
991
.pdf20
ции. На операциях окончательной обработки припуск составляет не более 0,5 мм. На промежуточных операциях припуск на обработку изменяется в пределах 0,5…5 мм. На операциях предварительной обработки заготовок в зависимости от их размеров и способа изготовления припуск может быть более 5 мм.
Припуск менее 7 мм может быть, например, срезан за один проход резца. В этом случае глубина резания равна припуску на обработку. При превышении некоторых критических значений глубины резания могут возникнуть вибрации станка, приспособления, инструмента, заготовки. Поэтому припуск более 7 мм срезают за два или несколько проходов. Причем глубина резания при каждом проходе может быть одинаковой или ее последовательно уменьшают.
Значение подачи S, как и глубины резания, определяется видом технологической операции. Операции окончательной обработки ведут с подачами на оборот SO<0,1 мм/об. При операциях промежуточного формообразования подачу назначают в пределах SO=0,1…0,4 мм/об. Для сокращения времени операции предварительной обработки стремятся вести с подачами SO=0,4…0,7 мм/об. На тяжелых станках обработку можно вести с глубиной резания до 30 мм и с подачей до
1,5 мм/об.
Предварительное значение скорости резания V вычисляют по формуле, которая приводится в справочниках по режимам резания, при известных глубине резания t и выбранном интервале подач S.
Твердость заготовки НВ устанавливают по технической документации, сопровождающей партию заготовок, поступающих на обработку.
Стойкость инструмента характеризуется периодом стойкости Т, т.е. временем работы инструмента между переточками. Его назначают согласно рекомендациям справочных материалов в зависимости от характера выполняемой операции и инструментального материала. При этом берут некоторый интервал значений периода стойкости. Например, для твердосплавных резцов при выполнении операций промежуточного формообразования можно принять период стойкости в пределах Т=30…45 мин.
По формуле вычисляют два значения скорости резания: большие – для меньших значений подачи S и периода стойкости Т и меньшие – для больших их значений. По найденным значениям скорости резания V, м/мин, для заданного диаметра D, мм, обрабатываемой заготовки по формуле n=1000V / πD, об/мин, рассчитывают два значения частоты вращения шпинделя – наибольшее и наименьшее.
21
Таким образом, определяют интервал значений частоты вращения шпинделя, в пределах которого можно выбрать определенное значение, обеспечиваемое кинематикой станка.
Если на предварительном этапе устанавливают некоторый интервал значений параметров резания, в пределах которого достигается заданная точность и качество обрабатываемой детали, то следующим этапом является выбор фактических (рабочих) значений основных параметров режимов резания.
Глубина резания (рабочая), как правило, равна полуразности диаметров обрабатываемой и обработанной деталей (при точении).
Рабочую подачу выбирают из числа имеющихся в коробке подач станка, причем это значение должно находиться в пределах интервала предварительно выбранных значений подач.
Рабочая частота вращения шпинделя берется из числа значений, обеспечиваемых коробкой скоростей станка, и должна находиться в интервале частот для меньшей и большей скоростей.
По установленным рабочим значениям основных параметров режимов резания – глубине резания t, подаче S и частоте вращения шпинделя n – проводят дальнейший расчет остальных рабочих режимов и соответствующих технико-экономических показателей.
Рабочая скорость резания V, м/мин, когда известна выбранная частота вращения шпинделя n, об/мин, может быть рассчитана по формуле V=10–3πDn.
Формулы для расчета рабочих значений периода стойкости инструмента, силы резания, момента вращения на шпинделе станка (в кН·м) и эффективной мощности, затрачиваемой на обработку заготовки резанием, приводятся в справочниках режимов резания металлов. Далее на примере конкретных операций точения, фрезерования, сверления и т.д. будет рассмотрен выбор режимов резания с применением справочных данных и паспорта станка.
9. ОСНОВНЫЕ СВЕДЕНИЯ О ПРОЦЕССЕ ТОЧЕНИЯ
Точение является главным способом обработки поверхностей тел вращения.
Процесс резания осуществляется на токарных станках при вращении обрабатываемой заготовки (главное движение, обозначается символом V) и перемещении резца (движение подачи, обозначается символом S).
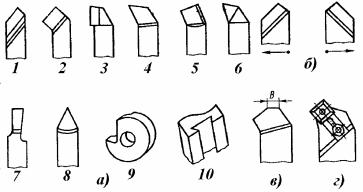
22
9.1.Токарные резцы
Вкачестве режущего инструмента при точении используются токарные резцы.
|
|
|
|
|
|
|
б) |
1 |
2 |
3 |
4 |
5 |
6 |
||
|
|
|
|
|
|
|
|
|
|
|
|
|
9 |
10 |
|
|
|
|
7 |
8 |
|
|
|
|
|||||
|
а) |
|
в) |
г) |
||||||
|
|
|
|
|
|
|
|
|
|
|
|
|
|
|
|
|
|
|
|
|
|
Рис. 5. Токарные резцы
По технологическому назначению различают резцы (рис. 5, а): проходные 1 – 3 для обтачивания наружных цилиндрических и конических поверхностей; подрезные 4 для обтачивания плоских торцовых поверхностей; расточные 5 и 6 для растачивания сквозных и глухих отверстий; отрезные 7 для разрезания заготовок; резьбовые для нарезания наружных 8 и внутренних резьб; фасонные круглые 9 и призматические 10 для обтачивания фасонных поверхностей; прорезные для обтачивания кольцевых канавок и др.
По характеру обработки различают резцы черновые, получистовые и чистовые. По форме рабочей части резцы (рис. 5, а) делят на прямые 1, отогнутые 2, оттянутые 7. По направлению подачи резцы подразделяют на правые и левые (рис. 5, б). Правые работают с подачей справа налево, левые – слева направо. По способу изготовления различают резцы целые, с приваренной встык рабочей частью, с приваренной или припаянной пластинкой инструментального материала, со сменными пластинками режущего материала.
Для высокопроизводительного точения с большими подачами используют резцы с дополнительной режущей кромкой (рис. 5, в).
В промышленности применяют резцы с многогранными неперетачиваемыми твердосплавными пластинками (рис. 5, г). Когда одна из режущих кромок выходит из строя вследствие затупления, открепляют механический прижим пластинки и устанавливают в рабочее положение следующую кромку.

|
|
|
|
23 |
|
|
|
|
|
|
|
Токарный |
прямой |
проходной |
резец |
|
|
|
|
|
|||
|
|
|
|
|
|||||||
(рис. 6) имеет головку – рабочую часть I и |
|
|
|
|
|||||||
|
|
II |
|||||||||
тело – стержень II, который служит для за- |
|
|
|
|
|
||||||
|
|
|
|
|
|||||||
крепления резца в резцедержателе. Головка |
|
|
|
|
|||||||
I |
|||||||||||
резца образуется при заточке и имеет |
|
|
|
|
|
||||||
|
|
|
|
|
|||||||
следующие |
|
элементы: |
переднюю |
|
|
|
|
|
|||
поверхность 1, по которой сходит стружка; |
|
|
|
|
|
||||||
главную |
заднюю |
поверхность |
2, |
|
|
|
|
|
|
||
обращенную |
к |
поверхности |
резания |
|
|
|
|
|
|
||
|
6 5 4 3 2 1 |
|
|||||||||
заготовки; |
вспомогательную |
заднюю |
|
|
|
|
|
|
|||
|
|
|
|
|
|
||||||
|
|
|
|
|
|||||||
поверхность 5, обращенную к обработанной |
Рис. 6. Элементы токарно- |
||||||||||
поверхности заготовки; главную режущую |
го прямого проходного |
||||||||||
кромку 3 и вспомогательную 6; вершину 4. |
|
|
резца |
||||||||
Инструмент затачивают по передней и |
|
|
|
|
|
||||||
задним поверхностям. |
|
|
|
|
|
|
|
|
|
9.2.Основные операции точения
Спомощью точения выполняют следующие основные опера-
ции:
1) обтачивание – обработка наружных цилиндрических и конических поверхностей (рис. 7, а). Выполняется прямыми, отогнутыми или упорными проходными резцами с продольной подачей;
|
|
|
|
|
|
v |
|
|
|
|
v |
|
|
|||
|
|
|
|
|
|
|
|
|
|
|
|
|
|
|
|
|
|
|
|
|
|
|
|
|
|
|
|
|
|
|
|
|
|
|
v |
|
|
|
|
|
|
|
|
|
|
|
||||
|
|
|
|
|
|
|
|
|
|
|
|
|
|
|
|
|
|
|
|
|
|
|
|
|
|
|
Sпр |
|
|
|
|
|
|
|
|
|
|
|
|
|
|
|
|
|
|
|
|
|
Sпр |
|
а) |
|
|
|
|||||||||||||
|
|
|
|
|
б) |
|||||||||||
|
|
|
|
|
|
в) |
||||||||||
|
|
|
|
|
|
|
|
|||||||||
|
|
Sпр |
|
|
|
|||||||||||
|
|
|
|
|
|
|
|
|
|
|
|
|||||
|
|
|
|
|
||||||||||||
|
|
|
|
|
|
|
|
|
|
|
||||||
|
|
|
|
|
|
|
|
|
|
|
|
|
|
|
|
|
|
|
|
v |
|
|
|
|
|
|
|
|
|
v |
|
|
|
v |
|
|
|
|
|
|
|
|
|
|
|
|
v |
|
|
|
|
|
|
|
|
|
|
|
|
|
|
|
|
|
|
|
|
|
|
|
|
|
|
|
|
|
|
|||||
|
|
|
|
|
|
|
|
|
|
|
|
|
|
|
|
|
|||||
|
|
|
|
|
|
|
|
|
|
|
|
|
|
|
|
|
|
|
|
|
|
|
|
|
|
|
|
|
|
|
|
|
|
|
|
|
|
|
|
|
|
ж) |
|
|
|
|
|
|
|
д) |
|
|
|
|
|
е) |
|
|
|
|
|
||||
г) |
|
|
|
|
|
|
|
|
|
|
|
|
|
||||||||
|
|
|
|
|
|
Sпр= Sн.р |
|
|
|
|
|
|
|
|
|||||||
|
|
|
|
|
|
|
|
|
|
|
|
|
|
|
|||||||
|
|
|
|
|
|
|
|
|
|||||||||||||
|
|
|
|
|
|
|
|
|
|
|
|
|
|
||||||||
|
|
|
Sп |
|
|
|
|
|
|
|
|
|
|
|
|
|
|
||||
|
|
|
|
|
|
|
|
|
|
|
|
|
Sп |
|
|
|
|
|
|||
|
|
|
|
|
|
|
|
|
|
|
|
|
|
|
|
Sп |
|
||||
|
|
|
|
|
|
|
|
|
|
|
|
|
|
|
|
|
|
||||
|
|
|
|
|
|
|
|
|
|
|
|
|
|
|
|
||||||
|
|
|
|
|
|
|
|
|
|
|
|
|
|
|
|
|
|
|
|
||
|
|
|
|
|
|
|
|
|
|
|
|
|
|
|
|
|
|
|
|
|
|
Рис. 7. Схемы обработки заготовок точением
24
2) растачивание – обработка внутренних поверхностей (рис. 7, б, в). Выполняется расточными резцами, закрепленными в резцедержателе станка, с продольной подачей. Гладкие сквозные отверстия растачивают проходными резцами (см. рис. 7, б), ступенчатые и глухие отверстия – упорными расточными резцами (см. рис. 7, в);
3)подрезание – обработка торцевых поверхностей (рис. 7, г). Выполняется перед обтачиванием наружных поверхностей. Торцы подрезают подрезными резцами с поперечной подачей к центру или от центра заготовки. При подрезании от центра к периферии поверхность торца получается менее шероховатой;
4)резьбонарезание – нарезание резьбы (рис. 7, д). Резьбу наре-
зают с продольной подачей резца SПР. Форма режущих кромок резьбовых резцов определяется профилем и размерами поперечного сечения нарезаемых резьб;
5)резка – разрезание заготовок на части (рис. 7, е, ж). Выполняется отрезными резцами с поперечной подачей. При отрезке детали резцом с прямой главной режущей кромкой (см. рис. 7, е) разрушается образующаяся шейка и приходится дополнительно подрезать торец готовой детали. При отрезке детали резцом с наклонной режущей кромкой (см. рис. 7, ж) торец получается чистым.
Кроме того, к токарным операциям относятся протачивание канавок и обтачивание фасонных поверхностей заготовок фасонными резцами или с помощью фасонных копиров.
9.3. Режимы резания
Основные задачи резания – обеспечить наибольшую производительность и требуемое качество поверхности детали при наименьшей себестоимости обработки. Таким образом, необходимо найти такие режимы резания, при которых сочетание всех факторов, влияющих на стоимость обработки, обеспечит наивыгоднейшие условия обработки конкретной заготовки. Такие режимы называют оптимальными.
Обязательные элементы режима резания при любом виде лез-
вийной обработки следующие: глубина резания t, скорость резания V, скорость подачи S.
Рассмотрим элементы режима резания при точении (рис. 8).
1. Глубина резания t (мм) – толщина слоя материала, срезаемая за один рабочий ход резца.
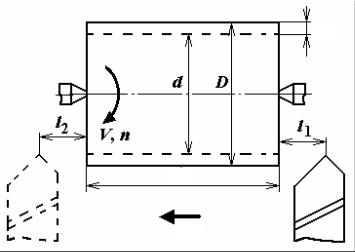
25
t
|
|
|
|
d |
|
D |
|
|
|
|
|
|
|
|
|
|
|
l2 |
|
|
|
|
|
|
|
|
|
|
|
|
|
|
|
l1 |
|
|
V, n |
|
|
|
|
|
||
|
|
|
|
|||||
|
|
|
|
|
|
|
|
l
S
Рис. 8. Эскиз операции продольного точения цилиндра
Это расстояние между обрабатываемой и обработанной поверхностями заготовки, измеренное перпендикулярно к последней. При точении цилиндрической поверхности глубина резания равна полуразности диаметров до и после обработки (см. рис. 8): t=(D–d)/2. При подрезке канавок и отрезке глубина резания равна ширине отрезного резца. Рекомендуется глубину резания назначать равной расчетному максимально возможному значению, способствующему получению поверхности требуемой формы и качества.
2. Скорость резания V (м/мин) – расстояние, пройденное точкой режущей кромки инструмента относительно заготовки в единицу времени.
Наибольшей скоростью при токарной обработке будет обладать точка с наибольшим радиусом цилиндрической или фасонной поверхности (на периферии заготовки). При частоте вращения заготовки n (об/мин) скорость резания будет равна V=πD n / 1000, где D – диаметр обрабатываемой поверхности, мм (см. рис. 8).
Скорость резания при точении |
назначается по эмпирической |
|||
(выведенной экспериментально) зависимости |
||||
V = C |
1 |
|
K . |
|
t x S y T m |
||||
|
|
Значения коэффициентов С, К и показателей степени x, y, m выбираются по таблицам из справочников (например, технологамашиностроителя) в зависимости от конкретных условий резания: вида обработки (черновая либо чистовая), материала инструмента и заготовки, глубины резания t, геометрии инструмента, применения сма- зочно-охлаждающей жидкости и т. д.
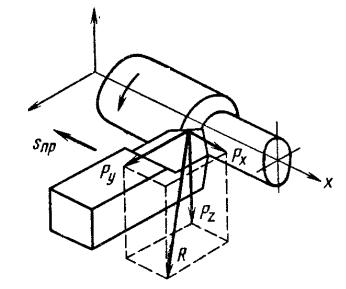
26
В формулу входят также подача резца за один оборот заготовки S (мм/об) и стойкость резца T (мин). Стойкость резца T – это время его непрерывной работы до затупления, после чего резец необходимо перетачивать или заменять. Стойкость зависит в основном от вида инструментального материала.
3. Подача S (мм/об) – при точении это путь точки режущей кромки инструмента относительно заготовки в направлении движения подачи за один оборот заготовки.
Назначается подача также по справочникам в зависимости от глубины резания и других условий резания. Обычно при точении
S=(0,05...0,25) t.
Проверка элементов режима резания по мощности электродвигателя станка
Выполняется проверка в следующей последовательности:
1. Вычисляется тангенциальная (вертикальная) составляющая усилия резания PZ, которая действует на резец в направлении движения резания (рис. 9).
Если обозначить символом R равнодействующую всех сил, действующих на резец (см. рис. 9), то PZ – главная составляющая силы резания, совпадающая по направлению со скоростью главного движения резания в вершине резца (тангенциальная); PX – осевая составляющая силы резания, параллельная оси X главного вращательного движения резания; PY – радиальная составляющая силы резания, направленная по радиусу главного вращательного движения резания в вершине резца перпендикулярно к оси заготовки.
Z
0
v
Y
Sпр |
|
|
|
|
|
|
|
|
|
|
|
|
|
|
|
|
|
Px |
|||
|
|
|
|
|
|
|
|
|
|
|
|
|
Py |
|
|
|
|
|
|
|
|
|
|
|
|
|
|
|
|
|||
|
|
|
|
|
|
X |
||||
|
|
|
|
|
|
|
|
|
|
|
|
|
|
|
|
|
|
|
|||
|
|
|
|
|
|
Pz |
||||
|
|
|
|
|
|
|
|
|
|
|
|
|
|
|
R |
Рис. 9. Разложение равнодействующей сил резания на составляющие
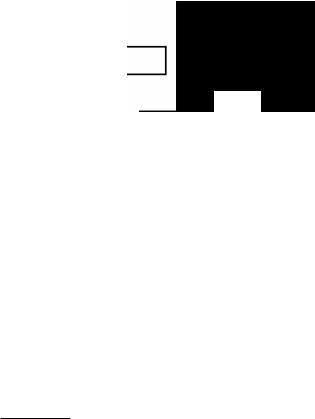
27
Наибольшее значение из всех трех компонентов имеет тангенциальная сила PZ, по которой могут быть определены крутящий момент на шпинделе станка и эффективная мощность резания (мощность, необходимая для осуществления процесса резания).
Компонент PZ можно считать совпадающим по направлению с вектором скорости главного движения резания в вершине резца V
(рис. 10).
Силу Pz (Н) определяют по эмпирической формуле
PZ = CP t x S y V n K P ,
где CP – коэффициент, учитывающий физикомеханические свойства материала обрабаты-
ваемой заготовки; KP – коэффициент, учитывающий факторы, не вошедшие в формулу (углы резца, материал резца и т. д.). Значения коэффициентов KP, CP и показателей степеней x, y, n даны в справочниках для конкретных условий обработки.
2. Определяется эффективная мощность резания NE (кВт). Это мощность, необходимая для вращения заготовки (она расходуется на деформирование и срезание с заготовки слоя металла). При точении цилиндрической поверхности
P V N E = 60Z1000 .
3. Должно выполняться условие
NЭЛ ≥ N E η,
где NЭЛ – мощность электродвигателя станка; η – КПД механизмов и передач станка.
Мощность электродвигателя станка должна быть больше или равна эффективной мощности резания с учетом потерь в приводе (КПД можно принять равным η=0,75).
Если данное условие не выполняется, необходимо снизить число оборотов и скорость, подачу и глубину резания либо вести обработку на более мощном станке.

28
9.4. Нормирование токарной операции
Производительность обработки Q при резании определяется числом деталей, изготовляемых в единицу времени:
Q=1/TШТ,
где TШТ – время изготовления одной детали.
TШТ = TO+ TИН+ TВСП,
где TO – основное (технологическое) время обработки, время, которое тратится непосредственно на обработку заготовки; TИН – время подвода и отвода инструмента при обработке одной детали; TВСП – вспомогательное время установки и настройки инструмента.
Таким образом, производительность обработки резанием в первую очередь определяется основным временем TO.
При токарной обработке основное технологическое время TO определяется по формуле
TO = nLS i ,
где i – число рабочих ходов резца, необходимое для снятия материала, оставленного на обработку; L – расчетная длина обработки за один проход; n – число оборотов заготовки; S – подача резца за один оборот заготовки.
Расчетная длина обработки будет равна (см. рис. 8):
L=l+l1+l2,
где l – длина обрабатываемой поверхности заготовки; l1 – длина врезки, l1 =t (ctg ϕ) + (1...3) мм; l2 – длина выхода резца (перебег), l2 = (1...3) мм.
Наибольшая производительность будет при обработке с максимальной глубиной резания, максимальной подачей и максимальной скоростью резания. Однако при увеличении производительности снижается качество поверхности и повышается износ инструмента. Поэтому при обработке резанием решается задача по установлению максимально допустимой производительности при сохранении требуемого качества поверхности и стойкости инструмента.
К конструкциям деталей, обрабатываемых точением, предъявляется ряд требований, обеспечивающих их технологичность при обработке. Технологичной является конструкция детали, если:
–масса ее уравновешена относительно оси вращения;
–отсутствуют нежесткие валы и втулки;
–в чертеже детали используются одинаковые радиусы скругле-
ний;
29
–режущий инструмент имеет свободный вход и выход из материала заготовки;
–отсутствуют фасонные поверхности, требующие изготовления фасонных резцов;
–диаметры ступеней ступенчатых валов располагаются по возрастающей степени;
–участки вала или отверстия, имеющие один и тот же размер, но разный допуск, разделены кольцевой разделительной канавкой.
10.ОСНОВНЫЕ СВЕДЕНИЯ О ПРОЦЕССЕ СВЕРЛЕНИЯ
Сверление – распространенный метод получения отверстий в сплошном материале.
Сверлением получают сквозные и несквозные (глухие) отверстия и обрабатывают предварительно полученные отверстия в целях увеличения их размеров, повышения точности и снижения шероховатости поверхности.
Сверление осуществляют при сочетании вращательного движения инструмента вокруг оси – главного движения и поступательного его движения вдоль оси – движения подачи. Оба движения на сверлильном станке сообщают инструменту.
Процесс резания при сверлении протекает в более сложных условиях, чем при точении. В процессе резания затруднены отвод стружки и подвод охлаждающей жидкости к режущим кромкам инструмента. При отводе стружки происходит трение ее о поверхность канавок сверла и сверла о поверхность отверстия. В результате повышаются деформация стружки и тепловыделение. На увеличение деформации стружки влияет изменение скорости резания вдоль режущей кромки от максимального значения на периферии сверла до нулевого значения у центра.
10.1. Режущий инструмент
Отверстия на сверлильных станках обрабатывают сверлами, зен-
керами, развертками и метчиками.
1. Сверла по конструкции и назначению подразделяют на спиральные, центровочные и специальные. Наиболее распространенный