
методички / 4006
.pdfТаблица 1.3 – Результаты испытания сплавов на плотность
Сплав |
Вес |
Вытесняемый |
Плотность, |
Удельная |
Тяжелый/легкий |
(металл) |
образца, г |
объем, см3 |
г/см3 |
прочность, см |
сплав (металл) |
|
|
|
|
|
|
Содержание отчета
В отчете привести: цель работы, расчеты механических свойств, таблицы результатов испытаний. Выводы должны указывать на зависимость свойств углеродистых сталей от содержания углерода (см. приложение 2).
Контрольные вопросы
1.Дайте определение «конструкционной прочности».
2.Перечислите критерии прочности.
3.Поясните методы определения твердости.
4.Дайте определение «твердости».
5.Почему используются разные инденторы в методе Роквелла?
6.Для чего применяется предварительное нагружение в методе Роквелла?
7.Как работает индикатор твердомера Роквелла?
8.Назовите прибор для определения твердости отожженной стали.
9.Назовите прибор для определения твердости закаленной стали.
10.Дайте определение «удельная прочность».
11.Сталь, какой марки 10 или 40 прочнее? С чем это связано?
ЛАБОРАТОРНАЯ РАБОТА № 2
МАКРОИССЛЕДОВАНИЕ МЕТАЛЛОВ И СПЛАВОВ
Цель работы: изучить особенности макроструктуры металлов и сплавов. Оборудование и материалы: комплект образцов для определения видов изломов
при разрушении деталей в процессе эксплуатации и с различными дефектами макроструктуры, бинокулярный микроскоп.
Основные теоретические сведения
Макроскопический анализ предусматривает определение особенностей строения металла изделий (макростроения) невооруженным глазом или при незначительных увеличениях с использованием лупы или бинокулярного микроскопа (увеличение до 30 раз). Исследование макроструктуры позволяет установить первичную структуру сплава при кристаллизации, химическую неоднородность (ликвацию), характер расположения воло-
11
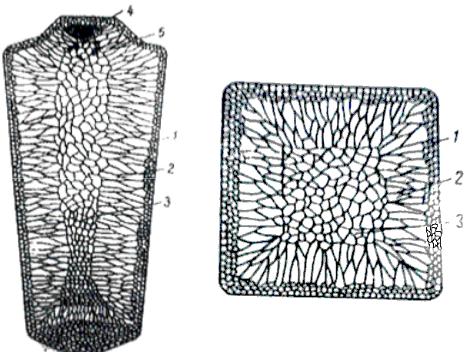
кон после пластической деформации, дефекты, вид излома. Строение металлов, изучаемое при помощи макроанализа, называется макроструктурой.
Макроанализ может проводиться как по виду излома металла, так и по специально подготовленной поверхности металлического образца. Подготовка образца заключается в шлифовании выбранной поверхности с последующим травлением специальными реактивами.
Шлифованныйипротравленныйдлямакроанализаобразец называетсямакрошлифом. Качество деталей в значительной степени определяется качеством стального слитка, из которого детали изготовлены. Условия затвердевания жидкого металла в изложни-
це влияют на кристаллическую, химическую неоднородность стального слитка (рис. 2.1).
Рисунок 2.1 – Макроструктура металлического слитка:
1 – зона мелких произвольно ориентрованных кристаллов; 2 – столбчатые кристаллы; 3 – зона крупных произвольно ориентированных кристаллов; 4 – усадочная раковина; 5 – усадочная рыхлость
По наличию дефектов в структуре изделий можно судить о нарушениях технологического процесса, приводящих к изменению свойств и появлению дефектов. Дефекты литейного производства: пузыри, поры, шлаковые включения, ликвация (химическая неоднородность), флокены, усадочная раковина, усадочная рыхлость и др. (рис. 2.2).
При сварке металлов плавлением в зоне сварного шва происходит изменение макроструктуры металла (рис. 2.4). В сварном соединении четко видны три зоны: основной металл, наплавленный металл, зона термического влияния, и шесть зон структур металла: зона неполного расплавление; перегрев; нормализация; неполная перекристаллизация; рекристаллизация; зона синеломкости.
12
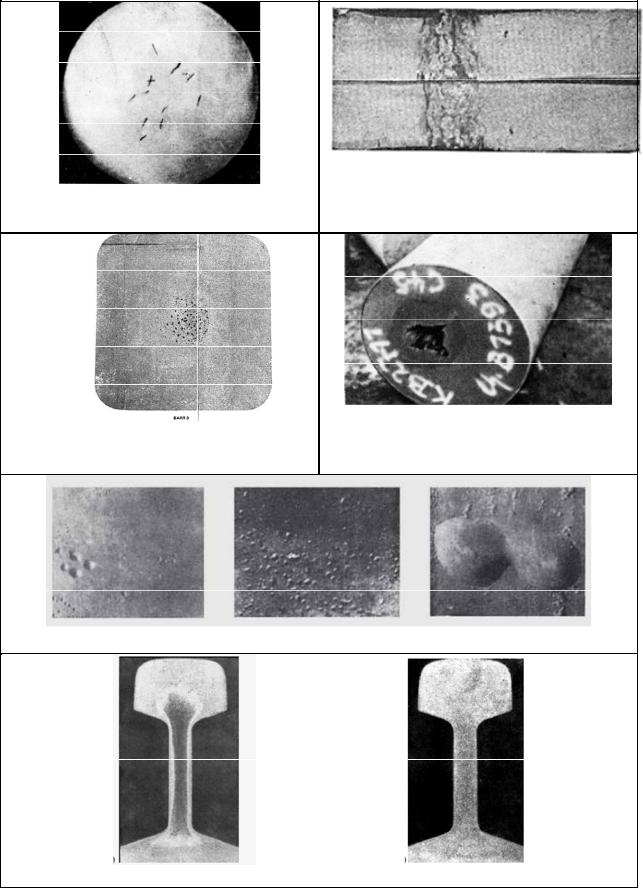
Литейные дефекты в стали – мелкие |
Литейный дефект – расслоение |
трещины (флокены) |
|
Литейные дефекты – центральная |
Полости в поковках от усадочных раковин |
|
пористость |
||
|
Дефекты стали – отдельные пузыри (вздутия) на поверхности
ярко выраженная ликвация серы в стали |
равномерное распределение серы |
Рисунок 2.2 – Литейные дефекты
13
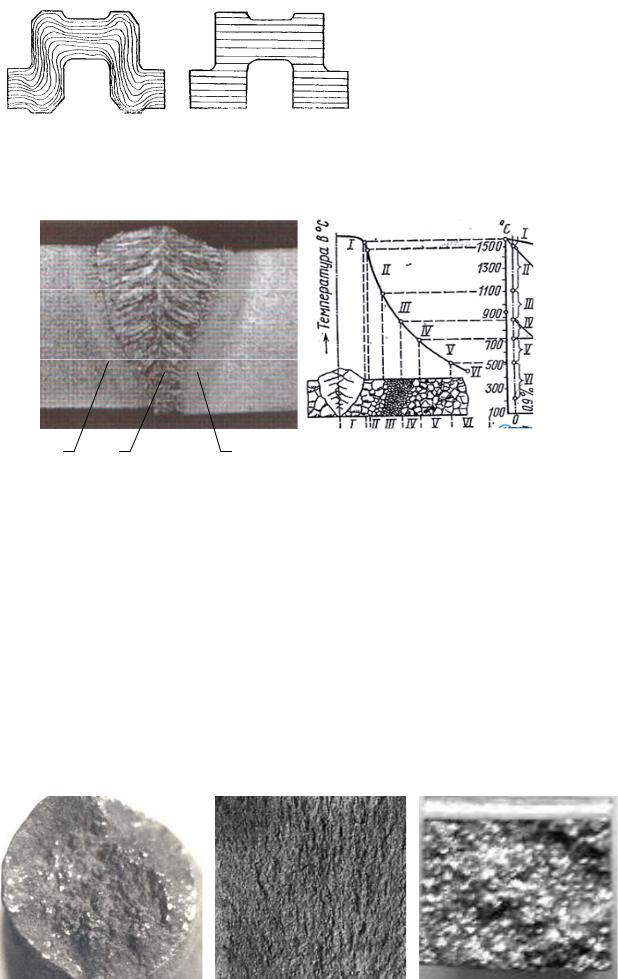
а) б)
Рисунок 2.3 – Схема макроструктуры продольного разреза коленчатого вала с правильным (а) и неправильным (б) расположением волокон
|
|
|
|
|
|
|
1 |
|
2 |
|
3 |
|
|
|
|
|
а) |
|
б) |
|
|
|
|
|
|
Рисунок 2.4 – Макроструктура сварного соединения а) макрошлиф: 1 – основной металл, 2 – наплавленный металл, 3 – зона термического влияния
б) Схема распределения структур в сварном шве и околошовной зоне: I – неполное расплавление; II – перегрев; III – нормализация; IV – неполная перекристаллизация; V – рекристаллизация; VI – синеломкость
Область материаловедения, изучающая характер излома при разрушении, называется фрактографией. Методом макроанализа определяют вид излома. Анализ изломов помогает судить о качестве термической обработки, характере рабочих нагрузок, а также может служить для установления причин поломок. Рельеф разрушенной поверхности указывает на вид излома: вязкий, хрупкий, смешанный (рис. 2.4).
а) |
б) |
в) |
Рисунок 2.4 – Виды излома металлов:
а – вязкий, б – волокнистый вязкий, в – хрупкий
14
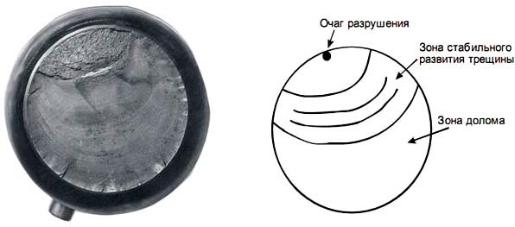
Вязкий излом (рис. 2.4, а) имеет матовый оттенок без ярко выраженного металлического блеска. Образец или деталь перед разрушением приобретает значительную местную пластическую деформацию, сопровождающуюся образованием шейки. Материал с вязким разрушением обеспечивает большую надежность конструкции. При разрушении вязкого материала требуется затрата значительной работы. В местах концентрации напряжений в результате локальной микродеформации материал упрочняется и разрушение предотвращается или оно происходит при более высоких напряжениях. По виду вязкого излома нельзя судить о форме и размерах зерен металла.
Хрупкие изломы (рис. 2.4, в) происходят без заметной пластической деформации путем отрыва или скола. Излом имеет кристаллический характер и металлический блеск. Разрушение может происходить по телу зерен (транскристаллический излом) или по границам зерен (межкристаллический излом). Хрупкое разрушение наиболее опасно, так как происходит чаще всего при напряжениях ниже предела текучести материала.
Усталостный излом (рис. 2.5) – следствие разрушения изделия в результате переменного (циклического) многократного нагружения. Усталостный излом имеет 3 характерные зоны: 1 – очаг разрушения, 2 – зона постепенного развития трещины, 3 – зона долома. Зарождение трещины начинается в очаге разрушения, где имеются концентраторы напряжений или дефекты. Зона развития трещины отличается мелкозернистым строением, поверхность гладкая. Зона долома – результат ослабления несущей способности изделия при уменьшении поперечного сечения детали. Вторая и третья зона образуются быстро – в течение нескольких циклов нагрузки, в то время как первая развивается постепенно.
а) |
б) |
Рисунок 2.5 – Усталостный излом: а – фото излома; б – схема усталостного излома
По характеру излома определяют температуру порога хладноломкости − температуру испытаний на ударный изгиб, когда в изломе фиксируются 50 % волокнистой и 50 % кристаллической составляющей сплава.
15
Порядок выполнения работы
1.Рассмотреть и изучить особенности макроструктур: металлического слитка; детали, изготовленной обработкой давлением, сварного соединения. Обратить внимание на характерные зоны: размер зерен, их расположение, цвет, дефекты.
2.Рассмотреть и изучить основные виды изломов (вязкий, хрупкий, усталостный). При изучении особенностей излома обратить внимание:
-на форму и расположении зерен в литом сплаве;
-характер и расположение волокон (деформированных зерен) в металле после пластической деформации (прокатки, ковки) и т.д.;
-наличие или отсутствие металлического блеска излома;
-наличие или отсутствие следов пластической деформации;
-форму краев излома;
-дефекты, нарушающие целостность образца (детали);
-вид излома;
-сделать предположение о способе изготовления образца (детали);
Содержание отчета
В отчете указать: название, цель работы, оборудование и материалы, зарисовать эскизы макрошлифов, изломов в квадратах 30х30 мм и их описание представить в таблице 2.1.
Таблица 2.1
Эскиз макрошлифа или излома |
Анализ и описание |
||
|
|
|
|
|
|
|
|
|
|
|
|
Контрольные вопросы
1.Что называется макроанализом?
2.Какие образцы используются для макроанализа?
3.Перечислите виды изломов, их отличительные характеристики.
4.Как приготавливается макрошлиф?
5.Что такое усталостный излом, его зоны, причины появления излома?
6.Как влияет направление волокон в деформированном металле на свойства детали?
7.Что такое ликвация, как она влияет на свойства сплава?
8.По какому излому нельзя судить о структуре сплава, почему?
9.Перечислите особенности макроструктуры сварного шва.
10.Перечислите виды макродефектов при литье, обработке давлением, сварке.
16
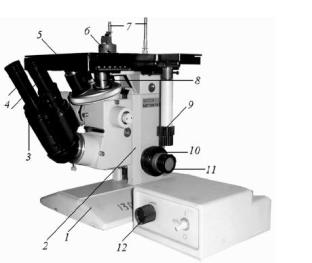
ЛАБОРАТОРНАЯ РАБОТА № 3
МИКРОИССЛЕДОВАНИЕ МЕТАЛЛОВ И СПЛАВОВ
Цель работы: изучение устройства металлографического микроскопа, приобретение навыков работы с ним; изучение особенностей микроструктуры углеродистых сталей различного назначения.
Оборудование, образцы, реактивы: металлографический микроскоп Метам РВ22, набор образцов микрошлифов сплавов, фотографии микрошлифов сплавов.
Основные теоретические сведения
Микроскопический анализ (микроанализ) – основной метод исследования структуры металлов при просмотре очень малых участков поверхностей образцов, специально подготовленных к исследованиям при больших (от 50 до 2000 раз) увеличениях с помощью микроскопа. Поверхностьобразца, подготовленнаядляисследования, называетсямикрошлифом.
Наблюдаемая структура называется микроструктурой. Оптический микроскоп позволяетразличатьчастицыразмеромнеменее0,2 мкм, аэлектронный−неменее0,01 мкм.
Микроанализ с применением оптического микроскопа позволяет определить: форму и размеры кристаллитов, из которых состоит сплав; структуру; микропоры: микротрещины, раковины и др.; наличие, размеры и характер распределения неметаллических включений: сульфидов, оксидов, силикатов, частицграфита.
Рисунок 3.1 – Общий вид металлографического микроскопа Метам РВ-22:
1 – основание; 2 – корпус(унифицированныйштатив); 3 – бинокулярнаянасадка; 4 – окуляры; 5 – предметныйстолик; 6 – исследуемыйобразец(микрошлиф); 7 – клеммы(прижимы); 8 – объектив; 9 – рукояткаперемещениястолика; 11,10 – винтрегулировкичеткостиизображения; 12 – регуляторосвещенности
Для настройки микроскопа и получения изображения микроструктуры необходимо микрошлиф 6 установить на предметный столик микроскопа 5, подготовленной поверхностью вниз – на световой поток. Наблюдая в окуляр 4, вращать винт 10 (на себя – от себя) до момента появления в поле зрения окуляра очертаний микроструктуры, затем, вра-
17
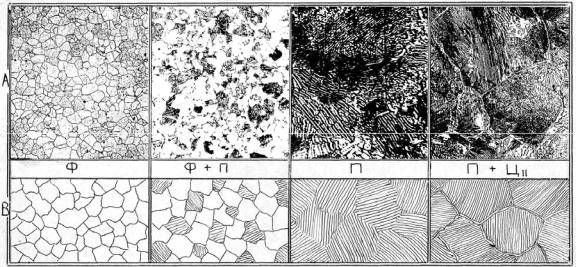
щая винт 11, добиться резкости ее изображения. При необходимости выбора для исследования наиболее характерного места структуры винтами рукоятки 9 перемещать предметный столик поочередно во взаимно-перпендикулярных направлениях.
Технология изготовления микрошлифа
Процесс изготовления шлифов включает вырезку образцов из материала, подлежащего исследованию, заторцовку, шлифование поверхности, предназначенной для исследования, и последующее полирование.
Плоскость образца шлифуют вручную или на специальных станках. Шлифование производят металлографической бумагой с крупным и мелким зерном (60…240). Смывают частицы абразива водой и полируют пастой ГОИ. После достижения зеркального блеска, поверхность шлифа промывают водой, обрабатывают спиртом и просушивают фильтровальной бумагой. Затем производят процесс травления в специальном реактиве. Травление осуществляют погружением образца полированной поверхностью в раствор на несколько секунд или реактив наносят на полированную поверхность пипеткой. Затем поверхность промывают водой, спиртом и просушивают фильтровальной бумагой.
Признаком протравления служит потускнение поверхности шлифа. Травлением создается микрорельеф: поверхность шлифа становится шероховатой. Растворимость отдельных элементов структуры (зерен, их границ) в реактиве различна, поэтому одни участки шлифа становятся более шероховатыми, чем другие, и по-разному отражают световые лучи. Границы зерен наблюдаются в виде черных линий, так как они протравливаются интенсивнее и практически не отражают света, а рассеивают его. Слабо травленые участки отражают больше лучей света в поле зрения микроскопа и будут светлыми. Разница состояний просматриваемых после травления поверхностей и определяет особенности микроструктур сплавов, например углеродистых сталей (рис. 3.2).
Рисунок 3.2 – Микроструктуры углеродистых сталей А – микроструктуры, В – схемы микроструктур: (слева направо) техническое железо, доэвтектоидная
сталь, эвтектоидная сталь, заэтвектоидная сталь (Ф – феррит, П – перлит, ЦВ – цементит вторичный)
18
Под микроструктурой сплава понимают видимое в микроскоп взаимное расположение фаз, их форму и размеры. Структурными составляющими углеродистых сталей являются феррит, цементит, перлит.
Феррит – твердый раствор углерода в α-железе. Цементит представляет собой химическое соединение железа и углерода Fe3C. Перлит – это эвтектоидная механическая смесь пластинок феррита и цементита. Зерна феррита и пластинки или сетка цементита на микрошлифе имеют вид светлых участков, разделенных темными границами. При процессе травления ферритные пластинки растворяются в кислоте более интенсивно, чем цементит. Поэтому падающий в микроскопе на микрошлиф свет, дает тени от выступов цементитных пластин и создается впечатление чередующихся белых и черных пластинок.
Порядок выполнения работы
1.Ознакомиться с особенностями микроскопического анализа, методикой приготовления микрошлифов, устройством микроскопа.
2.Изучить оптическую схему микроскопа, настроить на заданное увеличение (100…500) и отрегулировать контрастность изображения.
3.Изучить микроструктуры углеродистых конструкционных и инструментальных сталей в отожженном состоянии с помощью микроскопа и фотографий. Определить фазовый состав сталей. Эскизы микроструктур зарисовать в квадратах 30×30 мм. Результаты представить в таблице 3.1.
Таблица 3.1 – Результаты исследований микроструктуры и свойств углеродистых сталей
Марка |
Содержание углерода, |
Фазовый состав, |
|
Механические свойства |
|
|||
стали |
% |
% |
|
|
|
|
|
|
|
|
|
|
|
|
|
|
|
|
|
Ф, (Ц), % |
П, % |
НВ, |
σв, |
δ, % |
ψ, % |
КСU, |
|
|
|
|
МПа |
МПа |
|
|
Дж/м2 |
|
|
|
|
|
|
|
|
|
4. Для исследуемых сталей по рисунку 1.5 определить механические свойства в зависимости от содержания углерода. Количество фаз в сталях определить по таблице 3.2.
Таблица 3.2 – Химический и фазовый состав углеродистых сталей
Марка стали |
20 |
40 |
60 |
80 |
Содержание углерода, % |
0,2 |
0,4 |
0,6 |
0,8 |
Площадь перлита, % |
25 |
50 |
75 |
100 |
Площадь феррита, % |
75 |
50 |
25 |
– |
Площадь цементита, % |
– |
– |
– |
– |
|
|
|
|
|
19
Содержание отчета
Отчет должен включать в себя название и цель работы; назначение микроанализа; порядок приготовления микрошлифа. Результаты исследований представить в таблице 3.2. Вывод по работе должен отражать, как изменяется микроструктура и свойства сталей в зависимости от содержания углерода.
Контрольные вопросы
1.Что такое микроанализ?
2.Что можно определить микроскопическим анализом?
3.Что такое микрошлиф и способ его приготовления?
4.Какую микроструктуру имеют доэвтектоидные, эвтектоидные, заэвтектоидные
стали?
5.Для чего производится травление микрошлифов?
6.В чем заключаются принцип действия и настройка металлографического микро-
скопа?
7.Как определить увеличение микроскопа?
8.Поясните порядок проведения работ на микроскопе.
ЛАБОРАТОРНАЯ РАБОТА № 4
МИКРОСТРУКТУРА ЛЕГИРОВАННЫХ СТАЛЕЙ И СПЛАВОВ
Цель работы: ознакомиться с особенностями микроструктуры и основными механическими свойствами легированных сталей, приобрести навыки в определении (расшифровке) химического состава легированной стали по ее маркировке.
Оборудование и материалы: металлографический микроскоп, наборы микрошлифов легированных сталей различного назначения, фотографии микрошлифов сплавов, диаграммы состояния сплавов с открытой и замкнутой γ-областью.
Основные теоретические сведения
Легированной называется сталь, содержащая специально введенные элементы для получения требуемых свойств. Легирующие элементы обозначаются следующими буквами: Б – ниобий, В – вольфрам, Г – марганец, Д – медь, К – кобальт, М – молибден, Н – никель, Р – бор, С – кремний, Т – титан, Ф – ванадий, Х – хром, Ю – алюминий.
Маркировка стали состоит из сочетания букв и цифр. В конструкционных сталях первые две цифры обозначают содержание углерода в сотых долях процента, а количество легирующих элементов указывается в процентах цифрами, стоящими после соответ-
20