
1769
.pdf80
1) Глубина резания t (мм). При фрезеровании это толщина слоя металла, измеренная перпендикулярно к обрабатываемой поверхности. Глубина резания t равна припуску либо части припуска на фрезерование. Припуск выгодно снимать за один проход, если позволяет мощность станка. Обычно t=2...6 мм. Если требуется высокая точность обработки, то фрезерование может проводиться в два прохода – черновой и чистовой. Для чистовых проходов обычно t=0,75...2 мм. Глубина резания t показана на рис. 4.17.
2)Подача S. При фрезеровании используется три размерности
подачи:
а) минутная подача SМ (мм/мин). Это величина перемещения обрабатываемой заготовки относительно фрезы за одну минуту;
б) подача на один оборот фрезы SО= SМ/n (мм/об). Это величина пе-
ремещения обрабатываемой заготовки относительно фрезы за время одно-
го оборота фрезы;
в) подача на один зуб фрезы SZ= SО/z = SМ/(n.z) (мм/зуб), где z – чис-
ло зубьев фрезы. Это величина перемещения обрабатываемой заготовки относительно фрезы за время углового поворота фрезы на один зуб.
Подача на зуб характеризует интенсивность нагрузки зуба, а следовательно, стойкость фрезы. Чтобы уменьшить машинное время на фрезерование, применяют максимально возможную подачу на зуб фрезы. Величина подачи выбирается по справочным нормативам в зависимости от шероховатости обработанной поверхности, прочности материала и других условий резания.
3)Ширина фрезерования B (мм) – ширина обрабатываемой поверхности в направлении, параллельном оси фрезы. При увеличении ширины фрезерования B возрастают суммарная площадь поперечного сечения среза, работа резания и тепловыделение. В результате снижается допускаемая скорость резания и возрастает износ фрезы. Ширина фрезерования B показана на рис. 4.17.
4)Скорость резания V (м/мин). При фрезеровании это окружная скорость вращения фрезы. Скорость резания связана с диаметром фрезы и частотой ее вращения зависимостью
V= D n/1000,
где D – наружный диаметр фрезы, мм; n – частота вращения фрезы, об/мин.
Скорость резания при фрезеровании назначается по эмпирической зависимости
V C |
|
Dq |
|
K, |
|
tx SZy |
Tm |
Bu zp |
|||
|
|
где С – коэффициент, характеризующий конкретные условия обработки; К – общий поправочный коэффициент, учитывающий отличные от таб-

81
личных условия резания; T – стойкость фрезы, мин; D – диаметр фрезы; z – число зубьев фрезы. Значения показателей степени x, y, m, u, p, q и коэффициентов приводятся в справочниках.
Влияние элементов резания на скорость резания
1.Подача на зуб фрезы SZ. При увеличении SZ растет толщина среза, работа деформации и трение, что приводит к снижению стойкости фрезы и допустимой скорости резания (скорость V необходимо уменьшить).
2.Глубина резания t. С увеличением глубины резания увеличивается угол контакта и количество зубьев фрезы, находящихся одновременно в работе, количество выделяющегося тепла (скорость V необходимо уменьшить).
3.Диаметр фрезы D. При увеличении диаметра фрезы D уменьшается толщина среза и снижается нагрузка на режущие кромки фрезы. Стойкость фрезы повышается (скорость V можно увеличить).
4.С уменьшением числа зубьев z увеличивается масса каждого зуба. Это приводит к лучшему теплоотводу и повышает скорость резания (скорость V можно увеличить).
Проверка элементов режима резания по мощности электродвигателя станка
1) Вычисляется тангенциальное усилие резания Pz. Это составляющая равнодействующей сил резания R, приложенной к фрезе (рис. 4.21). Pz направлена по касательной к траектории движения режущей кромки.
Pz определяется по формуле
Pz 10 Cp tx Szy Bu z Kp . Dq nw
Значения коэффициентов и показателей степени приводятся в справочниках.
2) По значению Pz определяется эффективная мощность резания Ne (кВт).
Ne |
Pz V . |
Рис. 4.21. Силы резания при работе |
||
60 1000 |
|
цилиндрической |
прямозубой |
Это мощность, необходимая для фрезой вращения фрезы.
3) Мощность электродвигателя станка потребуется большего значения с учетом КПД механизмов станка:
Nэл > Ne / .
Нормирование операции фрезерования. Производительность обра-
ботки Q и время изготовления одной детали Tшт при фрезеровании определяются по тем же формулам, которые приводились выше для нормирования токарной операции.

82
Отличие состоит лишь в том, что основное технологическое время To (время, которое тратится непосредственно на срезание припуска) при фрезеровании определяется зависимостью
Tо L i, Sм
где i – число проходов; Sм – минутная подача заготовки; L – расчетная длина обработки за один проход:
L=l+l1+l2,
где l – длина обрабатываемой заготовки; l1 – длина врезки; l2 – длина выхода фрезы.
К конструкциям деталей, обрабатываемых фрезерованием, предъявляется ряд требований, обеспечивающих их технологичность при обработке. Технологичной является конструкция детали:
–у которой обрабатываемые выступы имеют одинаковую высоту;
–обрабатываемые посадочные места под присоединяемые детали располагаются с наружной стороны корпуса;
–пазы открыты для ввода фрезы, иначе при обработке закрытых пазов потребуется засверливание отверстий для входа фрезы;
–форма пазов и прорезей позволяет вести обработку дисковыми, а не концевыми (торцевыми) фрезами.
4.5. Протягивание
Протягивание – высокопроизводительный метод обработки внутренних и наружных поверхностей, обеспечивающий высокую точность формы и размеров обрабатываемой поверхности. Протягивают многолезвийным режущим инструментом – протяжкой – при его поступательном движении относительно неподвижной заготовки (главное движение).
Метод протягивания заключается в том, что каждый зуб протяжки срезает с обрабатываемой поверхности стружку небольшой толщины. Это возможно потому, что размер каждого последующего зуба протяжки больше предыдущего. Обработанная поверхность характеризуется малой шероховатостью.
Протягивание является одним из наиболее высокопроизводительных процессов обработки деталей машин резанием, так как в работе одновременно находится большое количество зубьев инструмента. Для некоторых видов отверстий, например шлицевых, протягивание является единственным методом формообразования.
83
Протяжки
При протягивании используется сложный дорогостоящий инструмент – протяжки. Они представляют собой сложный многолезвийный инструмент с необходимым числом зубьев, формообразующих периметр обрабатываемой поверхности с рядом последовательно выступающих одно над другим лезвий в направлении, перпендикулярном направлению скорости главного движения.
По характеру обрабатываемых поверхностей протяжки делят на две основные группы: внутренние и наружные. Внутренними протяжками обрабатывают различные замкнутые поверхности, а наружными – полузамкнутые и открытые поверхности различного профиля. Протягивание наружных поверхностей в ряде случаев успешно заменяет строгание, фрезерование и даже шлифование.
По форме различают круглые, шлицевые, шпоночные, многогранные и плоские протяжки. Из всех разновидностей чаще всего применяют протяжки для обработки круглых отверстий. Внутренняя круглая протяжка предназначена для протягивания цилиндрических отверстий после сверления, растачивания или зенкерования.
По конструкции зубьев протяжки бывают режущими, выглаживающими и деформирующими. В первом случае зубья имеют режущие кромки, в двух последних – скругленные, работающие по методу пластического деформирования. Различают также сборные протяжки со вставными ножами, оснащенными пластинками из твердого сплава.
Разновидность протяжки – прошивка – отличается отсутствием хвостовика и шейки и при обработке проталкивается через отверстие. Прошивка работает на сжатие, протяжка – на растяжение. Прошивкой обрабатываются короткие отверстия различного сечения.
Элементы круглой протяжки (рис. 4.22)
Замковая часть (хвостовик) l1 служит для закрепления протяжки в патроне тянущего устройства станка; шейка l2 – для соединения замковой части с передней направляющей частью; передняя направляющая часть l3 вместе с направляющим конусом – для центрирования обрабатываемой заготовки в начале резания. Режущая часть l4 состоит из режущих зубьев, высота которых последовательно увеличивается на толщину срезаемого слоя, и предназначена для срезания припуска. Калибрующая часть l5 состоит из калибрующих зубьев, форма и размеры которых соответствуют форме и размерам последнего режущего зуба, и предназначена для придания обработанной поверхности окончательных размеров, необходимой точности и шероховатости. Задняя направляющая часть l6 служит для направления и поддержания протяжки от провисания в момент выхода последних зубьев калибрующей части из отверстия. Для облегчения образования стружки на режущих зубьях выполняют стружкоделительные канавки.

84
|
Рис. 4.22. Элементы круглой протяжки |
|
Геометрия зуба протяжки. Передние и зад- |
|
ние углы протяжки измеряют в плоскости, перпен- |
|
дикулярной к главной режущей кромке (рис. 4.23). |
|
Передний угол выбирают в зависимости от |
|
свойств обрабатываемого материала, задний угол |
Рис. 4.23. Геометрия |
– в зависимости от требуемой точности обработки. |
зуба протяжки |
Шаг режущих зубьев tр протяжки определяют |
|
в зависимости от длины протягиваемой поверхно- |
сти, при этом исходят из того, чтобы в резании участвовало не менее трех зубьев.
Виды поверхностей, обрабатываемых протягиванием
Спомощью протягивания получают следующие виды поверхностей:
1)Цилиндрические отверстия протягивают круглыми протяжками после сверления, растачивания или зенкерования. Применяют также протягивание отверстий, полученных при литье и штамповке, без предварительной их обработки. Обычно длина отверстий не превышает трех диаметров.
Если торец отверстия в заготовке не обработан, то для ее установки применяют приспособления со сферической опорной поверхностью (рис. 4.24, а). Заготовка в этом случае может самоустанавливаться (центрироваться) по оси протяжки. В тех случаях, когда после предыдущей обработки получен торец детали, перпендикулярный к оси протягиваемого отверстия, заготовка опирается на жесткую (неподвижную) поверхность.
2)Многогранные отверстия (треугольные, квадратные и т. п.) протягивают многогранными протяжками. Исходной поверхностью для протягивания служит круглое отверстие. На рис. 4.24, б приведена схема протягивания квадратного отверстия.
3)Шлицевые отверстия с различным профилем шлицев протягивают многошлицевыми протяжками, формирующими одновременно весь профиль отверстия. На рис. 4.24, в приведена схема протягивания прямых шлицев. Винтовые шлицы протягивают протяжкой, режущие зубья которой расположены по винтовой линии, с приспособлением, обеспечивающим дополнительное вращение протяжки (рис. 4.24, г) или заготовки.
4)Шпоночные и другие пазы протягивают протяжками, форма зубьев которых в поперечном сечении соответствует профилю протягиваемого паза. Шпоночные пазы протягивают плоской шпоночной протяжкой (рис. 4.24, д) с применением специального приспособления – направляющей

85
втулки 3. Вдоль всей втулки прорезают прямоугольный паз, который является направляющим для протяжки.
Рис. 4.24. Схемы обработки заготовок на протяжных станках: 1 – заготовка; 2 – протяжка; 3 – направляющая втулка
5) Наружные поверхности различной геометрической формы с пря-
молинейной образующей протягивают на вертикально-протяжных станках для наружного протягивания, а также на станках непрерывной обработки конвейерного типа.
На рис. 4.24, е приведена схема протягивания вертикальной плоско-
сти.
На специальных протяжных станках можно обрабатывать наружные поверхности заготовок формы тел вращения плоскими (рис. 4.24, ж) и дисковыми (рис. 4.24, з) протяжками. В обоих случаях заготовке сообщают

86
круговую подачу. Плоская протяжка имеет главное движение – поступательное, а дисковая протяжка – вращательное вокруг своей оси.
Режим резания
Скорость резания при протягивании – это скорость поступательного движения V протяжки относительно заготовки. Скорость резания лимитируется условиями получения обработанной поверхности высокого качества и ограничивается технологическими возможностями протяжных станков. Обычно V = 8...15 м/мин.
Подача при протягивании как самостоятельное движение инструмента или заготовки отсутствует. За величину подачи Sz, определяющую толщину срезаемого слоя отдельным зубом протяжки, принимают подъем на зуб, т. е. разность размеров по высоте двух соседних зубьев протяжки.
Sz является одновременно и глубиной резания. Подача в основном зависит от обрабатываемого материала, конструкции протяжки и жесткости заготовки и составляет 0,01...0,2 мм/зуб. Оптимальные параметры режима резания выбирают из справочников.
При протягивании технологичной является конструкция детали:
–у которой торец заготовки перпендикулярен оси отверстия со стороны входа и выхода протяжки, что исключает перекос протяжки при обработке;
–фасонные отверстия при протяжке должны иметь симметричную
форму.
4.6. Строгание
Строгание применяется при обработке плоских и фасонных линейчатых поверхностей и различных канавок в условиях единичного и мелкосерийного производства.
Главное движение V при строгании – возвратно-поступательное прямолинейное, а движение подачи S – шагообразное, направленное перпендикулярно главному движению (рис. 4.25).
Обработку выполняют на строгальных станках. Инструмент – строгальные резцы, конструкция которых сходна с конструкцией токарных резцов.
Процесс резания при строгании имеет прерывистый характер, и срезание стружки происходит только при встречном относительном движении резца и заготовки. Во время обратного (вспомогательного) хода резец работу не производит. Врезание резца в заготовку в начале каждого рабочего
87
хода сопровождается ударом. За время холостого хода резец остывает, поэтому при строгании в большинстве случаев не применяются смазочноохлаждающие жидкости. Ударные нагрузки и циклический характер нагрева существенно снижают стойкость резцов в сравнении с непрерывным резанием, поэтому строгание производят при умеренных скоростях резания. Головки и державки строгальных резцов выполняют более массивными, чем у токарных.
При строгании параметрами режима резания, так же как и при точении, являются скорость резанияV, подача S и глубина резания t.
При строгании технологичной является конструкция детали:
–у которой форма поверхности представляет плоскость или сочетание плоскостей;
–обрабатываемые поверхности расположены в одной плоскости, что позволяет обрабатывать их за один проход;
–обрабатываемые поверхности заготовки расположены в параллельных плоскостях и имеют разделительные канавки для выхода резца;
–в углах пересечения обрабатываемых поверхностей предусмотрена разделительная канавка для выхода резца;
–пазы, обрабатываемые строганием, являются сквозными, обеспечивая свободный заход и выход резца.
5.АБРАЗИВНАЯ И ОТДЕЛОЧНАЯ ОБРАБОТКА ЗАГОТОВОК ДЕТАЛЕЙ МАШИН РЕЗАНИЕМ
5.1. Общая характеристика абразивной механической обработки резанием
Отличительной особенностью абразивной обработки является наличие различным образом ориентированных режущих зерен абразивного инструмента, каждое из которых представляет собой микроклин.
Основными видами абразивной обработки являются шлифование,
притирка (доводка), хонингование, суперфиниширование и полирование.
Абразивные зерна имеют острые кромки различных размеров, которыми снимается тонкий слой металла с заготовки, когда инструмент соприкасается с поверхностью обрабатываемой заготовки и перемещается (движется) относительно ее (рис. 5.1).
Процессы снятия стружки металлическими и абразивными инструментами принципиально одинаковы. Под действием приложенной силы лезвия зерен абразивного инструмента углубляются в поверхность обрабатываемой заготовки и при движении производят сдвиг и скалывание стружки.
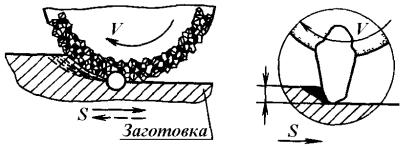
88
Рис. 5.1. Взаимодействие абразивного инструмента с поверхностью заготовки на примере шлифования
Например, при шлифовании заготовки при помощи шлифовального круга каждое абразивное зерно в зоне обработки работает как зуб фрезы, снимая стружку с детали в пределах определенного угла поворота (см. рис. 5.1).
Однако, в отличие от лезвийной обработки, при абразивной обработке материал срезается в виде очень большого числа тонких стружек. Обработанная поверхность представляет совокупность микроследов абразивных зерен, поэтому она имеет малую шероховатость.
При абразивной обработке часть зерен, ориентированных к направлению резания тупой гранью, в процессе резания не участвуют. Они вызывают потери энергии на трение, пластическое деформирование, увеличивают нагрев контактирующих поверхностей инструмента и заготовки. Эти явления проявляются сильнее при высоких скоростях и больших усилиях резания, что особенно характерно для метода шлифования. Возможно образование на поверхности детали дефектного слоя. Для отвода теплоты при абразивных методах обработки процесс ведется с обильной подачей смазочно-охлаждающей жидкости.
Основная область применения процессов абразивной обработки – чистовая и отделочная обработка заготовок деталей машин для обеспечения высокой точности размеров и малой шероховатости поверхности. Кроме того, шлифование используется как один из методов размерной обработки труднообрабатываемых материалов: керамики, ситаллов, твердых сплавов, деталей из закаленных сталей и т. д.
С развитием малоотходной технологии доля обработки лезвийным инструментом будет уменьшаться, а абразивным – увеличиваться.
Такие методы абразивной обработки, как притирка, хонингование, суперфиниширование и полирование, относятся исключительно к отделочной группе методов обработки резанием.
Область применения отделочных методов обработки: при необхо-
димости получения поверхностей с высокой точностью и малой шероховатостью, которых невозможно достичь обычными методами обработки.
89
Особенности отделочных методов обработки: малые силы резания,
малая толщина срезаемого слоя материала, незначительное тепловыделение и деформация заготовки.
Предварительно поверхность заготовки должна быть обработана с высокой точностью обычными методами.
В промышленности применяют несколько видов абразивных инструментов, используемых при разных видах абразивной обработки: 1)
шлифовальные круги (наиболее распространены); 2) абразивные головки; 3) абразивные бруски; 4) абразивные сегменты; 5) алмазные круги; 6) пасты и шкурки для доводки и полирования.
Абразивные инструменты пп. 1...5 стандартизированы и состоят из: а) абразивных зерен; б) связки, удерживающей зерна; в) пор (пустот).
Основные характеристики абразивного инструмента
1.Вид абразивного материала.
Вкачестве абразивных материалов наиболее часто используются электрокорунд, карбид кремния, природные и синтетические алмазы, эльбор (искусственный материал на основе нитрида бора) и другие материалы. Это минералы естественного или искусственного происхождения, зерна которых обладают достаточной твердостью и способностью резания. Высокая твердость обеспечивает зернам высокие режущие свойства, способность разрушать поверхностные слои очень твердых материалов, в том числе таких, которые трудно и невыгодно обрабатывать лезвийным металлическим инструментом.
2. Зернистость (размер абразивных зерен).
Чем крупнее зерна, тем выше производительность, однако ниже качество обработки (поверхность более шероховатая). Поэтому инструменты, изготовленные из крупнозернистого абразива, используются для черновой и обычной обработки (при шлифовании), мелкозернистые – для отделочных и особо тонких работ.
3.Вид материала связки.
Связка – это цементирующее вещество, скрепляющее зерна друг с другом. Связка может быть неорганической, органической и металлической. Из неорганических связок наиболее широко используется керамическая.
4. Твердость инструмента.
Под твердостью абразивного инструмента понимают сопротивление связки вырыванию абразивных зерен внешней силой.
Твердость инструмента должна быть подобрана для конкретного обрабатываемого материала таким образом, чтобы обеспечить самозатачивание круга или другого абразивного инструмента при максимальной его стойкости.
Если взять слишком мягкий круг, у которого связка слабо удерживает зерна, то они будут удаляться с круга раньше, чем затупятся. Произой-