
С хема режущего плазмотрона.
1 - Корпус;
2 - Электрод (катод);
3 - Формирующий наконечник;
4 - Изолятор;
5 - Разрезаемый металл;
6 - Дуговая камера; 7 - Столб дуги;
8 - Подача охлаждающей воды; 9 - Подача плазмообразующего газа;
10 - Слив воды;
11 - Источник тока; 12 - Устройство зажигания дуги;
Vр - Направление резки.
В корпусе плазмотрона находится цилиндрическая дуговая камера небольшого диаметра с выходным каналом, формирующим сжатую плазменную дугу. Электрод обычно расположен в тыльной стороне дуговой камеры. Непосредственное возбуждение плазмогенерирующей дуги между электродом и разрезаемым металлом, как правило, затруднительно. Поэтому вначале между электродом и наконечником плазмотрона зажигается дежурная дуга. Затем она выдувается из сопла, и при касании изделия ее факелом возникает рабочая режущая дуга, а дежурная дуга отключается.
Столб дуги заполняет формирующий канал. В дуговую камеру подается плазмообразующий газ. Он нагревается дугой, ионизируется и за счет теплового расширения увеличивается в объеме в 50–100 раз, что заставляет его истекать из сопла плазмотрона со скоростью до 2–3 км/c и больше. Температура в плазменной дуге может достигать 25000–30000°С.
Мощными плазменными горелками, работающими при напряжении дуги до 200 В, можно разрезать листы толщиной до 150 мм и более со скоростью до 1 м/мин, а листы толщиной до 66 мм - при скорости до 5 м/мин и более. Плазменная резка алюминиевых сплавов и других цветных металлов и легированных сталей позволяет получать резы с высоким качеством (по чистоте и точности) и отличается наибольшей экономичностью по сравнению со всеми другими методами резки. Для низкоуглеродистых сталей плазменная резка особенно эффективна при обработке листов толщиной до 30 мм.
В
арианты
плазменной резки
Обычная плазменная резка В данном процессе используется один газ (обычно воздух), который и охлаждает, и создает плазму. Большинство таких систем работают на токах ниже 100 А, разрезается материал толщиной до 12 мм. Часто применяется при ручной плазменной резке. Резка двумя газами В этом процессе используются два газа – один создает плазму, а другой – защитный. Защитный газ защищает место резки от воздействия атмосферы, создавая более чистый рез. Возможно использование самых различных комбинаций газов для достижения наилучшего качества.
Резка под защитой воды Это вариант резки, аналогичный варианту с двумя газами, только вместо защитного газа используется вода. Получается лучшее качество резки нержавеющей стали. Данный процесс не применяется при ручной резке.
Резка с водяным впрыском При таком типе используется газ для создания плазмы, а вода впрыскивается либо радиально, либо с завихрением прямо в дугу, чтобы улучшить форму дуги и увеличить плотность и температуру дуги. Такие процессы применяются от 260 до 750 А для высококачественной резки различных материалов и толщин. |
Рис.9 |
Плазмотрон.
Принципиальные схемы плазмотронов прямого действия (а) и косвенного (б):
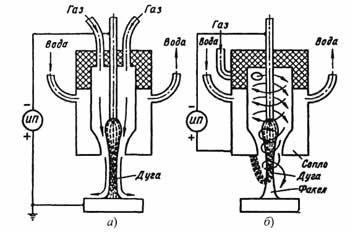
Физической основой воздушно-плазменной резки является выдувание электрической дуги сжатым воздухом, с последующим местным плавлением металла и удалением его из зоны резки разогретым газовым потоком. Дуга, свободно горящая в воздухе, имеет температуру 6000 - 8000 К. Если увеличить внешнее охлаждение дуги, сжав ее потоком газа, то ее температура возрастет до 20000 К и вокруг дуги формируется газовый поток. Такое состояние вещества называют низкотемпературной плазмой. Устройства, в которых электрическая энергия превращается в тепловую энергию потока низкотемпературной плазмы, носят название плазмотроны.
Воздушно-плазменная резка, как и газокислородная, относятся к одной группе термической резки металлов. Это обуславливается одним и тем же принципом действия: местный нагрев с последующим выдуванием расплавленного металла из зоны резки. Отличие их в том, что при газокислородной резке источниками энергии являются горючее и окислитель, а при использовании воздушно-плазменной резки - энергия электрической дуги. Но по сравнению с газокислородной, воздушно-плазменная резка имеет ряд существенных преимуществ.
Так как температура плазмы достигает десятков тысяч градусов, это позволяет резать любые металлы и их сплавы, в том числе углеродистую, нержавеющую и высоколегированную стали, чугун, медь, латунь, бронзу, алюминий, титан, а также биметаллы. Вследствие такой высокой температуры скорость резки в несколько раз выше, чем при газокислородной резке, а сам процесс начинается без предварительного разогрева металла. При этом металл не коробится и не деформируется, а грат, образующийся на краях реза, легко удаляется, после чего остается ровная кромка. Кроме этого потери металла минимальны из-за малой ширины реза.
Для работы аппаратов воздушно-плазменной резки требуются только электроэнергия и сжатый воздух, а при наличии компрессора только электроэнергия. По сравнению со сложностями, возникающими при использовании оборудования для газокислородной резки, такими как: заправка, переаттестация и доставка громоздких баллонов, взрывопожароопасность, использование присадок при необходимости работать с цветными металлами и сплавами, аппараты воздушно-плазменной резки требуют только замены расходных материалов (электродов и сопел), месячный запас которых легко умещается в дамской сумочке.
Одним из основных параметров плазменной резки является сила тока плазменной дуги. В настоящее время практическая верхняя граница тока кислородной плазмы составляет 440 A (при большей силе тока сокращается срок службы деталей).
В настоящее время существует большое количество оборудования плазменной резки. Оно разделяются на ручные установки плазменной резки, портативные установки, стационарные портального типа с применением рабочего стола и стационарные портального типа промышленного назначения без рабочего стола.
Ручные установки плазменной резки применяются в тех случаях когда нет необходимости в получении сложных контуров и требуемая точность обработки невысокая. Такие установки широко применяются в ЖКХ, на небольших производствах, где не требуется большая производительность.
На данном оборудовании можно обрабатывать заготовки до 50 мм толщиной, в зависимости от используемого источника питания.
Преимущества плазменной резки по сравнению с газовыми способами резки:
значительно выше скорость резки металла малой и средней толщины;
универсальность применения – плазменная резка используется для обработки сталей, алюминия и его сплавов, меди и сплавов, чугуна и др. материалов;
точные и высококачественные резы, при этом в большинстве случаев исключается или заметно сокращается последующая механическая обработка;
экономичность воздушно-плазменной резки – нет потребности в дорогостоящих газах (ацетилене, кислороде, пропан-бутане);
возможность вырезать детали сложной формы;
очень короткое время прожига (при кислородной резке требуется продолжительный предварительный прогрев);
более безопасная, поскольку отсутствуют взрывоопасные баллоны с газом;
низкий уровень загрязнения окружающей среды.