
991
.pdf
Б.И. Калмин, М.С. Корытов
МЕХАНИЧЕСКАЯ ОБРАБОТКА МЕТАЛЛОВ
Федеральное агентство по образованию Сибирская государственная автомобильно-дорожная академия
(СибАДИ)
Б.И. Калмин, М.С. Корытов
МЕХАНИЧЕСКАЯ ОБРАБОТКА МЕТАЛЛОВ
Учебное пособие
Омск Издательство СибАДИ
2006
УДК 621.9 ББК 34.722 К 17
Рецензенты:
д-р техн. наук, проф. А.П. Рауба, канд. техн. наук В.А. Глушец
Работа одобрена редакционно-издательским советом академии в качестве учебного пособия по учебной практике для студентов механических специальностей вузов.
Калмин Б.И., Корытов М.С. Механическая обработка металлов: Учебное пособие. – Омск: Изд-во СибАДИ, 2006. – 67 с.
Изложены сведения об основах обработки материалов резанием и применяемом режущем инструменте, наладке и эксплуатации металлорежущих станков с ручным управлением, рассматриваются вопросы технологии выполнения типовых операций на станочном оборудовании, выбора режима обработки, режущего и мерительного инструмента при прохождении студентами учебной практики в механических мастерских.
Табл. 5. Ил. 40. Библиогр.: 4 назв.
ISBN 5 – 93204 – 247 – 8 |
©Б.И. Калмин, М.С. Корытов, 2006 |
|
3 |
|
|
ОГЛАВЛЕНИЕ |
|
Введение.............................................................................................. |
4 |
|
1. |
Классификация металлорежущих станков.............................. |
4 |
2. |
Точность станков и качество обработки…………………….. |
8 |
3. |
Организация рабочего места станочника…………………… |
8 |
4. |
Охрана труда, безопасность труда……………………………. |
10 |
5. |
Основные понятия теории резания материалов…………… |
12 |
6. |
Элементы резания………………………………………………. |
14 |
7. |
Шероховатость поверхности и точность обработки………. |
17 |
8. |
Назначение режимов резания…………………………………. |
19 |
9. |
Основные сведения о процессе точения……………………… |
21 |
|
9.1. Токарные резцы.................................................................... |
22 |
|
9.2. Основные операции точения............................................... |
23 |
|
9.3. Режимы резания.................................................................... |
24 |
|
9.4. Нормирование токарной операции...................................... |
28 |
10. Основные сведения о процессе сверления.............................. |
29 |
|
|
10.1. Режущий инструмент.......................................................... |
29 |
|
10.2. Основные операции сверления.......................................... |
32 |
|
10.3. Режимы резания................................................................... |
34 |
11. Основные сведения о процессе фрезерования……………… |
36 |
|
|
11.1. Типы фрез............................................................................. |
38 |
|
11.2. Виды поверхностей, обрабатываемых фрезерованием.... |
39 |
|
11.3. Режимы резания................................................................... |
41 |
|
11.4. Нормирование операции фрезерования............................ |
44 |
12.Основные сведения о процессе строгания………………….. 44
13.Основные сведения о процессе шлифования………………. 45
13.1. Виды шлифования.............................................................. |
46 |
13.2.Режимы резания………………………………………….. 50
14.Основные сведения о процессе притирки………………….. 53
15.Основные сведения о процессе хонингования…………….. 54
16. |
Основные сведения о процессе суперфиниширования…... |
56 |
17. |
Основные сведения о процессе полирования……………… |
57 |
18. |
Примеры заданий по механической обработке…………… |
59 |
|
Задание № 1…………………………………………………….. |
59 |
|
Задание № 2…………………………………………………….. |
59 |
|
Задание № 3…………………………………………………….. |
61 |
|
Задание № 4…………………………………………………….. |
61 |
|
Задание № 5…………………………………………………….. |
62 |
Заключение....................................................................................... |
64 |
|
Контрольные вопросы…………………………………………… |
65 |
|
Библиографический список............................................................ |
66 |
4
ВВЕДЕНИЕ
Механическая обработка является основным технологическим процессом, позволяющим получить наибольшую точность и наименьшую шероховатость поверхностей деталей машин. Она выполняется на токарных, фрезерных, сверлильных, шлифовальных, хонинговальных и других металлорежущих станках. Проходя учебную практику в механических мастерских, студенты получают навыки работы на основных металлорежущих станках. Они овладевают основными рабочими приемами точения, фрезерования, сверления, строгания заготовок деталей машин, а также заточки режущего инструмента.
Студенты овладевают методикой настройки металлорежущих станков на основные технологические операции и изучают технику безопасности при работе на станках.
Таким образом, студенты-практиканты закрепляют знания, полученные в теоретических курсах, и подготавливаются к изучению технологических дисциплин на старших курсах.
Настоящее учебное пособие комплексное. Его материал охватывает общие сведения о специфике профессии станочника, основах обработки материалов резанием и применяемом режущем инструменте, об устройстве, наладке и эксплуатации металлорежущих станков с ручным управлением. Подробно рассмотрены вопросы технологии выполнения типовых операций на станочном оборудовании; выбора режущего инструмента и режима обработки; контрольного инструмента и приспособлений; наладки и переналадки, а также рациональных методов эксплуатации, в том числе организации рабочего места.
1. КЛАССИФИКАЦИЯ МЕТАЛЛОРЕЖУЩИХ СТАНКОВ
Металлорежущим станком (или просто станком) называют технологическую машину, на которой путем снятия стружки с заготовки получают деталь с заданными размерами, формой, шероховатостью и взаимным расположением поверхностей. Кроме металлических заготовок, на станках обрабатывают также детали из других материалов, поэтому термин «металлорежущие станки» устаревает и его можно считать условным. Заготовкой называют предмет труда, из которого изменением формы, размеров и свойств поверхности изготовляют деталь. Последняя представляет из себя продукт труда – изделие, пред-
5
назначенное для реализации (в основном производстве) или для собственных нужд предприятия (во вспомогательном производстве).
Станки могут быть классифицированы по разным признакам, например, по степени универсальности они относятся к одной из следующих групп:
•универсальные – для выполнения разнообразных операций на деталях широкой номенклатуры; используются главным образом в единичном или мелкосерийном производстве и на ремонтных работах (станки, предназначенные для особо широкого диапазона работ, называют широкоуниверсальными);
•специализированные, предназначенные для изготовления группы деталей, сходных по конфигурации, но отличающиеся размерами;
•специальные – для изготовления одной определенной детали. Специализированные и специальные станки используются в
крупносерийном и массовом производствах.
По степени точности станки делят на пять классов: нормальной точности (Н), к ним относится большинство универсальных станков; повышенной точности (П), изготовляемые на базе станков нормальной точности, но при повышенных требованиях к точности обработки ответственных деталей станка и качеству сборки и регулировки; высокой точности (В), достигаемой за счет специальной конструкции отдельных узлов, высоких требований к точности изготовления деталей, к качеству сборки и регулировки узлов станка в целом; особо высокой точности (А), при их изготовлении предъявляются еще более жесткие требования, чем при изготовлении станков класса В, и особо точные (С) станки, называемые иначе мастер-станки. Точность работы станков классов В, А и С достигается при эксплуатации их в помещениях с постоянными, автоматически регулируемыми температурой и влажностью.
По степени автоматизации различают механизированные и автоматизированные станки, в том числе автоматы и полуавтоматы.
Механизированный станок имеет одну автоматизированную операцию, например зажим заготовки или подачу инструмента. Автомат, осуществляя обработку, производит все рабочие и вспомогательные движения цикла и повторяет их без участия рабочего, который лишь наблюдает за работой станка, контролирует качество обработки и при необходимости подналаживает станок, т.е. регулирует его для восстановления достигнутых при наладке точности взаимного расположения инструмента и заготовки, качества обрабатываемой де-
6
тали. (Под циклом технологической операции понимают интервал календарного времени от начала до конца периодически повторяющейся технологической операции независимо от числа одновременно изготавливаемых деталей.) Полуавтомат – станок, работающий с автоматическим циклом, для повторения которого требуется вмешательство рабочего. Например, рабочий должен снять деталь и установить заготовку, а затем включить станок для автоматической работы в следующем цикле.
По расположению шпинделя станки делятся на горизонтальные, вертикальные, наклонные и комбинированные.
В зависимости от массы различают станки легкие (до 1т), средние (от 1 до 10 т) и тяжелые (свыше 10 т), среди которых можно выделить особо тяжелые или уникальные (более 100 т).
Совокупность всех типов и размеров выпускаемых станков называется типажом. Для обозначения модели станка, выпускаемого серийно, принята классификация, разработанная ЭНИМСом (Экспериментальный научно-исследовательский институт металлорежущих станков), в соответствии с которой все станки делят на девять групп, приведенных в табл. 1. Каждая группа, в свою очередь, подразделяется на девять типов, характеризующих назначение станка, его компоновку и другие особенности. Модель станка обозначается тремя или четырьмя цифрами с добавлением в некоторых случаях букв. Первая цифра указывает группу станка, вторая – тип, третья и четвертая характеризуют один из важнейших параметров станка (типоразмер). Буква, стоящая после первой или второй цифры, указывает на модернизацию основной базовой модели станка, а буква после основных трех или четырех цифр – на модификацию базовой модели (в том числе по точности обработки и системе управления). Например, 2Р135Ф2 означает, что это станок вертикально-сверлильный (вторая группа, первый тип), модернизированный (Р – оснащен шестишпиндельной револьверной головкой), 35 – максимальный диаметр сверления, Ф2 – станок оснащен позиционной системой числового программного управления.
Для обозначения специальных и специализированных станков каждому станкостроительному заводу присвоен индекс из одной или двух букв, после которого ставится регистрационный номер станка. Например, МК – Московское станкостроительное АО «Красный пролетарий» и т.д.
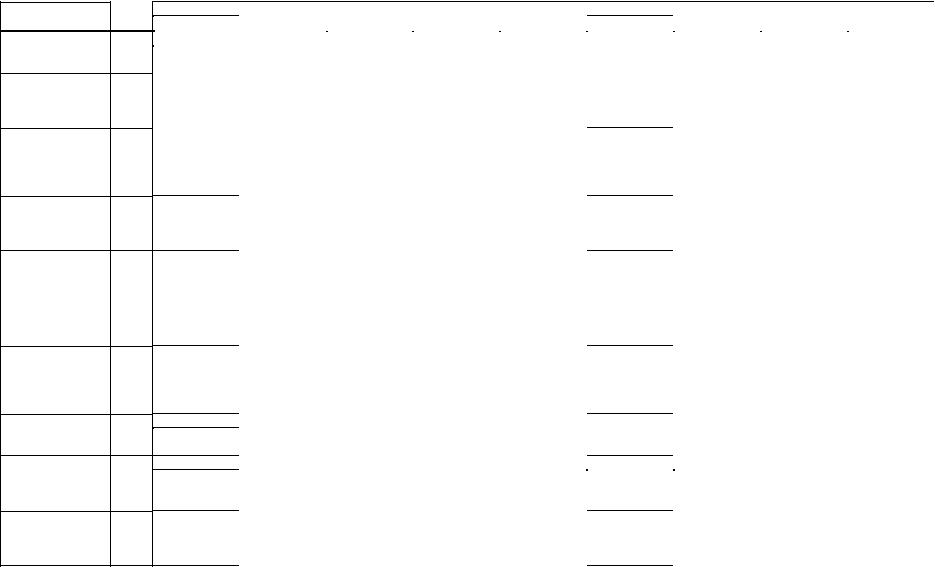
Т а б л и ц а 1. Классификация станков
Наименование Группа -
Токарные 1
Сверлильные и |
2 |
расточные |
|
Шлифовальные, |
|
полировальные, |
3 |
доводочные, |
|
заточные |
|
Электрофизиче- |
4 |
ские и электро- |
|
химические |
|
Зубо- и резьбо- |
5 |
обрабатываю- |
|
щие |
|
Фрезерные 6
Строгальные, долбежные, 7 протяжные
Разрезные 8
Разные 9
1 |
|
|
|
Тип станка |
6 |
|
|
|
|
|
|
|
|
|
|
||||
2 |
3 |
4 |
5 |
7 |
8 |
9 |
|||
Автоматы и полуавтоматы |
Токарно- |
Сверлильно- |
Карусель- |
Токарные и |
Многорезцо- |
Специали- |
Разные то- |
||
одношпин- |
многошпин- |
револьвер- |
отрезные |
ные |
лоботокар- |
вые и копи- |
зированные |
карные |
|
дельные |
дельные |
ные |
|
|
ные |
ровальные |
|
|
|
Настольно- |
Полуавтоматы |
Координат- |
Радиально- |
|
Отделочно- |
Горизон- |
Разные |
||
и верти- |
одношпин- |
многошпин- |
но- |
и коорди- |
Расточные |
тально- |
|||
кально- |
натно- |
расточные |
сверлильные |
||||||
сверлильные |
дельные |
дельные |
расточные |
сверлильные |
|
|
сверлильные |
|
|
|
|
|
|
||||||
Круглошли- |
|
|
|
|
|
|
|
|
|
Внутришли- |
|
Специали- |
|
|
|
Притироч- |
|
||
фовальные, |
фовальные, |
Обдирочно- |
Продольно- |
|
Плоско- |
ные, поли- |
Разные аб- |
||
зированные |
Заточные |
||||||||
бесцентро- |
координат- |
шлифоваль- |
шлифоваль- |
шлифоваль- |
шлифоваль- |
ровальные, |
разивные |
||
вошлифо- |
но-шлифо- |
ные |
ные |
ные |
|
ные |
хонинго- |
|
|
вальные |
вальные |
|
|
|
|
вальные |
|
||
|
|
|
|
|
|
||||
|
Светолуче- |
|
Электрохи- |
Электроис- |
|
Электроэро- |
Анодно- |
|
|
– |
– |
– |
зионные, |
механиче- |
– |
||||
вые |
мические |
кровые |
ультразву- |
ские отрез- |
|||||
|
|
|
|
|
|
ковые |
ные |
|
|
Зубодол- |
|
Зубофрезер- |
|
|
|
Зубоотде- |
|
|
|
Зуборезные |
ные для об- |
Для нареза- |
Для обра- |
|
Зубо- и |
Разные зубо- |
|||
бежные для |
работки ци- |
Резьбо- |
лочные, |
||||||
обработки |
для обра- |
линдриче- |
ния червяч- |
ботки тор- |
провероч- |
резьбо- |
и резьбооб- |
||
цилиндри- |
ботки кони- |
ских колес и |
ных колес |
цов зубьев |
фрезерные |
ные и об- |
шлифоваль- |
рабатываю- |
|
ческих колес |
ческих колес |
шлицевых |
|
колес |
|
катные |
ные |
щие |
|
|
|
валов |
|
|
|
|
|
|
|
Вертикаль- |
Фрезерные |
Продольные |
Копиро- |
Вертикаль- |
Продольные |
Консольно- |
Горизон- |
Разные фре- |
|
но- |
вальные и |
но- |
фрезерные |
тально- |
|||||
фрезерные, |
непрерывно- |
одностоеч- |
гравиро- |
фрезерные |
двухстоеч- |
операцион- |
фрезерные |
зерные |
|
консольные |
го действия |
ные |
вальные |
бесконсоль- |
ные |
ные |
консольные |
|
|
|
|
|
|
ные |
|
|
|
|
|
Продольные |
Поперечно- |
Долбежные |
Протяжные |
– |
Протяжные |
– |
Разные |
||
одностоеч- |
двухстоеч- |
горизон- |
вертикаль- |
||||||
строгальные |
строгальные |
||||||||
ные |
ные |
|
|
тальные |
|
ные |
|
|
|
|
|
|
|
|
|
|
|
|
|
Отрезные, оснащенные |
|
|
Отрезные с |
|
|
|
|||
токарным |
шлифоваль- |
гладким или |
Правильно- |
Ленточно- |
дисковой |
Отрезные |
– |
– |
|
резцом |
ным кругом |
насеченным |
отрезные |
пильные |
пилой |
ножовочные |
|
|
|
|
|
диском |
|
|
|
|
|
|
|
Муфто- и |
|
Правильно- |
|
Для испыта- |
|
|
|
|
|
Пилонасека- |
и бесцен- |
– |
Делитель- |
Балансиро- |
– |
– |
|||
трубообра- |
ния инстру- |
||||||||
батывающие |
тельные |
трово- |
|
ментов |
ные машины |
вочные |
|
|
|
|
|
обдирочные |
|
|
|
|
|
|
7
8
2. ТОЧНОСТЬ СТАНКОВ И КАЧЕСТВО ОБРАБОТКИ
Качество обработки на станке непосредственно связано с его точностью, которая характеризует степень влияния различных погрешностей станка на точность изготовляемых деталей. К основным погрешностям станка относят:
геометрические – зависят от точности изготовления деталей и сборки станка, а также его износа в процессе эксплуатации. Эти погрешности влияют на точность взаимного расположения режущего инструмента и заготовки в процессе формообразования;
кинематические – определяются ошибками в передаточных числах различных передач кинематической цепи, возникающими вследствие погрешностей отдельных элементов станка (зубчатых колес, червяков, винтовых пар и др.);
упругие – связаны с деформациями станка, которые вызывают отклонение взаимного расположения инструмента и заготовки под действием сил резания и характеризуются жесткостью станка, т.е. его способностью сопротивляться образованию деформации;
температурные – возникают главным образом вследствие неравномерного нагрева различных элементов станка в процессе его работы (что приводит к изменению начальной геометрической точности) и оказывают существенное влияние на качество обработки деталей, особенно высокоточных;
динамические – связаны с относительными колебаниями инструмента и заготовки. Они ухудшают качество обработки, могут снижать стойкость режущего инструмента и долговечность станка.
Кроме указанных погрешностей станка, на качество обработки значительное влияние оказывает погрешность режущего инструмента (его изготовления и установки на станке), а также износ режущей части в процессе эксплуатации.
3. ОРГАНИЗАЦИЯ РАБОЧЕГО МЕСТА СТАНОЧНИКА
Рабочим местом станочника называется участок производственной площади цеха, на котором расположен станок с комплектом приспособлений, вспомогательного и режущего инструмента, технической документации и других предметов и материалов, находящихся непосредственно в распоряжении рабочего.
9
Рабочее место является основным звеном любой производственной структуры, где производят механическую обработку на станках, поэтому очень важно, чтобы оно было рационально организовано. Под организацией рабочего места понимают упорядоченное расположение станка (станков при многостаночном обслуживании), организационной оснастки (инструментальных шкафов, подносов и лотков для инструментов, стеллажей для станочных приспособлений, планшетов и рамок для технической документации и др.) и других устройств, которые обеспечивают станочнику необходимые условия для высокопроизводительной и безопасной работы.
Рациональная организация рабочего места включает в себя его планировку, оснащение и обслуживание.
Под планировкой понимают наиболее целесообразное размещение на производственной площади рабочего и станочного оборудования, материалов, подъемно-транспортных средств и организационной оснастки. При планировании рабочего места в первую очередь необходимо учитывать рабочее положение станочника, а также величину и характер рабочих усилий (статических, динамических), объем и темп выполняемых движений, степень точности операций и т.п. При производстве подавляющего большинства станочных работ характерной рабочей позой является поза стоя, так как она обеспечивает наилучшие условия для обзора, возможность развития больших усилий и движений с большим размахом. Рациональная рабочая поза стоя обеспечивается при сохранении вертикального положения туловища или наклоне его вперед на 10 – 15°.
Оснащение рабочего места включает технические средства, необходимые для производства определенных видов работ и их контроля (станки, подъемно-транспортные устройства, технологическую и организационную оснастку, измерительные приспособления), а также средства для обеспечения комфорта на рабочем месте (соответствующее освещение, средства связи, ограничение уровня шума и вибраций, эстетические мероприятия и другие средства обеспечения безопасности труда).
Оснащение любого рабочего места включает технологическую и организационную оснастку. Под технологической оснасткой понимают средства, обеспечивающие выполнение технологического процесса в заданных параметрах. Это – станочные приспособления, режущий, вспомогательный и измерительный инструменты.
Организационная оснастка – средства, обеспечивающие размещение и хранение технологической оснастки, а также облегчающие