
1654
.pdfQТ 0,625kнk 1,2ma 2,24 L tп Va 0,25 ,
(7.13) |
|
|
|
|
|
|
|
где kнк |
|
- |
коэффициент |
неравномерной |
концентрации |
||
вредных газов, |
принимают kнк = 1,3 |
при L 2 км и kнк = 1,7 |
|||||
при L 2 км; |
|
|
|
|
|
||
ma |
- |
число машин, находящихся в забое; |
|
||||
L - длина тоннеля, м; |
|
|
|
|
|||
tп |
- |
продолжительность погрузки, с; принимают по |
|||||
формуле (7.8); |
|
|
|
|
|
||
Va |
- |
скорость движения машин, м/с ; |
одновременно |
||||
3) |
по |
наибольшему |
|
числу |
людей, |
||
находящихся в забое, м3/с: |
119 |
|
|
||||
|
|
|
|
Qл 01, n z , (7.14)
где n - наибольшее число людей в забое, обычно принимают равным удвоенному числу проходчиков в смене;
z - коэффициент запаса воздуха, принимают z
=1,2 1,5;
4)по минимальной скорости движения воздуха в тоннеле,
м3/с:
Qc 0,1...0,15 S .
(7.15)
Затем сравнивают полученные объемы воздуха по этим формулам и наибольший объем принимают за расчетный Qp .
Для подачи воздуха применяют вентиляторы местного проветривания типа ВМ и СВМ, металлические, прорезиненные или полимерные трубы диаметром 0,4 1,0 м. Подбор вентиляторов осуществляют в зависимости от необходимой производительности и напора вентилятора. Производительность принимают с учетом 5 10 % запаса от требуемого объема воздуха.
Требуемый напор, создаваемый вентилятором, Па: h 65 l Qp2 d5 ,
(7.16)
где l |
- |
длина воздуховода между смежными вентиляторами, |
|||||
обычно составляет 50 100 м; |
|
|
|
||||
|
- |
коэффициент местных сопротивлений в тройниках, |
|||||
отводах, коленах и т. п., принимают в пределах 1,1 1,3; |
|||||||
d |
- |
диаметр воздуховода, м; |
|
|
|
||
|
- |
коэффициент трения в трубах, принимают по табл. |
|||||
7.3. |
|
|
|
|
|
Т а б л и ц а 7.3 |
|
|
|
|
|
|
|
||
|
|
|
|
|
|
|
|
d , м |
|
0,4 |
0,5 |
0,6 |
|
0,7 |
|
|
|
|
0,00030 |
0,00025 |
0,00022 |
|
0,00020 |
Расчет компрессорной установки и требуемой мощности
электростанции или трансформаторной подстанции следует
120
производить по методике, изложенной в работе 16, с. 283 .
8. РАСЧЕТ ВРЕМЕННОЙ КРЕПИ ТОННЕЛЕЙ
8.1. Общие положения
Временная крепь должна обеспечивать устойчивость выработки до возведения постоянной обделки. В современной практике тоннелестроения наибольшее распространение получили крепи из анкеров, набрызг-бетона и металлических арок, а также комбинированные конструкции, в которые входят элементы крепи различных типов.
Конструкции и технологию устройства крепи выбирают с соблюдением требований действующих норм проектирования и строительства тоннелей исходя из степени устойчивости породного массива, в котором закладывается тоннель. По степени устойчивости горных пород в практике тоннелестроения выбирают конкретный тип временной крепи, наиболее целесообразный для данных условий. В табл. 8.1 приведены категории пород по степени устойчивости.
|
|
|
|
|
Т а б л и ц а 8.1 |
|
|
|
|
|
|
|
|
|
|
|
Допустимые сроки |
Катего- |
|
Коэффи- |
|
Степень |
обнажения выработки |
рия |
|
циент |
устойчивости |
(до установки |
|
пород |
|
крепости f |
|
|
временной крепи) |
I |
|
10 |
Вполне |
Неограниченно |
|
|
|
|
устойчивые |
|
|
II |
|
8 10 |
Устойчивые |
До 6 месяцев |
|
III |
|
5 8 |
Средней |
10 15 суток |
|
|
|
|
устойчивости |
|
|
IV |
|
3 5 |
Неустойчивые |
Менее 1 суток |
|
V |
|
3 |
Весьма |
Обнажение не |
|
|
|
|
неустойчивые |
допускается |
|
Большое |
|
значение |
для |
устойчивости |
выработки имеет |
состояние |
трещиноватости |
121 |
пород. По степени |
||
скальных |
трещиноватости породы подразделяют на пять категорий, которые оцениваются по коэффициенту трещиноватости массива (табл. 8.2).
|
|
|
Т а б л и ц а 8.2 |
|
|
|
|
Степень |
Количество |
Ориентировочное |
Коэффициент |
трещиноватости |
трещин на |
расстояние между |
трещиноватости |
пород |
1 м2 забоя |
трещинами, м |
kТ |
Нетрещиноватые |
До 1 |
|
1 |
Слаботрещиноватые |
1 2 |
1 2 |
1,5 |
Трещиноватые |
2 4 |
0,5 1 |
2 |
Сильнотрещиноватые |
4 10 |
0,2 0,5 |
2,5 |
Раздробленные |
Больше 10 |
Меньше 0,2 |
|
Удовлетворительную устойчивость выработки могут обеспечить различные типы и сочетания элементов крепи. Поэтому предпочтение следует отдавать тем, которые требуют наименьших трудозатрат или стоимости.
Тип временной крепи для конкретных условий, исходя из степени устойчивости горных пород, их трещиноватости, выветриваемости и обводненности, ориентировочно можно выбрать из табл. 8.3, составленной на основе опыта строительства подземных сооружений.
Расчет конструктивных параметров временной крепи выполняется для различных типов крепи следующим образом.
8.2. Анкерная крепь
Длина рабочей части анкера (рис. 8.1), м: lp 075, В kТ f ,
где В - |
(8.1) |
ширина выработки, м; |
|
f - |
коэффициент крепости породы; |
kТ - |
коэффициент трещиноватости массива (табл.8.2). |
|
122 |
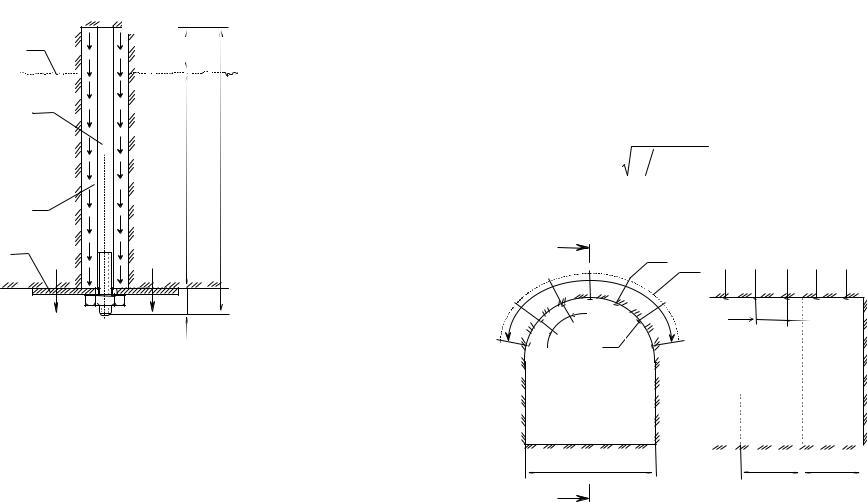
диаметром 25 мм и 60 кН при замке диаметром 36 мм; для железобетонных анкеров, кН, по формуле
N 10 3 l d |
сТ |
|
сц |
, |
з |
|
|
|
123 |
|
|
|
(8.3) |
|
|
|
124 |
|
|
|
|
|
|
|
где |
dсТ - |
|
|
|
|
м, принимают равным от |
||||
|
|
|
|
диаметр стержня анкера, |
|||||||||
3 |
lз |
|
14 до 20 мм; |
|
|
|
|
|
|
|
|||
|
|
|
сц |
- |
|
удельное сцепление |
бетона с |
армирующим |
|||||
|
|
|
|
|
|
||||||||
|
|
|
|
стержнем, принимают |
сц = 45 105 Па (при сроке твердения 6 |
||||||||
dсm |
|
|
|
ч). |
Предельное |
расстояние |
между |
анкерами |
по |
условию |
|||
|
|
|
|
||||||||||
|
|
|
la |
|
|||||||||
|
|
|
несущей способности замка (рис. 8.2), м: |
|
|
||||||||
|
|
lp |
|
|
|
|
|
an |
N 15 lp , |
|
|
|
|
1 |
|
|
|
|
(8.4) |
средняя плотность породы, т/м3. |
|
|
|||||
|
|
|
где |
|
- |
|
|
||||||
|
|
|
|
|
|
||||||||
2 |
|
|
|
|
|
|
A |
|
|
A - A |
|
|
|
|
|
|
|
|
|
|
|
1 |
|
|
|
|
|
|
|
|
|
|
|
|
|
|
3 |
|
|
|
|
|
|
|
|
|
|
|
|
la |
|
|
|
|
|
|
|
|
|
|
|
|
|
|
|
|
|
|
|
P/2 |
|
lk |
|
|
|
|
|
|
|
|
a |
|
|
P/2 |
|
|
|
|
|
a |
|
|
|
|
|
||
|
|
|
|
|
|
|
|
|
|
|
|
||
|
|
|
|
|
|
|
2 |
|
|
|
|
|
|
|
|
|
|
|
|
|
|
|
|
|
|
|
|
Рис. 8.1. Расчетная схема анкера: |
1 - анкер; |
|
|
|
|
|
|
|
|
|
|
||
2 - шайба; 3 - граница зоны |
возможного |
|
|
|
|
|
|
|
|
|
|
||
|
обрушения |
|
|
|
|
|
|
|
|
|
|
|
|
Длина замковой части |
lз |
принимается: для клиновых |
анкеров не менее 20 см, |
для |
железобетонных в пределах |
30 60 см.
Общая длина анкера (с учетом выступающей из породы части анкера длиной lk = 10 см), м:
la lp lз lk . (8.2)
Прочность закрепления замка анкера в породе N принимают: для клинощелевых анкеров - 90 кН при замке
B |
l |
l |
|
|
|
A
Рис.8.2. Схема к расчету анкеров на заходку
Чтобы исключить возможность образования вывалов между анкерами, должно быть выполнено условие: an lp .
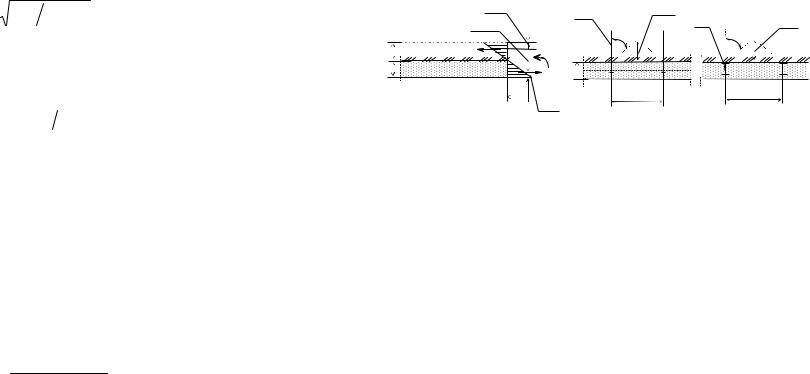
При этом длина анкера не может быть менее 1 м. В сильнотрещиноватых породах расстояние между анкерами следует уменьшить до 0,5 lp .
Расчетная нагрузка на анкер, кН, составит
P 15 a2 lp , |
(8.5) |
125 |
|
где а - принятое (откорректированное) расстояние между анкерами, м.
Расстояние а корректируют с учетом того, чтобы оно было кратным длине заходки lзах .
Диаметр стержня, см, анкера корректируют по формуле
|
|
|
d 2 10P Ra , |
|||
|
|
|
(8.6) |
|
|
|
где |
Ra - расчетное сопротивление материала стержня анкера |
|||||
на растяжение, для стали |
Ra = 225 МПа. |
|||||
Количество анкеров на заходку |
|
|
||||
|
|
|
n L l |
зах |
a2 , |
|
|
(8.7) |
|
a |
a |
|
|
|
|
|
|
|
|
|
где |
La |
- |
периметр |
свода выработки, закрепленного |
||
анкерами. |
|
|
|
|
|
8.3. Крепь из набрызг-бетона
Набрызг-бетонная крепь применяется как в виде самостоятельной конструкции, так и в комбинированных конструкцих, т. е. при сочетании с анкерами или металлическими арками. При расчете определяют толщину покрытия и объем набрызг-бетона на цикл.
Толщина покрытия из набрызг-бетона, применяющегося в качестве самостоятельной конструкции (рис.8.3, а), см:
h 346,qp
m k1 Rвt ,
(8.8)
где qp - расчетное давление, кН/м2;
m - |
коэффициент |
условий работы набрызг- |
бетона, определяют по формуле |
m = m1 + m2 , причем |
m1 = 0,7 для глиноземистого цемента; 1,0 для других видов цемента;
m2 = 0,7 для слаботрещиноватых пород; 0,5 для трещиноватых пород;
k1 - коэффициент влияния ширины выработки и крепости породы, определяют по табл. 8.4.
Rвt - расчетное сопротивление набрызг-бетона при осевом
126
растяжении, КПа, определяют по табл. 8.5.
а) |
б |
qp |
|
h/3 |
1 |
qp |
|
4/3h |
2 |
||
|
/4 |
|
/4 |
h |
M |
|
|
|
|
|
|
h |
N h |
|
a |
hp |
a |
|
|
|
h/3 |
|
|
Рис. 8.3. Расчетные схемы набрызг-бетонного покрытия: а - самостоятельная конструкция; б - в сочетании с анкерами 1 и арками 2
|
|
|
|
|
|
|
|
Т а б л и ц а 8.4 |
|
|
|
|
|
|
|
|
|
|
|
Коэффициент |
|
Значение k1 при ширине выработки, м |
|||||||
крепости |
|
||||||||
породы f |
4 |
6 |
|
8 |
|
|
10 |
||
3 |
0,2 |
0,1 |
|
|
|
|
|||
4 |
0,4 |
0,3 |
|
0,2 |
|
|
|
||
6 |
0,9 |
0,8 |
|
0,7 |
|
|
0,6 |
||
8 |
1,0 |
0,9 |
|
0,8 |
|
|
0,7 |
||
|
|
|
|
|
|
|
|
Т а б л и ц а 8.5 |
|
|
|
|
|
|
|
|
|||
Набрызг-бетон |
|
Расчетное сопротивление |
Rвt , |
КПа, при |
|||||
|
|
классе набрызг-бетона |
|
|
|||||
|
|
В25 |
|
В30 |
|
|
|
В40 |
|
Армированный |
|
1,2 |
|
1,4 |
|
|
1,6 |
||
Неармированный |
|
1,0 |
|
1,2 |
|
|
1,4 |
При армированном набрызг-бетоне покрытие выполняют по металлической сетке с ячейками 100 х 100 или 150 х 150 мм из проволоки диаметром 6 8 мм. Следует учитывать при
127
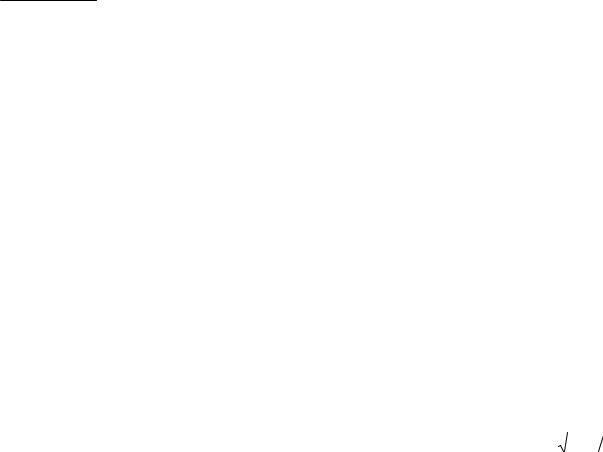
этом, что армированным может быть покрытие толщиной не менее 6 см.
Толщина покрытия из набрызг-бетона в сочетании с анкерами или арками (рис. 8.3,б), см:
h 10n1 aqр
m k2 Rвt , (8.9)
где при гарантированном расчетном сцеплении покрытия с породой коэффициент, зависящий от комбинации видов крепи:
n1 |
= |
0,6 |
при сочетании с анкерами; |
|
а - |
|
0,7 |
при сочетании с арками; |
|
расстояние между анкерами (арками), м; |
||||
qр |
- |
нагрузка от возможного |
вывала породы между |
|
анкерами (арками), кН/м2, определяют по формуле |
||||
|
|
|
qр n2 a; |
(8.10) |
n2 = 0,37 при сочетании с анкерами; 0,25 при сочетании с арками;
- удельный вес породы, кН/м3;
k2 - коэффициент влияния расстояния между анкерами (арками) и крепости породы, определяют по табл. 8.6.
|
|
|
|
|
|
Т а б л и ц а 8.6 |
|
|
|
|
|
|
|
||
Коэффициент |
Значение k2 |
при расстоянии между анкерами |
|||||
крепости |
|
|
(арками), м |
|
|
|
|
породы f |
0,5 |
|
1,0 |
|
1,5 |
|
2,0 |
2 |
0,3 |
|
0,2 |
|
0,2 |
|
0,1 |
3 |
0,5 |
|
0,4 |
|
0,3 |
|
0,2 |
4 |
1,0 |
|
0,9 |
|
0,8 |
|
0,6 |
6 |
1,0 |
|
1,0 |
|
0,9 |
|
0,8 |
Объем набрызг-бетона на цикл находят по формуле, м3:
Vнб lсв lзах h, |
(8.11) |
где lсв - периметр свода и стен выработки, по которому наносится набрызг-бетон, м.
8.4. Металлическая арочная крепь
Арки временной крепи рассчитываются на прочность и устойчивость при действии расчетных нагрузок от горного давления. Расчетным состоянием арки следует считать такое, при котором хотя бы одно из поперечных сечений переходит в предельное состояние (первая группа) от воздействия нормальной силы и изгибающего момента.
Расчетный коэффициент упругого отпора K рекомендуется принимать постоянным по всему контуру выработки, за исключением пят арок. При наличии забутовки в зазоре между аркой и поверхностью выработки величину
коэффициента упругого отпора определяют по формуле, кН/м3:
|
|
К Кo , |
(8.12) |
||
где Ko |
- коэффициент упругого отпора, принятый для расчета |
||||
обделки; |
|
|
|
|
|
|
- |
коэффициент учета влияния забутовки, определяют |
|||
по табл. 8.7. |
Т а б л и ц а 8.7 |
||||
|
|
|
|
|
|
|
|
|
|
|
|
|
|
Средняя толщина забутовки, см |
|
||
|
|
5 |
|
|
0,040 |
|
|
10 |
|
|
0,025 |
|
|
15 |
|
|
0,015 |
|
|
20 |
|
|
0,007 |
Коэффициент упругости под пятой арок |
определяют по |
||||
формуле, кН/м3: |
|
||||
|
|
Кn К |
|
, |
(8.13) |
где la |
|
05, la вп |
|||
- |
полная длина арки, м; |
|
|||
вп |
- ширина пяты арки, м. |
|
Расчет арки временной крепи выполняют методом сил. В качестве расчетной схемы принимают арку с шарнирами в пятах. Другие шарниры определяются конструкцией арки. В результате расчета находят изгибающие моменты Мi и
128 |
129 |
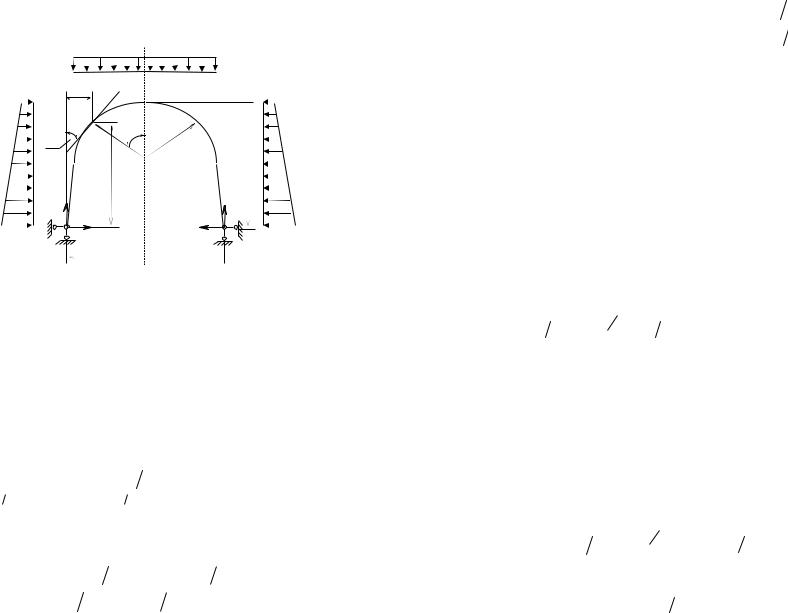
нормальные силы Ni в сечениях арки. Расчетная схема приведена на рис. 8.4.
|
|
|
q |
|
p1 |
x |
|
o |
p1 |
m |
|
|||
|
|
|
||
|
m |
|
|
|
|
|
r |
|
|
|
|
|
||
|
|
y |
h |
|
|
|
|
|
|
Y |
|
|
Y |
p2 |
p2 |
X |
|
X |
|
|
|
B |
|
|
|
|
|
|
|
Рис. 8.4. Расчетная схема арочной крепи |
|
Расчет выполняется следующим образом.
Определяют горное вертикальное q и горизонтальное р
давление на уровне замка |
h1 на уровне пяты свода h2. |
|||||||||||
Находят вертикальные реакции в нижних шарнирах арки: |
||||||||||||
|
|
|
|
|
Y 0,5q В. |
|
|
|
|
(8.14) |
||
Определяют горизонтальные реакции в нижних шарнирах |
||||||||||||
(распор арки): |
|
|
|
X 1p 11 , |
|
|
|
|
(8.15) |
|||
|
|
|
|
|
|
|
|
|||||
S 2 |
|
|
|
|
|
|
S 2 |
|
|
|
|
|
где 1p ds |
и |
11 |
1 ds . |
|
|
|
(8.16) |
|||||
0 |
|
|
|
|
|
|
0 |
|
|
|
|
|
Суммы смещений и 1 находят из уравнений |
|
|||||||||||
M |
p |
M |
i |
E J N |
p |
N |
i |
E A ; |
|
|||
|
|
|
|
|
|
|
|
(8.17) |
||||
|
|
M 2 |
E J N2 E A . |
|
||||||||
1 |
|
|
||||||||||
|
|
|
i |
|
|
i |
|
|
|
|
|
Моменты и нормальные силы130 определяют по формулам:
М1 |
y; |
N1 sin ; |
|
|
|
|
|
|
|
|
||
Mp |
Y x 0,5q x2 |
0,5p2 y2 p2 |
p1 y3 |
6h; |
|
|||||||
(8.18) |
||||||||||||
N |
p |
Y cos q x cos p |
2 |
0,5 |
p |
2 |
p y |
h y sin , |
||||
|
|
|
|
|
|
|
1 |
|
|
|||
где |
Y, A - момент инерции и площадь поперечного сечения |
|||||||||||
элементов крепи; |
|
|
|
|
|
|
|
|
||||
|
|
E - модуль упругости материала крепи; |
|
|||||||||
|
|
x, y |
- |
произвольные координаты искомой точки m; |
||||||||
|
|
|
- |
угол отклонения от вертикали касательной к оси |
||||||||
арки в сечении m с координатами x и y. |
|
|
||||||||||
|
Перемещения |
1р и |
|
11 |
определяют по формулам |
Симпсона при разбивке контура арки на равные отрезки (как для обделки). Для облегчения расчета составляют вспомогательные таблицы подобно таблицам, применявшимся при расчете обделки.
После определения изгибающих моментов и нормальных сил в сечениях арки находят несущую способность арки в наиболее опасных сечениях из условия максимума выражения
N |
i |
A |
R 32 |
M |
i |
W R , |
i 1,2,...,n , |
(8.19) |
||
|
|
а |
a |
|
n a |
|
|
|
||
где Аа |
- |
площадь поперечного сечения арки, м2; |
|
|||||||
Wn |
- пластический момент сопротивления сечения, м3, |
|||||||||
равный |
1,2W ; |
|
|
|
|
|
|
|||
W - момент сопротивления сечения арки, м3; |
|
|||||||||
Ni |
- |
|
нормальная сила в сечении i, кН; |
|
|
|||||
Mi |
- изгибающий момент в сечении i, |
кН м; |
|
|||||||
Ra |
- предел прочности материала арки, |
МПа. |
|
Обозначив расчетные значения нормальной силы и момента в опасном сечении соответственно через Nnp и Mnp , находят предельную нагрузку qmax из уравнения
N |
пр |
q |
А |
R 32 М |
пр |
q |
W |
R 1. |
(8.20) |
|
max |
а |
a |
max |
n |
a |
|
||
Затем определяют расстояние между арками (шаг арок) а |
|||||||||
по предельной нагрузке qmax , |
м: |
|
|
|
|||||
|
|
|
|
a qmax q, |
|
131 |
|
|
(8.21) |
где q - расчетная величина вертикального давления.
Шаг корректируют таким образом, чтобы он был кратен величине заходки.
Далее, производят расчет количества арок на заходку и их массу.
В курсовом проекте арки на несущую способность можно не выполнять, а только рассчитывать количество арок и их массу, исходя из крепости породы, сечения выработки, профиля двутавра. Обычно принимают профили двутавров № 16 27 и расстояния между арками от 0,5 до 1,5 м.
9. ОРГАНИЗАЦИЯ ПРОХОДЧЕСКИХ РАБОТ
Для обеспечения наиболее полного использования рабочей силы и принятого проходческого оборудования и ритмичного выполнения всех основных операций в заранее установленное время и без простоев проходка тоннелей производится по графику цикличности, т.е. путем последовательного повторения отдельного комплекса операций в определенный промежуток времени.
При этом следует учесть, что процессы установки временной крепи, подготовки к бурению шпуров и погрузке породы, выполнения прочих работ могут быть полностью или частично совмещены по времени с основными операциями - бурением и погрузкой.
Для определения продолжительности проходческого цикла составляют циклограмму, которая содержит: последовательность выполнения и объемы работ цикла; нормальное время, требуемое для их выполнения; количество людей, необходимое для выполнения той или иной операции; графическое изображение времени, принятого для выполнения операции.
Все виды работ, включенные в циклограмму, увязывают, исходя из их технологической последовательности и возможности совмещения во времени. Продолжительность
132
каждой технологической операции устанавливают в
соответствии с нормами времени и расчетами производительности оборудования.
При составлении циклограмм необходимо предусматривать последовательно выполнение основных операций проходческого цикла: бурения шпуров в забое и погрузки породы, а также максимального совмещения во времени операций по установке временной крепи и других вспомогательных операций с основными.
Состав проходческой бригады определяют по расстановке рабочих для обслуживания всех операций цикла. Общее число проходчиков находят из условия равномерной нагрузки рабочих и максимального совмещения операций цикла.
Равномерная нагрузка проходчиков достигается при равенстве числа рабочих, занятых на бурении шпуров и совмещаемых с бурением операциях, с числом рабочих, занятых на погрузке породы и совмещаемых с погрузкой операциях. Число рабочих, занятых выполнением совмещаемых операций, принимают из условия окончания их в срок, достаточный для выполнения основных операций цикла.
Наиболее рациональная организация работ обеспечивается при продолжительности цикла, равной целому числу рабочих смен, либо при выполнении целого числа циклов в сутки. Это позволяет устанавливать равномерную и постоянную нагрузку на каждое сменное звено проходческой бригады.
Рекомендуемая форма и примеры циклограмм приведены в работах 12, 13, 15, 16 . Порядок составления циклограмм следующий: вначале устанавливают последовательность основных ведущих работ и операций, затем определяют объем работ по отдельным операциям, после чего выявляют затраты времени на выполнение этих объемов работ и, наконец, подсчитывают количество рабочих по операциям и распределяют их по времени.
133
10.ВОЗВЕДЕНИЕ ОБДЕЛКИ
10.1.Технологические схемы работ
При возведении обделки из монолитного бетона применяют две схемы - параллельную и последовательную.
При параллельной схеме работы по выемке породы (проходческие работы) и возведению обделки ведутся одновременно, но бетонирование отстает от забоя на 100 300 м. Эту схему применяют при наличии недостаточно устойчивых пород, когда нельзя оставлять выработки с временной крепью на длительное время в тоннелях значительной длины. Величина отставания обделки от забоя зависит от инженерно-геологических условий, схемы движения транспорта и размещения оборудования в призабойной части тоннеля. Работы по выемке породы и возведению обделки в этих условиях не должны снижать безопасность работ и вызывать взаимные помехи, сдерживающие их нормальное выполнение. Скорость возведения обделки должна быть увязана со скоростью проходки.
При последовательной схеме возведение обделки производится после окончания проходческих работ на всю длину тоннеля. Эту схему применяют при проведении тоннелей в крепких, устойчивых породах, допускающих оставление выработки с временной крепью на длительное время, в тоннелях ограниченной длины. В организационном отношении последовательная схема работ является более простой, но она не может обеспечить достаточно высокой скорости сооружения тоннеля.
10.2. Оборудование для возведения обделки
Комплекс работ по возведению обделки состоит из подготовительных работ, монтажа (установки) опалубки,
приготовления и транспортирования бетонной смеси и укладки ее за опалубку.
Подготовительные работы ведут с опережением процесса укладки бетонной смеси и включают: подготовку поверхности к бетонированию - ликвидацию «недоборов», очистку породной поверхности от отслоившихся кусков породы, продувку сжатым воздухом или промывку водой; заготовку или установку арматуры и закладных деталей; отвод грунтовых вод; устройство пути для перемещения опалубки.
После выполнения подготовительных работ производится установка (монтаж) опалубки. В тоннелестроении применяют передвижные механизированные шарнирно складывающиеся и сборно-разборные тюбинговые опалубки.
Передвижные опалубки типа МО-2 состоят из одной или нескольких секций и перемещаются по рельсовому пути. Длина односекционной опалубки 6 12 м, многосекционные опалубки состоят из 2 6 секций шириной 2 8 м. Передвижные опалубки целесообразно применять при проведении тоннелей большой длины, когда затраты на изготовление опалубки компенсируются экономическим эффектом от повышения скорости возведения обделки.
Сборно-разборные опалубки типа ИО-18 и ИО-21 состоят из отдельных секций шириной 1 1,5 м, собираемых из сегментов (тюбингов) и соединяемых болтами. Длина опалубки 15 20 м. Монтаж сборно-разборных опалубок весьма трудоемок, и в основном они применяются в тоннелях небольшой длины.
В отечественном тоннелестроении для производства бетонной смеси широко распространены стационарные и передвижные бетоносмесительные установки, расположенные у порталов тоннелей. Применяют установки непрерывного действия С-548, С-543, С-780 с производительностью 15 30 м3/ч и установки периодического действия СБ-70, С-333, С- 221П с производительностью 10 16 м3/ч.
Транспортирование бетонной смеси производится на небольшое расстояние в автосамосвалах135 МАЗ-503, ММЗ-555
134
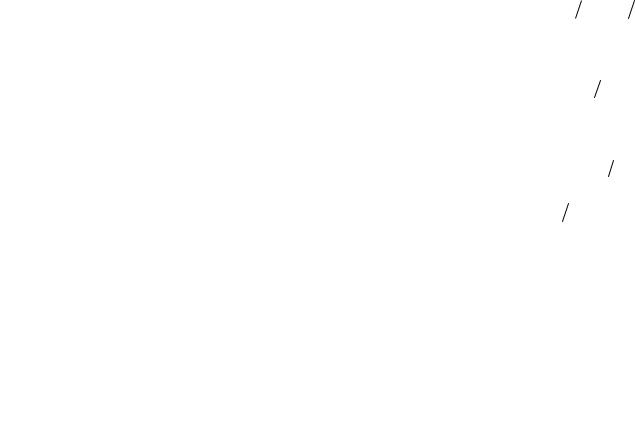
и других грузоподъемностью 4,5 7,0 т или в вагонеткахбетоновозках. При продолжительности транспортирования более 30 мин следует применять автобетоносмесители СБ-69 и СБ-92 или пневмобетононагнетатели типа миксер емкостью 3 м3 на рельсовом ходу.
Укладка бетонной смеси за опалубку производится пневмобетоноукладчиками ПБН-1,5, ПБН-3,3, ПН-0,5, миксерами или бетононасосами БН-40, СБ-126, БН-1 и др.
Бетонная смесь укладывается слоями высотой 30 50 см и уплотняется глубинными вибраторами ИВ-117, ИВ-114 и др.
После достижения бетоном прочности, достаточной для восприятия горного давления, производят нагнетание растворов за обделку с помощью растворонагнетателей и растворонасосов (С-263, РН-2, С-317, С-862 и др.).
Набрызг-бетон на поверхность выработки наносят специальными набрызг-бетономашинами БМ-68, БМ-70, С- 630А и другими.
Технические характеристики приведены в 18 и приложениях.
10.3. Расчет параметров бетонных работ
Для возведения обделки тоннеля из монолитного бетона (железобетона) назначают исходные показатели (скорость бетонирования, расход бетона на 1 пог.м тоннеля, время выдержки бетона) и выбирают оборудование необходимой производительности: опалубку, бетоноукладчики, бетоносмесители и пр. Темп бетонирования принимают в соответствии с технологической схемой производства работ.
Длина участка бетонирования определяется из условия непрерывности возведения обделки при заданных скорости бетонирования и времени выдержки бетона:
для переставной (сборно-разборной) опалубки, м: |
|
||
Lб lc |
136 |
24; |
(10.1) |
tв Vсут |
для механизированной односекционной опалубки, м:
Lб lc ; |
(10.2) |
для механизированной многосекционной опалубки, м: |
|
Lб n lc , |
(10.3) |
где lc - ширина секции опалубки, м; |
|
tв - время выдержки бетона, ч, принимают равным |
|
(24 48) ч; |
|
Vсут - скорость бетонирования, м/сут, принимают равной Vпр при параллельной схеме разборно-проходческих работ;
Vпр |
- скорость проходки, м/сут; |
|
n - |
число секций, определяют по формуле |
|
|
n tв Vсут 24 lc lc . |
(10.4) |
При применении многосекционной опалубки длину участка бетонирования уточняют, исходя из целого числа секций п.
Число требуемых секций опалубки |
|
no Lб lc . |
(10.5) |
При дробном по его округляют до |
полного числа и |
уточняют скорость бетонирования (для переставной опалубки), м/сут:
|
|
Vсут 24 Lб lc tв . |
(10.6) |
|
Продолжительность цикла бетонирования определяется как |
||||
|
|
Tц 24Lб |
Vсут . |
(10.7) |
Вместе с тем цикл бетонирования складывается из суммы |
||||
основных операций цикла, ч: |
|
|
||
|
|
Tц tу tn tо tуТ tрТ , |
(10.8) |
|
где ty |
- |
время на укладку бетонной смеси за опалубку; |
||
tn |
- |
время на перестановку (передвижку) опалубки; |
||
ta |
|
- время на установку арматуры (при применении |
||
железобетона); |
|
|
||
tуТ |
, |
tрТ - время на |
установку и разборку |
торцевой |
опалубки. |
137 |
|
||
|
|
Операции по сборке и разборке бетоновода, настилка основания рельсового пути, очистка и др. обычно совмещаются по времени с основными операциями.
Необходимым условием является проверка соотношения