
методички / 4006
.pdf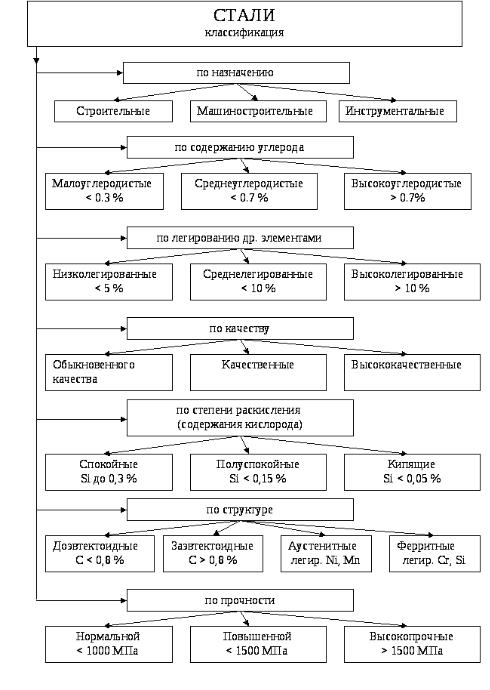
ствующей буквы. Если легирующего элемента около 1 % или менее, то цифра после буквы не ставится.
В инструментальных сталях и в сталях с особыми свойствами количество углерода обозначается только одной цифрой, указывающей содержание углерода в десятых долях процента.
Для высококачественных сталей в конце обозначения марки ставят букву А. Некоторые марки сталей выделены в особые группы и обозначаются буквами,
стоящими в начале марки: быстрорежущие – Р, шарикоподшипниковые – Ш, для постоянных магнитов – Е, электротехнические – Э и другие.
Углеродистые и легированные стали можно классифицировать по многим параметрам (рис. 4.1).
Рисунок 4.1 – Схема классификации сталей
21
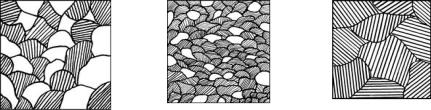
При суммарном содержании легирующих элементов до 5 % сталь является низколегированной, от 5 до 10 % − среднелегированной, более 10 % − высоколегированной.
Основные структурные составляющие легированных сталей − легированный феррит, легированный аустенит, легированный цементит и специальные карбиды.
Легирующие элементы образуют в стали карбиды, сульфиды и пр.; растворяются в решетке железа, искажая ее; влияют на полиморфное превращение в железе, тем самым, оказывая воздействие на состояние сплава. Введенные в сталь совместно легирующие элементы действуют иначе, чем в отдельности.
Легированный феррит представляет собой твердый раствор легирующих элементов в α-железе (феррите) и отличается от обычного феррита тем, что в его кристаллической решетке атомы железа частично замещены атомами легирующего элемента. Под микроскопом легированный феррит ничем не отличается от феррита углеродистой стали.
Легированный аустенит представляет собой твердый раствор легирующих элементов в γ-железе. Он наблюдается под микроскопом в виде однородных зерен, часто с наличием линии сдвига или двойников.
Легированный цементит представляет собой раствор легирующих элементов в карбиде железа Fе3С и отличается от цементита железа углеродистых сталей тем, что в его кристаллической решетке атомы железа частично замещены атомами карбидообразующих легирующих элементов. Под микроскопом легированный цементит ничем не отличается от обычного цементита углеродистых сталей.
Специальные карбиды − соединения легирующих элементов с углеродом. Они отличаются высокой твердостью и обычно большей, чем цементит, дисперсностью. Различают две группы карбидов: имеющие сложную кристаллическую решетку (Cr23C6, Cr3C7, Fe2W2C7) и имеющие простую кристаллическую решетку (W2C, WC, Mo2C, VC, TiC). Под микроскопом специальные карбиды трудно отличить от цементита. Для выявления состава карбида применяются специальные реактивы и методы травления. Некоторые специальные карбиды имеют специфическую форму, например, карбид титана имеет форму кубиков.
По структуре легированные стали делятся на пять классов: перлитный, мартенситный, ферритный, аустенитный и карбидный.
К перлитному классу относятся низколегированные стали, в которых, после нормализации, образуется перлитная (сорбитная, трооститная) структура.
Стали перлитного класса после |
|
|
|
||||
охлаждения на воздухе из аусте- |
|
|
|
||||
нитного |
состояния |
образуются |
|
|
|
||
перлитные структуры (перлит, |
|
|
|
||||
сорбит |
или |
троостит), которые |
|
3ОХГСА |
70С3А после полно- |
||
отличаются |
друг от |
друга раз- |
3ОХГСА |
||||
после нормализации |
го отжига от 860 °С |
||||||
личной |
дисперсностью пластин |
после полного |
|||||
от 880 °С |
(пластинчатый |
||||||
отжига от 880 °С |
|||||||
карбидов и легированного фер- |
(сорбит и феррит) |
перлит) |
|||||
рита |
|
|
|
(тонкопластинчатый |
|
|
|
|
|
|
перлит и феррит) |
|
|
||
|
|
|
|
|
|
22
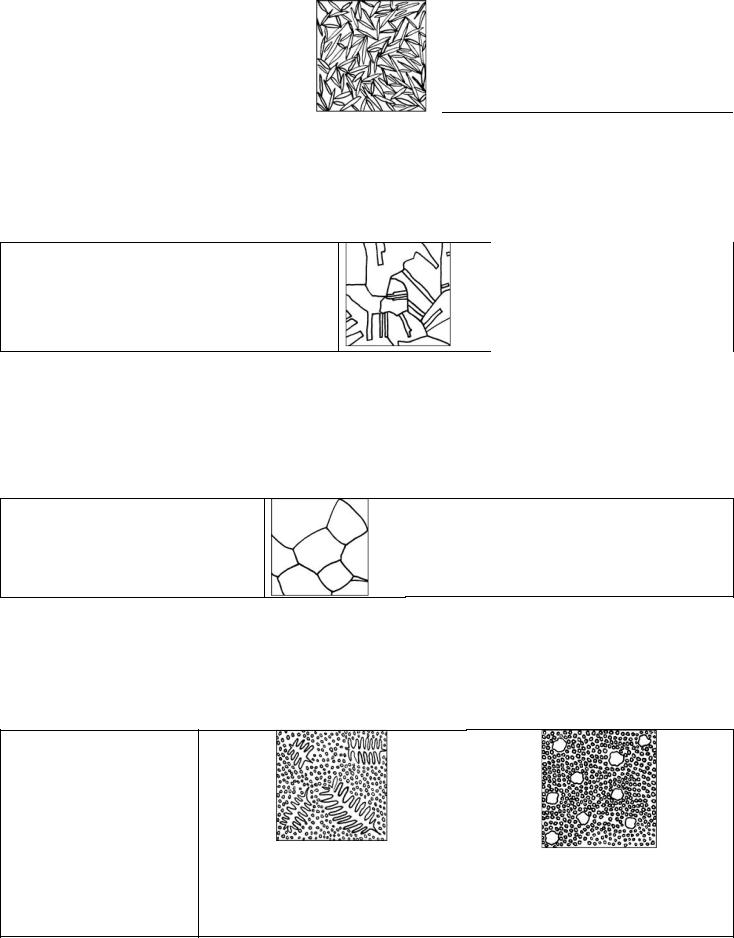
К мартенситному − среднелегированные стали, наличие легирующих элементов в которых обеспечивает образование мартенситной структуры.
Стали мартенситного класса при ох- |
|
Сталь 20Х2Н4А после нормализации |
лаждении из аустенитного состоянии на |
|
от 1050 °С (мартенсит |
воздухе сталь закаливается на мартен- |
|
и остаточный аустенит) |
ситную структуру |
|
|
|
|
|
К аустенитному − высоколегированные стали, в которых при нормализации не происходит превращение аустенита, и он полностью сохраняется в стали при комнатной температуре (приложение 4).
Стали аустенитного класса стали состоят из аустенитной структуры с характерными прямолинейными границами двойникования внутри зерен
Сталь 12ХН18Н9Т после закалки от 1050 °С в воде (аустенит)
К ферритному − стали, легированные значительным количеством элементов, расширяющих область α-твердого раствора (феррита). Такие стали не испытывают аллотропических превращений и при любых температурах находятся в состоянии α-твердого раствора (приложение 4).
Ферритного класса стали кри-
сталлизуются с образованием Сталь Э42 (Феррит) структуры легированного феррита
К карбидному классу относятся в основном инструментальные стали с большим содержанием карбидообразующих элементов (Cr, W, Mo, Ti). Структура сталей этого класса состоит из перлитной, мартенситной или аустенитной основы и большого количества карбидов.
Стали карбидного класса (ледебуритного клас-
са) содержат в структуре первичные карбиды, выделившиеся из жидкой фaзы при кристаллизации и вторичные, входящие в состав эвтектики – ледебурита
Сталь Р18 в литом состоянии |
Сталь Р18 после обработки давлени- |
(ледебурит, аустенит и эвтектоид) |
|
|
ем – ковки и отжига (крупные пер- |
|
вичные и мелкие вторичные карби- |
|
ды, мелкозернистый перлит) |
|
|
23
Конструкционные легированные стали
Строительные стали (09Г2, 17ГС). Термической обработке их не подвергают. Структура их − легированный феррит и перлит.
Машиностроительные стали делятся на цементуемые и улучшаемые. Цементуемые стали после отжига имеют в структуре легированный феррит и перлит, а некоторые и мартенсит (20Х, I2XH3A и др.). После цементации, закалки и низкого отпуска в структуре поверхностного слоя образуется мелкоигольчатый мартенсит (могут быть карбидные включения). Структура сердцевины при сплошной прокаливаемости – малоуглеродистый мартенсит и феррит легированные.
Улучшаемые стали (40Х, 45ХГ, 38ХМЮА) после отжига при температуре 860 °С состоят из перлита и феррита легированного, т. е. металлографически не отличаются от структуры углеродистой стали. Эта сталь подвергается объемной закалке с 860 °С в масле и последующему отпуску при 520 °С. Структура стали – сорбит легированный, сохранивший ориентировку мартенсита.
Пружинно-рессорные стали (65Г, 50С2, 55СГ) подвергают закалке и среднему отпуску на структуру троостита (троостит легированный).
Подшипниковые стали (ШХ9, ШХ15) подвергаются неполной закалке с низким отпуском. Получается структура мартенсита легированного с мелкими карбидами. Стали с такой структурой обладают высокой износостойкостью и пределом выносливости.
Высокомарганцовистые износостойкие стали аустенитного класса (Г1З, 110Г1ЗЛ).
Сталь имеет структуру легированного аустенита с избыточными карбидами (Fе, Mg3) С. После литья детали закаливают нагревом до 1000−1100 °C с последующим охлаждением в воде или на воздухе. Закаленная сталь обладает твердостью НВ 2000. Твердость стали повышается после сильного наклепа, т. к. в условиях ударного воздействия в поверхностном слое стали образуется большое количество дефектов кристаллического строения (дислокации, дефекты упаковки). В результате твердость поверхности повышается до НВ 6000 и сталь становится износостойкой. Применяют для крестовин железнодорожных и трамвайных путей, зубьев ковшей экскаваторов, для щек дробилок.
Инструментальные легированные стали
Стали для штампов и других инструментов холодной обработки металлов давлением должны обладать высокой твердостью, сочетающейся с удовлетворительной вязкостью. Данным требованиям удовлетворяют стали Х12, Х12М, Х12Ф1, Х6ВФ и др. Более высокой теплостойкостью должны обладать стали для штампов горячей обработки металлов давлением. В этом случае применяют стали 5ХНМ, 5ХНВ, 3Х2В8Ф и другие с твердостью после термической обработки 35−45 HRC, структура – троостит легированный.
Низколегированные инструментальные стали (Х9, ХВГ, X, 9ХС) после неполной закалки и низкого отпуска состоят из мартенсита отпуска легированного и легированного цементита.
24
Быстрорежущая сталь (Р9, P18) в равновесном состоянии относится к ледебуритному классу. Структура такой стали после литья будет состоять из перлита, ледебурита и вторичных карбидов. Для разрушения ледебуритной эвтектики и равномерного распределения карбидов, а также для подготовки структуры к последующей термической обработке эта сталь после литья подвергается ковке и отжигу, структура стали изменяется на сорбит с большим количеством равномерно распределенных вторичных и первичных карбидов. Окончательная термическая обработка быстрорежущей стали заключается в неполной закалке при 1250−1300 °С и трехкратного низкого отпуска при температуре 560 °С. Структура закаленной стали состоит из мартенсита легированного, первичных карбидов и значительного количества остаточного легированного аустенита (до 40 %). В процессе многократного отпуска из остаточного аустенита выделяются дисперсные карбиды, что ведет к обеднению аустенита углеродом и легирующими элементами. Структура после однократного отпуска состоит из мартенсита, первичных карбидов и отдельных участков нераспавшегося аустенита (светлый фон в поле микрошлифа). После трехкратного отпуска структура состоит из мартенсита и первичных карбидов, аустенита не более 3 %.
Коррозионно-стойкие и жаропрочные стали
Коррозионно-стойкие стали устойчивы к коррозии в воздушной атмосфере, морской и речной воде, а также в некоторых агрессивных средах при разных температурах.
Жаропрочные стали способны противостоять механическим нагрузкам при высоких температурах, обладают высокими значениями предела ползучести и длительной прочностью. По структуре делятся на несколько классов: перлитные, мартенситные, мар- тенситно-ферритные и аустенитные.
Стали мартенситного класса коррозионно-стойкие (20Х13, 30Х13 и др.), жаропрочные при температуре 500−600 °С (15Х11МФ, 40Х9С2 и др.) имеют структуру мартенсита легированного.
Стали аустенитного класса коррозионно-стойкие (12Х18Н9, 10Х14Г14Н10Т), жаропрочные при температуре 600−750 °С (45Х14Н14В2М, 40Х15Н7Г7Ф2МС и др.), после ТО имеют структуру аустенита легированного.
Стали ферритного класса являются коррозионно-стойкими (12Х17, 15Х25Т и др.), имеют структуру крупнозернистого легированного феррита с небольшим количеством карбида кремния. Стали имеют склонность к сильному росту зерна при нагреве, их подвергают рекристаллизационному отжигу.
Стали перлитного класса (15ХМ, 12Х1МФ и др.) являются жаропрочными при температуре 400−550 °С. После нормализации имеют структуру феррит + бейнит.
Стали аустенитно-мартенситного класса коррозионно-стойкие (09Х15Н8Ю и др.) после сложной ТО (закалка, обработка холодом, отпуск (старение)) имеют структуру мартенсита и аустенита.
25
Стали мартенситно-ферритного класса коррозионно-стойкие (12Х13 и др.), жаропрочные при 580−600 °С (15Х12ВМБФР) после закалки и отпуска имеют структуру мертенсит + феррит.
Стали аустенитно-ферритного класса (08Х21Н6М2Т и др.) имеют структуру аустенит + феррит.
Порядок выполнения работы
1.Изучите классификацию легирующих элементов, особенности маркировки и принципы классификации легированной стали по составу, назначению, структуре в равновесном состоянии и после охлаждения на воздухе из аустенитного состояния.
2.Рассмотреть структуры микрошлифов легированных сталей с помощью микроскопа, схематически зарисовать. Используя таблицу 4.2 описать и охарактеризовать структуры сталей.
3.Указать класс исследуемой стали по структуре в отожженном и нормализованном состоянии.
4.Исследовать особенности микроструктуры термически обработанных сталей, выявить характерные особенности их структурных составляющих.
5.Результаты исследований представить в таблице 4.1.
Таблица 4.1 – Результаты исследований микроструктуры и свойств легированных сталей
Марка стали |
Назначение |
Схема микроструктуры |
Структурные |
Свойства |
|
составляющие |
|||||
|
|
|
|
||
|
|
|
|
|
|
|
|
|
|
|
5.Определите химический состав конструкционных легированных сталей по их маркам: 12ХН9Т18, ХН77ЮР, 15Х28, 80НХС, 12Х25Н16Г7АР, 08Х14Н28В3Т3ЮР, 37Х12Н18МФ5, ШХ15СГ и др.
6.Определите химический состав инструментальных легированных сталей по их маркам: 7ХФ, Р10К5Ф5, 11ХФ, ХГС, 9Х5ВФ и др.
7.Определить области применения легированных сталей, используя Приложения 5 и Приложение 8.
7.Расшифровку марок сталей оформить в виде таблицы 4.2.
Таблица 4.2 – Марки легированных сталей, их химический состав и области применения
Марка стали |
Содержание |
Назначение |
Легирующие элементы |
Области |
|
|
углерода, % |
|
|
|
применения |
|
|
|
|
|
|
|
|
|
Обозначение |
Содержание, % |
|
|
|
|
легирующего |
|
|
|
|
|
элемента |
|
|
|
|
|
|
|
|
|
|
|
|
|
|
26
Содержание отчета
Отчет включает в себя цель работы; классификацию легированных сталей; зарисовки микроструктур легированных сталей с описанием особенностей; диаграммы состояния сплавов железо − легирующие элементы с открытой и замкнутой γ-областью (приложение 4), примеры расшифровок химического состава легированных сталей по их маркировкам.
Контрольные вопросы
1.Перечислите требования к цементуемым сталям.
2.Для чего предназначены цементуемые стали?
3.Опишите структуру сталей после улучшения.
4.Охарактеризуйте режимы упрочнения и структуру рессорно-пружинных сталей.
5.Какие классы легированных сталей бывают по структуре?
6.Подшипниковые, штамповые и инструментальные стали. Особенности структуры и свойства.
7.Назовите особенности структуры и свойств износостойких сталей.
8.Перечислите основные легирующие элементы коррозионно-стойких сталей.
9.Перечислите основные легирующие элементы жаропрочных сталей.
ЛАБОРАТОРНАЯ РАБОТА № 5
СТРУКТУРЫ ЧУГУНОВ
Цель работы: исследовать структуру, свойства, способы получение чугунов различного назначения, области применения.
Оборудование, материалы, наглядные пособия: металлографический микроскоп Метам РВ-22, микрошлифы чугунов, альбом фотографий микроструктур, плакат «структурные диаграммы чугунов».
Основные теоретические сведения
Белые чугуны (ГОСТ 805)
Чугуны – сплавы железа с углеродом и с другими элементами с содержанием углерода более 2 %.
Чугуны, в которых весь углерод находится в химически связанном состоянии в виде цементита, называются белыми. Поверхность излома таких чугунов светлая, блестящая. Представление о структурах белых чугунов дает диаграмма состояния железоуглеродистых сплавов. Чугуны с содержанием углерода до 4,3 % (левее точки С) называются
27
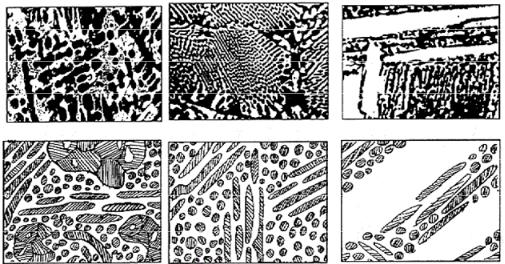
доэвтектическими, с содержанием углерода 4,3 % (точка С) – эвтектическими, с содержанием углерода более 4,3% (правее точки С) – заэвтектическими.
Характерной структурой в них является ледебурит вторичный ЛII (рисунок 5.1). Он представляет собой смесь цементита первичного с продуктами превращения аустенита (перлитом П и цементитом вторичным ЦII).
а) |
б) |
в) |
Рисунок 5.1 – Схемы микроструктур белых чугунов (верхний ряд ×100, нижний ряд ×500): а – доэвтектического; б – эвтектического; в – заэвтектического
Фазовый состав доэвтектических белых чугунов ЛII + П + ЦII. В заэвтектических белых чугунах присутствует ЛII и ЦI. Цементит в них просматривается в виде светлых пластин, расположенных под углом друг к другу, а перлит − в виде темных. При частичной графитизации цементита в структуре белого чугуна появляется графит. Такие чугуны называются половинчатыми.
Белый чугун получают при быстром охлаждении расплавленного металла с незначительным количеством кремния. Чугуны очень твердые, хрупкие, трудно обрабатываются резанием. Твердость эвтектического чугуна НВ 5500. Белые чугуны применяют для изготовления ковкого чугуна и стали, поэтому их часто называют передельными чугунами. Из белых чугунов изготавливают изделия – прокатные валки. Они имеют твердую износостойкую поверхность (отбеленную корку) и более пластичную, вязкую сердцевину (серый чугун).
Половинчатые чугуны применяют в качестве фрикционного материала, работающего в условиях сухого трения (тормозные колодки) и детали повышенной износостойкости (прокатные, мукомольные валки).
Серые чугуны (ГОСТ 1412)
Серым называют чугун, в котором часть или весь углерод находится в свободном состоянии в виде графита, имеющего в плоскости микрошлифа форму прямолинейных или слегка изогнутых пластин (рисунок 5.2).
28
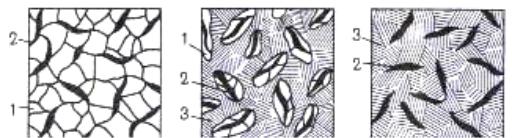
а) |
б) |
в) |
Рисунок 5.2 – Схемы микроструктур серых чугунов:
а – ферритного; б – ферритно-перлитного; в – перлитного: 1 – феррит, 2 – графит, 3 – перлит
Графит придает излому чугуна темно-серый цвет. Кроме железа и углерода в серых чугунах содержится кремний, а также марганец, фосфор и сера.
В машиностроении наиболее широкое применение получили доэвтектические чугуны, содержащие 2,4…3,8 % углерода. Чем больше количество углерода в чугуне, тем больше в нем графитовых включений, что приводит к снижению механических свойств чугунов. Уменьшение содержания углерода снижает жидкотекучесть чугуна (способность полностью заполнять литейную форму).
Кремний в качестве присадки при выплавке чугуна способствует графитизации. На повышение графитизации влияют увеличение углерода, введение меди, никеля. Марганец затрудняет графитизацию, способствует отбеливанию. Содержание марганца в серых чугунах не превышает 1,4 %. Аналогичное влияние оказывает сера и хром.
Фосфор оказывает двоякое влияние на чугун. Содержание фосфора в сером чугуне не должно превышать 0,2 %, так как образуется «фосфидная эвтектика». Присутствие ее обуславливает повышение твердости и хрупкости. Однако фосфидная эвтектика имеет низкую температуру плавления (950 ºС) и улучшает литейные свойства. Чугуны с повышенным содержанием фосфора (до 1 %) применяются для художественного литья. Отливки, к которым предъявляются повышенные требования по износоустойчивости, изготовляются из чугунов с содержанием фосфора до 0,7 %.
Сера − ухудшает литейные свойства чугуна, снижает жидкотекучесть, увеличивает усадку и склонность к образованию трещин.
Структура серого чугуна состоит из металлической основы (стальной) и графитовых включений. Особенности формирования структуры зависят не только от химического состава, но и от скорости охлаждения в процессе первичной кристаллизации. При данном содержании углерода и кремния в чугуне его графитизация тем полнее, чем медленнее отводится тепло (толстостенные отливки). Наглядное представление о влиянии углерода, кремния и скорости охлаждения на степень графитизации чугунов дают структурные диаграммы чугунов (приложение 6). Свойства серого чугуна зависят от структуры металлической основы (ферритная, ферритно-перлитная, перлитная), формы, величины, количества и характера распределения графитовых включений.
Стандартные марки серых чугунов обозначаются буквами СЧ. Число в марке ука-
зывает на предел прочности при растяжении в размерности кгс/мм2. Например, СЧ20 −
29
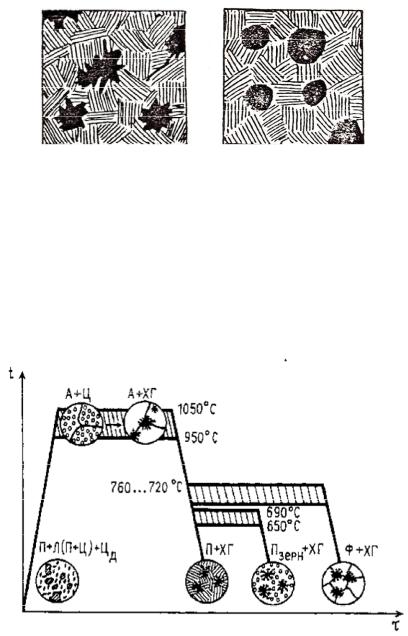
серый чугун с пределом прочности при растяжении 20 кгс/мм2 (200 МПа). Основные марки серых чугунов: СЧ 10; СЧ 15; СЧ 20; СЧ 25; СЧ 30; СЧ 35; СЧ 40; СЧ 45.
Для повышения механических свойств серого чугуна применяют модифицирование. Модифицирование включает операцию введения в расплав металла измельченного ферросилиция или силикокальция. Добавки измельчают структурные составляющие чугуна, положительно влияют на равномерность распределения графитовых включений. Чугуны марок СЧ 30, СЧ 35, СЧ 40, СЧ 45 относятся к модифицированным.
Ковкие чугуны (ГОСТ 1215)
К ковким относят чугуны с графитовыми включениями хлопьевидной формы (рисунок 5.3, а).
а) б)
Рисунок 5.3 – Схемы микроструктур ковкого перлитного (а) и высокопрочного перлитного(б) чугунов
Такой чугун получают в отливках, изготовленных из доэвтектического белого чугуна и подвергнутых последующему графитизирующему отжигу по заданному режиму (рис. 5.4). Отжиг приводит к распаду цементита и образованию графита.
Рисунок 5.4 – Схема получения ковкого чугуна
Механические свойства ковкого чугуна определяются структурой металлической основы (ферритная, ферритно-перлитная, перлитная) и степенью компактности включений
30