
НЕФТЬ И ГАЗ-1
.pdf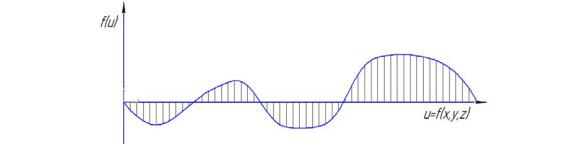
vk.com/club152685050 | vk.com/id446425943
На рис. 2 под цифрами обозначены: 1 – входные сигналы от органов управления и диагностики механообрабатывающего оборудования; 2 – сумматор входных сигналов; 3 – вычислитель передаточной функции; 4 – выходные сигналы.
Нейроны, в основном, классифицируют на основе их положения в топологии сети и разделяют на входные, выходные и промежуточные. Выходные нейроны — представляют из себя выходы сети, в которых производятся какие-либо вычислительные операции. Промежуточные нейроны — выполняют основные вычислительные операции [4]. Применительно к рассматриваемым условиям обработки на станках с ЧПУ зависимости (1,2) целесообразно использовать для определения единственно возможного выходного параметра через его входы, которые представляются в виде
|
y f u , |
(1) |
|
n |
|
|
u i xi 0 x0 , |
(2) |
где: i |
i 1 |
|
— сигналы на входе нейрона, |
|
|
xi |
— вес входа, |
|
u |
— функция или индуцированное локальное поле, |
|
f u |
— передаточная функция. |
|
Определение передаточной функции позволяет получить зависимость сигнала на выходе нейрона от взвешенной суммы сигналов на его входах. В большинстве случаев она является монотонно возрастающей и имеет область значений [-1,1] или [0,1]. Искусственный нейрон полностью характеризуется своей передаточной функцией. Использование различных передаточных функций вносит нелинейность в работу нейросетевой модели, что позволяет определять погрешности, возникающие при механической обработке на станках с ЧПУ. На рис. 3 приведена непараметрическая кривая погрешностей механообработки.
Рис. 3. Непараметрическая кривая погрешностей механообработки
Представленная на рис. 3 кривая на отдельных участках описывается различными зависимостями, которые могут быть представлены математическими уравнениями линейной функции. Таким образом, если уменьшить
56

vk.com/club152685050 | vk.com/id446425943
частоту дискретизации, то можно воспользоваться линейной передаточной функцией нейросетевой модели (формула 3).
f x tx , |
(3) |
где t – параметр функции.
Вискусственных нейронных сетях со слоистой структурой нейроны
слинейной передаточной функцией, составляют входной слой. Кроме простой линейной функции могут быть использованы ее модификации. Например: полулинейная функция [7] или шаговая (линейная функция с насыщением), может быть представлена в виде (4)
|
|
x 0 |
|
|
|
0 if |
|
|
|
f x |
1 if |
x 0 |
|
|
|
|
|
|
|
|
|
|
, |
(4) |
|
x else |
|
|
|
|
|
|
|
|
При этом сдвиг функции (в рассматриваемом варианте – коррекция траектории перемещения исполнительного рабочего органа станка с ЧПУ) возможен по обеим осям. Недостатками шаговой и полулинейной активационных функций относительно линейной можно назвать то, что они не являются дифференцируемыми на всей числовой оси, и, следовательно, не могут быть использованы при обучении нейронной сети по некоторым алгоритмам [8].
Таким образом, проведенный анализ и обоснование позволяют сделать заключение о возможности и целесообразности реализации нейросетевого подхода при проектировании системы диагностики и оперативного управления процессами обработки на станках с ЧПУ.
Список литературы
1.Дьяконов В.П, Круглов В.В. MATLAB 6.5 SP1/7/7 SP 1/7 SP2 Simulink 5/6.
Инструменты искусственного интеллекта и биоинформатики. М: СОЛОН-ПРЕСС, 2006. – 456 с.: ил.
2.Геометрические параметры и модель разрушений режущего лезвия инструмента Силич А.А., Утешев М.Х., Некрасов Р.Ю., Путилова У.С., Некрасов Ю.И. // Известия высших учебных заведений. Нефть и газ. 2012. № 2. С. 108-113.
3.Капалин В.И., Прокопов Б.И. Методы идентификации. М. МИЭМ. 1998.-89с.
4.Круглов В. В., Борисов В. В. — Искусственные нейронные сети. Теория и практика. М.: Горячая линия – Телеком, 2002. — 284 с.
5.Проскуряков Н.А. Разработка интегрированной системы диагностики и управления процессами обработки на токарных станках / Дисс. на соиск. учен. степ.
к.т.н. // Тюмень. 2005. – 302 с.
6.Пупков К.А., Капалин В.И., Ющенко А.С. Функциональные ряды теории нелинейных систем. М: Наука, 1976. – 448 с.: ил.
7.Терехов В. А. — Нейросетевые системы управления. М.: "Высшая школа", 2002. - 183 с. [10]
8.Усков А.А., Кузьмин А.В. Интеллектуальные технологии управления. Искусственные нейронные сети и нечеткая логика. М.: Горячая линия -Телеком, 2004. – 143 с.
57
vk.com/club152685050 | vk.com/id446425943
УДК 621.9.02.01
СОВРЕМЕННОЕ СОСТОЯНИЕ ОПРЕДЕЛЕНИЯ УСЛОВИЙ РАБОТОСПОСОБНОСТИ РЕЖУЩЕГО ИНСТРУМЕНТА ИЗ ИНСТРУМЕНТАЛЬНЫХ ТВЕРДЫХ СПЛАВОВ
Д. С. Альмагамбетова, Н. О. Позднякова, О. В. Сырцева
г. Тюмень, Тюменский государственный нефтегазовый университет
Всовременных условиях эффективность производственной деятельности предприятий машиностроения в значительной мере определяется использованием современной инструментальной и технологической оснастки, важнейшим элементом которой является режущий инструмент. В конструкциях режущего инструмента все более широкое распространение приобрело механическое крепление сменных многогранных пластин (СМП) из различных инструментальных материалов, чаще из металлокерамического инструментального твердого сплава, так как не требует пайки
изаточки, исключает появление микротрещин, создает благоприятные предпосылки для унификации, использования стандартных узлов и элементов, способствует повышению производительности обработки, а также росту экономической эффективности процессов металлообработки.
Существует большое количество практических рекомендаций в инструментальных каталогах и справочниках по применению сборного режущего инструмента, однако до сих пор не разработаны инженерные методики выбора и расчета СМП, направленные на повышение прочности и работоспособности.
Принципиально новый подход для решения этой проблемы стал возможным с появлением мощных программных комплексов на основе метода конечных элементов. Поэтому повышение эффективности применения сборного инструмента на основе исследования напряженнодеформированного состояния и прочности СМП при механической обработке путем создания инженерного метода расчета основных параметров СМП на основе «прочностного подхода» и определение условий их «максимальной работоспособности», является актуальной проблемой [1].
Вработе Е.В. Артамонова, А.Ю. Свиридова, М.Ю. Чернышова «Проблемы прочности и работоспособности сборных сверл» [2] установлены основные причины, определяющие характер разрушения и износа режущих элементов таких инструментов:
1) высокие силовые и температурные нагрузки;
2) износостойкость и прочность твердого сплава;
3) неоптимальные геометрические и конструктивные параметры. Анализ работы [2] позволяет сделать вывод о том, что оптимизиро-
вать конструктивные, геометрические параметры и условия нагружения
58
vk.com/club152685050 | vk.com/id446425943
режущих элементов из твердых сплавов, необходимо на основе исследования их напряженно-деформированного состояния.
При использовании инструмента с СМП одной из немаловажных становится проблема выбора конструктивных и геометрических параметров пластин. При обработке напайным инструментом его параметры необходимо довести до нужной геометрии с использованием заточки, что неприменимо при обработке сборным инструментом с СМП.
Всвязи с разнообразием форм изготавливаемых деталей возникает необходимость классифицировать их по какому-либо признаку. Для этого обработка «разбивается» на отдельные переходы, а затем выбирается пластина. Основные типы пластин различают по четырем конструктивным признакам: по числу рабочих граней, по форме передней грани, с отверстием и без отверстия, с задним углом, большим или равным нулю. При выборе формы передней поверхности режущей пластины необходимо учитывать с одной стороны получение оптимальных значений переднего угла режущего лезвия, переднего угла на фаске и ширины фаски, обеспечивающих высокую износостойкость, прочность и виброустойчивость инструмента, а с другой – гарантирование дробления стружки при данных условиях обработки [1].
Вработе Е. В. Артамонова, В. В. Киреева «Напряженнодеформированное состояние сменной режущей пластины червячной фрезы» [3] для анализа процесса фрезерования червяной фрезой в системе «Компас-3D» было графически промоделировано движение заготовки и червяной фрезы и построены контуры режущих кромок зубьев червячной фрезы. При исследовании влияние какого-либо параметра СМП на их на- пряженно-деформированное состояние сравнивались величины и характер распределения главных напряжений 1 , полученные при расчете конечно-
элементных моделей СМП.
Граничные силовые характеристики авторы определяли по методике профессора Ю. А. Розенберга, что позволило исследовать напряженнодеформированное состояние СМП с использованием графического определения «пятна контакта», и определять НДС пластины в любой момент фрезерования [3]. Таким образом, была разработана методика определения НДС пластин в зависимости от «пятна контакта» по передней поверхности зуба сборной фрезы для обработки зубчатых колес.
По данным авторов, неточный подбор марки инструментального твердого сплава (ИТС) также является причиной разрушения и износа режущих элементов. В настоящее время ИТС выбирают исходя из данных справочных таблиц или рекомендаций заводов изготовителей ИТС. Однако, по этим источникам для конкретного обрабатываемого материала трудно подобрать подходящую марку ИТС, так как рекомендации общие и предлагается несколько марок твердых сплавов, а следует выбор одного материала.
59
vk.com/club152685050 | vk.com/id446425943
Вработе Е.В. Артамонова, Д.С. Василеги, А. М. Тверякова «Диаграмма выбора инструментального твердого сплава по обрабатываемому материалу» предложена «модель выбора ИТС» по обрабатываемому материалу для конкретных условий с учетом характеристик как инструментального, так и обрабатываемого материалов.
По Е. В. Артамонову «температура максимальной работоспособности» твердого сплава определяется по его физико-механическим характеристикам [4] и она является «оптимальной с точки зрения ИТС». Температура «максимальной обрабатываемости», определяется по механическим характеристикам обрабатываемого материала [5] и является «оптимальной
сточки зрения обрабатываемого материала», что соответствует условиям «максимальной обрабатываемости». Следовательно, по данным авторов, «идеальным» будет вариант совпадения этих температур и из этого условия, очевидно, следует производить выбор ИТС.
Это условие было положено в основу модели выбора ИТС по физи- ко-механическим характеристикам инструментального и обрабатываемого материалов. Предложенная модель хороша еще тем, что помимо выбора марки ИТС, определена и температура, при которой необходимо производить обработку данного материала. А по известной температуре, подобрать режимы резания «не составляет большого труда» [6].
Вработе Е.В. Артамонова, Д.С. Васильева «Определение рациональных режимов резания по виду стружки» указано, что данные справочной литературы «не позволяют в полной мере определить» режимы резания для материалов новых марок. Несмотря на их «одинаковые физические характеристики», в процессе резания обрабатываемые материалы ведут себя совершенно по-разному. Для определения оптимальных режимов резания и условий «максимальной работоспособности инструментов» необходимы трудоемкие и дорогостоящие стойкостные лабораторные испытания, что ведет к существенным финансовым затратам, а также к потере времени.
Авторами были «спроектированы и собраны» несколько экспериментальных установок, с помощью которых был проведен ряд лабораторных опытов и разработана экспериментальная методика определения оптимальных режимов резания для новых обрабатываемых и инструментальных материалов. При этом использовалось устройство с «одноинструментальной» естественной термопарой. Исследование проводилось как при «разных режимах резания» (S=0,11; S=0,21 и S=0,52), так и «разных скоростях резания», а «режимные условия формировались» так, чтобы охватить
весь температурно-скоростной диапазон, начиная с температуры 200 С и заканчивая «температурой потери формоустойчивости» режущего клина из
ВК8 - более 9000 С [7].
При анализе данных, полученных Е.В. Артамоновым и Д.С. Василь-
евым, в ходе экспериментов ими прослеживалась «общая закономерность для всех материалов» в зависимости от температурного диапазона:
- температурный диапазон от 200 С до 3000 С - стружка элементная;
60
vk.com/club152685050 | vk.com/id446425943
o температурный диапазон от 3000 С до 4000 С - стружка суставчатая; o температурный диапазон от 4000 С до 5000 С - стружка сливная;
o температурный диапазон от 5000 С до 7000 С - стружка суставчатая; o температурный диапазон свыше 7000 С - стружка элементная [7]. Результаты этих исследований, по мнению авторов, подтверждают «гипотезу» профессора М.Ф. Полетики о «зависимости вида стружки от температурного диапазона», в котором происходит резание металлов, т.е. по виду стружки авторами могут быть определены условия «максимальной
работоспособности» режущего элемента.
В работе Е.В. Артамонова и Д.С. Васильева «О взаимосвязи формы передней поверхности режущей пластины с видом стружки» были изложены результаты исследования зависимости «изменения направления» стружки от геометрии инструмента при обработке материалов резанием. Основной причиной снижения точности обработки и ухудшения шероховатости обрабатываемой поверхности при резании металлов является попадание частиц нароста и обнаруженного авторами «наплыва» под главную и вспомогательную режущие кромки при «традиционных» режимах резания быстрорежущим и твердосплавным инструментом.
Основной тенденцией совершенствования СМП является «универсализация геометрии» с целью расширения диапазона стружкодробления. По-прежнему довольно широко используются режущие пластины со стружкозавивающими канавками, которые выпускаются многими фирмами (Impero, Safety S.A., Mitsubishi и др.). Применяются пластины с двумя и тремя стружечными канавками. Для увеличения деформаций и напряжений в стружке создаются условия для «ее завивания не только в вертикальной, но и в горизонтальной плоскости».
С этой целью изготовляются канавки переменного профиля с изменяющей геометрией вдоль режущей кромки инструмента. Кроме этого на передних поверхностях СМП выполняются различного рода выступы и впадины, «деформирующие стружку в поперечном сечении», что приводит к увеличению ее жесткости и снижению «угла изгиба стружки» для дробления. Таким образом, для успешного дробления стружки следует «правильно направлять стружку», и «угол отклонения» стружки становится «важной характеристикой процесса несвободного резания» [8]. Каждая из кромок «несвободнорежущего элемента» при этом должна работать отдельно без участия «другой кромки», а «образующаяся» стружка будет сходить в плоскости, перпендикулярной к «работающей кромке». На основании проведенных исследований авторами была разработана сменная многогранная твердосплавная пластина с новой формой передней поверхности, обеспечивающей стабильное дробление стружки для обработки деталей из жаропрочных сталей и сплавов.
Как указывают авторы, температурный фактор играет важную роль при обработке материала. Например, при изготовлении деталей нефтегазопромыслового оборудования, возникает необходимость применения высо-
61
vk.com/club152685050 | vk.com/id446425943
копрочных коррозионностойких материалов. Как правило, эти материалы относятся к разряду труднообрабатываемых, т.е. при обработке фрезерованием данных материалов возникают большие температуры в режущей части инструмента, которые, главным образом, определяют его работоспособность.
Режущая кромка, в начальный период фрезерования «находится в хрупком состоянии», а это неблагоприятно влияет на работу инструмента, так как в начальный период времени идет процесс приработки, сопровождающийся интенсивным износом режущего клина. Предварительный подогрев режущей части позволяет повысить работоспособность металлорежущего инструмента. Это объясняется «выводом» инструментального твердого сплава «из хрупкого» в «хрупко-пластическое состояние», что позволяет инструменту работать с гораздо большими нагрузками. Эффективность способа достигается возможностью регулирования температуры предварительного подогрева для каждого используемого инструментального материала [9].
В работе Е.В. Артамонова, С.С. Чуйкова, Р.С. Чуйкова «Установка для регулируемого подогрева твердосплавной режущей пластины» приведено описание разработанной ими новой конструкции металлорежущего инструмента, обеспечивающей «повышение работоспособности» путем предварительного подогрева сменной твердосплавной пластины сборного инструмента. Конструкция является полностью авторской работой, что подтверждено подачей заявки на получение патента на полезную модель.
Таким образом, в результате проведенного анализа показано, что на сегодняшний день определение «условий максимальной работоспособности режущих элементов» является не исчерпанным. Универсальной методики определения «условий максимальной работоспособности» и прочности режущего инструмента нет, поэтому повышение эффективности работы сборных режущих инструментов на стадии проектирования и эксплуатации является актуальной проблемой производства и научных исследований.
Список литературы
1.Артамонов Е.В., Помигалова Т.Е., Тверяков А.М., Утешев М.Х Механика разрушения и прочность сменных режущих пластин из твердых сплавов / под общ. ред. М.Х. Утешева.- Тюмень: ТюмГНГУ, 2013.- 148 с.
2.Артамонов Е.В., Свирид А.Ю., Чернышов М.О. Проблемы прочности и работоспособности сборных сверл / Новые материалы,неразрушающий контроль и наукоемкие технологии в машиностроении: материалы VI научно-технической интернетконференции с международным участием . - Тюмень: ТюмГНГУ, 2012- С. 3 -7.
3.Артамонов Е.В., Киреев В.В. Напряженно-деформированное состояние сменной режущей пластины червячной фрезы: / Новые материалы, неразрушающий контроль и наукоемкие технологии в машиностроении: материалы VI научнотехнической интернет-конференции с международным участием . - Тюмень: ТюмГН-
ГУ, 2012- С.7-11.
62
vk.com/club152685050 | vk.com/id446425943
4.Патент РФ №2373-29, МПК В23В1/00. Способ определения температуры максимальной работоспособности твердосплавных режущих пластин. [Текст] : Е.В.
Артамонов, В.Н. Кусков, Д.С. Василега (РФ).- №2008101015/02; Заявл. 09.01.2008,
Бюл.№32.
5.Артамонов Е.В. Работоспособность инструментов и физико-механические характеристики инструментальных твердых сплавов и обрабатываемых материалов. [Текст] монография / Е.В. Артамонов, Д.С. Василега, М.С. Остапенко, В.А. Шрайнер.- Тюмень: «Вектор Бук», 2008.-160с.
6.Артамонов Е.В., Василега Д.С., Тверяков А.М. Диаграмма выбора инструментального твердого сплава по обрабатываемому материалу: / Новые материалы, неразрушающий контроль и наукоемкие технологии в машиностроении: материалы VI научно-технической интернет-конференции с международным участием . - Тюмень:
ТюмГНГУ, 2012- С. 11-13.
7.Артамонов Е.В., Васильев Д.С. Определение рациональных режимов резания по виду стружки: / Новые материалы, неразрушающий контроль и наукоемкие технологии в машиностроении: материалы VI научно-технической интернет-конференции
смеждународным участием . - Тюмень: ТюмГНГУ, 2012- С.13 -17.
8.Артамонов Е.В., Васильев Д.В. О взаимосвязи передней поверхности режущей пластины с видом стружки: / Новые материалы, неразрушающий контроль и наукоемкие технологии в машиностроении: материалы VI научно-технической интернетконференции с международным участием . - Тюмень: ТюмГНГУ,2012- С. 48-53.
9.Артамонов Е.В. Прочность и работоспособность сменных твердосплавных пластин сборных режущих инструментов / Монография. – Тюмень: ТюмГНГУ, 2003.- 192 с.
УДК 681.786
ИСПОЛЬЗОВАНИЕМ МЕТОДА ЛАЗЕРНОЙ ДИФРАКТОМЕТРИИ ДЛЯ КОНТРОЛЯ МАЛОРАЗМЕРНЫХ ОБЪЕКТОВ
О. В. Сырцева, М. Х. Утешев, Р. Ю. Некрасов, Д. С. Альмагамбетова
г. Тюмень, Тюменский государственный нефтегазовый университет
Для улучшения качества изделий в машиностроении, приборостроении, и других отраслей промышленности в условиях современного наукоемкого производства и быстроменяющегося спроса необходимо освоение новых, эффективных технологий измерения и контроля. Новые технологии должны обеспечивать точность, надежность, высокую скорость проведения работ. В связи с быстроменяющимися потребностями в продукции эти приборы и устройства должны быть недорогими и компактными. Способность к созданию измерительных, контрольных аппаратов и приборов небольших размеров – также является большим преимуществом. На сегодняшний день все большее развитие получают бесконтактные методы измерения (например, оптические) и на второй план отходят такие известные методы как радиотехнические, теневые, емкостные и др.
Вопросом производства оптических измерителей занимались в России и за рубежом. Так еще в 1966 году М. Коедам [1]создал простейшую
63
vk.com/club152685050 | vk.com/id446425943
схему, измерительного устройства, построенного использовании гелийнеонового лазера для контроля диаметров прямых и спиральных нитей диаметром 0,005-0,5 мм. Позже, английской фирмой был разработан оптический дифракционный сумматор для измерения тонких проволочек методом сравнения с эталонной проволокой [2]. Для относительных дифракционных измерений в Швеции в 1968 г. было разработано устройство, состоящее из лазера, объекта измерения, экрана и двух детекторов, соединенных по мостовой схеме, в диагональ которой, включен нуль-прибор [3]. По аналогичной схеме в 1969 году польским институтом электронной технологии была разработана установка для измерения диаметров проволок [4]. Французским институтом топлива и смазочных материалов в 1966 году была разработана установка с визуальным отсчетом [5]. Для уменьшения размеров дифракционного изображения, введена линза, которая собирает дифрагированные на объекте лучи в фокальной плоскости. Установка позволяла измерять проволочки диаметром 0,005-0,5мм с погрешностью измерения 0,5%.
В 1969 году в США Ф. Гадлино, Р. Ламлей, Л. Воткино предложили два метода регистрации дифракционной картины с применением видикона или решетки фотодиодов, что повысило точность регистрации до 0,3%. Для улучшения качества дифракционной картины Л. А. Диеффера [6] ввел
всхему длиннофокусную линзу расширяющую пучок. При помещении измеряемого объекта в середину пучка, улучшается качество дифракционной картины, так как при этом используется только однородная центральная часть пучка. В 1969 году была предложена Д.К. Коопером коллиматорная схема, состоящая из коллиматора и зрительной трубы с источником света - оптическим квантовым генератором (ОКГ) . Объект измерения помещается
впараллельный пучок. Дифракционная картина, наблюдаемая в фокальной плоскости объектива зрительной трубы, регистрируется измерением фототока от фотоэлемента.
Исследованием возможности создания прибора для контроля малых диаметром на базе ОКГ (лазера) занимался Макаренко В. В. в Омском политехническом институте [8], в Московском станкоинструментальном институте велись работы по измерению ширины лент [6,7], в Ленинграде Митрофанов А. С. и Тарлыков В. А. занимались вопросами использования дифракции лазерного луча для точного измерения тонких волокон [9].
Приведенные выше данные, о научных разработках многих ученых, не могут в полной мере удовлетворять требования, предъявляемые к измерительным приборам. Таким образом, можно сделать вывод, о необходимости проведения экспериментальных исследований измерения малых размеров.
На основе теоретических и экспериментальных исследований ставится задача разработать полуавтомат для измерения проволочек и отверстий малых диаметров.
64
vk.com/club152685050 | vk.com/id446425943
Появление оптических квантовых генераторов (лазеров) позволило широко использовать явление дифракции света при оптических методах измерения линейных размеров. Обладая мощным, интенсивным излучением и имея стабильный во времени фронт световой волны, лазеры позволяют не только наблюдать, но и регистрировать дифракционную картину.
Явление дифракции света заключается в нарушении законов геометрической оптики, наблюдающееся в местах резкой неоднородности среды и приводящее к отклонению луча света от прямолинейного вблизи, краев непрозрачных и прозрачных тел к огибанию препятствий световыми лучами. Дифракция, обусловлена волновой природой света [10]. Дифракционные задачи, в которых нельзя пренебрегать кривизной волновых поверхностей падающей дифрагировавшие волны, называются дифракцией Френеля. При этом источник света и экран, служащий для наблюдения дифракционной картины, находятся на конечных расстояниях от объекта, вызвавшего дифракцию. Аналитический расчет этих задач обычно труден. Дифракция Фраунгофера или дифракция в параллельных лучах решает задачи, в которых источник света и точка наблюдения бесконечно удалены от объекта, на котором происходит дифракция. Этот вид дифракции обычно рассчитывают аналитически. На основании выше изложенного М. Х. Утешевым и П. В. Серковым и было предложено:
1.Исследовать дифракционные картины, получаемые от малых объектов (проволочек, щелей, дифракционных решеток, отверстий различной геометрической формы).
2.Исследовать возможность применения для дифракционных методов измерения многомодовых лазеров.
3.Провести анализ экспериментальных и теоретических данных. После исследования М. Х. Утешевым, П. В. Серковым и Ю. И. Не-
красовым дифракционных картин, одним из ожидаемых результатов в дальнейшем явилось использование в измерительных дифракционных устройствах многомодовых лазеров. Так же на основе анализа проделанной работы сделан вывод о возможности создания дифракционных приборов для измерения линейных размеров на базе гелий-неонового (He-Ne) лазера. При этом достигается большая точность измерений, чем при использовании дифракционной схемы с неподвижным экраном. Опираясь на полученные результаты в продолжение представленной выше работы были проведены расчеты и исследования, которые позволили авторам сделать вывод о возможности и целесообразности создания полуавтомата для контроля малых объектов дифракционным способом.
Разработанный прибор предназначен для измерения диаметров проволоки и отверстий алмазных волок, по дифракционной картине, получаемой с помощью газового лазера, с цифровой регистрацией расстояния между минимумами дифракционной картины на цифровом табло прибора и графической регистрацией положения минимумов и максимумов освещенности дифракционной картины, получаемой в увеличенном масштабе
65