
методички / 4006
.pdfПерлит (0,8 % С) – эвтектоидная механическая смесь феррита и цементита вторичного, чаще имеет пластинчатое строение зерен, прочная структурная составляющая сплавов: σв = 800…900 МПа; σ0,2 = 450 МПа; δ ≤ 1 6 %, HB 1800…2200.
Ледебурит первичный (4,3% С) – эвтектическая механическая смесь аустенита и цементита при температуре выше 727 ºС, вторичный − механическая смесь перлита и цементита при температуре ниже 727 ºС. В этой структурной составляющей цементит образует сплошную матрицу, в которой размещены колонии перлита. Такое строение обуславливает его высокую твердость (HB более 6000) и хрупкость. Присутствие ледебурита в сплавах обусловливает их неспособность к обработке давлением, затрудняет обработку резанием.
Сплав с содержанием углерода 0,4% имеет перитектическое и эвтектоидное превращения. Первичная кристаллизация начинается при 1520 ºС, сплав становится двухфазным: жидкость с высокотемпературным ферритом. Перитектическое превращение при 1500 ºС сопровождается превращением феррита высокотемпературного в аустенит. Сплав изменяет фазовый состав на Ж +А, который сохраняется до температуры 1445 ºС. При температуре 1445 ºС сплав становится однофазным, состоит из кристаллов аустенита А0,4 крупнозернистого. Вторичная кристаллизация – превращение затвердевшего сплава (Ж = 0 %), обусловленное полиморфным превращением, полным или частичным распадом твердого раствора. В интервале температур 1445…800 ºС аустенит крупнозернистый превращается в мелкозернистый, а затем из него выделяются кристаллы феррита, сплав становится двухфазным А + Ф = 100 % с переменным соотношением фаз в соответствии с изменением температуры. При температуре 727 ºС содержание углерода в аустените достигает 0,8 % и ниже линии PSK аустенит распадается на Ф + Ц − механическую смесь (перлит). Ниже 727 ºС охлаждение сплава не сопровождается изменением фазового состава и структуры. Сплав является доэвтектоидной сталью и состоит из 2-х структурных составляющих (Ф + П) = 100 % .
Сплав с содержанием углерода 1% имеет четыре критические температуры 1480, 1330, 820 и 727 ºС, это сплав имеет эвтектоидное превращением. Фазовые превращения в сплаве при охлаждении: Ж1,0 → Ж + А = 100 %, на линии солидус сплав имеет структуру А1,0 = 100 % крупнозернистого. Охлаждение до 820 ºС приводит к измельчению зерен аустенита. Снижение температуры при охлаждении вызывает выделение избытка углерода в виде зерен цементита. В интервале температур 820…727 ºС изменяется соотношение фаз А+ЦII = 100 %. Выделение цементитной фазы снижает содержание углерода в аустените до 0,8 %. При 727 ºС аустенит превращается в перлит А0,8 → П0,8. При охлаждения ниже 727 ºС сплав имеет структуру П + ЦII = 100 % с преобладанием перлитной составляющей в структуре. Сплав является заэвтектоидной сталью.
Критические температуры превращений белых чугунов доэвтектического и заэвтектического отличаются от сталей температурами первичной кристаллизации, и они имеют эвтектическое превращение (1147 ºС), которое соответствует линии солидус и эвтектоидное (727 ºС). Для чугуна с содержанием С = 3,0 % изменения фазового состава
41
происходят при 1300, 1147 и 727 ºС. Из Ж = 100 % при 1300 ºС выделяются кристаллы аустенита, сплав имеет двухфазную структуру Ж + А = 100 % до температуры 1147 ºС. Кристаллизация эвтектики (ледебурит) происходит при 1147 ºС, образуются ледебуритные колонии сросшихся между собой дендритов аустенита и цементита А + ЦII + ЛI = 100 %. Аустенит избыточный и аустенит ледебурита содержат 2,14 % углерода. При снижении температуры растворимость углерода в аустените падает и выделяется избыточный вторичный цементит. Содержание углерода в аустените достигает 0,8 % при 727 ºС. При этой температуре аустенит ледебурита превращается в перлит. Ниже 727 ºС охлаждение сплава не сопровождается изменением фазового состава, структура сплава (П + ЦII + ЛI) = 100 %. Сплав является доэвтектическим чугуном.
Заэвтектический белый чугун С = 5 % имеет соответственно критические точки при 1200, 1147 и 727 ºС. Кристаллизация начинается с выделения крупных зерен цементита (первичного), содержание углерода в жидкой фазе снижается. При температуре 1147 ºС Ж → ЛI. Структура сплава ЦI + ЛI = 100 % сохраняется до температуры 727 ºС. При этой температуре аустенит ледебурита превращается в перлит. Ледебурит выше линии PSK состоит из А + ЦI = 100 %, а ниже – из П + ЦI = 100 %.
Процессы, происходящие в сплавах при фазовых превращениях подчинены общему закону равновесия, который носит название правила фаз или (Закон Гиббса), выражает зависимость числа степеней свободы системы «С» от количества компонентов в сплаве «К», фаз «Ф» и внешних переменных факторов «n» в условиях равновесия.
С = k + n − ф.
При рассмотрении равновесия металлических сплавов, находящихся под воздействием атмосферного давления, единственным внешним переменным фактором является температура, поэтому n = 1. Система железо-цементит является двухкомпонентной, т.е. к = 2, отсюда следует, что
С = 2 + 1 − ф = 3 − ф.
Если С = 2, то это обозначает, что в рассматриваемом диапазоне температур в сплаве существует только одна фаза, равновесие в системе не нарушится даже при одновременном изменении температуры и концентрации сплава в определенных пределах, температура будет падать быстро, линия охлаждения идет круто вниз.
Если С = 1, это обозначает, что в рассматриваемом диапазоне температур в сплаве существует две фазы, при изменение температуры изменится количество фаз, но равновесия не нарушится. Кривая охлаждения в этом диапазоне температур станет более пологой.
Если С = 0, это означает, что в рассматриваемом диапазоне температур в сплаве существует три фазы, находится в равновесии они могут только при постоянной температуре, на линии охлаждения наблюдается горизонтальный участок.
По диаграмме состояния сплавов можно проследить за фазовыми превращениями любого сплава и определить состав и количественное соотношение фаз при любой температуре по правилу отрезков. Для определения концентрации компонентов в двух фаз-
42
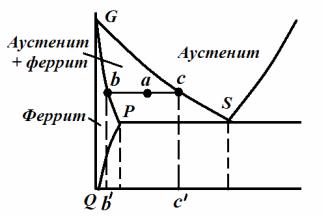
ной области через данную точку (на пересечении координат температура – содержание углерода) проводят горизонтальную линию до пересечения с основными линиями диаграммы, ограничивающими данную область. Проекции точек пересечения на ось концентраций укажут составы фаз. Отрезки этой линии (конода) между точкой с и точками а и в, определяющими составы фаз, обратно пропорциональны количествам этих фаз.
Рисунок 1.2 – Нахождение массовой концентрации фазы по правилу отрезков
Q аустенита = (ba/b′c′)·100%;
Q феррита = (ac/b′c′)·100%;
Порядок выполнения работы
1.Начертить диаграмму железо – цементит с буквенными обозначениями линий ликвидус, солидус, перитектических, эвтектических, эвтектоидных превращений , PQ, PG, GS, SE. Используя диаграмму, для заданного сплава постройте кривую охлаждения (нагрева) и опишите превращения в соответствии с полученными критическими точками
итемпературами. Задание выдает преподаватель.
2.Охарактеризуйте сплав: сталь (доэвтектоидная, эвтектоидная, заэвтектоидная); чугун (доэвтектический, эвтектический и заэвтектический).
3.Позаданнойтемпературеопределитесоставфазданногосплаваисоотношениефаз.
Содержание отчета
В отчете указать название, цель работы, привести диаграмму Fe – Fe3C, кривую охлаждения (нагрева) сплава с критическими температурами, описать превращения в критических точках и определить соотношения фаз при заданной температуре.
Контрольные вопросы
1.Что такое диаграмма состояния сплавов?
2.В каких координатах строится диаграмма Fe – Fe3C?
43
3.Что позволяет определить диаграмма состояния?
4.Как строится диаграмма?
5.Что такое критические точки?
6.Какие линии диаграммы называются ликвидус и солидус?
7.Какие линии диаграммы называются линиями эвтектических и эвтектоидных превращений?
8.Назовите фазы, обладающие самой низкой твердостью; самой высокой твердо-
стью.
9.Отличаются ли по фазовому составу стали доэвтектоидные, эвтектоидная и заэвтектоидные при комнатной температуре?
10.Какой белый чугун (доэвтектический, эвтектический, заэвтектический) тверже
ипочему?
11.Назовите самый легкоплавкий сплав изучаемой системы.
ПРАКТИЧЕСКАЯ РАБОТА № 2
МЕТАСТАБИЛЬНЫЕ СТРУКТУРЫ СТАЛЕЙ
Цель работы: изучение особенностей свойств, условий получения метастабильных структур сталей.
Учебно-демонстрационные материалы, наглядные пособия: диаграмма систе-
мы железо – цементит, фотографии метастабильных макроструктур сталей.
Основные теоретические сведения
К метастабильным (неустойчивым, непостоянным) структурам относятся мартенсит, троостит и сорбит. Мартенсит образуется из аустенита при охлаждении стали в воде. При этом изменяется кристаллическая решетка железа, γ-железо превращается α-железо, (Feγ) → (Feα ). Feγ способно растворить до 2,14 % C, а Feα – не более 0,02 %. При быстром охлаждении углерод не успеет выйти из ячейки Feα. Он сохраняется в ней и сильно искажает ячейку Feα, это приводит к резкому увеличению количества дислокаций в металле. Этим и объясняется значительное повышение прочности и твердости стали при получении структуры мартенсита. Мартенсит представляет собой неустойчивый пересыщенный твердый раствор углерода в Feα. Сталь, имеющая структуру аустенита, немагнитна, обладает невысокой твердостью, но максимальной пластичностью и хорошо куется, прокатывается и штампуется.
Сталь со структурой мартенсита обладает наиболее высокими магнитными свойствами, имеет высокую твердость и минимальную пластичность. Ее нельзя ковать, прокатывать и штамповать. При микроисследовании мартенсит виден в виде штрихов и игл, расположенных под углом друг к другу. Их величина зависит от температуры нагрева
44

стали под закалку и времени выдержки в нагретом состоянии. Чем выше температура и длительнее выдержка, тем крупнее зерна аустенита и тем большими при охлаждении получаются иглы мартенсита.
Превращения при термической обработке доэвтектоидной стали марки 50 на стадии нагрева можно проследить по стальному уголку диаграммы Fe–Fe3C в соответствии с рисунком 2.1. Маркой 50 обозначают конструкционную качественную сталь, для которой гарантируются химический состав и механические свойства, содержание углерода около 0,5 %. Структура стали после отжига: феррит + перлит.
Нормальная температура нагрева под закалку определяется по формуле: t = Ac3 + (20 ÷ 50) °С.
Согласно рисунку 1.1 Aс3 = 780 °С. Тогда t = 800 ÷ 830 °C .
При температуре t сталь имеет структуру мелкозернистого аустенита, а после охлаждения в воде получает структуру мелкоигольчатого мартенсита, твердость, примерно равную HB 6000, и относительное удлинение δ ~ 0 %. Такая закалка называется полной. Если сталь нагреть до t1 > t (перегрев), то она получит структуру крупнозернистого аустенита, а после закалки – структуру крупноигольчатого мартенсита с той же твердостью, но с меньшей пластичностью. В силу большей хрупкости такая термическая обработка для детали является браком.
Рисунок 2.1 – Оптимальный интервал температур закалки углеродистых сталей
Нагревом до температуры t2 , меньшей 780 ºC (см. рисунок 2.1), но большей 727 ºC (недогрев), в стали формируется структура: аустенит + феррит. Сталь после закалки имеет резко различные свойства по сечению детали: места расположения мартенсита имеют
45
твердость HB 6000, а места расположения феррита – HB 800…1000. Этот брак обычно исправляют повторной закалкой по оптимальному режиму.
Закалка заэвтектоидной стали марки У12А имеет свои принципиальные отличия. Маркой У12А обозначают высококачественную инструментальную углеродистую сталь с содержанием около 1,2 % C. После специального отжига она имеет структуру: зернистый перлит + зерна цементита. Твердость такой стали HB не больше 2070, относительное удлинение δ ~ 15 %. Сталь легко обрабатывается резанием.
Сохранение твердых зерен избыточного цементита желательно в закаленной стали, поэтому заэвтектоидные стали всегда подвергаются неполной закалке. Температура их нагрева не зависит от количества углерода (см. рисунок 1) и определяется по формуле:
T = Ac1 + (20 ÷ 50) °С = 727 + (20 ÷ 50) °С = 750 ÷ 780 °C .
При нагреве до Ac1 структура стали не изменяется. При Ac1 зернистый перлит пре-
вращается в аустенит. При этом α-железо (Feα) местах соприкосновения феррита с зернами цементита превращается в γ-железо (Feγ), которое начинает растворять в себе цементит и образуется аустенит. Превращение Feα в Feγ и растворение цементита, входящего в состав перлита, начинается при Ac1 . Сталь получает структуру: мелкозернистый ау-
стенит + избыточные зерна цементита. Нагрев от Ac1 до Т увеличивает растворимость
углерода в аустените.
При температуре Т сталь имеет структуру: мелкозернистый аустенит + зерна цементита. В процессе охлаждения в воде аустенит превратится в мелкоигольчатый мартенсит, а цементит сохранится. В микроструктуре на фоне мартенсита прослеживаются мелкие светлые зерна цементита. Сталь с такой структурой имеет HB ~ 6600 и δ ~ 0 %.
Если заэвтектоидную сталь подвергнуть полной закалке, т. е. нагреть до точки T1 (перегрев), то зерна избыточного цементита полностью растворятся, сталь получит структуру крупнозернистого аустенита, а после быстрого охлаждения – структуру мартенсита и остаточного аустенита. Не весь аустенит превратится в мартенсит, т.к. в заэвтектоидных сталях окончание мартенситных превращений Мк происходит при отрицательных температурах, что не достижимо при охлаждении в воде.
Такая сталь обладает значительно меньшей твердостью, чем после неполной закалки, места расположения мартенсита имеют твердость HB 6000, а места расположения ау-
стенита – НВ 1600…2000.
Превращение остаточного аустенита в мартенсит возможно, если в качестве среды охлаждения использовать жидкий азот.
Закалка на мартентсит обеспечивается охлаждением углеродистых сталей в воде со скоростью выше критической. При более медленном охлаждении стали из аустенитного состояния, например в масле, аустенит при температуре 400–500 ºC распадается на высокодисперсную ферритно-цементитную смесь, называемую трооститом.
46

При еще более медленном охлаждении стали из аустенитного состояния, например в струе холодного воздуха, аустенит при температуре 500–650 ºC распадается на грубую ферритно-цементитную смесь, называемую сорбитом.
Рисунок 2.2 – Диаграмма изотермического распада аустенита при скоростях охлаждения
(V1 < V2 < V3 < V4 < Vк < V5)
Стали, после закалки имеют высокие внутренние напряжения, которые уменьшают отпуском. Эффективность его зависит от температуры нагрева и времени выдержки. Уменьшение напряжений объясняется повышением подвижности атомов в металле при нагреве. Чем выше нагрев, тем быстрее и большей степени происходит снижение внутренних напряжения в металле. Выдержка должна обеспечить полное завершение изменений по всему сечению детали. В металле они идут медленно, особенно при невысоких температурах.
Нагрев до температуры 150…250 ºC (низкий отпуск) не вызывает изменений структуры мартенсита в стали, приводит к снижению напряжений и незначительному снижению твердости, образуется структура в доэвтектоидных сталях – мартенсит отпуска, в заэвтектоидных – (мартенсит отпуска +карбиды).
При нагреве закаленной стали примерно до температур 350…450 ºC (средний отпуск) подвижность атомов в стали увеличивается настолько, что углерод начинает выходить из ячеек Feα в виде мелких зерен цементита. Количество дислокации в металле уменьшается, твердость стали падает, а пластичность возрастает, образуется структура троостит отпуска.
Если закаленную сталь нагреть выше 400…650 ºC (высокий отпуск), то подвижность частиц в металле настолько увеличится, что мелкие зерна цементита начнут сливаться. Это слияние и есть процесс превращения троостита в сорбит. При этом твердость стали уменьшается, а пластичность возрастает.
47
Троостит и сорбит, полученные из мартенсита при отпуске стали, называют соответственно трооститом отпуска и сорбитом отпуска.
Свойства стали со структурой троостита и сорбита зависят от количества углерода (таблица 2.1).
Таблица 2.1 – Свойства сталей со структурой троостит и сорбит
|
Доэвтектоидная сталь |
Эвтектоидная сталь |
Заэвтектоидная сталь |
||||||
Структура |
(0,5 % C) |
|
(0,8 % C) |
|
(1,2 % C) |
|
|||
|
|
|
|
|
|
|
|
|
|
|
HB, МПа |
|
δ, % |
HB, МПа |
|
δ, % |
HB, МПа |
|
δ, % |
Троостит |
4000 |
|
5 |
5000 |
|
3 |
5500 |
|
2 |
Сорбит |
2700 |
|
3 |
3200 |
|
5 |
3500 |
|
4 |
|
|
|
|
|
|
|
|
|
|
Порядок выполнения работы
1.Для детали из стали, заданного содержания углерода, определить температуры нагрева полной и неполной закалок. Содержание углерода назначает преподаватель. Для определения температуры закалки использовать стальной уголок диаграммы Fe – Fe3C. Объяснить особенности фазовых превращений в процессе нагрева и охлаждения.
2.Обосновать превращения при резком охлаждении стали с формированием неравно-
весных структур Мзак; Мзак+ Ц + Аост.
3.Пояснить, как изменятся свойства сталей, если доэвтектоидная сталь будет иметь структуру (М + Ф); а заэвтектоидная сталь структуру (М + Аост).
4.Объяснить особенности фазовых превращений в процессе отпуска (низкого, среднего, высокого).
5.Построить график термической обработки детали для получения заданной твердости, включая и отпуск.
Содержание отчета
В отчете указать название, цель работы, по стальному уголку диаграммы Fe – Fe3C объяснить превращения стали при нагреве и быстром охлаждении, изменение твердости в процессе закаливания, формирование неравновесной структуры и изменение структуры при повторном нагреве (отпуске). Сделать вывод о зависимости твердости закаливаемой стали от содержания углерода в сплаве и режима термической обработки детали.
Контрольные вопросы
1.Дайте определение мартенсита.
2.Какая структура называется трооститом?
3.Какая структура называется сорбитом?
4.Назовите самую твердую неравновесную структуру доэвтектоидной стали.
48
5.Охарактеризуйте брак термической обработки под названием «пережог».
6.Охарактеризуйте брак термической обработки под названием «недогрев».
7.Опишите структуру доэвтектоидной и заэвтектоидной сталей после полной за-
калки.
8.Опишите структуру доэвтектоидной и заэвтектоидной сталей после неполной
закалки.
БИБЛИОГРАФИЧЕСКИЙ СПИСОК
1.Воронин Н.Н. Материаловедение и технология конструкционных материалов для железнодорожной техники / Н.Н. Воронин [и др.]. – М.: Маршрут, 2004. – 456 с.
2.Берлин В.И. Транспортное материаловедение : учебник для вузов ж.-д. тр-та / В.И. Берлин, Б.В. Захаров, П.А. Мельниченко. – М.: Транспорт, 1982. – 287 с.
3.Марочник сталей и сплавов / В.Г. Сорокин, А.В. Волосникова, С.А. Вяткин [и др.]. – М.: Машиностроение, 1989. – 640 с.
4.Физико-механические свойства металлов и сплавов : методические указания к выполнению лабораторной работы по дисциплине МТКМ для студентов специальностей 190301, 190302, 190303, 190205, 190701 очной и заочной форм обучения / составитель Т.П. Лукоянчева. – Самара : СамГУПС, 2010. – 12 с.
5.Макро- и микроструктуры сталей и чугунов : методические указания к лабораторным работам по дисциплине МТКМ для студентов специальностей 190301, 190302, 190303, 190205, 190701 очной и заочной форм обучения / составитель Т.П. Лукоянчева. – Самара : СамГУПС, 2010. – 26 с.
6.Термическая обработка сталей : методические указания к выполнению лабораторных работ по дисциплине МТКМ для студентов специальностей 190301, 190302, 190303, 190205, 190701 очной и заочной форм обучения / составитель Т.П. Лукоянчева. – Самара : СамГУПС, 2010. – 15 с.
7.Шубина Н.Б., Белянкина О.В., Набатников Ю.Ф. Материаловедение : учебное пособие. – М.: Горная книга, 2012. – 162 с.
8.Макро- и микроанализ металлических материалов. Оптическая микроскопия : метод. указания к лабораторной работе по дисциплине «Материаловедение и технология конструкционных материалов» для специальности 180405 «Эксплуатация судовых энергетических установок» / сост. Ю.А. Зорин, М.С. Пушкин. – СПб.: Изд-воГМА им. адм.
С.О. Макарова, 2012. – 20 с.
8.Методические указания по выполнению расчетно-графической работы по разделу «Материаловедение» дисциплины «Материаловедение. Технология конструкционных материалов» для студентов специальности 190300 (23.05.03) очной и заочной формы
обучения / Ж.В. Самохвалова. – Самара : СамГУПС, 2015. – 21 с. 9. http://edu.tltsu.ru/er/er_files/book1882/book.pdf
49
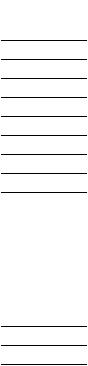
ПРИЛОЖЕНИЯ
|
|
|
|
|
|
|
|
Приложение 1 |
||
|
|
|
|
|
|
|
|
(справочное) |
||
|
|
Соотношение чисел твердости по Бринеллю и Роквеллу |
|
|
||||||
|
|
|
|
|
|
|
|
|
|
|
Твердость |
Твердость по Роквеллу |
Твердость |
Твердость по Роквеллу |
|||||||
по Бринеллю |
по Бринеллю |
|||||||||
|
|
|
|
|
|
|||||
Диаметр |
|
|
|
|
Диаметр |
|
|
|
|
|
отпечатка, |
НВ |
HRC |
HRB |
HRA |
отпечатка, |
HB |
HRC |
HRB |
HRA |
|
мм |
|
|
|
|
мм |
|
|
|
|
|
2,20 |
780 |
78 |
- |
84 |
4,00 |
229 |
20 |
100 |
61 |
|
2,30 |
712 |
68 |
- |
82 |
4,10 |
212 |
17 |
98 |
60 |
|
2,40 |
653 |
64 |
- |
80 |
4,20 |
207 |
14 |
95 |
59 |
|
2,50 |
601 |
60 |
- |
78 |
4,30 |
197 |
12 |
93 |
58 |
|
2,60 |
555 |
56 |
- |
77 |
4,40 |
187 |
9 |
91 |
57 |
|
2,70 |
514 |
52 |
- |
75 |
4,50 |
179 |
7 |
90 |
56 |
|
2,80 |
477 |
49 |
- |
74 |
4,60 |
170 |
4 |
88 |
55 |
|
2,90 |
444 |
46 |
- |
73 |
4,70 |
163 |
2 |
86 |
53 |
|
3,00 |
415 |
43 |
- |
72 |
4,80 |
156 |
0 |
84 |
52 |
|
3,10 |
388 |
41 |
- |
71 |
4,90 |
149 |
- |
82 |
- |
|
3,20 |
363 |
39 |
- |
70 |
5,00 |
143 |
- |
80 |
- |
|
3,30 |
341 |
36 |
- |
68 |
5,10 |
137 |
- |
78 |
- |
|
3,40 |
321 |
33 |
- |
67 |
5,20 |
131 |
- |
76 |
- |
|
3,50 |
302 |
31 |
- |
66 |
5,30 |
126 |
- |
74 |
- |
|
3,60 |
285 |
29 |
- |
65 |
5,40 |
121 |
- |
72 |
- |
|
3,70 |
269 |
27 |
- |
64 |
5,50 |
116 |
- |
70 |
- |
|
3,80 |
255 |
25 |
- |
63 |
5,60 |
111 |
- |
67 |
- |
|
3,90 |
241 |
23 |
102 |
62 |
5,70 |
107 |
- |
65 |
- |
Приложение 2
(справочное)
Качественные углеродистые стали (ГОСТ 1050)
|
|
|
|
Свойства после нормализации |
|
|||
Сталь |
С, % |
σв |
|
σ0,2 |
δ |
|
ψ |
НВ |
|
|
МПа |
|
|
% |
|||
|
|
|
|
|
||||
08 |
0,05 – 0,12 |
320 |
|
200 |
33 |
|
60 |
131 |
10 |
0,07 – 0,14 |
340 |
|
210 |
31 |
|
55 |
143 |
15 |
0,12 – 0,19 |
380 |
|
230 |
27 |
|
55 |
149 |
20 |
0,17 – 0,24 |
420 |
|
250 |
25 |
|
55 |
163 |
25 |
0,22 – 0,30 |
460 |
|
280 |
23 |
|
50 |
170 |
30 |
0,27 – 0,35 |
500 |
|
300 |
21 |
|
50 |
179 |
35 |
0,32 – 0,40 |
540 |
|
320 |
20 |
|
45 |
207 |
40 |
0,37 – 0,45 |
580 |
|
340 |
19 |
|
45 |
217 |
45 |
0,42 – 0,50 |
610 |
|
360 |
16 |
|
40 |
229 |
50 |
0,47 – 0,55 |
640 |
|
380 |
14 |
|
40 |
241 |
55 |
0,52 – 0,60 |
660 |
|
390 |
13 |
|
35 |
255 |
60 |
0,57 – 0,65 |
690 |
|
410 |
12 |
|
35 |
255 |
65 |
0,62 – 0,70 |
710 |
|
420 |
10 |
|
30 |
255 |
70 |
0,67 – 0,75 |
730 |
|
430 |
9 |
|
30 |
269 |
75 |
0,72 – 0,80 |
1100 |
|
900 |
7 |
|
30 |
285 |
80 |
0,77 – 0,85 |
1100 |
|
950 |
6 |
|
30 |
285 |
85 |
0,82 – 0,90 |
1150 |
|
1000 |
6 |
|
30 |
302 |
50