
1769
.pdf20
При изготовлении чугунных отливок для уменьшения пригара в формовочные смеси добавляют каменноугольную пыль. Расплавленный чугун подводят в тонкие сечения отливок. При изготовлении отливок из высокопрочного и ковкого чугунов для предупреждения усадочных раковин устанавливают прибыли или питающие бобышки. Для предупреждения трещин в отливках используют формовочную смесь повышенной податливости.
Для отливок из цветных сплавов формовочные и стержневые смеси приготовляют из мелкозернистых кварцевых песков. Формовочная смесь должна обладать повышенной податливостью для предупреждения в отливках трещин. При изготовлении магниевых отливок в формовочную смесь вводят фтористые добавки во избежание самовозгорания магния. Расплавленный металл в форму подводят через литниковую систему с увеличенным поперечным сечением питателей, что обеспечивает плавное заполнение полости формы. Для предупреждения усадочных раковин устанавливают прибыли и холодильники.
2. ОСНОВЫ ОБРАБОТКИ МЕТАЛЛОВ ДАВЛЕНИЕМ
2.1. Сущность процессов обработки металлов давлением
Обработкой давлением называют процессы получения заготовок или деталей машин силовым воздействием инструмента на исходную заготовку из пластичного материала без снятия стружки.
Обработка металлов давлением (ОМД) основана на их способности в определенных условиях пластически деформироваться в результате воздействия на деформируемое тело (заготовку) внешних сил. Пластическое деформирование при ОМД, состоящее в преобразовании заготовки простой формы в деталь более сложной формы того же объема, относится к малоотходной технологии.
Существенные преимущества ОМД по сравнению с обработкой резанием – возможность значительного уменьшения отхода металла, а также повышения производительности труда, поскольку в результате однократного приложения усилия можно значительно изменить форму и размеры деформируемой заготовки. Кроме того, пластическая деформация сопровождается изменением физико-механических свойств металла заготовки, что можно использовать для получения деталей с наилучшими эксплуатационными свойствами (прочностью, жесткостью, высокой износостойкостью и т. д.) при наименьшей их массе. Эти и другие преимущества ОМД способствуют неуклонному росту ее удельного веса в металлообработке.

21
О широком применении процессов ОМД свидетельствуют следующие данные: до 90 % всей выплавляемой стали и около 55 % выплавляемых цветных металлов и сплавов подвергаются обработке давлением.
Основные способы ОМД: прокатка, прессование, волочение, ковка (свободная ковка), штамповка: – объемная; – листовая,
Все пять перечисленных способов ОМД можно разделить на две группы:
1.Способы, при которых конечная продукция – это машиностроительные профили большой (в ряде случаев – неограниченной) длины, которые в дальнейшем подвергаются разделению на части. Способы ОМД,
относящиеся к данной группе, – прокатка, прессование, волочение.
2.Способы, при которых конечная продукция – это машиностроительные заготовки, приближенные по форме к готовым изделиям (в ряде случаев – готовые детали, не требующие дальнейшей обработки). Способы ОМД, относящиеся к данной группе, – ковка и штамповка.
Различают 2 вида процессов ОМД: холодную ОМД; горячую ОМД. Холодная деформация характеризуется изменением формы зерен, ко-
торые вытягиваются в направлении наиболее интенсивного течения металла (рис. 2.1, а). При холодной деформации формоизменение сопровождается изменением механических и физико-химических свойств металла. Это явление называют упрочнением (наклепом).
Горячей деформацией на-
зывают деформацию, характеризующуюся таким соотношением скоростей деформирования и рекристаллизации, при котором рекристаллизация успевает произойти во всем объеме заготовки
имикроструктура после обработ-
ки давлением оказывается равно- |
|
||
осной, без |
следов упрочнения |
|
|
(рис. 2.1, б). |
|
|
|
Чтобы обеспечить условия Рис. 2.1. Схемы изменения микроструктуры |
|||
протекания горячей деформации, |
металла при деформации: |
||
а – холодной; б – горячей |
|||
приходится |
с увеличением ее |
||
|
скорости повышать температуру нагрева заготовки (для увеличения скорости рекристаллизации).
Цели нагрева заготовок при ОМД:
Повышение пластичности деформируемого металла.
Снижение деформирующих усилий.
Предотвращение наклепа.

22
Наклеп – явление повышения твердости и предела прочности деформируемого материала при одновременном снижении его пластичности.
Наклеп может быть устранен последующей термообработкой (отжи-
гом).
При горячей деформации сопротивление деформированию примерно в 10 раз меньше, чем при холодной деформации, а отсутствие упрочнения приводит к тому, что сопротивление деформированию (предел текучести) незначительно изменяется в процессе обработки давлением. Этим обстоятельством объясняется в основном то, что горячую обработку применяют для изготовления крупных деталей, так как при этом требуются меньшие усилия деформирования (менее мощное оборудование).
2.2. Прокатка
Прокатка – технологический процесс пластической деформации заготовок между вращающимися валками путем захвата заготовок за счет сил трения.
Взаимное расположение валков и заготовки, форма и число валков могут быть различными. Выделяют три основных вида прокатки: продольную, поперечную и поперечно-винтовую.
При продольной прокатке (рис. 2.2, а) заготовка 2 деформируется между двумя валками 1, вращающимися в разные стороны, и перемещается перпендикулярно к осям валков.
При поперечной прокатке (рис. 2.2, б) валки 1, вращаясь в одном направлении, придают вращение заготовке 2 и деформируют ее.
При поперечно-винтовой прокатке (рис. 2.2, в) валки 1 расположены под углом и сообщают заготовке 2 при деформировании вращательное и поступательное движения.
Рис. 2.2. Основные виды прокатки: 1 – валки; 2 – заготовка; 3 – оправка

23
В процессе прокатки металл непрерывно втягивается в зазор между валками под действием сил трения между металлом и валками. Для осуществления процесса прокатки необходима определенная величина этих сил трения. Так, при наиболее распространенной продольной прокатке на заготовку со стороны валков действуют нормальные силы N и сила трения Т (рис. 2.3). Спроектировав эти силы на горизонтальную ось, можно записать условие захвата металла валками (по отношению к одному валку, так как система симметрична):
N sin( ) < Т cos( ).
Угол называется углом захвата. Выразив силу трения как Т= f N, где f – коэффициент трения, и подставив это выражение в условие захвата, получим
sin( ) < f cos( ) или f > tg( ).
Таким образом, для осуществле- |
|
|
ния захвата металла валками необхо- |
|
|
димо, чтобы коэффициент трения |
|
|
между валками и заготовкой был |
|
|
больше тангенса угла захвата. |
|
|
При горячей прокатке стали |
|
|
гладкими валками угол захвата равен |
Рис. 2.3. Схема действия сил |
|
15...24 0, при холодной 3...8 0. При ус- |
||
в момент захвата металла валками |
тановившемся процессе прокатки коэффициент трения может быть примерно вдвое меньше.
В процессе прокатки уменьшается толщина заготовки при одновременном увеличении ее длины и ширины. Деформацию заготовки обычно определяют относительным обжатием, %:
н=(H0 – H1)100/ H0,
где H0 и H1 – высота заготовки соответственно до и после прокатки. Площадь поперечного сечения заготовки всегда уменьшается. По-
этому для определения деформации (особенно, когда обжатие по сечению различно) используют показатель, называемый вытяжкой,
=l / l0=F0/F,
где l0 и F0 – первоначальные длина и площадь поперечного сечения; l и F – те же величины после прокатки.
Вытяжка при прокатке обычно составляет 1,1...1,6 за проход, но может быть и больше.
Инструмент и оборудование для прокатки
Инструментом для прокатки являются валки, которые в зависимости от прокатываемого профиля могут быть гладкими (рис. 2.4, а), применяе-

24
мыми для прокатки листов, лент и т. п., ступенчатыми, например для прокатки полосовой стали, и ручьевыми (рис. 2.4, б) для получения сортового проката. Ручьем называют вырез на боковой поверхности валка, а совокупность двух ручьев образует калибр (рис. 2.4, в). Каждая пара ручьевых валков обычно составляет несколько калибров.
Рис. 2.4. Инструмент для прокатки
Валки состоят из рабочей части – бочки 1, шеек 2 и трефы 3. Шейки валков вращаются в подшипниках. Комплект прокатных валков со станиной называют рабочей клетью.
Рабочие клети по числу и расположению валков могут быть двухвалковые (см. рис. 2.2, а); четырехвалковые (рис. 2.5, а), у которых два валка рабочих и два опорных; многовалковые (рис. 2.5, б), у которых также два валка рабочих, а остальные – опорные. Использование опорных валков позволяет
применять рабочие валки малого диаметра, благодаря чему увеличивается вытяжка и снижается усилие деформирования.
Прокатные станы могут быть одноклетьевыми (с одной рабочей клетью) и многоклетьевыми. Наиболее совершенные многоклетьевые станы – непрерывные, у которых рабочие клети располагают последовательно одну за другой. Прокатываемая полоса через каждую клеть проходит только один раз, т. е. число рабочих
клетей этих станов равно требуемому числу проходов полосы. На непрерывных станах достигается высокая производительность при полном исключении ручного труда.

25
Область применения прокатных станов – получение проката из сталей и цветных сплавов.
Продукция прокатного производства
1. Сортовой прокат: а) простой геометрической формы: круг, квадрат, прямоугольник, шестигранник (рис. 2.6); б) фасонный прокат сложной формы: угольник,тавр, двутавр, швеллер, рельс (рис. 2.7).
Рис. 2.7. Фасонный прокат сложной формы
Рис. 2.8. Последовательность процесса свертывания полосы в трубу в шести клетях непрерывного стана
Рис. 2.9. Схема прокатки шаров в стане поперечно-винтовой прокатки
Рис. 2.10. Профили с изменяющейся формой и площадью поперечного сечения
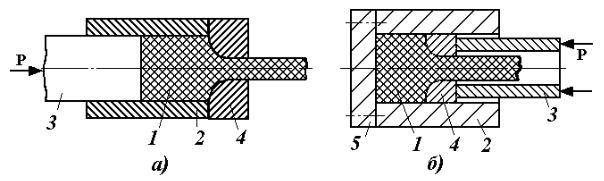
26
2.Листовой прокат.
3.Трубы: бесшовные (см. рис. 2.2, в), сварные (рис. 2.8).
4.Специальные виды проката: колеса, кольца, шары (рис. 2.9), периодические профили с периодически изменяющейся формой и площадью поперечного сечения вдоль оси заготовки (рис. 2.10).
2.3. Прессование
Прессование – это процесс выдавливания заготовок из замкнутого объема контейнера через отверстие в матрице с площадью меньшей, чем поперечное сечение исходной заготовки.
Рис. 2.11. Схемы прессования прямого (а) и обратного (б):
1 – заготовка; 2 – контейнер; 3 – пуансон; 4 – матрица; 5 – держатель
Прессование может выполняться двумя методами – прямым и обратным (рис. 2.11). При прямом методе (см. рис. 2.11, а) заготовку 1 помещают в полость контейнера 2 и с помощью мощного пресса пуансоном 3 выдавливают через отверстие в матрице 4.
При обратном прессовании (см. рис. 2.11, б) давление пресса передается через полый пуансон 3 с смонтированной внутри его матрицей 4. Таким образом, металл заготовки 1 течет навстречу движению пуансона.
При обратном прессовании усилие на 25...30 % меньше, чем при прямом, так как в последнем случае часть усилия затрачивается на преодоление трения при перемещении металла заготовки внутри матрицы. Прессостаток (остающаяся в контейнере часть металла заготовки) при обратном прессовании также меньше, чем при прямом. Однако сложность конструкции пресса, ограниченность длины изделия препятствуют широкому применению способа обратного прессования.
Исходной заготовкой при прессовании служит слиток или прокат.
Достоинства процесса прессования (особенности):
1. Реализуется одна из самых благоприятных схем нагружения, обеспечивающая максимальную пластичность – всестороннее неравномерное сжатие. Это позволяет обрабатывать даже малопластичные материалы.

27
Деформируемый металл подвергается всестороннему сжатию и поэтому обладает высокой пластичностью. Благодаря этому здесь возможна высокая степень деформации: Fзаг/Fпресс. изд. = (10...50)/1. И это является главным достоинством процесса.
2. Возможность получения профилей сложной формы, что зачастую невозможно при других способах обработки пластической деформацией, в том числе и пустотелых (рис. 2.12).
Рис. 2.12. Схема прессования полого профиля (а) и примеры прессованных профилей (б)
При прессовании полых профилей (см. рис. 2.12, а) при движении пуансона 1 с пресс-шайбой 5 металл заготовки 2 выдавливается в зазор между матрицей 3 и иглой 4.
Недостатки процесса:
1.Большие отходы металла: весь металл не может быть выдавлен из контейнера и в нем остается так называемый пресс-остаток, который после окончания прессования отрезается от полученного профиля. Масса прессостатка может достигать 40 % массы исходной заготовки (при прессовании труб большого диаметра).
2.Сильный износ инструмента за счет трения. Для уменьшения трения применяют смазку – графит или жидкое стекло.
Область применения прессования. Прессованием изготовляют изде-
лия разнообразного сортамента из цветных металлов и сплавов, в том числе прутки диаметром 3...250 мм, трубы диаметром 20...400 мм со стенкой толщиной 1,5...12 мм и другие профили (рис. 2.12, б). Из углеродистых сталей 20, 35, 45, 50, конструкционных ЗОХГСА, 40ХН, коррозионностойких 12Х18Н10Т и других высоколегированных сталей прессуют трубы
свнутренним диаметром 30...160 мм со стенкой толщиной 2...10 мм.

28
2.4. Волочение
Волочение – технологический процесс протягивания заготовки (прутка) через отверстие инструмента, сечение которого меньше исходного сечения деформируемой заготовки.
Инструмент называется волокой.
Рабочая часть инструмента имеет несколько зон (рис. 2.13): I – входная зона; II – деформирующая зона (угол при вершине конуса =8...24 0). Коэффициент трения должен быть меньше 0,1...0,12; III – цилиндрический калибрующий поясок; IV – выходной конус (угол около 45 0).
Рис. 2.13. Рабочая часть волоки
Рис. 2.14. Схема волочения трубы
Волочение, как правило, осуществляется в холодном состоянии. Волочение труб можно выполнять без оправки (для уменьшения внешнего диаметра) и с оправкой (для уменьшения внешнего диаметра и толщины стенки). На рис. 2.14, показана схема волочения трубы 1 на короткой удерживаемой оправке 3. В этом случае профиль полученной трубы определяется зазором между волокой 2 и оправкой 3.
При волочении сплошного и полого профилей площадь поперечного сечения заготовки уменьшается, а следовательно, длина (из условия посто-
29
янства объема при пластической деформации) увеличивается. Количественно деформацию, так же как и при прокатке, можно характеризовать отношением полученной длины к исходной, т. е. вытяжкой .
Вследствие того, что к заготовке при волочении приложено тянущее усилие, в отверстии волоки (очаге деформации) и после выхода из нее металл испытывает растягивающие напряжения. Но если в очаге деформации, в котором действуют и сжимающие напряжения со стороны инструмента, металл пластически деформируется, то на выходящем из волоки конце прутка пластическая деформация недопустима. В противном случае пруток искажается или разрывается. Поэтому величина деформации за один проход ограничена, и вытяжка обычно равна =1,25...1,45.
Основное условие волочения: напряжение растяжения, возникающее в выходящем из волочильной доски конце прутка, должно быть меньше предела упругости материала заготовки:
упр > (P/F),
где упр – предел упругости материала заготовки; P – усилие волочения; F – площадь сечения профиля при выходе из волоки.
В случае несоблюдения этого условия возникающие напряжения могут привести к местному течению металла и изменению сечения заготовки.
Поскольку тянущее усилие, приложенное к заготовке, необходимо не только для деформирования металла, но и для преодоления сил трения металла об инструмент, эти силы трения стараются уменьшить применением смазки и полированием отверстия в волоке.
Применяемые смазки:
–твердые (мыльный порошок, парафин, воск);
–консистентные (тавот, солидол);
–жидкие (водные эмульсии минеральных масел и мыла).
Достоинства метода:
–высокая точность (до 7 квалитета, что соответствует точности при обработке резанием);
–очень гладкая поверхность изделия с малой шероховатостью;
–высокая прочность изделия (в холодном состоянии металл упрочняется).
Недостатки метода:
1.Невысокая производительность (т. к. степень деформации за одну протяжку не может быть велика).
2.При холодном волочении возникает наклеп – приходится проводить промежуточный отжиг (обычно для получения необходимых профилей требуется деформация, превышающая допустимую за один проход, поэтому применяют волочение через ряд постепенно уменьшающихся по диаметру отверстий. Но поскольку волочение осуществляют в условиях холодной деформации, металл упрочняется. Для восстановления пластич-