
- •Глава 8 энергосбережение в теплотехнологиях
- •8.1. Принципиальные схемы технологий и структуры энергообеспечения предприятий
- •Технология черной металлургии
- •Технология целлюлозно-бумажной промышленности
- •Глава 8 1
- •Рнс. 8.13. Схема установки теплофикационного использования шлаков:
- •8.3. Рациональное энергоиспользование в низкотемпературных технологиях Энергосбережение в сушильных установках
Технология целлюлозно-бумажной промышленности
К числу основных технологических процессов относятся: подготовка древесного сырья; варка, промывка, отбелка целлюлозы; производство различных видов бумаги и картона, регенерация химикатов (рис. 8.3).
Цех подготовки древесного сырья предназначен для приемки древесного сырья, получения технологической щепы из древесины, приемки привозной щепы автомобильной поставки и подачи щепы в производство. Цех подготовки древесного сырья состоит из трех участков: выгрузки древесины; распиловочно-окорочного; древесно-сырьевого. Варка целлюлозы осуществляется сульфатным способом в трех непрерывно действующих установках. По породному составу перерабатываемой древесины имеются два потока: лиственный и хвойный.
Промывка целлюлозы проводится сначала в диффузоре непрерывного действия, далее предусмотрены две схемы промывки целлюлозы: для производства беленой и небеленой целлюлозы. Процесс получения раствора диоксида хлора осуществляется на четырех потоках по методу Метисона и основан на реакции взаимодействия хлората натрия и диоксида серы при наличии серной кислоты.
Регенерация химикатов происходит в выпарных аппаратах поверхностного типа. Выпарной цех оснащен тремя 6-корпусными вакуум-выпарными установками со смешанным ходом щелоков. Плотный черный щелок сжигается в содорегенерационных котлах с получением зеленого щелока и последующей его откачкой на каустизацию. В цехе регенерации щелоков и производства извести получают белый щелок на каустизационной установке непрерывного действия.
Технологический процесс производства термомеханической массы включает в себя подготовку щепы, ее пропарку и размол, отбелку, сортировку, очистку и сгущение древесной массы, переработку отходов. Отбелка термомеханической древесной массы производится в две ступени: первая ступень — пероксидом водорода, вторая — гидросульфитом натрия. Сортирование, очистка и сгущение массы производятся на пяти сортировочных пунктах, где происходит отделение грубого, неразмолотого волокна и костры.
(обозначения те же, что и на рис. 8.1)
Производство химико-термомеханической массы включает в себя два идентичных и взаимозаменяемых потока, один из которых предназначен для переработки хвойной, а другой — лиственной древесины. Отличие этого процесса от предыдущего состоит в использовании различных химических реагентов для обработки щепы перед ее размолом из условий технологического регламента.
Сушильная часть предназначена для обезвоживания бумажного полотна, поступающего после прессовой части. Она включает в себя: бума- госушильные цилиндры; холодильный цилиндр; сетко- и бумаговедущие валики; систему канатиковой заправки; игольчатый заправочный нож; электропривод; устройство натяжения и правки сушильных сеток; шаберы; систему карманной вентиляции; устройства чистки сеток. Сушильная часть (по пару) подразделяется на несколько групп. Это основной потребитель тепловой энергии.
Технология — совокупность методов обработки, изготовления, изменения состояния, свойств, формы сырья, материала или полуфабриката, применяемого в процессе производства для получения готовой продукции.
Все технологические процессы, в которых потребляется тепловая энергия, можно разделить по температурному уровню на низкотемпературные (НТП) и высокотемпературные (ВТП). К высокотемпературным теплотех- нологическим процессам относятся: технологические процессы в черной и цветной металлургии, такие как доменный процесс, выплавка стали, меди, никеля и других металлов; технологические процессы производства многих строительных материалов, такие как обжиг цементного клинкера, варка стекла, обжиг керамических изделий; технологические процессы химической, нефтяной и нефтеперерабатывающей промышленности, такие как термический и каталитический крекинг, пиролиз нефтепродуктов, газификация твердых топлив); процессы сжигания твердых и жидких отходов.
Высокотемпературные теплотехнологические процессы, осуществляемые, как правило, в промышленных печах, характеризуются не только большим потреблением ТЭР, но и невысокой энергетической эффективностью. Например, для получения 1 т алюминия требуется расход энергоресурсов примерно 9 т у.т., никеля — 13,4 т у.т., цинка — 2 т у.т., сортового проката — 1,0—2,5 т у.т., кокса— 1,3 —1,4 т у.т. В России потребление топлива в промышленных печах сопоставимо с его затратами на выработку электрической энергии [1].
Тепловой КПД многих объектов металлургических предприятий составляет примерно 0,25—0,3 и редко достигает 0,5—0,6. Сравнение энергоемкости производства меди, стали, алюминия, огнеупорных изделий в России и США показывает, что в ВТП имеются большие резервы экономии энергии. Так, например, удельный расход энергии на производство стали в слитках к концу XX в. составлял: в США — 0,776 т у.т/т; в Германии — 0,446 т у.т/т; в Швеции — 0,569 т у.т/т; в России — 0,790 т у.т/т. Теоретический минимум этой величины равен 0,238 т у.т/т.
Высокотемпературные теплотехнологические процессы характеризуются рядом особенностей:
в отличие от низкотемпературных технологических процессов, в которых чаще всего используется тепловая энергия горячей воды или пара, в высокотемпературных технологиях для организации процесса расходуется топливо или электроэнергия. Поэтому в высокотемпературных технологиях большое внимание уделяется наилучшей организации процесса горения;
большую роль играют процессы, в которых температура исходных материалов, промежуточных и конечных продуктов, элементов конструкций технологических агрегатов, имеющих большую массу, изменяется во времени. При этом значительная часть теплоты уходит в виде потерь в окружающую среду;
в ВТП велика физическая теплота уходящего из установок готового продукта, а также шлаковых отходов, которую целесообразно утилизировать;
значительны потери теплоты с поверхностей ограждающих конструкций технологических аппаратов в окружающую среду за счет конвекции и излучения.
Наиболее энергоемкими ВТП являются процессы в черной металлургии. Потребление энергоресурсов в этих процессах составляет до 70 % всего потребления энергии в высокотемпературных технологиях.
В энергетическом балансе предприятий металлургии на топливо приходится 70—80 %. Примерно 15—20 % приходится на электроэнергию, которая используется в основном для электротермического нагрева, плавления и электропривода.
В черной металлургии используются различные виды топлива. Каменноугольный кокс — продукт, получаемый при нагревании угля без доступа воздуха, его расход составляет 35—38 % общего потребления топлива. По химическому составу кокс на 96—98 % состоит из углерода. Кокс является не только топливом. Он участвует также в химической реакции восстановления железа из его оксидов в доменном процессе.
Приблизительная структура потребления различных видов топлива в чёрной металлургии представлена на рис. 8.4.
Степень полезного использования теплоты в высокотемпературных технологиях или составляющих её элементов определяется с помощью тепловых балансов, которые могут быть составлены для промышленного предприятия, цеха, теплотехнологической установки в целом или её составной части — теплотехнологического реактора.
Теплотехнологический реактор (аппарат, рабочее пространство тепло- технологической установки) — одно- или многокамерное устройство, в пределах которого осуществляются все стадии данного теплотехнологического процесса [1]. Наиболее распространен-ными теплотехнологическими реакторами для высокотемпературных процессов являются промышленные печи различных назначения и конструкции.



QТ.П,
QТ.М,
QО.Г,
QХ.Т,
QФ.Т,
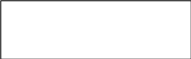
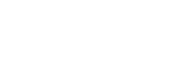
Теплотехнологический
реактор,QЭКЗ, QЭНД
QШ.О,
QФ.Д,
QО.С,



Рис. 8.5. Схема тепловых потоков в рабочей камере теплотехнологического реактора
Рассмотрим основные составляющие теплового баланса теплотехнологического реактора (рис. 8.5).
Приход:
физическая теплота поступающих в установку веществ: топлива, окислителя QФ.Т, исходного технологического материала QT.M
физическая теплота нагрева газа, выделяемая при работе двигателей нагнетателей QФ.Д суммарной мощностью ∑NД;
подводимая для организации процесса тепловая энергия, выделяющаяся в процессе химической реакции горения топлива либо в электротермических установках, QХ.Т;
тепловой эффект экзотермических реакций, протекающих в технологической зоне, QЭK3.
Расход:
физическая теплота уходящих из установки твёрдых веществ: технологического продукта QT.П, шлаковых отходов QШ.О;
тепловой эффект эндотермических реакций, протекающих в технологической зоне, QЭНД;
потери теплоты с отходящими газами QО.Г, в том числе потери теплоты от неполноты сгорания топлива, т.е. от химического и механического недожога;
потери теплоты в окружающую среду через обмуровку за счёт конвекции и излучения QО.С.
Если рассматривается нестационарный режим работы, то кроме составляющих теплового баланса, указанных на рис. 8.5, в расходной части должна быть учтена теплота, затраченная на разогрев конструкций технологических аппаратов и их обмуровки.
В ВТП потери теплоты с отходящими газами могут составлять 40 — 70 %; со шлаковыми отходами — 30 %; потери в окружающую среду через обмуровки— 2—20 %.
Тепловой баланс теплотехнологической установки является основой при выполнении её энергетического анализа.
На основе теплового баланса теплотехнологического реактора можно определить расход топлива или электрической энергии, затрачиваемый на единицу выпускаемой продукции, который служит важной характеристикой для оценки энергетической эффективности процесса. Например, удельный расход топлива на производство на 1 т меди в России составляет примерно 1,4 т у.т.
Тепловой КПД теплотехнологической установки определяется по формуле
(8.1)
Другим способом определения теплового КПД является его расчёт через тепловые потери:
где
В,
— расход
и низшая теплота сгорания используемого
топлива.
Пример 8.1. Определить КПД плавильной печи при следующих условиях: в тепловом балансе печи потери с отходящими газами составляют 50 % подведенной теплоты, потери теплоты через ограждения — 10 %, затраты на нагрев материала до температуры плавления — 15 % и затраты на плавление — 25 %. Регенерация теплоты отходящих газов и теплоты готового продукта отсутствует.
Решение. Полезными затратами теплоты в этом случае являются затраты на нагрев материала и его плавление. Тепловой КПД печи в этом случае составляет:
=-0,4.
Основные направления энергосбережения и энергосберегающие мероприятия в высокотемпературных технологиях изложены в [2].
Классификация
приемов
энергосбережения,
разработанная на кафедре энергетики
высокотемпературных технологий МЭИ,
представлена на рис. 8.6.
Рис. 8.6. Классификация энергосберегающих мероприятий в высокотемпературных технологиях
Для создания энергосберегающих высокотемпературных теплотехнологий и выбора энергосберегающих мероприятий была разработана и получила развитие концепция интенсивного энергосбережения, которая предполагает сравнение энергетических характеристик действующих объектов и их термодинамически идеальных моделей, имеющих теоретический минимум энергетических затрат [1]. Такой подход позволяет определить, насколько совершенной является предлагаемая технология и насколько велики действительные резервы энергосбережения. Наивысшего уровня использования энергии, как правило, нельзя достигнуть по ряду причин технического, экономического и экологического характера. Например, утилизация теплоты влажных продуктов сгорания ограничивается условиями недопущения выпадения влаги в газоходах и дымовых трубах, а также недопущения превышения допустимых концентраций вредных веществ в атмосфере.
Наиболее распространены экономические ограничения достижения наивысшего уровня энергосбережения. В настоящее время разрабатываются методы термоэкономического анализа, в котором связываются экономия энергии и необходимые для этого затраты.
Меры по снижению энергопотребления в высокотемпературных технологиях можно разделить на четыре основные группы [1]: использование передовых энергосберегающих технологий; уменьшение энергетических потерь и материальных отходов в высокотемпературной технологической установке (ВТУ);
регенеративное использование энергии вторичных энергетических ресурсов, уходящих из установки, за счёт её возвращения в технологический процесс;
внешнее теплоиспользование — использование энергии ВЭР для проведения технологических процессов в других установках либо для получения тепловой или электрической энергии (в зависимости от этого внешнее теплоиспользование подразделяют на технологическое и энергетическое).
Внешнее энергетическое использование теплоты может быть связано, например, с получением пара или горячей воды, направляемой на нужды теплоснабжения. Примером внешнего технологического использования теплоты отходящих газов может служить её применение для подогрева сушильного агента в сушильных установках (рис. 8.7).
Теплота газообразных ВЭР для получения пара используется в котлах- утилизаторах различной конструкции, которые в зависимости от температуры и запылённости отходящих газов делятся на радиационные, конвективно-радиационные и конвективные. Температура газов, используемых для выработки пара в котлах-утилизаторах, колеблется от 240 до 1300 °С. Получаемый в них пар имеет избыточное давление 0,5—4,7 МПа и температуру 151—440 °С. Паропроизводительность котлов-утилизаторов может составлять 0,53—200 т/ч. На рис. 8.8 представлена схема установки котлов-утилизаторов за нагревательной печью прокатного цеха завода черной металлургии [1]. Для надёжной работы котлов на запылённых дымовых газах необходимо предусматривать систему очистки поверхностей нагрева.
Рис. 8.7. Принципиальная схема внешнего дополнительного использова-ния тепловых отходов высокотемпера-турной теплотехнологии:
Т—топливо; О — окислитель; ТМ, ТП — технологические материал и продукт; УТ—утилизаторы теплоты
5
4
4
3
3
6
6
2
1
Рис. 8.8. Схема установки котлов-утилизаторов за нагревательной печью прокатного цеха:
1 — печь; 2 — рекуператор; 3 — котлы-утилизаторы; 4 — дымососы; 5 — дымовая труба; 6 — отсечные шиберы
Иногда кроме физической теплоты отходящих газов в котлах-утилизаторах используется тепловая энергия, получаемая при их сжигании.
Энергетический КПД технологического агрегата будет определяться по формуле
(8.3)
Рост КПД для внешнего дополнительного теплоиспользующего устройства будут вычисляться по соотношени