
Mechanical Properties of Ceramics and Composites
.pdf350 |
Chapter 5 |
106.R. W. Rice and B. K. Speronello. Effect of Microstructure on Rate of Machining of Ceramics. J. Am. Cer. Soc. 59(7–8):330–333, 1976.
107.L. F. Goyette, T. J. Kim, and P. J. Gielisse. Effect of Grain Size on Grinding High Density Aluminum Oxide. Am. Cer. Soc. Bull. 56(11):1018, 1977.
108.D. B. Marshall, B. R. Lawn, and R. F. Cook. Microstructural Effects on Grinding of Alumina and Glass-Ceramics. J. Am. Cer. Soc. 70(6):C-139–140, 1987.

6
Grain Effects on Thermal Shock Resistance and Elevated Temperature Crack Propagation, Toughness,
and Tensile Strength
I.INTRODUCTION
Previous chapters have addressed the grain, mainly size, dependence of mechanical properties nominally at 22°C. This chapter complements those by addressing the changes in the grain dependence of tensile properties as a function of temperature. Hardness, compressive strength, and wear and related behavior at elevated temperatures are addressed in the next chapter. Some attention is given to effects of temperatures < 22°C, but the primary focus is on effects of elevated temperatures, mainly where brittle fracture is still dominant. Thus while high-temperature creep, stress rupture, and related slow crack growth processes are addressed to a limited extent, they are large complex topics, commonly with even less specific attention to specific grain structure effects. Therefore the focus is on the grain dependence of mechanical properties in the range where fracture is still brittle or transitioning to nonbrittle processes such as creep rupture, where grain boundary sliding is commonly the dominant process. This restricted focus is still complex since (1) while there is more, but still limited, information on grain dependence, most data is more limited than at 22°C, and (2) the transition to nonbrittle processes is often subtle, not well defined, and can vary substantially with test parameters, e.g. stress/strain rates, the nature and amount of even limited grain boundary phases, grain structure, temperature, and the interactions of these.
351
352 |
Chapter 6 |
This chapter also briefly reviews effects of test environment and (mainly moderate) temperature on the flexure strength (σ) of polycrystalline ceramics as a function of grain size (G), in part complementing and extending discussion of slow crack growth (SCG) in Chap. 2. Additional insight is sought by comparing these polycrystalline strength trends with the behavior of single crystals (where available) and of Young’s modulus. This chapter draws substantially on a more recent review [1] and complements this and other reviews of σ–G-1/2 behavior at 22°C, updating and extending them [1–3]. The purpose of this chapter is to consider these factors as a guide to understand better the grain dependence of mechanisms of brittle fracture as a function of T. Thus while some behavior in the 1000–1500°C range is noted, the focus is on the –200 to 1000°C range; creep and high-temperature stress-rupture are only briefly considered. Similarly, while environmental effects are further considered, the focus is on their impact on σ–G relations. While useful information and implications regarding σ–G relations are obtained, uncertainties and inadequacies are shown that provide guidance for improved studies.
Properties are treated in the order of crack propagation and fracture toughness followed by tensile strength and then thermal stress and shock failure, for which there is limited data. This chapter shows that strengths can increase substantially more at T < 22°C than expected from increases in E due to suppression of SCG and that there is limited data at T > 22°C and < 800–1000°C, apparently due to the common assumption that no significant property changes occur in this temperature range. This is often found to be incorrect by limited more comprehensive tests. Comparison of the relative temperature dependence of Young’s modulus, toughness, and tensile strength is used to indicate mechanisms and changes. Some important strength changes in this intermediate range are shown, e.g. especially in Al2O3, where corresponding changes in hardness and compressive strength are shown in the next chapter. In general, more consistency is found between toughness and tensile strength at T > 22°C.
II.MODELS AND CONCEPTS
A.Young’s Modulus, Toughness, and Tensile (Flexure) Strength
Modeling of properties as a function of temperature is typically based on accessing the temperature dependence of the key parameters in the mechanism that is dominant in the temperature regime considered. Where there is a transition between mechanisms, some interpolation between the expectations of the different mechanisms may be sought for guidance. Where other mechanisms become operative, they must be addressed, with creep being a fundamental one, as is discussed below.
First consider the temperature dependence of elastic moduli, which are ba-
Grain Effects on Thermal Shock Resistance |
353 |
sic parameters, hence correlators, with properties discussed in previous chapters. While elastic moduli normally do not depend on grain parameters, comparison of their temperature dependence with that of other mechanical properties can indicate changes in mechanisms. This is particularly so for fracture toughness and related crack propagation and tensile strength, since they depend directly on Young’s modulus (E) [Eq. (2.2)]. This comparison with the temperature dependence of elastic moduli is aided by their typically better documented, better understood, and simpler decrease with increasing temperature due to their reflecting basic atomic bonding and the resultant decreases of this with temperature. Decreases of 1 to 2% per 100°C temperature rise are common. Thus Anderson [4] showed that Wachtman’s empirical equation [5] for Young’s modulus (E) at any temperature (T),
E = E0 – ATe–(T0/T) |
(6.1) |
where E0 = Young’s modulus at absolute zero temperature (T0) and A a is constant, was theoretically correct, i.e. could be derived from the Mie–Gruneisen equation of state if Young’s modulus was replaced by the bulk modulus. The equation was also theoretically correct for Young’s modulus provided that the temperature dependence of Poisson’s ratio is small, which is true for some, but not all, ceramics. Others have corroborated and extended these results, e.g. Ref. 6. Such intrinsic changes in elastic moduli with temperature are an important factor in the temperature changes of other properties that scale with elastic moduli, so deviations of other mechanical properties from such decreases with temperature are an important indication of changes in mechanisms. Greater deviations of polycrystalline versus single crystal behavior from the temperature dependence of E are also an important sign that microstructural effects are changing with temperature, as is shown in Sec. IV. Thus while grain boundary sliding (e.g. whose earlier onset may be indicated by internal friction) [7–11] may also affect the apparent elastic moduli if the stressing period is sufficiently long relative to the rate of creep such that some measurable nonelastic strain occurs during the stress cycle; such sliding typically has greater effect on other mechanical properties.
Other property changes with temperature may cause changes in the temperature dependence of other mechanical properties directly or via effects on elastic properties. A prime example of the latter is effects of temperature changes on microcracking from thermal expansion differences, e.g. anisotropy (TEA) between grains, which decreases as temperature increases and vice versa and also commonly depends on G, as was discussed in Chap. 2, Sec. III.C. As is discussed elsewhere [8], the significant decreases that substantial microcracking can make in elastic and other mechanical (and nonmechanical, e.g. thermal) properties can be reversed due to microcracks generally decreasing in size, number, or both, with many closing and partly or fully healing, as temperature substantially in-
354 |
Chapter 6 |
creases. Thus the normal decrease of elastic (and other mechanical) properties with increasing temperature may be temporarily reduced or reversed till further temperature increases result in the normal decrease in properties, with the reverse trend on cooling. Similarly, though less established and understood, elastic anisotropy (EA) may affect or cause such cracking, aiding or countering effects of TEA in noncubic materials, or by itself in cubic materials [8]. However, in contrast to the more consistent temperature dependence of TEA, that of EA may decrease, be nearly constant, increase, or show combinations of these as temperature increases, making evaluations material specific (Fig. 7.14).
Besides the above effects of temperature on properties via changes underlying those of interest, there are also the mobility and activity of water as the most pervasive sources of slow crack growth (SCG) via chemical effects that greatly decrease as temperature increases. Thus in materials such as Al2O3, which experience substantial SCG, their strengths at lower temperatures (e.g. commonly –196°C in liquid N2) are increased far more than expected from the 1–2% increase in E. Similarly, temperature increases, especially above 100°C, reduce the amount of moisture at crack tips and hence resultant SCG from it. The other important change in crack propagation and resultant mechanical properties arises from grain boundary sliding and its effects on both the crack size and character at failure and the energetics of propagation including impacts of possible effects on crack bridging and branching. However, all of these again raise questions and complications of the impact of crack size effects in crack propagation tests versus in the properties to be predicted such as tensile strength.
Beyond the above effects of temperature on underlying parameters such as Young’s modulus and crack size, e.g. the latter due to localized grain boundary sliding at and near crack tips, there are the broader mechanisms of nonelastic, i.e. creep or other deformation processes. These become of increasing significance, commonly on both a broader scale spatially in the sample or component and in terms of materials as temperatures increase and strain rates decrease. While there can be important differences between tensile and compressive stressing, for reference and guidance the following representative equation for the strain rate (d /dt) in creep is
dε |
= |
AMs b m |
σ n |
(6.2) |
|||||
|
|
|
|
|
|
|
|
|
|
dt |
kT G |
M |
|
||||||
|
|
||||||||
|
|
|
|
||||||
|
|
|
|
|
|
|
s |
|
|
where A = a constant, MS = the shear modulus, k= Boltzmann’s constant, T = absolute temperature, b = the Burgers vector, G = grain size, σ = stress, and m and n are constants for a given body and condition, which are respectively typically
Grain Effects on Thermal Shock Resistance |
355 |
0–3 and 1–5. Thus even in the case of the least dependence on G, strain rate increases as G–1, i.e. greater than the G dependence for brittle fracture of G–1/2. Such dependence of creep rate is essentially in the opposite direction from that of brittle fracture, since higher creep strain rates correspond to failure in faster times, at lower stresses, or both as G decreases versus increased strength in brittle fracture as G decreases.
B.Thermal Stress, Shock, and Fatigue Failure
The classical way of addressing thermal stress and shock failure was to solve the boundary value problems, or more commonly use existing compilations of solutions, e.g. Ref. 12. Such solutions almost invariably assumed isotropy of the body and that properties were temperature independent, since to do otherwise substantially complicates the problem. Application of these solutions, which are typically quite dependent on component geometry and boundary conditions, is by comparing the resulting thermal stresses to the known, or expected, failure stresses of the material, e.g. via use of Weibull statistics of failure [13]. Such solutions and experimental results yielded a number of thermal stress failure criteria depending on the material parameters and the thermal environment [14–18]. These basically fall into two broad categories of thermal stress failure resistance, i.e. where (1) no significant crack generation or growth occurs, so there is no loss of strength, or (2) thermal stresses are so extreme that crack generation, or more commonly growth, cannot be avoided but can sometimes be limited so that some reasonable level of strength remains.
The maximum tensile stress σt from a rapid temperature change is
σ |
= Eα ( T)(1 – ν)–1 |
(6.3) |
t |
|
|
Where E = Young’s modulus of the body, α = its thermal expansion, |
T = the |
temperature difference (typically in quenching), and ν = Poisson’s ratio. Various modifications of this are made, e.g. to account for time dependence of establishing this stress. Thus a factor reflecting the ratio of the time-dependent maximum stress to the theoretical maximum stress, i.e. of ≤ 1, is often multiplied into the right side of Eq. (6.3) to account for this [19]. Similarly, the right side of Eq. (6.3) may be multiplied by the thermal conductivity to reflect the higher temperature gradients from lower conduction in the body. Such equations are readily solved for the critical T, i.e. TC, and hence the critical quench temperature, TC, into a given environment, commonly a water bath, that causes measurable strength degradation. Thus though there are uncertainties or refinements such as specifics of the heat transfer from the specimen to the fluid [20] and effects of the bath temperature on this [21], such standardized quench tests are widely used to compare and rank materials.
Modeling of thermal stress and shock effects was advanced by analysis of
356 |
Chapter 6 |
bodies with arrays of cracks based on previous mechanical analysis of such bodies. Models based on such crack arrays were developed, applied, and extended by Hasselman [14–18], who showed their consistency with fracture mechanics formulation [18], providing direct analysis of the effects of microcracks [22,23]. Hasselman also noted that thermal stresses could also cause failure of function due to excessive buckling or fracture from bending stresses [24], with criteria for resistance to these being respectively (1) low thermal expansion and a low aspect ratio of the body, and (2) a high body aspect ratio and value of σ2(αE2)–1. Some analysis of thermal fatigue has also been made [25].
The changes in mechanisms and underlying mechanical properties with increased temperatures noted earlier can be factors in the thermal stress or shock failure in ceramics of high resistance to such failure. However, their impact is typically limited, since thermal stress failure, while determined by the extreme high temperature involved, is usually controlled by fracture in the cooler regions. This results from the fact that the main sources of flaws for failure in ceramics are typically in or near the body surface. Thus in rapid cooling of heated bodies, or of localized heating of part of a piece of ceramic, the coolest area(s) include much or all of the free surface, where many of the flaws for failure are located. Besides the above simpler model and more complex ones, there are now a variety of computer programs for thermal stress and shock, with some allowing consideration of temperature dependence of properties, which can be important in some cases.
III.FRACTURE TOUGHNESS AND RELATED CRACK PROPAGATION AS A FUNCTION OF G AND TEMPERATURE
A.Fracture Toughness as a Function of G and Temperature
This section addresses fracture toughness (and hence also energy) and related R–curve effects; high temperature SCG due to grain boundary sliding is addressed in the following section, as are effects of environments such as H2O on SCG at T < 22°C and possible effects of G on them, since they are typically evaluated by flexure measurements. Unfortunately there is very little direct information on the G dependence of crack propagation behavior for these two sections due to combinations of the limited G range of materials available (e.g. SiC to some extent, and especially Si3N4), the lack of tests on bodies of various G, and the lack of specifying the G values for bodies studied. However, limited data allowing comparison of singleand polycrystal results exists, as does somewhat more data comparing fracture toughness and elastic moduli as a function of test temperature. Such comparison indicates some effects of G, and effects of grain boundary phases, which are a factor in grain effects, as is also shown by some direct studies.
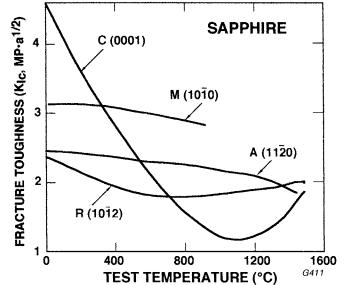
Grain Effects on Thermal Shock Resistance |
357 |
Consider first the fracture toughness and R–curve effects in Al2O3, for which there is more data than for other materials. Thus the data and survey for sapphire of Iwasa and Bradt [26] show considerable variation as a function of orientation, as does other data [27,28], but with a reduction in toughness anisotropy as the test temperature increases (Fig. 6.1). Their evaluation showed much greater decrease in the fracture toughness for basal plane fracture than expected elastically, indicating an increasing role of nonelastic processes as T increases, so such basal fracture goes from being by far the least preferred to the most preferred as temperature increases. This is consistent with indicated toughness minima, e.g. due first to increased ease of slip or twinning aiding crack growth and subsequent crack blunting as such deformation becomes more extensive, and especially direct TEM observations showing increasing slip deformation as T increases (Wiederhorn et al [29]).
There is a fair amount of fracture toughness data for polycrystalline
FIGURE 6.1 Fracture toughness of sapphire (mainly from indent tests) on various indicated fracture planes as a function of test temperature. Note that (1) data could indicate a less rapid decrease in (0001) fracture than shown to 200°C, and (2) the indicated expectation for much greater decrease of basal fracture, i.e. on (0001) planes, is based on the temperature dependence of E (close to results for the A and M planes). (From Ref. 26, published with permission of the American Ceramic Society.)
358 |
Chapter 6 |
Al2O3 to compare with the single crystal results. Most of this shows toughness nearly constant as a function of T or more commonly decreasing over most or all of the temperature range, with the rate of decrease increasing at higher temperatures. Kobayashi et al.’s [30] data for a commercial alumina via a wedge loaded DCB test is an extreme example of the former, showing little change from 22 to 1000, then to 1600°C. De With’s [31] data for dense alumina sintered with MgO additions showed, via NB tests, linear toughness (and strength) decreases to the limits of their tests, 1200°C, that were those expected for E for both G 23 and 36 m (the latter obtained with 40 ppm CaO addition). He also showed that while toughness levels were lower than data from other investigators for similar aluminas, they had similar slopes, as was expected for the temperature dependence of E. The values for the finer G body were 15% > for the larger G body, i.e. 3.8 and 3.3 MPa·m1/2 respectively at 22°C, indicating a G dependence different from that of toughness independent of or increasing with G at 22°C (Chap. 2, Sec. III.F). Also, his more extensive data for the finer G body would be consistent with a toughness minimum at 700°C and a maximum at 1100°C.
Dalgleish et al. [32] tested three commercial (95, 97.5, and 97.7%) aluminas in the G range of respectively 4, 24, and 2 m and P 0.06, 0.09, and 0.01 to 1000°C showing toughness minima at 300–600°C and then maxima at 800°C, respectively 10% below and 10–30% above values at 22°C. No significant change in acoustic emissions from each alumina occurred to 650°C, beyond which emission, attributed to flow of the glassy grain boundary phase, increased substantially, e.g. as indicated by intergranular fracture increasing with T. The most probable microstructural correlation was for lower toughness at larger G, e.g. by 40%, i.e. consistent with de With’s data above. Others also showed toughness decreasing with increasing T, e.g. Tai and Watanabe [33] by 30% to 700°C, and Moffatt et al. [34] showed a similar trend with accelerating decreases of 70–80% at 1400°C. Jakus et al. [35] evaluated an 85% commercial alumina (G 5 m) from 1150 to 1275°C showing that bridging of the crack by glassy ligaments occurred.
Xu et al. [36] reported grain bridging of a pure, dense alumina (G 10.5m) based on R–curve effects from indentation cracks (mostly 100–300 m) with modest toughness increases, e.g. 30%, with increasing crack size, with similar rates of increase for all test temperatures (25, 400, 700, 1000, and 1300°C). The decrease in toughness of 35% over the temperature range, which is somewhat greater than expected from decreases in E (i.e. 27%), occurred mostly by 400°C. They analyzed their data based on a bridging model assuming that toughness is the sum of an intrinsic toughness, K0, and bridging contributions, giving K0 values decreasing from 2.2 to 1.4 MPa·m1/2 from 25 to 1300°C. However, such values appear low in comparison to averaging single crystal values in Fig. 6.1, which would be for transgranular fracture with a crack size of
Grain Effects on Thermal Shock Resistance |
359 |
G rather than much larger cracks used. While fracture mode was not addressed, intergranular fracture is expected, especially at higher temperatures, which could lower K0 values, for cracks approaching or on the scale of G, but again such low values would appear to be low for cracks encompassing 5–10 grains.
Grimes et al. [37] studied toughness and R–curve behavior of a commercial, 99.5 pure (AD-995) alumina made with a SiO2 sintering aid giving G = 19 ± 4 m (range 2–40 m). They showed that while there was some variation for the two NB tests used (chevron and straight notch), as expected, there was little or no decrease in toughness values from 4 to 4.5 MPa·m1/2 from 22°C to 650°C and then an accelerating decrease to 1 MPa·m1/2 at 1400°C. They observed limited change in the fracture mode of mainly intergranular fracture for G < 15 m and mostly transgranular fracture for G > 20 m to 950°C, except for some reduction in the transgranular fracture, which accelerates at higher temperatures. By 1200°C, some crack branching was observed, with this increasing as temperature increased. Renotching of the specimens confirmed that the R–curve effects, which were similar in relative proportion to the toughness at each test temperature, were due to effects in the wake zone, which were attributed to bridging (and at higher temperatures, branching).
As was noted above, individually data of de With [31] and Dalgleish et al. [32] each indicated toughness decreasing as G increases. These data sets are also generally consistent with each other as well as other limited data for ≥ 95% alumina bodies where G values are available (Fig. 6. 2). Thus despite differing tests, limited differences in purity, and residual porosity, these data sets collectively reinforce a decrease in toughness as G increases, but with this G dependence decreasing as T increases.
Another material for which there is both singleand polycrystal data as a function of T is MgAl2O4. Stewart and Bradt [38,39] showed that the IF toughness of stoichiometric MgAl2O4 crystals stressed on <100>, <110>, <111> axes all showed limited decreases similar to, but less than, the expected decrease in E, to 900–1200°C, but then increased at an increasing rate with further T increases to the limit of testing (1500°C). White and Kelkar [40] and others [41–44] showed that the toughness of a large G ( 100 m), transparent MgAl2O4 hot pressed with LiF additions (that reduce toughness at room temperature, Fig. 2.13) initially decreased from 2.4 MPa·m1/2 at 22°C slower than E but then accelerated its decrease as the melting temperature (800+°C) of LiF was reached and then very modestly increased to the limit of testing at 1500°C (Fig. 6.3). To 800°C the fracture mode was 50% intergranular and then increased, consistent with indicated and expected effects of LiF and possible increased grain bridging as intergranular fracture increased.
Baudin et al. [43], using MgAl2O4 sintered from 99.6% pure spinel powder to 2.5% porosity with G = 1.5 ± 0.8 m, showed E decreasing from 205 GPa at 22°C to 170 GPa at 1300°C, i.e. a 10% decrease. Toughness decreased from