
Metod_Dipl_bak_2017_РВЦ (3)
.pdfКількість 0,6 н розчину гідроксиду натрію становить 530 м л. Для стерилізації лугу в автоклаві використовують колбу ємністю 1 л. Вміст колби асептично вносять в інокулятор за допомогою дозуючої системи.
6.2.4. Розрахунок кількості реакторів-змішувачів для приготування середовища для вирощування посівного матеріалу в інокуляторі геометричним об’ємом 50 л
а) Підбираємо геометричний об’єм реактора-змішувача для композиції А. Приблизний
геометричний об’єм реактора-змішувача при заданому |
Кзб = 0,8: |
|
|
VАг = VА/Кзб = 14,8/0,8 = 18,5 л |
|
|
|
Вибираємо з Таблиці 11.1. [1] найближчий за номінальним об’ємом реактор: |
Vнр = 20 л. |
||
Кількість реакторів при заданому Кзб становить: |
|
|
|
Nр = VАг/Vнр = 18,5/20= 0,9. Приймаємо – 1 од. |
|
|
|
Уточнюємо коефіцієнт заповнення реактора: |
|
|
|
Кзр = VА/(Vнр Nр) = 14,5/(20·1) = 0,73 |
|
|
|
Оскільки уточнений коефіцієнт заповнення |
лежить |
в заданих межах |
(0,7 – 0,85), |
приймаємо до установки кількість реакторів для приготування композиції А – 1 . Після приготування композиція А передається в інокулятор, де стерилізується.
2) Підбираємо геометричний об’єм реактора-змішувача для композиції Б. Приблизний геометричний об’єм реактора-змішувача при заданому Кзб = 0,8:
VБг = VБ/Кзб = 12,1/0,8 = 15,1 л
Вибираємо з Таблиці 11.1. [1] найближчий за номінальним об’ємом реактор: Vнр = 20 л. Кількість реакторів при заданому Кзб становить:
Nр = VАг/Vнр = 18,5/20= 0,9. Приймаємо – 1 од.
Уточнюємо коефіцієнт заповнення реактора:
Кзр = VА/(Vнр Nр) = 14,5/(20·1) = 0,73
Оскільки уточнений коефіцієнт заповнення лежить в заданих межах (0,7 – 0,85), приймаємо до установки кількість реакторів для приготування композиції Б – 1 .
Після приготування композиція Б стерилізується в реакторі і потім передається до інокулятора для змішування.
Для корегування рН в процесі приготування та після стерилізації поживного середовища для вирощування посівного матеріалу в інокуляторі об’ємом 50 л розраховуємо кількість розчину кислоти та лугу із розрахунку 2 мл на 1л поживного середовища.
Кислоту для підкислення композиції Б у кількості 25 мл вносять в процесі приготування композиції безпосередньо в реактор об’ємом 20л перед стерилізацією.
Кількість попередньо простерилізованого 0,6 н розчину гідроксиду натрія у кількості 54 мл вносять асептично в інокулятор після змішування композицій за домогою дозуючої системи.
6.3. Розрахунок реактора-змішувача для культуральної рідини після процесу біосинтеза
Підбираємо геометричний об’єм реактора-змішувача для культуральної рідини після процесу біосинтеза. Приблизний геометричний об’єм реактора-змішувача при заданому Кзб
= 0,8:
Vкрг = Vкр/Кзб = 25,6/0,8 =32 м3
Вибираємо з Таблиці 11.1. [1] найближчий за номінальним об’ємом реактор: Vнр = 32 л. Оскільки номінальний та приблизний об’єм реактора співпадають уточнення коефіцієнта заповнення реактора не проводимо.
Відповідно цей реактор використовується в процесі фільтрації культуральнї рідини за допомогою ФПАКМ.
6.4. Розрахунок фільтр-преса ФПАКМ
Для розрахунку можна скористатись прикладом 4.5., наведеним у [1].
51
Вихідні дані для розрахунку:
Об'єм суспензії, що йде на фільтрування, Vсус= Vкр = 25,6 м3. Загальний час фільтрування суспензії Тфт = 18 год.
Час відтискання осаду і пересування стрічки τд = 12 хв. Зазор між плитами апарата, h = 45 мм.
Робочий тиск в камерах ΔP = 1,2 МПа. Характеристики суспензії:
Питомий опір фільтруванню ro = 1,0·1013 м/кг.
Маса вологого осаду, який одержують під час фільтрування 1 м3 .
суспензії mо = 11 |
кг/м3 (див. п. 4.1.4. Продуктового розрахунку) |
Густина суспензії |
ρсус = 1050 кг/м3. |
Динамічна в'язкість суспензії, μсус = 1,5·10-3 Па·с. |
|
Обираємо стандартний ФПАКМ з табл.4.3. [1] за умови, що товщина осаду в камері |
становитиме δ = 10 мм.
6.4.1. Визначаємо об'єм осаду з 1м2 площі фільтра становитеме,
V1ос =1·δ/1000 = 1·10/1000 = 0,01 м3 .
6.4.2. Маса осаду з 1 м2 площі фільтра складе
G1ос = V1ос· ρсус = 0,01·1050 = 10,5 кг/м2.
6.4.3. За один технологічний цикл треба переробити суспензії
V1cуc =G1ос/mо = 10,5/11= 0,95 м3.
6.4.4. З даної суспензії один технологічний цикл одержують фільтрату ,
V1ф =V1cуc·(1-mо/ρсус) = 0,95 ·(1– 11/1050) = 0,94 м3.
6.4.5. Час фільтрування даної суспензії за один технологічний цикл
τф= (V1ф)2·mо·ro·μсус/2·3600·ΔР·106 = (0,94)2·11·1,0·1013·1,5·10-3/2·3600·1,2·106
= 17,1 год.
6.4.6.Тривалість періоду фільтруваня за один технологічний цикл фільтрування Т = τф+τд/60 = 17,1+12/60 = 17,3 год.
6.4.7. Необхідна площа фільтрування для всієї суспензії
∑F = Vсус·Т/Тфт·V1cуc = 25,6·17,3/18·0,95 = 25,9 м2
З таблиці 4.3. [1] обираємо ФПАКМ 25 - 45 з площею фільтрації 25 м2 (габарити
3780х1250х4240 мм).
6.4.8. Уточнюємо реальний час фільтрування суспензії за вибраним ФПАКМом.
Тфр = Тфт·∑F/Fфпакм = 18·25,9/25 =18,64 год.
6. 5. Розрахунок УФ-установки для концентрування та очищення розчину ферментного препарата
Для розрахунку та підбору УФ-установки можна скористатись прикладом 9.1. , наведеним у [1].
Вихідні дані:
Об'єм супернатанту Vсн = 23,53 м3.
Маса абсолютно сухих речовин в концентраті Gаск = 208 кг.
Коефіцієнт втрат при концентруванні Еуф (1-3 %). Приймаємо Eуф= 0,02 (частка). Час ультрафільтрації τуф = 12 год.
Ступінь концентрування Куф = 2. |
|
Молекулярна маса фермента ксилонази М=35000 Да. |
|
Густина супернатанту ρсн = 1 050 кг/м3. |
|
Динамічна в'язкість супернатанту |
μсн = 1,5·10-3 Па·с. |
Густина води ρв = 1000 кг/м3. |
|
Динамічна в'язкість води при 200 С |
μв = 1,0·10-3 Па·с. |
Робочий тиск Р = 0,2 Мпа. |
|
6.5.1. Підбираємо геометричний об’єм збірник для супернатанту. Приблизний
52

геометричний об’єм реактора-змішувача при заданому Кзб = 0,8:
Vзсн = Vсн/Кзб = 23,53/0,8 = 29,4 м3.
Вибираємо з Таблиці 11.1. [1] найближчий за номінальним об’ємом реактор: Vснг = 32 м3.
Кількість реакторів при заданому Кзб становить:
Nр = Vзсн/Vснг = 29,4/32 = 0,92. Приймаємо – 1 од.
Уточнюємо коефіцієнт заповнення реактора:
Кзр = Vсн/(Vснг Nр) = 23,53/(32·1) = 0,74
Оскільки уточнений коефіцієнт заповнення лежить в заданих межах (0,7 – 0,85), приймаємо до установки кількість збірників для супернатанту – 1.
6.5.2. Підбираємо тип мембрани для ультрафільтрації супернатанту.
Визначаємо приблизний діаметр молекули фермента ксилонази Dмол = 0,098 •M0,38 =
0,098· 35000 0,38 = 5,22 нм.
Для вибора необхідного типу УФ-мембрани скористаємось Табл.9.2 [1] Для порівняння вибираємо полісульфонамідну мембрану типу УПМ-50М з діаметром
пор = 5 нм , продуктивністю по дистилірованій воді 180 дм3/м2·год та полісульфонамідну мембрану типу УПМ-100 з діаметром пор = 10 нм, продуктивністю по дистилірованій воді
840дм3/м2·год.
6.5.3.Для обох типів мембран перевіряємо відношення К = Dмол/Dпор > 0,5. К1 = 5,22/5 = 1,044 (для УПМ-50М), К2 = 5,22/10 =0,522 (для УПМ-100). Для обох мембран
виконується умова К = 0,5 < Dмол/Dпор < 2.
6.5.4. За Таблицею 9.2. [1] визначаємо селективність вибраних мембран Для мембрани УПМ-50М величина φ складе , φ1 = 0,9996, відповідно для мембрани УПМ-100 - φ1
=0,9879.
Отже, ці дві мембрани можуть бути використані для ультрафільтрації супернатанту. Надалі проводимо розрахунки з метою визначитись – чи вкладаються втрати
супернатанту для вибраних мембран у визначені межі втрат Еуф = 2%.
6.5.5. Визначаємо концентрації сухих речови в супернатанті та концентраті, Хс та Хк, кг/кг:
Хс = Gаск/Vcн· ρсн = 208/23,53·1050 = 8,419·10-3 кг/кг;
Хк = Хс · Куф = 8,419·103 ·2 = 0,017 кг/кг.
6.5.6. Визначаємо середні концентрації Хср1, Хср2 супернатанту для мембран УПМ50М та УПМ-100 відповідно
Хср1 =
кг/кг;
Хср2 = .
6.5.7. Шукаємо витрати супернатанту Lс та витрати продукту Lпр, що подається разом з супернатантом
Lс = Vсн · ρсн / τуф·3600 = 23,53· 1050/12·3600 = 0,572 кг/с;
Lпр = Lс · Хс = 0,572·8,419·10-3 = 4,815 ·10-3 кг/с.
6.5.8. Витрати пермеату Lп1 для мембрани УПМ-50М
53
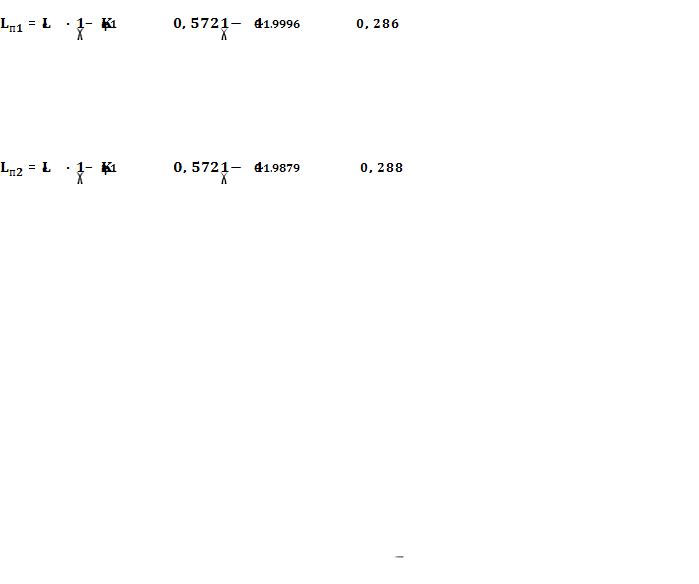
кг/с
Витрати пермеату Lп2 для мембрани УПМ-100
кг/с
6.5.9. Втрата продукту з пермеатом для мембрани УПМ-50М
В1п = Lп1· Хср1 = 0,286·4,67·10-6 = 1,335 · 10-6 кг/с
Втрата продукту з пермеатом для мембрани УПМ-100
В2п = Lп2· Хср2 = 0,288·1,412·10-4 = 4,07· 10-5 кг/с
6.5.10. Відсоток втрат продукту з пермеатом для мембрани УПМ-50М
%В1 |
= В1п· 100/ Lпр = 1,335 · 10-6 ·100/4,815·10-3 |
= 0,028 % |
Відсоток втрат продукту з пермеатом для мембрани УПМ-100 |
||
%В2 |
= В2п· 100/ Lпр = 4,07 · 10-5 ·100/ 4,815 ·10-3 |
= 0,845% |
Оскільки обидві мембрани задовольняють умові втрат продукту < 2 %, дані мембрани можна використовувати для концентрування, але згідно технічних характеристик мембрана
УПМ -100 випереджає УПМ-50М. Відповідно до |
Таблиці |
9.3. |
[1] продуктивністю по |
дистильованій воді мембрани УПМ-100 становить |
V0 = 840 дм3/м2·год, що значно більше, |
||
ніж у мембрани УПМ-50М (V0 =180 дм3/м2·год). |
Отже, |
для |
остаточних розрахунків |
вибираємо мембрану типу УПМ-100.
6.5.10. Знаходимо масову продуктивність мембрани УПМ-100 по чистій воді
G0 = AΔP =0,23· 0,2 =0,047 кг/м2·с,
де А = V0 ρв/3600·1000 = 840·1000/3600·1000 = 0,23; A проникність мембрани за чистою водою, кг/(м2·с·МПа); ρв – густина води при t = 20ºC, кг/м3.
6.5.11. Знаходимо масову продуктивність мембрани УПМ-100 за супернатантом
Gс = G0(μв/ μс) = 0,047(1,0·10-3/1,5·10-3) = 3,1·10-2 кг/м2·с. 6.5. 12. Необхідна загальна поверхня ультрафільтрації
∑F = Lп2/Gс =0,288 /3,1·10-2 = 9,3 м2
6.5.13. Вибираємо рулонний тип ультрафільтраційного модуля: для рулонних мембран
Fелм : 5, 10, 20, 40, 80, 90, 150, 240 м2.
Найближчий за поверхнею Fелм = 10 м2
Знаходимо потрібну кількість елементів n = ∑F/ Fелм = 9,3/10 = 0,93 Приймаємо кількість елементів для УФ-установки n = 1.
6.6. Розрахунок розпилювальної сушильної установки
Для розрахунку розпилювальної сушильної установки слід скористатись прикладом
10.1 [1].
Приймемо час сушіння τсуш = 24 год.
6.6.1. Об’єм концентрату, що йде на сушіння складає (п.4,2,2) Vкон = 11530 л Підбираємо геометричний об’єм реактор для концентрату. Приблизний геометричний
об’єм реактора-змішувача при заданому Кзб = 0,8:
Vзкон = Vкон/Кзб = 11,53/0,8 = 14,4 м3.
Вибираємо з Таблиці 11.1. [1] найближчий за номінальним об’ємом реактор: Vснг = 16 м3.
54
Кількість реакторів при заданому Кзб становить:
Nр = Vзкон/Vснг = 14,4/16 = 0,9. Приймаємо – 1 од.
Уточнюємо коефіцієнт заповнення реактора: |
|
|
|
|
|
|
Кзр = Vсн/(Vснг Nр) = 11,53/(16·1) = 0,72 |
|
|
|
|
|
|
Оскільки |
уточнений коефіцієнт заповнення лежить |
в заданих межах |
(0,7 – |
0,85), |
||
приймаємо до установки кількість реакторів для концентрату – 1. |
|
|
|
|
||
6.6.2. Масса концентрату, що йде на сушіння, при його густині |
ρуф |
= 1050 кг/м3 |
|
|||
становить |
|
|
|
|
|
|
Gкон = Vкон·ρуф/1000 =11530·1050/1000 =12107 кг. |
|
|
|
|
|
|
6.6.3. |
Маса висушеного препарату з врахуванням |
втрат |
Есш |
=0,1 |
(частка) |
сухої |
речовини з повітрям, що виходить з сушарки, при стандартному вмісті сухих речовин в готовому продукті СРгп = 0,88
Gcш = Gаск(1-Есш)/СРгп = 208(1-0,1)/0,88 = 213 кг.
6.6.4. Маса води, що підлягає видаленню
Wсш = Gкон(1- Есш)- Gcш =12107·(1-0,1) – 213 = 10683 кг, тоді витрати вологи, що підлягає видаленню, будуть
W = Wсш /τсуш = 10683/24 = 445 кг/год.
6.6.5. Приймемо температуру на вході гарячого газу (повітря) t1в= 130 °С; на виході гарячого газу (повітря) t2в= 65 °С; температуру висушеного матеріалу, яка не повинна перевищувати t1м= 45°С.
6.6.6. Визначимо середню питому продуктивність сушарки за вологою, що випарилась
Gсер =0,05[(t1в+t2в/2) -tм] = 0,05·[(130+65)/2 - 45] = 2,63 кг/(м3· год)
6.6.7. Орієнтовно об'єм розпилювальної сушарки Vcуш розраховують за формулою
Vсуш = W/ Gсер = 445/2,63 = 170 м3
6.6.8. Обираємо з Таблиці 10.1. [1] найближчу за об'ємом стандартну розпилювальну сушарку СРЦ-6,5/170 об'ємом 170 м3, яка має діаметр 6,5 м і висоту циліндричної частини 5 м, нижнє підведення повітря та конічну частину, маса сушарки 27,5 т.
6.7. Розрахунок бункера-змішувача для стандартизації ферментного препарата
6.7.1. Об’єм сухого продукту та наповнювача при густині суміші ρсм = 1200 кг/м3 складає
6.7.2.Vгп= (Gcш+Gнап)/ ρсм = (213+490)/1200 = 0,585 м3.
6.7.2.При заданому коефіцієнті заповнення Кзб = 0,8 приблизний геометричний об’єм
бункера-змішувача становить
Vгбз = Vгп/ Кзб = 0,585/0,8 = 0,73 м3.
Найближчий за об’ємом є змішувач геометричним об’ємом Vтбз = 1,0 м3 (Таблиця 11.1.
[1]).
6.7.3. Уточнюємо коефіцієнт заповнення :
Кзр = Vгп/ Vтбз = 0,585 /1,0 = 0,59
Оскільки уточнений коефіцієнт заповнення змішувача не перебуває в заданих межах (0,7
– 0,85), замовляємо його окремо геометричним об’ємом Vзр = 0,8.
6.8.Розрахунок фасувально-пакувального обладнання
6.8.1. Маса готового ферменту, що йде на фасування,
Gгп =703 кг.
Маса готового препарату, що фасується в 1 поліетиленовий пакет, а потім у паперовий крафт-мішок Gкрф = 10 кг. Кількість пакетів за цикл Nц = 703/10 = 70
Використовується напіватомат-дозатор з продуктивністю Gав = 100 пакетів за годину.
6.8.2.Час фасування партії готового препарату
τф = Gгп/ Gав = 70/100 = 0,7 год = 42 хв.
55

Розділ 7. Специфікація обладнання
Виконується згідно вимог курсових проектів, виконаних на 4-му курсі [2, 3]. У колонці «Технічна характеристика (виробник)» бажано вказувати конкретне інформаційне джерело, звідки взято технічну характеристику обраного обладнання.
Розділ 8. Опис технологічної схеми
Виконується аналогічно відповідним розділам курсових проектів, виконаних на 3 і 4-му курсі [2, 3, 5].
У цьому розділі наводиться конкретний опис кожної стадії і операції процесу. Під час опису підготовки поживного середовища розраховується (виходячи зі складу поживного середовища і робочих об’ємів інокуляторів, посівних апаратів і виробничого ферментера) кількість (г, кг) кожного з компонентів поживного середовища, необхідної для приготування певного об’єму середовища, а також води для приготування певних композицій (розчинів), особливості їх стерилізації, вирощування інокуляту на всіх стадіях його підготовки, умови проведення виробничого біосинтезу, виділення цільового продукту, методи контролю.
Викладаючи технологічний процес обов язково наводять номер позиції технологічного обладнання, за допомогою якого він здійснюється.
Зверніть увагу! Номер позиції технологічного обладнання, на який посилаються при описі відповідної стадії, повинен повністю співпадати з таким, що представлений на апаратурній схемі та у специфікації обладнання.
Приклад 24. Фрагмент опису технологічної схеми з переліком стадій
Технологічна схема виробництва ергостерину включає допоміжні роботи (санітарна підготовка виробництва, підготовка повітря, піногасника, розчину меляси для підживлення, титрувальних агентів, підготовка розчинів реагентів для дезінтеграції клітин і екстракції ергостерину, підготовка і стерилізація поживних середовищ,) та технологічний процес (підготовка посівного матеріалу, виробничий біосинтез, відділення біомаси, дезінтеграція клітин, екстракція ергостерину, концентрування органічного екстракту, кристалізація і висушування кристалів ергостерину).
ДР 1. Санітарна підготовка виробництва
ДР 1.1. Підготовка мийних та дезінфікуючих засобів ДР 1.2. Підготовка виробничих приміщень ДР 1.3. Підготовка технологічного обладнання
ДР 2. Підготовка аераційного повітря ДР 3. Підготовка піногасника ДР 4. Підготовка титрувальних агентів
ДР 5. Приготування і стерилізація розчину меляси для підживлення ДР 6. Підготовка розчинів реагентів для дезінтеграції клітин і екстракції ергостерину
ДР 6.1. Підготовка водно-спиртового розчину їдкого натру
ДР 7. Приготування та стерилізація поживних середовищ
ДР 7.1 Приготування і стерилізація поживного середовища для вирощування інокуляту в колбах на качалках
ДР 7.1.1 Приготування і стерилізація композиції А ДР 7.1.2 Приготування і стерилізація композиції Б
56
ДР 7.2. Приготування та стерилізація поживного середовища для вирощування посівного матеріалу в інокуляторі
ДР 7.2.1. Приготування і стерилізація композиції ДР 7.2.2. Приготування і стерилізація композиції Б
ДР 7.3. Приготування і стерилізація поживного середовища для виробничого біосинтезу
ТП 8. Підготовка посівного матеріалу
ТП 8.1. Підтримання колекційної культури ТП 8.2. Одержання робочої культури на агаризованих середовищах
ТП 8.3. Вирощування інокуляту на агаризованих середовищах ТП 8.4. Вирощування інокуляту в колбах на качалках ТП 8.5. Вирощування посівного матеріалу в інокуляторі
ТП 9. Біосинтез
9.1. Виробничий біосинтез (одержання культуральної рідини)
ТП 10. Відділення біомаси
ТП 10.1. Центрифугування культуральної рідини
ТП 11. Дезінтеграція клітин
ТП 11.1. Руйнування дріжджових клітин ТП 11.2. Охолодження дезінтеграту
ТП 12. Виділення ергостерину
ТП 12.1. Екстракція ергостерину ТП 12.2. Декантація екстракту
ТП 13. Концентрування органічного екстракту
ТП 13.1. Вакуум-випарювання екстракту
ТП 14. Отримання сухого ергостерину
ТП 14.1. Кристалізація ергостерину ТП 14.2. Висушування кристалів ергостерину
Приклад 25. Опис деяких стадій
ДР 5. Приготування і стерилізація розчину меляси для підживлення
Упроцесі біосинтезу, починаючи з 2-ї год культивування, вносять 330 г/л меляси порціями по 20 г/л кожні 2 год. Розчин меляси готують та стерилізують в окремих апаратах
(З-40) і (З-44).
ДР 5.1. Приготування і підкислення розчину меляси для підживлення
Узбірник (З-40) через об’ємно-ваговий дозатор (Д-6) вносять 768,9 кг меляси, додають 685,1 л питної води (враховуючи 10 % конденсату при подальшій стерилізації), суміш нагрівають до 40 ºС подачею у сорочку апарата глухої пари і включають мішалку (200 об/хв) до повного розчинення меляси.
До розчину меляси додають 7,7 л 1 н розчину сульфатної кислоти від ДР 4.1 до досягнення рН 4,0 (1 мл 1 н розчину сульфатної кислоти вноситься ≈ на 100 мл меляси) і включають мішалку (200 об/хв) на 30−40 хв. Далі суміш розчину меляси та осаду сульфату кальцію передають на центрифугу за допомогою насоса (Н-41).
ДР 5.2. Центрифугування розчину меляси
На центрифузі з ножовим зрізом осаду PPCS-960 (Ц-42) з розчину меляси видаляється осад та відправляється на знешкодження твердих відходів. Частота обертання барабана становить 3000 об/хв, час 20 хв. Освітлений розчин меляси передають насосом (Н-43) на стерилізацію у попередньо простерилізований збірник (З-44).
ДР 5.3. Стерилізація розчину меляси
Розчин меляси стерилізують гострою парою в збірнику (З-44) об’ємом 1 м3 при температурі 112 ºС упродовж 30 хв. Стерильний розчин меляси подають порціями в ферментер (ФР-39) до ТП 9.1 за допомогою насоса (Н-45).
57
ТП 11. Дезінтеграція клітин ТП 11.1. Руйнування дріжджових клітин
Біомасу від ТП 10.1 подають у збірник (З-56) об’ємом 250 л. У цей же збірник за допомогою насоса (Н-22) подають від ДР 6.1 21 л водно-спиртового розчину гідроксиду натрію. Суміш біомаси та водно-спиртового розчину витримують при температурі 82 ºС упродовж 4 год при постійному перемішуванні (200 об/хв.).
ТП 11.2. Охолодження дезінтеграту
Дезінтеграт охолоджують до температури 40 ºС у тому ж збірнику (З-56) за рахунок подачі холодної води в сорочку апарата.
ТП 12. Виділення ергостерину ТП 12.1. Екстракція ергостерину
До охолодженого дезінтеграту у збірник (З-56) через об’ємно-ваговий дозатор (Д-14) додають 70 л технічного ізопропанолу (співвідношення спирту до біомаси дріжджів не менше 0,6:1, тобто на 105 кг дріжджів 70 л спирту). Замість технічного ізопропанолу можна використовувати його відгін або суміш технічного ізопропанолу та відгону (1:1). Екстракцію ергостерину здійснюють упродовж 30 хв при перемішуванні (200 об/хв.), після чого виключають мішалку та залишають суміш на кілька годин для розділення фаз.
ТП 12.2. Декантація екстракту
Органічний екстракт ергостерину, отриманий на стадії ТП 12.1 (верхня фаза), перекачують з апарата (З-56) за допомогою вакуум-насоса (Н-25) у збірник (З-57) об’ємом 160 л. Водна фаза зливається через нижній патрубок збірника (З-56) та направляється на знешкодження відходів. Екстракт ергостерину подають на вакуум-випарну установку (В-59) за допомогою насоса (Н-27) до ТП 13.1.
ТП 13. Концентрування екстракту ергостерину ТП 13.1. Вакуум-випарювання екстракту
Екстракт ергостерину від ТП 12.2 упарюють на випарній установці (В-59) до 70 %-го вмісту сухих речовин. Випарювання здійснюють упродовж 1 год (продуктивність випарної установки 100 л/год) при температурі 70 ºС. Упарений продукт перекачується насосом (Н-28) на стрічковий кристалізатор (К-60) ТП 14.1.
Розділ 9. Контроль виробництва
Розділ включає в себе карту постадійного контролю із зазначенням усіх точок контролю (об’єднує карти постадійного контролю, виконані в ході попереднього курсового проектування) та обов’язкове наведення конкретних методик технологічного і мікробіологічного контролю.
Технологічний контроль включає визначення концентрації біомаси і конкретного цільового продукту у культуральній рідині, концентрації джерел вуглецю та азоту (не елементів С і N, а конкретних компонентів поживного середовища, що є джерелами вуглецю і азоту, наприклад, глюкози, етанолу, амонійного чи нітратного азоту), визначення показників, які згідно НТД мають контролюватися у напівпродуктах і готовій продукції (вміст діючої речовини, вологість, тощо).
У разі визначення концентрації позаклітинних продуктів мікробного синтезу ваговим методом необхідно пам’ятати, що на першому етапі потрібно відділити біомасу, а цільовий продукт виділяти (екстрагувати, осаджувати) з супернатанту культуральної рідини. Так само, й у процесі визначення концентрації позаклітинного цільового продукту методом газо-рідинної чи високоефективної рідинної хроматографії спочатку треба відділити біомасу, з супернатанту культуральної рідини виділити цільовий продукт і у вигляді
58
розчину певної концентрації аналізувати його хроматографічними методами.
Приклад 26. Визначення концентрації гліцерину (джерело вуглецю та енергії) у середовищі культивування P. pastoris PS103(pHBS)
Концентрацію гліцерину визначають у супернатанті, який одержують центрифугуванням культуральної рідини (3000 об/хв, 20 хв). Гліцерин аналізують методом високоефективної рідинної хроматографії (ВЕРХ) на хроматографі (Waters, Milford, MA, USA), оснащеному детектором (Model 2414, Waters) і колонкою Supelcogel C610H (30 см х
7,8 мм). Рухома фаза складається з 0,1% H3PO4 в деіонізованій воді (Mili-Q). Умови визначення: швидкість потоку 0,5 мл/хв, температура 30° С, об’єм проби 0,02 мл [6].
Визначення |
концентрації |
позаклітинних |
поверхнево-активних |
речовин |
|
|
|
Концентрацію ПАР |
(г/л) у культуральній рідині визначали |
ваговим методом після |
екстракції поверхнево-активних ліпідів сумішшю Фолча. Для відділення біомаси і одержання супернатанту, культуральну рідину N. vaccinii ІМВ В-7405 центрифугували (5000 g, 45 хв), надосадову рідину зливали. Після цього 25 мл супернатанту поміщали в циліндричну ділильну воронку об’ємом 100 мл, додавали 25 мл суміші хлороформу і метанолу (2:1, суміш Фолча) і струшували (з метою екстракції ліпідів) протягом 5 хв. Отриману після екстракції суміш залишали у воронці для розділення фаз, після чого нижню фракцію збирали (органічний екстракт 1), а водну фазу піддавали повторній екстракції. При повторній екстракції до водної фази додавали 25 мл Фолча і проводили екстракцію ліпіді упродовж 5 хв. Після розділння фаз, збирали нижню фракцію і отримували органічний екстракт 2. На третьому етапі до водної фази додавали 25 мл суміші хлороформу і метанолу (2:1) і здійснювали екстракцію, як описано вище, отримуючи органічний екстракт 3. Екстракти 1–3 змішували та упарювали на роторній випарній установці ИР-1М2 (Росія) при температурі 50 °С і абсолютному тиску 0,4–0,5 атм до постійної маси.
Розділ 10. Автоматизація виробництва
Цей розділ виконується згідно методичних рекомендацій до виконання індивідуального завдання з дисципліни «Автоматизація та управління біотехнологічних виробництв».
6. ВИМОГИ ДО ОФОРМЛЕННЯ КВАЛІФІКАЦІЙНОГО ПРОЕКТУ
6.1. Вимоги до оформлення текстової частини
Пояснювальну записку виконують із використанням комп'ютерної техніки (принтера) на аркушах білого паперу формату А-4 із залишенням полів (зліва і зверху не менше 20 мм, справа і знизу не менше 10 мм) або на стандартних аркушах з рамкою. Першу сторінку кожного нового розділу обов’язково розміщують на листі з основним написом (додаток 5). Всі інші листи допускається друкувати на листах без рамок.
Всі сторінки пояснювальної записки нумеруються й номери проставляються у правому кутку нижньої частини аркуша без крапки та у відповідному полі рамки. Нумерація сторінок пояснювальної записки починається з титульного аркуша, але на самому титульному аркуші номер сторінки не проставляється.
59

Вимоги до оформлення назв розділів, підрозділів, таблиць, рисунків, списку використаної літератури, додатків аналогічні попереднім курсовим проектам (роботам) і викладені у методичних рекомендаціях [1-6].
6.2. Вимоги до оформлення графічної частини
Всі графічні документи мають бути представлені переважно у вигляді роздруківок з використанням комп'ютерної графіки (як виключення у ручному варіанті виконання). У кожному разі для розміщення демонстраційних креслень і матеріалів використаються аркуші білого паперу формату А1. Використовувати аркуші формату А3 або А0 допускається тільки у вкрай необхідних випадках. Кількість та формат креслень визначає керівник проекту.
Кожний лист креслення обов’язково оформлюється згідно вимог ЄСКД (Єдиної системи конструкторської документації) основним надписом (згідно зразку, наведеному у додатку 4)
Зверніть увагу! Розмір штампу основного напису є величиною постійною (185 55 мм) для будь-якого формату креслення. Недотримання розмірів
штампу є грубою помилкою.
Графічна частина ВКДП включає в себе технологічну та апаратурну схеми виробництва цільового продукту.
Технологічна схема виробництва включає в себе технологічну схему доферментаційних стадій і виробничого біосинтезу, складену під час виконання курсового проекту з дисципліни «Основи проектування біотехнологічних виробництв» [2] і (для інженерних ВКДП) технологічну схему післяферментаційних процесів, складену під час виконання курсового проекту з дисципліни «Харчова біотехнологія» [3]. Нумерація стадій – наскрізна .
У технологічній схемі використовуються такі умовні позначення стадій: ДР – стадії допоміжних робіт; ТП – стадії основного технологічного процесу;
ПВ – стадії перероблення отриманих відходів; ЗВ – стадії знешкодження відходів (твердих, рідких та газоподібних,
вентиляційних викидів повітря в атмосферу); ПМВ – стадії пакування, маркування та відвантаження готового продукту.
На технологічній схемі показують точки контролю: Кт - контроль технологічний; Кх - контроль хімічний.
Км - контроль мікробіологічний Апаратурна схема є графічним зображенням технологічного процесу у
вигляді умовних позначень апаратів та трубопроводів відповідно до вимог ГОСТ, ДСТУ, ГСТУ, ОСТ. Послідовність розташування апаратури на апаратурній схемі відповідає послідовності стадій та операцій технологічної схеми.
Креслення апаратурної схеми має відобразити все технологічне обладнання, включаючи допоміжне (допоміжні збірники, теплообмінна апаратура, насоси, компресори тощо). Літерні позначення обладнання на апаратурній схемі мають співпадати з прийнятими раніше, під час курсового проектування. На схемі не наводять обладнання, якщо його використовують у
60