

Lesson 18
Refresh the words in Ex. I (Lesson 1 – 17) and get ready to have a dictation.
С |
|
|
|
||
|
I. Listen and repeat. Using the dictionary, write in the [træn'skripSn] |
||||
|
of the words into the table below. |
|
|
||
|
1 |
revolutionize |
……………… |
производить революцию |
|
|
2 |
rearrange |
……………… |
менять, переустраивать; транс- |
|
|
|
|
|
формировать |
|
|
3 |
software |
……………… |
программное обеспечение (ПО) |
|
|
4 |
estimator |
……………… |
оценщик; сметчик |
|
|
5 |
simulation |
……………… |
программное обеспечение моде- |
|
|
|
software |
|
лирования |
|
|
6 |
иsequence ……………… |
последовательность; ряд |
|
|
|
7 |
prevent |
……………… |
предотвращать |
|
|
8 |
interfere |
……………… |
мешать |
|
|
9 |
determine |
……………… |
определять, устанавливать |
|
|
10 |
impactб……………… |
сильное воздействие; влияние |
|
|
|
11 |
schedule |
……………… |
график, программа; каталог; |
|
|
|
|
|
опись, реестр |
|
|
12 |
due |
……………… |
Д |
|
|
должный, соответствующий |
|
|||
|
13 |
forecast |
………………Апрогнозирование |
|
|
|
14 |
utilization |
……………… использование, употребление, |
|
|
|
|
|
|
утилизация |
|
|
15 |
visualize |
……………… |
отчётливо представлять себе |
|
|
|
|
|
И |
|
II. Find the words in the text and translate the word combinations with these words.
III. Work in pairs.
Refresh all the Grammar material you have studied. Use the words from Ex. I to make up 5 questions based on different grammar rules and let your partner answer them.
IV. You are to read the text “Control system”. What do you expect to know after reading? Write down your ideas and then read the text.
127
CONTROL SYSTEM
Computers have revolutionized manufacturing. They gave manufacturing engineers control over events in the factory. With this information, processes can be reorganized for maximum efficiency and production steps
can be rearranged for maximum cost savings.
СSoftware. Computers cannot run without software; that is, without some instructions on what to do. Software controls the flow of information in a computer system. The software makes a computer a specific device – a
Because of computers tasks are done more quickly and accurately. It enables engineers to make changes or corrections that will utilize equip-
ment and people optimally.
An important quality of computers is that they are flexible. Change
иSimulation software is another type of software which is now becoming quite popular. This type of software lets you see your proposed factory
the program and you have a “new computer”.
mated workбcells, manufacturing systems and factories such as FMS.
calculator, a designer, a programmer, a cost estimator, an expert.
layout at work “on paper”.
The main problemsАthat FMS software should solve are as follows:
Simulation software helps in the design and development of auto-
An FMS without software is not flexible, has little use in man-
ufacturing and is not even a system.
- Keeping track of the materials being manufactured, determining the exact physical location in the system and performing the correct sequence of operations.
- Preventing the different operations from interfering with each other. - Determining error conditions and minimizing their impact on the sys-
tem. |
Д |
|
|
||
- Keeping management informed on parts, production, part pro- |
||
gramming, and system status. |
|
|
- Determining the best production schedule to meet due data and max- |
||
|
|
И |
imize machine utilization.
- Forecasting system needs at due time – fixtures, tools, lubricants and coolants.
- Directing in real-time the operations of people in charge of the above facilities. Comparing actual and forecast performances.
- Informing the plant management with the required data from FMS, for production planning and control, accounting and reporting.
128
Thus, the FMS control system manages the total combination of devices in the system that contributes to the automatic operation of the production process. This includes the machine-tool controllers, the material handling system, the system monitoring devices, the system communications, and finally the system computer. Computer software supplies all the
Сcontrol management and monitoring functions that enable the system to achieve high utilization.
The control system is easily visualized by considering all the elements of the system in a structured arrangement according to its function.
Have you found out everything you wanted? If not, try to do it using the Internet. Share your findings with your groupmates.
V. Work in pairs. Are the statements true or false?
1. |
Different tasks are performed much faster due to computers. |
||
2.иSoftware is the “feet” of computers which they use to be able to run. |
|||
3. |
An FMS is not a flexible system. |
|
|
4. FMS software should forecast system needs, determine the best produc- |
|||
|
|
А |
|
tion schedule, and increase impact of conditions on the system. |
|||
5. |
The FMSбcontrol system manages various other systems. |
||
6. It is not recommended to rearrange production steps as it is very expen- |
|||
sive. |
|
|
|
VI. Find the best continuation to the following ideas. |
|||
1. Computers make … |
|
||
2. |
Software controls … |
И |
|
3. |
Software lets … |
|
|
4. |
Software should … |
|
|
5. The FMS control system managesД… |
|||
VII. Read the following article and answer the questions: |
|||
1. |
What is simulation? |
|
|
2. |
What is the purpose of simulation? |
|
|
3. |
Where can simulation be used? |
|
129

С |
|
|
и |
|
|
б |
|
|
|
А |
|
|
Д |
|
IX*. Think of 3 examples of simulation usage and discuss them with |
||
your groupmates. |
|
|
X. Work in groups of 4 – 5. Tell one statement about an FMS control |
||
system, one by one, to make a story. |
И |
|
|
XI. What were the most difficult tasks for you in this book? Why? Make a list of problems that prevent you from studying English for specific purposes. Analyze them and think of possible solutions.
Problem |
Possible solution |
Go to Lesson 2 and look through the list of problems you made that time. Has anything changed? Which way?
130

HOME TASK 18
A. Look through the texts below (Texts 1 – 5). Choose 1 text you like and write an abstract and a summary.
B. Look through the texts below (Texts 1 – 5). Choose 2 texts you like and write an abstract and a summary for each of them.
СиText 1. History of Robotics
C. Write an abstract and a summary for each of the texts (1 – 5) given below.
The concept of robots dates back to ancient times, when some myths told of mechanical beings brought to life. Such automata also appeared in the clockworkбfigures of medieval churches, and in the 18th century some clockmakers gained fame for the clever mechanical figures that they constructed. Today the term automaton is usually applied to these
handcrafted, mechanical (rather than electromechanical) devices that imi- А
tate the motions of living creatures. Some of the “robots” used in advertising and entertainment are actually automata, even with the addition of remote radio control.
The term robot itself is derived from the Czech word “robota”, meaning “compulsory labour”. It was first used by the Czech novelist and playwright Karel Chapek, to describeДa mechanical device that looks like a human but, lacking human sensibility, can perform only automatic, mechanical operations. Robots as they are known today do not only imitate human or other living forms. True robots did not become possible, however, until the invention of the computer in the 1940s and the miniaturization of computer parts. One of the first trueИrobots was an experimental model designed by researchers at the Stanford Research Institute in the late 1960s. It was capable of arranging blocks into stacks through the use of a television camera as a visual sensor, processing this information in a small computer.
Computers today are equipped with microprocessors that can handle the data being fed to them by various sensors of the surrounding environment. Making use of the principle of feedback, robots can change their operations to some degree in response to changes in that environment. The commercial use of robots is spreading, with the increasing automation of factories, and they have become essential to many labora-
131

tory procedures. Japan is the most advanced nation exploring robot technology. Nowadays robots continue to expand their applications. The home-made robots available today may be one sign of the future.
Text 2. Industrial robots in FMS
СAn industrial robot is a reprogrammable, multi-functional manipulator designed to move materials, parts or tools through variable programmed movement to accept a variety of tasks.
It is important to note that robot application and programming methodsиhave progressed far beyond merely handling components since their controllers and sensors have developed the capability to communicate with other intelligent devices. Sensors particularly have been the focus of much development in recent years.
Robotsбare able to provide information not only about their arm position but also about the part being handled and about the gripper or more complex robot tool. They are capable of seeing, hearing, smelting, detecting and analyzing force, torque, heat, pressure, colour and other environmental changes orАconditions.
Sensors can provide information about the presence of a part in a buffer store, in a robot tool or in the chuck of a lathe, and they can, for example, interact with the robot controller and modify the programmed sequence in real time. More sophisticated sensors such as force and torque sensors send stress measurementДvalues. Vision systems use special purpose image processors and image data base which are interfaced with the control program of the arm.
Distributed sensory feedback processing makes robots more intelligent, more reliable and more flexible, and these important trends are
not to be ignored when designing the FMS. И It is necessary to stress that industrial robots have a very wide
range of potential applications in FMS because they are reprogrammable flexible devices themselves. The increasing power of their sensory feedback processing system allows them to work at a high level of intelligence. However, robots are not yet capable of solving most materials handling assembly or inspection tasks in FMS. A relatively low proportion of robots are capable of communicating at a high level with other robots and computers and their sensory systems are usually expensive compared with their performance.
132

The major application area of industrial robots include pick and place type of operations.
An example can be given of a robot which ensures smooth product flow in an FMS.
The cell, which includes two drilling machines, was developed to Сproduce 300,000 magnet housings a year on a three-shift operation. It was, therefore, essential to maintain a smooth flow of components into, through and out of the cell. To achieve this product flow the robot was fitted with a pneumatically operated triple gripper to handle raw material,
part machined and fully finished components in turn. иHaving a repeatability accuracy of 0.25 mm at maximum speed, the robot is able to maintain a handling transfer and location program whereby one magnet housing is picked by the triple gripper and moved to the first бtwin chuck machine. The empty grippers grasp a component from each chuck of the machine, remove the part and advance one step to load the chucks again.
A finished part is thus removed from the machine, a part-machined component is progressed to the second chuck, and a new component is loaded into chuck one.АThe robot returns to the unload pallet and deposits the finished part. It then repeats the handling sequence for the second machine, and so on, according to the computer program.
It is of interest to note that supercomputers are fast-functioning computers that were initially developedДfor a few specialized complex applications. They exceed mainframe computers by a factor of two to ten in measures of speed, accuracy, memory size, and memory speed. For example, a calculation that would take about 200 years on a handheld calculator, and about 8 minutes on a mainframe, takes about 1 second on a 1 billion-floating-point-operations-per-secondИsupercomputer.
With supercomputers scientists are able to simulate theories one of the most complex problems – how the universe began. But scientists and engineers have found other uses for these superfast machines: semicompound manufacturers are using them to design chips. Supercomputers are being used to run artificial intelligence programs.
It should be noted, however, that the market for minisupercomputers, a computer slightly less powerful than a supercomputer is growing even faster. They are less expensive. Minisupercomputers are expected to run about 90 per cent of the applications that a supercomputer will run but at a much lower cost.
133
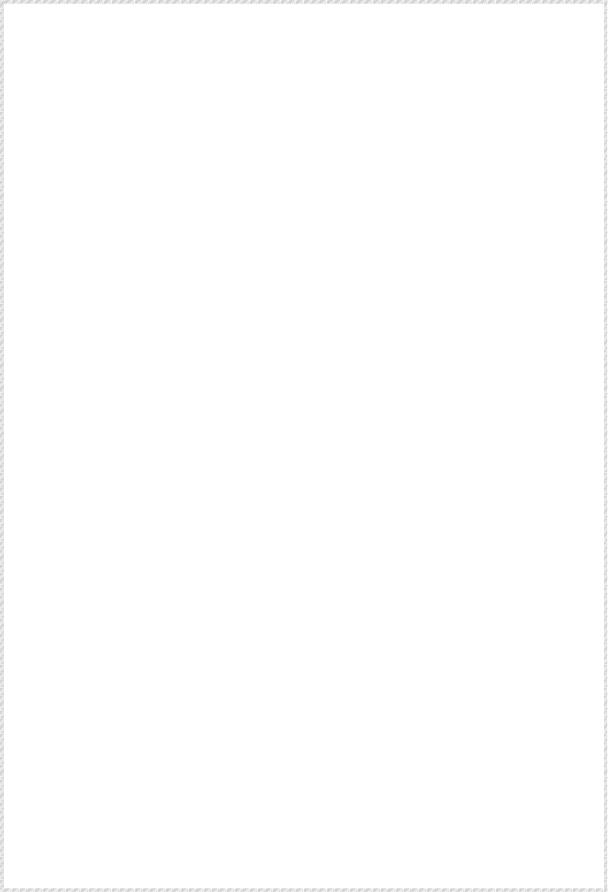
Another interesting fact is that a computer is never really fast enough nor has enough memory to satisfy users. That is why scientists and engineers continue to work on developing even faster computers and their components.
Сdling; 2) processing operations; 3) assembly and inspection. иMaterial-handling is the transfer of material and loading and unloading of machines. Material-transfer applications require the robot to move materials or work parts from one to another. Many of these tasks are relatively simple: robots pick up parts from one conveyor and place them on another. Otherбtransfer operations are more complex, such as placing parts in an arrangement that can be calculated by the robot. Machine loading and unloading operations utilize a robot to load and unload parts.
Text 3. ROBOTS IN MANUFACTURING
Today most robots are used in manufacturing operations. The applications of robots can be divided into three categories: 1) material han-
This requires the robot to be equipped with a gripper that can grasp parts. А
Usually the gripper must be designed specifically for the particular part geometry.
In robotic processing operations, the robot manipulates a tool to per-
form a process on the work part. Examples of such applications include spot welding, continuous arc welding and spray painting. Spot welding of automobile bodies is one of theДmost common applications of industrial robots. The robot positions a spot welder against the automobile panels and frames to join them. Arc welding is a continuous process in which robot moves the welding rod along the welding seam. Spray painting is the manipulation of a spray-painting gun over the surface of the object to be coated. Other operations in this categoryИinclude grinding and polishing in which a rotating spindle serves as the robot's tool.
The third application area of industrial robots is assembly and inspection. The use of robots in assembly is expected to increase because of the high cost of manual labour. But the design of the product is an important aspect of robotic assembly. Assembly methods that are satisfactory for humans are not always suitable for robots. Screws and nuts are widely used for fastening in manual assembly, but the same operations are extremely difficult for a one-armed robot.
Inspection is another area of factory operations in which the utilization of robots is growing. In a typical inspection job, the robot positions a
134

sensor with respect to the work part and determines whether the part answers the quality specifications. In nearly all industrial robotic applications, the robot provides a substitute for human labour. There are certain characteristics of industrial jobs performed by humans that can be done by robots:
С1) the operation is repetitive, involving the same basic work motions every cycle,
2) the operation is hazardous or uncomfortable for the human worker (for example: spray painting, spot welding, arc welding, and certain machine loading and unloading tasks),
и3) the workpiece or tool are too heavy and difficult to handle,
4) the operation allows the robot to be used on two or three shifts.
As is known, the use of computer-aided design and manufacturing (CAD/CAM) is growing now. Early CAD/CAM systems were based on large computers (mainframes) and focussed on design and drafting functions. During last years,Аhowever, powerful microprocessors have increased the flexibility and power of graphics terminals.
Textб4. CAD/CAM SYSTEM AND FMS
CADD (Computer-Aided Design and Drafting) technology allows
the designer to draw a picture of an object on a video display terminal (VDT) screen. The computer then converts this picture into a mathematical model and stores it in the data baseДfor later use.
Mathematical modelling is considered to be most important feature of a CADD system. This feature can produce a model of a structure for stress analysis, or it can provide input for automated drafting to produce engineering drawings. CADD systems can be ten times faster than man-
ual drafting. И If CAD/CAM systems are linked, the mathematical model can also
be used to create numerical control (NC) tapes for fabricating the part. The oldest CAM technology is numerical control, the technique of
controlling a machine tool with pre-recorded, coded information to fabricate a part. Today, engineers are trying to integrate the technologies of CAD, NC and IR (industrial robots).
135

Text 5. CAM
(Computer Aided Manufacturing)
Computer aided Manufacturing(CAM) is assistance of computer in manufacturing planning and processes like planning different operations to be done on product, sequencing all the operations and finally control
Сtems are associated with computer numerical control (CNC) or direct numerical control (DNC) systems. These systems differ from older forms of numerical control (NC) in that geometrical data is encoded mechanically. Since both CAD and CAM use computer-based methods for en-
the machine parameters like Feed, Speed, Depth of cut etc.
CAM uses CAD data to control automated machinery. CAM sys-
coding geometrical data, it is possible for the processes of design and |
|||
manufacture to be highly integrated. Computer-aided design and manu- |
|||
facturing systems are commonly referred to as CAD/CAM |
|||
иCAM uses CAD data to control automated machinery. CAM sys- |
|||
tems are associated with computer numerical control (CNC) or direct |
|||
numerical control (DNC) systems. These systems differ from older forms |
|||
of numerical control (NC) in that geometrical data is encoded mechani- |
|||
cally. Sinceбboth CAD and CAM use computer-based methods for en- |
|||
coding geometrical data, it is possible for the processes of design and |
|||
manufacture to be highly integrated. Computer-aided design and manu- |
|||
facturing systems are commonly referred to as CAD/CAM |
|||
|
Benefits of CAM: |
|
|
1) |
А |
||
Improve productivity. |
|
|
|
2) |
Lead time reduction. |
|
|
3) |
Reduce engineering personal requirements. |
||
4) |
Improve accuracy of product. |
|
|
5) |
|
Д |
|
Reduce training time for routine drafting tasks and NC part pro- |
|||
gramming. |
|
|
|
6) |
Fewer errors in NC part programming. |
|
|
7) |
Provide the potential of using more existing parts and tooling. |
||
8) |
Helps ensure design is appropriate to existing manufacturing tech- |
||
niques. |
|
И |
|
|
|
||
9) |
Saves material and machining time by optimizing algorithm. |
||
10) |
Provides operational results on the status of work in progress. |
||
11) |
Makes the management of design personnel on project more effec- |
||
tive. |
|
|
|
12) |
Assistance in inspection of complicated parts. |
136

13) Better communication interfaces and greater understanding among engineers, designers, drafters, management and different project groups.
Short-Comings:
CAM packages could not, and still cannot, reason as a machinist can. They could not optimize toolpaths to the extent required of mass Сproduction. Users would select the type of tool, machining process and paths to be used. While an engineer may have a working knowledge of g-
code programming, small optimization and wear issues compound over time. Mass-produced items that require machining are often initially created through casting or some other non-machine method. This enables handи-written, short, and highly optimized g-code that could not be produced in a CAM package.
There is a shortage of young, skilled machinists entering the workforce able to perform at the extremes of manufacturing; high precision and mass бproduction. As CAM software and machines become more complicated, the skills required of a machinist or machine operator advance to approach that of a computer programmer and engineer rather than eliminating the CNC machinist from the workforce.
|
Би лиографический список |
|
Д |
1. |
Баракова, М.Я. АГибкие автоматизированные производства. Пособие по |
обучению чтению на английском языке : учеб. пособие / М.Я. Баракова, |
|
Г.А. Мкртчян, Н.И. Наумова; под ред. М.Б. Генералова. – М. : Высш. шк., 1990. – |
|
140 с. |
И |
2. |
Основы автоматизации машиностроительного производства : учеб. для |
машиностроит. спец. вузов / Е.Р. Ковальчук, М.Г. Косов, В.Г. Митрофанов и др.; |
|
под ред. Ю.М. Соломенцева. – 2-е изд., испр. – М. : Высш. шк., 1999. – 312 с. |
|
3. |
Marion Grussendorf. English for Presentations. Express series. – Oxford : |
Oxford University Press, 2011. – 78 p.
137