
1769
.pdf
120
процессами. Вакуумные среды позволяют обрабатывать заготовки из легкоокисляющихся активных материалов. С помощью электронного луча можно наносить покрытия на поверхности заготовок в виде пленок толщиной от нескольких микрометров до десятых долей миллиметра.
Недостатком обработки является то, что она возможна только в вакууме.
Светолучевая обработка
Светолучевая (лазерная) обработка основана на тепловом воздействии светового луча высокой энергии на поверхность обрабатываемой заготовки. Источником светового излучения служит лазер – оптический квантовый генератор (ОКГ). Созданы конструкции твердотелых, газовых и полупроводниковых ОКГ. Их работа основана на принципе стимулированного генерирования светового излучения.
Атом вещества, имея определенный запас энергии, находится в устойчивом энергетическом состоянии и располагается на определенном энергетическом уровне. Для выведения атома из устойчивого энергетического состояния его необходимо возбудить. Возбуждение («накачку») активного вещества осуществляют световой импульсной лампой. Возбужденный атом, получив дополнительный фотон от системы накачки, излучает сразу два фотона, в результате чего происходит своеобразная цепная реакция генерации лазерного излучения.
Для механической обработки используют твердотелые ОКГ, рабочим элементом которых является рубиновый стержень, состоящий из оксидов алюминия, активированных 0,05 % хрома. Рубиновый ОКГ работает в импульсном режиме.
|
Принцип действия ОКГ (рис. 6.14): |
|
электрическая энергия источника тока 1, |
|
запасенная в батарее конденсаторов 2, |
|
преобразуется в световую энергию им- |
|
пульсной лампы 4. Свет лампы 4 фокуси- |
|
руется на рубиновый стержень 5, и атомы |
|
хрома в стержне под действием световой |
|
энергии переходят в возбужденное состоя- |
|
ние (электрон поднимается на более высо- |
Рис. 6.14. Схема оптического |
кую орбиту). Если в возбужденном со- |
квантового генератора: 1 – источ- стоянии атом получает еще один фотон, то
ник тока; |
2 – батарея конденсато- |
он излучает сразу два фотона, и одновре- |
ров; 3 – корпус; 4 – импульсная |
менно электрон переходит на более низ- |
|
лампа; 5 |
– рубин; 6 – линзы; 7 – |
кую орбиту, атом возвращается в нор- |
|
заготовка |
мальное состояние. В стержне 5 происхо- |
|
|
дит цепная реакция. Энергия, запасенная в течение 10–3 с, выделяется за очень короткое время (около 10–6 с) и сосредотачивается в луче диаметром
121
около 0,01 мм. Линза 6 фокусирует луч на заготовке, в результате чего элементарный объем материала заготовки 7 расплавляется и испаряется.
Лучи света имеют высокую направленность. Расходимость луча обычно не превышает 0,10. Энергия светового импульса ОКГ обычно невелика и составляет 20...100 Дж, но она выделяется в миллионные доли секунды и сосредоточивается в луче диаметром 0,01 мм. В фокусе диаметр светового луча составляет всего несколько микрометров, что обеспечивает температуру 6000...8000 0С. В результате этого поверхностный слой материала заготовки, находящийся в фокусе луча, мгновенно расплавляется и испаряется.
Лазерную обработку применяют для прошивания сквозных и глухих отверстий, разрезки заготовок на части, вырезания заготовок из листовых материалов, прорезания пазов. Этим методом можно обрабатывать заготовки из любых материалов, включая самые твердые и прочные. Например, лазерную обработку отверстий применяют при изготовлении диафрагм для электронно-лучевых установок, дюз для дозирования воздуха или газов, деталей топливной аппаратуры дизелей, сит. Диафрагмы изготовляют из вольфрамовой, танталовой, молибденовой или медной фольги толщиной около 50 мкм при диаметре отверстия 20...30 мкм. С помощью лазерного луча можно выполнять контурную обработку по аналогии с фрезерованием, т. е. обработку поверхностей по сложному периметру. Перемещениями заготовки относительно светового луча управляют системы ЧПУ, что позволяет прорезать в заготовках сложные криволинейные пазы или вырезать из заготовок детали сложной геометрической формы.
6.7. Плазменная обработка
Сущность плазменной обработки: поток плазмы (полностью ионизированный газ, состоящий из положительных ионов и электронов) направляется на поверхность обрабатываемой заготовки.
Плазму получают в плазмотронах (рис. 6.15). Дуговой разряд 3 возбуждается между вольфрамовым электродом 5 и медным электродом 4, выполненным в виде трубы и охлаждаемым проточной водой. В трубу подают газ (аргон, азот) или смесь газов. Обжимая дуговой разряд, газ при соединении с электронами ионизируется и выходит из сопла плазмотрона в виде ярко светящейся струи 2, которая направляется на обрабатываемую заготовку 1.
Плазма имеет температуру 10000...30000 0С и характеризуется высокой электропроводностью, что позволяет управлять формой плазменной струи посредством магнитных и электромагнитных полей, концентрировать тепловую энергию на узком участке (сжимать струю плазмы).

|
122 |
|
Плазменным методом обрабатыва- |
|
ют заготовки из любых материалов, вы- |
|
полняя прошивание отверстий, вырезку |
|
заготовок из листового материала, стро- |
|
гание, точение. При прошивании отвер- |
|
стий, разрезке и вырезке заготовок голов- |
|
ку устанавливают перпендикулярно к по- |
|
верхности заготовки, при строгании и то- |
|
чении – под углом 40...60 0. |
|
Основное преимущество плазмен- |
|
ной обработки – возможность обработ- |
|
ки практически любых материалов с вы- |
Рис. 6.15. Схема плазменной |
сокой производительностью. |
головки |
Метод плазменной обработки в це- |
|
лом характеризуется наибольшей произ- |
водительностью по сравнению с другими методами физико-химической обработки.
6.8. Комбинированные физико-химические методы обработки
Разработаны комбинированные методы обработки деталей, сочетающие преимущества методов электрохимической обработки (ЭХО, называемого также анодным растворением), электроэрозионной обработки, механической обработки, ультразвукового вибрационного воздействия, плазменной обработки.
Электроэрозионно-химический метод обработки (ЭЭХО)
В зазоре между электродами одновременно протекает два процесса – электроэрозионное разрушение металла искровыми разрядами, нагревом контактных перемычек и его анодное растворение в проточном электролите. В качестве электролита используется обычно водный раствор жидкого натриевого стекла. Материал инструмента должен быть эрозионностойким, теплостойким и прочным (графит, вольфрам). Разряд в электролите происходит после возникновения между электродами изолирующего газопарового слоя (водород, выделяющийся на катоде).
Преимуществом ЭЭХО является взаимное ослабление действия факторов, ограничивающих съем металла при раздельном использовании методов.
То есть комбинированный метод имеет большую производительность, чем ЭХО, при меньшей точности. Рекомендуется для выполнения черновых операций.

123
Анодно-механический метод обработки
Основан на электрохимическом растворении металла заготовки с последующим его удалением механическим путем. В общем случае происходит одновременно три процесса: 1) анодное растворение (как при электрохимической обработке); 2) электроэрозия; 3) механическое удаление металла с продуктами растворения и эрозии.
Производительность метода выше, чем при анодном растворении.
Рис. 6.16. Принципиальная схема анодно-механической установки и процесса обработки: 1 – инструмент-электрод; 2 – электролит; 3 – заготовка; 4 – продукты распада
Принципиальная схема процесса обработки показана на рис. 6.16. При сближении электродов 3 (обрабатываемое изделие) и 1 (инструмент) и при наличии между ними электролита (рабочей жидкости) 2 во время прохождения тока происходит разрушение электрода, соединенного с положительным источником тока (анодом). Это разрушение при низких плотностях тока осуществляется в виде анодного растворения металла, а при высоких плотностях – в виде его электроэрозионного разрушения. Образующиеся продукты распада 4 плохо проводят ток и изолируют один электрод от другого. Для удаления их осуществляют движение электрода 1 (инструмента) с небольшим усилием. В этом случае процесс протекает непрерывно, обнажающийся материал заготовки продолжает разрушаться и требуемая обработка осуществляется независимо от его твердости.
Процесс анодно-механической обработки зависит от электрического режима (плотности тока, напряжения) и механических параметров (давления на обрабатываемую поверхность, скорости движения инструмента). На рис. 6.16 (см. выноску I) показана одна из предполагаемых схем процесса.
В качестве электролита при анодно-механической обработке, так же как и при ЭЭХО, используется водный раствор жидкого натриевого стекла.
Анодно-механическим способом обрабатывают заготовки из всех токопроводящих материалов, высокопрочных и труднообрабатываемых металлов и сплавов, вязких материалов.

124
В станках для анодно-механической обработки используют системы ЧПУ. От программы осуществляется управление скоростями движений заготовки и инструмента, поддерживается постоянство зазора в рабочем пространстве между ними, задаются параметры электрического режима при переходе с черновой обработки на чистовую.
Рис. 6.17. Примеры анодно-механической обработки
Анодно-механическим методом (рис. 6.17) разрезают заготовки на части (а), прорезают пазы и щели, обтачивают поверхности тел вращения (б), шлифуют плоские поверхности и поверхности, имеющие форму тел вращения (в), полируют поверхности, затачивают режущий инструмент.
При электрохимическом шлифовании (см. рис. 6.17, в) инструмен- том-электродом служит шлифовальный круг на электропроводной связке (бакелитовая связка с графитовым наполнителем, металлическая связка). Межэлектродный зазор образован абразивными зернами, выступающими из связки (рис. 6.18). В зазор подается электролит.
Снятие припуска происходит за счет анодного растворения, механического резания абразивными зернами и электроэрозии. Продукты анодного растворения удаляются механически – абразивными зернами. Процесс электроэрозии препятствует засаливанию абразивного круга, вскрывая новые абразивные зерна (происходит непрерывная правка круга). Таким образом, факторы, ограничивающие съем металла при раздельном использовании методов, при использовании комбинированного метода взаимно ослабляются. Резко повышается производительность.
Кроме того, при электрохимическом шлифовании исключаются сколы и трещины в металле заготовки, что особенно важно при обработке хрупких сплавов. Также полностью исключаются прижоги при обработке вязких сталей.
125
Химико-механическая обработка
Метод основан на химическом растворении металла заготовки с последующим его удалением механическим путем.
Химико-механическую обработку чаще всего применяют для разрезания и шлифования пластинок из твердого сплава, доводки твердосплавного инструмента.
Заготовки из твердых сплавов приклеивают специальными клеями к пластинам и опускают в ванну, заполненную суспензией, состоящей из раствора сернокислой меди и абразивного порошка. В результате обменной химической реакции на поверхности заготовок выделяется рыхлая металлическая медь, а кобальтовая связка твердого сплава переходит в раствор в виде соли, освобождая тем самым зерна карбидов титана, вольфрама и тантала.
Медь вместе с карбидами сошлифовывается присутствующим в растворе абразивным порошком. В качестве инструмента используют чугунные диски или пластины. Карбиды удаляются в результате относительных движений инструмента и заготовок.
Ультразвуковая механическая обработка
Ультразвуковая механическая обработка включает операции точения, фрезерования, строгания, протягивания, сверления, зенкерования и нарезания резьб.
Ультразвуковые колебания прикладываются к инструменту в осевом направлении подачи. В зависимости от кинематики движений заготовки относительно режущей кромки они могут быть продольными, крутильными и изгибными. Механизм воздействия ультразвука на процесс обработки заключается в снижении сопротивления обрабатываемого материала пластической деформации в зоне стружкообразования, снижении трения в контактных зонах и облегчении поступления смазочно-охлаждающих веществ.
Как следствие снижения сопротивления обрабатываемого материала пластической деформации, снижается сила резания. Колебания инструмента улучшают подвод смазочно-охлаждающих веществ в контактные зоны и, повышая скорость перемещения относительно обрабатываемой поверхности, снижают коэффициент трения. Результатом этого являются снижение температуры в контактных зонах и исключение образования нароста, снижение пластической деформации обрабатываемой поверхности, ее наклепа и значения остаточных напряжений, улучшение условий схода стружки, повышение износостойкости режущего инструмента.
В качестве оборудования при ультразвуковом механическом резании используются стандартные станки, оснащенные сменными ультразвуковыми головками.
126
Плазменно-механическая обработка
Плазменно-механическая обработка включает локальный нагрев срезаемого слоя заготовки плазменной струей и последующий съем этого слоя режущим инструментом.
Основные затраты энергии при резании идут на пластическую деформацию обрабатываемого металла выше поверхности среза. Установлено, что в зоне стружкообразования в процессе пластической деформации углеродистая сталь нагревается до температур, не превышающих 300 0С. Термический нагрев зоны до 800...1000 0С увеличивает ее пластичность. При этом снижается усилие деформаций – усилие резания – и уменьшается объем металла, вовлеченного в упругопластическую деформацию при резании.
Удаляемый при резании металл нагревают плазменным электрическим разрядом на расстоянии, исключающем разогрев режущего инструмента. Регулированием тока разряда обеспечивается нагрев металла на глубину резания до высоких температур.
Увеличение пластичности материала и снижение его сопротивления деформированию позволяют увеличить производительность процесса резания, при этом в 2...3 раза возрастает стойкость режущего инструмента. При черновом точении плазменный нагрев увеличивает производительность обработки в 4...8 раз.
В качестве оборудования при плазменно-механической обработке применяются стандартные станки, оснащенные плазменной установкой. В качестве плазмообразующего газа используется воздух.
7. ОСНОВЫ ТЕХНОЛОГИИ ПРОИЗВОДСТВА ИЗДЕЛИЙ ИЗ НЕМЕТАЛЛИЧЕСКИХ И КОМПОЗИЦИОННЫХ МАТЕРИАЛОВ
7.1. Общая характеристика неметаллических материалов
Неметаллические материалы находят всё возрастающее применение в различных отраслях техники. Достаточная прочность, жесткость, эластичность при низкой плотности, химическая стойкость во многих агрессивных средах, уровень диэлектрических свойств при их технологичности делают неметаллические материалы незаменимыми.
По происхождению неметаллические материалы различают природные, искусственные и синтетические. К природным, например, относятся такие органические материалы, как натуральный каучук, древесина, смолы (янтарь, канифоль), хлопок, шерсть, лен и др. Неорганические природные материалы включают графит, асбест, слюду и некоторые горные породы. Искусственные органические материалы получают из природных полимерных продуктов (вискозное волокно, целлофан, сложные и простые
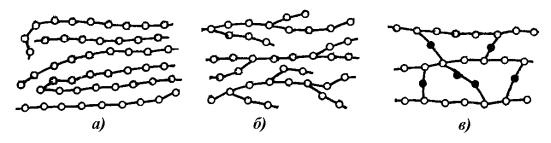
127
эфиры, целлюлозы). Синтетические материалы получают из простых низкомолекулярных соединений.
Именно в искусственных и синтетических материалах возможно проектировать и комбинировать свойства исходных веществ с целью получения заданных свойств конечного продукта и готовых изделий. В результате синтетические неметаллические материалы вытесняют природные и являются наиболее распространенными.
Из неметаллических материалов в машиностроении и приборостроении наиболее широкое применение находят пластмассы и резины – органические материалы на основе полимеров.
Полимерами называют вещества, макромолекулы которых состоят из многочисленных повторяющихся элементарных звеньев, представляющих собой одинаковую группу атомов. Такие макромолекулы обладают значительной молекулярной массой. Макромолекулы полимеров могут иметь линейную форму, разветвленную и пространственную (сшитую).
Линейные макромолекулы (рис. 7.1, а) имеют форму цепей, в которых атомы соединены между собой ковалентными связями. Отдельные цепи связаны межмолекулярными силами, в значительной степени определяющими свойства полимера. Наличие в цепях разветвлений (рис. 7.1, б) приводит к ослаблению межмолекулярных сил и тем самым к снижению температуры размягчения полимера. Пространственные структуры (рис. 7.1, в) получаются в результате химической связи (сшивки) отдельных цепей полимеров либо в результате поликонденсации или полимеризации. Большое значение для свойств «сшитого» полимера имеет частота поперечных связей. Если эти связи располагаются сравнительно редко, то образуется полимер с сетчатой структурой.
Рис. 7.1. Схемы строения молекул полимеров: а – линейная; б – разветвленная; в – пространственная
Полимеры с линейной структурой молекул хорошо растворяются, так как молекулы растворителя могут внедряться в промежутки между макромолекулами и ослаблять межмолекулярные силы. Полимеры с сетчатой структурой нерастворимы, они лишь набухают. При частом расположении связей полимер становится практически нерастворимым и неплавким.
128
Полимеры в зависимости от расположения и взаимосвязи макромолекул могут находиться в аморфном (с неупорядоченным расположением молекул) или кристаллическом (с упорядоченным расположением молекул) состоянии. При переходе полимеров из аморфного состояния в кристаллическое повышаются их прочность и теплостойкость. Значительное влияние на полимеры оказывает воздействие на них теплоты. В зависимости от поведения при повышенных температурах полимеры подразделяют на термопластичные (термопласты) и термореактивные (реактопласты).
Термопласты при нагреве размягчаются и расплавляются, затем вновь затвердевают при охлаждении. Переход термопластов из одного физического состояния в другое может осуществляться неоднократно без изменения химического состава. Термопласты имеют линейную или разветвленную структуру молекул.
Реактопласты при нагреве переходят в вязкотекучее состояние, а затем в результате химической реакции – в твердое, необратимое состояние. Отвержденные реактопласты нельзя повторным нагревом вновь перевести в вязкотекучее состояние. В процессе полимеризации под действием указанных факторов линейная структура полимера превращается в пространственную. Отдельные виды термореактивных смол (эпоксидные, полиэфирные) при введении в них отвердителя отверждаются при нормальной температуре.
Поведение термопластов и реактопластов под действием теплоты имеет решающее значение при технологическом процессе переработки пластмасс.
7.2. Основы технологии производства изделий из пластмасс
Пластмассы – органические материалы на основе полимеров.
В зависимости от числа компонентов все пластмассы подразделяются на простые и композиционные. Простые (полиэтилен, полистирол и т. д.) состоят из одного компонента – синтетической смолы; композиционные (фенопласты, аминопласты и др.) – из нескольких составляющих, каждая из которых выполняет определенную функциональную роль. В композиционных пластмассах смола является связующим для других составляющих. Свойства связующего во многом определяют физико-механические и технологические свойства пластмассы. Содержание связующего в пластмассах достигает 30...70 %.
Помимо связующего в состав композиционных пластмасс входят добавки – наполнители (для повышения механической прочности, теплостойкости и т. д.), пластификаторы (увеличивающие эластичность, текучесть, гибкость), красители, отвердители, катализаторы (ускоряющие про-
129
цесс отверждения) и т. д. При изготовлении газонаполненных пластмасс (поро- и пенопластов) в полимеры вводят газообразователи.
Конструкционные пластмассы в зависимости от показателей механической прочности подразделяют на три основные группы: низкой, средней и высокой прочности.
По поведению при нагревании пластмассы делятся на термопластичные и термореактивные. Термопластичные пластмассы размягчаются при нагревании и затвердевают при охлаждении. Это свойство имеет обратимость.
Термореактивные пластмассы при нагреве необратимо затвердевают в результате химической реакции.
Основными технологическими свойствами пластмасс являются текучесть, усадка, скорость отверждения (реактопластов) и термостабильность (термопластов).
Текучесть – способность материалов заполнять форму при определенных температуре и давлении.
Под усадкой понимают абсолютное или относительное уменьшение размеров детали по сравнению с размером полости пресс-формы.
Скорость отверждения – продолжительность процесса перехода реактопластов из высокоэластичного или вязкотекучего состояния в состояние полной полимеризации.
Под термостабильностью понимают время, в течение которого термопласт выдерживает определенную температуру без разложения.
Высокую термостабильность имеют полиэтилен, полипропилен, полистирол и др. Переработка их в детали сравнительно проста. Для материалов с низкой термостабильностью (полиформальдегид, поливинилхлорид и др.) необходимо предусматривать меры, предотвращающие возможность разложения их в процессе переработки.
В зависимости от физического состояния, технологических свойств и других факторов все способы переработки пластмасс в детали наиболее целесообразно разбить на следующие основные группы:
–переработка в вязкотекучем состоянии (прессованием, литьем под давлением, выдавливанием и др.);
–переработка в высокоэластичном состоянии (пневмо- и вакуумформовкой, штамповкой и др.);
–получение деталей из жидких пластмасс различными способами формообразования;
–переработка в твердом состоянии разделительной штамповкой и обработкой резанием;
–получение неразъемных соединений сваркой, склеиванием и др.;
–различные способы переработки (спекание, напыление и др.). Рассмотрим основные способы переработки.