
1769
.pdf
110
Под действием внешней электродвижущей силы слабосвязанные электроны из атомов поверхностного слоя уходят во внешнюю электрическую цепь, разрывая связь этих атомов с массой металла. Положительно ионизированные атомы металла вступают в реакцию с анионами электролита, образуя соединения, которые или растворяются в электролите, или создают на поверхности заготовки пленку, удаляемую механически.
Рис. 6.5. Схемы электрохимической размерной обработки: 1 – инструмент-электрод; 2 – заготовка; 3 – изолятор
Участки заготовки, не требующие обработки, изолируют. В качестве электролита используется чаще всего водный раствор поваренной соли NaCl, который имеет малую стоимость и длительную работоспособность. Кроме того, используют водные растворы азотнокислого и сернокислого натрия, серной и фосфорной кислот. Электролит применяется многократно после очистки в фильтрах. Заготовку погружают в ванну с электролитом либо электролит подают в зону обработки через сопло.
В состав электролита вводят специальные добавки, снижающие его вязкость (инертные газы, воздух), коррозионную активность, поверхност- но-активные вещества (для лучшей очистки обрабатываемой поверхности заготовки и самого электролита в фильтрах).
Преимущества ЭХО перед традиционными методами обработки металлов резанием:
1)Совершенно отсутствует износ электрода-инструмента (т. к. фактически при ЭХО инструментом является раствор электролита).
2)Возможность формообразования сложнофасонных поверхностей при поступательном перемещении электрода-инструмента (рис. 6.6).
Рис. 6.6. Схема последовательного (а, б, в) формообразования поверхности заготовок: 1 – электрод-инструмент; 2 – электрод-заготовка
111
3)Обработка материалов с высокой производительностью независимо от их физико-механических свойств.
4)Отсутствие не только силового, но и температурного воздействия на заготовку в зоне обработки.
5)Уменьшение шероховатости обработанной поверхности и глубины дефектного слоя.
6)Простота автоматизации процессов обработки.
Недостатки ЭХО:
–высокая стоимость и сложность изготовления оборудования;
–обязательно использование раствора электролита;
–высокая энергоемкость обработки.
Область применения ЭХО. Обработка материалов повышенной прочности и вязкости, хрупких, труднообрабатываемых материалов; обработка тонкостенных нежестких деталей; удаление заусенцев, притупление острых кромок; затачивание и доводка поверхностей режущего инструмента; получение поверхностей с малой шероховатостью и малой толщиной дефектного поверхностного слоя; декоративная отделка деталей.
Показателем электрохимической обрабатываемости металла является электрохимический эквивалент k. Металлы с различными механическими свойствами могут иметь близкие значения k.
Для сравнения: железо k=2,2; никель, кобальт k=2,05; хром k=2,24; алюминий k=2,1; медь k=2,2; молибден k=1,95.
Электрохимический эквивалент k определяет объем растворившегося металла при прохождении через электролит определенного количества электричества. Чем больше k, тем выше обрабатываемость. Затруднена обработка методом ЭХО сплавов с большим содержанием углерода C, кремния Si, а также титановых сплавов.
Производительность ЭХО определяется количеством вещества G, растворенного под действием тока. Согласно закону Фарадея оно прямо пропорционально количеству электричества, прошедшего через раствор
электролита. Для ЭХО будут справедливы следующие зависимости: G=k I ; tм=h/vл; vл= kv ia 10-2,
где k, kv – соответственно массовый, г/(А ч) и объемный, мм3/(А мин) электрохимический эквивалент обрабатываемого материала; I – сила тока, А;
– время обработки, ч; h – снимаемый припуск, мм; vл – линейная скорость растворения металла, мм/мин; ia – анодная плотность тока, А/см2; tм – машинное время, мин.
Максимальная производительность станков ЭХО теоретически может достигать 2000 мм3/мин.
Повышение производительности ЭХО за счет увеличения плотности тока ограничено, т. к. соли растворенного металла заготовки при больших плотностях тока не успевают растворяться в электролите и образуют по-
112
верхностную пленку, которая обладает значительным электрическим сопротивлением.
Увеличение плотности тока возможно за счет увеличения скорости движения электролита (продукты анодного растворения, обладающие значительным омическим сопротивлением, быстрее уносятся из рабочего зазора) и за счет уменьшения зазора между электродами. Однако, в свою очередь, уменьшение зазора ограничивается двумя причинами: 1) снижается скорость движения электролита, а также нарушается равномерность его подачи; 2) при очень малых зазорах происходит замыкание электродов и возникновение между ними дуговых разрядов.
Инструмент при ЭХО имеет форму, обратную форме обрабатываемой поверхности. Скорость растворения металла пропорциональна плотности тока, которая будет больше там, где меньше зазор. При проектировании катода-инструмента необходимо корректировать его форму с учетом технологических особенностей метода ЭХО. Например, если необходимо получить плоскую поверхность, используют электрод-инструмент со слегка выпуклым профилем, так как металл быстрее удаляется с краев заготовки. При изготовлении цилиндрических отверстий надо предусматривать корректировку возникающей конусности и т. д.
Интенсивное растворение металла заготовки и достаточно точное копирование профиля катода на аноде возможны только при достаточно малых расстояниях между электродами (порядка 0,2...0,5 мм). Копирование профиля катода происходит вследствие перераспределения плотности тока. Для получения больших плотностей тока в качестве источников питания используют агрегаты, дающие напряжение 5...30 В, при величине силы тока 10000 А и выше.
Точность получаемых размеров для обработки методом ЭХО – до
20 мкм.
Точность ЭХО снижается вследствие погрешности изготовления катода, погрешности установки заготовки, непостоянной плотности тока, непостоянства температуры и скорости движения электролита, неравномерности движения электродов.
6.4. Химическая обработка
Химическая обработка заключается в направленном и контролируемом разрушении металлов и сплавов травлением их в растворах кислот и щелочей.
Снятие слоя припуска (рис. 6.7) осуществляется за счет химического взаимодействия материала обрабатываемой заготовки 1 с кислотным или щелочным составом 2 травильных ванн 3. Поверхность детали предварительно очищается, необрабатываемые участки детали защищают химиче-

113
ски стойким покрытием. Детали устанавливаются на подпорках 4 или подвешиваются в корзинах. Травильный раствор циркулирует через ванну и блок регенерации 5, очищающий его от шлама и восстанавливающий концентрацию раствора.
Преимущества химических методов перед обработкой на металлорежущих станках:
1)Отсутствие механических и тепловых явлений в зоне съема металла позволяет обрабатывать детали любой жесткости и конфигурации.
2)Возможность обработки поч-
ти всех материалов в любом состоянии независимо от их механических свойств.
3) Достаточно высокая производительность вследствие протекания реакции одновременно по всей обрабатываемой поверхности.
4) Возможность съема металла Рис. 6.7. Схема химической обработки
на тех участках детали, где использовать другие методы обработки неэффективно или невозможно.
5)Сравнительно высокая точность обработки (до 0,05 мм против0,25 мм при механическом фрезеровании).
6)Возможность получения деталей переменной толщины, конической формы, ступенчатой формы травлением различных участков в течение различного времени (эшелонированное травление с последовательным удалением защитного покрытия поверхности).
7)Обработка магнитных материалов без снижения их магнитных
свойств.
8)Одновременная обработка большого числа деталей.
9)Простота промышленного внедрения и автоматизации, невысокая стоимость оборудования.
Недостатки химических методов:
Продолжительность процесса подготовки деталей под травление, большой расход материалов покрытий и растворителей покрытий (необходимость нанесения нескольких слоев защитных покрытий до обработки и снятия их после обработки. Путь решения этой проблемы– применение покрытий, которые можно использовать многократно).
Сравнительная продолжительность травления, особенно при удалении значительных толщин металла.
Снижение класса шероховатости поверхности.
Ограниченность обработки отверстий, невозможность получения узких, глубоких пазов вследствие плохой циркуляции раствора и подтравливания защитного покрытия.

114
Процесс химического травления можно разделить на три периода: 1. Растворение окисной пленки (окалины) на поверхности металла. В качестве примера на рис. 6.8 приводится строение поверхностного
слоя стали.
|
- Fe2O3 |
– «Гематит» (10 %) |
Окалина |
|
|
100 % |
- Fe3O4 |
– «Магнетит» (40 %) |
(толщи- |
|
|
на S – |
- FeO – «Вюстит» (50 %) |
|
доли |
||
мм) |
|
|
|
Fe – основной металл |
|
|
Рис. 6.8. Строение поверхностного слоя стали |
Окалина обладает значительно большей химической стойкостью, чем основной металл. Процесс протекает очень медленно, поэтому на данном этапе используют специальный, химически более активный раствор.
2.Основной период установившегося процесса растворения металла. Скорость съема металла в этом периоде характеризует скорость химического фрезерования.
3.Образование на металле значительного слоя из продуктов реакции, что снижает скорость растворения. В этом случае сам раствор требует смены или регенерации.
Размерное травление может быть: а) общим (по всей поверхности детали в основном для уменьшения веса); б) местным (травлению подвергаются лишь некоторые поверхности до определенных размеров и форм).
Факторы, влияющие на производительность процесса и качество поверхности: 1) материал заготовки; 2) метод получения заготовки и термическая обработка; 3) начальное состояние поверхности заготовки; 4) состав травильного раствора; 5) концентрация раствора; 6) температура раствора;
7)скорость циркуляции раствора; 8) глубина травления.
Последовательность операций технологического процесса химического травления металлов
1.Контроль толщины деталей (ультразвуковой) и состояния поверхностного слоя (наличие дефектов, повреждений).
2.Очистка поверхности детали (с целью снятия заусенцев, краски, окалины и обеспечения плотного сцепления защитного слоя с поверхностью):
2.1.Обезжиривание (бензин).
2.2.Травление для снятия окалины (растворы едкого натра, плавиковой, азотной кислот).
2.3.Пароабразивная обдувка (при большой толщине слоя окалины).
115
2.4.Промывка в горячей и холодной воде.
2.5.Сушка.
3. Нанесение защитных покрытий на необрабатываемые поверхно-
сти.
Виды защитных покрытий:
–механические и вакуумные экраны (для плоских деталей в мелкосерийном производстве. Крепятся винтами, или вакуумом);
–гальванические покрытия (электрическое омеднение для деталей из алюминиевых сплавов с плоскими поверхностями большой площади. Применение метода ограничено из-за сложности и трудоемкости);
–клейкая лента (для ступенчатого травления детали на различную глубину. Лента постепенно снимается с поверхности);
–сплавы на основе парафина (для травления в холодных растворах. Затем легко удаляются при погружении детали в горячую воду);
–светочувствительные эмульсии (в сочетании с негативами из пластмассы);
–лакокрасочные покрытия (наиболее распространенный и эффективный вид. Пример – перхлорвиниловая эмаль).
Существует два способа выборочного покрытия определенных участков заготовки: а) сначала покрывают всю деталь, затем обрабатываемые поверхности очищают; б) предварительно защищают места травления, а затем наносят покрытие на все открытые поверхности (применяется в массовом производстве).
Способы нанесения лакокрасочных покрытий: кистью; пульверизатором; обливом; окунанием всей заготовки.
4. Сушка покрытия (продолжается 2...3 часа до полного испарения растворителя во избежание пористости покрытия. Иногда применяют нагрев с целью полимеризации покрытия).
5. Предварительное травление для снятия окисных слоев с поверхности (заготовки на специальных рамах или в корзинах погружают в концентрированный раствор соляной кислоты).
6. Основное химическое травление.
В щелочном или кислотном растворе (растворы серной, соляной, азотной, фосфорной, плавиковой кислот в порядке значимости, едкого натра, со специальными добавками). Деталь необходимо периодически встряхивать или переворачивать для удаления из-под покрытия на границах контура образующихся газов, препятствующих нормальному травлению. Раствор необходимо периодически очищать от продуктов травления или менять, а также перемешивать для уравнивания температур. Внутренняя поверхность травильной ванны должна быть из кислостойкого материала (поливинилхлорид, фторопласт, эпоксидные смолы). Линейная скорость травления обычно составляет 0,013...0,045 мм/мин.

116
Способы контроля за процессом: а) определением размеров (ультразвуковым способом или толщиномерами); б) определением веса детали; в) по времени выдержки в растворе.
7. Очистка детали после травления:
7.1.Промывка в первичном травильном растворе для удаления солей, которые не смываются водой.
7.2.Промывка в воде.
7.3.Удаление защитного покрытия (обычно выполняется вручную ножами, щетками).
7.4.Промывка.
7.5.Сушка.
8. Окончательный контроль размеров и состояния поверхности дета-
ли.
Особенности химического травления
Процесс травления идет по всем направлениям с одинаковой скоростью, поэтому защитное покрытие должно перекрывать требуемую границу размера выемки A на величину, равную глубине травления R (рис. 6.9).
Под покрытием металл травится по радиусу R. При недостаточной ширине паза (менее 2 мм) в пространстве под покрытием скапливается газ, препятствующий травлению. Для его удаления деталь необходимо периодически встряхивать, переворачивать, прикладывать вибрации.
|
После травления шероховатость об- |
|
|
работанных поверхностей увеличивается |
|
|
на 1...2 класса (причем больше всего у |
|
|
литых заготовок). Глубина травления |
|
|
обычно составляет 6...8 мм (реже до 12 |
|
|
мм). Чем больше глубина травления, тем |
|
|
меньше точность и больше шероховатость |
|
Рис. 6.9. Травление металла заго- |
поверхности. |
|
Химическим травлением получают |
||
товки под покрытием: 1 – покры- |
||
местные утонения на нежестких заготов- |
||
тие; 2 – заготовка |
ках, ребра жесткости, извилистые канавки |
|
|
и щели, «вафельные» поверхности, обрабатывают поверхности, труднодоступные для режущего инструмента.
6.5. Ультразвуковая обработка
Ультразвуковая обработка (УЗО) основана на разрушении обрабатываемого материала абразивными зернами под ударами инструмента, колеблющегося с ультразвуковой частотой.
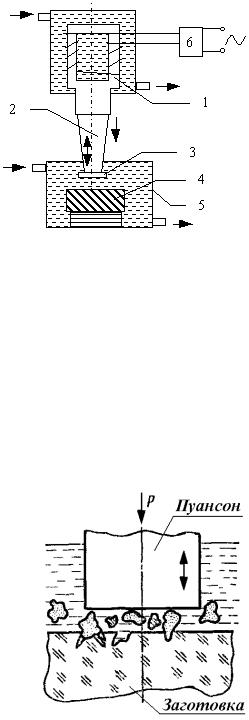
117
УЗО является частным случаем механического вибрационного воздействия, которое может быть низкочастотным и высокочастотным. Частота колебаний инструмента при УЗО превышает звуковой диапазон и со-
ставляет 16...30 кГц. |
|
|
|
|
Механическое |
вибрационное |
воз- |
|
|
действие инструмента на заготовку, как |
|
|||
правило, сочетается с равномерным меха- |
|
|||
ническим воздействием (давлением) того |
|
|||
же инструмента. При ультразвуковой аб- |
|
|||
разивной обработке в зону обработки по- |
|
|||
дается абразивная среда (суспензия). |
|
|
||
В основе получения ультразвуковых |
|
|||
колебаний лежит явление магнитострик- |
|
|||
ции – изменения линейных размеров ряда |
|
|||
материалов в магнитном поле. Эффектом |
|
|||
магнитострикции обладают никель, желе- |
Рис. 6.10. Принципиальная схема |
|||
зоникелевые сплавы |
(пермендюр), |
желе- |
||
зоалюминиевые |
сплавы |
(альфер), |
ультразвуковой обработки |
|
|
ферриты.
Магнитострикционный сердечник 1 (рис. 6.10) периодически изменяет свою длину (на 2...10 мкм) при наличии переменного электромагнитного поля, которое наводится при помощи генератора 6. Резонансный волновод 2 припаивают к торцу сердечника для увеличения амплитуды колебаний (до 10...60 мкм) и концентрации энергии. Через сердечник 1 прокачивают воду для охлаждения (нагрев на гистерезис, вихревые токи). Под пуансоном 3 помещают заготовку 4. Обработка ведется в ванне 5, заполненной абразивной суспензией (взвесь абразивных зерен в воде).
Припуск с поверхности заготовки сни- |
|
мают абразивные зерна, получающие энергию |
|
от удара пуансоном (рис. 6.11). |
|
Инструмент, колеблющийся с ультра- |
|
звуковой частотой, ударяет по зернам абрази- |
|
ва, лежащим на обрабатываемой поверхности |
|
заготовки, которые скалывают частицы мате- |
|
риала заготовки (см. рис. 6.11). |
|
В жидкости происходят кавитационные |
|
процессы (образование пузырьков при разря- |
|
жении, их ликвидация и удар при сжатии), |
|
которые способствуют перемешиванию абра- |
Рис. 6.11. Разрушение обраба- |
зивных зерен под инструментом и более ин- |
тываемого материала при |
тенсивному разрушению материала заготов- |
ультразвуковой обработке |
ки. Инструмент поджимают к заготовке с не- |
|
большим усилием P (до 60 Н). |
|

118
Ультразвуковым методом обрабатывают хрупкие твердые материалы: стекло, керамику, ферриты, кремний, кварц, драгоценные минералы, в том числе алмазы, твердые сплавы, титановые сплавы, вольфрам. Вязкие материалы (незакаленная сталь, латунь) плохо обрабатываются УЗО, так как в этом случае не происходит сколов.
Рис. 6.12. Схемы ультразвуковой обработки поверхностей заготовок:
аи б – прошивание цилиндрического и фасонного отверстий;
в– обработка внутренней полости; г – разрезание
Ультразвуковым методом получают (рис. 6.12) сквозные и глухие отверстия любой формы поперечного сечения (а, б), фасонные полости (в), разрезают заготовки на части (г), профилируют наружные поверхности, гравируют, прошивают отверстия с криволинейными осями, нарезают резьбы.
Рабочие движения для указанных видов обработки: скорость резания V (движение абразивных зерен в направлении обрабатываемой поверхности) и движение подачи S.
Инструменты изготовляют из закаленных (НRС 35...40), но вязких материалов.
Точность размеров и шероховатость поверхностей, обработанных ультразвуковым методом, зависят от зернистости используемых абразивных материалов и соответствуют точности и шероховатости поверхностей, обработанных шлифованием.
6.6.Лучевые методы обработки
Клучевым методам формообразования поверхностей деталей машин относят электронно-лучевую и светолучевую (лазерную) обработки.

119
Электронно-лучевая обработка
Электронно-лучевая обработка основана на превращении кинетической энергии направленного пучка электронов в тепловую. Высокая плотность энергии сфокусированного электронного луча позволяет обрабатывать заготовки за счет нагрева, расплавления и испарения материала с узколокального участка.
Схема установки для электронно-лучевой обработки (электронная пушка) показана на рис. 6.13. В вакуумной камере 1 установки 9 вольфрамовый катод 11, питаемый от источника тока, обеспечивает эмиссию свободных электронов. Электроны формируются в пучок специальным электродом и под действием электрического поля, создаваемого высокой разностью потенциалов между катодом 11 и анодом 10, ускоряются в осевом направлении. Луч электронов проходит систему юстировки 9, диафрагму 8, корректор изображения 7 и систему магнитных линз 6, которые окончательно формируют поток электронов в луч малого
диаметра и фокусируют его на поверхности заго- Рис. 6.13. Схема элек- товки 4, закрепленной в приспособлении 3 на сто- тронно-лучевой установки ле 2. Луч по поверхности заготовки перемещается отклоняющей системой 5, которая может управляться системой числового программного управления (ЧПУ).
Система ЧПУ также управляет продольными и поперечными перемещениями стола, на котором закреплена заготовка, продолжительностью импульсов и интервалов между ними.
При размерной обработке заготовок установка работает в импульсном режиме, что обеспечивает локальный нагрев заготовки. В зоне обработки температура достигает 6000 0С, а на расстоянии 1 мкм от кромки луча не превышает 300 0С. Продолжительность импульсов и интервалы между ними подбирают так, чтобы за один цикл успел нагреться и испариться металл только под лучом. Длительность импульсов составляет 10–4...10–6 с, а частота 50...6000 Гц. Диаметр сфокусированного электронного луча – несколько микрометров.
Электронно-лучевой метод перспективен при обработке отверстий диаметром от 1 мм до 10 мкм, прорезании пазов, резке заготовок, изготовлении тонких пленок и сеток из фольги. Обрабатывают заготовки из труднообрабатываемых металлов и сплавов, а также из неметаллических материалов: рубина, керамики, кварца, полупроводниковых материалов.
Электронно-лучевая обработка имеет преимущества, обусловливающие целесообразность ее применения: создание локальной концентрации высокой энергии, широкое регулирование и управление тепловыми