
методички / 4006
.pdf4006 |
МИНИСТЕРСТВО ТРАНСПОРТА РОССИЙСКОЙ ФЕДЕРАЦИИ |
ФЕДЕРАЛЬНОЕ АГЕНТСТВО ЖЕЛЕЗНОДОРОЖНОГО ТРАНСПОРТА |
ФЕДЕРАЛЬНОЕ ГОСУДАРСТВЕННОЕ БЮДЖЕТНОЕ ОБРАЗОВАТЕЛЬНОЕ УЧРЕЖДЕНИЕ ВЫСШЕГО ОБРАЗОВАНИЯ
«САМАРСКИЙ ГОСУДАРСТВЕННЫЙ УНИВЕРСИТЕТ ПУТЕЙ СООБЩЕНИЯ»
Кафедра «Строительные, дорожные машины и технология машиностроения»
ЛАБОРАТОРНЫЙ ПРАКТИКУМ ПО ДИСЦИПЛИНЕ «МАТЕРИАЛОВЕДЕНИЕ»
для обучающихся по специальности 23.05.01 «Наземные транспортно-технологические средства»
очной и заочной формы обучения
Составители: Ж.В. Самохвалова А.Г. Жданов
Самара
2016
1
УДК 669.18
Лабораторный практикум по дисциплине «Материаловедение» для обучающихся по специальности 23.05.01 «Наземные транспортно-технологические средства» очной и заочной формы обучения / составители : Ж.В. Самохвалова, А.Г. Жданов. – Самара :
СамГУПС, 2016. – 54 с.
Методические указания подготовлены в соответствии с действующей программой курса для обучающихся по специальности 23.05.01 «Наземные транспортнотехнологические средства». Методические указания содержат описание лабораторных работ по проведению испытаний и оценке основных физических и механических свойств сплавов, изучению особенностей макро- и микроструктуры железоуглеродистых и легированных сплавов. Второй раздел содержит описание практических работ по изучению диаграммы железо – цементит, определению зависимости между свойствами сплавов, фазовым составом и содержанием углерода; изучению особенностей свойств, условий получения метастабильных структур сталей. В приложениях даны необходимые справочные материалы.
Предназначены для самостоятельного выполнения работ обучающимися очной и заочной форм обучения.
Утверждены на заседании кафедры «Строительные, дорожные машины и технология машиностроения» 11 февраля 2016 г., протокол № 6.
Печатаются по решению редакционно-издательского совета университета.
Составители: Самохвалова Жанна Владимировна Жданов Андрей Геннадьевич
Рецензенты: д.т.н., доцент, профессор кафедры «Вагоны» СамГУПС А.Н. Балалаев; к.т.н., доцент кафедры ПЛА и УКМ Самарского национального исследовательского университета им. С.П. Королева А.А. Шаров
Под редакцией составителей Компьютерная верстка: Е.А. Самсонова
Подписано в печать 16.05.2016. Формат 60×90 1/16. Усл. печ. л. 3,4. Тираж 20 экз. Заказ 68.
© Самарский государственный университет путей сообщения, 2016
2
ВВЕДЕНИЕ
Материаловедение – наука о взаимосвязи строения, структуры материалов с их составом, физическими, химическими, технологическими и эксплуатационными свойствами. Разнообразие свойств материалов является главным фактором, предопределяющим их широкое применение в технике.
При изготовлении изделий и испытаниях машин на производстве постоянно проводится текущий контроль качества материалов. С этой целью используется ряд методов, к числу которых, прежде всего относятся макро- и микроструктурные методы анализа, методы определения механических свойств материалов.
Современному специалисту необходимы определенные знания в области материаловедения, умение рационально использовать обширную номенклатуру материалов и методы их обработки для достижения необходимых эксплуатационных свойств изделий.
Лабораторные и практические работы – важнейшая составная часть обучения, направленная на гармоничное развитие личности обучающегося. Они имеют большое теоретическое и практическое значение. Основной целью лабораторных и практических работ является углубление и закрепление знаний, полученных на теоретических занятиях. Лабораторные занятия должны вооружить обучающихся практическими навыками исследования, расчета и контроля.
В результате выполнения лабораторных и практических работ по дисциплине «Материаловедение» у обучающего формируются профессиональные компетенции ОК-7, ОК-8, ПК-6, в связи с которыми он должен:
Знать: основные методы механических испытаний материалов; механические свойства конструкционных материалов.
Уметь: идентифицировать на основании маркировки конструкционные и эксплуатационные материалы и определять возможные области их применения; по маркировке материала определять состав, назначение сплава; с использование приборов самостоятельно определять механические свойства материалов; выбирать марку материала, исходя из назначения детали.
Владеть: инженерной терминологией в области производства подъемнотранспортных, строительных, дорожных средств и оборудования; навыками работы с электронными измерительными приборами; методами обработки результатов измерений; методами выбора конструкционных и инструментальных материалов.
3
1 ЛАБОРАТОРНЫЕ РАБОТЫ
ЛАБОРАТОРНАЯ РАБОТА № 1
ФИЗИКО-МЕХАНИЧЕСКИЕ СВОЙСТВА МЕТАЛЛОВ И СПЛАВОВ
Цель работы: ознакомиться с методиками проведения испытаний и определить основные физические и механические свойства некоторых металлических сплавов неразрушающими и разрушающими методами; установить отличие материалов по физикомеханическим характеристикам (твердость, плотность, прочность, удельная прочность и др.).
Оборудование, материалы: шкала твердости материалов, твердомер Роквелла, электронный твердомер ТЭМП-3, весы, объемомер, образцы сталей в отожженном и закаленном состоянии, сплавы цветных металлов.
Основные теоретические сведения
Каждый материал обладает комплексом характерных свойств, которые определяют его вид и назначение для изготовления деталей и конструкций. Комплекс свойств, обеспечивающих надежную и длительную работу материала изделий в условиях эксплуатации, называется конструкционной прочностью. Оценку конструкционной прочности производят по критериям прочности и надежности.
При исследовании и испытании металлов определяют следующие показатели:
-предел текучести, временное сопротивление и относительное удлинение по ГОСТ 1497;
-ударную вязкость по ГОСТ 9454 для температур, соответствующих группе конструкций и климатическому району.
Прочность – способность материала сопротивляться, не разрушаясь, действию внутренних напряжений, возникающих в материале в результате приложения внешней нагрузки при испытании на сжатие, растяжение, удар и т.п. Критерии прочности: временное сопротивление (σв), пределы текучести (σт и σ0,2), модуль упругости (E), твердость по Бринеллю (HB).
Твердость – сопротивление материала местной пластической деформации, возникающей при внедрении в испытуемый образец другого более твердого тела.
Модуль упругости – характеристика сопротивления материала упругой (обратимой) деформации, величина равная отношению напряжения к вызванному им относительному удлинению в соответствии с законом Гука.
Надежность представляет собой комплекс технических характеристик, характеризующих изменение свойств материала изделий в процессе эксплуатации. Критерии надежности: относительное удлинение (δ), относительное сужение (ψ), ударная вязкость (KCT, KCV, KCU), температурный порог хладноломкости, удельная прочность и др.
4
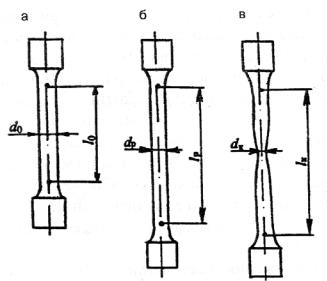
Относительное удлинение – отношение приращения длины образца после разрыва к его первоначальной расчетной длине.
Относительное сужение – уменьшение площади поперечного сечения образца в момент разрыва по сравнению с начальной площадью образца. Ударная вязкость оценивается работой, затраченной на ударный излом образца, отнесенной к площади его поперечного сечения в месте надреза. Составляющими ударной вязкости при испытании являются удельная работа зарождения трещины и удельная работа ее распространения. Характер падения ударной вязкости в зависимости от температуры испытаний позволяет определить начальную температуру порога хладноломкости и конечную. При переходе из вязкого состояния в хрупкое доля волокнистого строения металлического сплава в изломе уменьшается, а кристаллического – увеличивается.
Удельная характеристика прочности рассчитывается как отношение предела прочности к плотности материала.
Методики испытания материалов
1. Испытание образцов разрушающим методом
При статических испытаниях на растяжение нагрузка, прилагаемая к образцу стандартного размера (рисунок 1.1) по ГОСТ 1497, сравнительно медленно и плавно возрастает.
Рисунок 1.1 – Форма и размеры образцов для испытаний на растяжение:
а – образец до испытаний (l0 и d0 – начальные расчетные длина и диаметр); б – образец, растянутый до максимальной нагрузки (lр и dр – расчетные длины и диаметр образца в области равномерной деформации); в – образец после разрыва (lк – конечная расчетная длина; dк – минимальный диаметр в месте разрыва)
Машины для испытаний снабжены прибором, записывающим диаграмму растяжения в системе координат «усилие – абсолютное удлинение». Эту диаграмму заменяют другой: «условное напряжение σ – относительное удлинение ε» (рисунок 1.2).
5
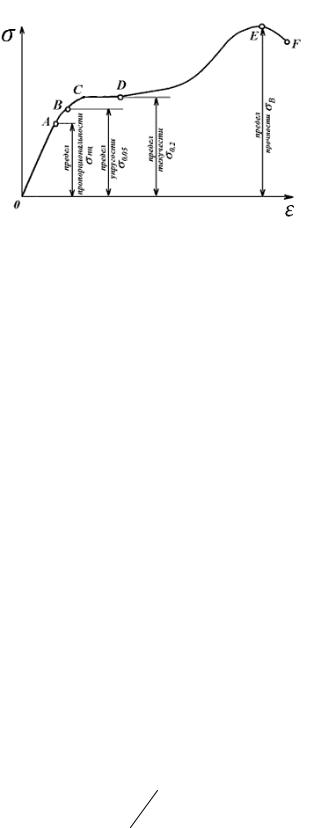
Рисунок 1.2 – Диаграмма растяжения малоуглеродистой стали
При испытаниях на растяжение расчетом определяют следующие характеристики:
-предел упругости σ0,05 – напряжение, при котором остаточное удлинение достигает 0,05 % от первоначальной длины образца;
-физический предел текучести σт – напряжение, при котором образец деформируется без заметного увеличения растягивающей нагрузки; предел текучести характеризует сопротивление материала пластической деформации, для хрупких сплавов определяют условный предел текучести σ0,2;
-временное сопротивление разрыву или предел прочности σв – напряжение, соответствующее наибольшей нагрузке, предшествующей разрушению образца;
-относительное сужение ψ – уменьшение площади поперечного сечения образца
вмомент разрыва по сравнению с начальной площадью поперечного сечения, характеризует пластичность материала;
-относительное удлинение δ – отношение приращения длины образца после разрыва к его первоначальной длине (l0), характеризует пластичность материала;
-модуль упругости Е – отношение приращения напряжения к соответствующему приращению относительного удлинения в пределах упругой деформации в соответствии
сзаконом Гука;
-удельная характеристика прочности σв/ρ – характеризует прочность материала
сучетом его плотности.
Предел прочности σв вычисляется по формуле:
σв = Рв |
, |
(1.1) |
|
F0 |
|
где Рв – максимальная нагрузка на образец в момент его разрушения, Н (кгс); F0 – площадь сечения образца, м2 (мм2).
Относительное сужение ψ определяется по формуле:
ψ = |
F0 − Fk |
100% , |
(1.2) |
|
|||
|
F0 |
|
где F0 – начальная площадь поперечного сечения образца, мм2; Fk – конечная площадь поперечного сечения образца, мм2.
6
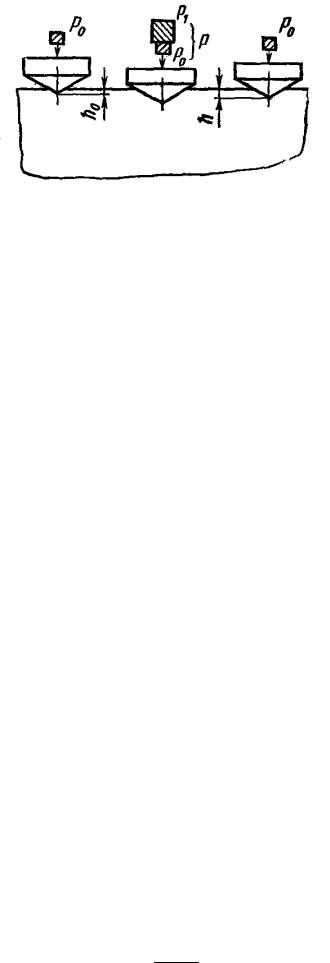
Относительное удлинение δ вычисляется по формуле:
δ = lk − l0 l0
где l0 – начальная длина образца, мм; lk – конечная длина образца, мм.
Удельная характеристика прочности определяется по формуле:
Уσв = σв / ρ ,
где ρ – плотность материала, кг/м3; σв – предел прочности, Н/м2 (кгс/мм2);
2. Определение твердости сплавов (неразрушающие методы)
(1.3)
(1.4)
Вэтом методе твердость определяют по глубине отпечатка. Определение твердости на приборе Роквелла проводят методом вдавливания в испытуемый образец индентора (наконечника). При испытании твердых металлов наконечником служит алмазный конус с углом при вершине 120º, при испытании мягких материалов – стальной закаленный шарик диаметром 1,588 мм.
Испытание проводят под действием двух последовательно прилагаемых нагрузок: предварительной Р0 = 100 Н и основной Р1. Общая нагрузка будет равна сумме двух указанных: Р = Р0 + Р1. Величина основной нагрузки Р1 для стального шарика составляет 900 Н (шкала В), 1400 для алмазного конуса (шкала С) и 500 Н для алмазного конуса (шкала А) при испытании твердых и более тонких материалов толщиной 1–3 мм.
Взависимости от того, по какой шкале проводят испытания (В, С, А), число твердости обозначают соответственно HRB, HRC, HRA. Перевод на НВ (твердость по Бринеллю) производят по таблице приложения 1.
Рисунок 1.3 – Схема определения твердости по Роквеллу
Число твердости по Роквеллу выражается в условных единицах. За единицу твердости принята величина, соответствующая осевому перемещению наконечника на 0,002 мм. Число твердости определяется:
-при измерении по шкале В HRB = 130 – e;
-при измерении по шкале С (А) HRC (HRA) = 100 – e. Величина e вычисляется из уравнения:
e = h − h0 , 0,002
7
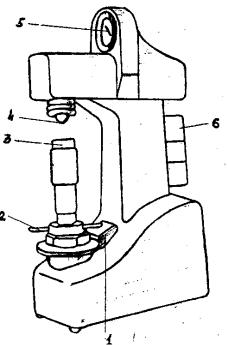
где h – глубина внедрения наконечника в испытуемый материал под действием общей нагрузки Р, измеренная после снятия основной нагрузки, но с оставленной предварительной; h0 – глубина внедрения наконечника в испытуемый материал под действием предварительной нагрузки Р0.
Запись значения твердости 50 HRC означает, что твердость, определенная методом Роквелла по шкале С вдавливанием алмазного конуса, равна 50 (размерность не указывается).
Рисунок 1.4 – Схема твердомера Роквелла
При измерении твердости металлов по методу Роквелла на приборе ТК-2М (рисунок 1.4) стол 3 с изделием поднимают вращением маховика 2 и прижимают изделие к наконечнику 4 до тех пор, пока малая стрелка индикатора 5 не встанет против красной точки, а большая на нуль. Этим обеспечивается предварительная нагрузка Ро. Плавным нажатием на клавишу 1 включают привод механизма нагрузки. Под действием груза 6 наконечник внедряется в металл. Затем нагрузку снимают и грузовой рычаг отводят в исходное положение. Циферблат индикатора 5, по которому отсчитывают число твердости, имеет две шкалы: черную для измерения алмазным конусом и красную для измерений стальным шариком.
Определение твердости электронным твердомером ТЭМП-3
Принцип измерения твердости прибором основан на определении отношения скоростей удара и отскока ударника (шарика), преобразуемого электронным блоком в условную единицу твердости H, которую затем по таблицам переводят в требуемые единицы твердости HB, HRC.
8
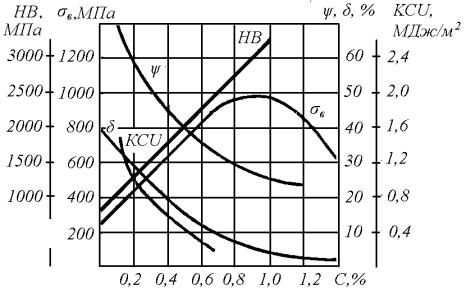
3. Определение механических свойств сплавов по твердости
Значение числа твердости по Бринеллю позволяет приближенно рассчитать значения механических свойств по эмпирическим соотношениям.
Условный предел текучести для конструкционных углеродистых сталей можно рассчитать по формуле, МПа:
σ0,2 = 0,367 НВ – 240. |
(1.5) |
который указывает, что с увеличением твердости возрастает условный предел текучести
(НВ, МПа). |
|
Временное сопротивление рассчитывается по формуле, МПа: |
|
σв = 0,365 НВ0,989. |
(1.6) |
Относительное поперечное сужение отожженных сталей, %: |
|
ψ = 105 – 0,0316 НВ. |
(1.7) |
Относительное удлинение для пятикратных образцов: |
|
δ5 = 420 · 100 / (2σв + σ0,2). |
(1.8) |
Зависимость механических характеристик стали в состоянии поставки от содержания в них углерода представлена на рисунке 1.5.
1000
Рисунок 1.5 – Зависимость механических свойств сталей от содержания углерода
4. Определение плотности
Плотность – физическая величина, определяемая как отношение массы тела к занимаемому этим телом объёму.
По плотности все металлы подразделяются на легкие (менее 4,5 г/см3) и тяжелые. Использование более легких металлов и сплавов способствует снижению массы изделий. Плотность рассчитывают по результатам испытаний с определением веса (Р) образца взвешиванием на технических весах и объема (V). Объем определяют с помощью объемомера, см3:
ρ = Р / V, |
(1.9) |
9

Для материалов, используемых в транспортной технике важное значение имеет эффективность материала по массе. Эффективность материала по плотности оценивают удельной прочностью.
Порядок выполнения работы
1. Получить образцы сплавов, испытанные на растяжение. Произвести их обмер штангенциркулем. По значению разрушающей нагрузки Рв и размерам образцов до и после испытания рассчитать значения механических свойств по формулам 1.1–1.3. Результаты расчетов представить в таблице 1.1.
Таблица 1.1 – Результаты расчетов и испытаний образцов на растяжение
Марка |
Размеры образца |
Нагрузка |
Предел |
|
|
|
Размеры |
|
Значения |
|||||||||
сплава |
до испытания |
Pв, кгс |
прочности при |
образца после |
относительного |
|||||||||||||
|
на растяжение |
|
растяженииσв , |
|
|
испытаний |
удлиненияисужения |
|||||||||||
|
|
|
|
|
|
|
кгс/мм2 (МПа) |
|
|
|
|
|
|
|
|
|
|
|
|
d |
0 |
, |
l , |
F , |
|
d |
k |
, |
|
l |
k |
, |
|
F ,, |
δ , % |
ψ , % |
|
|
|
|
0 |
0 |
|
|
|
|
|
|
|
|
k |
|
|
|||
|
мм |
мм |
мм2 |
|
|
мм |
|
мм |
|
мм2 |
|
|
||||||
|
|
|
|
|
|
|
|
|
|
|
|
|
|
|
|
|
|
|
2.Изучить конструкцию прибора Роквелла, способы настройки его на испытание отожженных и закаленных металлов. Определить твердость отожженного и закаленного образцов по методу Роквелла. Используя приложение 1, найти соответствующие значения твердости по шкале Бринелля.
3.Изучить методику определения твердости на приборе ТЭМП-3. Определить твердость испытуемых отожженных, закаленных образцов сталей. Результаты испытаний представить в таблице 1.2.
Таблица 1.2 – Результаты испытания сплавов на твердость
Марка сплава |
|
|
Твердость сплава |
|
|
|
|
|
|
По прибору Роквелла |
|
По прибору ТЭМП-3 |
|
||||
|
HRА |
HRB |
HRC |
Н |
|
НВ |
|
HRC |
|
|
|
|
|
|
|
|
|
4.Рассчитать основные механические свойства сталей марок: 10, 40, 70 по значениям их твердости (формулы 1.5–1.8). Значение твердости сплава определить по рисунку 1.5.
5.Определить плотность сплавов по (формуле 1.9), сравнить полученные экспериментальные значения со значениями плотности, приведенными в приложении 3. Рассчитать удельную прочность сплавов. Результаты испытаний представить в таблице 1.3.
10