
- •1 Машины и оборудование литейного производства
- •1.1 Общие сведения
- •1.2 Машины и оборудование литья в песчаные формы
- •1.2.1 Общая технологическая схема литья в песчаные формы
- •1.2.3 Модельные комплекты и опочная оснастка
- •1.3 Машины и оборудование специальных видов литья
- •1.3.1 Литье по выплавляемым моделям
- •1.3.2 Литье в оболочковые формы
- •1.3.3 Литье в металлические формы (кокили)
- •1.3.4 Литье под давлением
- •1.3.5 Центробежное литье
- •2 Машины и оборудование обработки металлов давлением
- •2.1 Общие сведения
- •2.4 Оборудование ковки
- •2.5 Оборудование горячей штамповки
- •3.4 Оборудование термической резки
- •3.4.1 Кислородная резка
- •3.4.2 Кислородно-флюсовая резка
- •3.4.3 Плазменная резка
- •Материаловедение. Особенности атомно-кристаллического строения металлов.
- •Металлы, особенности атомно-кристаллического строения
- •Понятие об изотропии и анизотропии
- •Аллотропия или полиморфные превращения.
- •Магнитные превращения
- •Лекция 2 Строение реальных металлов. Дефекты кристаллического строения
- •Лекция 3 Кристаллизации металлов. Методы исследования металлов.
- •Условия получения мелкозернистой структуры
- •Строение металлического слитка
- •Понятие о сплавах и методах их получения
- •Особенности строения, кристаллизации и свойств сплавов: механических смесей, твердых растворов, химических соединений
- •Классификация сплавов твердых растворов.
- •Кристаллизация сплавов.
- •Нагрузки, напряжения и деформации. Механические свойства.
- •Физическая природа деформации металлов.
- •Природа пластической деформации.
- •Дислокационный механизм пластической деформации.
- •Разрушение металлов.
- •Механические свойства и способы определения их количественных характеристик
- •Лекция 7 Механические свойства (продолжение).Технологические и эксплуатационные свойства
- •Механические свойства и способы определения их количественных характеристик: твердость, вязкость, усталостная прочность
- •Твердость по Бринеллю ( гост 9012)
- •Метод Роквелла гост 9013
- •Метод Виккерса
- •Основные характеристики:
- •Стали. Классификация и маркировка сталей.
- •Классификация и маркировка сталей Классификация сталей
- •Маркировка сталей
- •Классификация чугунов
- •Виды термической обработки металлов.
- •Лекция 14 Технологические особенности и возможности закалки и отпуска
- •Химико-термическая обработка стали
- •Назначение и технология видов химико-термической обработки: цементации, азотирования нитроцементации и диффузионной металлизации
- •Цветные металлы и сплавы на их основе. Титан и его сплавы. Алюминий и его сплавы. Магний и его сплавы. Медь и ее сплавы
- •5.7 Универсальные средства технических измерений
- •5.7.1 Механические измерительные приборы и инструменты
- •5.7.2 Оптические приборы
- •6.1 Общие понятия
- •4.2 Принципы построения системы допусков и посадок
- •4.3 Обозначения предельных отклонений и посадок на чертежах
- •4.4 Нормирование отклонений формы и расположения поверхностей деталей
- •4.4.1 Система нормирования отклонений формы и расположения поверхностей
- •4.4.2 Нормирование отклонений и допусков формы цилиндрических поверхностей
- •4.4.3 Нормирование отклонений и допусков формы плоских поверхностей
- •4.4.4 Нормирование отклонений и допусков расположения поверхностей
- •4.4.5 Нормирование суммарных отклонений и допусков формы и расположения поверхностей
- •4.4.6 Числовые значения и обозначение на чертежах допусков формы и расположения поверхностей
- •4.5 Система нормирования и обозначения шероховатости поверхности
- •Резание материалов 1.3 Кинематические схемы резания как основа формообразования.
- •2.1 Термины, определения и обозначения общих понятий
- •2.1.1 Процесс образования стружки
- •«Резание»
- •2.1.2 Условия, необходимые для осуществления процесса резания
- •2.2 Режимы резания в металлообработке
- •2.2.1 Элементы режима резания
- •Глубиной резания t (мм)
- •Движение подачи –
- •Результирующим движением резания
- •2.2.2 Количественная оценка скорости резания и подачи
- •Скоростью резания V (м/мин)
- •Линейной скорости точек заготовки или инструмента,
- •Подачей s
- •3.1 Типы режущих инструментов
- •Металлорежущий инструмент –
- •Тема 2 инструментальные материалы
- •§ 4 Характеристика современных инструментальных материалов
- •4.1 Общая характеристика инструментальных материалов
- •Инструментальными материалами
- •4.1.1 Физико-механические свойства инструментальных
- •4.2 Классификация инструментальных материалов
- •4.2.1 Углеродистые и низколегированные
- •4.2.2 Быстрорежущие стали
- •4.2.3 Твердые сплавы
- •4.3 Инструментальные материалы с износостойким покрытием
- •Тема 2. Основные принципы работы и конструктивные элементы режущих инструментов.
- •2.1. Требования к инструменту
- •Получение требуемого качества (точность и шероховатость) зависит:
- •Соответствие требованиям техники безопасности
- •Дополнительные требования к инструменту в условиях
- •Надежность в эксплуатации.
- •2.2. Классификация инструмента
- •Формообразование поверхности и схемы резания
- •Классификация по виду обработки
- •Классификация по направлению движения подачи
- •Классификация по инструментальному материалу
- •Классификация по конструкции резцов
- •Рабочая часть резцов
- •Твердость рабочей части
- •Геометрия резцов
- •Стружколомы
- •Твердосплавные резцы
- •Форма сменных пластин
- •Задний угол на пластине
- •Точность изготовления пластин
- •Тема 8. Инструмент для обработки отверстий
- •8.1. Кинематика резания
- •Спиральные сверла
- •Конструктивные параметры сверла
- •Геометрия сверла
- •Способы заточки спиральных сверл
- •Недостатки конструкции и методы улучшения геометрических параметров сверла
- •8.2.3.Центровочные сверла
- •8.2.4.Сверла, оснащенные твердым сплавом
- •8.2.5.Сверла для глубокого сверления
- •8.2.5.1.Шнековые сверла
- •8.2.5.2.Эжекторные сверла
- •8.2.5.3.С внутренним отводом стружки
- •8.2.5.4.Пушечные сверла
- •8.2.5.5.Ружейные сверла
- •8.2.5.6.Сверла для кольцевого сверления
- •Зенкеры и зенковки
- •8.3.1.Конструкция зенкера
- •8.3.2.Геометрия зенкера
- •8.3.3. Сборные зенкеры
- •Развертки
- •Конструкция развертки
- •Регулируемые развертки
- •Конические развертки
- •Расточной инструмент
- •Расточные резцы
- •8.5.1.1.Стержневые резцы
- •Тема 9. Фрезы
- •Классификация фрез
- •По расположению зубьев
- •9.1.3.По конструкции
- •9.2.2.Геометрия
- •9.2.2.Форма зубьев
- •9.3.Типы фрез
- •9.3.1.Цилиндрические фрезы
- •9.3.2.Торцовые фрезы
- •9.3.3.Концевые фрезы
- •9.3.4.Шпоночные фрезы
- •9.3.5.Дисковые и пазовые фрезы
- •9.3.6.Угловые фрезы
- •9.3.8.Сборные фрезы
- •9.4.Твердосплавные фрезы
- •Тгма 10. Резьбонарезной иструмент
- •10.Резьбонарезной инструмент
- •10.1.Резьбонарезные резцы
- •10.1.1.Типы резцов
- •10.1.1.1.Схемы резания
- •Боковое двухстороннее врезание (рис.11)
- •10.1.1.2.Геометрия
- •10.2.Метчики
- •10.2.1.Типы метчиков
- •10.2.2.Конструкция метчика
- •Комплектные метчики
- •Метчики с шахматным расположением резьбы
- •Метчик-протяжка
- •10.3.Плашки
- •Тема 7 зуборезный инструмент
- •§ 18 Методы формообразования зубчатых колес
- •18.1 Зубонарезание и зуборезный инструмент
- •18.1.1 Методы формообразования зубчатых колес
- •18.2 Инструменты, работающие по методу копирования
- •18.2.1 Дисковые модульные фрезы
- •18.2.2 Пальцевые модульные фрезы
- •18.2.3 Зуборезные головки
- •18.2.4 Протяжки
- •18.3 Инструменты, работающие по методу обката
- •18.3.1 Зуборезные долбяки
- •Тема 8 абразивные инструменты
- •§ 20 Конструктивные особенности абразивных инструментов
- •20.1 Технологические особенности шлифования
- •Абразивные инструменты –
- •20.1.1 Конструктивные особенности абразивного инструмента
- •20.1.2 Классификация абразивного инструмента
- •20.2 Конструктивные элементы абразивных инструментов
- •20.2.1 Форма и размеры
- •20.2.2 Шлифовальные материалы
- •20.2.3 Зернистость шлифовальных материалов
- •20.2.4 Структура шлифовального круга
- •20.2.5 Концентрация зерен
- •20.2.6 Твердость абразивных инструментов
- •20.2.7 Точность абразивных инструментов
- •20.2.8 Неуравновешенность шлифовальных кругов
- •20.2 Принципы выбора абразивных инструментов
- •20.4 Маркировка шлифовальных инструментов
- •1 А 1 300х40х76х5 ас4 100/80 100 бп2 2720-0139 гост 16167-80:
- •Г руппа 1. Токарные и токарно-винторезные станки
- •Основные технические характеристики 1к62
- •Т окарные автоматы, п/автоматы
- •Группа 2. Расточные станки
Рисунок 4.10 – Отклонения расположения поверхностей
Рассматривают также отклонение от параллельности осей в пространстве, отклонение от пересечения осей.
4.4.5 Нормирование суммарных отклонений и допусков формы и расположения поверхностей
Радиальное биение Δ поверхности вращения относительно базовой оси является результатом совместного проявления отклонения от круглости профиля рассматриваемого сечения и отклонение его центра относительно базовой оси. Оно равно разности наибольшего и наименьшего расстояний от точек реального профиля поверхности вращения до базовой оси в сечении, перпендикулярном этой оси (рисунок 4.11, а).
б)
а)
Рисунок
4.11 – Радиальное и торцовое биения
Торцовое биение – разность Δ наибольшего и наименьшего расстояния от точек всей торцовой поверхности до плоскости, перпендикулярной базовой оси; оно является результатом совместного проявления отклонения от плоскостности рассматриваемой поверхности и отклонения от ее перпендикулярности относительно базовой оси (рисунок 4.11, б).
4.4.6 Числовые значения и обозначение на чертежах допусков формы и расположения поверхностей
Для каждого вида допуска формы и расположения поверхностей и элементов установлено 16 степеней точности. Числовые значения допусков от одной степени к другой возрастают в 1,6 раза.
Допуски формы и расположения указываются индивидуально на чертеже детали в тех случаях, когда они должны быть меньше допусков размера для соответствующей поверхности по функциональным или технологическим причинам.
Допуски формы и расположения поверхностей и элементов, не указанные индивидуально, относятся к общим допускам формы и расположения, которые указываются на чертеже общей записью. Предусмотрено три класса точности: Н, К, L (по мере увеличения допуска), величина допуска в них зависит от интервала номинальных длин, на которых нормируется допуск.
Форма записи общих допусков формы и расположения:
"Общие допуски формы и расположения – ГОСТ 30893.2 – К" или
"ГОСТ 30893.2 – К".
В случае ссылки на общие допуски размеров, формы и расположения запись выполняется в виде:
"Общие допуски ГОСТ 30893.2 – mК" или " ГОСТ 30893.2 – mК".
Вид допуска формы и расположения обозначается знаками (графическими символами), указанными в таблице 4.1.
На чертеже детали знак, числовое значение допуска и, при необходимости, буквенное обозначение базы или поверхности, с которой связан допуск расположения, вписывают в рамку. Рамку соединяют с элементом, к которому относится допуск тонкой сплошной линией. Если допуск относится к оси или плоскости симметрии соединительная линия должна быть продолжением размерной линии; если допуск относится к общей оси, соединительную линию проводят к ней.
Перед числовым значением допуска указывается: символ Ø, если поле допуска задано его диаметром; символ R, если поле допуска задано радиусом; символ Т, если поле допуска симметричности, пересечения осей, формы заданной поверхности, а также позиционное поле допуска задано в диаметральном выражении; символ Т/2 – если они заданы в радиусном выражении; символ Ø или R, если поле допуска сферическое. Если допуск относится к участку поверхности заданной длины (площади), то ее значение указывают рядом со значением допуска через наклонную линию.
Таблица 4.1 – Условные обозначения допусков формы и расположения
Схемы указания допусков формы и расположения показаны на рисунке 4.12.
Рисунок 4.12 – Схемы указания допуска формы и расположения поверхностей
Базу, по отношению к которой нормируется допуск расположения, обозначают зачерненным треугольником (рисунок 4.13).
Если допуск формы или расположения зависимый, то дополнительно вводится обозначение М (рисунок 4.13), которое помещают:
- после числового значения допуска, если он связан с действительными размерами поверхности;
- после буквенного обозначения базы, а также и без ее обозначения в третьей части рамки, если допуск связан с действительными размерами базы;
- в обоих указанных местах, если допуск связан с их действительными размерами.
Рисунок
4.13 – Обозначение баз (а
– в) и
зависимого
допуска
(г)
в)
г)
б)
а)
в)
4.5 Система нормирования и обозначения шероховатости поверхности
Шероховатостью поверхности называют совокупность неровностей поверхности с относительно малыми шагами, выделенную с помощью базовой длины (рисунок 4.14).
Базовая длина l – длина базовой линии, используемая для выделения неровностей, характеризующих шероховатость поверхности. Базовая линия (поверхность) – линия (поверхность) заданной геометрической формы, определенным образом проведенная относительно профиля (поверхности) и служащая для оценки геометрических параметров поверхности.
Числовые значения шероховатости поверхности определяют от единой базы, за которую принята средняя линия профиля m, т. е. базовая линия, имеющая форму номинального профиля и проведенная так, что в пределах базовой длины среднее квадратическое отклонение профиля от этой линии минимально. Это отсчет по системе средней линии.
На базовой длине l другие неровности не учитываются (волнистость, отклонение формы), так как их шаг больше длины l. Измерение параметров шероховатости производят на одной или нескольких базовых длинах, по их результатам определяют среднее арифметическое значение параметра. Числовые значения базовых длин выбирают из ряда: 0,01; 0,03; 0,08; 0,25; 0,80; 2,5; 8; 25 мм.
Шероховатость поверхности можно оценивать одним или несколькими параметрами. Наиболее распространена оценка одним из двух параметров: Ra – средним арифметическим отклонением профиля и Rz – средней высотой неровностей по десяти точкам (рисунок 4.14).
Рисунок 4.14 – Профилограмма и основные параметры шероховатости
поверхности
Параметр Ra характеризует среднюю высоту всех неровностей профиля, Rz – среднюю высоту наибольших неровностей.
l n
Ra= 1/l ∫ [y(x)]dx или Ra= 1/nΣ|yi|, (1.7)
0 1
где l – базовая длина, n – число выбранных точек на базовой длине, y – расстояние между точкой профиля и средней линией.
5 5
Rz = 1/5[Σ|ypi| + Σ|yvi|, (1.8)
1 1
где |ypi| - высота i-го наибольшего выступа профиля, |yvi| - глубина i-ой наибольшей впадины профиля в пределах базовой длины.
Структура обозначения шероховатости поверхности приведена на рисунке 4.15, а.
Рисунок 4.15 – Структура обозначения шероховатости поверхности
В обозначении шероховатости поверхности, вид обработки которой конструктор не устанавливает, применяют знак, показанный на рисунок 4.16, а. Этот знак является предпочтительным. В обозначении шероховатости поверхности, образуемой удалением слоя материала, например, точением, фрезерованием и т. д. применяют знак, приведенный на рисунок 4.16, б. В обозначении шероховатости поверхности, образуемой без снятия слоя материала, например, штамповкой, литьем, применяют знак, показанный на рисунок 4.16, в. Поверхности, не обрабатываемые по данному чертежу, обозначают этим же знаком. Величина Н = (1,5…5)h.
в)
б)
а)
Рисунок
4.16 – Виды условных обозначений
шероховатости поверхности
Значение параметра шероховатости указывают в ее обозначении после соответствующего символа, например Rz10. Указываются наибольшие допустимые значения, диапазон значений указывается только при необходимости.
Обозначения шероховатости поверхностей на чертеже детали располагают на линии контура, выносных линиях, на полках линий-выносок (рисунок 4.17).
Рисунок
4.17 – Пример обозначения шероховатости
на размерных или выносных
линиях
При указании одинаковой шероховатости для всех поверхностей детали обозначение помещают в правом верхнем углу чертежа и на изображении не наносят (рисунок 4.18, а).
в)
б)
а)
Рисунок
4.18 – Примеры обозначения
повторяющихся
значений шероховатости поверхностей
детали
При указании одинаковой шероховатости для части поверхностей детали в правом верхнем углу чертежа помещают обозначение одинаковой шероховатости и знак, показанный на рисунок 4.18, б. Когда часть поверхностей детали не обрабатывается по данному чертежу, в правом верхнем углу чертежа помещают знаки в соответствии с рисунок 4.18, в.
Резание материалов 1.3 Кинематические схемы резания как основа формообразования.
Металлорежущие инструменты предназначены для изготовления различных деталей. При этом режущие кромки инструмента, внедряются непрерывно или последовательно в материал заготовки, срезая его в виде стружки. Поэтому при обработке резанием форма детали будет предопределяться:
формой и размерами режущих кромок, которыми инструмент срезает материал заготовки
движениями инструмента относительно заготовки.
Чтобы режущие кромки формировали обработанную поверхность, они должны располагаться на исходной инструментальной поверхности, касающейся в процессе обработки поверхности заготовки (рис. 1.4). Тогда деталь и инструмент можно представить как своеобразный механизм, состоящий из двух сопряженных звеньев. Траектории движений точек режущей кромки инструмента относительно заготовки как исходной поверхности детали – это результат сочетания движений, которые совершают на станке инструмент и обрабатываемая деталь.
Рисунок
1.4 Простейшие
схемы обработки деталей резанием: а
– точение;
б – строгание;
Dr
– главное
движение резания: вращательное или
поступательное; DS
– вспомогательное
движение резания или движение подачи;t
– глубина резания
Таким образом, рабочий процесс возможен только при непрерывном относительном взаимном перемещении обрабатываемой заготовки и лезвий режущего инструмента. Обрабатываемые заготовки и режущие инструменты приводятся во взаимосогласованные движения механизмами металлорежущих станков в соответствии с настройкой их кинематических цепей. Движения могут быть сообщены заготовке и инструменту одновременно, в последовательном порядке, чередуя движения каждого из них, а так же только одному из них – инструменту или заготовке.
Для осуществления процесса резания необходимо и достаточно иметь одно взаимное перемещение детали и инструмента. Однако для обработки поверхности одного взаимного перемещения, как правило, недостаточно. В этом случае бывает необходимо иметь два или более взаимосвязанных движений обрабатываемой детали и инструмента. Совокупность нескольких движений инструмента и обрабатываемой детали и обеспечивает получение поверхности требуемой формы. Движения, сообщаемые в процессе резания инструменту и заготовке, определяют кинематическую схему резания.
Количество движений, с помощью которых производится процесс резания, различно. В зависимости от количества и характера сочетаемых элементарных движений кинематические схемы резания были систематизированы Г.И. Грановским по группам [3]:
1) одно прямолинейное движение;
2) два прямолинейных движения;
3) одно вращательное движение;
4) одно вращательное и одно прямолинейное движение;
5) два вращательных движения;
6) два прямолинейных и одно вращательное движения;
7) два вращательных и одно прямолинейное движение;
8) три вращательных движения.
Любой реальный процесс резания входит в одну из этих групп. Например, строгание, протягивание – в первую группу: процесс резания осуществляется с помощью одного прямолинейного движения; точение, сверление, фрезерование плоских поверхностей – в четвертую группу: одно вращательное и одно прямолинейное движения; фрезерование тел вращения – в пятую: два вращательных движения; нарезание зубчатых колес методом обкатки – в седьмую: два вращательных и одно прямолинейное движение и т.д.
Наиболее простые кинематические схемы включают единственное прямолинейное движение. Например, при строгании и долблении в качестве режущих инструментов используют резцы (рис. 1.4, б). На продольно-строгальных станках прямолинейное движение в процессе резания совершает заготовка при неподвижном инструменте, а на поперечно-строгальных – резец при неподвижной заготовке. Когда резец еще не находится в контакте с заготовкой, происходит подача резца, а после этого начинается постепенное срезание материала заготовки. Также при протягивании инструмент движется прямолинейно, а заготовка остается неподвижной. Режущие зубья протяжки, увеличивающиеся от первого к последнему зубу, срезают материал заготовки и формируют обрабатываемую поверхность детали.
Наиболее распространены в промышленности схемы резания, основанные на сочетании одного вращательного и одного прямолинейного движения (рис. 1.6). Как мы уже видели, еще на заре развития техники нашла свое применение схема резания, включающая равномерное вращательное и равномерное прямолинейное движение, направление которого совпадает с осью вращения (рис. 1.6, а, б). В настоящее время на ней основаны такие методы обработки, как точение проходными и расточными резцами, нарезание резьбы резцами, метчиками и плашками, сверление, зенкерование и развертывание отверстий.
Рисунок
1.6 Элементы
движений в процессе резания: а
– при точении;
б
– при сверлении; в
– при фрезеровании
Широко распространена схема резания, основанная на комбинации вращательного движения и поступательного, направление которого перпендикулярно оси вращения (рис. 1.6, в). На этой схеме основаны процессы фрезерования плоских и фасонных поверхностей.
2.1 Термины, определения и обозначения общих понятий
2.1.1 Процесс образования стружки
Сущность технологии изготовления деталей машин состоит в последовательном использовании различных технологических способов воздействия на обрабатываемую заготовку с целью придания ей заданной формы и размеров указанной точности. Одним из таких способов является механическая обработка заготовок резанием. Она осуществляется металлорежущим инструментом и ведется на металлорежущих станках.
Обработка резанием заключается в удалении с обрабатываемой заготовки специально оставленной на обработку некоторой массы материала, называемой припуском
Припуск может удаляться одновременно с нескольких поверхностей заготовки или последовательно друг за другом с каждой обрабатываемой поверхности. В ряде случаев припуск может быть настолько большим, что его срезают не сразу, а за несколько проходов. После срезания с заготовки всего припуска, оставленного на обработку, заготовка прекращает свое существование и превращается в готовую деталь.
Материал, удаляемый в процессе резания с заготовки, подвергается пластическому деформированию и разрушению.
Материал припуска, отделенный от обрабатываемой заготовки, приобретает характерную форму и в таком виде его принято называть стружкой
Срезанная с заготовки стружка является побочным продуктом – отходом обработки материалов резанием.
Технология обработки материалов включает в себя последовательность действий: вначале инструмент режущей кромкой внедряется в массу заготовки; далее при своем движении инструмент передней поверхностью давит на верхний слой материала и отрывает его от основной массы заготовки. При этом срезаемый слой претерпевает сложную пластическую деформацию и, когда создавшиеся в этом слое напряжения превзойдут прочность металла, происходит относительный сдвиг частиц (скалывание). В это время образуется элемент стружки. Далее части припуска последовательно переходят в стружку.
Все способы и виды обработки материалов, основанные на срезании припуска и превращении его в стружку, составляют разновидности, определяемые термином
«Резание»
Таким образом, процесс резания – это последовательное срезание материала заготовки режущим инструментом и удаление его в виде стружки с целью получения детали определенной формы и размеров, заданных чертежом, и обеспечения определенного технологией качества поверхности.
2.1.2 Условия, необходимые для осуществления процесса резания
Для осуществления процесса резания необходимы как минимум следующие условия:
инструмент должен иметь соответствующую форму и рациональную геометрию заточки
твердость режущей части инструмента должна быть значительно выше твердости обрабатываемого материала
инструмент и заготовка в процессе резания должны перемещаться друг относительно друга строго по заданным траекториям
все взаимные перемещения должны происходить с определенными скоростями главного движения подачи в зависимости от различных технологических факторов и условий обработки.
2.2 Режимы резания в металлообработке
2.2.1 Элементы режима резания
Чтобы срезать слой металла, оставленный на заготовке как припуск на обработку, лезвия инструмента должны проникнуть в металл на глубину, равную этому припуску. В этом случае весь припуск срезается за один проход инструмента. Если припуск велик, то его срезают за два прохода и более.
Величину проникновения лезвий инструмента в металл заготовки во время каждого прохода принято называть
Глубиной резания t (мм)
В большинстве случаев обработки металлов резанием глубина резания определяется как расстояние между обрабатываемой и обработанной поверхностями, измеряемое в направлении, перпендикулярном обработанной поверхности (рис.1.4.)
При сплошном сверлении отверстий глубина резания равна радиусу сверла. При торцовом фрезеровании глубина фрезерования равна ширине обрабатываемой заготовки, если она меньше диаметра фрезы. При точении, расточке, рассверливании, развертывании отверстий глубина резания выражается уравнением
,
где D и d при наружной обточке соответственно диаметр обрабатываемой и обработанной поверхностей, а при внутренней обработке, наоборот, D – диаметр обработанной поверхности и d – диаметр обрабатываемой поверхности.
Совокупность нескольких движений инструмента и обрабатываемой детали и обеспечивает получение поверхности требуемой формы (см. рис. 2.1). При этом движение с наибольшей скоростью называется главным движением (Dr), а все остальные движения являются вспомогательными и определяют движения подачи (Ds). Главное движение может являться составным сложного формообразующего движения, например при зубонарезании. Движение подачи может быть непрерывным или прерывистым. В зависимости от направления движения различают продольную, поперечную, круговую и т.д.
Главное движение резания –
это прямолинейное поступательное или вращательное движение заготовки или режущего инструмента, происходящее с наибольшей скоростью
Движение подачи –
прямолинейное поступательное или вращательное движение режущего инструмента или заготовки, скорость которого меньше скорости главного движения резания. Движение подачи предназначено для того, чтобы распространить отделение слоя материала на всю обрабатываемую поверхность
Суммарное движение режущего инструмента относительно заготовки, включающее главное движение и движение
подачи, называется
Результирующим движением резания
Результирующее движение резания (De) является следствием нескольких одновременно осуществляемых движений: главного движения резания Dr со скоростью резания v, вспомогательного движения DS со скоростью подачи vS и движения формообразования (дополнительного движения). Большинство принципиальных кинематических схем резания предусматривает сочетание двух движений – главного движения и движения подачи. При сложных сочетаниях трех и более одновременно осуществляемых движений дополнительное движение определяет специфику формообразования, например, изготовление зубчатого венца методом обкатки.
2.2.2 Количественная оценка скорости резания и подачи
При реализации главного и вспомогательного движений станков необходима их количественная оценка. Главное движение, имея наибольшую скорость, определяет направление и скорость деформаций в материале срезаемого слоя и тем самым направление схода стружки и ее форму.
Скорость главного движения является
Скоростью резания V (м/мин)
Скорость резания может сообщаться как инструменту, так и обрабатываемой заготовке.
Если главное движение является вращательным, скорость резания количественно равна
Линейной скорости точек заготовки или инструмента,
находящихся во взаимодействии
Скорость резания определяется из уравнения
,
где D – диаметр обрабатываемой поверхности заготовки или рабочей поверхности инструмента, мм; n – частота вращения заготовки или инструмента, об/мин.
При количественной оценке движения подачи используется отношение расстояний, пройденных точками режущего лезвия в направлении движения подачи к соответствующему числу циклов (или их долей) главного движения, выражаемого численно
Подачей s
В зависимости от соотносимой единицы главного движения подача может выражаться:
в миллиметрах на оборот (мм/об), если устанавливается перемещение в направлении движения подачи, соответствующему одному обороту инструмента или заготовки, cсовершаемому во вращательном главном движении;
в миллиметрах на зуб (мм/зуб), если устанавливается перемещение в направлении движения подачи, соответствующее повороту инструмента на один угловой шаг его режущих зубьев;
в миллиметрах на двойной ход (мм/дв. ход), если перемещение соответствует одному двойному ходу заготовки или инструмента.
При выполнении отдельных операций удобно задавать подачу в мм/мин, как значение перемещения инструмента или заготовки в направлении движения подачи, совершаемого в течение одной минуты. Подачу принято обозначать латинской буквой S с индикацией, соответствующей используемым единицам: Sо, Sz, S₂x, S мин.
Таким образом, интенсивность процесса резания определяется напряженностью режима резания, который характеризуют три параметра:
глубина резания t (мм);
подача S (мм/об);
скорость резания v (мм/мин).
3.1 Типы режущих инструментов
Из теории резания известно, что в общем случае методы механической обработки характеризуются внедрением в поверхность обрабатываемой заготовки клинообразного твердого тела – режущей части инструмента, и перемещения его с силами, обеспечиваемыми приводом обрабатывающего оборудования, достаточными для образования стружки. При этом в зоне контакта режущего клина с поверхностью заготовки, происходит сложный физико-химический процесс пластической деформации поверхностного слоя, который приводит к преобразованию срезаемого слоя в стружку и отделению ее от заготовки в виде отходов материала. Инструмент, способный осуществить процесс механической обработки резанием заданного металла при заданных технических условиях, называют металлорежущим.
Металлорежущий инструмент –
орудие производства, предназначенное для изменения формы и размеров обрабатываемой заготовки из металла или другого конструкционного материала путём удаления части материала в виде стружки с целью получения готовой детали или полуфабриката
Несмотря на большое различие отдельных видов инструментов по назначению и конструкции, у них имеется много общего: условия работы, общие конструктивные элементы и алгоритм обоснования их выбора, принципы расчета конструктивных и геометрических параметров. Основные определения и обозначения общих понятий по режущим инструментам и обработке резанием даны соответственно в ГОСТ 25751 – 83 и ГОСТ 25762 – 83.
В зависимости от применяемого оборудования при осуществлении механической обработки различают станочный и ручной металлорежущий инструмент.
Станочный металлорежущий инструмент используют при условии возможности его использования с обеспечением привода станочного оборудования. В зависимости от технологического назначения он делится на следующие подгруппы: резцы, фрезы, протяжки, зуборезный, резьбонарезной, осевой режущий инструмент для обработки отверстий, абразивный и алмазный инструмент.
Резцы служат для лезвийной обработки резанием цилиндрических и плоских торцовых поверхностей тел вращения и применяются на токарных, токарно-револьверных, карусельных, расточных, строгальных, долбёжных и др. станках для обточки наружных поверхностей, расточки отверстий, обработки плоских и фасонных поверхностей, отрезания и прорезания канавок, нарезания наружной и внутренней резьбы.
Фрезы – многолезвийный вращающийся металлорежущий инструмент используют на фрезерных станках для обработки плоских и фасонных поверхностей, прямоугольных и фасонных пазов, профильного фрезерования на фрезерных станках и обрабатывающих центрах, а также для разрезки заготовок на разрезных станках.
Протяжки – многолезвийный инструмент для обработки гладких и фасонных внутренних и наружных поверхностей с линейной образующей и применяются, как правило, в массовом производстве, на протяжных станках, обеспечивающих высокую точность формы и размеров обработанной поверхности.
Для образования и обработки отверстий используют осевой режущий инструмент: сверла, зенкеры, зенковки, развертки, цековки, а также расточные резцы и комбинированный инструмент, который применяют на сверлильных, токарных, револьверных, расточных, координатно-расточных и др. станках.
Зуборезный инструмент предназначен для нарезания и обработки зубьев зубчатых колёс, зубчатых реек, червяков на зубообрабатывающих станках.
Резьбонарезной инструмент служит для получения и обработки наружных и внутренних резьб. Номенклатуру резьбонарезного инструмента составляют резьбовые резцы и фрезы, метчики, плашки и др. Инструмент используется как на специальных резьбообрабатывающих, так и на универсальных станках и станках с ЧПУ.
К абразивному инструменту относятся шлифовальные круги, бруски, хонинговальные головки, наждачные полотна и др., применяемые для шлифования, полирования, доводки деталей на шлифовальных станках, а также для заточки инструмента на заточных станках и станках с ЧПУ для вышлифовки осевого режущего инструмента.
Сверхтвердый инструмент с режущей частью из сверхтвердого инструментального материала – круги, резцы, фрезы и другой инструмент. Это может быть инструмент с режущей частью из алмазных пластин, который применяют для обработки труднообрабатываемых конструкционных материалов кроме углеродосодержащих, и кубического нитрида бора (эльбор) для обработки труднообрабатываемых сталей.
Рисунок
3.1 Станочный
металлорежущий инструмент:
1
- резец с механическим креплением
пластинки твёрдого сплава; 2 - винтовое
сверло; 3 - зенкер с коническим хвостовиком,
оснащенный твердосплавными пластинками;
4 - торцевая насадная фреза со вставными
ножами, оснащенными твёрдым сплавом;
5
- машинная развёртка с твердосплавными
пластинками;
6
-плашка; 7 - винторезная головка с круглыми
гребёнками;
8
- червячная фреза; 9 - шлицевая протяжка;
10 - резцовая головка для обработки
конических колёс с круговым зубом; 11 -
метчик;
12
—-зуборезный долбяк со спиральными
зубьями.
Ручной металлорежущий инструмент используют без металлорежущего оборудования. К ручным инструментам относятся зубила, напильники, надфили, ножовки, шаберы и др. В настоящее время получили распространение ручные машины с электрическим, гидравлическим и пневматическим приводом, рабочим органом которых являются ручные инструменты. Причем применение их значительно возросло не только в быту, но и на производстве из-за возможности механической обработки труднодоступных мест изделий (рис. 3.2).
Рисунок
3.2 Ручной
металлорежущий инструмент компании
PFERD,
Германия [24]: а
– напильники;
б –
борфрезы;
в
– инструмент
с алмазом и CBN; г
– шлифовальные
головки;
д
– приводные
устройства;
е
– пневматическая
машина с гибким валом; ж
– шлифовальная
машина с электрическим приводом
Современные ручные металлорежущие инструменты, снабженные электрическими, гидравлическими, пневматическими приводными устройствами, находят свое применение там, где поставлены высочайшие требования к эффективности обработки и качеству рабочего процесса. Инструмент применяется для таких операций металлообработки, как отрезка, шлифование, фрезерование, опиливание, полирование, очистка, обработка ржавчины, устранение заусенцев, маттирование.
Предпосылками для эффективного применения ручных инструментов являются оптимальное число оборотов приводных устройств и их соответствующая мощность. Основой экономичности применения современных ручных инструментов является возможность выбора продуктивного инструмента из широкого ассортимента.
Тема 2 инструментальные материалы
§ 4 Характеристика современных инструментальных материалов
План
4.1 Общая характеристика инструментальных материалов
4.2 Классификация инструментальных материалов
4.3 Инструментальные материалы с износостойким покрытием
4.1 Общая характеристика инструментальных материалов
Ранее отмечалось, что машиностроение в мировой практике всегда играло ведущую роль в развитии научно-технического потенциала страны, что значительного сокращения объема обработки конструкционных материалов резанием ожидать не приходится, так как с каждым годом конструктивные формы деталей усложняются, повышается их точность и требования к физико-механическим свойствам поверхностного слоя. Поскольку требования к точности машин и приборов стремительно повышаются, становится бесспорной перспективность развития процессов механической обработки. Их универсальность и гибкость обеспечивают преимущества перед другими способами изготовления деталей, особенно при производстве изделий небольшими партиями.
Очевидно, что процесс обработки металлов резанием является достаточно экономичным и эффективным. С целью увеличения производительности данного процесса все более широкое распространение получают станки с числовым программным управлением (ЧПУ), работающие с высокими скоростями резания. В соответствии с этим возрастают требования к режущему инструменту в части повышения периода стойкости, производительности и качества обработки. Основное место здесь принадлежит инструментальным материалам.
Разнообразие металлов и конструкционных материалов, применяемых в современном машиностроительном производстве, их классификация и принципы маркировки подробно описываются в дисциплинах «Технологические процессы в машиностроении» и «Материаловедение». В контексте данного курса рассматривается эффективность применения новых инструментальных материалов, разработанных и производимых у нас в стране и за рубежом.
Материалы, в той или иной мере отвечающие требованиям комплекса определенных физико-механических свойств и способные осуществлять резание, называются
Инструментальными материалами
4.1.1 Физико-механические свойства инструментальных
материалов, определяющие их режущую способность
Область рационального применения любого инструментального материала определяется совокупностью его эксплутационных свойств, а также экономическими факторами. К важнейшим эксплутационным свойствам инструментальных материалов относятся: твердость, прочность, износостойкость и теплопроводность.
Твердость контактных поверхностей инструмента должна быть выше твердости обрабатываемого материалов. Однако с увеличением твердости ухудшается сопротивляемость инструментального материала хрупкому разрушению. Поэтому для каждой пары обрабатываемого и инструментального материалов существует оптимальное значение отношения твердости инструментального материала к твердости обрабатываемого материала, при котором интенсивность износа инструмента минимальная.
Прочность инструментального материала представляет собой способность материала сопротивляться пластическому и хрупкому разрушению в условиях механических и тепловых, в том числе знакопеременных нагрузок. Прочность зависит от ударной вязкости, предела выносливости и предела текучести в условиях сжатия и изгиба, а также от законов изменения этих характеристик при увеличении температуры.
Износостойкость измеряется отношением работы, затраченной на удаление определенной массы инструментального материала, к величине этой массы. При абразивном изнашивании износостойкость определяется твердостью контактных поверхностей; при адгезионном – микропрочностью поверхностных слоев и склонностью к адгезии; при диффузионном изнашивании – степенью инертности инструментального материала по отношению к обрабатываемому.
Для характеристики режущих свойств инструментальных материалов при повышенных температурах пользуются понятиями красностойкости, теплостойкости, сопротивления тепловому удару и теплопроводности.
Под красностойкостью понимается температура, вызывающая снижение твердости инструментального материала не ниже заданного значения. Красностойкость быстрорежущих сталей составляет 620-640°С. Контрольная норма твердости после нагрева до таких температур, выдержки в течение 4 часов и последующего охлаждения составляет HRC 58.
Под теплостойкостью инструментального материала понимают его способностью сохранять при нагреве твердость, достаточную для осуществления процесса резания. Теплостойкость характеризуется так называемой критической температурой. Критическая температура – это температура, устанавливающаяся в процессе резания, при которой инструментальный материал еще не теряет своих режущих свойств, и инструмент, из которого он изготовлен, способен резать.
Сопротивление тепловому удару характеризует возможность разрушения инструмента в результате действия термических напряжений. Эта характеристика особенно важна в условиях использования относительно хрупких инструментальных материалов при прерывистом резании.
Теплопроводность инструментального материала определяет интенсивность теплоотвода из зоны резания, а следовательно, влияет на температуру контактных поверхностей инструмента.
Наиболее важным из технологических свойств инструментальных материалов является их обрабатываемость в горячем (ковка, штамповка, литье, сварка и др.) и холодном (резание) состояниях. Для закаливаемых материалов не меньшую значимость имеют условия их термической обработки: интервал закалочных температур, деформации при термообработке, склонность к перегреву и др.
Стоимость инструментального материала относится к экономическим факторам. Инструментальный материал должен быть по возможности дешевым. Однако, это требование условно, поскольку в ряде случаев более дорогой, но более качественный материал может обеспечить более экономичную обработку.
4.2 Классификация инструментальных материалов
Невозможно создать такой универсальный инструментальный материал, который был бы одинаково пригоден для всего многообразия условий механической обработки. Поэтому в промышленности используется широкая номенклатура инструментальных материалов, отвечающих рассмотренным выше требованиям.
Все инструментальные материалы подразделяются на следующие группы, ранжированные по степени повышения их режущих свойств:
Углеродистые и низколегированные инструментальные стали
Быстрорежущие стали
Твердые сплавы (металлокерамика) без покрытия и с покрытием
Минералокерамика и керметы;
Синтетические композиции из нитрида бора;
Синтетические и природные алмазы.
Сравнительные характеристики физико-механических свойств инструментальных материалов даны в таблице 4.1; график применяемости – на рисунке 4.2.
Таблица 4.1 Физико-механические свойства инструментальных материалов
Инструментальный материал |
Теплостойкость, °С |
Предел прочности при изгибе σВ, МПа |
1 |
2 |
3 |
Углеродистые стали |
200…250 |
1900…2000 |
Низколегированные инструментальные стали |
250…300 |
2000…2500 |
Быстрорежущие стали |
600…650 |
2050…3400 |
Твердые сплавы |
800…900 |
900…2000 |
Минералокерамика |
1100…1200 |
325…700 |
Алмазы |
700…800 |
210…400 |
Композиты КНБ |
1300…1500 |
400…1500 |
Следует отметить, что по применяемости в режущих лезвийных инструментах инструментальные материалы располагаются примерно следующим образом:
60…70 % приходится на быстрорежущие стали
20…30 % - на твердые сплавы
5…10 % - на остальные материалы.
Рисунок
4.1 Области
применения режущих материалов по
скорости резания v
и подаче s
[1]: 1
– быстрорежущие стали; 2
– твердые сплавы; 3
– твердые сплавы с покрытием; 4
– нитридная керамика; 5
– черная керамика (керметы);
6
– оксидная (белая) керамика; 7
– кубический нитрид бора
Высокий процент применяемости быстрорежущих сплавов объясняется главным образом их прочностными и технологическими свойствами, обеспечивающими высокую надежность и универсальность инструментов. На долю твердых сплавов, благодаря их высокой режущей способности, приходится более половины объема снимаемой стружки (рис. 4.1).
В настоящее время более 120 заводов-изготовителей во всем мире производят более 3500 сортов инструментальных материалов для режущего инструмента. В большинстве случаев марка материала не несет информации об ее химическом составе, за исключением России, Германии и еще нескольких стран.
4.2.1 Углеродистые и низколегированные
инструментальные стали
Вплоть до первого десятилетия XX века единственным инструментальным материалом, пригодным для изготовления металлорежущих инструментов, была углеродистая инструментальная сталь. Из-за низкой температуро- и износостойкости изготовленными из нее инструментами можно было обрабатывать углеродистые стали и чугуны с низкими скоростями резания (10…20 м/мин, в некоторых случаях до 30 м/мин) и невысоким эксплуатационным ресурсом.
Основным химическим элементом, определяющим физико-механические свойства углеродистых и низколегированных инструментальных сталей, является углерод. Углерод образует карбиды железа, которые в процессе термообработки активно участвуют в фазовых превращениях и образовании твердой мартенситной структуры.
Из группы углеродистых инструментальных сталей в инструментальном производстве наиболее широкое применение имеют стали марок У10А и У12А, содержащие 1,0…1,2 % углерода. Входящие в маркировку буквы обозначают: У – углеродистая инструментальная сталь, А – высшее качество выплавки (высококачественная).
Низколегированные стали, к которым относятся стали марок В2, Ф, 9ХС и ХВГ, по содержанию углерода соответствуют углеродистым инструментальным сталям, но дополнительно легированы небольшим количеством вольфрама, ванадия и других элементов. Незначительное количество в сталях обеих подгрупп хрома, марганца и кремния мало сказывается на эксплуатационных свойствах этих сталей. Эти компоненты входят в их состав для улучшения технологических свойств (литейных, закалочных и т.п.).
В связи с низкой температуростойкостью практическое использование углеродистых и низколегированных инструментальных сталей для изготовления из них режущих инструментов весьма ограничено. Из углеродистых инструментальных сталей изготавливают напильники, надфили и ножовочные полотна. Из углеродистых и низколегированных сталей изготавливают такие режущие инструменты, которые работают только с малыми скоростями резания – мелкоразмерные сверла, зенкеры, развертки, метчики и круглые плашки.
4.2.2 Быстрорежущие стали
В начале XX века была разработана первая высоколегированная инструментальная сталь. Эта сталь в качестве легирующих присадок содержала 18 % вольфрама, 4,5 % хрома и 1 % ванадия. По сравнению с углеродистой новая сталь имела значительно более высокие физико-механические свойства, в особенности температуро- и износостойкость. Металлорежущие инструменты изготовленные из этой стали могли обрабатывать стали и чугуны со скоростями резания 30…60 м/мин (в 2…2,5 раза выше, чем инструментами из углеродистых сталей). Благодаря этим качествам вновь разработанная сталь получила название быстрорежущей стали. По химическому составу она соответствует современной марке Р18.
Сейчас быстрорежущие стали представляют собой группу инструментальных сталей с повышенным содержанием вольфрама, молибдена и хрома. Кроме того, в ряде марок сталей, отличающихся повышенной теплостойкостью, дополнительно вводится определенное количество ванадия и кобальта.
В настоящее время в России выпускается более 30 марок быстрорежущих сталей, в США – более 25 марок, большое количество марок и в других странах. В большинстве случаев, за исключением России, Германии и некоторых других стран, обозначение марки быстрорежущей стали не несет информации о химическом составе, определяющим режущие свойства инструмента. Например, в США быстрорежущие стали делятся на две группы: М (молибденовые) и Т (вольфрамовые). Разные марки сталей обозначаются этими буквами с соответствующими индексами.
В России принято буквенно-цифровое обозначение, отражающее примерное процентное содержание основных легирующих элементов. Например, P12Ф2К8М3 означает: Р – сталь быстрорежущая; буквы Ф, К, М означают, соответственно, ванадий, кобальт, молибден; цифра, стоящая после буквы Р, означает примерное содержание вольфрама, остальные цифры означают содержание соответствующих легирующих элементов.
В мировых стандартах быстрорежущие стали обозначаются следующим образом:
HSS – быстрорежущая сталь
HSSV – быстрорежущая сталь, легированная ванадием
HSCo – быстрорежущая сталь, легированная кобальтом
CS – сталь, легированная хромом и др.
Согласно стандарту ISO, наряду с обозначениями, принятыми в национальных стандартах, в специальной технической литературе используется условное обозначение быстрорежущих сталей в виде набора цифр, расположенных в строго определенном порядке и показывающих среднее содержание основных легирующих элементов: W – Мо – V – Co. Для сталей с повышенным содержанием углерода впереди ставится буква S. Например, сталь Р6М5К5 обозначается S-6-5-2-5. Большинство марок быстрорежущих сталей содержат в своем составе хром в количестве 3,5-5,0 %.
Основным легирующим элементом в большинстве быстрорежущих сталей является вольфрам. Теплостойкость стали тем выше, чем больше растворяется карбидов в аустените при нагреве под закалку.
Рассмотрим влияние легирующих элементов на свойства быстрорежущей стали, их определяющую роль при назначении режимов резания и обработке различных конструкционных материалов.
Стали с высоким содержанием карбидов вольфрама (12-18 %) и малым содержанием других легирующих элементов отличаются широким интервалом закалочных температур, малой чувствительностью к перегреву и хорошей обрабатываемостью. Однако вольфрам является дорогостоящим и дефицитным материалом, запасы которого постоянно и быстро уменьшаются во всем мире. Поэтому во всех странах в последнее время создаются быстрорежущие стали, в которых часть вольфрама заменяется другими легирующими элементами, в частности, молибденом.
Молибден и вольфрам образуют однотипные карбиды. Замену вольфрама молибденом проводят обычно в сочетании 2:1. Одной из наиболее распространенных в мировой практике сталей такого типа является сталь 6-5-2 (Р6М5). С уменьшением содержания вольфрама и увеличением содержания молибдена увеличивается ее прочность, вязкость и теплопроводность. Однако вольфрамомолибденовые стали обладают большей склонностью к обезуглероживанию, меньшей стабильностью режущих свойств и допускают более узкий интервал закалочных температур, т.е. требует более высокой технологии инструментального производства.
Для улучшения режущих свойств быстрорежущих сталей в их состав вводятся ванадий и кобальт. При содержании ванадия более 1 % он находится в стали в виде несвязанных карбидов, обладающих большей твердостью, чем карбиды вольфрама. Поэтому ванадиевые стали отличаются более высокой износостойкостью при сравнительно низких скоростях резания. Однако, с увеличением содержания ванадия, уменьшается теплопроводность стали. Поэтому при высоких скоростях резания они практически не имеют преимуществ перед вольфрамовым и молибденовым сталями. Кроме того, низкая теплопроводность может быть причиной образования дефектного слоя в процессе заточки контактных поверхностей инструмента, что также приводит к снижению его стойкости. Содержание ванадия в сталях может доходить до 5 %. Ванадиевые стали наиболее эффективны для инструментов, предназначенных для чистовой обработки, а также для инструментов, работающих с низкими скоростями резания (развертки, протяжки, шеверы и д.р.).
Быстрорежущие стали с содержанием кобальта более 5 % называются кобальтовыми. Кобальт не образует карбидов, однако способствует большему растворению карбидов вольфрама и молибдена, а также образует с этими металлами очень твердые интерметаллические соединения. Теплостойкость кобальтовых сталей доходит до 650°С, теплопроводность на 25-30 %выше, чем у ванадиевых сталей. Однако этим сталям присуща повышенная хрупкость и склонность к обезуглероживанию при нагреве. Кроме того, кобальт, как и вольфрам, является дефицитным материалом. Поэтому содержание кобальта в быстрорежущих сталей редко превышает 10 %.
Увеличение содержания углерода на 0,1-0,2 % позволяет увеличить теплостойкость сталей на 15-20°С и твердость на 2-2,5 HRC. Однако при этом увеличивается склонность к обезуглероживанию при нагреве.
Следует отметить, что во всех случаях химический состав быстрорежущих сталей должен быть хорошо сбалансирован. Повышение концентрации кобальта, ванадия, углерода и других элементов затрудняет их металлургический передел, операции обработки давлением и приводит к увеличению карбидной неоднородности.
Инструмент из быстрорежущих сталей имеет широкое распространение до настоящего времени, тем более что за историю своего развития они получили значительное улучшение эксплуатационных и режущих свойств.
Коренное улучшение структуры быстрорежущих сталей, практически однородное распределение карбидов при малых размерах зерен (до 1-2 мкм), стали возможными при освоении производства порошковых сталей. Оно включает в себя следующие этапы: получение мелкозернистого порошка путем распыления расплава быстрорежущей стали; получение цельного слитка из порошка путем горячего или холодного прессования в специальных тонкостенных контейнерах; пластическая деформация слитка для получения требуемого профиля заготовки.
Порошковые стали, по сравнению с обычными того же состава, характеризуется повышенной вязкостью, прочностью, плотностью, более низкими температурами, меньшими размерными деформациями и лучшей шлифуемостью. В этих сталях содержание ванадия может быть доведено до 7-8,5 % и углерода до 2-2,8 % без увеличения карбидной неоднородности. Однако эти стали обладают худшей обрабатываемостью резанием и имеют в 1,5-2 раза большую стоимость.
Из порошковых быстрорежущих сталей изготавливают инструменты сложного профиля, больших размеров, с минимальными деформациями после термической обработки (фасонные резцы, протяжки, червячные фрезы и т.п.).
Как правило, инструмент из быстрорежущей стали приобретает свои режущие свойства в результате термической обработки и последующих операций шлифования и заточки. Тем не менее, существуют методы дальнейшего улучшения режущих свойств таких инструментов путем химико-термической обработки. Такие методы (например, азотирование – насыщение поверхностного слоя азотом; цианирование – насыщение одновременно азотом и углеродом) позволяют увеличить твердость поверхностных слоев при достаточно вязкой сердцевине, повысить износостойкость и снизить коэффициент трения. Химико-термическая обработка проводится в твердых, жидких или газообразных средах при температурах, не вызывающих фазовых превращений в закаленных быстрорежущих сталях.
Увеличение работоспособности инструментов из быстрорежущих сталей достигается в ряде случаев нанесением на контактные поверхности износостойких покрытий карбидов и нитридов тугоплавких металлов пластическим деформированием, хромированием поверхностей, обработкой холодом и другими методами.
4.2.3 Твердые сплавы
Технология производства первых вольфрамо-кобальтовых твердых сплавов состояла в расплавлении компонентов и отливке пластинок, припаиваемых к корпусу инструмента. Исследования резцов с припаянными пластинками литого вольфрамо-кобальтового твердого сплава показали, что их режущие свойства не намного выше, чем из инструментов из быстрорежущих сталей. Рентабельность практического использования твердых сплавов ставилась под сомнение. Дело коренным образом изменилось, когда исследователи отказались от технологии расплавления и перешли к применению методов порошковой металлургии. Твердосплавные пластинки, изготовленные по этой технологии, имели высокие физико-механические свойства и оказались весьма эффективным инструментальным материалом. В США, Германии и СССР приблизительно в одно и то же время (во второй половине 20-х годов) твердые сплавы, изготовленные по технологии порошковой металлургии, были выпущены как товарная продукция. Эти сплавы, полученные из карбидов вольфрама и металлического кобальта (группа ВК), в США назывались, как и производящая их фирма, «карболой», в Германии на заводах Крупа – «видиа», т.е «как алмаз», в СССР они получили название «победит». Все эти твердые сплавы оказались превосходным материалом для обработки чугунов, но совершенно непригодны для обработки сталей.
В настоящие время твердые сплавы представляют наиболее широкий класс инструментальных материалов. Они обладают высокой твердостью и износостойкостью, сохраняющимися при высоких температурах, значительным пределом прочности при сжатии, хорошей теплопроводностью. Замена быстрорежущего инструмента твердосплавным позволяет повысить уровень скоростей резания в 2-3 раза или увеличить стойкость его в 3-5 раз. На передовых промышленных предприятиях доля токарного твердосплавного инструмента достигает 80 %, фрезерного 60 %.
Твердые сплавы представляют собой продукты порошковой металлургии, состоящие из зерен карбидов тугоплавких металлов (WС, TiC, TaC), скрепленных вязкой металлической связкой. В качестве связки чаще всего используется кобальт, отличающейся хорошей способностью смачивать карбиды вольфрама. В твердых сплавах, не содержащих WC, в качестве связки используется никель с добавками молибдена. Карбиды WC, TiC, TaC обладают высокой твердостью и тугоплавкостью. Чем больше в твердом сплаве карбидов, тем выше его твердость и теплостойкость, но ниже механическая прочность. При увеличении содержания кобальта увеличивается прочность, но твердость и теплостойкость снижаются.
Все твердые сплавы можно разделить на 4 группы:
вольфрамовые, спекаемые из карбидов вольфрама и кобальта (ВК)
титано-вольфрамовые, состоящие из карбидов титана, карбидов вольфрама и кобальта (ТК)
титано-тантало-вольфрамовые, спекаемые из карбидов титана, карбидов тантала, карбидов вольфрама и кобальта (ТТК)
безвольфрамовые, не содержащие карбидов вольфрама КНТ016; ТН020 (в западной технической литературе последнюю группу называют титановыми сплавами).
Технологии изготовления всех видов инструментальных твердых сплавов примерно одинаковы. Прежде всего, необходимо получить исключительно чистое сырье – карбиды и металлы в виде тонкодисперсных порошков. Затем производятся размол и смешивание порошков в необходимой концентрации. После добавления пластификатора из приготовленной смеси прессуются заготовки. Окончательной операцией является спекание, заключающееся в нагреве заготовок до 1350-1550°С, выдержке при этой температуре и последующем охлаждении. При спекании плавится металлическая фаза, обволакивая и частично растворяя зерна карбидов. После остывания получается монолитное изделие с минимальной пористостью и относительно равномерными свойствами по объему. В случае необходимости поверхности режущих пластин или заготовок инструментов подвергаются шлифованию и доводке.
Вольфрамовые твердые сплавы состоят из твердого раствора кобальта в карбиде вольфрама и избыточных кристаллов карбидов вольфрама. В России сплавы этой группы обозначаются буквами ВК, где В означает вольфрам, К – кобальт. Цифра, стоящая за буквой К, означает процентное содержание кобальта, остальное – карбиды вольфрама. Например, ВК6 означает 6 % Со, 94 %WC. Буквы, стоящие за цифрой, означают: М – мелкозернистый сплав, ОМ – особо мелкозернистый, К – крупнозернистый.
Сплавы группы ВК могут содержать от 98 до 80 % WC при соответствующем увеличении содержания кобальта, что приводит к уменьшению твердости, но увеличивает прочность и ударную вязкость. Критическая температура, допускаемая сплавами ВК, составляет 800-850°С.
Эти сплавы используются в условиях обработки, характеризующихся сравнительно низкими температурами и меняющейся во времени нагрузкой. Это обработка чугуна, бронзы, а также резание высокопрочных нержавеющих никелевых и титановых сталей и сплавов.
Увеличение размеров зерен карбидов по сравнению с обычными (3-5 мкм) приводит к увеличению относительной толщины прослойки кобальтовой фазы, а следовательно, к увеличению прочности сплава. При уменьшении размеров зерен увеличивается твердость и износостойкость. Кроме того, у инструментов из мелкозернистых сплавов удается получить более острую режущую кромку.
Титано-вольфрамовые твердые сплавы при содержании TiC менее 15 % имеют структуру, состоящую из твердого раствора WC в TiC, твердого раствора Co в WC и TiС, а также избыточных карбидов WC. Если в сплаве более 15 % TiC, то весь вольфрам растворяется в TiC и структура состоит из твердого раствора WC в TiC и твердого раствора Со в WC и TiC.
В России сплавы этой группы обозначаются буквами ТК, где Т со следующей за ней цифрой означают процентное содержание TiC, К – процентное содержание Со, остальное WC.
Твердость и теплостойкость твердых сплавов группы ТК выше, чем у сплавов ВК. Критическая температура достигает 850-900°С. Содержание TiC меняется в разных сплавах от 5 до 30 %, при этом содержание кобальта соответственно меняется от 4 до 12 %. С увеличением содержания кобальта увеличивается прочность, но уменьшается твердость.
Твердые сплавы группы ТК используются при чистовой и черновой обработке сталей в условиях образования сливной стружки. При неравномерной нагрузке, больших припусках и повышенных требованиях к надежности инструмента используются сплавы с большим содержанием кобальта.
Титано-тантало-вольфрамовые твердые сплавы являются универсальными и могут использоваться при обработке сталей и чугунов, особенно в условиях прерывистого резания. Критическая температура для сплавов этой группы равна 750°С. Основными их преимуществами являются более высокая прочность по сравнению по сплавами ТК и меньшая стоимость по сравнению со сплавами ВК.
Принятое в России обозначение группы ТТК означает: ТТ со следующей за ними цифрой – процентное содержание TiC и TaC, К – процентное содержание Со, остальное WC.
Безвольфрамовые твердые сплавы (керметы) имеют в своем составе в качестве износостойкой фазы карбиды и карбонитриды титана, а в качестве связки применяют никель с добавками молибдена и ниобия. Кроме того, сплавы содержат в небольшом количестве карбиды других элементов. Керметы изготавливаются только в виде пластин. Безвольфрамовые сплавы обладают примерно одинаковой твердостью с титано-вольфрамовыми, но превосходят их по окалино-стойкости. Образующаяся на их поверхности при резании пленка окислов прочно сцеплена с основой и играет роль твердой смазки. Кроме того, безвольфрамовые сплавы мало склонны к адгезионному взаимодействию, что особенно важно при обработке никелевых и других вязких материалов.
К недостаткам безвольфрамовых сплавов следует отнести более низкие по сравнению с титано-вольфрамовыми сплавами значения модуля упругости, теплопроводности, а также более высокий коэффициент термического расширения, что предопределяет их более высокую чувствительность к ударным и тепловым нагрузкам.
Для твердых сплавов, как наиболее распространенных для металлообработки, Международной организацией стандартов ISO разработана система классификаций по группам применяемости, которые в свою очередь делятся на подгруппы применения в зависимости от условий обработки (табл. 4.2).
Таблица 4.2 Классификация материалов по ISO
ISO |
Обрабатываемый материал |
Типичный представитель |
Твердость |
1 |
2 |
3 |
4 |
Р |
Сталь |
Низколегированная |
HB 180 |
Окончание таблицы 4.2
1 |
2 |
3 |
4 |
|
|
сталь |
|
М |
Нержавеющая сталь |
Аустенитная нержавеющая сталь |
HB 180 |
К |
Чугун |
Серый чугун Чугун с шаровидным графитом |
HB 220 HB 250 |
N |
Алюминиевые, медные сплавы, неметаллы, пластмассы |
Литье, не подвергнутое старению |
HB 75 |
S |
Жаропрочные сплавы |
Никелевые сплавы |
HB 350 |
Н |
Сверхтвердая сталь |
Закаленная и отпущенная |
HRC 60 |
После буквы, обозначающей обрабатываемый материал, ставится индекс 01, 10, 20, 25, 30, 40, 50. Увеличение индекса соответствует увеличению прочности и уменьшению износостойкости твердого сплава. Кроме букв, группы маркируются цветом: Р – синий, М – желтый, К – красный, N – зеленый, S – оранжевый, Н – серый.
Все ведущие фирмы-изготовители наряду с товарной маркой своего сплава указывают его соответствие той или иной группе и подгруппе применяемости по ISO.
В приложении В приведена таблица соответствия некоторых типичных марок металлов по ISO и ГОСТ.
Основными путями улучшения качества твердых сплавов являются совершение технологии их изготовления и совершенствование состава. Так, легирование сплавов ВК карбидами хрома и ванадия позволяет резко ограничить рост зерен при спекании, а следовательно, увеличить прочность кобальтовой связки. Замена карбидов тантала карбидами гафния и ниобия, имеющими более высокую износостойкость при равной прочности, позволяет увеличивать работоспособность твердых сплавов и снизить их стоимость. Легирование рутением позволяет расширить диапазон применяемости сплавов группы Р30 от Р25 до Р40, особенно в условиях прерывистого резания.
В России наибольшее распространение получили безвольфрамовые сплавы КНТ016 и ТН020, применяемые вместо сплавов Т15К6, Т14К8 и ВК8 при обработке конструкционных, нержавеющих и инструментальных сталей. Увеличение объема производства и потребления безвольфрамовых твердых сплавов связано с дефицитом вольфрама и кобальта. Поэтому в США, Германии, Японии, России и других промышленно-развитых странах постоянно проводятся исследования в целях разработки новых безвольфрамовых твердых сплавов и замены ими традиционных инструментальных материалов. Так, в США фирма «Adamas Carbide Co» выпускает безвольфрамовые сплавы Titan 50,60,80,100 на основе карбидов титана и молибдена. В порядке увеличения номера увеличивается прочность сплавов Titan. Сплавы Titan100 имеет прочность 1000 МПа и по своим режущим свойствам конкурирует с режущей керамикой.
4.3 Инструментальные материалы с износостойким покрытием
Эффективным способом повышения стойкости режущего инструмента является нанесение на его рабочие поверхности износостойких покрытий. В этом случае получаем сочетание:
хорошие физико-механические свойства покрытий: твердость; красностойкость; слабое адгезионное взаимодействие с обрабатываемым материалом
положительные свойства инструментального материала: термодинамическая прочность основы.
Сегодня промышленность располагает достаточно большим арсеналом методов нанесения износостойких покрытий, из которых в инструментальном производстве наиболее широко применяются методы химического осаждения покрытий из газовой фазы – Chemical Vapour Deposition (CVD) и физического осаждения покрытий в вакууме – Physical Vapour Deposition (PVD).
К разновидностям метода CVD относятся:
высокотемпературное осаждение покрытий – high-temperature (HT-CVD)
среднетемпературное осаждение покрытий – medium-temperature (MT-CVD)
осаждение покрытий с плазменным сопровождением – plasma assisted (PA- CVD).
К разновидностям метода PVD относятся:
электронно-лучевое испарение
вакуумно-дуговое испарение
магнетронное распыление.
Методы PVD и CVD существенно различаются по температурам и давлениям, при которых они реализуются, по составам наносимых покрытий, а также по областям применения (рис. 4.2; табл. 4.3).
Рисунок
4.2 Схемы
многослойных покрытий твердосплавных
пластин
По ISO твердые сплавы без покрытия, содержащие в основном карбид вольфрама (WC) обозначаются HW; безвольфрамовые твердые сплавы без покрытия (керметы), содержащие в основном
карбиды или нитриды титана (TiC, TiN) или и те, и другие вместе, обозначаются НТ; твердые сплавы с покрытием – НС.
Таблица 4.3 Свойства и области применения некоторых покрытий
Покрытие |
Цвет |
Свойства, особенности и область применения |
1 |
2 |
3 |
TiN |
золотис-тый |
Благодаря простой технологии получения и невысокой стоимости исходных материалов получило наиболее широкое промышленное применение. Обладает твердостью по Виккерсу 22-25 ГПа и коэффициент трения по стали 0,55. |
|
|
Применяется для всех видов режущих инструментов при резании конструкционных сталей и сплавов нормальной обрабатываемости. |
Продолжение таблицы 4.3
1 |
2 |
3 |
|
TiCN |
серо-голубой |
Обладает высокой твердостью по Виккерсу – до 37 ГПа, имеет низкий коэффициент трения по стали – 0,25, но имеет относительно невысокую стойкость к окислительному износу и является достаточно хрупким. Применяется для чистовой обработки конструкционных сталей и сплавов нормальной обрабатываемости. |
|
(Ti,Al)N |
бронзо- вый |
Характерной особенностью является образование в процессе резания на его поверхности слоя Al2O3, служащего тепловым барьером. Обладает повышенной стойкостью к окислительному износу, высокой твердостью по Виккерсу – до 37 ГПа и имеет коэффициент трения по стали 0,6. Применяется для операций с большими термическими нагрузками – при высокоскоростной обработке, резании материалов с пониженной теплопроводностью, а также обработки твердых материалов, в том числе без применения СОЖ. |
|
CrN |
сереб- ристый |
Обладает высокой пластичностью, хорошими трибологическими свойствами. Имеет твердость по Виккерсу не более 143 ГПа и коэффициент трения по стали 0,3. Применяется для снижения налипания материала заготовки на режущий инструмент при обработке мягких металлов – алюминия, меди и сплавов на их основе. |
|
MoS2 |
черный |
Является трибологическим покрытием, обладающим достаточно низкой твердостью, но имеющим чрезвычайно низкий коэффициент трения (до 0,05). Применяется для обработки материалов без использования СОЖ, а также для обработки цветных металлов и сплавов. |
Окончание таблицы 4.3
(Ti,Cr)N |
золотис- то-серый |
Свойства и область применения аналогичны покрытию TiN, но является более пластичным, что делает предпочтительным его применение для инструментов, эксплуатирующихся в условиях ударно-циклических нагрузок и больших сечений срезаемого слоя. |
Сравнительные исследования работоспособности инструмента с износостойким покрытием показали, что нанесение на инструмент многослойных покрытий является перспективным в этой области. Установлено, что эффективность применения многослойных покрытий зависит от числа слоев, их химического состава, а так же от последовательности их расположения по отношению к покрываемой основе.
Анализ результатов показывает, что верхний слой покрытия из Al2O3 обеспечивает повышение износостойкости пластин, особенно в случае введения второго слоя Al2O3, расположенного около покрываемой основы. Удаление слоя из TiC от основы способствует повышению прочности пластин.
Наряду с применением многослойных покрытий совершенствуется их структура, определяется их оптимальная толщина. Так, на твердосплавных пластинах, предназначенных для фрезерования, толщина покрытий в 2 раза меньше по сравнению с толщиной покрытий на пластинах для токарной обработки. В этом случае структура покрытия не колончатая, а зернистая, что позволяет выдерживать требуемый радиус округления режущей кромки. Кроме того, снижается опасность образования трещин и замедляется или прекращается разрастание микротрещин вглубь основы.
Следует отметить, что для наиболее эффективного применения режущего инструмента с износостойким покрытием необходимо отрабатывать технологические процессы нанесения покрытий на конкретные виды инструмента.
Тема 2. Основные принципы работы и конструктивные элементы режущих инструментов.
(Принцип работы режущих инструментов. Составные части инструментов: крепежная и рабочая, требования предъявляемые к ним .Конструкция и геометрические параметры режущей части. Влияние конструктивных параметров режущей части на процесс резания и формирования обработанной поверхности.)
Режущий инструмент – та часть металлорежущих станков, которая непосредственно изменяет форму и размеры обрабатываемой детали, как правило, путем срезания стружки.
2.1. Требования к инструменту
Работоспособность – способность осуществлять обработку резанием. Обеспечивается:
материалом режущей части и его свойствами,
геометрическими параметрами инструмента.
Получение требуемой формы и размеров обеспечивается:
конструкцией инструментов,
размерами профиля режущих кромок,
способом крепления и базирования,
возможностью регулирования исполнительных размеров.
Получение требуемого качества (точность и шероховатость) зависит:
от схемы резания,
геометрии инструмента,
качества рабочих поверхностей режущего лезвия,
режима обработки,
наличия СОС (смазывающе-охлаждающей среды).
Экономическая эффективность предполагает минимум приведенных затрат на операции использования инструмента. Этот обобщенный критерий раскладывается на составляющие:
Высокая производительность характеризуется объемом металла, срезаемого в единицу времени. Высокую производительность обеспечивают следующие свойства инструмента:
возможность работы на высоких режимах и с большой суммарной длиной режущих кромок;
возможность быстрой замены после затупления или другим инструментом;
возможность быстрой размерной настройки вне станка.
высокая стойкость, которая зависит от материала режущей части, конструкции, геометрии и т.д.
Высокая экономичность инструмента достигается
уменьшением первоначальной стоимости инструмента (повышение технологичности, малый расход дорогостоящих материалов);
увеличением срока службы (повышение надежности, стойкости и числа переточек);
экономичность восстановления режущих свойств;
возможность переработки отработанного инструмента;
простота и полнота утилизации отходов инструментального материала.
Малая энергоемкость резания – минимальный расход электроэнергии на единицу объема срезаемого материала в единицу времени (малая мощность резания). Достигается уменьшением ширины срезаемого слоя с одновременным увеличением его толщины при прочих равных условиях. Оптимизация геометрических параметров.
Удобство в обращении (установка на станке, хранение, транспортировка)
Соответствие требованиям техники безопасности
Дополнительные требования к инструменту в условиях
автоматизированного производства
Надежность в эксплуатации.
Универсальность.
Гибкость.
Возможность быстрой замены.
Точность и надежность базирования при установке на станке.
Возможность и быстрота размерной настройки.
Ограниченность номенклатуры компонентов.
Получение стружки удобной для отвода из зоны резания.
2.2. Классификация инструмента
В общем классификаторе продукции (ОКП) инструмент отнесен к 39 классу. Обозначение (код ОКП) включает 10 знаков:
Подклассы и группы приведены в таблице. Каждая группа подразделяется на подгруппы и виды.
Группа |
Подкласс и его состав |
|
39 1000 |
39 2000 |
|
1 |
- |
Резцы |
2 |
Сверла |
Пилы круглые |
3 |
Метчики |
Протяжки |
4 |
- |
Инструмент зуборезный |
5 |
Плашки (резьбонарезные) |
Резьбонакатной и головки резьбонарезные |
6 |
Зенкеры |
Инструмент слесарно-монтажный |
7 |
Развертки |
- |
8 |
Фрезы |
Инструмент зажимной |
9 |
- |
Напильники и борфрезы |
Пример обозначения сверл спиральных быстрорежущих с цилиндрическим хвостовиком средней серии правых, диаметром 1,55 мм, обычного исполнения, без поводка: 39 1213 3121.
Геометрия инструмента
Системы координат
Инструментальная система координат
Прямоугольная система координат с началом в вершине режущего лезвия, ориентированная относительно базы крепления. Применяется для изготовления и контроля инструмента.
Статическая система координат
Прямоугольная система координат с началом в рассматриваемой точке режущей кромки, ориентированная относительно вектора скорости главного движения. Применяется для определения изменения геометрии инструмента при его установке на станке.
Кинематическая система координат
Прямоугольная система координат с началом в рассматриваемой точке режущей кромки, ориентированная относительно вектора скорости результирующего движения. Применяется для определения геометрии инструмента в процессе резания.
Координатные плоскости
Pv - Основная плоскость перпендикулярна
вектору скорости главного движения (статическая система координат);
вектору скорости результирующего движения (кинематическая система координат).
В инструментальной системе координат Pv ориентирована относительно базы крепления инструмента.
Pn - Плоскость резания - касательная к режущей кромке в рассматриваемой точке и перпендикулярная к основной плоскости.
Pτ - Главная секущая плоскость – перпендикулярная к линии пересечения основной плоскости и плоскости резания.
Ps - Рабочая плоскость – плоскость, в которой расположены векторы скоростей главного движения и движения подачи.
Углы
Передний угол – угол в секущей плоскости между передней поверхностью и основной плоскостью. Влияет на процесс стружкообразования и прочность режущего лезвия. С увеличением переднего угла уменьшается степень деформации срезаемого слоя и снижается прочность режущего лезвия.
Задний угол – угол в секущей плоскости между задней поверхностью и плоскостью резания. Увеличение заднего угла снижает силы трения по задней поверхности и прочность режущего лезвия.
Угол заострения – угол в секущей плоскости между передней и задней поверхностями резца.
Угол в плане - угол в основной плоскости между плоскостью резания и рабочей плоскостью. Влияет на размеры срезаемого слоя, составляющие силы резания, теплоотвод, прочность вершины и шероховатость обработанной поверхности.
Угол наклона режущей кромки – угол в плоскости резания между режущей кромкой и основной плоскостью. Влияет на условия первоначального контакта инструмента и заготовки, и направление схода стружки.
Формообразование поверхности и схемы резания
При обработке любым инструментом применяется одна из трех схем резания:следа, копирования, огибания.
По схеме следа обработанная поверхность образуется траекторией движения точки( вершины инструмента) в направлении подачи.
По схеме копирования форма обработанной поверхности соответствует форме режущей кромке инструмента (необходимо рассчитывать координаты точек,лежащих на кромке инструмента)
По схеме огибания форма поверхности образуется каждой точкой режущей кромки инструмента при взаимном перемещения инструмента и детали. .
Тема 5. Резцы общего назначения.
(Принципы работы и основные понятия о конструктивных элементов резцов.Конструкция резцов,требования,предъявляемые к кострукции, резцы составные и сборные, материал рабочей и крепежной частей. Методика выбора резцов для различных методов обработки.)
5.1.Рабочие движения резцов
Резцы - однолезвийный режущий инструмент для обработки с вращательным или поступательным главным движением и возможностью движения подачи в любом направлении.
. Область применения резцов
Резцы применяются на станках:
токарных;
револьверных;
карусельных;
расточных;
строгальных;
долбежных.
Классификация резцов
Классификация резцов по характеру обработки
черновые ( Sо = 0,4…0,8 мм/об; t = 4…10 мм);
получерновые; ( Sо = 0,2…0,4 мм/об; t = 1,5…4 мм);
чистовые (Sо = 0,2…,04 мм/об; t = 1,5…4 мм);
для тонкого точения (Sо = 0,05…0,2 мм/об; t= 0,2…2 мм),
где Sо – подача на оборот, t – глубина резания.
Классификация по конструкции головки
прямые; отогнутые; оттянутые, когда
режущее лезвие
смещено относительно оси симметрии державки вправо или влево;
изогнутые – ось резца изогнута в
боковой проекции;
Классификация по виду обработки
проходные резцы для обработки наружных поверхностей тел вращения
упорные
(угол φ=
900)
для обработки
ступенчатых
и нежестких валиков
нежестких
валиков
отогнутые
для работы
с продольной и поперечной
подачами
прямые
для работы
с продольной подачей
подрезные резцы для обработки торцовых поверхностей;
расточные резцы для обработки внутренних поверхностей
проходные упорные канавочные
отрезные резцы; ● прорезные торцовые;
фасонные резцы для обработки деталей сложного профиля;
резьбовые резцы для нарезания наружных и внутренних резьб
для наружной обработки для внутренней обработки
Классификация по направлению движения подачи
Правые – такие, у которых при наложении ладони правой руки на переднюю поверхность резца (указательный палец направлен к вершине резца), главная режущая кромка расположена со стороны большого пальца
левые– такие, у которых при наложении ладони левой руки на переднюю поверхность резца (указательный палец направлен к вершине резца) главная режущая кромка расположена со стороны большого пальца.
правый левый
Радиальные - с поперечной подачей в радиальном направлении
Тангенциальные - с подачей по касательной к обработанной поверхности.
радиальный резец тангенциальный резец
Классификация по инструментальному материалу
Быстрорежущие резцы
Твердосплавные резцы
Керамические резцы
Резцы из сверхтвердых материалов
Классификация по конструкции резцов
Цельные резцы (монолитные)
Составные резцы с неразъемным соединением частей
сваркой,
пайкой,
склеиванием.
Напайные резцы используются в случаях, когда невозможно или не рационально применение сборных конструкций.
Достоинства напайных резцов:
возможность изготовления требуемой формы и размеров рабочей части;
возможность получения требуемых значений углов резания, т.к. они получаются заточкой;
Недостатки:
внутренние термические напряжения.
Требования к конструкции:
Гнездо под режущую пластину должно обеспечить минимальные напряжения в результате пайки.
Угол врезания пластины (λ) желательно иметь больше переднего угла – это ускоряет переточку и уменьшает расход твердого сплава.
На стойкость и прочность напайных резцов кроме размерных параметров влияет правильность геометрической формы опорной поверхности пластины. Наличие выпуклости и вогнутости опорной поверхности приводит к неравномерной толщине слоя припоя между пластинкой и корпусом, неравномерному распределению напряжений, а выпуклость опорной поверхности способствует возникновению изгибающих деформаций.
Сборные резцы с механическим (разъемным) соединением составляющих элементов:
с механическим креплением вставок с напаянными твердосплавными пластинками;
с механическим креплением неперетачиваемых поворотных твердосплавных пластин;
с механическим креплением вставок с механически закрепленными пластинами;
Достоинства:
высокие режимы и стойкость (нет термических напряжений);
снижение потерь времени на смену инструмента, заточку и переточку;
быстрая смена инструментального материала при переходе на обработку других материалов;
стабильное формирование и отвод стружки;
постоянство размера;
удлиняется срок службы державки.
Недостатки:
ограниченность технологических возможностей (изменение геометрии ограничено возможностями пластин;
увеличение габаритных размеров;
выше стоимость ,т.к. они:
сложнее в изготовлении,
требуют повышения точности.
Рабочая часть резцов
Твердость рабочей части
Для резцов из быстрорежущих сталей определяется режимами термообработки и химическим составом сталей и для вольфрамовых и вольфрамомолибденовых сталей должна быть HRCэ 62…65, а для кобальтовых, ванадиевых и кобальтованадиевых быстрорежущих сталей с массовой долей ванадия не менее 3% и кобальта не менее 5% - HRCэ 63…67.
Твердость рабочей части резцов из твердых сплавов, минералокерамики и сверхтвердых материалов определяется свойствами этих материалов.
Геометрия резцов
Передний угол γ зависит от свойств обрабатываемого материала и материала инструмента.
С увеличением прочности и твердости обрабатываемого материала оптимальный передний угол уменьшается, а с увеличением прочности инструментального материала – возрастает.
Передние углы заметно влияют на интенсивность вибраций. С уменьшением γ вибрации усиливаются.
При работе с толщиной среза а > 0,2 мм на передней поверхности целесообразно делать фаску шириной от 0,2 до 1,0 мм (табл.1.).
Таблица 1.
|
Ширина фаски |
γф |
γ |
Быстрорез |
f = а |
00 …50 |
250 … 300 |
Твердый сплав |
f = (1,5…2) а |
-50 …-100 |
100 … 250 |
При обработке хрупких материалов, форма передней поверхности с фаской неэффективна.
Задний угол α служит для уменьшения трения между задней поверхностью и поверхностью резания.
Чрезмерное увеличение заднего угла приводит к снижению прочности и ухудшению теплоотвода. Обычно угол α принимают равным 6…12
Оптимальное значение α, обеспечивающее максимальную стойкость, зависит от толщины срезаемого слоя. С увеличением толщины срезаемого слоя оптимальный задний угол уменьшается.
При обработке твердых и прочных материалов величины задних углов уменьшаются, а при обработке легких сплавов - увеличиваются.
Для уменьшения вибраций при обработке задние углы приходиться уменьшать.
Главный угол в плане φ влияет:
на размеры поперечного сечения срезаемого слоя;
на стойкость резца;
на шероховатость обработанной поверхности.
Угол φ выбирают в зависимости от жесткости станка и заготовки, а также от типа и конструкции резца. Его значения находятся в пределах
10 ≤ φ ≤ 100
Угол наклона режущей кромки λ оказывает влияние:
на направление схода стружки;
на последовательность вступления в работу различных точек режущей кромки;
на ее активную длину;
на плавность врезания и выхода режущей кромки из контакта с заготовкой.
Значения угла λ находятся в пределах −15 ≤ λ ≤ +45. При λ >6 резко возрастают силы Py и Pz (а Pх - уменьшается), что предъявляет повышенные требования к жесткости системы СПИД.
Р
адиус закругления вершины резца r влияет на работу резца примерно так же, как и углы в плане.
С увеличением r
прочность режущей кромки у вершины возрастает,
стойкость повышается,
шероховатость обработанной поверхности снижается.
Но при этом резко возрастает Pу , что способствует увеличению отжима заготовки и появлению вибраций.
Оформление передней поверхности:
плоская – для обработки прочных сталей, чугуна, хрупких материалов,
ломанная,
криволинейная – способствует завиванию стружки. С увеличением толщины срезаемого слоя радиус выемки увеличивается. Рекомендуется при обработке мягких, пластичных сталей, вязких цветных металлов и легких сплавов.
Стружколомы
При определенных условиях обработки (вязкий обрабатываемый материал, режимы резания и т.п.) образуется сливная (длинная непрерывная стружка).
Это затрудняет процесс резания, опасно для станочника, создает проблемы со стружкоотводом и ее хранением. Для получения короткой стружки (обычно длиной в несколько сантиметров – рис.) используют стружколомание.
Стружколомание и стружкозавивание необходимо при скоростном точении, при обработке труднообрабатываемых материалов и особенно на станках с ЧПУ и автоматических линиях.
Виды стружколомания
В процессе резания благодаря правильно выбранным геометрии инструмента и параметрам режима резания
От соприкосновения с задней поверхностью пластины или корпуса резца. Может привести к поломке режущей пластины
При контакте с обрабатываемой деталью, что может привести к увеличению шероховатости
Стружка ломается о специальный стружколом, прикрепленный на режущий инструмент или станок.
Виды стружколомов:
Уступы и лунки на передней поверхности, получаемые в процессе изготовления пластинки или инструмента.
Не универсальны, так как их параметры зависят от конкретных условий обработки (обрабатываемого материала, подачи).
Накладные стружколомы
нерегулируемые, из твердого сплава и припаянные к передней поверхности пластины (г),
регулируемые - более эффективны при различных режимах обработки (д, е).
Твердосплавные резцы
Форма сменных пластин
Правильный
трехгранник,
наиболее универсальная пластинка,
может использоваться в резцах,
работающих с врезанием и с продольной
подачей в прямом и обратном
направлении, а с точки зрения удельного
расхода твердого сплава на одну режущую
кромку наиболее экономичны. Недостатком
этой формы является малая прочность
вершины
Пластинки
неправильной трехгранной формы
имеют усиленную вершину, но уменьшенную
длину режущей кромки, а также увеличенный
удельный расход твердого сплава по
сравнению с предыдущей.
Пластинки
квадратной формы
достаточно универсальны при среднем
удельном расходе сплава на одну режущую
кромку, производительны и эффективны.
Наиболее распространенная форма для
резцов из минералокерамики
Пластины
пятигранной и шестигранной формы
не эффективны при работе врезанием,
используются для черновых и проходных
резцов, удельный расход твердого сплава
на режущую кромку достаточно велик, но
в проходных резцах он компенсируется
повышенной стойкостью резцов, что
объясняется высокой прочность пластины.
В зарубежной практике пятигранные
пластины практически не применяются,
а шестигранные имеют ограниченное
применение.
Пластинки
ромбической и параллелограммной
формы
используются при контурной обработке
и в этом случае оказываются достаточно
эффективными, хотя с точки зрения
рационального использования длины
режущей кромки и удельного расхода
твердого сплава они уступают пластинкам
других форм.
Задний угол на пластине
Пластинки без заднего угла (типа N) называют отрицательными. Некоторые пластинки этого типа можно использовать в перевернутом положении, получая дополнительные режущие кромки
Пластинки с задним углом называют положительными.
Точность изготовления пластин
Механическое крепление пластин накладывает определенные требования к точности их изготовления. В зависимости от точности исполнения пластины выпускаются четырех степеней:
нормальной степени точности (U), шлифованные по ленточкам и опорным поверхностям;
повышенной степени точности (М) – то же, что и нормальные, но с более жесткими допусками;
высокой степени точности (G) – шлифованные по опорным и боковым поверхностям;
особо высокой степени точности - шлифованные по опорным и боковым поверхностям с более жесткими допусками.
Пластинки нормальной степени точности (U) применяются в стандартных резцах; (M) и (G) – в резцах, оснащенных минералокерамикой.
Применение пластинок более высокой, чем (U), степени точности целесообразно в условиях автоматизированного производства, когда за счет повышения точности изготовления как пластинки, так и корпуса резца без подналадок обеспечивается высокая точность расположения режущих кромок резца относительно станка.
Тема 8. Инструмент для обработки отверстий
(Особенности обработки отверстий: удаление стружки, увод инструмента, охлаждение. Конструкция иструменьов: сверла, зенкеры, развертки, расточной инструмент, Выбор инструмента в зависимости от параметров обработанной поверхности.)
8.1. Кинематика резания
Главное движение – вращение инструмента или заготовки относительно оси обрабатываемого отверстия
Движение подачи – поступательное перемещение вдоль оси вращения
Результирующее движение - винтовое
Методы получения отверстий
Существует три основных метода получения отверстий:
сверление в сплошном материале – образование отверстия определенного диаметра в сплошном материале за одну операцию. Наиболее распространенный метод.
кольцевое сверление также выполняется за одну операцию. В заготовке вырезается кольцевая полость, а в середине остается сердечник. При обработке больших диаметров снижается расход мощности и снижается осевая сила.
рассверливание – увеличение диаметра отверстия с целью повышения его точности и снижения шероховатости.
Сверла
Сверло – осевой режущий инструмент для обработки отверстий в сплошном материале и увеличения диаметра имеющегося отверстия (Рис.1).
Рис.1. Спиральное сверло
Спиральные сверла
Спиральные сверла используются для обработки отверстий диаметром до 80 мм, обеспечивают точность, соответствующую 11…12 квалитету, и шероховатость Rz =40…160 мкм.
Рис.2.
Конструкция спирального сверла
Рабочая часть состоит из
режущей части с двумя главными режущими кромками, которая предназначена для срезания всего припуска;
направляющей части предназначенной для направления сверла в работе, обеспечивающей удаление стружки и служащей запасом на переточку.
Хвостовик служит для закрепления сверла на станке. Может быть цилиндрическим (для сверл малого диаметра) или коническим. Конические хвостовики обеспечивают передачу большего крутящего момента, лучше центрируют и позволяют быструю установку.
Шейка облегчает шлифование хвостовика.
Лапка для облегчения выбивания сверла из патрона станка
Конструктивные параметры сверла
(Рис.2.)
Диаметр сверла D выбирается с учетом неизбежной разбивки обрабатываемого отверстия.
Для уменьшения трения на направляющей части выполняют обратную конусность, т.е. диаметр сверла уменьшается от вершины к хвостовику. Угол обратного конуса φ΄ 1΄… 4΄, больший угол недопустим из-за значительного изменения диаметра при переточках.
Длина рабочей части l0 сверла зависит от глубины сверления и запаса на переточку l0 ≥ l + 3D (l – глубина отверстия). С увеличением длины рабочей части количество переточек сверла возрастает, но снижается жесткость сверла и стойкость между переточками. Для обработки прочных материалов желательно выбирать короткие сверла.
Выемка по затылку зуба t выполняется для уменьшения трения сверла об обработанную поверхность, t =0,1…1,2 мм.
Винтовые ленточки предназначены для направления сверла в процессе резания. Ширина ленточки f должна быть минимальной и выбирается в зависимости от диаметра сверла. f = 0,3…2,6 мм.
Поперечная кромка – линия пересечения задних поверхностей двух зубьев сверла. Она характеризуется длиной и углом ψ между осью симметрии сверла и направлением проекции поперечной кромки на плоскость, перпендикулярную оси сверла. Ψ = 550
Поперечная кромка – неблагоприятный элемент конструкции сверла. Из-за наличия большого угла резания поперечная кромка не режет, а скоблит и выдавливает материал.
Диаметр сердцевины dс влияет на прочность и жесткость сверла и на величину поперечной кромки. Увеличение dс с одной стороны повышает стойкость за счет увеличения жесткости, с другой стороны при этом увеличивается длина поперечной кромки – увеличивается работа резания, тепловыделение и стойкость снижается. Оптимальный d сопт обеспечивает максимальную стойкость сверла d сопт = (0,12…0,2)D. Для увеличения жесткости dс увеличивается от вершины к хвостовику, т.е. сердцевина выполняется конической.
Стружечная канавка. Ее размеры и профиль выбираются из условия обеспечения прочности сверла и достаточного пространства для стружки. Профиль канавки создается профилем фасонной фрезы, накатных роликов или других инструментов, определяется графически или рассчитывается.
Геометрия сверла
(рис.3.)
Угол конуса при вершине 2φ определяет производительность и стойкость сверла. Играет роль главного угла в плане, подобно ему влияет на составляющие силы резания, длину режущей кромки и параметры сечения срезаемого слоя.
При уменьшении 2φ сила подачи снижается, а крутящий момент возрастает. Длина режущей кромки увеличивается – отвод тепла улучшается. Толщина стружки уменьшается. Снижается прочность вершины сверла. Угол 2φ выбирается экспериментально в зависимости от обрабатываемого материала.
Рис.3. Геометрия спирального сверла
Угол наклона винтовой стружечной канавки ω измеряется на наружном диаметре сверла
,
где
Pz - шаг винтовой стружечной канавки.
От угла ω зависят:
сход стружки, с увеличением этого угла отвод стружки улучшается;
прочность и жесткость сверла, с увеличением ω жесткость на изгиб снижается, а жесткость на кручение возрастает;
величина переднего угла, с увеличением ω передний угол возрастает.
Международная организация по стандартизации ISO рекомендует три типа сверл:
тип Н для обработки хрупких материалов с ω = 10…160;
тип N для обработки материалов, дающих элементную стружку с
ω = 25…350;
тип W для обработки вязких материалов (алюминий, медь и т.п.) с
ω = 35…450
Передний угол γ главных режущих кромок в рабочей плоскости 0-0 (рис.3.) для каждой точки режущей кромки равняется углу наклона винтовой канавки на диаметре рассматриваемой точки:
,
где
ωА – угол наклона винтовой канавки в данном сечении.
Передний угол в главной секущей плоскости N-N
,
Как видно из формулы, передний угол зависит от угла ω и уменьшается на режущей кромке от периферии к центру. На поперечной кромке передний угол имеет отрицательные значения.
Задний угол принято рассматривать в рабочей плоскости О-О (Рис.3.).
Кинематический задний угол ρ (Рис.4.) определяют как угол между винтовой траекторией результирую-щего движения резания и касательной к задней поверхности ρi = i – μi , где μi – угол скорости резания
Угол скорости резания увеличивается с ростом подачи и уменьшением диаметра рассматриваемой точки. Для выравнивания кинематических задних углов инструментальный задний угол делают переменным вдоль режущей кромки. На периферии он равен 8…140 , а у сердце-вины 20…250
Рис.4. Геометрия задней поверхности сверла
Способы заточки спиральных сверл
(рис.5).
Рис. 5. Схемы заточки сверл.
Одноплоскостная (г) – наиболее простая в технологическом плане, но требует больших задних углов, дает прямолинейную поперечную кромку, не обеспечивающую правильного центрирования сверла при работе без кондуктора. Значения заднего угла и угла наклона поперечной кромки зависят от угла при вершине и заднего угла на периферии. Используют для мелких сверл диаметром до 3 мм.
Двухплоскостная (д)- устраняет возможность затирания поверхности детали. Распространена для заточки твердосплавных сверл
Коническая форма (а, б ) - обеспечивает изменение инструментальных задних углов вдоль режущей кромки, способ (б) дает более резкое изменение этих углов, поэтому он более распространен.
Винтовая форма(в) – позволяет получить более рациональное распределение значений задних углов и более выпуклую поперечную кромку сверла, что улучшает самоцентрирование сверла. Возможна автоматизация процесса заточки.
Недостатки конструкции и методы улучшения геометрических параметров сверла
Недостатки:
уменьшение переднего угла к центру сверла;
неблагоприятная геометрия на поперечной кромке;
отсутствие заднего угла на вспомогательной режущей кромке;
большое тепловыделение и плохой теплоотвод на периферийных участках режущей кромки, их повышенный износ.
Способы подточки спиральных сверл
(Рис.6.)
Рис. 6. Методы подточки спиральных сверл
Двойная заточка режущей кромки уменьшает износ наиболее напряженного участка режущей кромки за счет уменьшения толщины срезаемого слоя на периферии и улучшения теплоотвода.
Подточка поперечной кромки уменьшает ее длину, облегчается резание, повышается стойкость сверла. Рекомендуется для обработки сталей малой и средней твердости, особенно для крупных сверл.
Подточка цилиндрических ленточек – создается задний угол (в = 6…80) на вспомогательной режущей кромке на небольшой длине 1,5…5 мм. Приводит к увеличению стойкости до 2…3 раз.
Образование стружкоразделительных канавок на передней поверхности сверла не требует их восстановления после заточки
Образование стружкоразделительных канавок на задней поверхности сверла проще в изготовлении, но канавки после переточки приходится восстанавливать. Наличие стружкоразделительных канавок дает повышение стойкости до 2 раз за счет улучшения отвода стружки. Рекомендуется при глубоком сверлении.
Подточка передней поверхности проводится у сверл с малыми углами ω у центра сверла с целью увеличения переднего угла. У сверл с большими углами ω подточка передней поверхности выполняется на периферии с целью уменьшения переднего угла и увеличения прочности режущего лезвия.
8.2.2.Перовые сверла (Рис.7.)
Режущая часть выполнена в виде пластины.
Обладают повышенной жесткостью.
Применяются для обработки поковок, ступенчатых и фасонных отверстий (б) и отверстий малых диаметров (меньше 1…1,5 мм).
Для уменьшения трения калибрующая часть имеет вспомогательный задний угол 1 = 5…100 и утонение по диаметру 0,05…0,1 мм на всю длину сверла.
Достоинства:
повышенная жесткость,
Рис.7. Перовые сверла
простота конструкции.
Недостатки:
большие отрицательные передние углы, требующие подточки по передней поверхности, но она снижает прочность сверла;
плохое направление сверла в отверстии;
малое число возможных переточек.
8.2.3.Центровочные сверла
Предназначены для сверления центровых отверстий.
Изготовляют двухсторонними.
Относятся к комбинированным инструментам, т.к. одновременно обрабатывают несколько поверхностей.
Рис.8. Центровочные сверла
8.2.4.Сверла, оснащенные твердым сплавом
Обеспечивают повышение производительности до двух раз по сравнению с быстрорезом.
Предъявляют повышенные требования к жесткости и виброустойчивости системы СПИД.
Длина твердосплавных сверл меньше, чем у сверл из быстрорежущей стали, что способствует повышению жесткости, кроме того, число переточек твердосплавных сверл ограничено и соответствует длине твердосплавной пластинки.
Цельные
П
рименяются для обработки отверстий малого диаметра
(3…20 мм).
Могут иметь отверстия для внутреннего подвода СОЖ.
Глубина сверления (2…5)D.
Для повышения прочности и жесткости диаметр сердцевины увеличивают до (0,22…0,3)D.
С напайной пластинкой
Для обработки отверстий диаметром 17…30 мм.
Для повышения стойкости на длине твердосплавной пластинки делают обратную конусность 0,6…0,8 мм на 100 мм длины.
Недостаток – ослабление корпуса, напайка осуществляется в зоне резания.
С коронкой
Применяются на станках с ЧПУ, обладающих повышенной жесткостью.
Со сменной твердосплавной головкой для обработки отверстий диаметром 7…30 мм
С
окращает
время на смену инструмента. Для установки
головки используется специальный ключ.
Для удаления использованной головки
достаточно пол-оборота ключа. Само
сверло остается неподвижным в станке.
Рис.9. Сменная твердосплавная коронка
С пластинками
Рис.
10. Твердосплавные сверла со сменными
пластинами
Применяются для обработки отверстий диаметром больше 12 мм.
Режущая кромка образована двумя или более пластинками, перекрывающими друг друга, поэтому она формирует практически плоское дно отверстия.
Центральная пластина располагается таким образом, чтобы ее режущая пластина находилась на оси сверла. Расположение центральной пластины с перекрытием оси сверла может привести при сверлении к поломке вершины пластинки, т.к. участок режущей кромки переходящий за ось будет работать с отрицательными задними углами (обратной стороной).
Конструкция пластины оптимизирована в зависимости от положения пластины на сверле (на периферии или в центре) и требований к обработке.
Сочетание центральной и периферийной пластин, уравновешивающее радиальные составляющие силы резания, позволяет обрабатывать точные отверстия.
П
ластины
изготавливаются треугольного или
прямоугольного типа, позитивные,
крепятся, как правило, винтом через
отверстие.
Форма режущей кромки треугольной пластинки позволяет производить ступенчатую обработку, обеспечивая разделение стружки по ширине, облегчающее ее отвод из зоны резания.
8.2.5.Сверла для глубокого сверления
Глубоким считается сверление отверстий на глубину, превышающую диаметр сверла в 5 и более раз.
Глубокое сверление производится, как правило, при вращающейся заготовке, реже при вращении инструмента и заготовки вместе.
При сверлении глубоких отверстий возникают проблемы:
затруднен отвод стружки;
затруднен отвод тепла, необходимо обеспечить подвод СОЖ в зону резания;
требуется обеспечить более точное направление сверла в процессе работы.
Сверла для глубокого сверления можно разделить на две группы:
Многокромочные сверла с поперечной кромкой, имеющие две главные режущие кромки.
Их преимущество – высокая производительность.
Недостаток – наличие поперечной кромки, вследствие чего появляются вибрации в работе, снижается качество обработки. Возможен увод сверла с оси детали, не обеспечивается прямолинейность оси.
Однокромочные сверла или сверла одностороннего резания.
8.2.5.1.Шнековые сверла
Рис.11. Шнековое сверло
Конструкция канавки этого сверла обеспечивает хороший отвод стружки.
Особенности шнековых сверл:
Большой угол наклона стружечных канавок (ω = 60…650).
Увеличенный диаметр сердцевины сверла dc =(0,3…0,35)D.
Треугольный профиль стружечных канавок в осевом сечении. Образующая рабочей стороны канавки перпендикулярна оси сверла.
Уменьшенная ширина направляющей ленточки по сравнению со спиральным сверлом fшн = (0,5…0,8) fсп.
Подточка передней поверхности.
Наличие стружколомающего уступа.
Шнековые сверла обеспечивают высокую производительность, благодаря непрерывности процесса обработки.
8.2.5.2.Эжекторные сверла
В
основе эжекторного сверла лежит
сверлильная головка с твердосплавными
ножами, навинченная на сверлильную
трубу. Внутри наружного стебля находится
внутренний стебель. Они служат для
разграничения потоков СОЖ. Жидкость
под давлением 2…3 МПа насосом подается
в полость между наружным и внутренним
стеблем к режущей части сверла. Основное
количество СОЖ (около 70%) нагнетается
через отверстия к режущей части сверла,
что обеспечивает смазку и охлаждение
опорной втулки и ножей. Остальная
жидкость через щели во внутреннем стебле
попадает в центральную полость. В
результате перепада давления создается
разряжение внутри корпуса сверла.
Основной поток жидкости со стружкой из
зоны резания как бы засасывается
жидкостью в центральной части и движется
с большей скоростью.
Сверло обеспечивает точность обработки по 9…11 квалитетам и шероховатость поверхности Ra = 2,5…0,63 мкм.
Рис.
Схема работы эжекторного сверла
8.2.5.3.С внутренним отводом стружки
Рис.12.
Сверло с четырьмя направляющими
ленточками
верло
с четырьмя направляющими ленточками,
образующими каналы для подачи СОЖ .
Отвод стружки через внутреннее отверстие.
СОЖ подается под
большим давлением (10…20 кгс/мм2) в пространство между наружным диаметром стебля и стенками отверстия.
Для спокойной работы на режущих кромках выполняют стружкоразделительные канавки.
В
отличие от эжекторной системы данный
метод предъявляет определенные требования
к гидравлическим уплотнениям аппаратуры
снабжения СОЖ и обрабатываемой заготовки.
8.2.5.4.Пушечные сверла
Рис. 13. Пушечное сверло
Пушечное сверло представляет собой стержень, передний конец которого срезан и заточен под соответствующими углами. Во избежание заедания сверла в отверстии передняя поверхность располагается выше центра на 0,2…0,5 мм в зависимости от диаметра сверла.
Сверло имеет главную режущую кромку, направленную перпендикулярно оси отверстия и на 0,5…0,8 мм проходящую через центр. Вспомогательная режущая кромка может быть срезана под углом 100. сверло работает с направлением по предварительно надсверленному отверстию. Для направления сверло имеет цилиндрическую поверхность. Геометрия сверла не выгодная. Передний угол нулевой. Задний – 8…100. Для уменьшения трения направляющей о стенки отверстия срезана лыска под углом 300 и направляющая имеет обратную конусность 0,03…0,05 мм на 100мм длины.
Сверло не обеспечивает непрерывного процесса резания, т.к. для удаления стружки и охлаждения сверло периодически необходимо выводить из отверстия.
8.2.5.5.Ружейные сверла
Применяются для получения точных отверстий с прямолинейной осью
Рис. 14. Ружейное сверло
Основные части сверла:
режущая часть из быстрорежущей стали или твердого сплава;
стебель из углеродистой стали, диаметр которого несколько меньше, чем у режущей и зажимной части;
хвостовик в виде гильзы, вставляемой в станок и подсоединяемой к системе подачи СОЖ.
Рабочая часть представляет собой трубку с продольным прямолинейным V- образным пазом. Через отверстие в трубке к режущей части сверла под высоким давлением подается охлаждающая жидкость. Отработанная жидкость вместе со стружкой выходит по пазу.
a
ля
облегчения резания и лучшего направления
вершина сверла смещена относительно
оси сверла на величину а.
Смещение образует конус, служащий опорой
сверлу и обеспечивает ему направление
в процессе резания.
b
Рис.15.
Схема действия сил на ружейном сверле
Во избежание прогиба и поломки сверла дно канавки делают с занижением относительно оси на 0,05…0,15 мм. При этом при сверлении в отверстии получается сердечник, обеспечивающий дополнительное направление
Ружейные сверла обеспечивают
высокую точность ( 7…9 квалитет),
прямолинейность оси отверстия,
высокое качество поверхности.
Оборудование для подвода смазочно-охлаждающей жидкости
Рис. 16. Станок для глубокого сверления
В системе имеется насосный агрегат, мощность которого должна обеспечить нужное давление и поток. Для удаления стружки и других включений из рабочей жидкости, циркулирующей в системе, требуется фильтр. Содержимого бака смазочно-охлаждающей жидкости должно быть достаточно для заполнения системы до состояния, исключающего слишком быструю циркуляцию и обеспечивающего хорошее осаждение стружки и охлаждение жидкости. Можно использовать аппаратуру дополнительного охлаждения. Для надежной работы системе необходимо иметь автоматические средства техники безопасности, так как сверло в процессе работы не находится в поле зрения.
8.2.5.6.Сверла для кольцевого сверления
Рис. 17.Сверла для кольцевого сверления
Сверло представляет собой трубу, на одном конце которой располагаются режущие элементы. Зубья режущей части имеют различную заточку для того, чтобы обеспечить разделение стружки по ширине. Трапецевидный зуб срезает среднюю часть, плоский нож срезает боковые части.
СОЖ подается под давлением по наружной поверхности трубы и отводится со стружкой через внутреннюю ее полость. Направление сверла и гидравлическое уплотнение обеспечивает втулка.
Зенкеры и зенковки
Зенкеры (Рис. а) предназначены для повышения точности формы отверстий, полученных сверлением, отливкой, ковкой или штамповкой; обеспечивают точность, соответствующую 9…10 квалитету, и шероховатость
Ra =6,3 мкм.
Зенковки предназначены для обработки: цилиндрических углублений под головки винтов и т.д. (Рис. б); конических углублений и снятия фасок в отверстиях(Рис. в); торцовых поверхностей бобышек (Рис. г).
Рис. 18. Зенкеры и зенковки
Зенкеры бывают:
хвостовые с цилиндрическим или коническим хвостовиком;
насадные с коническим посадочным отверстием (конусность 1:30) и торцовой шпонкой пря предохранения от проворачивания в работе,
цельные,
сборные.
Основные отличия зенкеров от сверл:
отсутствие поперечной кромки;
большее число режущих кромок (3…6)
8.3.1.Конструкция зенкера
Рис. 19. Хвостовой зенкер
Режущая часть имеет длину
, где а – дополнительная длина для обеспечения предварительного центрирования зенкера в отверстии в начале работы.
Калибрующая часть имеет направляющую ленточку шириной 0,8…2,5 мм. Увеличение ширины ленточки ведет к налипанию на нее стружки, что ухудшает процесс резания. Для снижения трения выполняется обратная конусность 0,04…0,1 мм на 100 мм длины.
Стружечные канавки могут быть:
прямые (у твердосплавных зенкеров для обработки материалов, дающих стружку надлома),
косые (у зенкеров со вставными ножами),
винтовые
8.3.2.Геометрия зенкера
Угол φ при обработке стали принимают равным 600; для увеличения стойкости делают переходную кромку с φ1 =300. При обработке чугуна φ=450 . При обработке глухих отверстий φ=900.
Задний угол на режущей части =6…100. Задняя поверхность, как и у сверл, выполняется плоской, конической или винтовой.
Угол наклона стружечной канавки цельного зенкера ω = 150…250
8.3.3. Сборные зенкеры
Изготовляются диаметром 50…100 мм. Твердосплавная пластинка припаивается к ножу, который закрепляется в корпусе с помощью рифлений и клина.
Крепление должно обеспечить возможность регулирования ножей в диаметральном и осевом направлениях, прочность и жесткость крепления, простоту изготовления, быстросменность.
Продольные рифления в корпусе и на ноже позволяют производить регулировку в диаметральном направлении. Отсутствие регулировки в осевом направлении сокращает число возможных переточек.
Наличие продольных и поперечных рифлений позволяют производить регулировку в диаметральном и осевом направлениях.
Регулировка по диаметру (рифления) и в осевом направлении (клином).
Рис.
20.Зенкеры сборные
Развертки
Развертывание выполняют для получения точных отверстий после сверления, зенкерования или растачивания. Достигается точность, соответствующая 6…9 квалитету, и шероховатость Ra = 0,32…1,25 мкм.
Высокая точность и качество поверхности при развертывании обеспечиваются малыми припусками (0,05…0,25 мм для чистовых и 0,15…0,5 мм для черновых) и срезанием весьма тонких стружек, благодаря наличию у разверток сравнительно большого числа зубьев (6…14) и малого угла φ.
Развертки бывают:
Хвостовые и насадные;
цилиндрические и конические;
ручные и машинные;
быстрорежущие и твердосплавные;
цельные и сборные.
Конструкция развертки
Рис.21. Цельная цилиндрическая ручная развертка
Режущая часть
Угол φ у ручных разверток – 10…20, что улучшает направление развертки при входе и уменьшает осевую силу; у машинных при обработке стали φ = 120…150; при обработке хрупких материалов (чугуна) φ = 30… 50.
С
тандартные развертки делают с неравномерным окружным шагом с целью предупреждения появления в развертываемом отверстии продольных рисок. Из-за неоднородности обрабатываемого материала на зубьях развертки происходит периодическое изменение нагрузки, что ведет к отжиму развертки и появлению на обработанной поверхности следов в виде продольных рисок.
Калибрующая часть состоит из двух участков: цилиндрического и участка с обратной конусностью. Длина цилиндрического участка около 75% от длины калибрующей части.
Цилиндрический участок калибрует отверстие, а участок с обратной конусностью служит для направления развертки в работе. Обратная конусность уменьшает трение об обработанную поверхность и снижает разбивку. Т.к. при ручном развертывании разбивка меньше, то и угол обратной конусности меньше, чем у машинной развертки. При этом цилиндрический участок у ручных разверток может отсутствовать.
Цилиндрическая ленточка на калибрующей части калибрует и выглаживает отверстие. Уменьшение ее ширины снижает стойкость развертки, однако повышает точность обработки и снижает шероховатость, т.к. уменьшает трение. Рекомендуемая ширина ленточки f = 0,08…0,5 мм в зависимости от диаметра развертки.
Число зубьев z ограничивается их жесткостью. С увеличением z улучшается направление развертки (больше направляющих ленточек), повышаются точность и чистота отверстия, но снижается жесткость зуба и ухудшается отвод стружки. Z принимается четное - для облегчения контроля диаметра развертки.
Канавки чаще выполняют прямыми, что упрощает изготовление и контроль. Для обработки прерывистых поверхностей целесообразно применять развертки с винтовым зубом. Направление канавок делается противоположным направлению вращения для избежания самозатягивания и заедания развертки.
Задний угол выполняют небольшой (50…80) для повышения стойкости развертки. Режущую часть затачивают до остра а на калибрующей делают цилиндрическую ленточку для повышения размерной стойкости и улучшения направления в работе.
Передний угол принимают равным нулю.
Регулируемые развертки
Применяются для ремонтных работ.
Ручная разжимная развертка (Рис. б) имеет на корпусе прорезанные вдоль зубьев шлицы. В корпусе имеется коническое отверстие, куда помещается шарик. Перемещение шарика винтом в осевом направлении вызывает деформацию корпуса и увеличение диаметра развертки. Диапазон регулирования 0,16…0,5 мм в зависимости от диаметра развертки.
Ручная раздвижная развертка (Рис. в). В корпусе выфрезерованы конусные пазы, в которые вставлены ножы. Перемещение ножей в осевом направлении приводит к изменению диаметра развертки. Предел регулирования 0,5…4,5 мм.
Рис.22.
Регулируемые развертки
Конические развертки
Применяются для превращения цилиндрического отверстия в коническое или для калибрования цилиндрического отверстия.
Конические развертки для конусов Морзе (Рис.) работают в комплекте из трех или двух штук:
Обдирочная развертка (рис. а) снимает значительный припуск. Для облегчения работы режущую кромку делают ступенчатой. На конической образующей поверхности нарезают затылованный винтовой зуб. Направление резьбы совпадает с направлением резания. Эта развертка превращает цилиндрическое отверстие в ступенчатое.
Промежуточная развертка (рис. б) имеет стружкоразделительные канавки в виде конической прямоугольной резьбы, по направлению противоположной обдирочной развертке. Шаг резьбы Р = 1,5…3 мм в зависимости от номера обрабатываемого конуса. Зубья незатылованные, с ленточкой f =1…2 мм
Чистовая развертка имеет прямые зубья по всей длине. Ленточка минимальна (0,05 мм). Шаг зубьев равномерный.
Рис.
23. Конические развертки
Расточной инструмент
Растачивание обеспечивает шероховатость Ra = 0,32 и точность, соответствующую 6…7 квалитету
Расточные резцы
Применяются для обработки отверстий. Работают в более тяжелых условиях, чем резцы для наружной обработки:
поперечные размеры должны быть меньше, чем обрабатываемое отверстие (отношение диаметра державки к диаметру растачиваемого отверстия 0,5…0,8);
вылет резца должен быть больше длины растачиваемого отверстия (до (6…8)d);
из-за малой жесткости склонны к вибрации, что не позволяет снимать стружку большого сечения
8.5.1.1.Стержневые резцы
Крепятся в суппорте станка или устанавливаются на оправке. Державки могут быть круглой, квадратной или прямоугольной формы
При растачивании глубоких отверстий для повышения жесткости резцы крепятся в специальных оправках. Резцы имеют квадратное сечение. Крепятся в оправке в перпендикуляр-ном или наклонном по отношению к оси державки положении.
При расположении резца относительно оси отверстия под некоторым углом ξ углы в плане у резца меняются φн = φ + ξ , φ1н = φ1 +ξ . Это надо учитывать при проектировании резца.
2
В тех случаях, когда нет необходимости точной настройки резца на заданный размер крепление в гнездах оправок и борштанг может быть нерегулируемым (а). Резец закрепляется в оправке одним или двумя винтами.
Регулируемое крепление резцов предусматривает выдвижение резца при настройке с помощью упорных винтов, что позволяет устанавливать резцы с погрешностью, позволяющей производить обработку отверстия до 8 квалитета точности.
Упорный винт может быть установлен по оси паза (б) и под углом к пазу и резцу (в).
Смещение резцов при настройке с помощью дифференциального винта (г) повышает точность регулировки, однако применение дифференциальных резьб требует повышения точности изготовления и соосности резьб. Упорный винт с проточкой, в которую входит выступ резца (д), позволяет смещать резец при настройке в обоих направлениях, что в ряде случаев является очень удобным.
Некоторые виды крепления инструмента в борштангах и оправках предусматривают применение специальных резцов(е). Расточной резец с твердосплавной пластиной выполнен в виде резьбового стержня с отверстием, в котором на резьбе расположен винт стопорения. На торце стержня имеются два шпоночных выступа, входящих в пазы посадочного отверстия и предохраняющих резец от проворота. На переднем конце стержня резца 1 навинчена гайка-лимб 2, снабженная делениями для точной настройки. Вылет резца на заданный размер устанавливают вращением лимба, после чего резец закрепляется (затягивается) стопорным винтом 3.
Точная настройка резца (ж) выполняется с помощью подвижного плунжера в узле установки и крепления специальных расточных резцов, имеющих рифленую боковую поверхность. Рифления на резце 1 нарезаны под углом и находятся в соединении с рифлениями плунжера 2, расположенного в гнезде борштанги перпендикулярно к плоскости резца и связанного с винтом-лимбом 3. При вращении винта-лимба плунжер смещается и рифлениями передвигает резец. Крепление установленного резца выполняется стопорным винтом 4. Цена деления шкалы на головке регулировочного винта равна 0,01 мм. Такая точность настройки позволяет применять данный узел в борштангах, предназначенных для расточки отверстий 6-го и 7-го квалитетов точности.
Тема 9. Фрезы
(Особенности процесса фрезерования как процесса прерывистого резания.Конструкция фрез общего назначения: цилиндрические, торцевые, острозаточенные, затылованные, фрезы сборной конструкции.Определение конструктивных параметров фрез. Выбор фрез для различных методов обработки.)
Фреза – многолезвийный режущий инструмент, выполненный в виде тела вращения, на образующей которого и (или) на торце расположены зубья. Предназначены для обработки плоскостей, пазов, прорезей, уступов, фасонных и винтовых поверхностей, нарезания резьб и т.д.
Точность обработки – 7…9 квалитеты.
Шероховатость обработанной поверхности - Ra =1,25 мкм.
Главное движение при фрезеровании – вращение фрезы.
Классификация фрез
По расположению зубьев
а) цилиндрические;
б) торцовые;
в) угловые;
г) фасонные;
д)дисковые;
е)концевые;
ж,з,и)шпоночные;
к)фасонные;
Рис.1.
Типы фрез
. 9.1.2.направлению зубьев
С прямыми зубьями (Рис.1,д)
С косыми зубьями (Рис.1,б)
С
винтовыми зубьями (Рис.2)
Рис.2.
Фреза цельная цилиндрическая с винтовым
зубом
9.1.3.По конструкции
Цельные, изготовленные из одного куска быстрорежущей стали (Рис.2).
С
оставные, состоящие из отдельных цельных частей, в том числе фрезы комплектные
Рис.3
Составная фреза
Рис. 4 Сборная фреза
Сборные, оснащены режущей частью в виде ножей из быстрорежущей стали, многогранными и круглыми пластинками из твердых сплавов или из сверхтвердых или керамических материалов.
9.1.4.По способу крепления на станке
Хвостовые с цилиндрическим или коническим хвостовиком;
Насадные, с посадочным отверстием.
9.1.5.По конструкции зубьев
Незатылованные – с прямолинейной образующей задней поверхности (Рис.1,и).
Затылованные – с криволинейной образующей задней поверхности (Рис.1,к).
9.2.Незатылованные фрезы
Незатылованные фрезы перетачиваются преимущественно по задней поверхности.
Незатылованные зубья широко применяются для фрез общего назначения.
Достоинства незатылованных фрез:
Высокая стойкость (в 1,5…3 раза выше, чем у затылованных).
Простота изготовления.
Повышенная чистота обработанной поверхности.
9.2.1.Конструктивные параметры
Диаметр фрезы da
Наружные диаметры стандартизованы. Размерные ряды диаметров фрез составлены по геометрической прогрессии со знаменателем φ = 1,26; 1,58, равным знаменателю ряда частоты вращения шпинделя фрезерных станков. Это обеспечивает неизменность скорости резания при применении фрез любого диаметра.
Уменьшение наружного диаметра способствует снижению машинного времени обработки. Однако при этом может снижаться жесткость оправки и прочность фрезы в сечении между окружностью впадин и посадочным отверстием.
От диаметра фрезы зависят:
отвод тепла,
толщина стружки,
число зубьев,
диаметр посадочного отверстия.
Диаметр посадочного отверстия D0 зависит от наружного диаметра и округляется до стандартного значения (16; 22; 27; 32; 40; 50 и 60 мм).
Для фрез с мелкими зубьями для чистовой обработки диаметры оправок могут быть меньше, чем для фрез с крупными зубьями.
Для фрез, оснащенных твердым сплавом, и для обработки труднообрабатываемых материалов диаметры оправок должны быть большими.
Диаметр окружности впадин d1
Число зубьев выбирают из условия равномерности фрезерования с учетом эффективной мощности оборудования. Увеличение числа зубьев ведет к улучшению качества обработки, но растут энергозатраты на фрезерование, снижаются число возможных переточек фрезы, прочность зуба, размеры стружечной канавки, растут эксплуатационные затраты.
9.2.2.Геометрия
Передний угол γ зависит от физико-механических свойств обрабатываемого материала и режущей и прочностной характеристики инструментального материала.
Задний угол зависит от максимальной толщины срезаемого слоя amax
С увеличением заднего угла возрастает износ режущей кромки в радиальном направлении, а от величины радиального износа зависит точность обработки. Для фрез из твердого сплава для получения малой шероховатости обрабатываемой поверхности задний угол рекомендуется 5…80.
Угол наклона зубьев ω
Улучшает равномерность фрезерования (ω= 10…150).
Влияет на направление схода стружки.
Позволяет получить положительные передние углы на торцовых зубьях дисковых двух- и трехсторонних фрез.
Повышает стойкость фрезы вследствие увеличения кинематических передних углов. При этом можно уменьшить инструментальный передний угол в нормальном сечении и повысить прочность зуба, что позволяет увеличить в 1,5…2 раза подачу на зуб.
Направление угла наклона зуба ω выбирают так, чтобы осевая составляющая силы резания была направлена в сторону шпинделя.
9.2.2.Форма зубьев
Форма зубьев должна обеспечивать
прочность зуба,
достаточное пространство для размещения стружки,
допускать максимально возможное число переточек.
Существует три основные формы незатылованных зубьев: трапецеидальная форма, параболическая форма и с двойной спинкой зуба
(Рис. )
Трапецеидальная форма проста в изготовлении, но зуб ослаблен. Применяется для фрез с мелким зубом. Угол тела зуба = 47…520 (для концевых и прорезных – 30…400) . Угол стружечной канавки υ = +. Фаска f = 0,5…2 мм. Радиус закругления дна впадины r =0,5…2 мм. Высота зуба h = 0,5…0,65 окружного шага зубьев.
Параболическая форма обеспечивает повышенную прочность зуба на изгиб. Для изготовления требуются специальные фрезы. Применяется для фрез с малым числом зубьев.
Форма зуба с двойной спинкой по прочности близка к параболической, но проще в изготовлении. Спинка образуется двойным фрезерованием угловой фрезой. Наиболее распространена.
9.3.Типы фрез
9.3.1.Цилиндрические фрезы
П
рименяются
на горизонтально-фрезерных станках для
обработки плоскостей.
Фрезы с прямыми зубьями используются только для обработки узких плоскостей. Винтовой зуб повышает плавность работы, однако в этом случае возникают осевые усилия. Применение сдвоенных цилиндрических фрез с разнонаправленными винтовыми зубьями позволяет уравновесить осевые усилия, действующие на фрезы, в процессе резания. В месте стыка фрез предусматривается перекрытие режущих кромок одной фрезы режущими кромками другой для устранения недообработанных участков.
Ц
илиндрические
фрезы с винтовыми пластинками из твердого
сплава дают хорошие результаты при
обработке жаропрочных и коррозионно-стойких
сталей и сплавов (по сравнению с
быстрорежущи-ми фрезами обеспечивают
повышение производитель-ности с
одновременным повышением стойкости ),
но сложны в изготовлении. Стыки между
напаянными пластинами оформляются в
виде стружкоделителей и должны
располагаться в шахматном порядке.
9.3.2.Торцовые фрезы
П
рименяются
при обработке плоскостей и уступов на
вертикально-фрезерных станках. Кроме
торцовых режущих кромок имеет режущие
кромки на образующей тела вращения.
Д
остоинства
торцовых фрез:
Большой угол контакта, зависящий от диаметра фрезы и ширины фрезерования, обеспечивает равномерность фрезерования.
Высокая производительность
Проще оснастить твердым сплавом
Угол в плане φ может изменяться в широких пределах (450…900). Его уменьшение обеспечивает виброустойчивость процесса и способствует повышению точности обработки.
9.3.3.Концевые фрезы
Применяются для обработки пазов, уступов, прямоугольных пазов и т.д.
Рис.8.
Конструкция и геометрия концевой фрезы
Концевые фрезы выполняют с цилиндрическим (диаметром 3…20 мм) хвостовиком или с конусом Морзе с резьбовым отверстием для затяжного болта.
Концевые фрезы выпускают с нормальным или крупным зубом. Для повышения равномерности фрезерования у фрез с крупным зубом рекомендуется больший угол наклона винтовых канавок.
Для снижения вибраций рекомендуется делать неравномерный окружной шаг зубьев.
При обработке пазов и уступов (Рис.) направление винтовых канавок противоположно направлению вращения, что обеспечивает лучший отвод стружки и положительный передний угол на торцовых зубьях.
Рис.
При обработке плоскостей (Рис. ) направление канавок совпадает с направлением вращения. В этом случае осевая составляющая силы резания направлена к шпинделю станка, а сход стружки обеспечивается от шпинделя.
Для
чернового фрезерования широких
поверхностей и пазов с большими припусками
предназначены концевые обдирочные
(кукурузные) фрезы, зубья которых снабжены
стружкораздели-тельными канавками,
расположенными в шахматном порядке,
обеспечивающими разделение стружки
по ширине и способствующими гашению
вибраций.
9.3.4.Шпоночные фрезы
Рис.11.
Шпоночная фреза
Особенность работы –фрезерование в несколько проходов, как в одну, так и в другую сторону, в конце каждого прохода осуществляется вертикальная подача.
Для обеспечения жесткости длину режущей части делают равной трем наружным диаметрам при диаметре сердцевины до 0,3 диаметра фрезы. Канавки прямые или винтовые. Два зуба, один из торцовых зубьев делают равным половине диаметра фрезы, а второй стачивают у оси.
9.3.5.Дисковые и пазовые фрезы
Предназначены для фрезерования пазов и канавок
Прорезные (шлицевые) и отрезные (пилы) фрезы применяют для разрезки заготовок.
Для уменьшения трения по боковым сторонам выполняют угол φ' = 15…30'
Пазовые фрезы имеют зубья только на цилиндрической поверхности. Для уменьшения трения на торцах выполняется вспомогательный угол в плане φ1 = 1…2°.Для увеличения размерной стойкости на боковых сторонах оставляют фаски f =1…2 мм. Применяются для обработки неглубоких пазов.
Недостаток - быстро теряют размер по ширине. Для сохранения размера применяют составные фрезы, регулируемые по ширине с помощью прокладок. Для перекрытия режущих кромок обе половинки соединяют в замок.
Дисковые двух- и трехсторонние фрезы имеют главные режущие кромки на поверхности цилиндра и вспомогательные - на одном или обоих торцах. Для получения положительных передних углов на торцовых режущих кромках зубья выполняют с углом наклона ω= 10…15°. У трехсторонних фрез зубья делают разнонаправленными.
9.3.6.Угловые фрезы
Одноугловые с одной образующей, расположенной под углом к оси фрезы.
Двуугловые с двумя образующими, расположенными под одинаковыми или различными углами к оси фрезы.
9.3.7.Т-образные фрезы
Рис.15.
Т- образные фрезы
9.3.8.Сборные фрезы
Оснащаются режущими элементами, перетачиваемыми в сборе или вне фрезы, или неперетачиваемыми пластинками.
Особенности фрез с перетачиваемыми ножами:
Возможность создания оптимальной с точки зрения эксплуатации геометрической формы и размеров.
Точность взаимного расположения режущих элементов различных зубьев определяется качеством заточки и установки.
Особенности фрез с неперетачиваемыми режущими элементами:
Фиксированное расположение пластин в корпусе фрезы.
Геометрические параметры постоянны и определяются конструкцией фрезы.
Точность взаимного расположения режущих элементов определяется точностью исполнения базовых поверхностей корпуса и сменных пластин.
Наиболее простым и надежным способом крепления зубьев фрез из быстрорежущих сталей является применение рифлений, обеспечивающих компактность крепления, а значит и возможность размещения большого числа зубьев. Применяется для цилиндрических, торцовых и дисковых двух- и трехсторонних фрез.
Варианты
крепления:
а) клиновые нож и паз, рифления в осевом направлении. Регулировка возможна только в радиальном направлении;
б,в) крепление клином позволяет производить регулировку размера и в осевом и в радиальном направлении;
г) нож двойной клиновидности позволяет производить одновременное регулирование в осевом и радиальном направлениях.
9.4.Твердосплавные фрезы
Обеспечивают повышение производительности труда и возможность обработки труднообрабатываемых материалов.
Могут быть:
монолитными (дисковые и концевые мелкоразмерные фрезы),
составными (концевые фрезы с коронками или винтовыми пластинками, цилиндрические с винтовыми пластинками),
сборными.
Сборные фрезы с многогранными неперетачиваемыми пластинами
обладают высокой прочностью и надежностью,
не требуют переточек,
обеспечивают многократное использование корпусов
Широко распространены два типа сборных торцовых фрез с многогранными пластинами:
з
акрепление пластин непосредственно в корпусе;
Рис.
17.Фреза с многогранными неперетачиваемыми
пластинками
закрепление в корпусе сменных ножей с неперетачиваемыми пластинами.
Конструкция установки и крепления многогранной неперетачиваемой пластины в корпусе фрезы должна обеспечивать:
прочное и жесткое крепление пластины;
точную установку пластины относительно торцовой опорной поверхности и оси фрезы .
Это достигается повышенной точностью изготовления пластин и корпуса фрезы, а также введением регулирования.
Тгма 10. Резьбонарезной иструмент
(Методы нарезания резьбы:резцами, фрезами, метчиками, плашками,резьбонарезными головками. Конструкция резьбонарезных инструментов. Выбор и назначение геометрических параметров резьбонарезных инструментов.)
10.Резьбонарезной инструмент
10.1.Резьбонарезные резцы
Резьбонарезные
резцы – однолезвийный фасонный режущий
инструмент, образующий профиль нарезаемой
резьбы одновременно всеми точками
режущей кромки. В процессе резания
инструмент совершает относительно
заготовки винтовое движение, ось которого
совпадает с осью нарезаемой резьбы, а
параметр – равен параметру резьбы.
Резцы предназначены для нарезания внутренних и наружных резьб различного профиля.
Достоинства резцов:
простота конструкции и технологии изготовления;
универсальность;
точность расположения оси;
возможность обработки конических резьб и резьб с переменным шагом.
10.1.1.Типы резцов
По виду нарезаемой резьбы:
метрические,
трапецеидальные,
трубные,
дюймовые и т. д.
по конструкции:
стержневые :
круглые с кольцевой и винтовой нарезкой :
призматические :
по форме режущей кромки:
однопрофильные (Рис.2. а, б, в, г),
многопрофильные (Рис.2. д, е,ж) –
резьбовые гребенки;
по исполнению режущей части:
цельные (Рис.2 д, е),
составные (Рис.2 а),
сборные (Рис.2 в, г, ж);
по виду работы:
черновые,
чистовые;
Рис.2
Типы резьбовых резцов
по типу нарезаемой резьбы:
наружные (Рис. 3, а),
внутренние (Рис. 3, б);
по профилю режущей кромки:
с полным профилем
полностью формируют профиль резьбы, включая и поверхность вершин; обеспечивается точность профиля по высоте и радиусов по вершине и впадине, что гарантирует прочность резьбы,
не требуется точного исполнения отверстия в заготовке и снятие заусенцев после обработки, но для каждого шага резьбы требуется свой инструмент.
с неполным профилем обеспечивают минимальную номенклатуру инструмента,
не обрабатывают наружного диаметра резьбы, поэтому требуют точного диаметра заготовки,
могут использоваться для обработки резьб с разными шагами,
количество пластин на инструментальном складе сокращается,
10.1.1.1.Схемы резания
Форма и сечение срезаемого слоя для каждого реза зависят от последовательности срезания припуска, т.е. от схемы резания.
Нарезание резьб мелкого модуля осуществляется за один проход. При нарезании однопрофильным резцом глубина резания tр равна высоте профиля резьбы h. При нарезании многопрофильным резцом (гребенкой) глубина резания уменьшается (рис.6):
,
где Р – шаг резьбы; l1 – длина режущей части.
Многопроходное нарезание
Радиальное врезание (рис.5)
Достоинства:
простой способ,
высокая точность профиля,
равномерный износ пластины.
Недостатки:
жесткая стружка,
повышенное давление на вершину,
при нарезании крупной резьбы существует риск возникновения вибраций и плохого стружкообразования.
Используется для нарезания мелких резьб и при обработке закаленных материалов.
Постепенное
уменьшение глубины врезания (Рис.8.)
обеспечивает постоянный объем стружки,
срезаемой за каждый проход. Глубина
врезания может изменяться от 0,2…0,35 мм
вначале обработки до 0,02…0,09 мм на
последнем проходе.
Постоянная глубина врезания (Рис.9.) обеспечивает наилучшее формирование стружки и повышение стойкости инструмента.
Начальное значение глубины врезания не должно превышать 0,12…0,18 мм, а на последнем проходе не должна быть менее 0,08 мм.
Боковое врезание (рис.10)
Достоинства:
Лучше форма стружки
Возможность направить стружку в нужную сторону
Уменьшается тепловыделение
Можно снизить вибрации
Недостатки:
Ухудшение качества обработанной поверхности
Боковое двухстороннее врезание (рис.11)
Применяется для обработки резьб с большим профилем.
Обеспечивает минимальный и равномерный износ пластины.
10.1.1.2.Геометрия
Задний угол на вершине – 15…200
И
нструментальные
боковые задние углы можно рассчитать
по формуле:
где ε – угол профиля резьбы.
Геометрия резца зависят от его установки на станке. При малом угле подъема ось симметрии профиля резца располагают перпендикулярно к оси заготовки (рис. 6. б).
Если угол подъема резьбы больше 3…40, то резец наклоняют к оси заготовки под углом β = (рис 6.а)
подъема резьбы
При установке резца без разворота (рис. 6.б) при равенстве инструментальных углов на левой и правой стороне профиля статические углы изменяются. С одной стороны инструментальный передний угол увеличивается а задний уменьшается, с другой стороны профиля – наоборот, передний уменьшается , а задний увеличивается.
При установке резца без разворота значения статических задних углов с правой и левой стороны профиля можно выравнять, если произвеести заточку разных по величине инструментальных задних углов (рис.13 б).
При равенстве инструментальных углов на левой и правой стороне профиля статические углы можно выравнять, если произвести разворот резца на станке (рис.13 в). Но в этом случае профиль резца отличается от профиля нарезаемой резьбы. Требуется коррекционный расчет профиля.
Наличие положительных передних углов также вызывает необходимость коррекционного расчета профиля резца (рис.14).
10.2.Метчики
Назначение – нарезание и калибрование резьбы в отверстиях. Метчики представляют собой винт, сопряженный с нарезаемой резьбой и превращенный в режущий инструмент.
10.2.1.Типы метчиков
ручные – для нарезания резьбы вручную, обычно выполняются комплектными;
машинные – для нарезания резьб на станках или с помощью электродрелей;
Рис.7.. Гаечный метчик с изогнутым хвостовиком
гаечные – для нарезания резьбы в гайках на гайконарезных станках. Длинный хвостовик гаечного метчика позволяет устранить свинчивание готовой гайки. Нарезанные гайки размещаются на хвостовике и периодически удаляются, для чего метчик вынимается из патрона станка. Изогнутый хвостовик позволяет удалять готовые гайки, не вынимая метчика из патрона станка, что повышает производительность.
плашечные и маточные для нарезания и калибрования резьбы в плашках;
трубные – для нарезания трубных резьб в муфтах и трубах;
конические для нарезания конических резьб;
сборные метчики, регулируемые, нерегулируемые и самовыключающиеся;
калибровочные;
специальные.
10.2.2.Конструкция метчика
Основные элементы метчика:
режущая часть,
калибрующая часть,
хвостовик,
кольцевая канавка для закрепления в патроне и передачи осевого перемещения,
квадрат (или лыска) для передачи крутящего момента,
перья,
стружечные канавки.
Режущая часть производит основную работу срезания припуска, выполняется в виде конуса с углом наклона образующей φ. Может применяться последовательная (рис.17.а) или профильная (рис.17 б) схемы резания. Длина режущей части l1 (рия.16) влияет на производительность, стойкость инструмента и точность нарезаемой резьбы.
Для глухих отверстий и чистовых комплектных метчиков длину режущей части уменьшают до (1,5…2)Р, где Р – шаг резьбы. Гаечные метчики имеют длину (6…12)Р, машинно-ручные -6Р.
Угол φ влияет на толщину срезаемого слоя (рис.18)
,
где
а – толщина срезаемого слоя в направлении, перпендикулярном главной режущей кромке,
ар – толщина срезаемого слоя в радиальном направлении .
,
где
t – фактическая высота резьбы,
,
где
l
э
– эффективная
длина режущей части, которая определяется
по формуле:
,
где
d – наружный диаметр метчика,
d0 – диаметр отверстия под резьбу;
n
– число
резов, формирующих профиль
, где Z
– число перьев метчика.
Следовательно,
.
Оптимальная толщина срезаемого слоя определяется с учетом обрабатываемого материала, типа метчика, требований к качеству обработки. Предельные значения толщины срезаемого слоя 0,02…0,15 мм. При толщине менее 0,02 наблюдается не резание а смятие и скобление, т.к. в этом случае радиус скругления режущей кромки оказывается больше толщины срезаемого слоя. При толщине более 0,15 мм резко ухудшается чистота обработанной поверхности.
Диаметр переднего торца метчика выполняют меньше диаметра отверстия под резьбу на 0,2…1 мм для обеспечения направления метчика при входе в отверстие.
Длина режущей части метчика l1 зависит от его назначения. При обработке глухих отверстий от длины заборной части зависит длина недореза резьбы и ее желательно уменьшать. При обработке сквозных отверстий от соотношения длины режущей части и длины резьбы зависит крутящий момент резания . Для уменьшения крутящего момента желательно, чтобы длина режущей части была больше длины резьбового отверстия.
Калибрующая часть окончательно формирует профиль, обеспечивает направление в работе и является запасом на переточку.
Преимущественный износ метчика происходит по задней поверхности в месте перехода от режущей к калибрующей части. Поэтому переточку рационально производить как по передней так и по задней поверхностям.
Заточка задней поверхности по конусу режущей части приводит к уменьшению длины калибрующей части. Длина калибрующей части предельно переточенного метчика должна быть не менее 0,5d для крупных и средних метчиков и не менее (1,2…1)d для мелких.
Рис.
19 Зависимость момента резания от
соотношения длины резьбы и длины режущей
части метчика
Чрезмерное увеличение длины калибрующей части приводит к увеличению крутящего момента и росту энергозатрат. Рекомендуемая длина калибрующей части lк – (6…12)Р.
Для устранения заклинивания на калибрующей части выполняется обратная конусность по профилю 0,05…0,1 мм на 100 мм длины (при обработке легких сплавов – 0,2…0,3 мм на 100 мм длины).
Число канавок Z влияет на толщину срезаемого слоя, а следовательно на величину крутящего момента. Уменьшение числа канавок снижает склонность метчика к заеданию, особенно при обработке вязких материалов. Улучшается размещение стружки в канавке, но ухудшается направление в работе. Число канавок выбирается в зависимости от диаметра метчика d.
Профиль канавки (рис. 9.) оказывает большое влияние на работу метчика.
Канавка должна:
способствовать хорошему стружкообразованию и стружкоотводу из зоны резани;
обеспечить хорошее размещение стружки, особенно при обработке глухих отверстий;
препятствовать резанию при вывинчивании метчика из обработанного отверстия;
препятствовать налипанию и заклиниванию стружки в канавке;
не иметь резких переходов и концентраторов напряжений.
Рис.
9. Форма канавок метчика
Диаметр сердцевины dсер выбирается из условия обеспечения достаточного пространства для размещения стружки и прочности метчика.
.
Рекомендуется углублять канавку на режущей части, т.к. здесь удаляется больший объем стружки, чем на калибрующей части.
При выборе величины ширины пера F необходимо учитывать, что с увеличением этого параметра возрастает усилие трения и возрастает опасность забивания канавки стружкой, но с другой стороны увеличивается количество переточек и улучшается направление метчика в работе.
Для режущей части целесообразно уменьшать диаметр сердцевины dсер до 0,7…0,8, а ширину пера F до 0,6…0,7 соответствующих величин на калибрующей части.
Угол у нерабочей кромки μ целесообразно уменьшать для устранения резания при вывинчивании метчика из обработанного отверстия, однако, чрезмерное уменьшение этого угла приводит к защемлению стружки при вывинчивании. Рекомендуется
.Также для исключения резания при вывинчивании можно снять фаску под углом 300 или притупить шлифовальным кругом острый уголок у нерабочей кромки вдоль всего зуба.
Передняя поверхность может иметь прямолинейную (рис.20 б, в) или криволинейную (рис.20 а) образующую. Прямолинейная образующая более распространена, т.к. упрощает заточку метчика и не приводит к резкому изменению величины переднего угла по высоте резьбы, как у метчиков с криволинейной образующей. Однако при обработке вязких материалов криволинейная образующая передней поверхности способствует лучшему образованию и отводу стружки.
Форма канавки
Радиусная форма (рис.21 а) проста в изготовлении, но имеет неблагоприятную геометрию):
передний угол изменяется от отрицательных значений в начале режущей части (точка 1) до положительных значений в конце режущей части (точка 2);
угол у нерабочей кромки μ больше 900, что приводит к резанию при вывинчивании метчика из обработанного отверстия.
Применяется для гаечных метчиков при обработке вязких материалов.
Рис.
10. Влияние формы канавки на величину
передних углов
Сложная форма требует специального инструмента для изготовления, но обеспечивает лучшую геометрию:
угол у нерабочей кромки μ меньше 900;
передний угол уменьшается вдоль режущей части, но остается положительным во всех точках режущей кромки и имеет максимальное значение там, где длина вершинной режущей кромки максимальна.
Направление канавок
Прямые канавки (рис. 10. а) проще в изготовлении, но создают неопределенное направление схода стружки и различные по величине боковые передние углы на правой и левой стороне профиля, что приводит к снижению стойкости.
Винтовые канавки с направлением противоположным направлению нарезки резьбы обеспечивают повышение стойкости за счет выравнивания величины боковых передних углов на правой и левой стороне профиля. Сход стружки идет в сторону обрабатываемого отверстия, поэтому такие канавки рационально применять для нарезания резьб в сквозных отверстиях.
Винтовые канавки с направлением одноименным направлению нарезки резьбы обеспечивают сход стружки в сторону хвостовика. Применяются при обработке глухих отверстий, но геометрия самая неблагоприятная.
Рис.
22 Направление канавок метчика
Геометрия метчиков
Передний угол зависит от обрабатываемого материала.
Боковые передние углы в главной секущей плоскости в точках режущей кромки, лежащих на диаметре di:
,
где ε – угол профиля резьбы.
Задний угол получают путем затылования режущей части по Архимедовой спирали (рис. 24 в). Величину затылования определяют по формуле:
Боковые задние углы в главной секущей плоскости в точках режущей кромки, лежащих на диаметре di:
.
Задний угол на вершине должен обеспечивать боковые задние углы в пределах 15…20΄ . Кинематический задний угол отличается от статического (рис. 23) и определяется по формуле:
Затылование калибрующей части метчика приводит:
к снижению сил трения;
к уменьшению опорной поверхности и ухудшению направления метчика в работе;
к быстрому уменьшению диаметра метчика при переточках;
к защемлению стружки между задней затылованной поверхностью и нарезаемой резьбой при вывинчивании метчика из обработанного отверстия.
Поэтому у ручных метчиков калибрующая часть не затылуется Гаечные метчики не вывертываются из обработанного отверстия, поэтому затылуются и по калибрующей части по наружному диаметру. Для обеспечения достаточной опоры затылуют не на всю ширину зуба, а оставляют 1/3 часть незатылованной .
а)
б) в) Рис.
24 Форма задней поверхности метчика
Комплектные метчики
Нарезание резьбы вручную одним метчиком можно осуществить только в сквозных отверстиях небольшого диаметра. Глухое отверстие трудно нарезать одним метчиком из-за большой толщины срезаемого слоя и возможного скопления стружки в канавках. Приходится применять комплект из нескольких метчиков и соответственно распределять между ними работу.
Применение комплекта метчиков позволяет:
уменьшить усилие резания,
улучшить качество и точность обработки,
уменьшить длину недореза при обработке глухих отверстий.
Черновой метчик выполняет основную работу по вырезанию профиля резьбы (50…70%) и имеет минимальный угол φ, а чистовой зачищает резьбу и калибрует (20…30%). Нагрузка может распределяться как по профильной (рис. 25 б) так и по последовательной (рис. 25 в) схемам резания.
В первом случае наружный и средний диаметры резьбы метчиков различны, резание осуществляется по всему профилю резьбы; каждый последующий метчик зачищает резьбу по сторонам, поэтому в точном исполнении нуждается только чистовой метчик. Чистовой метчик срезает металл по всей высоте профиля – стружка получается толстая, что приводит к увеличению интенсивности износа. Такая схема распространена для метрических резьб.
В случае последовательной схемы распределения припуска у метчиков в комплекте изменяется только наружный диаметр. Чистовой метчик менее нагружен. Отсутствие понижения по среднему диаметру у предварительных метчиков и неточное их изготовление может привести к браку. Применяется для трапецеидальных резьб с широким допуском и для труднообрабатываемых материалов.
в)
б)
Рис.
12. Распределение нагрузки между метчиками
комплекта
10.2.3.Бесканавочные метчики (рис. 13.)
Стружечная канавка не сквозная, а прорезается на длине несколько превышающей длину режущей части под углом наклона к оси 100…150. Направление канавки противоположно направлению нарезки резьбы. Дно канавки располагается под углом к оси метчика 50…100. на калибрующей части выполняется обратная конусность не менее 0,2 мм на 100 мм длины.
Достоинства бесканавочных метчиков:
снижение шероховатости обрабатываемой поверхности,
повышение прчности,
более полное использование материала за счет увеличения длины канавки.
Рекомендуются
при обработке легких сплавов, цветных
металлов, вязкой и нержавеющей сталей.
Метчики с шахматным расположением резьбы
Срезание зубьев метчиков в шахматном порядке(рис. 27) на калибрующей части позволяет снизить силы трения за счет уменьшения поверхности контакта резьбы метчика и нарезаемой детали. Рекомендуются для обработки тонкостенных деталей и при обработке вязких и труднообрабатываемых материалов.
При
обработке жаропрочных материалов и
титановых сплавов шахматное расположение
зубьев на режущей части позволяет без
увеличения крутящего момента повысить
толщину срезаемого слоя и осуществить
резание вне зоны наклепанного слоя.
Метчик-протяжка
Метчики-протяжки (рис.28) применяются для нарезания резьб крупного профиля, например трапецеидальных, в сквозных отверстиях. Обработка производится за один проход на токарном станке. Метчик-протяжка отличается повышенной прочностью и жесткостью, т.к. в отличие от обычных метчиков работают не на сжатие, а на растяжение. Это позволяет уменьшать толщину срезаемого слоя за счет увеличения длины режущей части.
10.3.Плашки
Плашка (рис.14.) предназначена для нарезания наружной резьбы и представляют собой гайку, сопряженную с нарезаемой резьбой, для чего у плашки прорезаются стружечные канавки и создаются задние углы.
Рис.
14. Резьбонарезная плашка
Наружный диаметр плашки D должен обеспечить прочность корпуса (рис.29):
,
где
D1 – диаметр на котором располагаются центры стружечных отверстий;
dc – диаметр стружечных отверстий;
Е
– размер, обеспечивающий прочность
плашки.
Режущая часть (рис.30) выполняется с двух сторон плашки, что повышает срок ее службы. Угол заборного конуса 2φ зависит от обрабатываемого материала и уменьшается с увеличением его прочности. Угол 2 φ может принимать значения от 250 до 900
Рис.30
Режущая часть плашки
Длина режущей части
,
где d – наружный диаметр резьбы,
d1 – внутренний диаметр резьбы,
B – величина облегчающая направление плашки в начале работы, В=0,2…0,4 мм.
Передний угол γ задают на внутреннем диаметре резьбы и выбирают в зависимости от обрабатываемого материала, γ =100…300.
Задние
углы получают путем затылования по
архимедовой спирали на режущей части
. Величина затылования
,
где z
- число перьев плашки, зависящее от
диаметра резьбы, z
= 3…12, α - задний угол, α = 60…90.
Между шириной пера F и шириной просвета C выдерживается соотношение F/C = 0,65…0,8; что обеспечивает прочность и жесткость пера, достаточное пространство для размещения стружки и число переточек, а также направление плашки в работе.
10.4.резьбовые фрезы
10.4.1.дисковые фрезы
гребенчатые фрезы
Универсальный метод:
Одним инструментом можно обрабатывать правые и левые резьбы, разные диаметры,
резьба нарезается до самого дна глухого отверстия
Требование к оборудованию: способность перемещения одновременно по трем координатам(xyz)
10.5.резьбонарезные головки
Резьбонакатной инструмент
Резьбонакатные плашки
Резьбонакатные ролики
Тема 7 зуборезный инструмент
§ 18 Методы формообразования зубчатых колес
План
18.1 Зубонарезание и зуборезный инструмент
18.2 Инструменты, работающие по методу копирования
18.3 Инструменты, работающие по методу обката
18.1 Зубонарезание и зуборезный инструмент
В современных машинах широко применяются зубчатые передачи. Различают силовые зубчатые передачи, предназначенные для передачи крутящего момента с изменением частоты вращения валов, и кинематические передачи, служащие для передачи вращательного движения между валами при относительно небольших крутящих моментах. Зубчатые передачи осуществляются путем зацепления различного вида зубчатых колес, которые относятся к числу наиболее распространенных деталей современных машин.
К зубчатым передачам предъявляются особые требования, характеризуемые условиями их эксплуатации. В процессе работы зубчатые колеса испытывают:
изгибающие деформационные нагрузки, вызывающие излом ножку зуба;
значительные контактные давления на поверхность зубьев, приводящие к истиранию, выкрашиванию (питтингу) и износу.
Поэтому к поверхности зубьев предъявляются требования по высокой поверхностной твердости (HRC 58-62), и шероховатости (Ra = 2,5-1,25 мкм) при относительно вязкой и пластичной сердцевине, что необходимо для обеспечения повышенной прочности при циклических и ударных нагрузках.
Исходя из таких высоких требования, производство зубчатых колес представляет собой трудоемкую работу на сложном оборудовании дорогостоящим зуборезным инструментом. Годовой расход на инструмент для зуборезных станков часто превышает стоимость самого станка и в несколько раз превышает заработную плату рабочего.
Способы формообразования зубьев зубчатых колес занимают самостоятельное место в общей классификации методов механиче механической обработки. Классификация основных методов формообразования зубчатых поверхностей и их возможности по обеспечению степеней точности и шероховатости приведены на рис. 18.1. Сюда включены все виды механической обработки посредством лезвийного инструмента (зубодолбление, зуботочение, зубопротягивание, зубофрезероване), отделочные операции (шлифование, шевингование, обкатывание зубьев, пр.), а также холодное накатывание зубьев как вид обработки давлением.
Как правило, обработка зубчатых колес осуществляется на зубообрабатывающих станках (зубострогальных, зубодолбежных, зубофрезерных, зубошлифовальных, пр.) режущими инструментами специальных конструкций (долбяки, резцы, протяжки, модульные и червячные фрезы, абразивные круги, пр.). Технологический процесс зубонарезания можно представить как выполнение ряда последовательных этапов:
черновая или предварительная нарезка зубьев;
чистовая нарезка зубьев;
отделка зубьев.
В зависимости от конструкции зубчатого колеса, формы его зубьев, требований к точности и чистоте поверхностей и объема производства применяются различные способы его изготовления и, соответственно, различные зуборезные инструменты.
При выборе зуборезного инструмента необходимо учитывать терминологию и обозначения, установленные:
ГОСТ 16530 – 83 Передачи зубчатые. Термины, определения и обозначения»
ГОСТ 16531 – 83 «Передачи зубчатые цилиндрические. Термины, определения и обозначения»
ГОСТ 18498 – 73 «Передачи червячные, определения и обозначения».
Наибольшее распространение в машиностроении получили зубчатые передачи с малочувствительным к изменению межцентрового расстояния эвольвентным зацеплением. И, следовательно, основная масса зубообрабатывающих инструментов, станков и оснастки предназначена для воспроизведения соответствующих этому зацеплению эвольвентных профилей и дна впадины на заготовках.
Основными элементами, точность которых определяет качество зубчатого зацепления, являются: профиль зуба; шаг зубьев; толщина зуба; концентричность зубьев и посадочного места; параллельность зубьев и оси колеса (для цилиндрических прямозубых колес), угол спирали (для косозубых колес).
18.1.1 Методы формообразования зубчатых колес
Получить зубья требуемого качества и притом достаточно экономично можно только при правильном выборе метода обработки. В основе получения этих профилей используют два принципиально различных метода формообразования: копирования и обката. Оба метода используются на различных зубообрабатывающих станках.
При методе копирования применяют инструменты, профиль режущей кромки которых совпадает с профилем впадины и при обработке копируется на заготовке. Сложный эвольвентный профиль режущей кромки такого инструмента позволяет выполнять обработку по этому методу при минимальном числе формообразующих движений на станках с простой кинематикой. При методе обката профиль режущей кромки отличается от профиля впадины, которая получается как огибающая нескольких последовательных положений инструмента. Режущая кромка этого инструмента при обработке эвольвентного профиля получает дополнительные движения формообразования, что усложняет кинематическую схему станка.
Таким образом, все зубообрабатывающие инструменты могут быть разделены на инструменты, работающие по методу копирования, и инструменты, работающие по методу обката.
18.2 Инструменты, работающие по методу копирования
К инструментам, работающим по методу копирования, относятся дисковые и пальцевые модульные фрезы, используемые в единичном производстве, зуборезные головки и протяжки, применяемые в массовом производстве.
18.2.1 Дисковые модульные фрезы
Дисковые модульные фрезы (рис. 18.2, а) – это фасонные фрезы с затылованными зубьями. Их основное преимущество в том, что они позволяют обрабатывать прямозубые и косозубые зубчатые колеса на универсальных фрезерных станках, а также нарезать крупномодульные колеса.
Рисунок
18.2 Схемы
обработки и инструменты, работающие
по методу копирования:
а
– дисковые модульные фрезы; б
– пальцевые модульные фрезы; в
– многорезцовая головка; г
– схемы нарезания цилиндрических колес
дисковыми и модульными фрезами; д
– схема нарезания шевронного колеса
пальцевой модульной фрезой 1
- корпус; 2
- сводящее кольцо; 3
- разводящее кольцо;
4
- специальные резцы DSрад
- движение радиальной подачи; ΔDSкр
- движение
круговой подачи; ΔDSпр
- движение
продольной подачи;
β
- угол наклона зубьев косозубого колеса
Обработка колес на универсальных фрезерных станках сопровождается погрешностями периодического деления, выполняемого делительной головкой, что вместе с погрешностями установки фрезы и отклонениями ее профиля не позволяет получить колеса выше 10-й и 9-й степеней точности. Отклонение профиля связано не только с погрешностями, возникающими при изготовлении фрезы, но также и с тем, что каждому числу зубьев соответствует свой профиль. Но иметь в условиях единичного производства для каждого числа зубьев свою фрезу экономически нецелесообразно, и поэтому приходится применять один и тот же инструмент для нарезания группы колес с близкими числами зубьев.
В основном наборе дисковых модульных фрез (до модуля m = 8) весь диапазон чисел зубьев с z = 12 и до ∞ (рейка) разбит на восемь групп, каждой из которых соответствует фреза своего номера (табл. 18.3).
С увеличением модуля усиливается влияние числа зубьев на профиль зуба, из-за чего для модулей колеса m > 8 диапазон зубьев разбивают не на 8, а на 15, а для более точных колес – на 26 номеров фрез.
Таблица 18.3 Группы дисковых модульных фрез
Номер фрезы |
1 |
2 |
3 |
4 |
5 |
6 |
7 |
8 |
Число зубьев колеса |
12-13 |
14-16 |
17-20 |
21-25 |
26-34 |
35-54 |
55-134 |
135 и более |
Обработку крупномодульных колес выполняют за два рабочих хода: черновой (подготовительный) и чистовой. Предварительная обработка выполняется фрезой сборной конструкции с зубьями упрощенного прямолинейного профиля и передним углом γ = 8…10о.
Сборные дисковые фрезы (рис. 18.2, а) оснащают ножами, затачиваемыми отдельно и при сборке вставляемыми в гнезда корпуса, где их перед закреплением выставляют на размер специальными клиньями. Вставные ножи сборных фрез так же, как и мелкомодульные (m = 1 мм) дисковые фрезы, изготовляют из твердых сплавов ВК6 и ВК8.
Чистовую обработку выполняют, имея небольшой припуск чистовыми цельными фрезами, изготовленными из быстрорежущих сталей повышенной производительности Р9К5, Р9К10, Р10К5Ф5 по ГОСТ 19265 – 73.
18.2.2 Пальцевые модульные фрезы
Пальцевые модульные фрезы (рис. 18.2, б) используют для нарезания крупномодульных прямозубых, косозубых и шевронных колес. Чистовые пальцевые фрезы выполняют с затылованными зубьями (z = 2…8), затачиваемыми по передней поверхности (γ = 0). Черновые пальцевые фрезы для улучшения условий резания имеют γ ≤ 8о и канавки на режущих зубьях для дробления стружки. Режущую часть пальцевых модульных фрез изготовляют из легированных и быстрорежущих сталей типа Р6М5.
Черновые и чистовые пальцевые фрезы выполняют цельной и сборной конструкции, крепят на станке с помощью резьбы и центрируют внутренней цилиндрической выточкой либо наружной проточкой.
При нарезании зубчатых колес дисковыми и пальцевыми модульными фрезами главное движение резания (рис. 18.2, г, д) сообщается инструменту, а движение подачи – заготовке, установленной в делительном приспособлении на столе станка. Направление движения подачи при обработке прямозубых колес совпадает с направлением зуба. Таким же образом направлено движение подачи при нарезании косозубых колес дисковой модульной фрезой, но при этом стол фрезерного станка разворачивают на угол β наклона зубьев и его ходовой винт зубчатыми передачами связывают со шпинделем делительной головки, где установлена заготовка. При нарезании косозубых и шевронных колес пальцевой модульной фрезой стол не разворачивают, но вращение его ходового винта передается зубчатыми колесами заготовке, установленной в шпинделе делительного устройства на столе.
В результате сложения движения стола и поворота заготовки нарезается наклонный или шевронный зуб (рис. 18.12 д).
18.2.3 Зуборезные головки
Зуборезные головки (рис. 18.2, в) представляют собой сложное устройство, в корпусе 1 которого установлены специальные резцы 4, перемещаемые в радиальном направлении сводящим 2 (при рабочем ходе) и разводящем 3 (при вспомогательном ходе) кольцами. Особенность работы зуборезных головок заключается в том, что резцы головки, по своему числу и профилю режущей кромки, совпадающие с числом и профилем впадин колеса, в процессе обработки постепенно подаются к центру колеса, обеспечивая одновременное нарезание всех зубьев. Зуборезные головки предназначены для нарезания зубьев лишь на одном определенном колесе. Использование головок требует применения специального оборудования и поэтому целесообразно лишь в массовом и крупносерийном производстве.
18.2.4 Протяжки
Протяжки применяют для обработки зубчатых колес внутреннего и наружного профиля. Протяжки для колес внутреннего профиля аналогичны шлицевым протяжкам с фасонным эвольвентным профилем режущих кромок. Протяжки для обработки колес наружного профиля могут быть однопрофильные, секторного и охватывающего типов.
П
ротяжки
однопрофильного типа используют для
последовательной обработки впадины с
поворотом заготовки (делением) на угловой
шаг (рис. 18.3, а).
Применяют протяжки прямолинейной (типа
шпоночных) или дисковой конструкции.
Протяжки секторного типа (рис. 18.3, б)
аналогичны наружным протяжкам с
соответствующим профилем режущих
кромок. Ими обрабатывают группу зубьев
колеса; для обработки следующей группы
зубьев необходим поворот заготовки.
Рисунок
18.3. Протяжки
для обработки зубчатых колес
Протяжки охватывающего типа могут быть разных конструктивных выполнений. У сборной протяжки (рис. 18.3, в) в корпусе в виде трубы установлены кольца с внутренними режущими зубьями эвольвентного профиля, соответствующего профилям впадин зубьев нарезаемых колес. Высота зубьев в кольцах, расположенных по длине протяжки, изменяется для создания подъема на зуб (tz). У протяжек другого вида (рис. 18.3, г) в продольных внутренних пазах корпуса установлены режущие секции, аналогичные рабочей части шпоночных протяжек с профилем, соответствующим впадинам зубьев обработанного колеса. В обоих видах протяжек рабочее движение резания сообщается заготовке.
Для чистовой обработки предварительно обработанных зубьев колес применяют шлифовальные круги дисковой формы с рабочим профилем, соответствующем профилю впадины зубьев колеса. Профиль образуется при фасонной правке круга алмазом на специальных приспособлениях, обеспечивающих теоретическую эвольвентную форму, с помощью копировальных приспособлений по шаблонам или путем замены эвольвентного профиля дугами окружности.
18.3 Инструменты, работающие по методу обката
Инструменты, работающие по методу обката, более универсальны, так как позволяют нарезать одним инструментом данного модуля колеса того же модуля с любым числом зубьев. Замена периодических делительных и связанных с ними вспомогательных движений (метод копирования) непрерывными делительными движениями, характерными для метода обката, не только повышает производительность, но и увеличивает точность обработки путем устранения случайных отклонений профиля. При нарезании по методу обката цилиндрических колес с прямым и винтовым зубом в процессе обработки имитируется зацепление воображаемого зубчатого колеса или рейки с нарезаемым колесом-заготовкой. Роль воображаемого зубчатого колеса выполняет инструмент – зуборезный долбяк, а роль рейки – зуборезные гребенки или червячные модульные фрезы.
18.3.1 Зуборезные долбяки
З
уборезные
долбяки (рис. 18.4) представляют собой
эвольвентные колеса, прямые или винтовые,
зубья которых изготовлены в виде режущих
элементов. Эти элементы у прямозубых
долбяков (рис. 18.4, б)
ограничены передней конической
поверхностью с γ = 5о
и задними поверхностями, две из которых
эвольвентные, а третья, коническая,
расположена при вершине зуба и образует
задний угол αв = 6…7о.
Рисунок
18.4. Схемы
работы и конструкции зуборезных долбяков
Для увеличения срока службы долбяка, повторно затачиваемого по передней поверхности, последняя смещена на величину а относительно исходного контура, в котором профиль зуба соответствует профилю и размерам некоррегированного колеса. Габаритные размеры долбяка определяются диаметром делительной окружности в исходном сечении dд, числом зубьев zд и высотой долбяка Н. Согласно ГОСТ 9323 – 79 принят ряд номинальных диаметров долбяка (dд ≈ mzд): 25, 38, 50, 80, 100, 125, 160 и 200 мм.
Размеры долбяка оказывают влияние на конструкцию (рис. 18.4, г) его крепежной части, которую у мелкомодульных долбяков выполняют в виде хвостовика, а у крупномодульных – в виде посадочного отверстия в диске, чашке или втулке, на периферии которых выполнены режущие зубья.
Э
ти
зубья изготовляют за одно целое с
корпусом долбяка либо образуют с ним
сборную конструкцию (для m = 10…40 мм),
в которой их закрепляют. Главным движением
резания при зубодолблении является
поступательное перемещение долбяка,
состоящее из рабочего (рис. 18.4, а)
хода, при котором срезается стружка, и
вспомогательного хода, при котором
заготовка для устранения трения отводится
от долбяка. Движениями подачи являются:
радиальное врезание Dsрад
долбяка на высоту зуба и обкат долбяка
и заготовки. При нарезании колес с
винтовым зубом (рис. 18.4, в)
используемый косозубый долбяк, винтовые
линии зубьев которого противоположны
направлению зубьев нарезаемого колеса,
совершает главное движение резания по
винтовой линии. Для создания нормальных
условий резания передние поверхности
зубьев косозубых долбяков затачивают
отдельно у каждого зуба.
Рисунок
18.5. Схемы
образования эвольвентного профиля при
обработке зуборезным долбяком (а)
и червячной модульной фрезой (б)
Материалом для изготовления долбяков служат быстрорежущие стали. Долбяк и обрабатываемое колесо при зубонарезании обкатываются по начальным окружностям без проскальзывания.
Из схемы формообразования впадины колеса (рис. 18.5. а), на которой показан ряд последовательных положений (обозначены цифрами 0, 1, 2, 3 и т.д.) режущих кромок долбяка, следует, что толщина срезаемого слоя при зубодолблении является величиной переменной не только при каждом последующем ходе долбяка, но и в течение срезания одного слоя. Наибольшую толщину срезаемого слоя снимают режущие кромки, расположенные по вершинам зубьев, а наименьшую – боковые выходные режущие кромки. С увеличением модуля нарезаемого колеса возрастает число рабочих ходов долбяка, необходимых для образования одной впадины, но средняя толщина срезаемого слоя при этом остается практически постоянной, так как изменяется только пропорционально скорости движения обката.
Долбяками нарезают прямозубые и косозубые колеса внешнего и внутреннего зацепления, а также шевронные колеса. Точность обработки при зубодолблении соответствует 6–7-й степени при Rz = 15…30 мкм.
Зуборезные гребенки
З
уборезная
гребенка представляет собой прямозубую
или косозубую рейку, зубья которой
превращены путем заточки в резцы (рис.
18.6). Прямозубые гребенки используют для
нарезания цилиндрических колес, а
косозубые – для нарезания шевронных
колес (рис. 18.6, б).
Прямозубые гребенки изготовляют двух
типов:

Рисунок 18.6 Схемы работы и конструкции зуборезных гребенок
гребенки (рис. 18.6, в), у которых положительное значение переднего угла обеспечивается ее наклоном при установке (под углом 6о30′) на станке,
гребенки с передним углом γ = 4о, устанавливаемые перпендикулярно направлению скорости резания.
Различают гребенки для предварительного (чернового) и для чистового нарезания. Гребенки для чистового нарезания имеют несколько большую ширину зуба. Рабочую часть гребенок выполняют из быстрорежущей стали, а крепежную, привариваемую к рабочей части, - из стали 45 или 40Х.
В процессе обработки нарезаемое колесо своей начальной окружностью обкатывается по начальной прямой гребенки (рис. 18.6, а). Главное движение резания – возвратно-поступательное перемещение – получает гребенка, которая при рабочем ходе снимает стружку, а при вспомогательном ходе для уменьшения трения она отводится от заготовки. Движение обката (движение подачи) складывается из медленного вращения заготовки и связанного с ним поступательного перемещения гребенки вдоль начальной прямой. Число рабочих ходов гребенки, а, следовательно, и толщина срезаемого слоя при нарезании одной впадины зависят только от скорости движения обката. В связи с тем, что длина гребенки короче длины начальной окружности колеса, в станке предусмотрен механизм, позволяющий после нарезания каждых одного-трех зубьев отводить гребенку в исходное положение для продолжения обработки.
Особенностью нарезания шевронных колес является использование работающих в паре косозубых гребенок с углом наклона зубьев β = 30о. Каждая из гребенок обрабатывает свою сторону шеврона, при этом происходит возвратно-поступательное движение резания. Гребенки, работающие в паре, изготовляют комплектами, а для улучшения условий резания заточку переднего угла на гребенках делают с двух сторон (18.6, г).
Червячные зуборезные фрезы
Червячная зуборезная фреза может быть представлена в виде совокупности закрепленных на цилиндрической поверхности гребенок, либо в виде червяка, витки которого превращены в режущие зубья прорезанием поперечных канавок так, что на них образуются передние углы γ, и затылованием зубьев для получения задних углов α.
Основой профиля стандартных червячных фрез является конволютный червяк, витки которого в сечении, нормальном к направлению витка, имеют прямолинейный профиль исходной зубчатой рейки (рис. 18.7, б). Профиль исходной рейки характеризуется углом профиля αп = 20о, шагом зубьев Рп = πт, расчетной высотой зуба hи и его головки h′, а также толщиной зуба фрезы по нормали sn.
Рисунок
18.7 Схемы
работы и конструкции червячных фрез
о
назначению различают червячные фрезы
для нарезания цилиндрических прямозубых
и косозубых колес, для обработки червячных
колес, шлицевых валов, звездочек и т.д.
По конструкции червячные фрезы бывают
цельными и сборными, могут закрепляться
на оправках (насадках) или с помощью
хвостовиков.
Так как червячные фрезы обрабатывают шлифованием для получения требуемой точности, их режущую часть изготовляют из быстрорежущих сталей Р6М5 и Р12. У фрез со шлифованным профилем необходимо делать двойное затылование. Для обеспечения благоприятных условий резания при зубонарезании затылование на вершинах зубьев необходимо выполнять с αв = 10…12о, что позволяет обеспечить задние углы на боковых сторонах зубьев αб = 2…3о. Наряду с затылованными при черновой обработке находят применение сборные червячные фрезы с острозаточенным зубом (α = 10…12о; γ = 10…15о). Для увеличения стойкости и повышения в 2-3 раза производительности сборных фрез в их конструкции используют неперетачиваемые пластины или режущие гребенки, изготовленные из твердого сплава ВК6-М, ВК8, Т5К10, Т15К6 и т.д.
При зубофрезеровании в формообразовании впадины колеса (рис. 18.7, б) участвуют режущие кромки, расположенные по вершинам и боковым поверхностям зубьев фрезы. При этом режущие кромки, расположенные по вершинам, снимают средние толщины срезаемого слоя в 3 раза большие, чем толщины слоя, срезаемого боковыми режущими кромками. Число срезаемых слоев, приходящихся при зубофрезеровании на одну впадину колеса, возрастает с увеличением числа канавок на фрезе, снижая толщину срезаемого слоя и уменьшая нагрузку на зуб фрезы.
При нарезании прямозубых и косозубых колес червячными модульными фрезами имитируется зацепление обрабатываемого колеса с червяком, роль которого выполняет червячная фреза. За главное движение резания принимают вращение (рис. 18.7, а) фрезы, частоту пф которого для создания движения обката согласуют с вращением заготовки так, чтобы за время одного оборота фрезы заготовка повернулась на k/zз – часть оборота, где k – число заходов червячной фрезы. Для радиального врезания фрезы в заготовку и нарезания зубьев по всей ее высоте фрезе соответственно сообщают радиальное движение подачи Dsрад и вертикальное движение подачи Dsв, направленное вдоль оси нарезаемого колеса. Перед обработкой червячную фрезу разворачивают так, чтобы направление ее винтовой линии совпадало с направлением нарезаемых зубьев. Заготовке косозубого колеса дифференциал, установленный в цепи обката станка, сообщает дополнительное вращение ± Ds, обеспечивающее при сложении с Dsв формообразование винтовых зубьев колеса. Знак дополнительного поворота ΔDs зависит от совпадения или несовпадения направления винтовой линии зуба колеса с направлением вращения заготовки (рис. 18.7, в).
При черновом зубофрезеровании расстояние, на которое перемещается фреза в радиальном направлении, выбирают обычно таким, чтобы всю обработку выполнить за один рабочий ход. Чистовое зубонарезание выполняют за несколько рабочих ходов, последний из которых проводится с радиальным припуском 0,10-0,15 мм, обеспечивая при этом шероховатость Ra = 6,3…0,8 мкм. В зависимости от направления подачи Dsв относительно скорости резания различают попутное и встречное зубофрезерование. Попутное зубофрезерование обеспечивает меньший износ инструмента и соответствует меньшей шероховатости, но требует отсутствия свободного хода в механизме подачи (Dsв) станка (рис. 18.7, в).
Назначение режимов резания при обработке червячными фрезами происходит по известному алгоритму для фрез. Исходными данными при этом являются требования по обеспечению точности и состояния поверхностного слоя при заданном качестве обработки, а также технологическая себестоимость обработки. За основу принимается значение допустимого износа зубьев фрезы по задней поверхности и соответствующая этому износу стойкость фрезы. Червячные фрезы являются одним из самых сложных в изготовлении и, соответственно, дорогостоящим инструментом. Поэтому значительный эффект в повышении стойкости и возможности назначения повышенных скоростей резания может обеспечить применение новых инструментальных материалов.
Тема 8 абразивные инструменты
§ 20 Конструктивные особенности абразивных инструментов
План
20.1 Технологические особенности шлифования
20.2 Конструктивные элементы абразивных инструментов
20.3 Принципы выбора абразивных инструментов
20.4 Маркировка шлифовальных кругов
20.5 Режимы резания при шлифовании
20.1 Технологические особенности шлифования
В современном машиностроении для снижения шероховатости обрабатываемой поверхности применяют метод шлифовальной обработки. Шлифованию подвергают различные поверхности деталей машин: плоские, цилиндрические, фасонные, внутренние, наружные и т.п. Наиболее часто обрабатывают поверхности деталей, имеющих ось вращения (валы, втулки, резьбы и др.), а также плоские поверхности (плоскости, уступы, пазы и др.). В условиях такого разнообразия обработки имеется множество различных схем шлифования. Но для всех способов кинематическая схема одинакова: главным движением резания является вращательное движение шлифовального круга Dг, а движение подачи Ds совершает заготовка (рис. 20.1.).
Рисунок
20.1 Схема
срезания припуска при шлифовании и
конструктивные особенности абразивного
инструмента:
1
– зерна; 2
– связка; 3
– поры;
4
- заготовка
Для окончательной обработки заготовок методом шлифования, а также отделочной обработки хонингованием, суперфинишированием, полированием применяются абразивные инструменты.
Абразивные инструменты –
это режущие инструменты, изготовленные из зерен шлифовальных материалов, сцепленных между собой связующим веществом – связкой, и разделенных друг от друга порами.
20.1.1 Конструктивные особенности абразивного инструмента
Абразивные инструменты имеют свои конструктивные особенности. Для операций шлифования, хонингования, полирования и других отделочных операций применяют шлифовальные круги, головки, бруски, сегменты. Для шлифования и отделочной обработки заготовок фасонного профиля применяют шлифовальные ленты. При притирке и полировке, а также жидкостной отделочной обработке применяют свободные абразивные порошки и пасты.
Геометрические особенности конструкции абразивных инструментов в том, что, в отличие от лезвийных, они не имеют сплошных режущих кромок. Режущая часть абразивных инструментов – это множество мелких абразивных зерен, которые расположены хаотически и находятся на некотором расстоянии друг от друга. Зерна имеют неправильную геометрическую форму с несколькими режущими лезвиями, каждое из которых имеет свои геометрические параметры α, β, γ, φ, φ1, λ. Передний угол γ у режущих лезвий зерен, как правило, отрицательный. Радиус закругления режущих кромок абразивных зерен близок к нулю в отличие от лезвийного инструмента, радиус при вершине режущего клина которых составляет от нескольких десятков до нескольких сотен микрон.
Таким образом, процесс резания заключается в том, что каждое зерно-резец царапает материал. Такое хаотичное царапание абразивными зернами в совокупности приводит к срезанию с обрабатываемой поверхности тончайших слоев конструкционного материала (несколько микрометров).
Абразивные зерна изготовлены из инструментальных материалов, обладающих высокой твердостью и теплостойкостью, что позволяет обрабатывать твердые, труднообрабатываемые материалы с высокими скоростями резания. Исходя из этого, процесс резания в условиях обработки абразивными инструментами происходит с высоким температурным режимом. В зоне контакта абразивных зерен с материалом заготовки возникают мгновенные температуры до 1000…1600оС. Это оказывает влияние на физико-химические и эксплуатационные свойства обрабатываемой поверхности, часто вызывает на поверхности детали прижоги, остаточные напряжения и шлифовальные трещины. Эти явления определяют сдерживающий фактор повышения производительности и предъявляют специфические требования к процессу резания при шлифовании:
применение обильного охлаждения (СОТС);
выбор круга с оптимальными характеристиками;
назначение оптимальных режимов обработки.
Кроме того, абразивный инструмент, как и любой лезвийный, по мере затупления и износа или разрушения зерен требует периодической заточки. Нельзя говорит о заточке в том виде, которая применяется для режущего инструмента. Мы уже определили, что каждое зерно имеет свою геометрию. Поэтому восстановление режущих свойств абразивных инструментов называется правкой.
Правка - процесс обновления режущей поверхности круга для повышения режущих свойств и качества поверхностного слоя обрабатываемой поверхности
20.1.2 Классификация абразивного инструмента
Классифицируют абразивный инструмент по следующим признакам:
геометрическая форма: шлифовальные круги, головки, сегменты, бруски, абразивные ленты и шкурки;
род абразивного материала: абразивные, алмазные, эльборовые и др.;
вид основы:
- жесткая: шлифовальные круги, головки, сегменты, бруски;
- гибкая: эластичные круги, абразивные ленты и шкурки;
- жидкая: пасты, суспензии.
20.2 Конструктивные элементы абразивных инструментов
Абразивные инструменты на жесткой основе характеризуются: формой и размерами;
- шлифовальным материалом;
- зернистостью шлифовального материала;
- связкой;
- твердостью;
- точностью;
- неуравновешенностью;
- концентрацией зерен в рабочем слое (для алмазных и эльборовых инструментов).
Рисунок
20.2 Некоторые
типы абразивных инструментов: а
– абразивные круги; б
– алмазные и эльборовые круги; в
– шлифовальные головки; г
– шлифовальные бруски; д
– шлифовальные сегменты
20.2.1 Форма и размеры
Конструктивные и геометрические параметры абразивных инструментов задаются:
станком, на котором предполагается их использование;
формами и размерами обрабатываемых поверхностей;
характером движений инструмента.
Основные размеры абразивных инструментов регламентированы нормативно-технической документацией (см. рис. 20.2, табл. 20.1).
Таблица 20.1 Применение абразивных инструментов
Абразивный инструмент |
Характеристика формы |
Область применения |
1 |
2 |
3 |
Абразивные круги (рис. 20.2, а) По форме они представляют собой различные тела вращения
|
ПП – Плоские круги прямого профиля |
|
2П – Плоские круги с двухсторонним коническим профилем |
|
|
ПВ – Плоские круги с выточкой ПВД – Плоские круги с двухсторонней выточкой |
|
|
ЧЦ, ЧК – Цилиндрические и конические круги-чашки |
|
|
Т – Тарельчатые круги |
|
|
Алмазные круги (рис. 20.2, б) |
Плоского прямого профиля, чашечные, тарельчатые, дисковые и др |
|
Эльборовые круги |
Формы, подобные алмазным кругам |
|
Шлифовальные головки (рис. 20.2, в) |
Шлифовальные круги небольшого диаметра (3…40 мм) |
|
Окончание таблицы 20.1
1 |
2 |
3 |
Шлифовальные бруски (рис. 20.2, г) |
|
|
Шлифовальные сегменты (рис. 20.2, д) |
Шлифовальный круг состоит из нескольких сегментов, закрепленных в головке или патроне |
|
Шлифовальные шкурки |
Ленты на гибкой или комбинированной основе – бумага, ткань, металлическая лента, с наклеенным на нее слоем шлифовального материала, закрепленного связкой |
|
Основные размеры абразивных инструментов регламентированы нормативно-технической документацией.
20.2.2 Шлифовальные материалы
Рабочими элементами любого абразивного инструмента являются частицы абразивного материала после сортировки, дробления, измельчения, очистки от посторонних примесей. Их твердость выше твердости обрабатываемого материала. А выбор их осуществляется в зависимости от физико-механических свойств и химического состава обрабатываемого материала и условий шлифования. В качестве абразивного материала широко применяются электрокорунды, карбид кремния, алмаз, кубический нитрид бора (эльбор). Наиболее широкое применение в машиностроении находят круги из электрокорунда и карбида кремния по ГОСТ 2424 – 83, алмазные круги по ГОСТ 16167 – 80, 16172 – 80Е и др., а также эльборовые круги по ГОСТ 17123 – 79Е.
Каждая группа абразивных материалов обладает своими особенностями при обработке различных материалов: режущие свойства, износостойкость, теплостойкость, способность сопротивляться адгезионному изнашиванию и др.
Электрокорунды (кристаллическая окись алюминия Al2O3) получают из естественных бокситов с незначительными примесями некоторых материалов. Выпускают следующие разновидности электрокорундов:
- нормальный (13А – 16А);
- белый (22А – 25А);
- хромистый (32А – 34А);
- титановый (37А);
- монокорунд (43А – 45А);
- циркониевый (38А).
По мере возрастания номера индекса растет процентное содержание окиси алюминия и увеличивается режущая способность. Легируя глинозем в процессе плавки титаном, цирконием, хромом, получают абразивные материалы с требуемыми свойствами.
Круги из электрокорунда белого применяют в основном при чистовой и отделочной обработке закаленных сталей, а также углеродистых, быстрорежущих, легированных и нержавеющих сталей. Круги из электрокорунда нормального широко применяют на обдирочных и чистовых операциях обработки материалов, имеющих высокий предел прочности на растяжение.
Круги из монокорунда используют чаще всего для получистовой и чистовой обработки средне- и высоколегированных сталей, подвергнутых хромированию, азотированию и закалке.
Круги из хромотитанистых электрокорундов используют на операциях, где имеется опасность появления прижогов или требуется высокая стойкость инструментов, особенно по сохранению профиля рабочей поверхности.
Карбид кремния (карборунд) содержит 97-99 % SiC и незначительные примеси других элементов. Выпускают две разновидности карбида кремния:
- черный (53С, 54С);
- зеленый (63С, 64С).
Зеленый карбид кремния более хрупок, чем черный, и применяется для обработки чугуна, твердых сплавов, цветных металлов, камня. Черный карбид кремния более прочен и применяется в аналогичных случаях, но более тяжелых условиях обработки. Крупнозернистые круги из карбида кремния используют для обработки неметаллических материалов и правки шлифовальных кругов.
Алмазные инструменты в настоящее время широко используются в машиностроении в виде кругов, порошков, правящего инструмента. В инструментах природный алмаз условно обозначают А, синтетические алмазы – АС. По ГОСТ 9206 – 80Е выпускают алмазные шлифпорошки следующих марок: АСО, АСР, АСВ, АСК, АСС (шлифзерно 2000-160 мкм, шлифпорошки 125-40 мкм, микропорошки 63-14 мкм, тонкие шлифпорошки 10-3 мкм).
Абразивный инструмент из природного и синтетических алмазов широко применяют для обработки заготовок и инструмента из твердых сплавов, стекла, керамики, кремния, бурового инструмента.
Кубический нитрид бора – синтезированный абразивный материал, который можно встретить под названиями: борозон, композит, гексанит, эльбор, кубонит, КНБ. По своим прочностным характеристикам и режущей способности эльбор близок к алмазу. Его условно обозначают Л
Шлифовальные круги, бруски, шкурки из эльбора применяют для обработки легированных труднообрабатываемых жаропрочных сталей и сплавов.
Для заточки и вышлифовки канавок инструментов из закаленных инструментальных сталей используют эльбор, а из твердых сплавов – синтетический алмаз.
20.2.3 Зернистость шлифовальных материалов
Зернистость инструмента характеризует размер зерен основной группы:
- шлифзерно сортируют специальными ситами с размером ячеек 200-16 мкм,
- а шлифпорошки с размером ячеек 12-3 мкм,
- мелкие зерна называют микропорошками (М63-М14) или тонкими микропорошками (М10-М5).
Зернистость шлифовального материала на абразивном инструменте указывают в десятках микрометров, например, зернистость 40 означает размер зерна 400 мкм.
Номер зернистости круга увеличивают:
- для уменьшения опасности «засаливания» круга и появления прижогов на заготовке;
- при увеличении припуска на обработку;
- для увеличения производительности процесса шлифования;
- при увеличении скорости шлифовального круга;
- при переходе от кругов с керамической связкой на круги с бакелитовой или вулканитовой связками;
- при увеличении вязкости и уменьшении твердости материала заготовки;
- при уменьшении номера структуры круга.
Алмазные материалы делят на шлифпорошки и микропорошки. Размер шлифпорошков находится в пределах от 630 до 40 мкм (по размерам ячеек верхнего и нижнего сита), а размер микропорошков – от 60 до 1 мкм и менее (контролируется на микроскопе). Зернистость алмазных порошков обозначается дробью, в которой числитель соответствует наибольшему размеру зерен основной фракции, а знаменатель – наименьшему размеру, например:
- алмазных порошков – 60/40, 40/28 и т.д.,
- эльборовых порошков – Л315/250 (Л25), Л250/200 (Л20) и т.д.
Связка абразивных инструментов
Зерна в теле инструмента должны быть связаны между собой для придания формы абразивному инструменту. Для сцепления зерен шлифовальных материалов используются специальные связующие материалы, которые удерживают их от преждевременного выкрашивания в процессе шлифования. Такой связующий материал называется связкой. Она оказывает большое влияние на работоспособность абразивных кругов. От количества, вида, качества и равномерности распределения связки в абразивном круге зависят твердость, прочность, структура, неуравновешенность круга и допускаемая скорость шлифования.
Связка играет сложную роль в процессе механической обработки абразивным инструментом. Для удержания зерен, она должна удовлетворять следующим требованиям:
- быть хрупкой – легко разрушаться;
- в то же время быть вязкой – выдерживать большие колебания резания без разрушения;
- быть очень прочной – удерживать абразивные зерна до их полного изнашивания или выкрашивания;
- выдерживать высокую температуру в зоне резания и т.д.
Существует три группы связок абразивных инструментов, в основе которых лежат их физико-механические свойства:
органические (бакелитовая, вулканическая, глифталиевая);
минеральные (керамические, силикатные);
металлические (сплавы на основе меди, олова, железа, алюминия и др.).
Бакелитовая связка (Б, Б1, Б2 и др.) представляет собой смолу (пульвербакелит) в виде порошка и бакелитового лака. Абразивные круги с такой связкой обладают высокой прочностью и упругостью, что позволяет изготавливать их малой толщины. Недостатком бакелитовой связки является ее низкая теплоемкость, вследствие чего связка при температуре 250…300ОС выгорает, а зерна абразива выкрашиваются. Твердость таких кругов резко снижается при работе с СОЖ, поэтому круги на бакелитовой связке обычно работают всухую. При добавлении в бакелитовую связку наполнителя – криолита, стойкость кругов повышается.
Вулканитовая связка (В, В1, В2 и др.) в основе имеет синтетический каучук, смешанный с небольшим количеством серы. По сравнению с кругами на бакелитовой основе, круги на вулканитовой связке более упруги, но менее теплостойки. Такая эластичная связка позволяет изготовлять тонкие, до десятых долей миллиметра, отрезные круги диаметром 150…200 мм.
Глифталиевая связка также относится к органическим. В ее основе – синтетические смолы из глицерина. Ее применяют как связующее вещество карбида кремния зеленого малой зернистости и используют для полирования. Эта связка находит применение при изготовлении поропластовых (высокопористых) кругов, объем пор которых доходит до 80 %.
Керамическая связка (К0, К1, К3 и др.) состоит из огнеупорной глины, полевого шпата, кварца и других материалов. Их изготавливают с использованием электрокорунда и карбида кремния. Круги на керамической связке обладают высокой прочностью, кромкостойкостью, допускают применение СОЖ. Однако они обладают повышенной хрупкостью и малоупруги, поэтому тонкие круги на керамической связке не могут воспринимать боковые нагрузки. Применяют такие круги для всех видов шлифования, за исключением отрезки и прорезания узких пазов.
Металлическая связка отличается высокой прочностью и износостойкостью. Круги на этой связке длительно сохраняют рабочий профиль и применяются в основном при съеме небольших припусков.
Алмазные и эльборовые круги изготавливают на бакелитовой, металлической и реже на керамической связке. Из них металлическая связка применяется наиболее часто.
По отношению к общему объему производства выпуск шлифовальных кругов на керамической связке составляет 50-60 %, несмотря на сравнительную сложность изготовления. Кругов на бакелитовой связке выпускается 30_35 %, на вулканитовой – 4-7 %, на других связках – не более 1 %.
20.2.4 Структура шлифовального круга
Процентное соотношение трех основных фазовых составляющих – зерен, связки и пор, в объеме абразивного инструмента называют структурой. Структуры абразивных инструментов обозначают номерами от 0 до 20. С увеличением номера структуры число зерен уменьшается, а объем связки увеличивается (табл. 20.2).
Структуры подразделяет на закрытые или плотные (1-4), средние (5-8), и открытые (9-12). Структуры 13-20 – высокопористые или очень открытые. Например, у инструмента со структурой 0 объемная концентрация зерен 62 %, а со структурой 20-22 %.
Таблица 20.2 Зависимость объема зерен от номера структуры
Структура |
|||||||||
плотная |
средняя |
открытая |
очень открытая |
||||||
№ |
Объем зерен, % |
№ |
Объем зерен, % |
№ |
Объем зерен, % |
№ |
Объем зерен, % |
||
0 1 2 3 4 |
62 60 58 56 54 |
5 6 7 8 |
52 50 48 46 |
9 10 11 12 |
44 42 40 38 |
11-14 15-16 17-18 19-20 |
36-34 32-30 28-26 24-22 |
20.2.5 Концентрация зерен
Это условная характеристика режущей способности алмазных и эльборовых кругов. Под 100 %-ной концентрацией алмаза или эльбора понимают 25 % объема абразивной составляющей или 0,878 г (4,4 карата) зерен в 1 см3 абразивного слоя. Остальные 75 % - связка, поры, наполнители. При 150 %-ной концентрации в составе абразивного инструмента содержится 37,5 % зерен алмаза или эльбора и т.д. С увеличением концентрации повышается режущая способность и стойкость кругов.
20.2.6 Твердость абразивных инструментов
Твердостью абразивного инструмента называют способность связки противодействовать выкрашиванию абразивных зерен инструмента при воздействии на него внешних сил при сохранении инструментом требуемых характеристик в пределах установленной нормы.
Таблица 20.3 Шкала степени твердости абразивных инструментов
Твердость инструмента |
Обозначение |
Твердость инструментов на связках |
|
керамической и бакелитовой |
вулканитовой |
||
Чрезвычайно мягкий |
ЧМ |
– |
– |
Весьма мягкий |
ВМ ВМ1 ВМ2 |
– |
– |
Мягкий |
М |
М1, М2, М3 |
– |
Среднемягкий |
СМ |
СМ1, СМ2 |
– |
Средний |
С |
С1, С2 |
С |
Среднетвердый |
СТ |
СТ1, СТ2, СТ3 |
СТ |
Твердый |
Т |
Т1, Т2 |
Т |
Весьма твердый |
ВТ |
ВТ1, ВТ2 |
– |
Чрезвычайно твердый |
ЧТ |
ЧТ1, ЧТ2, ЧТ3, ЧТ4, ЧТ5, ЧТ6, ЧТ7, ЧТ8, ЧТ9, ЧТ10 |
– |
Здесь цифры характеризуют твердость абразивного инструмента в порядке ее возрастания.
Твердость – один из самых важных показателей работоспособности инструмента: в чрезвычайно мягком круге могут вырываться из связки еще работоспособные зерна. В то же время в чрезмерно твердом круге изношенные зерна сохраняются в связке, что ухудшает параметры качества обрабатываемой поверхности. Чем меньше твердость инструмента, тем мене прочна связь между зернами и тем легче и быстрее из него удаляются изношенные зерна. Чем выше твердость, тем больше связки и меньше пор. Таким образом, абразивные инструменты из одного и того же материала с одной и той же связкой могут иметь различную твердость. Изменение объема связки на 1,5 % приводит к изменению твердости на одну степень.
При шлифовании в большинстве случаев применяют абразивные круги средней твердости. Они обеспечивают высокую производительность и бо́льшую стойкость. При бесцентровом, внутреннем и плоском шлифовании применяют более мягкие круги, чем при круглом наружном шлифовании. При профильном шлифовании, резьбошлифовании, шлифовании прерывистых поверхностей и заготовок малых диаметров используют более твердые круги. Более твердыми кругами выполняют также шлифование с применением СОЖ.
20.2.7 Точность абразивных инструментов
Класс точности абразивного инструмента зависит:
- от отклонений его параметров при изготовлении – размеров, формы, расположения поверхностей и т.п.;
- от требований к зерновому составу;
- от наличию сколов, трещин и раковин.
Шлифовальные круги выпускают трех классов точности: АА, А и Б, в то время, как остальные инструменты имею два класса точности: А и Б.
Круга класса АА имеют наименьшие отклонения от заданных размеров. Допускаемые отклонения для инструментов класса Б в 1,5…2,0 раза превышают отклонения аналогичных параметров класса А, которые в свою очередь больше, соответствующих классу АА.
20.2.8 Неуравновешенность шлифовальных кругов
При несовпадении центра масс шлифовального круга с центром вращения возникает его неуравновешенность. Причинами неуравновешенности могут быть:
- погрешности установки круга на планшайбе и планшайбы с кругом на шпинделе станка;
- погрешности геометрической формы круга;
- неравномерный износ круга в процессе шлифования.
Неуравновешенность круга приводит к появлению вибраций, а вследствие этого к ухудшению качества обрабатываемой поверхности (огранка, волнистость, прижоги и т.п.), преждевременному выходу из строя шпиндельного узла станка, а иногда даже разрушению круга в процессе работы.
В зависимости от допускаемых неуравновешенных масс установлены четыре класса неуравновешенности по мере их возрастания: 1, 2, 3, 4. Причем круги класса точности АА должны иметь наименьшую неуравновешенность 1 класса, класса точности А могут иметь неуравновешенность 1 и 2 классов, а класса точности Б – 1, 2 и 3 классов неуравновешенности.
20.2 Принципы выбора абразивных инструментов
1. Размеры шлифовальных кругов рекомендуется брать возможно бо́льшими, так как в этом случае улучшаются условия шлифования и снижается стоимость обработки. При этом верхний предел размеров круга ограничивается конструкцией и размерами станка, а иногда – размерами и формой обрабатываемой заготовки. Так, например, при шлифовании отверстий диаметр круга должен быть не более 0,7…0,9 диаметра обрабатываемого отверстия.
2. Зернистость абразивного круга зависит от вида шлифования, требуемой шероховатости и точности обработки, материала заготовки и снимаемого припуска. Чаще всего применяют абразивные круги средней зернистости 40…16, которые обеспечивают высокую производительность при требуемой шероховатости и точности обработки.
При использовании алмазных кругов рекомендуется брать:
- для предварительного шлифования круги зернистостью – 200/160…100/80 (марок АС4, АС6),
- для чистового шлифования – зернистостью 80/63…50/40 (марок АС2, АС4),
- для доводочного шлифования – зернистостью 40/28 и мельче.
В случае, когда предварительное и окончательное шлифование производятся одним кругом, следует применять круги зернистостью 100/80…63/50 (марок АС4, АС6).
3. Структуру шлифовального круга выбирают исходя из области его применения, табл. 20.4.
Таблица 20.4 Область применения абразивного инструмента в зависимости от его структуры
Номер структуры |
Область применения |
0 … 3 |
|
5 … 8 5 … 6 7 … 8 8 … 9 |
|
9 … 12 |
|
высокопористые |
|
4. В зависимости от концентрации зерен для окончательного шлифования и доводки рекомендуют алмазные или эльборовые круги 100 % и 150 % концентрации, а для профильного шлифования – круги 150 % и 200 % концентрации.
Предварительное шлифование и заточку твердосплавных инструментов выполняют кругами на металлической связке со 100 % или 150 % концентрацией; резьбошлифование и шлифование твердосплавных инструментов и мелкомодульных фрез – кругами со 150 % концентрацией алмазов.
5. При выборе твердости абразивного инструмента рекомендуется придерживаться следующего правила: чем мягче обрабатываемый материал, тем твердость круга должна быть выше и наоборот.
6. В зависимости от класса точности абразивный инструмент выбирают от требований к качеству обрабатываемой поверхности:
АА – для прецизионной обработки шлифованием высокоточных заготовок из материалов всех групп обрабатываемости, а также скоростного и высокоскоростного прецизионного шлифования особо точных заготовок;
А – для окончательной обработки шлифованием заготовок из материалов всех групп обрабатываемости, а также для скоростного и высокоскоростного окончательного шлифования;
Б – для менее ответственных операций абразивной обработки.
20.4 Маркировка шлифовальных инструментов
Маркировка наносится на одной из сторон шлифовального круга, например,
ПП 500х50х305 24А 10-П С2 7 К5 325 м/с А 1 кл ГОСТ 2424-83,
и содержит в себе следующие данные:
- ПП – тип круга;
- 500х50х305 – наружный диаметр х высота х диаметр посадочного отверстия;
- 24А – марка шлифовального материала;
- 10-П – зернистость;
- С2 – степень твердости;
- 7 – номер структуры;
- К5 – марка связки;
- 35 м/с – рабочая окружная скорость;
- А – класс точности круга;
- 1 кл – класс неуравновешенности.
Пример маркировки алмазного шлифовального круга
1 А 1 300х40х76х5 ас4 100/80 100 бп2 2720-0139 гост 16167-80:
- 1 – форма сечения корпуса;
- А – форма сечения алмазоносного слоя;
- 1 – расположение алмазоносного слоя на корпусе круга;
- 300х40х76х5 – наружный диаметр х высота х диаметр посадочного отверстия х толщина алмазоносного слоя;
- АС4 – марка алмазного шлифпорошка;
- 100/80 – зернистость алмазного шлифпорошка;
- 100 – условная концентрация шлифматериала;
- БП2 – марка связки;
- 2720-0139 – обозначение типоразмера круга.
МЕТАЛЛОРЕЖУЩИЕ СТАНКИ.
Таблица 1 Нумерация серийно выпускаемых станков
Наименование станков |
Шифр группы |
Шифр типа |
|||||||||||
0 |
1 |
2 |
3 |
4 |
5 |
6 |
7 |
8 |
9 |
||||
Резервные |
0 |
- |
|||||||||||
Токарные |
1 |
Автоматы и полуавтоматы: |
Токарно- револьверные |
Сверлильно- отрезные |
Карусельные |
Токарные и лобовые |
Многорезцевые и копировальные |
Специализи- рованные |
Разные токарные |
||||
специализи- рованные |
одношпин- дельные |
многошпин- дельные |
|||||||||||
Сверлильные и расточные |
2 |
- |
Вертикально- сверлильные |
Полуавтоматы |
Координатно-расточные |
Радиально- сверлильные |
Горизонтально- расточные |
Алмазно- расточные |
Горизонтально- сверлильные |
Разные сверлильные |
|||
одношпин- дельные |
многошпин- дельные |
||||||||||||
Шлифовальные и доводочные |
3 |
Круглошли- фовальные |
Внутришли- фовальные |
Обдирочно- шлифовальные |
Специализи- рованные шлифовальные |
- |
Заточные |
Плоско- шлифовальные |
Притирочные, полировальные, хонинговальные, доводочные |
Разные образивные |
|||
Электро- физические и электро- химические |
4 |
- |
Светолучевые |
- |
Электро- химические |
Электро- искровые |
- |
Электро- эрозионные, ультрозвуковые прошивочные |
Анодно- механические отрезные |
- |
|||
Зубо- и резьбо-обрабатываю- щие |
5 |
Резьбо- нарезные |
Зубодолбежные для обработки цилиндри- ческих колес |
Зуборезные для обработки конических колес |
Зубофрезер- ные для обработки цилиндрических колес и шлицевых валов |
Для нарезания червячных колес |
Для обработки торцов зубьев колес |
Резьбофре- зерные |
Зубоотделоч- ные, провероч- ные и обкатные |
Зубо- и резь- бошлифоваль- ные |
Разные зубо- и резьбо- обрабатываю- шие |
||
Фрезерные |
6 |
- |
Вертикально- фрезерные консольные |
Фрезерные не- прерывного действия |
Продольные одностоеч- ные |
Копироваль- ные и грави- ровальные |
Вертикаль- ные бесконсольные |
Продольные двухстоеч- ные |
Консольно- фрезерные опе- рационные |
Горизонталь- но-фрезерные консольные |
Разные фрезерные |
||
Строгальные, долбёжные, протяжные |
7 |
Продольные |
Поперечно- строгальные |
Долбёжные |
Протяжные горизонталь- ные |
Протяжные вертикальные для протягивания |
- |
Разные строгальные |
|||||
одно- стоечные |
двух- стоечные |
внутренного |
наружного |
||||||||||
Разрезные |
8 |
Отрезные, оснащенные |
Правильно- отрезные |
Пилы |
- |
- |
|||||||
токарным резцом |
шлифоваль- ным кругом |
гладким или насеченным диском |
ленточные |
дисковые |
Ножовочные |
||||||||
Разные |
9 |
Муфто- и трубообра- батывающие |
Пило- насекальные |
Правильно- и безцентрово- обдирочные |
Балансировочные |
Для испыта- ния инструментов |
Делитель- ные машины |
Балансиро- вочные |
- |
- |
Г руппа 1. Токарные и токарно-винторезные станки
1М63
1А616
1К62
ИЖ250ИТВМ ГС526У
Основные технические характеристики 1к62
токарно-винторезный (3 варианта)- 2003г., 1966г., 1983г.
Станок является универсальным. Он предназначен для выполнения разнообразных токар-ных работ: для нарезания метрической, дюймовой, модульной, питчевой, правой и левой, с нормальным и увеличенным шагом, одно- и многозаходной резьбы, для нарезания торцовой резьбы. Станок применяется в условиях индивидуального и мелкосерийного производства.
|
1К62/1000 |
1К62/1500 |
||
Наибольший диаметр обрабатываемой заготовки, мм |
над станиной |
435 |
435 |
|
над суппортом |
224 |
224 |
||
Наибольшая длина обрабатываемой заготовки, мм |
1000 |
1500 |
||
Размер внутреннего конуса в шпинделе |
Морзе 6 |
Морзе 6 |
||
Диаметр цилиндрического отверстия в шпинделе |
55 |
55 |
||
Число ступеней частот вращения шпинделя |
23 |
23 |
||
Частота вращения шпинделя, мин-1 |
12,5...2000 |
12,5...2000 |
||
Число ступеней рабочих подач |
продольных |
42 |
42 |
|
поперечных |
42 |
42 |
||
Рабочие подачи, мм/об |
продольные |
0,70...4,16 |
0,70...4,16 |
|
поперечные |
0,035...2,08 |
0,035...2,08 |
||
Число нарезаемых резьб |
метрических |
45 |
45 |
|
дюймовых |
28 |
28 |
||
модульных |
38 |
38 |
||
питчевых |
37 |
37 |
||
архимедовой спирали |
5 |
5 |
||
Шаг нарезаемой резьбы |
метрической, мм |
0,5...192 |
0,5...192 |
|
модульной, модулей |
0,5...48 |
0,5...48 |
||
дюймовой, ниток на дюйм |
24...15/8 |
24...15/8 |
||
питчевой, питч |
96...1 |
96...1 |
||
Быстрые установочные перемещения суппорта, м/мин |
продольного |
4,5 |
4,5 |
|
поперечного |
2,25 |
2,25 |
||
Размер внутреннего конуса в задней бабке |
Морзе 5 |
Морзе 5 |
||
Наибольшее перемещение пиноли задней бабки, мм |
200 |
200 |
||
Поперечное смещение корпуса задней бабки, мм |
±15 |
±15 |
||
Наибольшее сечение резца |
25 |
25 |
||
Давление воздуха, МПа |
0,4...0,6 |
0,4...0,6 |
||
Питание от электросети напряжением |
220/380 В (50Гц) |
220/380 В (50Гц) |
||
Мощность электродвигателя главного привода, кВт |
11 |
11 |
||
Габаритные размеры станка, мм |
длина |
2786 |
3286 |
|
ширина |
1200 |
1200 |
||
высота |
1500 |
1500 |
||
Масса станка, кг |
3080 |
3440 |
Токарные автоматы, п/автоматы. Станки токарной группы, работающие в автоматическом и полуавтоматическом режимах, предназначаются для обработки разнообразных поверхностей тел вращения из штучных или прутковых заготовок. Здесь широко используются высокоэффективные технологические способы обработки элементарных поверхностей: обработка широкими резцами с поперечной подачей, обтачивание фасонными резцами наружных и внутренних поверхностей, применение резьбонарезных головок и т. д. Одношпиндельные автоматы и полуавтоматы относят к первому типу, а многошпиндельные — ко второму типу станков первой (токарной) группы, что находит отражение в обозначении моделей этих станков: 1112, 1Б125, 1Д118, ПОЗА, 1Ш6П, 1А225-6, 1К282, 1А240П-8, 1265М-8, 1283 и т. п. При изготовлении любых одинаковых деталей на данном станках должен быть выделен так называемый рабочий цикл, т. е. периодическая повторяемость отдельных действий и движений. За время рабочего цикла автомат или полуавтомат обрабатывает одну деталь.
Многорезцовые полуавтоматы (мод. 1А730 и 1А720) по компоновке соответствуют обычным токарным станкам, но отличаются наличием двух суппортов: переднего или продольного и заднего или поперечного. Они предназначены для токарных работ при установке заготовки в центрах; или патроне. На них обрабатываются цилиндрические и торцовые поверхности несколькими резцами в каждом суппорте. Их рационально используют в массовом и крупносерийном производстве для обработки многоступенчатых валов, поршней, шкивов, блоков зубчатых колес и других деталей. Настройка частоты вращения шпинделя и подач суппортов осуществляется с помощью специальных колес. Жесткая конструкция станка позволяет вести многорезцовую обработку инструментами с твердосплавным лезвием. Копировальные полуавтоматы (мод. 1712, 1722) позволяют вести обработку при меньших мощностях привода, так как основной профиль обрабатывается всего одним-двумя резцами. Полуавтомат имеет гидравлический привод для перемещения суппортов и зажима заготовки, а также гидрокопировальное устройство для воспроизведения профиля детали по копиру. Кроме копироваль-ного верхнего суппорта, имеется один-два нижних поперечных суппорта для прорезания канавок и подрезки торцов.
Т окарные автоматы, п/автоматы
Токарный многошпиндельный автомат Токарный многошпиндельный автомат
1Б216-6К 1Б240-6К, 1Б240-8К
Токарный двухшпиндельный вертикальный Одношпиндельный токарный станок с ЧПУ с
станок c ЧПУ ПАБ-350/600 автоматической загрузкой- выгрузкой ПАБ-133
Токарно-револьверные. Они предназначены для токарной обработки в серийном производстве деталей сложной конфигурации различными инструментами, большая часть которых закреплена в револьверной головке. Токарно-револьверные станки делятся на прутковые и патронные. На этих станках можно выполнять почти все основные токарные операции. Применение этих станков считается рациональным в том случае, если по технологическому процессу обработки детали требуется последовательное применение различных режущих инструментов: резцов, свёрл, развёрток, метчиков и т.д. Инструменты в необходимой последовательности крепят в соответствующих позициях револьверной головки и резцедержателях поперечных суппортов. Ходовой винт револьверным станкам не требуется, т.к. резьба на них нарезается только метчиками или плашками. В токарно-револьверных станках частота вращения и подача переключаются в основном с помощью командоаппаратов. Основными размерами, характеризующими прутковые револьверные станки, являются наибольший диаметр обрабатываемой в патроне детали над станиной и над суппортом. К основным размерам относятся, и максимальное расстояние от переднего конца шпинделя до передней грани или торца револьверной головки и наибольшее перемещение головки.
Патронные токарно-револьверные станки выпускают с наибольшим диаметром обрабатываемой детали от 160 до 630 мм.
Токарно-револьверный 1Д325 Токарный центр с 2 шпинделями и 1
револьверной головкой BHA-34S/42S
Токарно-карусельные. Основными размерами карусельных станков является наибольший диаметр и наибольшая высота заготовки. Карусельные станки имеют максимальный диаметр обработки от 800 до 2500 мм. Станки с диаметром обработки до 1600 мм изготавливают одностоечными, а больших типоразмеров – двухстоечными. Первые имеют на траверсе один вертикальный суппорт с револьверной головкой и один горизонтальный суппорт на стойке. У вторых на траверсе два вертикальных суппорта и один или два боковых, горизонтальных - на стойках.
Главное движение резания создаётся вращением планшайбы. Каждый из суппортов имеет вертикальную и горизонтальную подачу, а также быстрое перемещение в этих же направлениях. Траверса имеет установочное вертикальное перемещение с автоматическим закреплением на направляющих.
1512, 1516, 1525, 1540, 1541, 1550, 1553, 1563, 1325Ф30-01, 1512Ф1, 1512Ф2, 1512Ф3
1516Ф1, 1516Ф2, 1516Ф3, 1520Ф2, 1525Ф1, 1525Ф2, 1531м, 1532Т, 1540П. 1540Т
1540Ф1, 1550П, 1550Т, 1563Ф1, 1А512МФ3, 1А516МФ3, 1Е512Ф2И, 1Е512ПФ2И
1Е516Ф2И, 1Е516ПФ2И, 1Л532, 1Л532Ф1, 1Л532Ф2, 1М557, DKZ-2000-2500, SC14
SC17, SC22-27-33-43, SC2500, SC25А, SC25B, К488, КС475, КУ101, КУ107, КУ477
КУ478, КУ488, КУ-50, КУ501Ф1, КУ507Ф1, КУ514Ф1, КУ518Ф1, КУ563Ф1
КУ564Ф1, КУ565Ф1, КУ580ЛФ1, КУ-63, КУ63Ф1, КУ-64, КУ-65, КУ-80Л.
Группа 2. Сверлильные станки ТЕМА 6
Сверлильные станки предназначены для получения сквозных или глухих отверстий в призматических деталях, для чистовой обработки отверстий зенкерованием и развёртыванием, для нарезания внутренних резьб метчиками, для зенкования торцовых поверхностей и отверстий.
Существуют следующие типы универсальных сверлильных станков:
1. Настольно-сверлильные; 2. Вертикально-сверлильные (одношпиндельные);
3. Радиально-сверлильные; 4. Многошпиндельные 5. Для глубокого сверления.
Основным характерным размером сверлильных станков является наибольший диаметр сверления в стали средней твёрдости.
Рис 6.1 Настольно–сверлиль-ный станок ГС 2112
астольно-сверлильные. Настольно-сверлильные станки – самого малого ипоразмера среди сверлильных станков. Они устанавливаются на столе и предназначены для обработки отверстий в мелких и средних деталях. Позволяют сверлить, рассверливать, зенкеровать и зенковать, развертывать отверстия диаметром до 10-18 мм, нарезать метрическую резьбу метчиками в изделиях из черных и цветных металлов, неметаллических материалов. Частота вращения шпинделя в них регулируется перекидыванием ремня на 3-5-ступенчатых шкивах. Эти станки эффективно используется в условиях промышленных предприятий, ремонтных мастерских и в бытовых условиях в индивидуальном, мелкосерийном, иногда в крупносерийном производствах.
Технические характеристики настольно-сверлильного станка ГС2112
Наибольший условный диаметр сверления в стали 45 ГОСТ 1050-88, мм
12
Вылет шпинделя (расст/. от оси шпинделя до образующей колонны), мм
190
Расстояние от нижнего торца шпинделя до рабочей поверхности плиты, мм:
наибольшее, не менее
450
наименьшее, не более
100
Наибольший ход шпиндельной головки, мм
250
наибольший ход шпинделя, мм
100
Размер конуса шпинделя наружный по ГОСТ 9953-82
В18
Цена деления лимба, мм
1
Число скоростей шпинделя
5
Предел чисел оборотов шпинделя, об/мин.
450; 800; 1400; 2500; 4500
Габаритные размеры станка (LxBxH), мм, не более
780x420х982
Масса станка (нетто брутто), кг, не более
100/150
Характеристика электродвигателя: номинальная мощность, кВт
0,55
частота вращения, об/мин.
1500
напряжение, В
380
Габаритные размеры упаковки (LxBxH), мм
900x595x1130
Рис. 6.2 Станок настольно-
сверлильный СНВШ-2
Рис 6.3 Станок настольно-сверлильный 2М112
Рис. 6.4 Станок настольно- Рис.6.5 Станок настольно-сверлильный DMIF-25/400
сверлильный НС-16
2 Вертикально-сверлильные (одношпиндельные). В вертикально-сверлильных станках главным движением v является вращение шпинделя с закрепленным в нем инструментом, а движением подачи Sx — вертикальное перемещение шпин-деля. Обрабатываемую заготовку устанавливают на столе или непосредственно на фундаментной плите, причем соосность отверстия заготовки и шпинделя достига-ется перемещением заготовки. Основными узлами вертикально-сверлильного станка являются станина (стойка, колонна), фундаментная плита, коробка скорос-тей, шпиндель, коробка подач и механизм подачи, стол.
Модели: 2А135, 2Н135, 2Н125, KST-340, KSD-32, KST-560, GHD-22, 2C125, 2С125-04, GHD-27, GHD-27, GHD-46PF, GHD-27PF, МН25 Н-01, GHD-50PF, 2С50, 2С132, 2Т140, 2С132Л, CC700M.
Техническая характеристика 2А135
Наибольший диаметр сверления в мм
35
Наибольший ход шпинделя в мм
225
Вылет шпинделя в мм
300
Наибольшее расстояние от торца шпинделя до стола в мм
750
Конус шпинделя
Морзе 4
Наибольшее установочное пере-мещение шпиндельной бабки в мм
200
Рабочие размеры стола (ширина X длина) в мм
450X500
Наибольшее вертикальное перемещение стола в мм
325
Число скоростей шпинделя
9
Пределы чисел оборотов шпинделя в минуту
68—1100
Число подач
11
Пределы подач шпинделя в мм/об
0,115—1,6
Наибольшее усилие подачи в кг
1600
Мощность главного электродвигателя в квт
4,5
Габариты станка (длина X ширина X высота) в мм
810Х1240Х2500
Вес станка в кг
1300
3. Радиально-сверлильные. Предназначены для многоинструментальной обработки отверстий в заготовках крупных деталей при единичном и серийном производстве. В отличие от вертикально-сверлильных в радиально-сверлильных станках совмещение оси отверстия заготовки с осью шпинделя достигается перемещением шпинделя (в полярных координатах) относительно неподвижной заготовки. Компоновка радиально сверлильного позволяет установить шпиндель с инструментом в любой точке рабочей зоны радиального станка за счет перемещения шпиндельной головки (бабки) по направляющим траверсы (рукава) и поворота траверсы вокруг колонны. Главным движением в радиально-сверлильных станках является вращение шпинделя, а движением подачи s — осевое перемещение шпинделя вместе с пинолью (гильзой). К вспомогательным движениям радиально сверлильных станков относятся: поворот траверсы и закрепление ее на колонне, вертикальное перемещение и закрепление траверсы на нужной высоте, перемещение и закрепление шпиндель-ной головки на траверсе, переключение скоростей и подач шпинделя и т. д. Основными узлами радиально-сверлильных станков являются: колонна, фундаментная плита, траверса (рукав), механизм перемещения и зажима рукава, шпиндельная головка.
Модели: ГС544, 2М55, JRD-1600R, 2А554, 2А576, 2А587 , JRD-720R,
JRD-920R, 2К522, Z3040x12, Z3050x16, ГС545, JRD-1100R, SRB-50,
JRD-1230H, 2К550.
Т
ехническая характеристика станка 2М.
Наибольший диаметр сверления в стали средней твердости, мм
50
Вылет шпинделя (расстояние от оси шпинделя до образующей колонны), мм.
450 - 1500
Расстояние от нижнего торца шпинделя до плиты, мм.
470 - 1500
Наибольшее вертикальное перемещение рукава по колонне,
680
Наибол. осевое перемещение шпинделя, мм.
350
Конус шпинделя
Морзе 5
Количество скоростей вращения шпинделя
19
Пределы чисел оборотов в минуту
30 - 1700
Мощность электродвигателя привода шпинделя, кВт.
4,5
Мощность электродвигателя перемещения рукава, кВт.
1,7
Габариты, мм
2625 х 968 х 3265
Масса, кг
4100
Многошпиндельные сверлильные станки. Применяют в серийном производ-стве для обработки Изделий, в которых требуется одновременно просверлить, развернуть, нарезать резьбу в большом количестве отверстий на разных плоскостях изделия. Каждый шпиндель получает вращение от отдельного электродвигателя.
а) б)
Рисунок 6.6 Многошпиндельные станки ф. ERLO, а) - модель BV-70/CM,
б) - TRV-18/CM.
5
. Специализированные. Для глубокого сверления. Станки для глубокого сверления предназначены для сверления глубоких отверстий в сплошном материале и растачивания глубоких или сквозных отверстий в валах, распределительных валиках, колоннах гидропрессов, когда глубина сверления или растачивания в 10 и более раз превосходит их диаметр. В связи с тем, что условия обработки глубоких отверстий очень разнообразны, на производстве встречается большое количество типов этих станков. вращение подаётся на сверло или на деталь или на то и другое одновременно.
Инструментом являются пушечное или ружейное свёрла. Стружка непрерывно вымывается СОЖ, подаваемой через центральное отверстие сверла под давлением в 5-20 кг/см2.
Станки могут быть одно- и двухсто-
Рисунок 6.8. Свёрла глубокого сверления: ронними,т.е. предназначенными для
а) –пушечное; б)- ружейное; в)- шнековое; обработки отверстий с одной или двух
г)-четырёхленточное. сторон одновременно.
Рисунок 6.8 Станок для глубокого сверления РТ – 602
Рисунок 6.9 Станок для глубокого сверления AF 15X2
-
Рисунок 6.10 Глубокое сверление головок блоков цилиндров, блоков двигателей и матриц
штампов.
Группа 2. Расточные станки
Расточные станки – предназначены для растачивания, сверления, зенкеро-вания, нарезания внутренней и наружной резьбы, обтачивания цилиндрических поверхностей, подрезки торцов, цилиндрического и торцового фрезерования крупноразмерных металлических заготовок. Станок имеет неподвижную перед-нюю стойку, установленную на основании. На направляющих стойки может перемещаться вверх-вниз шпиндельная бабка с расточным шпинделем и план-шайбой . На направляющих основания расположены салазки, а на них стол, который может перемещаться в продольном и поперечном направлениях относительно оси шпинделя и совершать круговое движение. Управление станком осуществляется с пульта. Координаты перемещения шпиндельной бабки, люнета, задней стойки и стола отсчитываются по лимбам или с помощью навесных оптических устройств (с точностью до 0,01 мм). Подразделяются на 1. горизон- тально-расточные; 2. координатно-расточные; 3. алмазно-расточные (отделочно-расточные); 4. станки для глубокой расточки.
1. Горизонтально-расточные. В горизонтально-расточных станках основной размер – диаметр шпинделя. Главное движение резания – вращение шпинделя или вращение планшайбы. К подачам кроме движения стола и бабки относятся ещё осевое движение шпинделя и радиальное движение резцового суппорта на планшайбе. На этих станках могут выполнятся следующие работы:
1. сверление; 2. растачивание отверстий; 3. подрезка торцов; 4. нарезание резьбы; 5. фрезерование плоскости.
Некоторые модели: 2614, 2615, 2620А, 2620В (2А620), 2622В (2А622), 2637Г, 2652, 2657, 2А614, 2А636, 2А637, 2А656 РФ11, ТХ 611В, ТХК 160, РС 2620ВФ1, ТРХ6111 В/2, ТРХ 6113 В/2.
Рисунок 6.11 Горизонтально-расточный станок 2620А
Рисунок 6.12 Эскиз общего вида станка 2620А.
Рисунок 6.13 Кинематическая схема станка 2620А (а) и сетка для
построения графика частот вращения шпинделя (б).
2. Координатно-расточные станки (КРС). В координатно-расточных станках основной размер – ширина стола. Эти станки предназначены для обработки точных отверстий при допуске на расстояние между их осями порядка 5…10 мкм. Бывают одностоечные и двухстоечные КРС, Рис.6.14
а) б)
Рисунок 6.14 Одностоечные (а) и двухстоечные (б) координатно-расточные станки
Главным движением является вращение шпинделя, а движением подачи — вертикальное перемещение шпинделя. Установочные движения в одностоечных станках — это продольное и поперечное перемещение стола на заданные координаты и вертикальное перемещение шпиндельной бабки в зависимости от высоты детали. В двухстоечных станках — это продольное перемещение стола, поперечное перемещение шпиндельной бабки по траверсе и вертикальное перемещение траверсы со шпиндельной бабкой. Станки снабжены универсальными поворотными столами, дающими возможность обрабатывать отверстия в полярной системе координат и наклонные отверстия. Для точного измерения координатных перемещений станки снабжены различными индуктивными, механическими, оптико-механическими и электронными устройствами отсчета, которые позволяют измерять перемещения подвижных узлов с высокой точностью.
Координатно-расточной станок мод. 2А450, например, имеет размеры стола 630×1100, одностоечный. Электродвигатель Д1 имеет бесступенчатое регу-лирование.
Подача шпинделя также регулируется бесступенчато с помощью механи-ческого вариатора с раздвижными коническими шкивами и стальным кольцом. Бесступенчатое регулирование скоростей и подач позволяет на ходу вывести станок из резонанса, обеспечив тем самым малую шероховатость обрабатываемой поверхности. К станку прилагается накладной, поворотный в двух плоскостях стол.
Некоторые модели КРС: 2418, 2421, 2431, 2455АФ1, 2А450, 2Е460А, 2Д450, 2Л450А, 2Е440А, ВКоЕ 630х1000, 2А470, BFT 90/3-1.
Рисунок 6.15 Координатно-расточной станок 2Е440А.
Техническая характеристика 2Е440А
-
Класс точности
А
Длина рабочей поверхности стола, мм
710
Ширина стола, мм
400
Диаметр, мм - сверления - растачивания
25 250
Мощность главного привода, кВт
4,5
Пределы частот вращения шпинделя, об/мин
50..2000
Габариты станка, мм
- длина
2440
- ширина
2195
- высота
2430
Вес станка, кг
3500
3. Отделочно-расточные станки. Алмазно-расточные станки подразделяются на вертикальные, горизонтальные, одношпиндельные, многошпиндельные, односторонние и двусторонние. В качестве инструмента на этих станках применяются алмазные и твердосплавные резцы. Режим тонкого растачивания: скорость резания до 1000 м/мин, подача 0,01—-0,1 мм/об и глубина резания 0,05—0,55 мм. Высокая точность обработки отверстий, отклонение по диаметру 0,003—0,005 мм и шероховатость поверхности 8—9-го класса на алмазно-расточных станках обеспечиваются благодаря применению малых подач и высоких скоростей резания. На алмазно-расточных станках, кроме чистовой обработки отверстий, выполняется наружное обтачивание, растачивание и обтачивание конусов, подрезание торцов и растачивание канавок. Основными потребителями алмазно-расточных станков являются заводы крупносерийного и массового производства автомобильной, тракторной и авиационной промышленности.
К числу деталей, для обработки которых применяются алмазно-расточные станки, относятся шатуны, втулки, вкладыши, гильзы, головки блока и блоки цилиндров.
А
Б
Рисунок 6.16 Отделочно - расточные станки:
А- вертикальный 2Е78П;
Б – вертикальный 2А776В;
В - горизонтальный СТАН-САМАРА.
В
4. Cтанки для глубокой расточки. Мало отличаются от станков для глубокого сверления, только работают расточными головками разной конструкции, рис.6.18.
Рисунок 6.17. Станок глубокой расточки SIG B16-1500 KT, Швейцария.
Рисунок 6.18.Универсальные расточные головки Vhu, ф. Narex, Чехия.Рисунок 6.18.
Карусельный двухстоечный 1540 Карусельный одностоечный 1512
Техническая характеристика одностоечных карусельных станков
Технические данные станков |
1512, 1512Ф1 |
1516, 1516Ф1 |
|
|
Максимальный диаметр обрабатываемой детали, мм |
1250 |
1600 |
|
|
Максимальная высота обрабатываемой детали, мм |
1000 |
|||
Наибольшая масса обрабатываемой заготовки,кг |
6000 |
8000 |
|
|
Диаметр планшайбы, мм |
1120 |
1400 |
|
|
Диапазон частот вращения планшайбы, об/мин |
1.25-250 |
1.00-200 |
|
|
Диапазон рабочих подач, мм/об |
0.02-10 |
|
||
Мощность двигателя главного привода, кВт |
30 |
|
||
Нарезание резьб и обработка конических поверхностей |
По заказу |
|
||
Обработка криволинейных поверхностей по копиру |
По заказу |
|
||
Самоцентрирующая планшайба |
По заказу |
|
||
Устройство подачи СОЖ |
По заказу |
|
||
Габариты ( LxBxH ), мм |
2920x2705x4100 |
3170x3025x4100 |
|
|
Масса станка,кг |
14800 |
18100 |
|
Л
оботокарные
станки.
Предназначены для токарной обработки
тяжёлых деталей большого диаметра, но
небольшой длины. Передняя бабка
лоботокарных станков монтируется на
одной станине с суппортом, а у более
крупных станков – на отдельном фундаменте.
Заготовка крепится на планшайбе или в
четырёх
кулачковом патроне.
Рис… Станок лоботокарный 1М693
Группа 6. Фрезерные станки ТЕМА7
На фрезерных станках обрабатываются плоскости, фасонные поверхности, канавки, нарезаются наружные и внутренние резьбы, зубчатые колёса и многолезвийные инструменты с прямыми и винтовыми зубьями (фрезы, развёртки и др.)
Фрезерные станки общего назначения различают по компоновке:
1. Консольные (с консольным столом), в том числе а) вертикальные;
б) горизонтальные; в) широкоуниверсальные.
2. Бесконсольные (или иначе с крестовым столом). Они чаще вертикальные, но есть и горизонтальные.
3. Продольно-фрезерные (ПФС). Они бывают одностоечные и двухстоечные.
Специализированные (например, карусельно-фрезерные).
Основным размером фрезерных станков являются ширина стола, которая у консольных станков бывает от 100 до 500 мм; у бесконсольных – от 320 до 1000 мм, у ПФС – от 320 до 5000 мм.
Главное движение резания у всех фрезерных станков – вращение фрезы. Характерной особенностью фрезерных станков является независимость подач от главного движения резания. Размерность подач – мм/мин.
Рисунок 7.1. Основные типы фрез: а – цилиндрическая; б – дисковая; в – концевая;
г – торцовые; д – фасонная.
У консольных фрезерных станков стол имеет продольную и поперечную подачи и вместе с консолью перемещается вертикально по направляющим стойки. У бесконсольных станков стол также имеет продольную и поперечную подачи, но расположен на станине, а вертикальное перемещение передано шпиндельной бабке.
У продольно-фрезерных станков столу с тяжёлыми заготовками оставлено только продольное перемещение, а остальные движения подач переданы фрезерным бабкам, т.к. заготовки на этих станках имеют вес от нескольких тонн, до нескольких сотен тонн.
Вертикально-фрезерные консольные станки - предназначены для выполнения широкого круга фрезерных работ, выполняемых торцовыми, концевыми и другими фрезами, которые крепятся в цанговых патронах и на оправках.
Отличительной приметой этих станков является вертикальное расположение шпинделя и наличие консоли. Станки позволяют использовать режущие свойства быстрорежущего и твердосплавного инструмента. Заготовки устанавливаются на прямоугольные столы размером от 200 х 800 до 630 х 1600 мм или круглый накладной стол диаметром 320 мм и более.
Имеют идентичные органы управления, относительно мало отличающиеся друг от друга, рис. 7.2, а, б.
Рис. 7.2
шпиндель»; 23 – кнопка «Быстрый ход стол»; 24 – ручное медленное перемещение стола; 25 – зажим стола; 26 – место установки путевых
кулачков; 27 – ручное перемещение гильзы шпинделя; 28 – квадрат поворота фрезерной головки; 30 – зажим консоли на станине; 31 – переключатель автоматического управления и механической подачи круглого поворотного стола (съёмная принадлежность станка); 32 и 33 – зажимы головки.
Некоторые модели вертикально-фрезерных станков: 6102А, 6103, 6104, 6Н11, 6Т12 (6Р12, рис.7.3,а), 6Д10, 6С12Ц, 6К11, 6К12, 6М12ПБ, 6Т10, 6Т13, 6Н14, FSS350MR (FSS315MR), FSS450MR, FV-251M, FV-301(рис. 7.3, б), FV-401, JTM-1050TS, XW 5032B, ВМ - 127, ГФ3571.
а) б)
Рисунок 7.3. Вертикально фрезерные консольные станки а) – 6Р12; б) – FV 301.
Харака ТЕХНИЧЕСКИЕ ХАРАКТЕРИСТИКИ, ВЕРТИКАЛЬНО - КОНСОЛЬНО - ФРЕЗЕРНЫЙ СТАНОК 6Р12 |
|
Размеры стола, мм |
320х1250 |
Перемещение стола, мм - продольное (X) - поперечное (Y) - вертикальное (Z) |
800 320 420 |
Угол поворота шпиндельной головки в продольной плоскости, град |
± 45 |
Частота вращения основного шпинделя, об/мин |
31,5...1600 |
Конус основного шпинделя |
50 |
Подача стола, мм/мин: - продольная (X) - поперечная (Y) - вертикальная (Z) |
12,5...1600 12,5...1600 4,1...430 |
Быстрый ход, мм/мин: - продольный (X) 4000 - поперечный (Y) 4000 - вертикальный (Z) 1330 |
4000 4000 1330 |
Мощность основного шпинделя, кВт |
7,5 |
Габариты станка, мм |
2280х1965х2265 |
Масса станка, кг |
3250 |
Бесконсольные вертикально-фрезерные станки. Отличительными особенностями конструкций станков этого типа являются: отсутствие консоли, более жесткие станина и стойка, повышенная мощность, червячно-реечный привод (Рис. 7.4). Фрезерование производится главным образом торцовыми головками, а также торцовыми, цилиндрическими и фасонными фрезами. Повышенная мощность и жесткость, а также высокие числа оборотов шпинделя позволяют производить на этих станках скоростное фрезерование торцовыми головками с пластинками твердых сплавов. Продольные и поперечные подачи стола осуществляются отдельными электродвигателями постоянного тока с бесступенчатым регулированием чисел оборотов. Бесступенчатое регулирование подачи в широком диапазоне позволяет производить выбор оптимальной минутной подачи при фрезеровании.
Т а б л и ц а 2. Основные характеристики бесконсольных вертикально-фрезерных станков.
Рисунок 7.4 Бесконсольный вертикально-фрезерный (с крестовым столом)
станок DEKA ХА7140.
Станки непрерывного фрезерования бывают карусельно-фрезерные, у которых стол с заготовками (карусель) поворачивается относительно вертикальной оси, и барабанно-фрезерные, с горизонтальной осью поворота барабана (стола) также при круговой подаче. Станки применяют в условиях серийного и массового производства, при этом часто загрузка-выгрузка заготовок на карусель или барабан осуществляется на ходу, без их остановки. Отдельные станки имеют больше одного шпинделя. Коробка скоростей таких станков зачастую включает сменные колеса, которые подбираются для обработки конкретной заготовки, но есть и с обычные коробки скоростей.
Модели карусельно-фрезерных станков: 6210, 6А21, 6А23 (Рис.7.5,а), 6М23, 6М23В, 621М, ГФ-261М, ГФ-3210, ГФ-3223, 6М23С13, КС630, КС631, УФ-0946.
;
Рис. 7.5. Карусельно-фрезерные станки:
а) – 6А23;
б) - УФ5144.
а) б)
Модели барабанно-фрезерных станков: 6021, 6022, 6023, ГФ-428, ГФ-699.
Рисунок 7.6. Компоновка барабанно-фрезерного станка. |
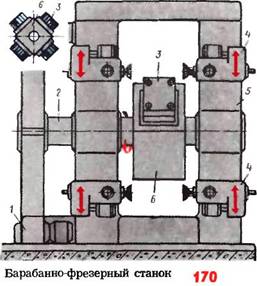
Барабанно-фрезерные станки (Рис.7.6) служат для обработки параллельных плоскостей заготовок одновременно с двух сторон. Заготовки, подлежащие обработке, устанавливают на барабан, который вращается внутри станины, имеющей портальную форму. Фрезы помещены на расположенных с двух сторон одношпиндельных или двухшпиндель-ных бабках, с каждой стороны по две. Одна бабка с каждой стороны служит для чернового фрезерования, другая - для чистового.
Копировально-фрезерные станки выполняются универсальными и специализи-рованными, для обработки конкретной детали (шинных пресс-форм, профиля плоских шаблонов, лонжеронов, лопаток турбин и т. п.). Универсальные копировальные станки позволяют делать гравировку или изготовлять штампы, матрицы, пресс-формы и другие детали с рельефными поверхностями и контурами. Собственно копирование осуществляется по разметке с ручным управлением, по плоскому шаблону, по объемной модели (из гипса, дерева, металла), по программе, записанной на магнитной пленке, или по копиру. Станки этого типа работают специальными или обычными стандартными фрезами.
Модели копировальных станков: 6464, 6Л463, 6А426, 6М42К, 6441Пр, TM-4С414, R600 (Рис.7.7), 6А463.
Рисунок 7.7. Копировально-фрезер-ный станок R 600 фирмы HIGH POINT INC, США. |
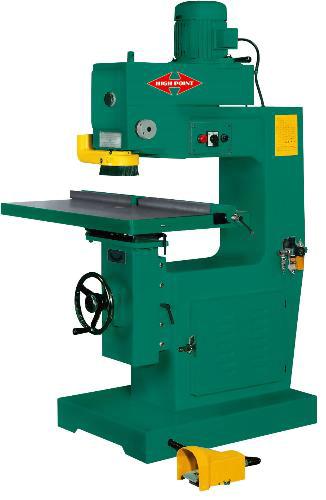
На копировально-фрезерном станке R 600 можно выполнять такие работы, как фрезерование внутри контура щитовых деталей различных фигурных пазов. Кроме того на копировально-фрезерном станке R 600, можно вырезать фигурные детали с высоким качеством поверхности реза.
Технология обработки деталей на копировально-фрезерном станке: снизу к заготовке крепится шаблон, затем конструкция укладывается на рабочий стол и край шаблона упирается в установленный на столе копир. После нажатия на педаль, сверху на заготовку опускается фреза на установленную глубину, заготовка с шаблоном перемещается относительно копира и на поверхности заготовки получается соответствующий фигурный контур. Высокая частота вращения фрезы (до 20 тыс. об/мин) копировально-фрезерного станка позволяет получать идеальное качество поверхности не требующее последующего шлифования.
Рисунок 7.8. Станок гравировальный копи-ро вально-фрезерный с пантографом 6Л463. |
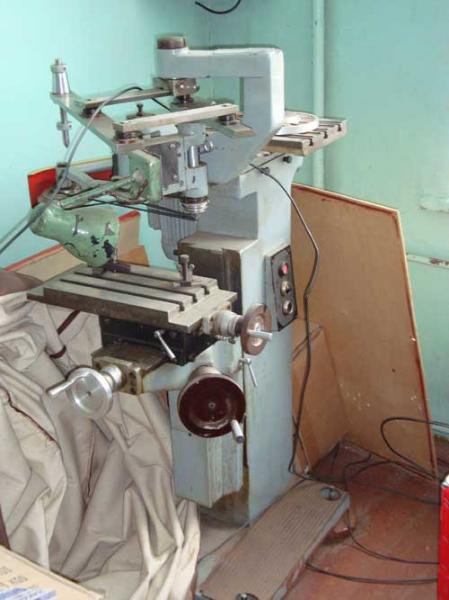
Н - класс точности станка по ГОСТ 8-82, (Н, П, В, А, С) 320 - длина рабочей поверхности стола, мм 200 - ширина стола, мм Наибольшее перемещение по осям, мм: 200- X 125- Y 250- Z 1260 15900 - пределы частоты вращения шпинделя, Min/Max, об/мин 0,27- мощность двигателя гл. движения, кВт Габаритные размеры станка, мм: 1100 - длина 1000 - ширина 1260 - высота 250 - масса станка с выносным оборуд., кг
П
родольно-фрезерные
станки.
Одностоечные и двухстоечные (портальные),
с одним или несколькими шпинделями
позволяют фрезеровать вертикальные,
горизонтальные и наклонные плоскости,
пазы и т. п. на самых длинных и крупных
заготовках (массой до 30 т) или группы
заготовок одновременно в условиях
серийного производства с применением
быстрорежущих и твердосплавных
цилиндрических, торцовых, концевых,
дисковых, угловых и фасонных фрез.
Рисунок 7.9. Угловая фреза.
Некоторые станки позволяют вести встречное и попутное фрезерование, а также фрезерование по полуавтоматическому циклу: подвод фрезы — фрезерование — останов — разгрузка — возврат фрезы в исходное положение — загрузка и т. д. Оптимальные режимы фрезерования устанавливаются путем бесступенчатого регулирования частоты вращения шпинделя и величины подачи. Значительные припуски обрабатываемых заготовок приводят к образованию стружки, которая отводится вибротранспортером. Одной из главных характеристик станков этого видаявляется площадь стола; у серийных станков она определяется габаритами от 400 х 1250 мм (мод. 6304 одностоечная) до 2500 х 8000 мм (мод. 6625 двухстоечная). Характеристики станков приведены в Табл. 7.2.
Одностоечные модели (третий тип станков): 6303, 6308, 6310, 6У312 (Рис.7.10).
П
ортальные
модели (шестой тип станков):
6604, 6605, 6606, 6Г608, 6У612 (Рис. 7.12).
Рисунок 7.10 Одностоечный продольно-фрезерный станок 6У312,
Ульяновский завод тяжёлых станков (УЗТС).
Рисунок 7.11 Двухстоечный продольно-фрезерный станок 6625,
Горьковский завод фрезерных станков.
Широкоуниверсальные фрезерные станки могут работать с горизонтальным, наклонным или вертикальным расположением одного или двух шпинделей при обработке средних по величине деталей различной формы цилиндрическими, дисковыми, торцовыми фрезами и набором фрез. Эти станки оснащаются большим набором принадлежностей: угловыми и круглыми столами, тисками, делительными головками и столами, быстроходными головками и т. п. Стол станка имеет размеры от 200 х 500 мм (мод. 675) до 400 х 1600 мм (мод. 6М83Ш).
Модели широкоуниверсальных станков (седьмой тип): 675, 675П, 676П, 6А73В, СФ-676, 6М76П-1, ДФ6725, 6725ПМ.
Станок СФ-676 позволяет выполнять следующие операции: фрезерование, сверление, развёр-тывание, растачивание, зенкерование, долбёжка. Обработка плоскостей производится дисковыми, торцевыми, концевыми угловыми и фасонными фрезами.
Фрезерные станок модели ФСМ 250/676М, предназначен для обработки деталей из черных и цветных металлов и их сплавов фрезерованием, сверлением, развертыванием, зенкерованием и растачиванием под различными углами к плоскости стола в производственных условиях.
|
|
|
СФ - 676
|
ФСМ 250/676М |
6М76П-1 |
Рисунок 7.14 Модели «семёрочных» широкоуниверсальных станков. |
Горизонтально-фрезерные консольные станки отличаются наличием консоли и горизонтальным расположением шпинделя при обработке цилиндрическими, угловыми и фасонными фрезами плоских и фасонных поверхностей заготовок из различных материалов. Могут также использоваться торцовые и концевые фрезы. Универсальные станки этого вида отличаются тем, что их стол может поворачиваться относительно вертикальной оси ±45°, что позволяет вести обработку винтовых канавок на цилиндрических поверхностях с использованием делительной головки. Столы этих станков имеют размер от 160 х 630 мм (мод. 6Н80Г) до 400 х х 1600 мм (мод. 6М83) и имеют продольные Т-образные пазы для установки различных приспособлений. Ширина этих пазов обычно 14—28 мм. Этот размер следует учитывать при подборе или конструировании приспособления.
Рисунок 7.15 Горизонтально-фрезерный станок 6Т83Д. |
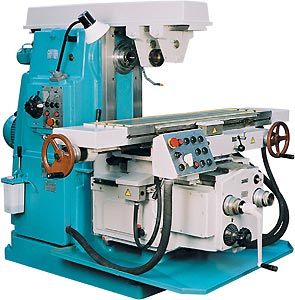
Основные преимущества станка 6Т83Д: Конструктивные:
механизированное крепление инструмента в шпинделе;
устройство периодического регулирования величины зазора в винтовой паре продольной подачи;
предохранительная муфта защиты привода подач от перегрузок;
торможение шпинделя при остановке электромагнитной муфтой. Технологические :
разнообразные автоматические циклы работы станка;
широкий диапазон частот вращения шпинделя и подач стола;
большая мощность приводов;
высокая жесткость;
надежность и долговечность.
К восьмому типу относятся и некоторые модели универсальных (6Т82, 6Т83 и др.) и широко-универсальных горизонтально-фрезерных станков, имеющих в маркировке букву «Ш» (6Т82Ш, 6К81Ш, 6ДМ80Ш, 6ДМ83Ш, FUV-401).
Универсальные фрезерные станки. Технологические возможности универсально фрезерных станков расширены по сравнению с обычными горизонтально-фрезерными за счёт использова-ния вертикальной фрезерной головки, универсальной фрезерной головки, универсального делительного аппарата, круглого делительного стола, долбежной головки, устройства для нарезания гребенок и других приборов и приспособлений.
Широкоуниверсальные фрезерные станки. Предназначены для выполнения всех видов фрезерных работ, сверления, зенкерования и растачивания отверстий на деталях из черных и цветных металлов, их сплавов и пластмасс в условиях единичного, мелкосерийного и серийного производства. В отличие от горизонтально-фрезерных станков широкоуниверсальные имеет еще одну шпиндельную головку, смонтированную на выдвижном хоботе, которую можно поворачивать под любым углом в двух взаимно перпендикулярных плоскостях. Возможна раздельная и одновременная работа обоими шпинделями. Для большей универсальности станка на поворотной головке монтируют накладную фрезерную головку, которая позволяет обработать на станке детали сложной формы не только фрезерованием, но и сверлением, зенкерованием, растачиванием и т. д. В некоторых широкоуниверсальных станках отсутствует консоль, а вместо нее по вертикальным направляющим станины. перемещается каретка. Каретка имеет горизонтальные направляющие для салазок с вертикальной рабочей поверхностью и Т-образными пазами, на которых крепят стол, делительные и другие приспособления. Широкая универсальность станка позволяет использовать его в экспериментальных и инструментальных цехах для производства кондукторов, зажимных приспособлений всех типов, инструментов, штампов, пресс-форм и других деталей.
Рисунок 7.16 Современный широкоуниверсальный фрезерный станок OMM64S.
Разные фрезерные. Разные станки фрезерной группы включают металлорежущее оборудование, предназначенное для обработки конкретных заготовок или видов поверхностей: резьбофрезерные, шпоночно-фрезерные, шлицефрезерные, а также станки для обработки шлицев корончатых гаек, канавок спиральных и центровочных сверл, канавок шпоночных и дисковых фрез, плоскостей слитков и т. д.
- резьбофрезерные станки:
а) б)
Рисунок 7.17 - а) - резьбофрезерный станок 5Д63; б) – резьбовая гребёнчатая насадная фреза.
- шпоночно-фрезерные станки:
а) б)
Рисунок 7.18 – а)- шпоночно-фрезерный станок 692М; б) – набор шпоночных фрез.
- шлицефрезерные станки:
а) б)
Рисунок 7.19 – а)- шлицефрезерный полуавтомат 5350; б) – нарезание шлиц червячной
фрезой на шлицефрезерном станке.
- настольные фрезерные станки. Модели настольных станков: FPX-25Е, FP-48SP, ВМД-16В, ВМД-25В, JMD-15, JMD-2, JMD-18, ВМД-30В, OPTI BF20L Vario, JMD-3, JMD-18PF, JMD-45PF, JMD-45PFD.
-
ТЕХНИЧЕСКИЕ ХАРАКТЕРИСТИКИ МАЛОГАБАРИТНГО НАСТОЛЬНОГО ФРЕЗЕРНОГО СТАНКА ВМД-30В
Максимальный диаметр сверления, мм
32
Максимальный диаметр концевой фрезы, мм
20
Максимальный диаметр торцевой фрезы, мм
76
Размер стола, мм
700х210
Поперечное перемещение, мм
220
Продольное перемещение, мм
425
Вертикальное перемещение, мм
370
Конус шпинделя
МТ3
Ход пиноли шпинделя, мм
70
Т-образные пазы, шт х мм
3х12
Частота вращения шпинделя, мм/об
50-3000
Диапазон поворота головки, град
90 в обе стороны
Мощность двигателя 220в, кВт
1,1
Габаритные размеры, мм
710 х 890 х 1120
Вес нетто / брутто, кг
220/250
Рисунок 7.20 Настольный малогабаритный
Фрезерный станок ВМД – 30В.
Группа 3. Шлифовальные и доводочные станки ТЕМА 8
Шлифовальные станки применяются в основном для снижения шероховатости обрабатываемых деталей и получения точных размеров. В большинстве случаев на шлифование детали поступают после предварительной черновой обработки и термических операций, хотя бывают случаи, когда шлифование является единственным методом обработки. Основной инструмент при шлифовании – шлифовальный круг. На шлифовальных станках можно обрабатывать наружные и внутренние цилиндрические, конические и фасонные поверхности и плоскости, разрезать заготовки, шлифовать резьбу и зубья зубчатых колёс, затачивать режущий инструмент и т.д. Шлифовальные станки в зависимости от назначения подразделяются на круглошлифовальные, внутришлифовальные, бесцентровошлифовальные, плоскошлифовальные и специальные.
Главным движением резания во всех шлифовальных станках является вращение шлифовального круга, измеряемое в м/сек. Vшл = 30…40 м/сек, а движение подачи — поступательное перемещение либо вращение заготовки или инструмента. В доводочных станках движение резания может сообщаться и заготовке.
В основу классификации станков этой третьей группы положены следующие признаки:
вид шлифуемой поверхности (наружная или внутренняя, плоская или цилиндрическая);
виды деталей, для обработки которых предназначен станок (вальцы, кулачковые валы, коленчатые валы и т. п.);
конструктивные особенности станков (двухстоечный, бесцентровый, планетарный);
особенности обрабатываемых конструктивных элементов деталей (резьба, шлицы, профили и др.).
К
руглошлифовальные
станки.
Относятся к первому типу станков и
используются для обработки цилиндрических
и конических поверхностей гладких и
ступенчатых заготовок, установленных
на неподвижных центрах. Заготовки перед
шлифованием проходят обработку,
позволяющую получить достаточно точные
их форму и размеры, и для шлифования
оставляется небольшой припуск, обычно
измеряемый десятыми долями миллиметра.
Обработка длинных валов (рис. а). Станок имеет следующие движения: главное движение – вращение шлифовального круга, круговая подача – вращение заготовки. Кроме того, имеется продольная подача заготовки Ппр и поперечная подача шлифовального круга (подача врезания) Пвр.
Станки, работающие методом врезания (б) имеют круговую подачу, подачу на врезание (Пвр), а также осциллирующую подачу, т.е. колебательное осевое движение, которое могут совершать шлифовальная бабка или стол.
Круглошлифовальные станки бывают простые и универсальные, т.е. имеющие поворот оси шпиндельной бабки и бабки изделия для шлифования конусов. Основной размер в них – наибольший диаметр обработки. Он равен 100-1600 мм.
Рисунок 8.1 Устройство круглошлифовального станка: 1- рычаг; 2, 10 – маховик;
3 – передняя бабка; 4 – шлифовальный круг; 5 – шлифовальная бабка; 6 – задняя
бабка; 7 – стол; 8 – станина; 9 – кулачки.
М
одели
круглошлифовальных станков: 3У10, ЗЕ12,
3А130, ЗА141, 3А10П, 3А151, 3У142 ЗА172, 3А423, 3М174
(Рис.8.2), 3С120В, 3С130В, 3У131ВМ, М1420А-500, SHU-321,
ВШ-152РВ, КШ-3М, RSM-500,
М1363, МЕ1350, МD1320В.
Многие заводы выпускают разнообразные станки, например, ОАО «Харьковский станкостроительный завод» выпускает:
- круглошлифовальные полуавтоматы общего назначения - 3М152ВМ, 3М162В, 3К152ВФ20; - универсальные круглошлифовальные полуавтоматы - 3М132В, 3У142МВ, 3У143МВ, 3У144МВ; - тяжелые круглошлифовальные станки - 3М193, 3М194, 3М195, 3М196, 3М198.
Рисунок 8.2 Круглошлифовальный станок 3М174. Станок используется для
шлифования наружных цилиндрических поверхностей диаметром до 700мм,
длиной до 6100мм, вес заготовки до 5,0 тонн.
|
|
а) б)
Рисунок 8.3 Круглошлифовальные станки фирмы «DANOBAT», а) – типа UG; б) – типа HG.
Технические характеристики |
UG-41 |
UG-51 |
HG-71 |
HG-72 |
HG-91 |
Максимальная длина шлифования, мм |
600 1000 |
600 1200 1800 |
1600 2300 3000 |
1600 2300 3000 |
2000 3000 4000 5000 6000 |
Максимальный диаметр шлифования, мм |
348 |
270 / 320 |
445 / 550 |
445 / 550 |
650 / 850 |
Максимальный вес заготовки, кг |
125 |
125 250 700 |
125 500 1500 |
125 500 1500 |
5000 6000 |
Максимальный размер шлифовального круга, мм |
400 х 63 500 х 80 |
500 х 80 610 х 170 |
500 х 80 610 х 80 |
610 х 170 760 х 300 915 х 200 |
760х300 915х200 1060х150 |
Мощность шлифовального головки, кВт |
5,5 / 7,5 |
7,5 / 11 / 15 |
7,5 / 11 / 15 |
11 / 15 / 22 / 30 / 37 / 45 |
11 / 15 / 22 / 30 / 37 / 45 |
Скорость шлифования, м/с |
45 |
50 / 60 |
45 / 60 |
45 / 60 |
45 / 60 |
Бесцентровошлифовальные станки. Применяются в крупносерийном и массо-
Рисунок 8.4 схемы бесцентренного шлифования:
а) – наружных поверхностей;
б) – с уступом до упора;
в) – врезанием поперечным перемещением ведущего круга;
вом производстве для наружного и внутреннего шлифования тел вращения. (Рис. 8.4). При шлифовании наружных поверхностей заготовка 3, поддерживаемая ножом 4, располагается между двумя абразивными кругами из которых шлифу-емый круг 1, вращаясь с окружной скоростью 30…40 м/с, снимает с заготовки припуск, а другой ведущий круг 2, вращающийся с окружной скоростью 10…50 м/мин, сообщает заготовке вращение (круговую подачу) VSкр и продольную (осевую) подачу Ппр. Установочное поперечное перемещение ведущего круга Пвр определяет диаметр шлифуемой детали. Ось ведущего круга 2 поворачивает на угол α, чтобы он не только вращая заготовку VSкр , но и выполняя её осевую подачу Ппр. При черновом шлифовании α = 1,5…6º, при чистовом α = 0,5…1,5º.
Для прилегания к заготовке ведущего круга, повёрнутого на угол α, по линии, он заправляется как однополостный гиперболоид вращения, движением алмаза параллельно оси заготовки.
Наиболее часто на этих станках применяют сквозное шлифование деталей с постоянным наибольшим диаметром (рис. а), но применяют и шлифование деталей с уступом до упора 5 (рис. б). В этом случае для заготовки 3 и её снятие ведущий круг 2 отводится.
Недлинные заготовки сложной формы шлифуют методом врезания поперечным перемещением ведущего круга 2 (рис. в). При этом в осевом направлении заготовка 3 фиксируется упорами 5, к которому поджимается за счёт небольшого (порядка 30”) поворота оси ведущего круга 2.
Модели бесцентровошлифовальных станков: 3В182, 3М184А, 3Е184В, М1020А, MG1020, М11100, SASL 125/1.
Рис. 8.5. Бесцентрово-шлифовальный станок: 1 – станина; 2, 4 – бабки; 3, 5 – механизмы для правки кругов; 6 – нож.
Внутришлифовальные станки. Относятся ко второму типу станков рассматриваемой группы и используются для окончательной обработки цилиндрических и конических отверстий, как сквозных, так и глухих. В ряде случаев одновременно с отверстием на этих станках могут обрабатываться и торцы заготовок.
Рисунок 8.6 Устройство внутришлифовального станка: 1- станина; 2передняя бабка;
3 – самоцентрирующее приспособление; 4 – деталь; 5 – шлифовальный шпиндель;
6, 10 – маховик; 7 – стол; 8 – кулачки; 9 – рычаг.
Max. размер стола,мм |
550 |
||
Цена деления лимба,мм |
0.002 |
||
Перемещение продольное |
ручное и гидравлическое |
||
Мощность,кВт |
3.8 |
||
Масса,кг |
1600 |
||
Габариты,мм |
2363x1260x1310 |
||
Точность |
Округлость,мм |
0,0025 |
|
Цилиндричность,мм |
0,004 |
||
Шероховатость(μm) |
Ra0.63 |
Рисунок 8.7 Станок М2110С и
его краткая техническая характеристика.
Рисунок 8.8 Внутришлифо-
вальные головки (ВШГ).
Рисунок 8.9 Внутреннее шлифование на станке фирмы BWF, Германия.
Некоторые модели внутришлифовальных станков: 3К 225В, 3К227В, 3К228А, 3А228П, 3К228А, 3К229А, 3А230, М2110С (Рис. 8.7), 3М225ВМ, JAG-3JAW, IGD10A (Китай), IG32C (Китай).
О
бдирочно-шлифовальные
станки. Обдирочно-шлифовальные
станки, относящиеся к третьему типу,
обычно работают на более жестких режимах
и предназначаются для глубокой зачистки
труднообрабатываемых элементов
заготовок, полученных литьем, сваркой,
штамповкой (заусенцев, швов, неровностей
и т. п.). Их применяют также для обработки
заготовок из неметаллов, например при
изготовлении шлифовальных кругов.
Рисунок 8.10 Обдирочно- шлифовальный 3Н340. |
1. Шлифовальные круги, мм ПВ400х50х203(400х50х127)
ПП400х50х203(400х50х127)
2. Количество шлифовальных кругов, шт 2
3. Высота центров шлифовал. кругов от пола, не менее, мм 900
4. Расстояние между шлифовальными кругами, мм 500
5. Скорость окружная, м/с 30
6. Питание от сети переменного тока:
- напряжение, В 380
- частота, Гц 50
7. Электродвигатель:
- тип 4АМ100S4УЗ
- мощность, кВт 3
- частота вращения, об/мин 1435
8. Габариты станка, мм (длина/ширина/высота)1060х700х1250
9. Масса станка, не более, кг 340
Некоторые модели: 3Н340, 3А306К-90, ВЗ-379, ВШ-041, ГС555.
Специализированные и заточные шлифовальные станки. Четвертый и пятый типы включают специализированные шлифовальные станки. Так, мод. ЗА544 используется для плоского шлифования направляющих станков, мод. 3510 отличается повышенной точностью обработки, мод. 3451 применяется для шлицешлифовальных работ и т. п.
а) б)
Рисунок 8.11 Специализированные шлифовальные станки: а) – шлицешлифовальный 3М451Г;
продольно-шлифовальный 3К544 для шлифования направляющих.
Заточные станки относятся к шестому типу и используются для заточки различного металлорежущего инструмента (резцов, слесарного инструмента, сверл и т. п.) и многих других работ. Универсально-заточные станки мод. 3644, ЗВ641, ЗМ642К и др. позволяют затачивать многолезвийный инструмент, а заточные станки мод. 3622, ЗВ659 и 3663 служат для заточки соответственно резцов, сверл и червячных фрез.
а) б)
Рисунок 8.12 Специализированный шлифовальный станок для перешлифовки шеек коленвала 3Д4230 – а) и процесс шлифования на этом станке – б).
а) б)
Рисунок 8.13 Заточные станки: а) – универсально-заточной 3М642Е;
б) – алмазно-заточной для резцов модели 3622.
А) Б)
Рисунок 8.14 Современные заточные станки: А) – для заточки свёрл XT 3000i, ф. DAREX, США
Б) – шлифовально-заточной центр с ЧПУ ВЗ-531Ф4, заточка червяка.
Плоскошлифовальные
станки.
По расположению оси шпинделя плоскошлифовальные станки подразделяются на горизонтальные (рис. а и в), работающие периферией круга и на вертикальные (рис. б и г), работающие торцом круга.
По форме стола они подразделяются на имеющие круглый стол (в и г) имеющие прямоугольный стол (а и б).
Главное движение резания у всех разновидностей – вращение шлифовального круга Vкр. При прямоугольном столе имеется его продольное возвратно-поступательное движение Ппр, при круглом – вращение стола Vст. При работе дисковым кругом на станках с горизонтальным шпинделем имеется периодическая поперечная подача Ппоп вдоль оси шпинделя для обработки заготовок по всей их ширине.
У
всех вариантов плоскошлифовальных
станков имеется ещё периодическая
вертикальная подача врезания Пвр,
выполняемая в начале каждого хода или
оборо-та стола. Шероховатость поверхностей,
обрабатываемых на плоскошлифовальных
станках после чернового шлифования
достигает от 3,2 до 0,8 Ra,
после чистового от 0,8 до 0,4 Ra
и после тонкого шлифования – 0,4 до 0,2
Ra.
а) б)
Рисунок 8.15 Плоскошлифовальные станки: а) – 3Д711АФ11, с крестовым столом:
Б) – 3Л741ВФ10, с круглым магнитным столом.
Притирочные, полировальные, хонинговальные и доводочные станки относятся к восьмому типу. В ряде случаев шероховатость и качество поверхности, обработанной лезвийным инструментом и шлифовальными абразивными кругами, оказываются недостаточными для удовлетворения техническим условиям на те или иные детали. В подобных случаях применяют специальные отделочные технологические методы: хонингование, притирку и суперфиниш.
Хонингование применяется для обработки внутренних и наружных поверхностей до 7-го квалитета точности с шероховатостью Ra = 0,32 - 0,08 мкм. Этой обработке преимущественно подвергаются внутренние поверхности таких деталей, как гидроцилиндры, орудийные стволы, гильзы цилиндров двигателей внутреннего сгорания и поршневых компрессоров и т. п.
Рисунок 8.16 Хон: 1- корпус; 2 – бруски; 3 – раздвигающие конусы;
4 – шарниры; 5 – шпиндель станка.
Хонинговальная головка (хон, хона) представляет собой инструмент, состоящий из металлической конструкции, несущей абразивные или алмазные бруски, расположенные по окружности (рис. 236). Эти бруски принудительно, специальным механизмом головки раздвигаются по радиусам постепенно за каждый ход увеличивая обрабатываемый диаметр отверстия. Зерна бруска при хонинговании образуют неповторяющиеся пересекающиеся винтовые траектории (Рис. 8.17), что способствует получению поверхности с высокими эксплуатационными свойствами.
Хонинговальные
станки могут иметь горизонтальное или
вертикальное расположение шпинделя,
совершающего вращательное движение
резания v и возвратно-поступательное
движение продольной подачи vs
относительно обычно неподвижной
заготовки. Станки имеют много общего
со сверлильными станками.
.
Рисунок 8.17 Траектория движения зёрен бруска хона.
Рисунок 8.18 Хонинговальный станок с вертикальным шпинделем: 1 - стол; 2 – хон;
3 – коробка скоростей; 4 – пульт управления; 5 – насосная станция.
Для отделки наружных поверхностей чаще применяют суперфиниширование — обработку колеблющимися брусками (рис. 8.18). Бруски закрепляются в головке не жестко, как при хонинговании, а упруго.
Рисунок
8.18 Суперфиниширование
Добавляется вибрационное движение L бруска вдоль оси (Рис. 8.18, а) с частотой до 50 Гц и амплитудой / = 2 - 5 мм. Подпружиненный брусок снимает шероховатости поверхности и некоторые погрешности ее предыдущей обработки. Выравнивание поверхности до Ra = 0,16 ч- 0,02 мкм приводит к снижению давления бруска на деталь, и процесс обработки прекращается.
Отделке этим технологическим методом подвергаются ролики подшипников и их кольца, шейки коленчатого и распределительного вала, кулачки, калибры, поршни, клапаны и другие ответственные детали (Рис. 8.18, б). Припуск под суперфиниширование — около 0,01 мм на диаметр. Бруски (от одного до четырех) — с алмазоносным слоем или абразивные из карбида кремния зеленого либо электрокорунда белого на керамической связке.
Доводка и притирка позволяют получить самые точные (5-го квалитета и выше) и чистые (Ra = 0,16 - 0,08 мкм) поверхности деталей, предварительно прошедших обработку шлифованием. Припуск около 0,01 мм снимается при доводке (притирке) абразивными пастами, нанесенными на чугунный притир, мелкозернистыми доводочными кругами или свободным абразивом.
Доводка применяется для обеспечения герметичности соединений, повышения усталостной прочности деталей, срока их службы и т. п. Этот метод используется при заточке режущего инструмента, изготовлении плунжерных пар топливной аппаратуры дизелей, калибров, ответственных подшипников и т. п. Доводка и притирка осуществляются вручную или на специальных станках при скорости 0,1-2,0 м/с и малых давлениях (Рис. 8.19)
Важную роль в процессе играют не только траектории взаимного перемещения зерен и заготовки, режимы обработки и состав абразивных элементов, но и жидкие компоненты суспензии или СОЖ, используемых при обработке (например, минеральные масла с различными добавками). Доводку существляют в несколько операций, изменяя пасту и режимы работы.
.
Рисунок 8.19 Схемы доводки:
Станки для финишной обработки предназначены для исправления отклонений от геометрической формы деталей и получения высокого качества поверхностей. Так, мод. 3881 и 3881Б применяют для изготовления шлифов при металлографических исследованиях, а мод. 3867 используют для доводки при бесцентровой обработке.
Полировальные станки позволяют получать заготовки с весьма малой шероховатостью поверхности, а притирочные обеспечивают, кроме того, высокую геометрическую и размерную точность. Для достижения высокой герметичности соединения применяют также притирочные работы и станки.
Группа 5. Зубо - и резьбообрабатывающие станки ТЕМА 9
Пятая группа станков включает многообразные зубообрабатывающне, а также специальные резьбообрабатывающие станки. Зуборезные станки, пожалуй, самые сложные из металлорежущих станков и едва ли не самые малопроизводительные. Для обработки зубьев колес используются следующие способы мехобработки: фрезерование, строгание, долбление, протягивание, точение, шлифование и другие технологические методы, что можно увидеть в названии станка. В групповой классификации зубообрабатывающнх станков отражаются:
технологический метод резания;
вид зубчатого колеса;
назначение обработки (образование зубьев, их отделка);
другие признаки.
Методы нарезания зубьев зубчатых колёс. Основные: метод копирования и метод обкатки.
Метод копирования (Рис.9.1). При обработке этим методом впадина зубчатого колеса образуется режущим инструментом, профиль режущих кромок которого выполнен по форме впадины нарезаемого колеса. К данному методу относятся фрезерование зубьев модульными дисковыми и пальцевыми фрезами, строгание профильными резцами, обработка протяжками и профильными шлифовальными кругами. Следует отметить, что профиль зуба (кривизна эвольвенты) зубчатого колеса зависит от модуля, угла зацепления и числа зубьев, следовательно, теоретически для обработки каждого зубчатого колеса с определённым числом зубьев и модулем потребуется свой режущий инструмент. Поэтому, например, при обработке дисковыми модульными фрезами зубчатых колёс одного модуля, но с различным числом зубьев применяют наборы фрез из 8, 15 или 27 шт. Метод копирования при изготовлении зубчатых колёс имеет ограниченное применение.
Рисунок 9.1 Нарезание зубьев зубчатых колёс методом копирования.
Рисунок 9.2 Нарезание червяком (фрезой) поз.1 зубьев цилиндрического колеса поз.2. |
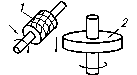
Виды зубчатых колёс. В зависимости от эксплуатационных требований зубчатые колеса разделяют на три группы: скоростные, силовые и отсчётные.
В зависимости от типа передачи движений:
для передачи вращения при параллельных осях валов служат цилиндрические
зубчатые колеса с прямыми и спиральными (косыми) или шевронными зубьями.
для передачи вращения при пересекающихся осях служат конические зубчатые
колеса с прямыми и криволинейными зубьями.
для передач со скрещивающимися осями применяют зубчатые колеса с
винтовыми зубьями и червячные пары (червячное колесо, находящееся в зацеплении с ведущим червяком).
для преобразования прямолинейного движения во вращательное, или наоборот,
применяют реечные передачи, где зубчатое колесо находится в зацеплении с зубчатой рейкой; зубья колеса и рейки могут быть прямые или спиральные (косые).
Зубодолбежные станки для обработки по методу обкатки зуборезным долбяком цилиндрических колес, а также зубчатых секторов внутреннего и внешнего зацепления с прямым, косым или винтовым зубом.
Обработка зубчатых колёс долбяками. Долбяк 1, Рис.9.3, имеет форму цилиндрического колеса, зубья которого выполнены с углами резания. При нарезании воспроизводиться работа пары цилиндрических зубчатых колёс (долбяк 1 и заготовки 2). Во время обработки долбяк получает прямолинейное возвратно-поступательное главное движение и медленное вращение вокруг своей оси. В начале нарезания зубьев при согласованном вращении заготовки и долбяка (движение обкатки) происходит радиальное врезание долбяка (или заготовки) до полной глубины резания. Для получения полностью обработанных зубьев на всей окружности заготовка после окончания радиального врезания долбяка должна сделать полный оборот. Резание происходит только при прямом ходе долбяка, а при обратном холостом ходе шпиндель долбяка или стол несколько отводится образуя зазор между инструментом и заготовкой для устранения трения задних поверхностей долбяка в впадине нарезаемого колеса. Долбяками можно производить нарезание цилиндрических колёс наружного зацепления внутреннего зацепления, зубчатых блоков, цилиндрических колёс с косыми зубьями.
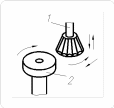
2
1
а) б)
Рисунок 9.3 Нарезание зубьев цилиндрических колёс: а) – наружного зацепления хвостовым долбяком; б) – внутреннего зацепления дисковым долбяком.
Для нарезания цилиндрических колёс с косыми зубьями необходимы специальные долбяки.
Модели зубодолбёжных станков: 5107, 5В150, 511.1 и другие (Рис.9.4) полуавтоматические станки. В парке зуборезных станков они составляют более 20% .
а) б)
Рисунок 9.4 Зубонарезные станки 1 группы: а) – универсальный долбёжный 5А140П;
б) – полуавтомат зубодолбёжный 5М150П.
Ко второму типу относятся зуборезные станки для обработки конических колёс (ГОСТ 659-89), Рис.9.5.
а) б)
Рисунок 9.5 Полавтомат зуборезный для конических колёс с круговыми зубьями 5С26П:
а) – общий вид полуавтомата; б) – станочная наладка.
Техническая характеристика модели 5С26П Предназначен для нарезания прямозубых конических и гипоидных колес, работает по методу обкатки или врезания. |
|
ОКП: |
381523 |
Год начала выпуска: |
1974 |
Класс точности: |
П |
Наибольший диаметр обрабатываемой детали, мм |
320 |
Наибольший модуль обрабатываемых зубчатых колес |
6 |
Наибольшая ширина зубчатого венца, мм |
50 |
Min частота вращения шпинделя об/м: |
30 |
Max частота вращения шпинделя, об/м: |
200 |
Мощность, кВт: |
3 |
Размеры (Д_Ш_В), мм: 2940х2090х2050 |
|
Масса станка с выносным оборудованием, кг: |
9000 |
По методу обкатки зуборезной головкой, Рис. 9.6, обрабатываются круговые зубья на станках мод. 525, 5Б231 и др.
Рисунок 9.6 Зуборезные головки для нарезания конических и гипоидных колёс с
круговыми зубьями.
П
рямозубые
колеса получают на зубострогальных
станках (Рис.5.9) мод. 5А250, 5282, 5А283 и др.,
которые тоже относятся ко 2 группе.
Рабочие движения сообщаются инструменту
и заготовке.
Движение резания осуществляют
резцы (Рис.5.7), движущиеся возвратно-поступательно
в радиальном направлении к центру станка
и закрепляемые в резцовых салазках.
Заготовка закрепляется в шпинделе
делительной головки. Заготовке через
зубчатую передачу сообщается вращение
в период обкатки.
Рисунок 9.7 Зубострогальный резец: а - углы
заточки; б - внешний вид.
Рис. 9.8 Станок зубострогальный 5А250П для нарезвния прямозубых конических колёс
двумя резцами по методу обкатки.
По методу кругового протягивания каждой впадины работает зубопротяжный станок мод. 5245 для обработки конических прямозубых колес в условиях массового производства. Зубофрезерные станки мод. 5П23, 5230 и др. применяют для обработки двумя дисковыми фрезами конических прямозубых колес по методу обкатки. За один цикл обрабатываются обе стороны профиля зуба модулем до 8 мм.
а) б)
Рисунок 9.9 Зуборезные станки 2 группы: а) – зубопротяжный автомат 5С269 для обработки дифференциалов автомобилей и тракторов; б) – зубофрезерный станок 5230.
Зубофрезерные станки для обработки по методу обкатки червячной фрезой цилиндрических прямозубых и косозубых колёс, червячных колес и шлицевых валов в условиях единичного, серийного и массового производства.
Рисунок 9.10 Нарезание зубчатого колеса на зубофрезерном станке методом обкатки с помощью червячной фрезы; а) – одного колеса; б) – двух колёс (на универсальном фрезерном полуавтомате 53А50Н).
Рисунок 9.11 Станок 53А11. Нарезание зубчатых колес производится по способу обкатки червячной фрезы и обрабатываемой заготовки. Станок работает по замкнутому полуавтоматическому циклу и по циклу наладки. Станок имеет неподвижный стол и подвижную стойку. Наличие в станке универсального фрезерного суппорта позволяет обрабатывать цилиндрические и червячные колеса методом радиального врезания и тангенциальной подачи.
Они относятся к третьему типу и составляют около 50% зуборезного оборудования. К ним относятся мод. 530П, 5К32, 5А342, 5300 и др. На некоторых моделях можно работать и пальцевыми модульными фрезами по методу копирования, обрабатывая шевронные зубья. По специфике процесса нарезания эти станки относятся к полуавтоматическим. На станках этого типа нарезаются шлицы на валах, так же как на обычных зуборезных и специальных шлицефрезерных станках (мод. 5350, 5350Б и др.).
4. Зубофрезерные станки для нарезания червячных колес работают только по методу обкатки. Следует отметить, что с каждым червячным колесом может входить в зацепление только червяк одного определенного размера. Поэтому червячное колесо необходимо нарезать червячной фрезой, имеющей все основные параметры (модуль, диаметр делительной окружности, число заходов, угол винтовой нарезки) такие же, как у червяка, которой будет работать с данным нарезаемым колесом. Червячные колеса могут быть нарезаны двумя способами: радиальной подачей фрезы и осевой или тангенциальной подачей фрезы (Рис.9.12). В обоих случаях ось червячной фрезы устанавливают перпендикулярно оси заготовки и в средней плоскости нарезаемого червячного колеса.
Рисунок 9.12 Способы нарезания червячных колёс: а) – с радиальной подачей фрезы;
б) – с осевой (тангенциальной) подачей фрезы.
При способе нарезания червячных колёс с радиальной подачей фрезы (рис. а) червячная фреза получает главное вращательное движение nф и перемещение в направлении l (радиальная подача), заготовка – вращение, согласованное с вращением червячной фрезы (движение обкатки). Процесс нарезания заканчивается после перемещения фрезы на полную глубину зубьев нарезаемого колеса.
При способе нарезания червячных колёс с осевой или тангенциальной подачей (рис. б) фреза выполняется с заборным конусом и при настройке станка её устанавливают на полную глубину фрезерования. При обработке червячная фреза получает главное вращательное движение nф и движение осевой подачи в направлении l, заготовка при этом должна получить вращение, как при работе червячной пары (движение обкатки), и дополнительный поворот как при работе реечной пары при перемещении червячной фрезы на величину l.
Как и станки для обработки реек, их относят к четвертому типу (хотя станки для обработки реек могут работать как фрезой по методу копирования, так и зуборезным долбяком). Примером станков этого типа являются мод. 5412, 5414 и др.
Станки для обработки торцов зубьев колёс относятся к пятому типу и позволяют обрабатывать фаски, снимать заусенцы или закруглять торцы зубьев.
Рисунок 9.13. Схема зубозакругления зубьев: а) – наружных; б) – внутренних.
|
Рисунок 9.14 Схема снятия фасок с острых кромок зубьев 5: 3 – шлифовальным кругом; 4 – дисковой фрезой.
|
К этим станкам относятся модели:
- зубозакругляющие и зубозаостряющие 5А580, 5Н580,5Е580, 5Н582, ЕЗ101, КН50;
- зубофасочные и для снятия заусенцев 5525, 5Б525, 5Б525-2, 5527, ВС320А, ВС500.
Рисунок 9.15 Полуавтомат ВС-81 для заострения зубьев на торцах прямозубых цилиндричес-ких зубчатых колес наружного и внутреннего зацепления двумя торцевыми фрезами.
Шестой тип станков пятой группы включает рсзьбофрезерные станки (ГОСТ 1797-78).
Резьбофрезерные станки предназначены для нарезания наружных и внутренних резьб гребенчатыми, дисковыми фрезами и резцовыми головками. Гребенчатые фрезы применяют при нарезании коротких резьб, а дисковые фрезы и резцовые головки — длинных резьб. В зависимости от степени универсальности резьбофрезерного станка узлы регулирования движений выполнены в нем по-разному. В более универсальных резьбофрезерных станках скорость главного движения и подачи изменяют с помощью коробок скоростей и подач или сочетанием коробок скоростей и подач со сменными гитарами зубчатых колес. В менее универсальных станках скорость главного движения регулируют, например, сменными зубчатыми колесами, а винторезную цепь настраивают с помощью гитары сменных зубчатых колес или плоской поворотной линейки, или сменными дисковыми или торцовыми кулачками.
Модели резьбофрезерных станков: 5Б63, 5Б63Г, 5Д63Г(Рис.9.16), 5Б64, 5Б65 используются как резьбофре-зерные полуавтоматы.
Рисунок 9.16 Станок 5Д63Г резьбофрезерный патронно.
Зубоотделочные станки относятся к седьмому типу зубообрабатывающих станков. Зубоотделочные станки служат для получения точной формы и размеров зубьев и улучшения качества их поверхности. Отделка зубьев производится методами обкатывания, шевингования, притирки, шлифования и хонингования. Обкатывание и шевингование применяют для отделки незакаленных колес, а шлифование, притирку, хонингование - для закаленных.
Обкатные (нагартовочные) станки (мод. 5А725, 5А726, 5Б725 и др.) предназначены для получения гладкой и уплотненной поверхности зубьев методом наклепа. Обрабатываемое колесо вводят в зацепление с тремя эталонными колесами. Прижим колеса к эталонным колесам осуществляется гидравлически. Периодически движение всех колес реверсируется. На отделку одного зуба затрачивается 0,1-1 с. При обработке на этих станках погрешности профиля шага не устраняются. На контрольно-обкатных станках контролируются пятна контакта зубьев, бокового зазора и уровня шума в зубчатых передачах.
Рисунок 9.17 Станок контрольно-обкатной СЗ-14.
Зубопритирочные станки (мод. 5П725и др). Притираемое колесо насаживается на оправку, свободно вращающуюся в центрах, и вводится в зацепление с одним или несколькими чугунными притирами. Притир - это изготовленное с высокой точностью зубчатое колесо, зубья которого смазываются смесью масла с мелкозернистым абразивным порошком. Притиры получают вращение и возвратно-поступательное движение вдоль оси заготовки. Оси притиров и зубчатого колеса могут скрещиваться или быть параллельными между собой. После обработки зубьев с одной стороны притиры вращаются в обратном направлении и зубья обрабатываются с другой стороны. Притирка повышает степень точности и качество поверхности зубчатых колес.
Рисунок95.18 Полуавтомат зубопритирочный 5П725Е.
Зубошевинговальные станки (мод. 5702, 5717 и др.) применяют для отделки поверхностей термически не обработанных и улучшенных колес. Выпускаются зубошевинговальные полуавтоматы для обработки зубчатых колес диаметром до 4000 мм. При относительном скольжении профилей обрабатываемого колеса и шевера с боковых поверхностей зубьев снимается стружка толщиной 0,005-0,1 мм. При обработке прямозубых колес применяют косозубый шевер и наоборот. Для обеспечения относительного проскальзывания профилей зубьев заготовку и шевер устанавливают под углом скрещивания 10-15°.
Рисунок 9.19 Полуавтомат зубошевин-говальный 5Б703. |
Рисунок 9.20 Схема шевингования. |
||||||||||||||||||||||||
Техническая характеристика 5Б703
|
|||||||||||||||||||||||||
|
Шевингование происходит следующим образом. Шевер получает вращение (движение резания) и ведет за собой заготовку (движение обкатывания ). Заготовка установлена на оправке в центрах передней и задней бабок, размещенных на специальном столе, обеспечивающем получение бочкообразного зуба. Стол с заготовкой получает возвратно-поступательное движение подачи S1 по направляющим кронштейна ; причем в конце каждого хода вращение шевера и заготовки реверсируется. Радиальная подача S (врезание) сообщается столу с заготовкой или шпиндельной головке.
Зубо- и резьбошлифовальные станки относятся к восьмому типу. К нему также относятся станки для шлифования цилиндрических колес мод. 5В830, 5891, 5831 и др. Зубошлифовальные станки применяют для шлифования зуборезных долбяков, шеверов и эталонных зубчатых колес. Такие специальные прецизионные станки работают по методу обката (огибания) с помощью эвольвентного копира. Очень важной и сложной операцией является шлифование профиля зубьев. Например, у долбяков эвольвентный профиль зубьев шлифуют на специальных полуавтоматах, работающих по методу обката с периодическим делением. За каждый цикл обрабатывается лишь одна сторона зуба. Движение обката выполняется заготовкой. На Рис. 9.21 изображён зубошлифовальный полуавтомат мод. 5893.
Рисунок 9.21 Зубошлифовальный полуавтомат мод. 5893: 1 — педаль тормоза; 2 — станина; 3 — нижний стол; 4 — квадрат продольного перемещения круга; 5 - верхний стол; 6— маховичок поперечного перемещения круга; 7— маховичок вертикального перемещения круга; 8 — пы-лесос; 9— колонна; 10 — поворот колонны; 11 — рукоятка продольного перемещения приспособления для правки круга; 12 — кнопка для установочного перемещения приспособле-ния; 13 — поворотная кнопка для поперечного перемещения приспособления; 14— шлифо-вальная бабка; 15— рукоятка ручного поворота рабочей головки; 16— рабочая головка; 17— маховичок тонкой поперечной подачи шлифовального круга; 18— салазки.