
НЕФТЬ И ГАЗ-1
.pdfvk.com/club152685050 | vk.com/id446425943
ровать только у новых подшипников, однако, повреждения могут происходить и при маленьких нагрузках, так как шарики и ролики имеют склонность к скольжению вместо качения. В обычных условиях правильно выбранный и правильно эксплуатирующийся подшипник может проработать в течение назначенного срока службы.
Повреждения, возникающие при работе подшипника, могут носить разный характер и иметь разные предпосылки. Внешние причины вызывают большинство преждевременных отказов. К явным причинам внешних повреждений, не компенсируемых самой лучшей подшипниковой сталью, можно отнести плохую смазку, некачественный монтаж, недостатки уплотнения, несоответствующие расчетам условия эксплуатации. По статистике около половины подшипников преждевременно выходят из строя по причине плохой смазки и около трети в результате некачественного монтажа. При этом дефекты в смазке влекут за собой перегрев, что может стать причиной заклинивания, а в предельных ситуациях смазка в подшипнике может даже воспламениться. К повреждениям, связанным с собственно подшипником – не соответствующая качеству подшипниковая сталь, неточная внутренняя геометрия, дефектные сепараторы и уплотнения. Кроме вышеперечисленных причинами выхода из строя подшипников являются усталостное (расслоение) и поверхностное (шелушение) выкрашивания, заедание (заклинивание), оттиски (отпечатки) от деформации, инкрустация инородными частицами, образование дорожек (канавок) на контактирующих поверхностях, надрывы, поверхностное окрашивание, абразивное и адгезивное изнашивания, электрическая точечная и фреттингкоррозии.
В качестве объектов исследования были взяты фрагменты (ролики, сепараторы, обоймы) однорядного роликового упорного подшипника регенеративного подогревателя (РП) с наружным и внутренним диаметром 780 и 440 мм соответственно и двухрядного роликового радиального подшипника дутьевого вентилятора (ДВ) с диаметрами наружным 380 мм и внутренним 180 мм.
С целью выявления причин разрушения обоих подшипников в соответствии со стандартной методологией для всех фрагментов были проведены визуальный осмотр для определения характера повреждений, механические испытания, определен химический состав материала, исследованы макро- и микроструктуры.
Визуальный осмотр подшипника РП показал повреждение одного из двух сепараторов в виде вырванных сегментов основы и поперечных элементов, разделяющих ролики. На поверхности обоих сепараторов присутствует сажистый налет. На наружной обойме видимых дефектов не зафиксировано. У подшипника ДВ все ролики по рабочей поверхности и наружная обойма имеют повреждения в виде выкрашивания. На поверхности качения наружной обоймы наблюдаются кратеры выкрошенного металла
46
vk.com/club152685050 | vk.com/id446425943
диаметром до 50 мм, налипшие раскатанные фрагменты вырванного металла из обоймы и тел качения, а также трещины различной протяженности. Внутренняя поверхность сепаратора, а также его поверхность в местах прилегания роликов, имеет концентрические линии срезанного металла, и налипшие частицы, выкрошенные из тел качения.
Перед механическими испытаниями были проведены геометрические измерения роликов, которые показали незначительный разброс по их высоте и диаметрам.
Твердость определялась по методу Роквелла в соответствии со стандартной методикой алмазным конусом по шкале С на стационарном твердомере.
Для подшипника ДВ твердость на поверхности и в сердцевине роликов отличается незначительно, но не соответствует требованиям, предъявляемым к термической обработке элементов подшипников качения.
Для подшипника РП твердость на поверхности и в сердцевине роликов также отличается незначительно, но лежит в нижнем пределе требований, предъявляемым к термической обработке элементов подшипников качения, что говорит об удовлетворительном качестве термической обработки.
Результаты химического анализа материала фрагментов подшипников показали, что химический состав полностью соответствует подшипниковой стали марки ШХ15.
Для проведения металлографических исследований были вырезаны несколько участков подшипников. В число вырезанных элементов входили участки роликов и обоймы. Методика анализа включила: оценку состояния микроструктуры, исследование количества и характера распределения неметаллических включений, изучение качества наружной поверхности подшипников. Исследование загрязненности металла неметаллическими включениями проводилось при увеличении 100 крат на нетравленых шлифах по всему сечению элементов, после чего шлифы подвергались травлению в 3-4 % растворе азотной кислоты в спирте.
Вметалле подшипника ДВ наблюдались множественные неметаллические включения (преимущественно сульфиды), по размеру и количеству соответствующие 3,5 баллу по шкале (рис. 1), что не удовлетворяет требованиям, предъявляемым к загрязненности подшипниковых сталей неметаллическими включениями.
Вметалле подшипника РП наблюдались множественные неметаллические включения (преимущественно сульфиды), по размеру и количеству соответствующие 2 баллу по шкале (рис. 2), что удовлетворяет требованиям, предъявляемым к загрязненности подшипниковых сталей неметаллическими включениями.
47
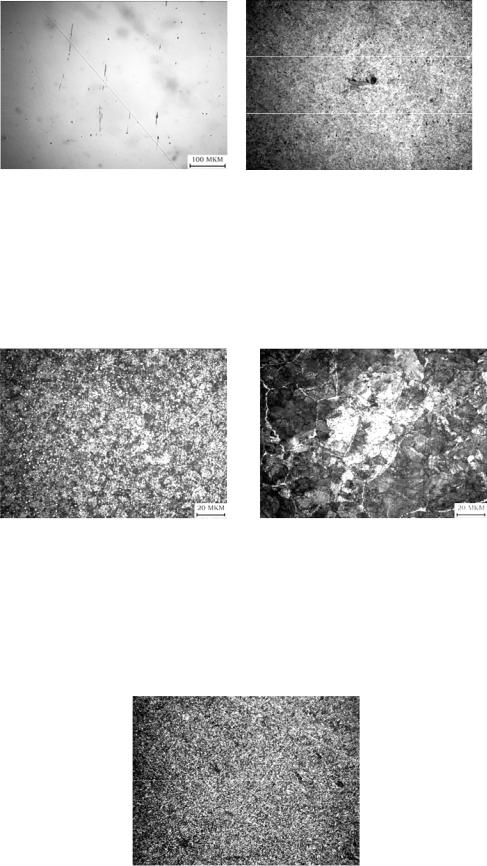
vk.com/club152685050 | vk.com/id446425943
Рис. 1. Неметаллические |
Рис. 2. Неметаллические |
включения, 100 |
включения, 400 |
Металлографические исследования проводились при увеличениях 100 и 500 крат. Микроструктура металла роликов подшипника ДВ различна по сечению: в центре ролика бесструктурный мартенсит с равномерно распределенными мелкими карбидами (рис. 3), по кромкам мелкозернистый перлит с карбидами (рис. 4).
Рис. 3. Микроструктура |
Рис. 4. Микроструктура |
металла ролика |
металла ролика на наружной |
в центральной части, ×500 |
поверхности, ×500 |
Микроструктура металла роликов и наружной обоймы подшипника РП одинакова по сечению и состоит из бесструктурного мартенсита с равномерно распределенными мелкими карбидами (рис. 5), что характерно для данного типа стали и термообработки.
Рис. 5. Микроструктура металла роликов и обоймы, ×500
48
vk.com/club152685050 | vk.com/id446425943
На основании комплексных исследований, проведенных сотрудниками на базе лаборатории металлов "Запсиборгрес", можно сделать следующие выводы.
Вподшипнике РП со стороны внутренней обоймы в локальных местах температура достигала температуры плавления сепаратора, что подтверждается наличием припоев металла сепаратора к поверхности роликов; превращение мартенситной структуры в перлитную металла роликов могло быть вызвано нагревом до температур, приведших к снижению твердости роликов и как следствие к снижению требуемых эксплуатационных характеристик; одной из причин перегрева могло послужить недостаточное количество смазки или плохой ее подвод к телам качения.
Вподшипнике ДВ при недостаточной толщине масляной пленки происходил сухой контакт поверхности качения роликов с беговыми дорожками на обоймах. В результате происходило точечное выкрашивание металла с образованием мостиков сварки. Во второй стадии развития повреждения, которая происходила после восстановления масляных пленок, масло, попадая в микротрещины от первичных повреждений, привело к массовым разрывам металла под действием гидродинамических сил и увеличению массы отделяемых фрагментов. Крупные частицы металла были раскатаны другими роликами, что в дальнейшем привело к стадии катастрофического износа.
Кроме указанных, вероятными причинами повреждения обоих подшипников могли стать применение смазки недостаточной плотности, либо перекос обойм при сборке (монтаже), о чем косвенно свидетельствует неравномерный износ поверхности роликов и обойм.
УДК 621.941.2.01
НАГРУЖЕНИЕ ЭЛЕМЕНТОВ ТЕХНОЛОГИЧЕСКИХ СИСТЕМ В ПРОЦЕССЕ НЕСТАЦИОНАРНОГО РЕЗАНИЯ И МОДЕЛИ ОТКЛОНЕНИЙ ИХ РАСПОЛОЖЕНИЯ
Р. Ю. Некрасов, У. С. Путилова, Д. А. Харитонов
г. Тюмень, Тюменский государственный нефтегазовый университет
В процессе точения характерных для авиастроения фасонных деталей, имеющих, как правило, пониженную жесткость, доля их деформаций и отклонений расположения сложных поверхностей вращения (СПВ) деталей даже при относительно высокой жесткости станков с ЧПУ зачастую значительно превышает все остальные деформации и перемещения в ТС вместе взятые. В связи с этим необходимо решить задачу создания комплекса диагностических устройств для определения составляющих силы резания во взаимосвязи с деформациями и отклонениями расположения нагружаемых в процессе точения заготовок и других элементов ТС с це-
49
vk.com/club152685050 | vk.com/id446425943
лью обеспечения последующего ввода коррекций в процесс обработки на станках с ЧПУ, компенсирующих погрешности обработки, выявленные при диагностике. При этом в соответствии с формируемой моделью компенсирующих коррекций траекторий движения ИРО станков с ЧПУ, их ввод должен компенсировать погрешности, связанные с переменными деформациями, отличающимися по величине при точении каждого фасонного конструктивного элемента заготовки.
С учетом назначения и функциональных возможностей комплекса элементов диагностической системы в работе реализована конструктивная проработка компоновочных решений в привязке к базе токарного станка ЧПУ мод. 16К20Ф3 с использованием метода 3D-моделирования, что позволило сформировать модель измерительного модуля.
Разработанная конструкция в ходе выполнения работы реализована в виде специализированного станочного диагностического модуля. Станочный диагностический модуль оснащен высокоточным индикатором перемещений 1 мод. ЛИР -17, обеспечивающим точность измерения до 0,1 мкм, а также шаговым приводом 2, управляемым от PCNC. Индикатор перемещений установлен в каретке 4 с возможностью ее точных перемещений в направлениях осей ОХ, ОZ по задаваемой управляющей программе. Модуль включает блок 3 цифровой индикации результатов измерений мод. ЛИР-531, при этом обеспечивается возможность передачи данных измерений и их регистрация на жесткий диск PCNC.
Работа с диагностическим модулем предусматривает следующую последовательность операций. В процессе предварительной диагностики конкретной технологической наладки перед обработкой первой заготовки в партии в соответствии с количеством отдельных конструктивных элементов обрабатываемой заготовки, устанавливается совокупность Ai, Bi,… Fi зон приложения нагрузки PXj, PYj к отдельным конструктивным элементам детали 4 (для которых технолог прогнозирует изменение размеров и формы сечения среза по принятой им схеме выполнения технологических переходов). При этом измерительный стержень 3 индикатора 1, перемещаемого в технологическом пространстве наладки с управлением от PCNC, последовательно взаимодействует с поверхностями Ai, Bi,… Fi конструктивных элементов фасонной детали 4.
Схема нагружения и соответствующего отклонения расположения конструктивного элемента Ai детали под нагрузкой представлена на рисунке. На схеме показан индикатор перемещений 1, установленный в каретке 2 диагностического модуля; измерительный стержень 3 индикатора 1; деталь 4; поджимаемый пружиной 5, элемент 6 нажимного устройства 7; инструментальная головка станка 8 и блок цифровой индикации БЦИ. Конструктивная привязка диагностического и нагрузочного модулей к базе токарного станка с ЧПУ мод. 16К20Ф3 вработевыполненасиспользованием3D-моделирования.
Иллюстрации наладок станочной диагностики нагружения и измерения отклонений расположения детали на участках траектории движения
50
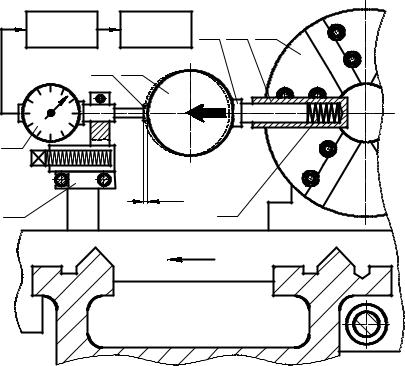
vk.com/club152685050 | vk.com/id446425943
ИРО станка с ЧПУ, соответствующих обработке ее отдельных конструк-
тивных элементов Ai, Bi, Ci, … Fi.
Для реализации представленной выше схемы диагностики разработаны алгоритмы управления процессами нагружения деталей и измерения отклонений расположения элементов ТС с использованием системы диагностических модулей, оснащенных шаговыми приводами исполнительных механизмов с управлением от PCNC. Управление от PCNC процессом диагностики реализовано в полуавтоматическом режиме с использованием разработанного программно-аппаратного комплекса, обеспечивающего согласованные перемещения исполнительных устройств диагностического и нагрузочного модулей с «привязкой» к системе координат XOY станка с ЧПУ.
|
БЦИ |
PCNC |
6 |
7 |
8 |
|
3 |
4 |
|
|
|
|
|
|
Py |
|
|
А |
1 |
|
|
|
|
|
|
A |
|
|
|
|
2 |
i |
|
5 |
|
|
|
|
|
||
|
|
|
|
Si |
|
|
|
|
|
поп |
|
1- индикатор перемещений; 2 - каретка диагностического модуля; 3 - измерительный стержень; 4 - элемент детали; 5 – пружина; 6 - нажимной элемент; 7 – нагрузочное устройство;
8 - инструментальная головка станка
Рисунок. Схема нагружения и диагностики отклонений расположения детали при использовании нагрузочного устройства
При предварительно настроенной и отлаженной системе электроавтоматики станка в процессе диагностики (см. рисунок) включением поперечной подачи суппорта Siпоп нажимное устройство 7, установленное в инструментальной головке 8 токарного станка с ЧПУ, приводится во взаимодействие с закрепленной в патроне деталью 4, имитируя ее нагружение в направлении технологической составляющей PYj силы резания. Нажимным устройством 7, при включении поперечной подачи Siпоп= const, в установленных точках (Аi, Bi,…Fi) осуществляется нагружение заготовки силой
51
vk.com/club152685050 | vk.com/id446425943
PYj. В процессе последовательного нагружения каждого конструктивного элемента детали постепенное сжатие пружины 5, обеспечивает плавное возрастание нагрузки PYj. Данные об изменяющихся отклонениях расположения конструктивных элементов Аi, Bi,…Fi детали и определяемых ап-
паратно соответствующих изменениях величины рассогласования положения iqi в следящем приводе поперечных подач станка при этом синхронно регистрируются на жесткий диск PCNC.
В результате диагностики [49] в PCNC формируется система данных соответствия величин отклонений расположения отдельных конструктивных элементов детали iqi величинам рассогласования положения iqi в следящих приводах подач станков с ЧПУ.
Сформированная система данных соответствия iqi =f( iqi) с использованием представленных ниже зависимостей (3.6) преобразуется к виду iqi =f(PXiYi), что позволяет получить адекватные модели отклонений расположения каждого конструктивного элемента конкретной детали при его нагружении в конкретной ТС и на этой основе реализовать в режиме «реального времени» определение и ввод соответствующих коррекций в траектории движения ИРО станка с системой ЧПУ класса PCNC.
Таким образом, разработана и реализована система предварительной и оперативной диагностики процессов нагружения и деформирования элементов ТС при обработке на станках, оснащенных системами ЧПУ класса PCNC, которая обеспечивает возможность измерения и регистрации величин составляющих силы резания и соответствующих деформаций фасонных деталей. При этом обеспечивается регистрация системы параметров диагностики на жесткий диск ПЭВМ с целью дальнейшего их использования при определении величин и вводе коррекций в траектории движения ИРО станков для компенсации погрешностей обработки, выявленных при диагностике.
Представленные выше системы диагностики, программное обеспечение и аппаратные ресурсы станков с ЧПУ, а также базы данных диагно-
стики позволяют формировать в PCNC математические модели нагрузочных характеристик приводов и модели отклонений расположения эле-
ментов ТС при их нагружении и, тем самым, реализовать комплексную диагностику процессов обработки на станках с ЧПУ.
Диагностику процессов нагружения элементов ТС и приводов станков с ЧПУ, как было показано выше, целесообразно разделять на предварительную и оперативную, что обеспечивает снижение трудоемкости наладки конкретных ТС и соответствует требованиям, предъявляемым к реализации гибких технологий обработки. На этапе предварительной диагностики необходимое установление нагрузочных характеристик конкретных приводов станков (при удовлетворительном состоянии систем электроавтоматики технологического оборудования) целесообразно проводить 2 - 3 раза в течении календарного года при двухсменной эксплуатации станков с ЧПУ.
52
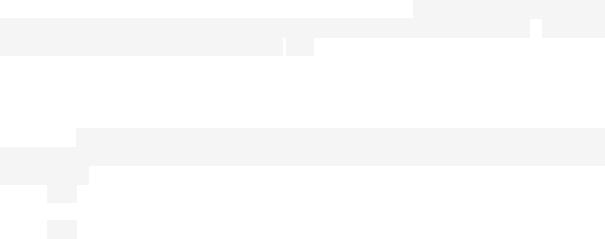
vk.com/club152685050 | vk.com/id446425943
ЗАКЛЮЧЕНИЕ
Разработана система диагностики отклонений расположения элементов ТС, включающая нагрузочные устройства, динамометрическую аппаратуру, диагностические модули и высокоточные индикаторы перемещений. Это позволяет с использованием PCNC формировать системы данных диагностики для дальнейшего определения и ввода коррекций в управляющие программы станков с ЧПУ при компенсации погрешностей обработки в конкретных технологических системах. С учетом изложенного, на основании полученных результатов исследований можно сделать следующие выводы:
Список литературы
1.Ковенский И.М., Некрасов Р.Ю., Путилова У.С. Повышение эффективности управления обработкой высокопрочных сталей и сплавов на станках с ЧПУ // Известия высших учебных заведений. нефть и газ, №2, г. Тюмень: Изд-во ТюмГНГУ, 2008. - С. 116-118.
2.Ласуков А.А., Дурев В.В. Стружкообразование при обработке конструкционных материалов // Горный информационно-аналитический бюллетень. Том 2, №12. -
Москва, 2011. - С. 314-322
3.Янюшкин А.С., Сафонов С.О., Лобанов Д.В. и др. Совершенствование технологических процессов машиностроительных производств. - Братск: Изд-во БрГУ, 2006. - 302 с.
4.Шаламов В.Г. Математическое моделирование при резании металлов: учебное пособие. – Челябинск: Изд-во ЮжУрГУ, 2007.
5.Шаламов B.Г., Савельев Д.А., Сметанин C.Д. Получение порошковых материалов ротационным точением // Вестник машиностроения. – 2012. – № 11. – С. 56-58.
УДК 621.9.06-529
НЕЙРОСЕТЕВОЕ МОДЕЛИРОВАНИЕ И ОПЕРАТИВНЫЙ ВВОД КОРРЕКЦИЙ ПРИ ОБРАБОТКЕ НА СТАНКАХ С ЧПУ
А. И. Стариков, Р. Ю. Некрасов, У. С. Путилова
г. Тюмень, Тюменский государственный нефтегазовый университет
Для повышения точности обработки на станках с ЧПУ предусматривается использование специализированных управляющих программ, в которых траектория движения формообразующего инструмента предварительно искажается с целью компенсации прогнозируемых отклонений расположения элементов технологических систем, возникающих при изменении входных параметров процесса резания. Определение параметров предварительных коррекций обуславливает необходимость прогнозирования силовых и температурных нагрузок и диагностирования процесса обработки с учетом вариации припусков на обработку, изменений износа инструмента, колебаний твердости заготовок и др. Решение задачи определения
53
vk.com/club152685050 | vk.com/id446425943
коррекций осложняется тем, что в условиях современного отечественного производства в эксплуатации находится технологическое оборудование, имеющее существенно различающуюся, а, зачастую, и высокую степень износа (до 80% станков с ЧПУ по нормам точности выработали свой ресурс). При этом параметры жесткости даже однотипных станков, различаются настолько, что в общем случае расчетный метод определения погрешностей обработки становится неприемлемым.
В современных металлорежущих станках используются различного рода диагностические системы, основной функцией которых является контроль параметров состояния элементов технологических систем (например, изнашивание инструмента) в процессе обработки. Однако большая часть этих систем предназначена для использования в статическом режиме и, соответственно, диагностирует статические отклонения. Для диагностики текущих изменений отклонений, которые возникают в процессе резания и зависят от жесткости технологической системы, функциональных изменений сил резания и др., использование традиционных расчетных методов также не применимо.
Суммарная погрешность механической обработки проявляется как результат совместного влияния факторов, вызывающих появление погрешностей. Определить суммарную погрешность простым арифметическим сложением составляющих погрешностей нельзя, так как направление вектора отклонений расположения элементов технологических систем в процессе обработки, например, сложных фасонных поверхностей на станках с ЧПУ, как правило, непрерывно изменяется. Меняется и степень влияния переменных параметров процесса резания на точность обработки, т. е. на величину результирующей погрешности. Поэтому, чаще всего, отдельные погрешности, возникающие при механической обработке, рассматривают как случайные, т. е. такие, о которых нельзя заранее сказать, когда они появятся и каково будет их действительное значение при обработке очередной заготовки.
Создать систему диагностики и управления, которая в режиме реального времени обеспечивает не только определение возникающих погрешностей механической обработки, но и оперативно вводит коррекции в траекторию движения инструмента с целью компенсации непрерывно изменяющихся отклонений расположения элементов технологических систем, позволяет нейросетевое моделирование. Построение данной системы возможно по схеме диагностики и оперативного ввода коррекции в траекторию движения исполнительного рабочего органа (рис. 1), представленной в работе Н.А. Проскурякова [5]. Использование предлагаемой системы обуславливает целесообразность замены работающего по методу аппроксимации интерполятора при применении которого кривая задаваемой функции проходит точно через определенные предварительными расчетами точки и в режиме реального времени не позволяет вводить изменение их координат.
54
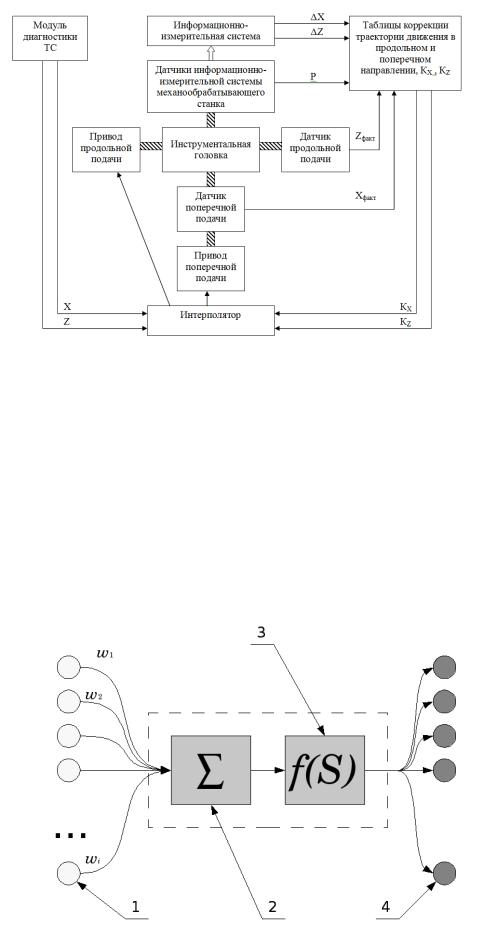
vk.com/club152685050 | vk.com/id446425943
Рис. 1. Схема диагностики и оперативного ввода коррекции в траекторию
Анализ показывает, что априорной информации об уравнении модели не существует и для решения поставленной задачи наиболее подходит метод непараметрической идентификации, который реализуется с использованием нейросетевого подхода и нейронной сети [2]. Нейронная сеть - это программная реализация математической модели, основной задачей которой является прогнозирование возникающих погрешностей и оперативное вмешательство в процесс управления.
На рис. 2 [1] изображена схема нейронной сети, использование которой применимо к решению поставленной задачи.
Рис. 2. Схема нейронной сети
55