
1769
.pdf
100
5.5. Суперфиниширование
Это процесс сверхтонкой абразивной обработки наружных и внутренних цилиндрических и конических поверхностей, а также плоскостей колеблющимися брусками.
Суперфинишем в основном уменьшают шероховатость поверхности, оставшуюся от предыдущей обработки. При этом изменяются глубина и вид микронеровностей, обрабатываемые поверхности получают сетчатый рельеф. Поверхность становится чрезвычайно гладкой, что обеспечивает более благоприятные условия взаимодействия трущихся поверхностей.
Поверхности обрабатывают абразивными брусками, устанавливаемыми в специальной головке. Для суперфиниша характерно колебательное движение брусков наряду с движением заготовки. Процесс резания происходит при давлении брусков (0,5...3) 105 Па и в присутствии смазочного материала малой вязкости.
Схема обработки наружной цилиндрической поверхности приведена на рис. 5.12, а. Плотная сетка микронеровностей создается сочетанием трех движений: вращательного Sкр заготовки, возвратно-поступательного Sпр и колебательного брусков со скоростью V. Амплитуда колебаний брусков составляет 1,5...6 мм, а частота 400...1200 колебаний в минуту. Движение V ускоряет процесс съема металла и улучшает однородность поверхности. Бруски, будучи подпружиненными, самоустанавливаются по обрабатываемой поверхности.
Рис. 5.12. Отделка суперфинишированием
Процесс характеризуется сравнительно малыми скоростями резания
(5...7 м/мин).
Важную роль играет смазочно-охлаждающая жидкость. Масляная пленка покрывает обрабатываемую поверхность, но наиболее крупные микровыступы (рис. 5.12, б) прорывают ее и в первую очередь срезаются абразивом. Давление брусков на выступы оказывается большим. По мере дальнейшей обработки давление снижается, так как все большее число вы-
101
ступов прорывает масляную пленку. Наконец, наступает такой момент (рис. 5.12, в), когда давление бруска не может разорвать пленку, она становится сплошной. Создаются условия для жидкостного трения. Процесс отделки автоматически прекращается. В качестве жидкости используют смесь керосина (80...90 %) с веретенным или турбинным маслом
(20...10 %).
При суперфинишировании погрешности формы поверхности, полученные на предшествующей обработке (волнистость, конусность, овальность), не исправляются, хотя могут быть значительно уменьшены.
5.6. Полирование
Полированием уменьшают шероховатость поверхности. Этим методом получают зеркальный блеск на ответственных частях деталей (дорожки качения подшипников) либо на деталях, применяемых для декоративных целей (облицовочные части автомобилей). Для этого используют полировальные пасты или абразивные зерна, смешанные со смазочным материалом. Эти материалы наносят на быстровращающиеся эластичные (например, фетровые) круги или колеблющиеся щетки. Хорошие результаты дает полирование быстродвижущимися бесконечными абразивными лентами (шкурками).
В зоне полирования одновременно протекают следующие основные процессы: а) тонкое резание; б) пластическое деформирование поверхностного слоя; в) химические реакции – воздействие на металл химически активных веществ, находящихся в полировальном материале.
При полировании абразивной шкуркой положительную роль играет подвижность ее режущих зерен. Эта особенность шкурок приводит к тому, что зернами в процессе обработки не могут наноситься микроследы, существенно различные по глубине.
В качестве абразивного материала применяют порошки из электрокорунда и оксиды железа при полировании стали, карбида кремния и оксиды железа при полировании чугуна, оксиды хрома и наждака при полировании алюминия и сплавов меди. Порошок смешивают со смазочным материалом, который состоит из смеси воска, сала, парафина и керосина. Полировальные круги изготовляют из войлока, фетра, кожи, капрона, спрессованной ткани и других материалов.
Процесс полирования проводят на больших скоростях (до 50 м/с). Заготовка поджимается к кругу усилием Р (рис. 5.13, а) и совершает движения подачи Sпр и Sкр в соответствии с профилем обрабатываемой поверхности. Полирование лентами (рис. 5.13, б) имеет ряд преимуществ. Эластичная лента может огибать всю шлифуемую поверхность. Поэтому движения подачи могут отсутствовать.

102
Рис. 5.13. Схемы полирования
Главное движение при полировании иногда совершает и заготовка 3 (рис. 5.13, в), имеющая, например, форму кольца с фасонной внутренней поверхностью. Абразивная лента 1 поджимается полировальником 2 к обрабатываемой поверхности и периодически перемещается (движение Sпр).
Полирование возможно в автоматическом или полуавтоматическом режиме. Заготовки, закрепленные на конвейере, непрерывно перемещаются относительно круга или ленты. Съем деталей происходит на ходу конвейера.
Впроцессе полирования не удается исправлять погрешности формы,
атакже местные дефекты предыдущей обработки.
6.ЭЛЕКТРОФИЗИЧЕСКИЕ И ЭЛЕКТРОХИМИЧЕСКИЕ МЕТОДЫ ОБРАБОТКИ ЗАГОТОВОК ДЕТАЛЕЙ МАШИН
6.1.Общая характеристика электрофизических и электрохимических
методов обработки
В машиностроении часто возникают технологические проблемы, связанные с обработкой материалов и деталей, форму и состояние поверхностного слоя которых трудно получить механическими методами. К таким проблемам относится обработка весьма прочных, очень вязких, хрупких и неметаллических материалов, тонкостенных нежестких деталей, пазов и отверстий, имеющих размеры в несколько микрометров, поверхностей деталей с малой шероховатостью или малой толщиной дефектного поверхностного слоя. Подобные проблемы решаются применением электрофизических и электрохимических (ЭФЭХ) методов обработки.
103
К ЭФЭХ методам размерной обработки материалов относят методы, обеспечивающие съем обрабатываемого материала в результате физико-химических процессов.
Для осуществления размерной обработки заготовок ЭФЭХ методами используют электрическую, химическую, звуковую, световую, лучевую и другие виды энергии.
По механизму разрушения и съема материала все физикохимические процессы обработки могут быть разделены на три группы: электрофизические методы обработки (ЭФО), электрохимические методы обработки (ЭХО) и комбинированные методы. Рассмотрим основные, наиболее применяемые и перспективные методы обработки:
–электроэрозионную;
–электрохимическую;
–химическую;
–лучевые;
–ультразвуковую;
–плазменную;
–а также комбинированные методы.
Каждый из методов ЭФЭХ обладает уникальными технологическими возможностями, но все они более энергоемки и менее производительны в сравнении с методами механической обработки.
Поэтому использование методов ЭФЭХ оправдано только для обработки:
–конструкционных материалов, имеющих низкую обрабатываемость лезвийным и абразивными инструментами, в том числе высоколегированных сталей, твердых сплавов, ферритов, керамики, полупроводников, ситалла и др.;
–деталей сложной геометрической формы из труднообрабатываемых материалов (пресс–формы, детали лопаток турбин и т. п.);
–миниатюрных тонкостенных нежестких деталей, а также деталей сложной формы с пазами и отверстиями.
Эффективность применения методов ЭФЭХ проявляется тем больше, чем сложнее форма обрабатываемой поверхности детали, выше физико-механические свойства материала и чем большие трудности возникают при ее изготовлении методами механической обработки.
ЭФЭХ методы обработки успешно дополняют обработку резанием, а
вотдельных случаях имеют преимущества перед ней. При ЭФЭХ методах обработки силовые нагрузки либо отсутствуют, либо настолько малы, что практически не влияют на суммарную погрешность точности обработки. Методы позволяют не только изменять форму обрабатываемой поверхности заготовки, но и влиять на состояние поверхностного слоя. Так, например, обработанная поверхность не упрочняется, дефектный слой незначителен, удаляются прижоги поверхности, полученные при шлифовании

104
ит. п. При этом повышаются износостойкие, коррозионные, прочностные
идругие эксплуатационные характеристики деталей.
Кинематика формообразования поверхностей деталей ЭФЭХ методами обработки, как правило, проста, что обеспечивает точное регулирование процессов и их автоматизацию.
ЭФЭХ методы обработки универсальны и непрерывны, позволяют выполнять одновременное формообразование всех обрабатываемых поверхностей. На обрабатываемость заготовок ЭФЭХ методами (за исключением ультразвукового и некоторых других) твердость и вязкость обрабатываемого материала практически не влияют. В промышленности широко применяют комбинированные методы обработки, которые дают значительно больший эффект, чем каждый из методов отдельно.
6.2. Электроэрозионная обработка
Электроэрозионными методами обработки материалов называют методы электрофизической обработки, основанные на законах эрозии (разрушения) электродов из токопроводящих материалов при пропускании между ними импульсного электрического тока.
Электроэрозионная обработка металлов (ЭЭО) дополняет обработку резанием, а в отдельных случаях имеет преимущества перед ней:
1)обработка материалов с высокой производительностью независимо от их механических свойств;
2)одновременное формообразование всех обрабатываемых поверх-
ностей;
3)возможность изготовления деталей сложных форм (штампы, пресс-формы), недоступных другими методами обработки;
4)малоотходное разделение заготовок по любым траекториям слож-
Рис. 6.1. Схема электроэрозионной обработки: 1 – электрод-инструмент; 2 – заго- товка-электрод; 3 – ванна; 4 – диэлектрическая жидкость; 5 – изолятор
ного профиля;
5)силовые нагрузки практически отсутствуют;
6)улучшается состояние поверхностного слоя заготовки;
7)простота автоматизации процессов обработки.
Область применения ЭЭО.
Обработка материалов повышенной прочности, повышенной вязкости, хрупких, труднообрабатываемых материалов (твердые сплавы, закаленная сталь, вольфрам, молибден и др.); обработка
105
тонкостенных нежестких деталей, пазов и отверстий малого и сверхмалого размеров (до 1–6 м); получение поверхностей с малой шероховатостью и малой толщиной дефектного поверхностного слоя.
Сущность методов ЭЭО
Между электродом-заготовкой 2 (рис. 6.1) и электродоминструментом 1 генератором импульсов 6 создается разность потенциалов (от источника питания постоянного, пульсирующего постоянного или переменного тока различных частот).
Разность напряжений периодически приводит к образованию в среде между электродами временного канала проводимости (импульсный искровой или дуговой разряд продолжительностью 10–2...10–8 с). Высокая концентрация энергии, плотность тока (до 10000 А/мм2) приводят к возрастанию температуры на поверхности электрода-заготовки до 4000...12000 0С, в результате чего элементарный объем металла заготовки мгновенно оплавляется и испаряется. На поверхности образуется лунка. Удаленный металл застывает в диэлектрической жидкости 4 в виде гранул диаметром менее 0,01 мм. Определенному напряжению на электродах соответствует определенное расстояние электрического пробоя dп (0,01...0,05 мм).
Сечение прошиваемого отверстия может быть фасонным.
Процесс образования импульсных разрядов продолжается до полного удаления металла заготовки в пределах расстояния пробоя от поверхности электрода-инструмента. Для продолжения процесса необходимо сблизить электроды до расстояния рабочего зазора dр при условии dр<dп. Сближение выполняется непрерывно автоматически с помощью следящих систем, в результате чего электрод-инструмент поступательно перемещается к заготовке с постоянной скоростью Vи.
При ЭЭО используют два способа включения электродов: прямую полярность (отрицательно заряженный катод – инструмент) и обратную полярность (катод – заготовка). В процессе обработки происходит сглаживание поверхности заготовки за счет удаления микровыступов, поскольку каналы проводимости возникают по наименьшему расстоянию между электродами.
Межэлектродный промежуток заполнен диэлектриком 4 (это может быть вакуум, газ, жидкость, порошок или флюс). Наиболее часто применяется жидкость, т. к. в жидкой среде процесс эрозии происходит интенсивнее. Кроме того, жидкость уменьшает нагрев электродов (инструмента и заготовки), охлаждает продукты разрушения, уменьшает величину боковых разрядов между инструментом и заготовкой, что повышает точность обработки. Процесс обработки при этом осуществляется в ванне 3 (см. рис. 6.1). Возможна принудительная циркуляция жидкости между электродами для более полного удаления продуктов разрушения и охлаждения электродов.

106
Применяемые диэлектрические жидкости: керосин, дизельное топливо, минеральные масла, вода, водные растворы и эмульсии.
Рис. 6.2. Схемы ряда основных операций ЭЭО: а – прошивание отверстия; б – обработка фасонной полости штампа; в – прошивание отверстия по способу трепанации; г – прошивание отверстия с криволинейной осью; д – вырезание заготовки из листа; е – шлифование внутренней поверхности фильеры
Методом ЭЭО (рис. 6.2) получают сквозные отверстия любой формы поперечного сечения (а), глухие отверстия и полости (б), фасонные отверстия и полости по способу трепанации (в), отверстия с криволинейными осями (г); вырезают заготовки из листа при использовании проволочного или ленточного инструмента-электрода (д), выполняют плоское, круглое и внутреннее (е) шлифование, разрезают заготовки, клеймят детали.
ЭЭО применяют для изготовления штампов, пресс-форм, фильер, режущего инструмента, деталей топливной аппаратуры двигателей внутреннего сгорания, сеток и сит.
Методом ЭЭО обрабатывают практически все токопроводящие материалы, но эффект эрозии при одних и тех же параметрах электрических импульсов различен. Он определяется временем нагрева поверхности заготовки до температуры плавления. Зависимость интенсивности эрозии от свойств металлов называют электроэрозионной обрабатываемостью. Если
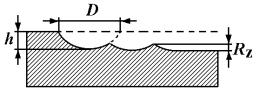
107
принять электроэрозионную обрабатываемость стали за единицу, то для других металлов ее можно представить в следующих относительных единицах: твердые сплавы – 0,5; титан – 0,6; никель – 0,8; медь – 1,1; латунь – 1,6; алюминий – 4; магний – 6.
Электроискровым методом целесообразно обрабатывать твердые сплавы, труднообрабатываемые металлы и сплавы, тантал, молибден и другие материалы.
Факторы, вызывающие эрозию металла при ЭЭО: а) тепловое воздействие разрядов; б) электростатические и электродинамические силы; в) газообразование в результате распада жидкой рабочей среды; г) кавитационный удар жидкости.
Производительность ЭЭО характеризуется количеством снятого металла в единицу времени (мм3/мин), (г/мин) и зависит от обрабатываемости материала заготовки, вида рабочей среды, энергии импульса, частоты действия импульсов.
В результате единичного искрового разряда на обрабатываемой поверхности образуется углубление диаметром D и глубиной h (рис. 6.3). Размеры углубления пропорциональны энергии импульса W:
D=k1W(1/3); h= k2W(1/3),
где k1, k2 – коэффициенты, зависящие от материала электродов и состава межэлектродной среды.
При воздействии на металл серии импульсов обрабатываемая поверхность формируется в результате перекрытия отдельных лунок. Высота микронеровностей Rz будет равна
Rz=(1/3) h=(k2/3) W(1/3).
Отсюда можно выразить соот-
ношение энергии импульса W и показателя шероховатости обработанной поверхности Rz:
W=(27/k23) Rz3.
Обработанная поверхность представляет собой поверхность, образованную перекрытием множества лунок глубиной h и диаметром D (см. рис. 6.3). Исходя из требуемой шероховатости поверхности детали после обработки, могут быть выбраны показатели процесса ЭЭО, прежде всего мощность импульсов W.
Различают следующие методы ЭЭО: а) электроискровую обработку
(ЭИсО); б) электроимпульсную обработку (ЭИмО); в) электроконтактную обработку (ЭКО).
108
Первые два метода – бесконтактные. Они отличаются друг от друга параметрами электрических разрядов, прежде всего их мощностью и продолжительностью.
Сравнительные характеристики бесконтактных методов ЭЭО
Характеристика метода |
Метод ЭЭО |
||
ЭИсО |
ЭИмО |
||
|
|||
Вид разряда |
Импульсный |
Импульсный |
|
|
искровой |
дуговой |
|
Полярность |
Прямая |
Обратная |
|
Длительность импульса, с |
10-4...10-7 |
10-2...10-4 |
|
Частота следования импульсов, кГц |
0,1...100 |
0,15...3 |
|
Напряжение источника питания max, В |
300 |
30 |
|
Сила тока источника питания max, А |
125 |
500 |
|
Температура канала разряда, 0С |
10000...12000 |
4000...5000 |
|
Производительность max, мм3/мин |
1900 |
15000 |
|
Шероховатость обработанной поверхности Ra, мкм |
0,6...5 |
5...20 |
Мощность импульсов при ЭИмО больше, чем при ЭИсО. Это обеспечивает методу ЭИмО более высокую производительность при более низком качестве поверхности. Поэтому целесообразно применение комбинированной ЭЭО, когда черновая обработка ведется методом ЭИмО, затем чистовая – методом ЭИсО. Сравнительные характеристики бесконтактных методов ЭЭО даны в таблице.
Метод электроконтактной обработки (ЭКО)
Метод ЭКО основан на локальном нагреве заготовки в месте контакта с электродом-инструментом за счет подвода тока большой плотности. Размягченный или расплавленный металл заготовки удаляется из зоны обработки механически движением инструмента. Обработка возможна со значительным давлением инструмента на заготовку или без давления в режиме электрического оплавления.
Размягчение, расплавление и частичное испарение металла происходят за счет нагрева контактных перемычек между электродами, а также за счет дуговых разрядов между ними. Контактные перемычки образуются сначала в твердой фазе материала заготовки, а затем в жидкой фазе. Возможно также кратковременное замыкание электродов диспергированными частицами металла. Разряды возникают в результате размыкания (электрического взрыва) контактных перемычек или вследствие непосредственного пробоя промежутка между электродами по аналогии с бесконтактными методами ЭЭО. Размыкание контактных перемычек происходит при разрыве контактов между электродами за счет их относительного движения, сопровождается скачком напряжения и возникновением дугового разряда.
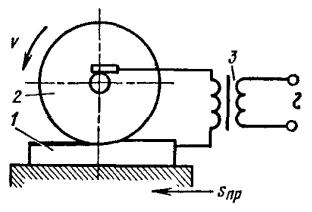
109
Преимущества ЭКО по сравнению с бесконтактными методами
ЭЭО:
–высокая производительность;
–не требуются жидкие рабочие среды;
–не требуется источник постоянного тока;
–малый износ режущего инструмента;
–безопасное для работы напряжение на электродах.
Недостатки ЭКО по срав-
нению с бесконтактными мето- |
|
|
дами ЭЭО: низкая точность; не- |
|
|
высокое качество поверхности. |
|
|
ЭКО применяют при зачи- |
|
|
стке отливок от заливов, отрезке |
|
|
литниковых систем и прибылей, |
|
|
зачистке проката из спецсплавов, |
|
|
черновом круглом |
наружном, |
|
внутреннем и плоском шлифова- |
|
|
нии корпусных деталей машин из |
Рис. 6.4. Схема электроконтактной |
|
труднообрабатываемых |
сплавов |
обработки плоской поверхности: |
(рис. 6.4). |
|
1 – обрабатываемая заготовка; 2 – инстру- |
Пример применения ЭЭО |
мент-электрод; 3 – трансформатор |
(ЭИсО): прошивка отверстия диаметром 0,15 мм в распылителях дизельных форсунок на станках ЛКЗ - 34, ЛКЗ - 59 с затратой времени от 15 до 35 с на одно отверстие.
6.3. Электрохимическая обработка
Электрохимическая обработка металлов (ЭХО) основана на явлении анодного растворения металла, осуществляемого при прохождении постоянного тока через электролит между электродом-инструментом и электродом-заготовкой.
Инструмент 1 при ЭХО является отрицательно заряженным катодом, заготовка 2 – положительно заряженным анодом (рис. 6.5).
На рис. 6.5 показаны схемы обработки заготовок в струе проточного электролита: турбинной лопатки (а), штампа (б) и схема прошивания сквозного цилиндрического отверстия (в).
Сущность метода ЭХО
Под действием электрического тока от источника питания атомы поверхностного слоя металла заготовки вступают в химическое соединение с анионами (отрицательно заряженными ионами) электролита, переходят в раствор и удаляются потоком электролита.