
1769
.pdf
130
А. Переработка пластмасс в вязкотекучем состоянии 1) Прессование (один из основных способов переработки реактопла-
стов в детали).
Рис. 7.2. Схема прямого прессования
В полость матрицы пресс-формы 8 (рис. 7.2, а) загружают предварительно таблетизированный или порошкообразный материал 2. При замыкании пресс-формы под действием усилия пресса пуансон 1 создает давление на прессуемый материал (рис. 7.2, б). Под действием этого давления и теплоты от нагретой пресс-формы материал размягчается и заполняет формообразующую полость пресс-формы. После определенной выдержки, необходимой для отверждения материала, пресс-форма раскрывается и с помощью выталкивателя 5 из нее извлекается готовая деталь 4 (рис. 7.2, в).
Прямым прессованием получают детали средней сложности и небольших размеров.
2) Литье под давлением (один из основных способов переработки термопластов в детали).
Рис. 7.3. Схема литья под давлением
Перерабатываемый материал из загрузочного бункера 8 (рис. 7.3) подается дозатором 9 в рабочий цилиндр 6 с электронагревателем 4. При движении поршня 7 определенная доза материала поступает в зону обогре-

131
ва, а уже расплавленный материал через сопло 8 и литниковый канал – в полость пресс-формы 1, в которой формируется изготовляемая деталь 2. В рабочем (нагревательном) цилиндре на пути потока расплава установлен рассекатель 5, который заставляет расплав протекать тонким слоем у стенок цилиндра. Это ускоряет прогрев и обеспечивает более равномерную температуру расплава. При движении поршня в исходное положение с помощью дозатора 9 очередная порция материала попадает в рабочий цилиндр. Для предотвращения перегрева выше 50...70 0С в процессе литья пресс-форма охлаждается проточной водой. После охлаждения материала пресс-форма размыкается и готовая деталь с помощью выталкивателей извлекается из нее.
Литьем под давлением получают детали сложной конфигурации с различными толщинами стенок, ребрами жесткости, с резьбами и т. д. Применяют литейные машины, позволяющие механизировать и автоматизировать процесс получения деталей. Производительность процесса литья
в20...40 раз выше производительности прессования.
3)Непрерывное выдавливание, или экструзия (способ переработки термопластов).
Отличается от других способов переработки термопластов непрерывностью, высокой производительностью процесса и возможностью получения на одном и том же оборудовании большого многообразия деталей.
Рис. 7.4. Непрерывное выдавливание: а – схема установки; б – профили получаемых деталей
Выдавливание осуществляют на специальных червячных машинах. Перерабатываемый материал в виде порошка или гранул из бункера 1 (рис. 7.4, а) попадает в рабочий цилиндр 8, где захватывается вращающимся червяком 2. Червяк продвигает материал, перемешивает и уплотняет его. В результате передачи теплоты от нагревательного элемента 4 и выделения теплоты при трении частиц материала друг о друга и о стенки цилиндра перерабатываемый материал переходит в вязкотекучее состояние и непре-

132
рывно выдавливается через калиброванное отверстие головки 6. Расплавленный материал проходит через радиальные канавки оправки 5. Оправку применяют для получения отверстия при выдавливании труб.
Непрерывным выдавливанием можно получить детали различного профиля (рис. 7.4, б). При получении пленок из термопластов (полиэтилена, полипропилена и др.) используют метод раздува сжатым воздухом.
Б. Переработка пластмасс в высокоэластичном состоянии
В высокоэластичном состоянии из нагретых термопластов получают в основном крупногабаритные детали.
Рис. 7.5. Схема пневматической формовки
1. Пневмоформовка.
Нагнетанием воздуха создается разность давлений, под действием которой происходит формоизменение заготовки согласно профилю матри-
цы (рис. 7.5).
2. Вакуум-формовка.
Для вакуумной формовки схема будет аналогична схеме пневматической формовки (см. рис. 7.5), только перепад давления будет создаваться откачиванием воздуха из полости матрицы. Нагнетатель при этом отсутствует.
Рис. 7.6. Схемы штамповки пластмасс: а – жесткими пуансонами; б – эластичными пуансонами
133
Ограничение метода вакуумной формовки – максимальная толщина стенок заготовки должна быть не более 2 мм из-за небольшого возможного перепада давлений.
3. Штамповка жесткими и эластичными пуансонами.
Выполняется по технологии, аналогичной технологии листовой штамповки металлов. Схемы процессов штамповки жесткими и эластичными пуансонами приведены на рис. 7.6.
Сварка пластмасс выполняется следующими основными методами:
–газовым теплоносителем;
–нагретым инструментом (контактная сварка);
–экструдируемой присадкой (расплавом);
–токами высокой частоты;
–ультразвуком, трением и вибротрением.
Обработка пластмасс резанием. Производится на обычных метал-
лообрабатывающих станках по традиционным схемам обработки. Пластмассы имеют более низкие механические характеристики, чем металлы, однако низкая теплопроводность пластмасс приводит к концентрации теплоты, образующейся в зоне резания. Это ограничивает допустимую скорость резания.
Склеивание пластмасс. Выполняется растворителями (дихлорэтан, бензол и др.).
Изделия из пластмасс находят самое широкое применение во всех отраслях техники.
7.3. Основы технологии производства изделий из резины
Резина – органический материал на основе каучука, представляющий собой пластмассу с редкосетчатой структурой, в которой связующим выступает полимер, находящийся в высокопластическом состоянии. В резинах связующими являются каучуки натуральные или синтетические (последние наиболее широко применяются).
В зависимости от числа поперечных связей между макромолекулами каучука, образовавшихся при вулканизации, различают твердые и мягкие резины (чем больше этих связей, тем тверже резина).
Основные этапы изготовления резиновых изделий: а) приготовление резиновой смеси; б) формование; в) вулканизация.
Сырьем для получения синтетических каучуков является нефть, нефтепродукты, природный газ, древесина и т. д.
Для приготовления резиновой смеси каучук разрезают на куски и пластифицируют (рязмягчают) путем многократного пропускания через нагретые валки, предварительно подогретые до температуры 40...50 0С. Находясь в пластичном состоянии, каучук обладает способностью хорошо
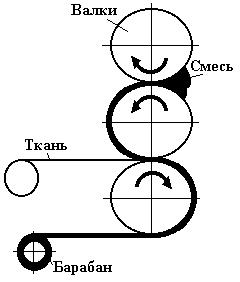
134
смешиваться с другими компонентами. Смешение проводят в червячных или валковых смесителях. Каучук смешивают с порошкообразными компонентами: вулканизаторами (сера), наполнителями и т. д. Получается сырая резина – пластичная клейкая масса.
|
Листовую резину (сырую) и проре- |
|
зиненную ткань получают каландрирова- |
|
нием (рис. 7.7). Операцию выполняют на |
|
многовалковых машинах – каландрах. |
|
В процессе получения прорезинен- |
|
ной ткани в зазор между валками каланд- |
|
ров (см. рис. 7.7) одновременно пропуска- |
|
ют пластифицированную сырую резино- |
|
вую смесь и ткань. Резиновая смесь посту- |
|
пает в зазор между верхним и средним |
|
валками, обволакивает средний валок и |
|
поступает в зазор между средним и ниж- |
|
ним валками, через который проходит |
Рис. 7.7. Схема получения проре- |
ткань. Средний валок вращается с большей |
зиненных тканей |
скоростью, чем нижний. Разность скоро- |
|
стей обеспечивает втирание резиновой |
смеси в ткань. Толщину резиновой пленки на ткани регулируют, изменяя зазор между валками каландра. Полученную ткань наматывают на барабан и затем вулканизируют.
Валки каландров снабжают системой внутреннего обогрева или охлаждения, что позволяет регулировать температурный режим. Листы резины, полученные прокаткой на каландрах, сматывают в рулоны и используют затем в качестве полуфабриката для других процессов формообразования резиновых деталей.
Во избежание слипания резины в рулоне ее посыпают тальком или мелом при выходе из каландра.
Резиновые изделия сложной формы получают выдавливанием, прессованием, литьем под давлением. Схемы аналогичны схемам обработки пластмасс.
Каучук в натуральном виде в промышленности не применяют, его после формообразования превращают в резину вулканизацией. В качестве вулканизирующего вещества обычно используют серу. Количество серы определяет эластичность (мягкость) резиновых деталей. Чем больше вулканизирующего вещества, тем эластичность ниже. Готовые изделия вулканизируют в специальных камерах при температуре 120...150 0С в атмосфере водяного пара. Происходит химическая реакция серы и каучука с образованием поперечных связей между макромолекулами каучука.
Высокая эластичность, способность к большим обратимым деформациям, стойкость к действию активных химических веществ, малая водо-
135
и газопроницаемость, хорошие диэлектрические и другие свойства резины обусловили ее применение во всех отраслях народного хозяйства. В машиностроении применяют разнообразные резиновые технические детали; ремни – для передачи вращательного движения с одного вала на другой; шланги и напорные рукава – для передачи жидкостей и газов под давлением; сальники, манжеты, прокладочные кольца и уплотнители – для уплотнения подвижных и неподвижных соединений; муфты, амортизаторы – для гашения динамических нагрузок; конвейерные ленты – для оснащения по- грузочно-разгрузочных устройств и т. д.
7.4. Основы технологии производства композиционных материалов
Композиционный материал – это искусственный материал, который состоит из двух и более компонентов различного химического состава, объединенных в монолит. Его свойства отличны от свойств компонентов, взятых в отдельности (например, гораздо выше прочность, жесткость).
Компонент композиционного материала, который обладает непрерывностью по всему объему, называется матрицей. Прерывистый компонент, имеющий обычно большую прочность и твердость, называется уп-
рочнителем или наполнителем.
По геометрии наполнителя композиты подразделяют:
1)с нуль-мерными наполнителями, размеры которых в трех измерениях имеют один порядок (частицы);
2)с одномерными наполнителями, один из размеров которых значительно превосходит два других (нитевидные кристаллы, волокна);
3)с двухмерными наполнителями (пластины, фольга в плоскостях). Композит 1 типа обычно представляет собой металлическую матри-
цу (Al, Ni) с дисперсными частицами тугоплавких оксидов, нитридов, боридов, карбидов. Размеры частиц составляют 0,01...50 мкм.
В таких материалах матрица воспринимает всю нагрузку, а частицы наполнителя препятствуют развитию пластической деформации. Эффективное упрочнение достигается при 5...10 % объема частиц наполнителя.
Получение композитов 1 типа возможно: а) методами порошковой металлургии (смешивание порошков матрицы и наполнителя, изостатическое прессование, спекание); б) введением частиц наполнителя в жидкий расплав металла в сочетании с перемешиванием ультразвуком.
Характерные примеры композитов 1 типа:
– Алюминий с частицами Al2O3. Он хорошо обрабатывается резанием, деформируется в горячем состоянии ковкой и штамповкой, сваривается аргонодуговой и контактной сваркой. Детали (лопатки компрессоров, вен-
136
тиляторов, турбин, поршневые штоки) работают при 300...500 0C. Обычный алюминий при этих температурах разупрочняется.
–Никель с частицами диоксида тория ThO2 или диоксида гафния HfO2 (не более 2 %). При низких температурах уступает по прочности жаропрочным никелевым сплавам, однако при высоких температурах намного превосходит. Деформируется ковкой, штамповкой и т. д. Детали соединяют пайкой или диффузионной сваркой без расплавления (при расплав-
лении происходит агломерация частиц наполнителя и потеря жаропрочности). Детали (авиационных двигателей) работают при 1100...1200 0C в агрессивных средах. Это сопловые лопатки, стабилизаторы пламени, камеры сгорания, трубопроводы.
В композитах 2 типа упрочнителями являются нитевидные кристаллы, волокна или проволоки. Матрица чаще всего металлическая (Al, Ni и др.). Матрица защищает волокна от повреждений, передает нагрузку на волокна и перераспределяет напряжения в случае разрыва отдельных волокон.
Требования к композитам 2 типа:
–волокно должно иметь более высокие значения модуля упругости, чем у матрицы;
–прочные волокна должны быть равномерно распределены в пластичной матрице;
–объем упрочняющих волокон в матрице должен быть больше критического значения (иначепрочностьнеповышается,анаоборот, снижается);
–на границе между матрицей и волокном при нагружении композита не должно возникать проскальзывания вплоть до разрушения композита.
На границе между матрицей и волокном композита происходят диффузионные процессы, химические реакции, образуются интерметаллиды (хрупкие фазы – соединения металлов). С одной стороны, это увеличивает сцепление между матрицей и волокном, с другой – снижает прочность волокна. Проблему снижения прочности решают нанесением покрытий на волокна и легированием матрицы.
Композиты, армированные волокнами, – анизотропный материал (механические свойства зависят от угла взаимного расположения волокон
ивектора нагрузки, то есть механические свойства будут неодинаковы в разных направлениях). Недостаток анизотропии может быть устранен при армировании матрицы сетками из волокон.
Методы получения композитов, армированных волокнами
1. Твердофазные.
Материал матрицы в виде листов, проволоки или порошка соединяют с волокнами диффузионной сваркой под давлением, сваркой взрывом, прокаткой, прессованием с последующим спеканием (порошковой металлургией).
2. Жидкофазные.
137
Волокна пропитываются расплавом материала матрицы в вакууме или под давлением (применение метода ограничено из-за реакции волокон с металлическим расплавом).
3. Газопарофазные.
Этим методом наносят на волокна барьерные покрытия, которые защищают их от разрушения (нитриды, бориды, оксиды, карбиды). Покрытия получают разложением летучих карбонилов либо испарением металлов с одновременным термическим воздействием электронного луча, ионного пучка. Производительность этих методов крайне низкая.
4. Плазменное напыление.
Покрытие из матричного материала наносится на волокна без существенного повышения их температуры, однако прочность связи такого покрытия невысокая.
5. Химические.
Позволяют осаждать металлические покрытия на непроводящие ток кристаллы сапфира, углеродные волокна и т. д. Ионы металла восстанавливаются на поверхности волокон.
6. Электролиз.
Волокна находятся в контакте с катодом.
Армирующие материалы и их свойства
1. Проволоки.
Это наиболее экономичный и доступный армирующий материал. Диаметр – десятые и сотые доли миллиметра. Используется сталь, бериллий (при невысоких температурах эксплуатации композита), молибден, вольфрам (при высоких температурах). Проволоку получают волочением, при этом происходит увеличение прочности и снижается пластичность.
2. Волокна.
2.1. Углеродные волокна.
Получают из полиакрилнитрильного гидроцеллюлозного волокна или из волокон на основе нефтяных смол методом термического разложения. При этом происходит окисление (при t=200...300 0С, создается оптимальная структура углерода), карбонизация (свыше 900 0С в атмосфере водорода, волокнам придается огнестойкость) и графитизация (свыше 2500 0С в инертной среде). Температура графитизации влияет на свойства волокон (прочность, упругость).
Промышленно выпускаются волокна в виде жгутов из 1000...160000 волокон каждый. Диаметр отдельного волокна около 7 мкм.
Углеродные волокна окисляются на воздухе, химически активны при взаимодействии с металлическими матрицами, имеют слабую адгезию с полимерными матрицами. Эти недостатки устраняются при нанесении на волокна защитных покрытий (металл, керамика).
2.2. Борные волокна.
138
Получают осаждением бора из газовой фазы на нагретую вольфрамовую проволоку диаметром 12 мкм. Образуется волокно из поликристаллов бора диаметром 70...200 мкм, у которого сердцевина диаметром 15...17 мкм состоит из боридов вольфрама, имеющих меньшую прочность. Борное волокно сочетает низкую плотность, высокую прочность и высокий модуль упругости при температуре плавления 2300 0С. Промышленно выпускаются в виде моноволокон на катушках и в виде лент полотняного плетения шириной 5...50 см. Волокнами бора армируют полимерные и алюминиевые матрицы.
2.3. Волокна карбида кремния.
Получают аналогично борным. Уступают борным по прочности и качеству.
2.4. Стеклянные волокна.
Основа – диоксид кремния SiO2. Получают пропусканием расплавленного стекла при 1200...1400 0С через фильеры диаметром 0,8...3 мм и дальнейшим быстрым вытягиванием до диаметра 3...100 мкм. Соединяют в пряди на барабанах. Широко используют для армирования пластиков.
2.5. Волокна из оксида алюминия. 3. Нитевидные кристаллы (усы).
SiC, Al2O3, B4C, Si3N4 и другие тугоплавкие карбиды и нитриды. Получают осаждением из газовой фазы. Длина кристаллов достигает 60...80 мкм. Имеют прочность близкую к теоретической.
Эвтектические композиты – это сплавы эвтектического состава (механическая смесь), в которых упрочняющей фазой выступают ориентированные кристаллы, полученные направленной кристаллизацией.
В качестве кристаллов твердой прочной фазы выступают карбиды, интерметаллиды. Форма кристаллов – волокна (если их доля меньше 32 %) или пластины.
Достоинства эвтектических композитов:
–простота получения за одну операцию;
–направленная ориентированная структура может быть получена на уже готовых изделиях;
–композит имеет высокую термическую стабильность;
–нет химического взаимодействия, ослабляющего волокна.
Матрица – Al, Mg, Cu, Ni, Co, Ti, Nb, Ta и др.
Пример эвтектического композита: композиция Al + Al3Ni. Направ-
ленность частиц Al3Ni достигается кристаллизацией со скоростью 2...10 см/ч, при этом прочность сплава возрастает от 90 до 330 МПа.
Композиты на неметаллической основе. Матрица – эпоксидная, по-
лиэфирная, фенольная и др. смолы. Волокна: стеклянные, углеродные, борные, органические.
139
Достоинства неметаллических композитов: стойкость к воздействию агрессивных сред, хорошие антифрикционные и фрикционные свойства, теплозащитные и амортизационные свойства, невысокая стоимость.
Недостатки неметаллических композитов: низкая прочность и жесткость при сжатии и сдвиге, снижение прочности уже при T=100...200 0С, старение.
Обработка и соединение композитов
Ввиду того, что изменение размеров и формы композитов связано с объективными трудностями (разрушение волокон и др.), необходимо по возможности совмещать процесс получения композита и изготовления из него детали.
При необходимости соединение композитов производят через матрицу. Если в месте соединения волокна разрываются, то для обеспечения прочности соединения используют большие перекрытия (отношение длины перекрытия к толщине изделия L/S > 20).
Металлические композиты надежнее и дешевле всего соединять точечной сваркой (волокна при этом не перерезаются).
Соединение с помощью болтов, заклепок менее эффективно (разрушаются волокна).
Также используется пайка и склеивание.
Композиты в основном хорошо обрабатываются резанием. Широко применяется резка абразивным инструментом. Трудности возникают при резании композитов с вольфрамовой проволокой диаметром 0,3 мм и более. Не поддаются обработке резанием (быстро разрушают инструмент и сами разрушаются) композиты с борным волокном.
8. АВТОМАТИЗАЦИЯ ПРОИЗВОДСТВА ИЗДЕЛИЙ
8.1. Основные направления автоматизации
Автоматизация представляет собой совокупность мероприятий по разработке, созданию и внедрению автоматически действующих средств производства. Она позволяет существенно повысить производительность труда, облегчить условия работы, повысить качество выпускаемой продукции.
Основными направлениями автоматизации сварочных процессов, литейного производства, обработки заготовок давлением, резанием и фи- зико-химическими методами являются: автоматизация органов управления машин и оборудования, повышение производительности и точности их работы, автоматизация установки и снятия заготовок, автоматизированный контроль; разработка конструкций быстропереналаживаемых автоматов и автоматических систем. Одним из основных направлений в решении задач