
991
.pdf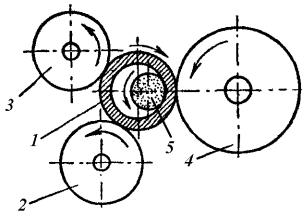
50
правлении, но с разными скоростями. Трение между ведущим кругом и заготовкой больше, чем между ней и рабочим кругом. Вследствие этого заготовка увлекается во вращение со скоростью, близкой к окружной скорости ведущего круга.
|
|
|
|
|
|
|
|
|
|
Перед шлифованием веду- |
|
|
|
|
|
|
|
|
|
|
|
|
|
|
|
|
|
|
|
|
|
щий круг устанавливают на- |
|
|
|
|
|
|
|
|
|
|
клонно под углом 1...7 0 к оси |
|
|
|
|
|
|
|
|
|
|
вращения заготовки. Вектор |
|
|
|
|
|
|
|
|
|
|
скорости этого круга разлагается |
3 |
|
|
|
|
|
|
|
|||
|
|
|
|
|
|
|
на составляющие, и возникает |
|||
|
|
|
|
|
|
|
|
|
|
|
|
|
1 |
|
|
|
|
|
|
продольная подача SПР. Поэтому |
|
|
|
|
|
5 |
|
|
|
|||
|
|
|
|
|
|
|
4 |
|
заготовка перемещается по ножу |
|
|
|
|
|
|
||||||
|
|
|
|
|
|
|
||||
|
|
|
|
|
|
|
|
|
|
вдоль своей оси и может быть |
|
2 |
|
|
|
|
|
|
|
||
|
|
|
|
|
|
|
|
прошлифована на всю длину. |
||
|
|
|
|
Рис. 31. Схема бесцентрового |
Чем больше угол наклона веду- |
|||||
|
|
|
|
щего круга, тем больше подача |
||||||
|
|
|
|
|
внутреннего шлифования |
SПР. Процесс легко автоматизи- |
||||
|
|
|
|
|
|
|
|
|
|
ровать, установив наклонный лоток, по которому заготовки будут сползать на нож, проходить процесс шлифования и падать в тару.
• Аналогичный принцип работы используют при бесцентровом внутреннем шлифовании для обработки цилиндрических и конических отверстий в заготовках, имеющих наружную цилиндрическую поверхность (рис. 31). Заготовку 1 устанавливают по наружной поверхности между тремя вращающимися элементами: опорным роликом 2, прижимным роликом 3 и ведущим барабаном 4. Шлифующий круг 5 располагают в отверстии консольно, он движется возвратнопоступательно вдоль оси отверстия.
13.2. Режимы резания
Основные элементы режима резания при шлифовании – скорость резания VК, круговая подача заготовки при круглом шлифовании SКР (продольная подача стола с заготовкой при плоском шлифовании SПР) и глубина резания t. Для рационального ведения процесса шлифования необходимо выбирать их оптимальные значения:
1.Характеристики шлифовального круга в зависимости от свойств обрабатываемого материала и технических требований.
2.Глубину резания t.

51
На черновых проходах t=0,05...0,1 мм; на чистовых проходах t=0,005...0,02 мм; при обработке неметаллов t=0,4...0,8 мм.
3.Круговую подачу заготовки SКР (скорость продольной подачи стола при плоском шлифовании SПР) выбирают в зависимости от ширины шлифовального круга и корректируют ее по кинематическим данным станка.
4.Скорость резания VК в зависимости от прочности круга. Она равна окружной скорости точки на периферии шлифовального круга:
VК = π D n , 1000
где n – частота вращения круга, об/мин; D – наружный диаметр шлифовального круга, мм. Обычно VК=30...50 м/с. При скоростном шлифовании VК>50 м/с.
Оптимальные значения элементов режима резания выбирают по справочным данным.
Проверка элементов режима резания по мощности электродвигателя станка:
1. Вычисляется тангенциальное усилие резания PZ. Это составляющая равнодействующей сил резания R, приложенной к шлифовальному кругу (рис. 32). PZ направлена по касательной к траектории движения периферийной точки круга.
Vк
Sпр
Px Sкр
Py
Pz
R
Рис. 32. Силы резания при шлифовании
52
PZ определяется по формуле
PZ=СP (SКР)а (SПР)b tc.
Значения коэффициента СP и показателей степени приводятся в справочниках.
2. По значению PZ определяется мощность электродвигателя привода шлифовального круга (кВт) с учетом КПД привода η:
NК= PZ VК /(1000 η).
Требования техники безопасности при шлифовании:
•Круги должны быть отбалансированы.
•Круги должны быть испытаны на прочность при окружной скорости 150 % от рабочей.
•Круг на станке должен быть защищен стальным кожухом на случай разрушения.
•Для защиты от разбрызгиваемой смазочно-охлаждающей жидкости устанавливают щитки.
•Обязательно наличие пылеулавливающих вентиляционных устройств.
К конструкциям деталей, обрабатываемых шлифованием, предъявляется ряд требований, обеспечивающих их технологичность. Технологичной является конструкция детали у которой:
– необрабатываемые и обрабатываемые поверхности детали, находящиеся в одной плоскости, разделены канавкой;
– предусмотрены центровые отверстия для ступенчатых валов и установочные фаски у пустотелых валов для их фиксации при обработке;
– предусмотрены технологические канавки для входа и выхода шлифовального круга;
– обрабатываемые поверхности должны располагаться в одной плоскости;
– все плоские обрабатываемые поверхности в конструкции должны располагаться параллельно или перпендикулярно базовой поверхности детали.
Шлифованием обрабатываются только жесткие детали, не деформирующиеся в процессе обработки. Способ не допускает обработки малых отверстий.
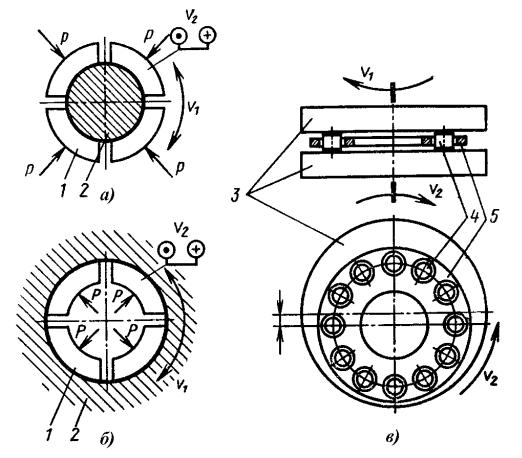
53
14. ОСНОВНЫЕ СВЕДЕНИЯ О ПРОЦЕССЕ ПРИТИРКИ
Притирка относится к отделочным методам обработки поверхностей.
Сущность метода притирки: на поверхность инструмента (т. н. притира), копирующего форму обрабатываемой поверхности, наносится мелкозернистый абразивный материал вместе со смазкой (абразивная паста). Паста или порошок внедряется в поверхность притира и удерживается ею. При относительном движении притира и заготовки абразивные зерна на поверхности притира снимают стружку малой толщины с поверхности заготовки.
Требования, предъявляемые к инструменту: а) высокая точность изготовления (т. к. он копирует форму обрабатываемой поверхности); б) материал притира должен быть мягче обрабатываемого материала заготовки (используют серый чугун, бронзу, красную медь, дерево).
Состав притирочной пасты: а) абразивный материал (электрокорунд, карбид кремния, карбид бора, оксид хрома и др.); б) материал смазки (масло, керосин, вазелин); в) химически активные вещества (олеиновая, стеариновая и другие кислоты).
|
|
|
|
|
|
|
|
|
|
|
|
v2 |
|
|
|
|
|
|
|
|
|
|||||
|
|
|
p |
|
|
p |
|
|
|
|
|
|
|
|
|
|
|
|
|
|
|
|
|
|||
|
|
|
|
|
|
|
|
|
|
|
|
|
|
|
|
|
|
|
|
|
|
|
|
|
||
|
|
|
|
|
|
|
|
|
|
|
|
|
|
|
|
|
|
|
|
|
|
|
|
|
|
|
|
|
|
|
|
|
|
|
|
|
|
|
|
|
|
|
|
|
|
|
v1 |
|
|
||||
|
|
|
|
|
|
|
|
|
|
|
|
|
|
|
|
|
|
|
|
|
|
|
|
|
|
|
|
|
|
|
|
|
|
|
|
|
|
|
|
v1 |
|
|
|
|
|
|
|
|
|||||
|
|
|
|
|
|
|
|
|
|
|
|
|
|
|
|
|
|
|
|
|
|
|||||
p |
|
|
|
|
|
|
|
|
|
|
|
|
|
|
|
|
|
|
|
|||||||
|
|
|
|
|
p |
|
|
|
|
|
|
|
|
|||||||||||||
|
|
|
|
|
|
|
|
|
|
|
|
|
|
|
|
|
|
|
|
|
|
v2 |
|
|
|
|
|
|
|
|
|
|
|
|
|
|
|
|
|
|
|
|
|
|
|
|
|
||||||
|
|
|
|
|
|
|
|
|
|
|
|
|
|
|
|
|
|
|
|
|
||||||
1 2 |
|
|
|
|
|
|
|
|
|
|
|
|
|
|
|
|
||||||||||
|
|
|
а) |
3 |
|
|
||||||||||||||||||||
|
|
|
|
|
|
|
|
|
|
|
|
|
|
|
|
|
|
|
|
|||||||
|
|
|
|
|
|
|
|
|
|
|
|
|
|
|
|
|
|
|
|
|
|
|
|
|
|
|
|
|
|
|
|
|
|
|
|
|
|
|
|
|
|
|
|
|
|
||||||||
|
|
|
|
|
|
|
|
|
|
|
|
|
|
|
|
|
|
|
4 |
5 |
||||||
|
|
|
|
|
|
|
|
|
|
|
|
|
|
|
|
|
|
|
||||||||
|
|
|
|
|
|
|
|
|
|
|
|
v2 |
|
|
|
|
|
|
|
|
|
|
|
|||
|
|
|
|
|
|
|
|
|
|
|
|
|
|
|
|
|
|
|
|
|
e
|
|
|
|
|
|
|
|
|
|
|
v2 |
|
|
|
|
|
|
|
v1 |
|
|
||
|
|
|
|
|
|
|
|
|
|
|
|
|
|
|
|
|
|
|
|
|
|
|
|
1 |
|
|
|
|
|
в) |
|
|
|||
2 |
|
б) |
|
|
|
|
|
|
|||
|
|
|
|
|
|
|
|
|
|
|
|
|
|
|
|
|
Рис. 33. Схемы притирки поверхностей |
54
Требование к относительному движению притира и заготовки: необходимо, чтобы траектория движения каждого абразивного зерна притира не повторялась (это дает наилучшие результаты по шероховатости). Для выполнения данного условия необходимо совместить несколько простых движений притира относительно заготовки, например возвратно-поступательное и возвратно-вращательное движения.
Схема притирки наружной цилиндрической поверхности приведена на рис. 33, а. Притир 1 представляет собой втулку с прорезями, которые необходимы для полного его прилегания под действием сил Р к обрабатываемой заготовке 2 по мере ее обработки. Притиру сообщают возвратно-поступательное движение V2 и одно временно воз- вратно-вращательное движение V1. Аналогичные движения осуществляются при притирке отверстий (рис. 33, б), однако притир должен равномерно разжиматься под действием сил Р. Приведенные схемы осуществляются вручную и на металлорежущих станках.
Плоские поверхности притирают также вручную или на специальных доводочных станках (рис. 33, в). Заготовки 4 располагаются между двумя чугунными дисками 3 в окнах сепаратора 5. Дискипритиры имеют плоские торцовые поверхности и вращаются в противоположных направлениях с разными частотами вращения. Сепаратор относительно дисков расположен эксцентрично на величину е. Поэтому при вращении дисков притираемые детали совершают сложные движения со скольжением и металл снимается одновременно с их параллельных торцов.
Глубина припуска на притирку составляет 0,01...0,05 мм.
15. ОСНОВНЫЕ СВЕДЕНИЯ О ПРОЦЕССЕ ХОНИНГОВАНИЯ
Хонингование – метод отделочной обработки цилиндрических отверстий.
Инструмент называется хоном. Это особая державка, на которой закреплены мелкозернистые абразивные бруски.
Бруски совершают вращательное V1 и одновременно возвратнопоступательное V2 движения вдоль оси обрабатываемого цилиндрического отверстия высотой h (рис. 34, а).
При сочетании движений на обрабатываемой поверхности появляется сетка микроскопических винтовых царапин – следов перемещения абразивных зерен. На рис. 34, б приведены развертка внутрен-
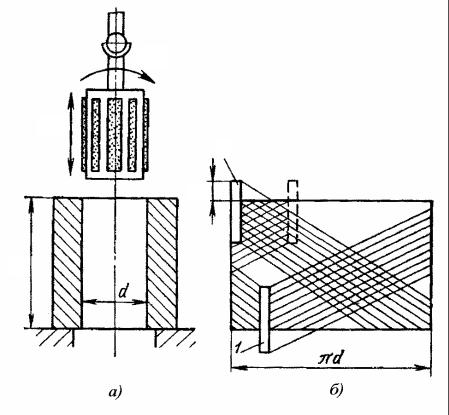
55
ней цилиндрической поверхности заготовки и схема образования сетки.
v1
v2
2
n
h
|
d |
|
|
|
|
|
|
|
|
|
|
|
|
|
|||
1 |
|
|
|
|
||||
|
|
|
πd |
|||||
|
|
|
||||||
|
|
|
|
|
|
|
|
|
|
а) |
б) |
||||||
|
|
|
|
|
|
|
|
|
Рис. 34. Схема хонингования отверстия
Такой профиль может быть необходим для удержания смазочного материала при работе машины (например, двигателя внутреннего сгорания) на поверхности ее деталей.
Крайние нижнее 1 и верхнее 2 положения абразивных брусков устанавливают так, что создается перебег n (см. рис. 34, б). Он необходим для того, чтобы образующие отверстия получались прямолинейными даже при неравномерном износе брусков.
Абразивные бруски всегда контактируют с обрабатываемой поверхностью, так как раздвигаются в радиальном направлении механически (пружинами), гидравлически или пневматически. Давление брусков на обрабатываемую поверхность контролируется. В зону обработки обильно подается смазочно-охлаждающая жидкость (керосин, веретенное масло).
Хонингование по сравнению с внутренним шлифованием имеет преимущества: отсутствует упругий отжим инструмента, реже наблюдается вибрация, резание происходит более плавно.
Хонингованием исправляют погрешности формы отверстия: отклонение от круглости, цилиндричности. Погрешность взаимного
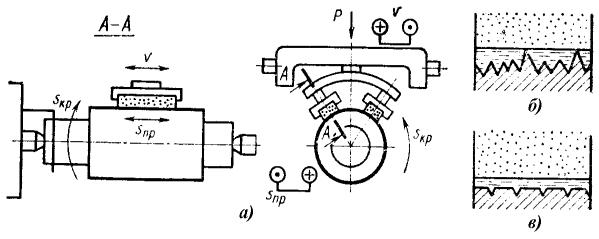
56
расположения оси отверстия относительно торца детали (например, неперпендикулярность) хонингованием исправить невозможно, так как режущий инструмент самоустанавливается по отверстию.
В последние годы для хонингования стали широко применяться алмазные бруски (синтетические), стойкость которых в десятки и сотни раз выше стойкости обычных абразивных брусков. Припуск на обработку при хонинговании составляет 0,01...0,2 мм.
16. ОСНОВНЫЕ СВЕДЕНИЯ О ПРОЦЕССЕ СУПЕРФИНИШИРОВАНИЯ
Это процесс сверхтонкой абразивной обработки наружных и внутренних цилиндрических и конических поверхностей, а также плоскостей колеблющимися брусками.
Суперфинишем в основном уменьшают шероховатость поверхности, оставшуюся от предыдущей обработки. При этом изменяются глубина и вид микронеровностей, обрабатываемые поверхности получают сетчатый рельеф. Поверхность становится чрезвычайно гладкой, что обеспечивает более благоприятные условия взаимодействия трущихся поверхностей.
Поверхности обрабатывают абразивными брусками, устанавливаемыми в специальной головке. Для суперфиниша характерно колебательное движение брусков наряду с движением заготовки. Процесс резания происходит при давлении брусков (0,5...3) 105 Па и в присутствии смазочного материала малой вязкости.
|
|
|
|
|
|
|
|
|
|
|
|
|
|
|
|
v |
|
|
|
||
|
|
|
|
|
|
|
|
|
|
|
|
|
|
P |
|
|
|
||||
|
|
|
А–А |
|
|
|
|
||||||||||||||
|
|
|
|
|
|
|
|
|
|
|
|
|
|
||||||||
|
|
|
|
|
|
|
|
|
|
|
|
|
|
|
|
|
|
|
|
|
|
|
|
|
|
|
|
|
|
|
|
|
|
|
|
|
|
||||||
|
|
|
|
v |
|
|
|
|
|
|
|||||||||||
|
|
|
|
|
|
|
|
|
А |
|
|
|
|
|
|
|
|
|
|
|
|
|
|
|
|
|
|
|
|
|
|
|
|
|
|
|
|
|
|
|
|
|
|
|
Sкр |
|
|
|
|
|
|
|
|
|
|
|
|
|
|
|
|
|
|
||
|
|
|
|
|
|
|
|
|
|
|
|
|
|
|
|
б) |
|||||
|
|
|
|
|
|
|
|
|
|
|
|
|
|
|
|
|
|
|
|||
|
|
|
|
|
|
|
|
|
|
|
|
|
|
|
|
|
|
|
|
|
|
|
|
|
|
|
|
|
|
|
|
|
|
А |
|
|
|
|
Sкр |
|
|
|
|
|
|
|
|
|
|
|
|
|
|
|
|
|
|
|
|
|
|||||
|
|
|
|
|
|
|
|
Sпр |
|
|
|
|
|
|
|||||||
|
|
|
|
|
|
|
а) |
|
|
|
|
|
|
||||||||
|
|
|
|
|
|
|
|
|
|
|
в) |
|
|||||||||
|
|
|
|
|
|
|
|
|
|
|
|
|
|||||||||
|
|
|
|
|
|
|
|
|
|
|
|
|
|
|
|
|
|
|
|
|
|
|
|
|
|
|
|
|
|
|
|
|
|
|
|
|
|
|
|
|
|
|
|
|
|
|
|
|
|
|
|
|
|
|
|
|
|
|
|
|
|
|
|
|
|
Рис. 35. Отделка суперфинишированием
57
Схема обработки наружной цилиндрической поверхности приведена на рис. 35, а. Плотная сетка микронеровностей создается сочетанием трех движений: вращательного SКР заготовки, возвратнопоступательного SПР и колебательного брусков со скоростью V. Амплитуда колебаний брусков составляет 1,5...6 мм, а частота 400...1200 колебаний в минуту. Движение V ускоряет процесс съема металла и улучшает однородность поверхности. Бруски, будучи подпружиненными, самоустанавливаются по обрабатываемой поверхности.
Процесс характеризуется сравнительно малыми скоростями резания (5...7 м/мин).
Важную роль играет смазочно-охлаждающая жидкость. Масляная пленка покрывает обрабатываемую поверхность, но наиболее крупные микровыступы (рис. 35, б) прорывают ее и в первую очередь срезаются абразивом. Давление брусков на выступы оказывается большим. По мере дальнейшей обработки давление снижается, так как все большее число выступов прорывает масляную пленку. Наконец, наступает такой момент (рис. 35, в), когда давление бруска не может разорвать пленку, она становится сплошной. Создаются условия для жидкостного трения. Процесс отделки автоматически прекращается. В качестве жидкости используют смесь керосина (80...90 %) с веретенным или турбинным маслом (20...10 %).
При суперфинишировании погрешности формы поверхности, полученные на предшествующей обработке (волнистость, конусность, овальность), не исправляются, хотя могут быть значительно уменьшены.
17. ОСНОВНЫЕ СВЕДЕНИЯ О ПРОЦЕССЕ ПОЛИРОВАНИЯ
Полированием уменьшают шероховатость поверхности. Этим методом получают зеркальный блеск на ответственных частях деталей (дорожки качения подшипников) либо на деталях, применяемых для декоративных целей (облицовочные части автомобилей). Для этого используют полировальные пасты или абразивные зерна, смешанные со смазочным материалом. Эти материалы наносят на быстровращающиеся эластичные (например, фетровые) круги или колеблющиеся щетки. Хорошие результаты дает полирование быстродвижущимися бесконечными абразивными лентами (шкурками).
В зоне полирования одновременно протекают следующие основные процессы: а) тонкое резание; б) пластическое деформирова-
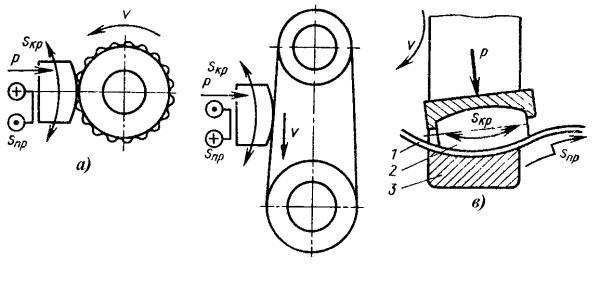
58
ние поверхностного слоя; в) химические реакции – воздействие на металл химически активных веществ, находящихся в полировальном материале.
|
|
|
|
|
|
|
|
|
|
v |
|
|
|
|
|
|
|
|
|
|
|
|
|
|
|
|
|
|
|
|
|
|
|
|
|
|
|
|
|
|
|
|
|
|
|
|
|
|
|
|
|
|
|
|
|
|
|
|
|
|
|
|
|
|
|
|
|
|
|
Sкр |
|
|
|
|
|
|
|
|
|
|
|
|
|
|
|
|
|
|
|
|
|
|
|
|
|
|
|
|
|||
|
|
|
|
|
|
|
|
|
|
|
|
|
|
|
|
|
|
|
|
|
|
|
v |
|
|
|
|
|
|
||||
|
|
|
|
|
|
|
|
|
|
|
|
|
|
|
|
|
|
|
|
|
|
|
|
|
|
P |
|
|
|
||||
|
P |
|
|
|
|
|
|
|
|
|
|
|
|
|
|
|
|
|
|
|
|
|
|
|
|
|
|
|
|
|
|||
|
|
|
|
|
|
|
|
|
|
|
|
|
|
|
|
|
|
|
|
|
|
|
|
|
|
||||||||
|
|
|
|
А–А |
|
|
|
|
|
|
|
|
|
|
|
|
|
|
|
|
|
|
|
|
|||||||||
|
|
|
|
|
|
|
|
|
|
|
Sкр |
|
|
|
|
|
|
|
|
|
|
|
|||||||||||
|
|
|
|
|
|
|
|
|
|
|
|
|
|
|
|
|
|
|
|
|
|
|
|
|
|
||||||||
|
|
|
|
|
|
|
|
|
|
|
|
|
|
|
|
|
|
|
|
|
|
|
|
|
|
||||||||
|
|
|
|
|
|
|
|
|
|
|
|
|
|
|
|
|
|
|
|
|
|
|
|
||||||||||
|
|
|
|
|
|
|
|
|
|
|
|
P |
|
|
|
|
|
|
|
|
|
|
|
|
|
|
|
|
|
||||
|
|
|
|
|
|
|
|
|
|
|
|
|
|
|
|
|
|
|
|
|
|
|
|
|
|
|
|
|
|
|
|
||
|
|
|
|
|
|
|
|
|
|
|
|
|
|
|
|
|
|
|
|
|
|
|
|
|
|
|
|
|
|
|
|
|
|
|
|
|
|
|
|
|
|
|
|
|
|
|
|
|
|
|
|
А |
|
|
|
|
|
|
|
|
|
|
|
|
|||
|
|
|
|
|
|
|
|
|
|
|
|
|
|
|
|
|
|
|
|
|
|
|
|
|
|
|
|
Sкр |
|
|
|
||
|
|
|
|
|
|
|
|
|
|
|
|
|
|
|
|
|
|
|
|
|
v |
|
|
|
|
|
|
|
|
||||
|
|
|
|
|
|
|
|
|
|
|
|
|
|
|
|
|
|
|
|
|
|
|
|
|
|
|
|
||||||
|
|
|
|
|
|
|
|
|
|
|
|
|
|
|
|
|
|
|
|
|
|
|
|
|
|
|
|
|
|
|
|||
Sпр |
|
|
|
|
|
|
|
|
|
|
|
|
|
|
|
|
|
|
|
|
|
|
|
|
|
|
|||||||
|
|
|
|
|
|
|
|
|
|
|
|
|
|
|
|
|
|
|
|
|
|
|
|
|
|
|
|
|
|
||||
|
|
|
|
|
|
|
|
|
|
|
|
|
|
|
|
|
|
|
|
|
1 |
|
|
|
|
|
|
|
|
||||
|
|
|
|
|
|
|
|
|
|
|
|
|
|
|
|
|
|
|
|
|
|
|
|
|
|
|
|
Sпр |
|||||
|
|
|
|
|
|
|
|
|
Sпр |
|
|
|
|
|
|
|
|
|
|
|
|
|
|
|
|
||||||||
|
|
|
|
|
|
|
а) |
|
|
|
|
|
|
|
|
|
|
|
|
|
|
|
|
|
|
|
|
||||||
|
|
|
|
|
|
|
|
|
|
|
|
|
|
|
|
|
|
|
|
|
|
||||||||||||
|
|
|
|
|
|
|
|
|
|
|
|
|
|
|
|
|
|
|
|||||||||||||||
|
|
|
|
|
|
|
|
|
|
|
|
|
|
|
|
|
|
|
|
А |
|
|
|
2 |
|
|
|
|
|
|
|
|
|
|
|
|
|
|
|
|
|
|
|
|
|
|
|
|
|
|
|
|
|
|
|
|
|
|
|
|
|
|
|||||
|
|
|
|
|
|
|
|
|
|
|
|
|
|
|
|
|
|
|
|
|
|
|
|
|
|
|
|
|
|
|
|
|
|
|
|
|
|
|
|
|
|
|
|
|
|
|
|
|
|
|
|
|
|
|
|
|
3 |
|
|
|
|
|
|
|
|
||
|
|
|
|
|
|
|
|
|
|
|
|
|
|
|
|
|
|
|
|
|
|
|
|
|
|
|
|
|
|
||||
|
|
|
|
|
|
|
|
|
|
|
|
|
|
|
|
|
|
|
|
|
|
|
|
|
в) |
|
|
||||||
|
|
|
|
|
|
|
|
|
|
|
|
|
|
|
|
|
|
|
|
|
|
|
|
|
|
|
|
|
|
|
|||
|
|
|
|
|
|
|
|
|
|
|
|
|
|
|
|
|
|
|
|
|
|
|
|
|
|
|
|
|
|
|
|
|
|
б)
Рис. 36. Схемы полирования
При полировании абразивной шкуркой положительную роль играет подвижность ее режущих зерен. Эта особенность шкурок приводит к тому, что зернами в процессе обработки не могут наноситься микроследы, существенно различные по глубине.
В качестве абразивного материала применяют порошки из электрокорунда и оксиды железа при полировании стали, карбида кремния и оксиды железа при полировании чугуна, оксиды хрома и наждака при полировании алюминия и сплавов меди. Порошок смешивают со смазочным материалом, который состоит из смеси воска, сала, парафина и керосина. Полировальные круги изготовляют из войлока, фетра, кожи, капрона, спрессованной ткани и других материалов.
Процесс полирования проводят на больших скоростях (до 50 м/с). Заготовка поджимается к кругу усилием Р (рис. 36, а) и совершает движения подачи SПР и SКР в соответствии с профилем обрабатываемой поверхности. Полирование лентами (рис. 36, б) имеет ряд преимуществ. Эластичная лента может огибать всю шлифуемую поверхность. Поэтому движения подачи могут отсутствовать.
Главное движение при полировании иногда совершает и заготовка 3 (рис. 36, в), имеющая, например, форму кольца с фасонной внутренней поверхностью. Абразивная лента 1 поджимается полировальником 2 к обрабатываемой поверхности и периодически перемещается (движение SПР).
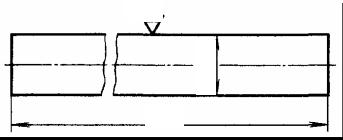
59
Полирование возможно в автоматическом или полуавтоматическом режиме. Заготовки, закрепленные на конвейере, непрерывно перемещаются относительно круга или ленты. Съем деталей происходит на ходу конвейера.
В процессе полирования не удается исправлять погрешности формы, а также местные дефекты предыдущей обработки.
18. ПРИМЕРЫ ЗАДАНИЙ ПО МЕХАНИЧЕСКОЙ ОБРАБОТКЕ
Задание № 1
Требуется выполнить в жестких центрах черновое и чистовое обтачивания заготовки Ø36 мм из стального проката и получить цилиндрическую поверхность у гладкого вала Ø30–0,12 мм. Заготовка подрезана в размер 250 мм и зацентрована.
1. Изобразить вал, нанести размеры, отклонение от размера Ø30 мм и знак шероховатости цилиндрической поверхности (рис. 37).
Rz40
Ø30–0,12
250
Рис. 37. Гладкий вал после чернового
ичистового обтачиваний
2.Подготовить предписания токарю на обработку вала.
3.Занумеровать в этих предписаниях установы и технологические переходы в порядке их выполнения (в предписаниях поставить диаметры, длины и характер обработки поверхностей).
Задание № 2
Требуется обточить в центрах (начерно) зацентрованную заготовку Ø46 мм и длиной 154 мм и получить вал с двухсторонней ступенчатостью (рис. 38).