачно сочетая теоретические достижения и функциональную насыщенность программы КВ РЦ, а также простоту, удобство и наглядность балансировочного модуля прибора АГАТ-М, балансировочная программа виброанализатора ОНИКС по правуИзанимает лидирующие позиции в данном сегменте решений.
А также для проведения синхронного многоканального анализа в рамках разрабатываемой платформы ОНИКС может быть использован специальный автономно функционирующий измерительный блок, который имеет общую с виброанализатором ОНИКС базу данных.
4. Стационарная система контроля вибрации и защиты В БРО-
БИТ пользуется спросом, как на отечественном, так и на зарубежном рынке автоматизированных систем и применяется на атомных, тепловых электростанциях и других промышленных объектах.
При этом аналоговая система Вибробит-100 предназначена для измерения и контроля параметров механического состояния паровых и газовых
124
турбин, центробежных насосов, турбокомпрессоров и другого промышленного оборудования во время их технической эксплуатации.
Также разработан программно-технический комплекс Вибробит-200, который предназначен для непрерывного контроля вибропараметров, виброзащиты и вибродиагностики турбоагрегатов. При этом возможна одновременная работа комплекса Вибробит-200 с несколькими агрегатами, а также с насосами и другими роторными машинами на атомных,
Степловых электростанциях и прочих объектах энергетики и промышленности, как автономно, так и интегрировано в автоматизированные системы управлен я программно-технического комплекса.
Инновац онная разработка автоматизированной системы программ- но-техническогоикомплекса Вибробит-300 основана на применении цифровых методов обработки сигналов, которая позволяет изготавливать функциональные эконом чные системы Вибробит-300, в большинстве случаев, не меющ х аналогов на отечественном и зарубежном рынке.
При этом функцбАонально автоматизированные системы программнотехнические комплексы В ро ит можно разделить на 3-и уровня, а именно:
- на первом уровне про сходит преобразование физической величины в пропорциональный токовый сигнал, поступающий на цифровые модули контроля. В цифровых модулях контроля выполняется пересчет уровня сигнала в значение физического измеряемого параметра. В свою очередь, первый уровень системы Ви ро ит делится на две части:
а) первичные преобразователи включают в себя датчики, преобразователи (выносные усилители), соединительныеДкабели;
б) вторичные преобразователи включают в себя модули контроля, логические модули технологической защиты, модули проверки исправности каналов измерения и схем защиты, источники питания (включая источники бесперебойного питания), удаленные модули индикации;
-второй уровень автоматизированной системы программнотехнических комплексов Вибробит функционально предусмотрен как распределенная клиент-серверная система с возможностями гибкого наращивания. Программное обеспечение системы ведет мониторинг вибропараметров и механических величин, в том числе отслеживает сводное состояние турбоагрегатов, проводит оперативную диагностику состояния турбоагрегатов в режиме реального времени и т.д.
-к третьему уровню автоматизированной системы программнотехнических комплексов Вибробит относятся удаленные рабочие станции
(персональные компьютеры), которые имеют доступ к базе данных и текущему состоянию агрегатов, для их просмотра и анализа.И
125

При этом аппаратура автоматизированной системы программнотехнических комплексов Вибробит имеет комплектность, исходя из потребностей предприятия-заказчика, с соответствующим составом датчиков, измерительных и сервисных модулей. При реализации автоматизированной программно-технических комплексов Вибробит существуют готовые шаблоны измерения различных вибромеханических параметров и построения схем защиты. По индивидуальному заказу предприятия-
Сзаказчика изготавливаются датчики с нестандартными габаритными размерами и электрическими характеристиками.
и бА Д
-CAN2.0B интерфейсы для удаленного отображенияИизмеренных параметров, автономного хранения;
-RS485 с протоколом ModBus интерфейсы для включения аппаратуры Вибробит-300, которые входят в состав создаваемых и существующих автоматизированных систем управления и подключения персональных компьютеров;
126