
- •1 Машины и оборудование литейного производства
- •1.1 Общие сведения
- •1.2 Машины и оборудование литья в песчаные формы
- •1.2.1 Общая технологическая схема литья в песчаные формы
- •1.2.3 Модельные комплекты и опочная оснастка
- •1.3 Машины и оборудование специальных видов литья
- •1.3.1 Литье по выплавляемым моделям
- •1.3.2 Литье в оболочковые формы
- •1.3.3 Литье в металлические формы (кокили)
- •1.3.4 Литье под давлением
- •1.3.5 Центробежное литье
- •2 Машины и оборудование обработки металлов давлением
- •2.1 Общие сведения
- •2.4 Оборудование ковки
- •2.5 Оборудование горячей штамповки
- •3.4 Оборудование термической резки
- •3.4.1 Кислородная резка
- •3.4.2 Кислородно-флюсовая резка
- •3.4.3 Плазменная резка
- •Материаловедение. Особенности атомно-кристаллического строения металлов.
- •Металлы, особенности атомно-кристаллического строения
- •Понятие об изотропии и анизотропии
- •Аллотропия или полиморфные превращения.
- •Магнитные превращения
- •Лекция 2 Строение реальных металлов. Дефекты кристаллического строения
- •Лекция 3 Кристаллизации металлов. Методы исследования металлов.
- •Условия получения мелкозернистой структуры
- •Строение металлического слитка
- •Понятие о сплавах и методах их получения
- •Особенности строения, кристаллизации и свойств сплавов: механических смесей, твердых растворов, химических соединений
- •Классификация сплавов твердых растворов.
- •Кристаллизация сплавов.
- •Нагрузки, напряжения и деформации. Механические свойства.
- •Физическая природа деформации металлов.
- •Природа пластической деформации.
- •Дислокационный механизм пластической деформации.
- •Разрушение металлов.
- •Механические свойства и способы определения их количественных характеристик
- •Лекция 7 Механические свойства (продолжение).Технологические и эксплуатационные свойства
- •Механические свойства и способы определения их количественных характеристик: твердость, вязкость, усталостная прочность
- •Твердость по Бринеллю ( гост 9012)
- •Метод Роквелла гост 9013
- •Метод Виккерса
- •Основные характеристики:
- •Стали. Классификация и маркировка сталей.
- •Классификация и маркировка сталей Классификация сталей
- •Маркировка сталей
- •Классификация чугунов
- •Виды термической обработки металлов.
- •Лекция 14 Технологические особенности и возможности закалки и отпуска
- •Химико-термическая обработка стали
- •Назначение и технология видов химико-термической обработки: цементации, азотирования нитроцементации и диффузионной металлизации
- •Цветные металлы и сплавы на их основе. Титан и его сплавы. Алюминий и его сплавы. Магний и его сплавы. Медь и ее сплавы
- •5.7 Универсальные средства технических измерений
- •5.7.1 Механические измерительные приборы и инструменты
- •5.7.2 Оптические приборы
- •6.1 Общие понятия
- •4.2 Принципы построения системы допусков и посадок
- •4.3 Обозначения предельных отклонений и посадок на чертежах
- •4.4 Нормирование отклонений формы и расположения поверхностей деталей
- •4.4.1 Система нормирования отклонений формы и расположения поверхностей
- •4.4.2 Нормирование отклонений и допусков формы цилиндрических поверхностей
- •4.4.3 Нормирование отклонений и допусков формы плоских поверхностей
- •4.4.4 Нормирование отклонений и допусков расположения поверхностей
- •4.4.5 Нормирование суммарных отклонений и допусков формы и расположения поверхностей
- •4.4.6 Числовые значения и обозначение на чертежах допусков формы и расположения поверхностей
- •4.5 Система нормирования и обозначения шероховатости поверхности
- •Резание материалов 1.3 Кинематические схемы резания как основа формообразования.
- •2.1 Термины, определения и обозначения общих понятий
- •2.1.1 Процесс образования стружки
- •«Резание»
- •2.1.2 Условия, необходимые для осуществления процесса резания
- •2.2 Режимы резания в металлообработке
- •2.2.1 Элементы режима резания
- •Глубиной резания t (мм)
- •Движение подачи –
- •Результирующим движением резания
- •2.2.2 Количественная оценка скорости резания и подачи
- •Скоростью резания V (м/мин)
- •Линейной скорости точек заготовки или инструмента,
- •Подачей s
- •3.1 Типы режущих инструментов
- •Металлорежущий инструмент –
- •Тема 2 инструментальные материалы
- •§ 4 Характеристика современных инструментальных материалов
- •4.1 Общая характеристика инструментальных материалов
- •Инструментальными материалами
- •4.1.1 Физико-механические свойства инструментальных
- •4.2 Классификация инструментальных материалов
- •4.2.1 Углеродистые и низколегированные
- •4.2.2 Быстрорежущие стали
- •4.2.3 Твердые сплавы
- •4.3 Инструментальные материалы с износостойким покрытием
- •Тема 2. Основные принципы работы и конструктивные элементы режущих инструментов.
- •2.1. Требования к инструменту
- •Получение требуемого качества (точность и шероховатость) зависит:
- •Соответствие требованиям техники безопасности
- •Дополнительные требования к инструменту в условиях
- •Надежность в эксплуатации.
- •2.2. Классификация инструмента
- •Формообразование поверхности и схемы резания
- •Классификация по виду обработки
- •Классификация по направлению движения подачи
- •Классификация по инструментальному материалу
- •Классификация по конструкции резцов
- •Рабочая часть резцов
- •Твердость рабочей части
- •Геометрия резцов
- •Стружколомы
- •Твердосплавные резцы
- •Форма сменных пластин
- •Задний угол на пластине
- •Точность изготовления пластин
- •Тема 8. Инструмент для обработки отверстий
- •8.1. Кинематика резания
- •Спиральные сверла
- •Конструктивные параметры сверла
- •Геометрия сверла
- •Способы заточки спиральных сверл
- •Недостатки конструкции и методы улучшения геометрических параметров сверла
- •8.2.3.Центровочные сверла
- •8.2.4.Сверла, оснащенные твердым сплавом
- •8.2.5.Сверла для глубокого сверления
- •8.2.5.1.Шнековые сверла
- •8.2.5.2.Эжекторные сверла
- •8.2.5.3.С внутренним отводом стружки
- •8.2.5.4.Пушечные сверла
- •8.2.5.5.Ружейные сверла
- •8.2.5.6.Сверла для кольцевого сверления
- •Зенкеры и зенковки
- •8.3.1.Конструкция зенкера
- •8.3.2.Геометрия зенкера
- •8.3.3. Сборные зенкеры
- •Развертки
- •Конструкция развертки
- •Регулируемые развертки
- •Конические развертки
- •Расточной инструмент
- •Расточные резцы
- •8.5.1.1.Стержневые резцы
- •Тема 9. Фрезы
- •Классификация фрез
- •По расположению зубьев
- •9.1.3.По конструкции
- •9.2.2.Геометрия
- •9.2.2.Форма зубьев
- •9.3.Типы фрез
- •9.3.1.Цилиндрические фрезы
- •9.3.2.Торцовые фрезы
- •9.3.3.Концевые фрезы
- •9.3.4.Шпоночные фрезы
- •9.3.5.Дисковые и пазовые фрезы
- •9.3.6.Угловые фрезы
- •9.3.8.Сборные фрезы
- •9.4.Твердосплавные фрезы
- •Тгма 10. Резьбонарезной иструмент
- •10.Резьбонарезной инструмент
- •10.1.Резьбонарезные резцы
- •10.1.1.Типы резцов
- •10.1.1.1.Схемы резания
- •Боковое двухстороннее врезание (рис.11)
- •10.1.1.2.Геометрия
- •10.2.Метчики
- •10.2.1.Типы метчиков
- •10.2.2.Конструкция метчика
- •Комплектные метчики
- •Метчики с шахматным расположением резьбы
- •Метчик-протяжка
- •10.3.Плашки
- •Тема 7 зуборезный инструмент
- •§ 18 Методы формообразования зубчатых колес
- •18.1 Зубонарезание и зуборезный инструмент
- •18.1.1 Методы формообразования зубчатых колес
- •18.2 Инструменты, работающие по методу копирования
- •18.2.1 Дисковые модульные фрезы
- •18.2.2 Пальцевые модульные фрезы
- •18.2.3 Зуборезные головки
- •18.2.4 Протяжки
- •18.3 Инструменты, работающие по методу обката
- •18.3.1 Зуборезные долбяки
- •Тема 8 абразивные инструменты
- •§ 20 Конструктивные особенности абразивных инструментов
- •20.1 Технологические особенности шлифования
- •Абразивные инструменты –
- •20.1.1 Конструктивные особенности абразивного инструмента
- •20.1.2 Классификация абразивного инструмента
- •20.2 Конструктивные элементы абразивных инструментов
- •20.2.1 Форма и размеры
- •20.2.2 Шлифовальные материалы
- •20.2.3 Зернистость шлифовальных материалов
- •20.2.4 Структура шлифовального круга
- •20.2.5 Концентрация зерен
- •20.2.6 Твердость абразивных инструментов
- •20.2.7 Точность абразивных инструментов
- •20.2.8 Неуравновешенность шлифовальных кругов
- •20.2 Принципы выбора абразивных инструментов
- •20.4 Маркировка шлифовальных инструментов
- •1 А 1 300х40х76х5 ас4 100/80 100 бп2 2720-0139 гост 16167-80:
- •Г руппа 1. Токарные и токарно-винторезные станки
- •Основные технические характеристики 1к62
- •Т окарные автоматы, п/автоматы
- •Группа 2. Расточные станки
3.4.2 Кислородно-флюсовая резка
Процесс кислородно-флюсовой резки позволяет применить газокислородную резку для высоколегированных сталей толщиной до 500 мм, серого чугуна толщиной до 300 мм, меди толщиной до 50 мм и латуни толщиной до 150 мм. В зону реза одновременно с режущим кислородом вводят порошкообразные вещества, которые способствуют расплавлению или механическому удалению образующихся тугоплавких окислов из зоны реза. Основой для большинства флюсов, применяемых при резке, является железный порошок, к которому добавляют в зависимости от разрезаемого металла порошок феррофосфора и (или) алюминия.
Для кислородно-флюсовой резки применяют специальные установки, в комплект которых кроме резаков особой конструкции входит флюсопитатель для подачи флюса в режущую струю кислорода. Наибольшее распространение в промышленности получили установки типа УРХС (установка резки хромистых сталей).
Установка УРХС-5 (рисунок 3.21) предназначена для ручной разделительной кислородно-флюсовой резки одним резаком высоколегированных хромистых и хромоникелевых сталей толщиной 10 – 200 мм. Установка работает по схеме внешней подачи флюса из флюсопитателя 1 через циклонное устройство 2 и рукав 3 к резаку 6. В составе резака имеется флюсовая приставка и тележка с циркульным устройством, применяемая при вырезке заготовок круглой формы. Подача флюса регулируется вентилем 7.
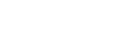
Рисунок 3.21 – Схема установки УРХС-5
Основная часть кислорода подается из кислородного баллона по шлангу 4 в резак, другая часть поступает в редуктор, после которого разветвляется на два направления: в верхнюю часть флюсопитателя для выдавливания из него флюсового порошка в циклонную камеру и в циклонную камеру, где захватывает флюс и по рукаву 3 доставляет в резак. Флюс перед засыпкой в бункер флюсопитателя просеивается через сито. Питание резака ацетиленом производится из ацетиленового баллона.
3.4.3 Плазменная резка
В последнее время начинают широко применять производительный процесс резки плазменной проникающей дугой (точнее – дугой сильно ионизированного газа), температура которой порядка 10000 – 300000С. Этот способ универсален относительно марки разрезаемого металла, им успешно режут коррозионно-стойкие стали, цветные металлы и сплавы, неметаллические материалы.
Установка для плазменной резки состоит из источника питания с аппаратурой управления процессом резки и инструмента-плазмотрона, основными элементами которого являются электрод и сопло. Плазмотроны изготавливаются для машинной и ручной резки с водяным и жидкостным охлаждением.
Рисунок
3.22 – Схема образования плазменной дуги
в головке плазмотрона
хема
получения плазменной дуги в плазмотроне
показана на рисунке 3.22. Дуговой разряд
возникает между вольфрамовым электродом
1 и металлом
заготовки 5.
Дуга горит в замкнутом цилиндрическом
канале 4,
стенки которого энергично охлаждаются
водой или сжатым воздухом. Через канал
под давлением подают плазмообразующую
газовую среду – воздух, аргон, азот,
смесь аргона и азота с водородом, аммиак.
Реже в данном качестве используется
вода, которая при высокой температуре
дуги превращается в пар и частично
диссоциирует на кислород и водород.
Вследствие сжатия газового (ионного)
проводника силами магнитного поля и
охлаждения наружной поверхности столба
дуги стенками канала, появляется
центральная тонкая плазменная струя 2
с высокой степенью ионизации, большим
избыточным давлением и температурой,
достигающей 10000 – 300000С.
Источники питания плазменной резки работают от сети переменного тока напряжением 380 и 220 В, преобразуют его в постоянный и подают на плазмотрон, обеспечивающий рабочее напряжение на дуге при ручной резке 120 – 150 В, при машинной – до 250 В. К плазмотрону подводят коммуникации с плазмообразующим газом (смесями газов) и охлаждающей средой.
Общий вид установки плазменной резки с программным управлением для раскроя листа толщиной до 150 мм и точностью позиционирования режущей головки (плазмотрона) 0,1 мм показан на рисунке 3.23.
Рисунок 3.23 – Установка плазменной резки с программным управлением
Размер стола 1700 х 3100 мм. Плазмотрон (на рисунке 3.23 у правой стойки) расположен на портале и может осуществлять координатное перемещение (вдоль стола за счет движения по направляющим портала, поперек стола за счет движения портала по приставным направляющим) относительно листа, размещаемого на столе.