
- •Фирма «Русский дизель»
- •Химическая промышленность
- •Производство капролактама
- •Городской автотранспорт
- •Железнодорожный транспорт
- •Применение НИОДа для обработки гребней бандажей колесных пар электроподвижного состава депо Свердловск-пассажирский позволило увеличить ресурс бандажей до обточки от 1,5 до 2,4 раз.

vk.com/club152685050 | vk.com/id446425943
Трение – проблема, с которой человечество столкнулось при строительстве пирамид и которая до сих пор остается весьма существенной. С древнейших времен крупным единственным достижением в борьбе с трением можно считать изобретение смазки, то есть перевод трения из сухого в жидкостный режим) ,обретение колеса не решает проблему трения, а обходит ее). В случае, когда не удается перевести трение в жидкостное, оно сопровождается интенсивным износом рабочих поверхностей, приводящим к необходимости периодического ремонта узла трения.
Затраты на эксплуатацию механизмов |
||
12% |
16% |
|
20% |
Изготовление |
|
Техническое обслуживание |
||
|
||
|
Текущие ремонты |
|
|
Капитальный ремонт |
|
|
52% |
Обратившись к диаграмме, мы видим, что по затратам ремонт сопоставим с изготовлением нового механизма (не случайно во многих случаях ремонту предпочитают блочную замену).
Если же учесть, что значительная часть технического обслуживания направлена на борьбу с трением (смена смазки, регулировка узлов трения и т.д.), становиться понятно, что именно трению и вызванному им износу мы обязаны большей частью связанных с техникой затрат.
Очевидно, что противостоять износу, повышая механические свойства поверхностей трения, можно только в определенных пределах, поскольку из двух взаимодействующих поверхностей одна всегда окажется менее стойкой и, следовательно, будет изнашиваться. Наиболее эффективным является разделение трущихся поверхностей при помощи смазки, однако, несмотря на очевидные достижения в этой области, полностью исключить взаимодействие трущихся поверхностей (и их изнашивание) удается только в отдельных случаях, да и то требуется, как правило, применение сложных дополнительных устройств. Особые проблемы здесь возникают при нестабильных режимах работы механизмов, таких, как запуск, остановка, перегрев, переохлаждение и т.п., когда изменяются свойства смазки или не обеспечивается ее оптимальное распределение в зоне трения. Кроме того, при изнашивании поверхностей условия смазывания значительно ухудшаются, что, в свою очередь, дополнительно увеличивает износ.
vk.com/club152685050 | vk.com/id446425943
Современные технологии борьбы с трением
Методы упрочнения, накопленные в течение десятилетий в процессе развития машиностроения, разделены на шесть основных классов:
образование пленки на поверхности, изменение химического состава поверхностного слоя, изменение структуры поверхностного слоя, изменение энергетического запаса поверхностного слоя, изменение шероховатости поверхностного слоя, изменение структуры по всему объему металла.
Чтобы предотвратить или замедлить изнашивание трущихся поверхностей, обычно стремятся повысить их твердость. При этом используют традиционные методы: цементирование, азотирование, поверхностную закалку, наплавку твердыми материалами, цианирование, хромирование и др.
Менее распространены, но находят все большее применение напыление (газоплазменное, электродуговое) твердых материалов на изнашиваемые поверхности. Наиболее перспективными считаются методы, основанные на использовании новейших достижений научно-технического прогресса – лазерную электронно-лучевую и ионную обработку изнашиваемых поверхностей.
Известен способ повышения механической прочности трущихся поверхностей за счет введения в состав основного металлического сплава легирующих элементов (Cr, Ni, Mo, W, V, Ti, и других). Однако этот способ помимо значительных энергетических затрат связан с определенными технологическими трудностями из-за необходимости тщательной полировки твердых трущихся поверхностей.
Определенного эффекта позволяют достичь разработанные в последнее время различные присадки к смазкам, однако к недостаткам присадок можно отнести необходимость постоянного поддержания их концентраций в смазке и наличие во многих случаях определенных побочных эффектов (в частности, практически полную несовместимость с некоторыми видами смазки и между собой). К тому же применение присадок только изменяет количественные параметры взаимодействия в триаде: поверхность – смазка – поверхность, не приводя к изменению самого процесса трения.
Немного о физике явления…
Трение может увеличить или уменьшить прочность металла, повысить или уменьшить в нем содержание углерода, насытить или обеднить металл водородом, отполировать поверхности деталей или «ободрать» их. Материал, претерпевший многократную пластическую деформацию и неоднократный наклеп, теряет способность пластически деформироваться, и происходит чешуйчатое отделение металлов.
При взаимодействии пар трения поверхностная энергия может выделяться в виде тепла или затрачиваться на подстройку в кристаллической решетке
vk.com/club152685050 | vk.com/id446425943
одного кристалла к другому. Под действием этой энергии в процессе эксплуатации непрерывно изменяются в значительно большей степени конфигурация и структура поверхностного слоя, чем всего объема тела.
Этот слой формируется в результате разнообразных механических процессов, которые не только придают необходимую форму поверхности, но и изменяют физико-химические и прочностные свойства материала.
ПРОЦЕССЫ В КРИСТАЛЛИЧЕСКОЙ РЕШЕТКЕ
Поверхностный слой имеет избыточную энергию, следовательно, он обладает повышенной активностью. Внутри твердого тела каждый атом кристаллов окружен другими атомами и связан с ними прочно по всем направлениям. У атомов расположенных на поверхности с внешней стороны от «соседей» – в виде таких же атомов.
В связи с этим у атомов поверхностного слоя остаются свободными связи, наличие которых создает вблизи поверхности атомное (молекулярное) напряжение.
Чтобы при таком несимметричном силовом поле атом кристалла находился в равновесии, необходимо иное, чем внутри кристалла, расположение атомов самого верхнего слоя. Поэтому физико-химические параметры поверхностного слоя, его структура и напряженное состояние, как правило, сильно отличаются от свойств всего объема материала.
ТЕХНОЛОГИЯ ТРЕТЬЕГО ТЫСЯЧЕЛЕТИЯ!!!
С 1991 года успешно применяется принципиально новый метод борьбы с врагом номер один механизмов – трением, позволяющий не только остановить изнашивание, но и в некоторых случаях восстановить состояние изношенных поверхностей. Метод заключается в обработке трущихся поверхностей триботехническим составом НИОД.
ЧТО ТАКОЕ ТРИБОТЕХНИЧЕСКИЙ СОСТАВ НИОД?
Триботехнический состав (ТС) – это вещество, которое при внесении его в зону трения коренным образом изменяет протекающие там процессы за счет изменения свойств контактирующих поверхностей. Таким образом, ТС не является смазкой, т.е. веществом, разделяющим поверхности трения. Не является ТС и модификатором смазки, поскольку функцией модификаторов является изменение свойств смазки или изменение ее взаимодействия с поверхностями трения (например, удержание смазки на поверхности путем создания на ней пористых или волокнистых структур). Отличительной особенностью ТС является то, что по завершении необходимых процессов, не требуется его дальнейшее присутствие в узле трения, в отличие от смазок, присадок к ним и модификаторов, концентрацию которых в узлах трения необходимо поддерживать постоянно.
vk.com/club152685050 | vk.com/id446425943
ТС НИОД предназначен для создания прочного, износостойкого покрытия на местах контактов трущихся поверхностей во вращающихся, скользящих и качающихся механизмах, применяемых в металлообрабатывающей, станкостроительной, авиационной и во многих других областях народного хозяйства. Позволяет уменьшить коэффициент трения трущихся поверхностей, повысить износоустойчивость и антикоррозионную устойчивость. Состав НИОД представляет собой многокомпонентную мелкодисперсную минеральную смесь, полученную из сочетания различным минералов, основными из которых являются серпентин, энстанит и магнетит. Предлагаемый состав применяется в виде суспензии сухой смеси в вязком носителе, в качестве которого может быть использовано любое смазочное масло (моторное, индустриальное и др.), например нефтяные масла, синтетические масла или солидолы. Вязкий носитель служит средством для транспортировки состава на трущиеся поверхности в закрытые системы.
Способ нанесения состава заключается в нанесении на трущиеся поверхности металлов смеси в виде суспензии, при этом время приработки механизма со смесью (т.е. время, за которое образуется легирующее покрытие) составляет от 30 мин до 8 час в зависимости от состояния и вида механизма. За это время образуется покрытие (легирующий слой) толщиной от 1 до 30 мкм, которое увеличивает износостойкость трущихся поверхностей механизмов.
Физические процессы при образовании покрытия
Покрытие, состоящее из многокомпонентной мелкодисперсной минеральной смеси, включает окислы химических элементов, имеющих разнообразную конфигурацию и размеры электронного облака, которые избирательно встраиваются (внедряются) в образовавшиеся дефекты поверхности металлов, связывая все или большинство свободных валентностей и, соединяясь, друг с другом, образуют прочно сцепленную с подложкой (металлической поверхностью) пленку с чрезвычайно скользкой поверхностью. Наличие в порошке элементов с ярко выраженными аморфными и легирующими свойствами создает не только прочную «керамическую» структуру пленки, но и усиливает механическую прочность подложки. Отсутствие на поверхности пленки свободных валентностей делает ее инертной к агрессивным средам и окислителям, обеспечивая ее антикоррозионную устойчивость. Таким образом, покрытие позволяет увеличивать механическую прочность поверхности металла, снизить коэффициент трения, восстановить дефекты поверхности и повысить антикоррозионную устойчивость.
Обратимся теперь к процессам, протекающим в зоне трения при наличии в ней ТС. Условно их можно разделить на три фазы.
1 - активирование ТС и поверхностей в зоне трения. 2 – диффузия ТС в поверхностные слои металла.
3 – диффузия ТС из поверхностного слоя в глубь металла.
vk.com/club152685050 | vk.com/id446425943
Рассмотрим эти фазы подробнее.
ФАЗА 1
В зоне трения, в микрорайоне пятна контакта действует давление до 1000 МПа. Мелкодисперсные частицы НИОД попадают со смазкой в зону трения, где подвергаются воздействию этого давления. В результате кристаллы НИОД разрушаются, образуя активные радикалы. Одновременно происходит микрошлифование контактирующих поверхностей кристаллами НИОД, имеющими более высокую твердость. При этом с поверхности металла удаляются окисные пленки и т.п., таким образом, поверхность «активируется».
ФАЗА 2
Вторая фаза процесса начинается, когда в зоне контакта образуется достаточная концентрация активированных частиц НИОД и появляется активная поверхность. Под действием контактных нагрузок активированные частицы НИОД диффундируют в кристаллическую решетку металла с образование твердых растворов. Диффузии способствует направленное действие высокой (на уровне предела текучести) нагрузки, а также сходность параметров кристаллических решеток составляющих НИОД и стали.
В результате на поверхности образуется стеклокерамический слой, органически связанный с поверхностным слоем металла. Твердость поверхности существенно увеличивается, приостанавливается ее абразивный износ.
Вторая фаза продолжается до тех пор, пока вся поверхность металла в пятне контакта не будет насыщена НИОД. О ее завершении можно судить по резкому снижению коэффициента трения, и, следовательно, температуре узла трения.
ФАЗА 3
В процессе дальнейшей эксплуатации механизма НИОД из поверхностного слоя под действием контактных нагрузок диффундирует вглубь кристаллической решетки металла. При этом происходит изменение в структуре как поверхностных, так и более глубоких слоев. Процесс заканчивается с образованием стабильной кристаллической структуры поверхностных и подповерхностных слоев. В некоторых случаях количества НИОД, внедрившегося в поверхность, оказывается недостаточно для полного завершения процесса, тогда требуется дополнительное внесение НИОД и повторение всего процесса.
vk.com/club152685050 | vk.com/id446425943
Общая продолжительность третьего этапа может достигать нескольких тысяч часов.
ОСОБЕННОСТИ ПРОЦЕССА
Отметим некоторые особенности процесса, оказывающие существенное влияние на свойства образующихся поверхностей.
1.Процесс протекает одновременно в обеих контактирующих поверхностях под действием одинаковых нагрузок.
2.Процесс обладает способностью к само регуляции, поскольку изменение свойств поверхностей и условий трения вызывает изменение скорости и направления диффузии.
Процесс завершается с образованием структур, адаптированных к конкретным условиям трения.
РЕЗУЛЬТАТЫ ВОЗДЕЙСТВИЯ ТС НИОД
В результате воздействия НИОД образуются поверхности, обладающие уникальными свойствами:
-шлифование поверхностей частицами НИОД и образование поверхностного стеклокерамического микро слоя приводит к значительному снижению шероховатости поверхности (до Ra = 0,1 мкм);
-диффузия НИОД в поверхностные слои металла вызывает упрочняющие их дислокации, что, в совокупности с образованием поверхностного слоя, приводит
кповышению твердости поверхности (до HRC 56-58);
-при одинаковых условиях диффузия в более твердую поверхность происходит медленнее, поэтому менее твердая в паре трения поверхность упрочняется в большей степени и, в конечном этапе, происходит выравнивание твердости взаимодействующих поверхностей;
-низкая шероховатость, высокая и, что более существенно, одинаковая твердость поверхностей и образование на них идентичных стеклокерамических микро слоёв приводит к значительному снижению коэффициента трения. Эксперименты, проведенные на машине трения СМЦ-2, показали, что в результате воздействия НИОД коэффициент трения снижается, в среднем, в 4- 6 раз, а в отдельных опытах было зафиксировано его снижение в 9 раз;
-изменение структуры поверхностных слоев приводит к значительному снижению износа при трении. Экспериментально было зафиксировано снижение износа в 6-10 раз;
-образовавшийся на поверхности металла стеклокерамический слой обладает значительно меньшей, чем у стали, теплопроводностью, в результате чего снижается нагрев узла трения в целом;
vk.com/club152685050 | vk.com/id446425943
-приведенные исследования, а также опыт эксплуатации реальных механизмов показали, что после обработки НИОД узлы трения могут нормально работать без смазки. В настоящее время в «сухом» режиме эксплуатируются сотни механизмов, в том числе десятки редукторов электровозов, мосты легковых и грузовых автомобилей. Известны случаи эксплуатации без смазки воздушных компрессоров и даже двигателей внутреннего сгорания. Контроль, осуществляемый за этими механизмами, не выявил повышенного износа работающих без смазки пар трения или их перегрева при эксплуатации;
-важной особенностью НИОД является то, что эффект от его применения достигается в условиях обычной эксплуатации, то есть не требует существенных затрат времени.
ЭКСПЕРИМЕНТЫ ГОВОРЯТ «ДА»!!!!
Приведем несколько результатов проведенных экспериментов, на примере которых можно сделать выводы о целесообразности применения ТС НИОД в различных механизмах.
Пример 1.
Состав был использован для обработки трущихся поверхностей роликов подшипников 7311К и 15ГПХ.
Подшипники закреплялись за внутреннюю обойму на сверлильном станке, имевшем неизменные обороты шпинделя 315 об/мин, и погружались в стакан с 3- х % суспензии состава НИОД в масле. Наружные обоймы подшипников поджимались к внутренним с усилием 10 МПа. Подшипники вращались 15 мин в одну сторону и дополнительно 15 мин в другую. После обработки этих подшипников на трущихся поверхностях образовывался легирующий слой покрытия.
Были проведены испытания этих подшипников на токарном станке в сравнении с необработанными.
На токарном станке закрепили подшипник (7311К), не обработанный составом НИОД, нанеся на его рабочую поверхность тонкий слой веретенного масла, и стали обкатывать при оборотах шпинделя в 315 об/мин, вращая наружную обойму (режим зажатого подшипника) и застопорив внутреннюю. Через 5 мин работы станка внутренняя обойма начала медленно проворачиваться. Через 13 мин к подшипнику нельзя было притронуться из-за его нагрева. На 20-ой мин переключили режим на 800 об/мин. Через 3 мин подшипник стал издавать звук, а через 4 мин звук стал монотонным. Станок был отключен. Обкатка подшипника закончена. Подшипник сильно перегрет. На роликах и обоймах заметны следы задиров.
Обкатку обработанных покрытием подшипников проводили в том же режиме: сначала при 315 об/мин шпинделя, а затем при 800 об/мин. В результате работы обойма подшипника чуть теплая и никакого звука не отмечалось в течение всего времени обкатки (20мин). Увеличили обороты шпинделя станка до 1200 об/мин, но и в этом случае температура подшипника была в норме. После
vk.com/club152685050 | vk.com/id446425943
остановки была осмотрена поверхность трущихся частей: ни на обойме, ни на роликах изменений не отмечено. Затем были обмазаны внутренняя поверхность обоймы и ролики дорожной грязью и возобновлена обкатка подшипников при 315 об/мин. После 15 мин. обкатки обойма подшипника была чуть теплая. При оборотах шпинделя 800 об/мин через 5 мин ситуация не изменилась. Осмотр трущихся поверхностей показал, что они остались чистыми, без задиров, темных пятен и прочих следов износа. Аналогичные результаты получены при испытаниях покрытия на подшипниках 15ГПЗ.
Пример 2.
Триботехническим составом НИОД был обработан двигатель автомобиля БелАЗ-540, который по графику должен был быть поставлен на капитальный ремонт. Компрессия в цилиндрах двигателя составляла 15-20 кгс/см2. Обработка двигателя по времени заняла 6 часов. В результате непосредственно после обработки компрессия в цилиндрах увеличилась до 25-27 кгс/см2. Через 5 месяцев эксплуатации был произведен замер компрессии в цилиндрах двигателя. Во всех цилиндрах значение компрессии было 28-29 кгс/см2 и автомобиль эксплуатировался в течение года без какого-либо ремонта двигателя.
Пример 3.
Вданном примере состав использовался в виде 3%-ной суспензии в смазочном масле – нигрол.
Покрытие было испытано на локомотивах серии ВЛ-23 в зубчатых передачах тяговых электродвигателей НБ-406.
Впервой тележке электровоза была заменена стандартная смазка (нигрол) зубчатых передач тяговых двигателей на смесь с составом НИОД, вторая продолжала работать с использованием штатного нигрола. После 8 час обкатки электровоза смесь из зубчатых передач первой тележки была удалена и машина была отдана в эксплуатацию без каких-либо ограничений. При техническом осмотре локомотива во второй тележке производилась дозаправка по 1,5 кг нигрола в каждый кожух зубчатой передачи, первая тележка эксплуатировалась без последующего добавления нигрола. Электровоз использовался на вывозной работе: средний вес поездов 2500-3200 т, максимальный вес поезда 4500 т, количество вагонов 56-60. Профиль участка равнинный.
Через 3 месяца эксплуатации был произведен визуальный осмотр зубчатых передач и произведены замеры. Состояние зубчатых передач экспериментальной первой тележки явно улучшилось: на поверхности зубьев образовался блестящий, скользкий слой. На зубьях в месте пятна контакта были предприняты попытки нанести царапины резцом с наплавкой из твердого сплава. На зубчатых передачах второй тележки царапины оставались, на первой (обработанной) тележке нанести царапины не удавалось.
Пример 4.
vk.com/club152685050 | vk.com/id446425943
В качестве носителя триботехнического состава НИОД использовалось смазочное масло ТАД-17И. Обработка была проведена среднего и заднего мостов автомобиля Татра-815 С-1. Через 6 часов обкатки (пробег автомобиля составил 190 км) остатки смеси были удалены и в дальнейшем автомобиль эксплуатировался при полном отсутствии каких-либо смазок в испытуемых узлах (на сухую). Наработал 17561 км пробега без замечаний и поломок.
НАУКА ДАЕТ ДОБРО!
Уникальные свойства состава НИОД подтверждены заключениями ряда научно - исследовательских институтов, в том числе: ВНИИХИММАШ, НИИТЯЖМАШ, ВНИИАТ, ВНИИЖТ, НИИ им. Менделеева, а также исследованиями: предприятий «Русский Дизель», ЗАО НПК «Завод им. Шаумяна», ОАО «Уралмаш» и многочисленными ведомственными лабораториями. Вот некоторые из них:
НИИТЯЖМАШ
Опыт применения ТС НИОД-2 специалистами ОАО «Уралмаш» на выпускаемом оборудовании (машины непрерывного литья заготовок) и других объектах подтвердил целесообразность применения ТС для приработки нового оборудования и без разборного увеличения ресурса оборудования, бывшего в эксплуатации. Эффективность ТС была проверена при экстремальных условиях с целью сокращения сроков испытаний.
В ходе лабораторных и натурных испытаний установлено: происходит модификация поверхностей трения (физико-химические изменения поверхностных слоев, в некоторых случаях, вплоть до образования пленочных покрытий толщиной 1-2 мкм и Rа до 0,12-0,15 мкм), обеспечивающих снижение износа и потерь на трение; коэффициенты трения после модификации поверхностей были измерены на специальном стенде (линейная скорость – 0,03 м/с, давление 150 кг/см2, смазка ЦИАТИМ-201) для пары сталь-бронза и были ниже в 1,4 – 1,8 раза коэффициентов трения без модификации.
ВНИИ ХИММАШ
На стендах института, имитирующих работу узлов трения, в том числе, подшипников скольжения, зубчатых колес редукторов, торцевых уплотнений, сальниковых набивок и т.п., изучены антифрикционные свойства пар трения.
Исследования показали, что при трении в интервале давления от 5 до 1000 кг/см2 в присутствии в масле НИОД происходит снижение в 1,5-2 раза скорости изнашивания, уменьшение приблизительно в 10 раз значения коэффициента трения.
vk.com/club152685050 | vk.com/id446425943
При этом на поверхности стали, проработавшей в масле с составом НИОД, отсутствуют следы схватывания даже при давлении 1000 кг/см2, в то время как без состава НИОД схватывание поверхности наблюдается при давлении 40 кг/см2.
Проведенные исследования позволили также установить, что после специальной приработки узлов трения в масле с составом НИОД узел трения может работать «всухую» (после слива масла) при нагрузках до 60 кг/см2 и скорости скольжения до 1,8 м/сек.
НИИ РХТУ им Менделеева
Проведением испытаний триботехнических свойств ТС «НИОД» в условиях модельных трибосистем было установлено следующее. Твердость элементов трибосистемы составила: для контр тела – HRC3 50…60, для образца - HRC3 40…50 (сталь по стали). Смазка ЛИТОЛ–24 и ЛИТОЛ-24+НИОД. Интенсивность изнашивания образцов с НИОД ≈ 0,0037 мг/м, образцов (без НИОД) ≈ 0,023 мг/м. Интенсивность изнашивания необработанных ТС НИОД образцов в 6 раз выше, чем у обработанных
Фирма «Русский дизель»
При определении эффективности состава НИОД в условиях моделирования работы триады трения: хромированное кольцо – смазка – чугунная гильза, на машине трения СМЦ-2 было установлено следующее: Испытания на смазке без НИОД показали, что стабилизация режима трения наступает после 1-го часа работы.
Температура в контакте достигает 3000С в начале испытаний и снижается до 2750С в конце, момент трения, соответственно: 35-37 кгс. мм и 35 кгс.мм.
Ввод в смазку НИОД-5 заметно меняет режим работы пары трения. На первом этапе НИОД-5 способствует интенсификации износов образцов. Износ возрастает в 1,5 – 1,8 раза. Возрастает температура и момент трения. Однако это наблюдается до определенного времени. После изменения условий работы образцов (через 2-4 часа) НИОД-5 проявляет себя как высокоэффективная и противоизносная присадка.
Наблюдается резкое снижение не только износа, но и температуры и момента трения после появления эффекта (температура снижается с 310 до 650С, момент трения – с 37 кгс.мм до 2-4 кгс.мм, коэффициент трения – с
0,1675-0,250 до 0,01-0,05).
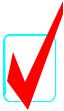
vk.com/club152685050 | vk.com/id446425943
Химико-Технологическая лаборатория Управления Северо-Кавказской железной Дороги
При определении влияния обработки ТС НИОД на микротвердость поверхностных слоев пар трения на примере пары: бандажная сталь - рельсовая сталь было установлено, что в результате испытаний микротвердость, испытанная на приборе ПМТ-3, поверхностного слоя образца из бандажной стали на участке формирования покрытия составила Hμ=330-376 кгс/мм2 (до обработки – 272-285 кгс/мм2), рельсовой стали: Hμ=424-446 кгс/мм2 (до обработки 376-386 кгс/мм2), т.е. твердость образцов возросла: образец из бандажной стали – на 31%; образец из рельсовой стали - на 19,8%.
Уральский университет инженеров железнодорожного транспорта
На стационарной машине трения СМТ-1 испытали несколько пар трения: необработанную ТС НИОД со смазкой ТАД-17И; обработанную со смазкой ТАД17И; пару трения обработанную ТС без смазки. Нагрузки изменяли от минимальной до запредельной (от 135 до 4500 кгс/мм2). Твердость измеряли на твердомере ПМТ-3. Металлографическое исследование проводили на оптическом микроскопе.
Во всем диапазоне рабочих нагрузок (от 145 до 2300 кгс/мм2 и более) отмечено позитивное влияние состава НИОД как на время приработки пар трения и уменьшение температуры образцов и момента трения, так и на изменение микроструктуры поверхностного слоя и триботехнические качества поверхности. Обработанные поверхности эффективно удерживают смазку в зоне трения.
НИОД РАБОТАЕТ!!!
Результаты практических испытаний на сотнях предприятий в различных отраслях промышленности, на тысячах агрегатах и механизмов в разнообразных узлах трения убедительно показывают, что даже разовая обработка пар трения триботехническими составами «НИОД» увеличивает их сроки эксплуатации в 2 и более раз. Помимо увеличения сроков эксплуатации оборудования, снижения уровня шума, потребления электрической энергии (5 –15%) удалось решить много конкретных практических задач.
Машиностроение и металлургия
На АО «Кузнецкий металлургический комбинат» обработано 69 единиц оборудования, в т.ч. 884 различных узлов трения. Все редукторы, обработанные
vk.com/club152685050 | vk.com/id446425943
ТС НИОД, работают в «сухом» режиме. За три года эксплуатации экономия только по смазке составила 1,8 млн. руб. (деноминированных).
Обработаны 16 редукторов хода и подъема различного кранового оборудования, барабанные шестерни скипового подъема, шестерни трансмиссии стана 900 и стана 450, редуктор вращения кабины ж/д крана, печные рольганги (подшипники качения в роликах), редукторы группового привода ребристых роликов, редукторы привода стационарных роликов, зубчатые муфты листоправильных машин и главного привода чистовой клети, подшипники опорных роликов листоправильной машины, червячные редукторы и подшипники закалочной печи, ролики опускной печи, редуктор двойного рольганга перед 1-ым подъемным столом, рольганг подъемного стола стана 360 подводящий рольганг стана 759, ШПС - редукторы привода нагрева печи и несколько единиц автотранспорта.
Все обработанные узлы трения даже в «сухом» режиме показывают надежную их работу, а отсутствие масла в редукторах во многих случаях повышает пожаробезопасность при эксплуатации оборудования.
На ОАО «Уралмаш» практические результаты применения ТС НИОД получены на различных видах оборудования, например:
1.Редукторы машин непрерывного литья.
Обработке было подвергнуто 9 планетарных редукторов рольгангов машин непрерывного литья заготовок:
-три редуктора для Ново-Липецкого металлургического комбината;
-шесть редукторов для Магнитогорского металлургического комбината. Кроме того, было обработано 10 цилиндрических редукторов приводов
роликов рольгангов для этого же комбината.
Обработка планетарных редукторов производилась в масле И-50А с добавками на 1 литр масла 30 гр. НИОД-2 и антикоррозийной присадки «Акор»-
150 гр.
При штатной нагрузке и частоте вращения быстроходного вала 900 мин-1 в течение 12-15 мин. прослушивался шум передач, после 30-35 мин. работы шум снижался до нормативных значений, и обкатка прекращалась. Пятно контакта по длине и высоте зуба составляло100% и имело зеркальный вид. Аналогичные результаты были получены при обработке цилиндрических редукторов. В течение двух лет все редукторы находятся в эксплуатации. Замечаний по их работе не имеется.
2.Механизм подъема тележки промковшей машины непрерывного литья.
При контрольных испытаниях механизм подъема тележки промковша под нагрузкой 85т. (согласно техническим требованиям разработчика) не срабатывал на заданной высоте подъема с предельной величиной токовой
vk.com/club152685050 | vk.com/id446425943
нагрузки 300 А. Кинематическая схема механизма включала две гайки, в которых вращались винты от индивидуальной червячной глобоидной пары. Перемещение винтов обеспечивало подъем промковша. Такой схеме механизма присущи большие потери энергии на трение. Масло И-100Р/с/ в корпусах глобоидных пар оказалось в данном случае не эффективным. Требовалось кардинальное снижение коэффициента трения при обкатке, хотя бы в доступных оперативно для этого парах трения, таких как глобоидные.
С этой целью поверхности трения глобоидных пар были покрыты в доступных местах консистентной смесью (Литол-24-200гр. + НИОД-2 -30гр.). Уровень жидкой смазки в картерах был понижен, чтобы не смывать смесь с глобоидных пар. Затем произведена приработка глобоидных пар под нагрузкой 55т. путем пятикратного подъема и опускания груза на заданную высоту. После этой приработки был увеличен груз до 85т., а уровень смазки в картерах глобоидных передач – до проектного. Трехкратный подъем, и опускание груза удалось произвести без каких-либо осложнений, с первой попытки. При этом ток двигателя не превышал 200 А. Приемной комиссией было дано разрешение на отгрузку оборудования заказчику в установленные контрактом сроки.
3. Горнопроходческий комплекс «ВИРТ»
Проходка тоннеля метро в г. Екатеринбурге осуществляется с помощью горнопроходческого комплекса /ГПК/ «ВИРТ». При плановом обследовании состояния зубчатого зацепления редуктора главного подшипника ГПК обнаружился интенсивный износ зубьев солнечной шестерни (внутреннее зацепление, модуль-16 мм, кол-во зубьев – 151, твердость – 260 275 НВ, смазка ИРП-150, угловая скорость-2,8 мин-1). Средняя интенсивность износа за время проходки составила 0,0123 мм/м. Толщина зуба на расстоянии 15 мм от вершины составила 13,7мм (50% от номинальной расчетной).
На запрос ОАО «Свердметростроя» специалисты ОАО «Уралмаш» рекомендовали применить обработку зубчатых колес редуктора ТС НИОД-2, опираясь на свой опыт обработки этим составом колес с низкой твердостью. Следует отметить, что до случая с износом зубьев ГПК обработка ТС производилась только зубьев с высокой твердостью. Впервые не упрочненные зубья обрабатывались на стенде зубчатых передач, где и был выявлен положительный эффект обработки.
Специфика работы редуктора ГПК (низкие угловая скорость солнечной шестерни – 2,8 мин-1 и суточный коэффициент технического использования – 0,2), а также большие объемы смазки в картере /до 450 л/ требовали разработки особых условий процесса обработки во избежание больших потерь НИОД-2 из-за седиментации /осаждения/ при остановках.
По регламенту обработки смесь масла ИРП-150 и ТС НИОД-2 (в соотношении 15 г/л) в течение 2-х месяцев выполняла роль смазки редуктора
vk.com/club152685050 | vk.com/id446425943
главного подшипника. В этот период солнечная шестерня непрерывно вращалась в реверсивном режиме не только при технологической нагрузке /режим проходки/, но и на холостом ходу. За два месяца работы ГПК износ практически не был обнаружен. Толщина зуба на расстоянии 15 мм осталась прежней 13,7 мм, по длине зубьев образовались две зоны зеркальной поверхности /покрытия/, вверху и внизу от полюса зацепления по высоте зуба. После замены смеси на чистое масло редуктор проработал 1,5 месяца. За этот период износ проявился вновь, и толщина зуба уменьшилась до 12.75 мм. Поэтому чистое масло было вновь заменено на смесь ТС НИОД-2, которая не менялась в последующие два месяца. Средняя интенсивность износа с момента применения НИОД-2 уменьшилась в пять раз и составила 0,0024 мм/м. Проходка тоннеля составила более 2 км после начала применения ТС и продолжается в настоящее время.
4.Шарико-винтовая пара вальце шлифовального станка.
Обработка ТС винта шарико-винтовой пары поперечной подачи суппорта станка была выполнена по острой производственной необходимости: вновь изготовленный винт взамен штатного отработавшего свой ресурс, оказался забракованным по твердости (45-47 HRC вместо 55-60 HRC). Параметры винта: длина - 1400 мм, диаметр – 60 мм, шаг ходовой резьбы 6 мм. Винт в паре с гайкой специальной конструкции (две гайки, между которыми встроены тарельчатые пружины, диаметр шариков - 3 мм) прирабатывался на токарном станке в течение 6 часов в реверсивном режиме при 120 об/мин. Усилие на обе стороны резьбы создавалось тарельчатыми пружинами и составляло 85-90 кг. Во время приработки винт смазывался хорошо перемешанной смесью густой смазки и ТС в соотношении 95% ЦИАТИМ-201 и 5% НИОД-2.
Обработка была прекращена после падения температуры винта с 80 С до 40 С. На резьбе после обработки отчетливо просматривались дорожки качения. Срок службы винта составил 4 года 4 месяца. Ресурс винта мог быть выше, однако из-за неисправности смазочной системы неопределенное время винтовая пара работала без смазки.
На Абагурской аглофабрике Кемеровской обл. обработано 36 единиц оборудования. В марте 1994 г. обработана пара М16 Z1=274 и Z2=31 шаровой мельницы 2700х3600. Зубчатая пара работает до сих пор. Срок службы приводной шестерни увеличен в 3 раза, венцовой – на 20%. Экономический эффект – 65 тыс. руб. (деноминированных). По шаровым мельницам 1,2,3,4,5,10, 15,21,23,24 – эффект – 200,0 тыс. руб.
Вмарте 1995 г. начался обвальный износ зубьев зубчатого венца смесителя
№2 на агломашине №2, а запасной венец не был еще получен из Орска. После обработки он проработал 6 месяцев (до поступления нового венца). Была предотвращена остановка агломашины №2, что привело бы к огромным потерям.
vk.com/club152685050 | vk.com/id446425943
Обработаны привод агломашины № 8, редукторы крана - перегружателя, редукторы конвейеров и т.п., что дало ощутимый эффект и позволило удлинить сроки службы уникального оборудования.
Объекты РАО ЕЭС России
На Нерюнгринской ГРЭС (республика Саха-Якутия, г. Нерюнгри) обработано 384 единицы различного оборудования, в том числе, 203 редуктора, 96 насосов, 85 единиц станков, компрессоров и отдельных узлов механизмов.
60 редукторов после обработки ТС НИОД длительное время работали в «сухом» режиме, в том числе:
-с 1994 года25 шт. насос - дозаторов плунжерного типа (НД). Работают по настоящее время. Повторная обработка произведена в 1999 году. Износ бронзовых деталей, даже в «сухом» режиме уменьшился в 4 раза. Экономия электроэнергии (снижение) – на 8-11%;
-редукторы дробилок ШШУ (РДЦ-400) шнеков шлакоудаления – 27 шт. с 1993 –94 гг., масло залито в 1997 году. Износа нет;
-редуктор привода скрепковой цепи ПСУ-1л – 4 месяца;
-редукторы качающих питателей РМ350 – 5 шт. – 1 год 2 месяца;
-редукторы привода ленточных питателей вагон опрокидывателя КЦ–1- 250 – 2 шт. – 2 месяца;
-обработка компрессоров привела к увеличению их производительности на 25%. Обработка, токарных станков привела к снижению потребления электроэнергии на 14%;
-по насосам значительно увеличился ресурс подшипников – в 2 и более раз,
то же – по электродвигателям.
Экономический эффект от внедрения только за первые 2 года составил 595,0 тыс. руб. (в ценах деноминированных) при семикратной окупаемости затрат.
На Новорязанской ТЭЦ в 1997-1998 г.г. обработано 12 нижних подшипниковых узлов РВП, которые эксплуатировались на жидкой смазке МС-20. Система смазки - циркуляционная, принудительная, с масло станциями на каждые 2 РВП. Средняя температура эксплуатации 70-780С (выведена на щит).
После обработки станции отключены, подшипники запущены на консистентной смазке с маслом в стакане 80 л. Температура эксплуатации 45-66 0С. За 4 года эксплуатации из строя вышел один подшипник по причине просевшего фундамента.
На Новосибирской ТЭЦ-5 обработано 138 единиц оборудования, в т.ч. 96 редукторов и 42 отдельных подшипниковых узла, сальниковых и полумуфт, в т.ч. нижних подшипниковых узлов РВП. 4 единицы редукторов работали в «сухом»