
991
.pdf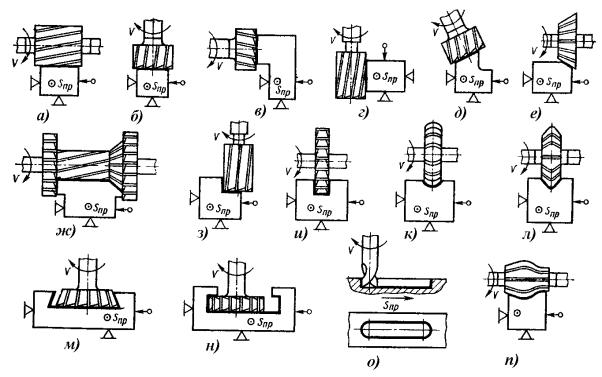
40
2.Вертикальные плоскости фрезеруют на горизонтальнофрезерных станках торцовыми фрезами (рис. 22, в) и торцовыми фрезерными головками, а на вертикально-фрезерных станках – концевыми фрезами (рис. 22, г).
3.Наклонные плоскости и скосы фрезеруют торцовыми (рис. 22,
д) и концевыми фрезами на вертикально-фрезерных станках, у которых фрезерная головка со шпинделем поворачивается в вертикальной плоскости. Скосы фрезеруют на горизонтально-фрезерном станке одноугловой фрезой (рис. 22, е).
4.Комбинированные поверхности фрезеруют набором фрез
(рис. 22, ж) на горизонтально-фрезерных станках. Точность взаиморасположения обработанных поверхностей зависит от жесткости крепления фрез по длине оправки. С этой целью применяют дополнительные опоры (подвески), избегают использования несоразмерных по диаметру фрез (рекомендуемое отношение диаметра фрез не более
1,5).
5.Уступы и прямоугольные пазы фрезеруют концевыми (рис. 22, з) и дисковыми (рис. 22, и) фрезами на вертикально- и горизон- тально-фрезерных станках. Уступы и пазы целесообразнее фрезеровать дисковыми фрезами, так как они имеют большее число зубьев и допускают работу с большими скоростями резания.
|
|
|
|
в) |
|
г) |
|
|
|
|
|
|
|
|
|
|
|
д) |
|||||
|
|
|
|
|
|
|
е) |
||||
а) |
|||||||||||
|
б) |
||||||||||
|
|
|
|||||||||
|
|
|
|
|
|||||||
|
|
|
|
|
|
|
|||||
|
|
|
|
|
|
|
|
|
|||
|
|
|
|
|
|
|
|
|
|
|
ж) |
|
з) |
|
|
|
|
|
|
|
|
|
и) |
|
|
|||||
|
|
|
к) |
||||||
|
|
|
|
л) |
|||||
|
|||||||||
|
|
|
|
|
|
|
|
|
|
|
|
|
|
|
|
|
|
|
м) |
|
н) |
|
|
|
|
|
|
|
|
п) |
||
|
|
|
|
о) |
|
|
|
|
|
||||
|
|
|
|
|
|
|
|
Рис. 22. Схемы обработки заготовок фрезерованием |
|
41
6.Фасонные пазы фрезеруют фасонной дисковой фрезой (рис. 22, к), угловые пазы – одноугловой и двухугловой (рис. 22, л) фрезами на горизонтально-фрезерных станках.
7.Паз клиновой фрезеруют на вертикально-фрезерном станке за два прохода: прямоугольный паз – концевой фрезой, затем скосы паза
–концевой одноугловой фрезой (рис. 22, м), Т-образные пазы (рис. 22, н), которые широко применяют в машиностроении как станочные пазы, например на столах фрезерных станков, фрезеруют обычно за два прохода: вначале паз прямоугольного профиля концевой фрезой, затем нижнюю часть паза – фрезой для Т-образных пазов.
8.Шпоночные пазы фрезеруют концевыми или шпоночными (рис. 22, о) фрезами на вертикально-фрезерных станках. Точность получения шпоночного паза – важное условие при фрезеровании, так как от нее зависит характер посадки на шпонку сопрягаемых с валом деталей. Фрезерование шпоночной фрезой обеспечивает получение более точного паза, при переточке по торцовым зубьям диаметр шпоночной фрезы практически не изменяется.
9.Фасонные поверхности незамкнутого контура с криволинейной образующей и прямолинейной направляющей фрезеруют на горизонтально- и вертикально-фрезерных станках фасонными фрезами соответствующего профиля (рис. 22, п).
Применение фасонных фрез эффективно при обработке узких и длинных фасонных поверхностей. Широкие профили обрабатывают набором фасонных фрез.
11.3.Режимы резания
Крежиму резания при фрезеровании относят скорость резания V, подачу S, глубину резания t, ширину фрезерования B.
Глубина резания t (мм). При фрезеровании это толщина слоя металла, измеренная перпендикулярно к обрабатываемой поверхности. Глубина резания t равна припуску либо части припуска на фрезерование. Припуск выгодно снимать за один проход, если позволяет мощность станка. Обычно t=2...6 мм. Если требуется высокая точность обработки, то фрезерование может проводиться в два прохода – черновой и чистовой. Для чистовых проходов обычно t=0,75...2 мм. Глубина резания t показана на рис. 19.
Подача S. При фрезеровании используются три размерности по-
дачи:
42
а) минутная подача SМ (мм/мин). Это величина перемещения обрабатываемой заготовки относительно фрезы за 1 мин;
б) подача на один оборот фрезы SО= SМ/n (мм/об). Это величи-
на перемещения обрабатываемой заготовки относительно фрезы за время одного оборота фрезы;
в) подача на один зуб фрезы SZ= SО/z = SМ/(n.z) (мм/зуб), где z –
число зубьев фрезы. Это величина перемещения обрабатываемой заготовки относительно фрезы за время углового поворота фрезы на один зуб.
Подача на зуб характеризует интенсивность нагрузки зуба, а следовательно, стойкость фрезы. Чтобы уменьшить машинное время на фрезерование, применяют максимально возможную подачу на зуб фрезы. Величина подачи выбирается по справочным нормативам в зависимости от шероховатости обработанной поверхности, прочности материала и других условий резания.
Ширина фрезерования B (мм) – ширина обрабатываемой поверхности в направлении, параллельном оси фрезы. При увеличении ширины фрезерования B возрастают суммарная площадь поперечного сечения среза, работа резания и тепловыделение. В результате снижается допускаемая скорость резания и возрастает износ фрезы. Ширина фрезерования B показана на рис. 19.
Скорость резания V (м/мин). При фрезеровании это окружная скорость вращения фрезы. Скорость резания связана с диаметром фрезы и частотой ее вращения зависимостью
V=πD n/1000,
где D – наружный диаметр фрезы, мм; n – частота вращения фрезы, об/мин.
Скорость резания при фрезеровании назначается по эмпирической зависимости
V = C |
Dq |
|
K , |
|
t x SZy T m |
Bu z p |
|||
|
|
где С – коэффициент, характеризующий конкретные условия обработки; К – общий поправочный коэффициент, учитывающий отличные от табличных условия резания; T – стойкость фрезы, мин; D – диаметр фрезы; z – число зубьев фрезы. Значения показателей степени x, y, m, u, p, q и коэффициентов приводятся в справочниках.
Влияние элементов резания на скорость резания
Подача на зуб фрезы SZ. При увеличении SZ растет толщина среза, работа деформации и трение, что приводит к снижению стойкости
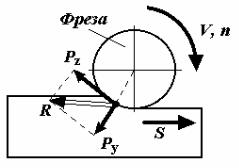
43
фрезы и допустимой скорости резания (скорость V необходимо уменьшить).
Глубина резания t. С увеличением глубины резания увеличиваются угол контакта и количество зубьев фрезы, находящихся одновременно в работе, количество выделяющегося тепла (скорость V необходимо уменьшить).
Диаметр фрезы D. При увеличении диаметра фрезы D уменьшается толщина среза и снижается нагрузка на режущие кромки фрезы. Стойкость фрезы повышается (скорость V можно увеличить).
С уменьшением числа зубьев z увеличивается масса каждого зуба. Это приводит к лучшему теплоотводу и повышает скорость резания (скорость V можно увеличить).
Проверка элементов режима резания по мощности электродвигателя станка:
1. Вычисляется тангенциальное усилие резания PZ. Это составляющая равнодействующей сил резания R, приложенной к фрезе (рис. 23). PZ направлена по касательной к траектории движения режущей кромки.
PZ определяется по формуле
|
|
P |
= |
10 CP t x SZy Bu z |
K |
P |
. |
|
|
|
|
|
|
||||||
|
|
|
|
|
|
||||||||||||||
|
|
Z |
|
|
Dq nw |
|
|
|
|
|
|
|
|
|
|
|
|
||
|
|
|
|
|
|
|
|
|
|
|
|
|
|
|
|
|
|
||
Значения коэффициентов и пока- |
|
|
|
|
|
|
|
|
|
|
|
|
|
||||||
|
|
|
|
|
|
|
|
|
|
|
|
|
|||||||
|
|
|
|
|
Фреза |
|
|
|
|
|
|||||||||
зателей |
степени |
приводятся |
в |
|
|
|
|
|
|
|
|
|
V, n |
||||||
|
|
|
|
|
|
|
|
|
|
|
|
||||||||
|
|
|
|
|
|
|
|
|
|
|
|
|
|||||||
справочниках. |
|
|
|
|
|
|
|
|
|
|
PZ |
|
|
|
|||||
|
|
|
|
|
|
|
|
|
|
|
|
||||||||
2. По значению PZ определяется |
|
|
|
|
|
|
|
|
|
|
|
|
|
||||||
эффективная мощность резания |
NE |
|
|
|
|
|
|
|
|
|
|
|
|||||||
|
R |
|
|
|
|
|
|
|
|
||||||||||
(кВт). |
|
|
|
|
|
|
|
|
|
|
|
|
|
|
|
|
S |
|
|
N E = |
PZ V |
. |
|
|
|
|
|
|
|
|
PY |
|
|
|
|||||
|
|
|
|
|
|
|
|
|
|
|
|
|
|||||||
|
|
|
|
|
|
|
|
|
|
|
|
|
|
|
|||||
|
|
|
|
|
|
|
|
|
|
|
|
|
|
|
|||||
|
|
|
|
|
|
|
|
|
|
|
|
|
|
|
|
||||
|
|
60 1000 |
|
|
Рис. 23. Силы резания при |
||||||||||||||
Это |
мощность, |
необходимая |
для |
|
|||||||||||||||
вращения фрезы. |
|
|
|
|
|
|
|
работе цилиндрической |
|||||||||||
|
электродвигателя |
|
|
прямозубой фрезой |
|
||||||||||||||
3. |
Мощность |
|
|
|
|
|
|
|
|
|
|
|
|
|
станка потребуется большего значения с учетом КПД механизмов станка:
NЭЛ > NE / η.

44
11.4. Нормирование операции фрезерования
Производительность обработки Q и время изготовления одной детали TШТ при фрезеровании определяются по тем же формулам, которые приводились выше для нормирования токарной операции.
Отличие состоит лишь в том, что основное технологическое время TO (время, которое тратится непосредственно на срезание припуска) при фрезеровании определяется зависимостью
TO = SL i ,
M
где i – число проходов; SМ – минутная подача заготовки; L – расчетная длина обработки за один проход,
L=l+l1+l2,
здесь l – длина обрабатываемой заготовки; l1 – длина врезки; l2 – длина выхода фрезы.
К конструкциям деталей, обрабатываемых фрезерованием, предъявляется ряд требований, обеспечивающих их технологичность при обработке. Технологичной является конструкция детали, у которой:
–обрабатываемые выступы имеют одинаковую высоту;
–обрабатываемые посадочные места под присоединяемые детали располагаются с наружной стороны корпуса;
–пазы открыты для ввода фрезы, иначе при обработке закрытых пазов потребуется засверливание отверстий для входа фрезы;
–форма пазов и прорезей позволяет вести обработку дисковыми, а не концевыми (торцевыми) фрезами.
12.ОСНОВНЫЕ СВЕДЕНИЯ О ПРОЦЕССЕ СТРОГАНИЯ
Строгание применяется при обработке плоских и фасонных линейчатых поверхностей и различных канавок в условиях единичного и мелкосерийного производства.
Главное движение V при строгании – возвратно-поступательное прямолинейное, а движение подачи S – шагообразное, направленное перпендикулярно главному движению (рис. 24). Обработку выполняют на строгальных станках. Инструмент – строгальные резцы, конструкция которых сходна с конструкцией токарных резцов.
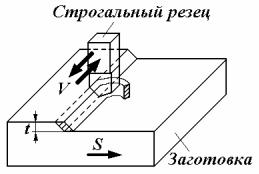
|
45 |
|
|
|
|
|
|
|
|
|
|
Процесс резания при строгании |
|
|
|
|
|
|
|
|
|
|
|
|
|
|
|
Строгальный резец |
|
||||||
имеет прерывистый характер, и сре- |
|
|
|
|
|
||||||
|
|
|
|
|
|
|
|
|
|
||
зание стружки происходит |
только |
|
|
|
|
|
|
|
|
|
|
при встречном относительном дви- |
|
|
|
|
|
|
|
|
|
|
|
жении резца и заготовки. Во время |
|
|
|
|
V |
|
|
|
|||
|
|
|
|
|
|||||||
обратного (вспомогательного) хода |
|
|
|
|
|
|
|
|
|
|
|
|
t |
|
|
|
|
|
|
|
|
||
резец работу не производит. |
Вреза- |
|
|
|
|
|
|
|
|||
|
|
|
S |
||||||||
|
|
|
|
|
|
|
|
||||
ние резца в заготовку в начале каж- |
|
|
|
|
|
|
|
|
Заготовка |
||
дого рабочего хода сопровождается |
|
|
|
|
|
|
|
|
|
|
ударом. За время холостого хода резец остывает, поэтому при строгании в большинстве случаев не при-
меняются смазочно-охлаждающие жидкости. Ударные нагрузки и циклический характер нагрева существенно снижают стойкость резцов в сравнении с непрерывным резанием, поэтому строгание производят при умеренных скоростях резания. Головки и державки строгальных резцов выполняют более массивными, чем у токарных.
При строгании параметрами режима резания, так же как и при точении, являются скорость резания V, подача S и глубина резания t.
При строгании технологичной является конструкция детали, у которой:
–форма поверхности представляет плоскость или сочетание плоскостей;
–обрабатываемые поверхности расположены в одной плоскости, что позволяет обрабатывать их за один проход;
–обрабатываемые поверхности заготовки расположены в параллельных плоскостях и имеют разделительные канавки для выхода резца;
–в углах пересечения обрабатываемых поверхностей предусмотрена разделительная канавка для выхода резца;
–пазы, обрабатываемые строганием, являются сквозными, обеспечивая свободный заход и выход резца.
13.ОСНОВНЫЕ СВЕДЕНИЯ О ПРОЦЕССЕ ШЛИФОВАНИЯ
Шлифование – процесс обработки заготовок деталей машин
резанием с помощью абразивных кругов.
Абразивные зерна расположены в шлифовальном круге беспорядочно и удерживаются связующим материалом. При вращательном движении круга в зоне его контакта с заготовкой часть зерен срезает
46
материал в виде очень большого числа тонких стружек (до 107 стружек в минуту). Шлифовальные круги срезают стружки на очень больших скоростях – от 30 до 80 м/с. При этом глубина резания составляет t=0,005...0,05 мм. Процесс резания каждым зерном осуществляется почти мгновенно.
Все большее применение находит силовое шлифование для обработки труднообрабатываемых резанием материалов. При силовом или врезном шлифовании глубина резания может достигать 10...12 мм.
Шлифование сопровождается выделением большого количества тепловой энергии (значительная часть абразивных зерен в шлифовальном круге расположена так, что не режет заготовку, а пластически деформирует ее с выделением тепла за счет трения). Это приводит к образованию на поверхности детали дефектного слоя. Поэтому в зону обработки при шлифовании обильно подается смазочноохлаждающая жидкость.
Обработанная поверхность представляет собой совокупность микроследов абразивных зерен и имеет малую шероховатость.
Шлифование применяют для чистовой и отделочной обработки деталей с высокой точностью. Для заготовок из закаленных сталей шлифование является одним из наиболее распространенных методов формообразования.
Эффективность шлифования оценивают по коэффициенту удельной производительности: q=VМ/VA, где VA – объем изношенного круга в единицу времени; VМ – объем снятого материала заготовки в единицу времени.
При обработке углеродистых сталей q= 50...80; быстрорежущих сталей q= 6...12; жаропрочных и тугоплавких сплавов q= 0,5...5.
13.1.Виды шлифования
Взависимости от формы обрабатываемой поверхности шлифование делится на следующие виды:
1. Плоское шлифование.
Применяется для шлифования плоских поверхностей, отсюда его название. Плоское шлифование может производиться периферией (рис. 25, а) или торцом круга (рис. 25, б).
Шлифование периферией круга менее производительно, чем шлифование торцом круга, но более точно.
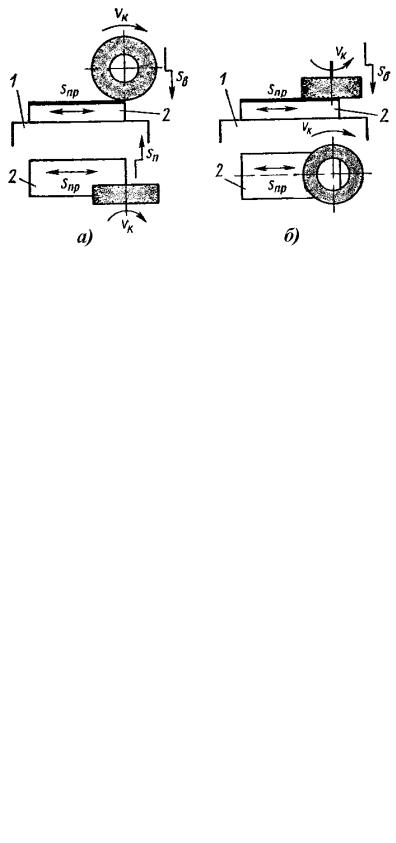
47
|
|
|
|
|
|
|
|
|
|
|
|
|
|
|
|
|
|
|
|
|
|
|
|
|
|
|
|
|
|
|
|
|
|
|
|
|
|
|
|
|
|
|
|
|
|
|
|
|
|
|
|
|
|
Vк |
|
|
|
|
|
|
|
|
|
|
|
|
|
|
|
|
|
|
|
|
|
|
|
|
|
|
|
|
|
|
Sв |
|
|
1 |
|
|
|
|
|
|
|
|
|
|
|
Sв |
|
|
1 |
|
|
|
|
|
|
|
|
|
|
||
|
|
|
Sпр |
|
|
|
|
|
|
|
|
|
|
|
Sпр |
|
|
|
|
|
||||||||
|
|
|
|
|
|
|
|
|
|
|
|
|
|
|
|
|
|
|
|
|||||||||
|
|
|
|
|
|
|
|
|
|
|
|
|
|
|
|
|
|
|
|
|
|
|
|
|||||
|
|
|
|
|
|
|
|
|
|
|
2 |
|
|
|
|
|
|
|
|
|
|
|
|
2 |
|
|||
|
|
|
|
|
|
|
|
|
|
|
|
|
|
|
|
|
|
|
|
|
|
|
Vк |
|
|
|
||
|
|
|
|
|
|
|
|
|
|
|
|
|
|
|
|
|
|
|
|
|
|
|
||||||
|
|
|
|
|
|
|
|
|
|
Sп |
|
|
|
|
|
|
|
|
|
|
|
|
|
|
|
|
||
|
|
|
|
|
|
|
|
2 |
|
|
|
|
|
|
|
|
|
|
|
|||||||||
|
2 |
|
|
|
|
|
|
|
|
|
|
|
|
|
|
|
|
|||||||||||
|
|
|
|
|
|
|
|
|
|
|
|
|
|
|
|
|
|
|
|
|
|
|
|
|
|
|
||
|
|
|
Sпр |
|
|
|
|
|
|
|
|
|
|
|
|
|
|
Sпр |
|
|
|
|
|
|
||||
|
|
|
|
|
|
|
|
|
|
|
|
|
|
|
|
|
|
|
|
|
|
|
||||||
|
|
|
|
|
|
|
|
|
|
|
|
|
|
|
|
|
|
|
|
|
|
|
|
|||||
|
|
|
|
|
|
|
|
|
|
|
|
|
|
|
|
|
|
|
|
|
|
|||||||
|
|
|
|
|
|
|
|
Vк |
|
|
|
|
б) |
|
|
|
|
|
||||||||||
|
|
|
|
|
а) |
|
|
|
||||||||||||||||||||
|
|
|
|
|
|
|
|
|
|
|
|
|
|
|
|
|||||||||||||
|
|
|
|
|
|
|
|
|
|
|
|
|
|
|
|
|
|
|
|
|
|
|
|
|
|
|
|
|
|
|
|
|
|
|
|
|
|
|
|
|
|
|
|
|
|
|
|
|
|
|
|
|
|
|
|
|
|
Рис. 25. Схемы обработки заготовок плоским шлифованием: а – периферией круга; б – торцом круга
При шлифовании торцом круга одновременно в работе участвует большее число абразивных зерен, чем при шлифовании периферией круга. Но шлифование периферией круга с использованием прямоугольных столов позволяет выполнить большее число разнообразных видов работ.
Главным движением резания VК (м/с) для всех технологических способов шлифовальной обработки является вращение круга. Прямолинейное поступательное движение подачи при плоском шлифовании совершает заготовка вместе со столом станка. Последовательность подач при плоском шлифовании – продольная SПР (м/мин), затем поперечная SП (мм/дв. ход), затем вертикальная SВ.
|
|
|
|
|
|
|
|
|
|
|
|
|
|
|
|
|
|
|
|
|
|
|
|
|
|
|
|
|
|
Sп |
|
|
|
|
|
|
|
|
|
|
|
||||
|
|
|
|
|
|
|
|
|
|
|
|
|
|
|
Vк |
|
|
|
|
|
|
|
|
|
|
|
|
|
|
|
|
|
|
|
|
|
|
|
Sв |
|
|
|
|||
|
|
|
|
|
Sв |
|
|
|
Vк |
1 |
|
|
|
|
|
|
|
|
||||
|
|
|
|
|
|
|
|
|
|
|
|
|
|
|
|
|
||||||
|
|
|
|
|
|
|
|
|
|
|
|
|
|
|
|
|
|
|
|
|||
|
|
|
|
|
|
|
|
|
|
|
|
|
|
|
|
|
|
Sкр |
||||
|
|
|
Sкр |
|
|
|
|
|
|
|
|
|
|
|
|
|
|
|||||
|
|
|
|
|
|
|
|
|
|
|
|
|
|
|
|
|
||||||
|
|
|
|
|
|
|
|
|
|
|
|
|
|
|
|
|
|
|
|
|
|
|
|
|
|
|
|
|
|
|
Sп |
|
|
|
|
|
|
|
|
|
|
|
|||
|
|
|
|
|
|
|
Vк |
|
|
|
|
|
|
|
|
|||||||
|
|
|
|
|
|
|
|
|
|
|
|
|
|
Sкр |
||||||||
|
|
|
|
|
|
|
|
|
|
|
|
|
|
|
|
|
|
|||||
|
|
|
|
|
|
|
|
|
|
|
|
|
Sпр |
|
|
|||||||
Sкр |
|
|
|
|
|
|
|
|
Vк |
|
|
|
|
|
|
|
|
|||||
|
|
|
|
|
|
|
|
|
|
|
|
|
|
|
|
|
|
|||||
|
|
|
|
|
|
|
|
|
|
|
|
|
|
|
|
|
|
|
|
|
|
|
|
1 |
2 |
|
|
|
|
|
|
|
|
1 |
2 |
|
|
|
|
|
|
||||
а) |
|
|
|
|
|
б) |
||||||||||||||||
|
|
|
|
|
|
|
|
|
|
|
|
|
|
|
|
|
|
|
||||
|
|
|
|
|
|
|
|
|
|
|
|
|
|
|
|
|
|
|
|
|
|
|
|
|
|
|
|
|
|
|
|
|
|
|
|
|
|
|
|
|
|
|
|
|
|
Рис. 26. Схемы непрерывной обработки заготовок на плоскошлифовальных станках с круглым столом:
а – периферией круга; б – торцом круга

48
Поперечная подача SП необходима в тех случаях, когда ширина круга меньше ширины заготовки (см. рис. 25, а). Движение SП происходит прерывисто (периодически) при крайних положениях заготовки в конце продольного хода.
Периодически происходит и подача SВ на глубину резания. Это перемещение осуществляется также в крайних положениях заготовки, но в конце поперечного хода.
Небольшие детали шлифуют на высокопроизводительных шлифовальныхстанкахнепрерывногодействияскруглымстолом(рис. 26).
Vк 2. Круглое шлифование.
Применяется для шлифования
Sп
Sкр
Sпр
t
цилиндрических и конических поверх-
ностей вращения, отсюда его название. Круглое шлифование делится на следующие подвиды: наружное, внутреннее, внутреннее планетарное, бесцентровое наружное и бесцентровое внутреннее.
Рассмотрим схемы круглого шлифования.
Рис. 27. Схема круглого |
• При круглом наружном шли- |
|
фовании (рис. 27) обрабатывается на- |
||
наружного шлифования |
||
ружная цилиндрическая поверх- |
||
|
ность. Продольная подача SПР происходит за счет возвратнопоступательного перемещения заготовки. Подача SПР (мм/об. заг) равна осевому перемещению заготовки за один ее оборот. Вращение за-
|
|
|
|
|
|
|
|
|
|
|
|
|
|
|
|
|
готовки |
является |
круго- |
|
|
|
|
A–A |
|
|
|
|
|
|
|
|
|||||||||
|
|
|
|
|
|
|
|
|
|
вой подачей SКР (м/мин). |
||||||||||
|
|
(Повернуто) |
|
|
|
|
|
|
||||||||||||
|
|
|
|
|
|
|
|
|
|
|
|
|
|
|
|
|
Подача |
SП |
(мм/дв. |
|
|
|
|
|
|
|
|
|
|
|
|
|
|
|
|
|
|
||||
|
|
|
|
|
|
|
|
|
|
|
|
|
Sкр |
|
|
|||||
|
|
|
|
|
|
|
|
|
|
|
|
|
|
|
|
ход или мм/ход) на глу- |
||||
|
|
|
|
|
|
|
|
|
|
|
|
|
|
|
|
|
||||
|
|
|
|
|
|
|
|
|
|
|
|
|
|
|
|
|
бину резания для приве- |
|||
|
|
|
|
|
|
|
|
A |
|
|
|
|
|
|
A |
|
||||
|
|
|
|
|
|
|
|
|
|
|
|
|
|
денной схемы обработки |
||||||
|
|
|
|
|
|
|
|
|
|
|
|
|
|
|
|
|
||||
t |
|
|
|
|
|
|
|
|
|
|
|
|
|
|
|
происходит при крайних |
||||
|
|
|
|
|
|
|
|
|
|
|
Vк |
|
|
|
|
|
|
|
|
|
|
|
|
|
|
|
|
|
Sп |
|
|
|
|
|
|
положениях заготовки. |
|||||
|
|
|
|
|
|
|
|
|
|
|
|
|
|
|
||||||
|
|
|
|
|
|
|
|
|
|
|
|
|
|
|
|
|
||||
|
|
|
|
|
|
|
|
|
|
|
|
|
|
|
|
|
• |
При |
|
круглом |
|
|
|
|
|
|
|
|
|
|
|
|
|
|
|
внутреннем шлифовании |
|||||
|
|
|
|
Sпр |
|
|
|
|
|
|||||||||||
|
|
|
|
|
|
|
|
|
|
|
|
|
|
|
|
|
(рис. 28) характер дви- |
|||
|
|
|
|
|
|
|
|
|
|
|
|
|
|
|
|
|||||
|
|
Рис. 28. Схема круглого внутреннего |
|
|
|
жений инструмента и за- |
||||||||||||||
|
|
|
|
|
|
|
шлифования |
|
|
|
|
|
|
готовки |
и |
последова- |
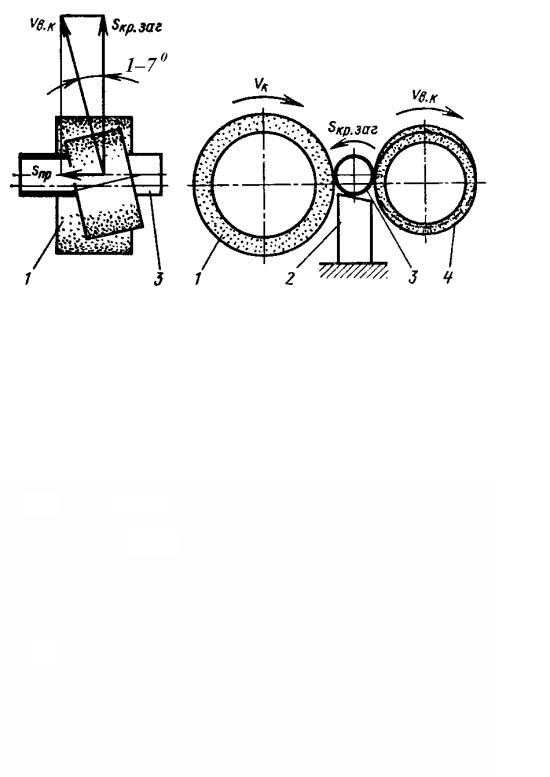
49
тельность подач те же, что и при круглом наружном шлифовании, только обрабатывается внутренняя цилиндрическая поверхность.
• Внутреннее планетарное шли- |
|
|
|
|
|
|
|
|
|
|
|||
|
|
|
|
|
|
|
|
|
|
||||
|
|
|
Sп |
|
|
|
|
|
|||||
фование (рис. 29) применяют при об- |
|
|
|
|
|
|
|
|
|||||
|
|
|
|
|
|
|
|
|
|
||||
работке заготовок больших размеров и |
|
|
|
|
|
|
|
|
|
|
|||
|
|
|
|
|
Vк |
|
|
|
|
||||
массы, |
которые шлифовать описан- |
|
|
|
|
|
|
|
|
||||
|
|
|
|
|
|
|
|
|
|
||||
ными выше |
способами нерациональ- |
|
|
|
|
|
|
|
|
|
|
||
|
Sпр |
|
|
|
|
|
|
|
|
||||
но. Заготовку закрепляют |
на столе |
|
|
|
|
|
|
|
Sпл |
|
|||
|
|
|
|
|
|
|
|
|
|||||
|
|
|
|
|
|
|
|
|
|||||
станка |
неподвижно. Шлифовальный |
|
|
|
|
|
|
|
|
|
|
||
|
|
|
|
|
|
|
|
|
|
||||
круг вращается не только вокруг сво- |
|
|
|
|
|
|
|
|
|
|
|||
ей оси, но также вокруг оси отверстия |
|
|
|
|
|
|
|
|
|
|
|||
заготовки (планетарная подача SПЛ), |
|
|
|
|
|
|
|
|
|
|
|||
что аналогично круговой подаче заго- |
|
|
|
|
|
|
|
|
|
|
|||
товки при обычном внутреннем шли- |
|
|
|
|
|
|
|
|
|
|
|||
|
|
|
|
|
|
|
|
|
|
||||
фовании (положение круга, совер- |
Рис. 29. Схема внутреннего |
|
|
||||||||||
шившего |
в |
планетарном |
движении |
|
|
||||||||
пол-оборота, |
показано на |
рис. 29 |
планетарного шлифования |
|
|
||||||||
|
|
|
|
|
|
|
|
|
|
штриховой линией).
• Бесцентровое наружное шлифование (рис. 30) наружных ци-
линдрических поверхностей производится в незакрепленном состоянии обрабатываемых заготовок, и для них не требуется центровых отверстий. Поэтому данный способ шлифования характеризуется высокой производительностью.
Vв.к Sкр.заг
1–7°
Vк |
|
|
|
|
|
|
|
Vв.к |
|
|
|
|
|
|
|
|
|
|
|
|
|
Sкр.заг |
Sпр
|
|
3 |
|
|
|
2 |
|
3 |
|
4 |
1 |
1 |
|||||||||
|
|
|
|
|
|
|
|
|
|
|
|
|
|
|
|
|
|
|
|
|
|
|
|
|
|
|
|
|
|
|
|
|
Рис. 30. Схема бесцентрового наружного шлифования
Заготовку 3 (см. рис. 30) устанавливают на нож 2 между двумя кругами – рабочим 1 и ведущим 4. Эти круги вращаются в одном на-