
методички / 4006
.pdfграфита. Наиболее высокими свойствами обладает ковкий чугун со структурой зернистого перлита основы. Твердость ковких чугунов колеблется в пределах 1630…2690 НВ.
Стандартные марки ковких чугунов включают предел прочности при растяжении и относительное удлинение. Например, КЧ 30-6 означает: ковкий чугун, предел прочности при растяжении 30 кгс/мм2 (300 МПа), относительное удлинение – 6 %. Из них изготавливают детали высокой прочности, работающие в тяжелых условиях износа, способные воспринимать ударные и знакопеременные нагрузки. Ковкие чугуны заменяют высокопрочными, так как отливки из них имеют ограниченные размеры сечения (не более 30…40 мм) и получают их в процессе длительной, дорогостоящей термической обработки.
Высокопрочные чугуны (ГОСТ 7293)
Высокопрочные чугуны получают модифицированием жидкого чугуна присадками магния, церия, иттрия и др. элементами. Чаще применяют магний в количестве 0,03…0,07 %. Под действием модификатора графит в процессе кристаллизации принимает шаровидную форму (рисунок 5.4, б).
Стандартные марки высокопрочного чугуна включают предел прочности при растяжении. Например, ВЧ 60 – высокопрочный чугун с шаровидным графитом, предел прочности при растяжении 60 кгс/мм2 (600 МПа). Марки высокопрочных чугунов: с ферритной металлической основой ВЧ 38; ВЧ 42; с ферритно-перлитной металлической основой ВЧ 45; ВЧ 50; с перлитной металлической основой ВЧ 60; ВЧ70; ВЧ 80; ВЧ 100; ВЧ 120. Твердость высокопрочных чугунов в пределах 1400…3800 НВ. Применяются как заменитель стали, ковкого и серого чугунов. По сравнению со сталью обладает большей износостойкостью, лучшими коррозионными и антифрикционными свойствами и обрабатываемостью резанием. Детали из высокопрочного чугуна: суппорты, резцедержатели, шпиндели, прокатные валки, коленчатые валы и др.
Антифрикционные чугуны (ГОСТ 1589)
Антифрикционные чугуны обладают удовлетворительной стойкостью против износа и низким коэффициентом трения. Применяют для изготовления подшипников, втулок и подобных деталей в качестве заменителей бронзы при сравнительно легких условиях работы. Графитовые гнезда на поверхности детали удерживают смазку и обеспечивают снижение трения. Подшипники из антифрикционных чугунов успешно работают в паре с валом, в узлах трения с температурой до 300 ºС, при повышенных окружных скоростях. Стандартные марки антифрикционных чугунов обозначаются тремя буквами и условным номером: АЧС–5, АЧК–2, АЧВ–1. Пример маркировки: АЧС–5: АЧ – антифрикционный, С – серый чугун с пластинчатым графитом (К – ковкий, В – высокопрочный). Порядковый номер присваивается по химическому составу и назначению. Чугуны отличаются по виду металлической основы: перлитная, перлитно-ферритная, ферритно-перлитная, аустенитная. Для получения заданной металлической основы чугуны легируют хромом, медью, никелем, титаном и другими элементами в различных сочетаниях и соотношениях.
31

Из чугунов специального назначения изготавливают детали жаростойкие (жаростойкость 700…800 ºС), марки – ЧС5, ЧХ28, ЧХ32, жаропрочные – ЧН19Х3Ш, ЧН11Г7Ш, коррозионностойкие – ЧС13, ЧС15, ЧХ22, ЧХ28, ЧС15М4, ЧН15Д7.
Порядок выполнения работы
1.Установить микрошлиф на предметный столик микроскопа. Настроить резкость вначале с помощью макро-, а затем микровинта. Рассмотреть различные поверхности микрошлифа, выбрать и зарисовать поверхность с наиболее четко выраженной микроструктурой.
2.В исследуемых микрошлифах белого, серого, ковкого, высокопрочного чугунов определить основные структурные составляющие и указать его марку.
3.Привести структурную диаграмму чугунов (приложение 6) и указать область, которой соответствует исследованный чугун, условия его получения и назначение.
4.Пользуясь Приложением 7 установит зависимость свойств (прочность, твердость, пластичность) чугунов от формы графитовых включений и соотношения феррита
иперлита.
5.Результаты исследований представить в таблице 5.1.
Таблица 5.1 – Результаты исследования микроструктуры и свойств чугунов
Марка чугуна |
Особенности |
|
Механические свойства |
|
||
структуры |
σв, МПа |
|
δ, % |
|
НВ |
|
|
|
|
||||
|
|
|
|
|
|
|
Содержание отчета
В отчете указать название, цель работы, изобразить микроструктуры чугунов по результатам микроскопических исследований и дать их описание (вид металлической основы, форма графитовых включений и т. д.). Начертить структурную диаграмму чугунов. Сделать выводы о зависимости свойств (НВ) от фазового состава и структуры, формы, величины и количества графитовых включений.
Контрольные вопросы
1.Какой чугун называют передельным и почему?
2.В чем принципиальное отличие между белым и серым чугунами?
3.В каком чугуне весь углерод находится в химически связанном состоянии?
4.Перечислите основные формы графитовых включений. В каких чугунах они встречаются?
5.Перечислите разновидности металлических основ чугунов.
6.Какие механические свойства включают марки чугунов?
32
7.Что такое фосфидная эвтектика чугунов? Опишите ее влияние на свойства чугунов.
8.Графит какой формы менее всего ослабляет металлическую основу чугуна?
9.Перечислите способы получения серого и высокопрочного чугунов.
10.Какой чугун превращают в ковкий и каким образом?
11.Какие преимущества имеют чугуны перед сталями?
12.Назовитемарку чугуновдляизготовленияколенчатоговала, зубчатогоколесаидр.
ЛАБОРАТОРНАЯ РАБОТА № 6
ТЕРМИЧЕСКАЯ ОБРАБОТКА СТАЛЕЙ
Цель работы: приобрести навыки изменения структуры и свойств сплавов в процессе отжига, нормализации, закалки и отпуска; установить зависимость твердости стали от температуры нагрева и скорости охлаждения при закаливании.
Оборудование и материалы: твердомер, печь нагревательная, емкости с охлаждающими средами (соленая вода, вода, масло), клещи, образцы из стали 40.
Основные теоретические сведения
Термическая обработка (ТО) сплавов – процесс тепловой обработки сплавов с целью изменения структуры, а следовательно, и свойств, заключающийся в нагреве до определенной температуры, выдержки и последующем охлаждении с заданной скоростью. Основные виды ТО: отжиг, нормализация, закалка, отпуск. Термической обработке подвергают как заготовки (кованные, штампованные, литые), так и детали машин и инструмент. Заготовки подвергают термической обработке для снижения твердости, а детали – для придания требуемых свойств: твердости, прочности, упругости, износостойкости и др.
Отжиг металлов – ТО, заключающаяся в нагреве металла или сплава, структура которого находится в неустойчивом состоянии в результате предшествующих механических обработок, выдержке при температуре нагрева и последующем медленном охлаждении для получения структур, близких к равновесному состоянию. Отжиг металлов проводят для улучшения обрабатываемости резанием, повышения пластичности, уменьшения остаточных напряжений. Основные виды отжига металлов: полный, неполный, рекристаллизационный, диффузионный (гомогенизация), изотермический.
Нормализация – ТО стали, заключающаяся в ее нагреве, выдержке и последующем охлаждении на воздухе. Нормализацию производят для улучшения механических свойств стали, а также для улучшения обрабатываемости стали резанием. Во многих случаях нормализация – операция, предшествующая закалке. При нормализации происходит перекристаллизация структуры стали, устраняющая крупнозернистую структуру, полученную при литье или ковке. В результате охлаждения на воздухе распад аустенита
33
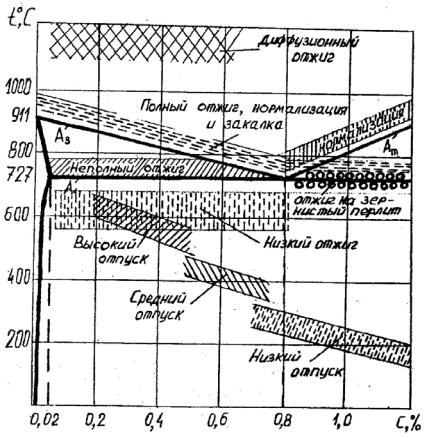
на ферритно-цементитную смесь происходит при более низких температурах и повышается дисперсность смеси фаз.
Рисунок 6.1 – Диаграмма температурного режима для различных видов термической обработки стали
Закалка стали также основана на фазовых превращения при нагреве и охлаждении, но отличается от отжига и нормализации тем, что охлаждение производят быстро. В зависимости от скорости охлаждения может произойти диффузионное превращение с распадом аустенита или бездиффузионное превращение аустенита в мартенсит. Наименьшая скорость охлаждения, при которой происходит превращение аустенита в мартенсит, на-
зывается критической скоростью закалки.
В процессе закалки получают неравновесные, нестабильные (метастабильные) структуры: мартенсит закалки, мартенсит закалки с цементитом (карбидом железа).
Выбор способа ТО зависит от химического состава стали, требуемых свойств и особенностей конфигурации изделий. Для каждого вида ТО детали необходимо правильно выбрать основные параметры процесса: температуру и скорость нагрева, продолжительность выдержки в нагретом состоянии, скорость и среду охлаждения.
При промышленных скоростях нагрева под отжиг или закалку перлит вплоть до температуры Ac1 сохраняет пластинчатое строение. Превращение перлита в аустенит при
достижении температуры Ac1 включает два параллельно идущих процесса: полиморфное превращение Feα (C0,02 )→ Feγ (C0,02 ) и растворение в Feγ (C0,02 ) кристаллов цементита при
34
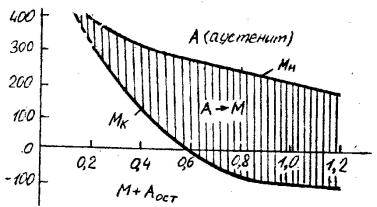
температурах (Ac1 до Ac3 ). Чем выше температура нагрева и чем длительнее выдержка,
тем крупнее будут кристаллы аустенита.
По скорости роста аустенитовых зерен различают природно-крупнозернистые и природно-мелкозернистые стали. Стали, имеющие грубую крупнозернистую структуру вследствие высокотемпературного нагрева, называют перегретыми. Перегрев исправляют повторной аустенизацией (нагрев выше линии АС3 на 30÷50 ºС).
От размеров кристаллов аустенита в большей мере зависят свойства продуктов превращения после охлаждения. Сплавы, структура которых образовалась при превращениях мелкозернистого аустенита, имеют высокую пластичность и вязкость и меньшую чувствительность к концентраторам напряжений.
Повышение скорости охлаждения с υ1 до υкр приводит к снижению температуры (727 ºС) перлитного превращения. При непрерывном охлаждении превращение развивается в интервале температур от +400 ºС до –100 ºС. Повышение скорости охлаждения также приводит к увеличению дисперсности образующихся ферритно-цементитных смесей, перлит заменяется сорбитом, а затем трооститом.
При скоростях охлаждения больших, чем υкр, аустенит переохлаждается до температуры Мн (начало превращения аустенита). Бездиффузионное мартенситное превращение происходит в интервале температур Мн – Мк (температура конца превращения). Каждой температуре в этом интервале соответствует определенная доля распавшегося аустенита (рисунок 6.2).
Рисунок 6.2 – Зависимости температур начала и конца мартенситных превращений (Мн и Мк) от содержания углерода
Отпуск – ТО сплавов, осуществляемая после закалки. Деталь нагревают до температур ниже Ac1 , выдерживают при заданной температуре и охлаждают. Различают три
вида отпуска: низкий (150÷250 ºС), средний (350÷450 ºС) и высокий (400÷650 ºС). Отпуск может быть однократный и многократный.
В процессе отпуска происходит: распад мартенсита с выделением углерода в виде карбидов, распад остаточного аустенита с превращением в мартенсит, коагуляция карби-
35
дов, уменьшение несовершенств кристаллического строения мартенсита и снижение остаточных напряжений.
Улучшение – двойная термообработка железоуглеродистых сплавов, заключающаяся в закалке на мартенсит с последующим высоким отпуском (550÷650 ºС). После улучшения сталь приобретает структуру сорбита отпуска. Такая сталь обладает достаточной прочностью, пластичностью и ударной вязкостью.
Порядок выполнения работы
1.У четырех образцов стали 40 определить твердость до термообработки по шкале HRB, полученные значения перевести в значения твердости по шкале HB .
2.Образцы загрузить в муфельную печь, включить печь и нагреть до 650 ºС. После выдержки 10 минут, при заданной температуре нагрева, один образец взять щипцами, опустить в соленую воду и охладить, постоянно вращая его. Таким же образом готовить образцы, нагретые до температур 750, 850, 950 ºС.
3.Наждачной бумагой снять окалину с поверхности образца.
4.Определить твердость образцов после охлаждения по шкале HRB для образцов, нагретых в печи до температур 650, 750 ºС и по шкале HRC – для образцов, нагретых до температур 850, 950 ºС. Результаты испытаний представить в таблице 6.1.
Таблица 6.1 – Твердость образцов (С = 0,4 %), охлажденных после нагрева в соленой воде
№№ |
Твердость ото- |
Температура |
Твердость после |
|
Структура стали |
||||
образца |
жженных образцов |
нагрева, ºС |
закалки |
|
|
|
|
||
|
|
|
|
|
|
|
|
|
|
|
HRB |
HB |
|
HRВ |
HB |
до |
|
нагретой |
после |
|
|
|
|
(HRС) |
|
нагрева |
|
|
охлажд. |
|
|
|
|
|
|
|
|
|
|
|
|
|
|
|
|
|
|
|
|
5.Перевести значения твердости HRB и HRС в значения твердости по шкале HB, используя приложение 1. Построить график HB = f (tнагр) для υохл = const.
6.Структуру стали, нагретой до разных температур, определить по диаграмме Fe –
Fe3C.
7.Комплект из пяти образцов погрузить в печь и нагреть печь до температуры, обеспечивающей получение максимальной твердости (tнагр = const), выдержать при температуре нагрева 10 минут, а затем щипцами поочередно вынуть их из печи для охлаждения.
8.Охлаждать один образец в отключенной печи (lg υ = 0), второй – на спокойном воздухе рядом с печью (lg υ = 1,2), а третий, четвертый и пятый соответственно, в жидких средах: соленая вода (lg υ = 3,0), пресная вода (lg υ = 2,8), масло (lg υ = 2,2). Охлаждение в жидких средах проводить с вращением образцов после погружения.
9.Удалить окалину с торца образцов.
36
10. Определить твердость на твердомере по шкале HRB для образцов, охлаждавшихся на воздухе и с отключенной печью, и по шкале HRС – для образцов, охлаждавшихся в жидких средах. Результаты испытаний представит в таблице 6.2.
Таблица 6.2 – Твердость образцов (С = 0,4 %), охлажденных после нагрева в разных средах
№№ |
Температура |
Охлаждение |
Твердость |
|
Структура стали |
|
||||
образцов |
нагрева, °С |
|
|
после ТО |
|
|
|
|
|
|
|
|
|
|
|
|
|
|
|
|
|
|
|
среда |
скорость |
HRВ |
HB |
до |
|
нагретой |
|
после |
|
|
|
lg υ |
(HRС) |
|
нагрева |
|
|
|
охлажд. |
|
|
|
|
|
|
|
|
|
|
|
|
|
|
|
|
|
|
|
|
|
|
11. Перевести значения твердости НRВ и НRC в значения твердости по шкале Бринелля HB, используя приложение 1. Построить график HB = f (υохл) для tнагр = const.
Содержание отчета
Отчет включает в себя название, цель работы, таблицы результатов определения твердости сталей в зависимости от температуры нагрева и скорости охлаждения , графики НВ = f(tнагр) и НВ = f(υохл). Вывод по работе: значения оптимальной температуры нагрева стали 40 при закаливании и критическая скорость охлаждения.
Контрольные вопросы
1.Что такое закалка сталей и каковы ее цели?
2.Почему повышается твердость стали после закалки?
3.Назовите характерные особенности мартенситного превращения.
4.Изменится ли твердость стали, нагретой до температуры ниже Ac1 , после быст-
рого охлаждения?
5.Зависит ли оптимальная температура нагрева при закалке доэвтектоидной стали от содержания углерода?
6.Почему перегрев стали значительно выше Ac3 приводит к снижению ее твердо-
сти после быстрого охлаждения?
7.Опишите структуру доэвтектоидной стали, нагретой до температуры в интервале Ac1 – Ac3 , после быстрого охлаждения.
8.Что такое полная и неполная закалка стали?
9.Структура доэвтектоидной и заэвтектоидной сталей после полной закалки.
10.Структура доэвтектоидной и заэвтектоидной сталей после неполной закалки.
11.Какая закалка рекомендуется для доэвтектоидной и заэвтектоидной сталей?
12.Почему твердость мартенсита повышается с увеличением содержания углерода?
13.Как влияет содержание углерода в сталях на количество остаточного аустенита?
14.Что такое обработка холодом? Каковы ее цели?
37
15.Какие механические и физические свойства закаленной стали изменяются при обработке холодом?
16.Что такое отпуск закаленной стали?
17.Структурные изменения в закаленной на мартенсит стали при увеличении температур отпуска.
18.Как изменяются характеристики механических свойств закаленных сталей при повышении температур отпуска?
19.Что такое улучшение стали?
20.Структура стали состоит из мартенсита. Какая это сталь (доэвтектоидная или заэвтектоидная)? Какому виду закалки она подвергалась?
21.Значения температур Мн и Мк для заэвтектоидных и доэвтектоидных сталей.
2 ПРАКТИЧЕСКИЕ РАБОТЫ
ПРАКТИЧЕСКАЯ РАБОТА № 1
ЭЛЕМЕНТАРНЫЕ СТРУКТУРЫ ЖЕЛЕЗОУГЛЕРОДИСТЫХ СПЛАВОВ СИСТЕМЫ Fe – Fe3C
Цель работы: изучить диаграмму Fe – Fe3C системы и установить зависимости между свойствами сплавов в равновесном состоянии, их фазовым составом и содержанием углерода.
Учебно-демонстрационные материалы, наглядные пособия: диаграмма систе-
мы железо – цементит, фотографии макроструктур углеродистых сталей и технического железа.
Основные теоретические сведения
Диаграмма состояния сплава – графическое изображение зависимости состояния сплава от температуры и концентрации компонентов сплава. Она позволяет определить температуры начала и конца плавления сплавов, их фазовый состав в условиях равновесия при различных температурах и концентрации компонентов, позволяет охарактеризовать многие физико-химические, механические и технологические свойства (литейные, ковочные, свариваемость, обрабатываемость резанием и др.) сплавов. Анализ диаграммы состояния позволяет решать инженерные задачи материаловедения и технологии конструкционных материалов. Диаграмма состояния железо – цементит представлена на рисунке 1.1.
38
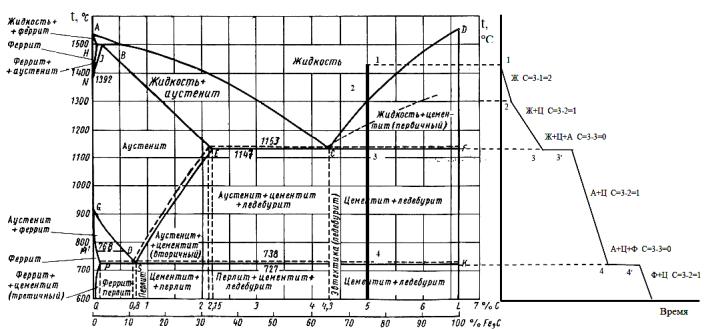
Рисунок 1.1 – Диаграмма состояния железо – цементит и линия охлаждения для сплава с содержанием углерода 5 %
Сплавы, содержащие менее 2,14 % углерода, называются сталями, более 2,14 % углерода – чугунами.
Сталь, содержащая менее 0,8 % углерода называется доэвтектоидной, 0,8 % углерода – эвтектоидной, более 0,8 % углерода – заэвтектоидной. Чугун до 4,3 % углерода называются доэвтектическим, 4,3 % углерода – эвтектическим чугуном, более 4,3 % углерода – заэвтектическим.
Превращения в зависимости от состава сплава и температуры могут протекать различно, следовательно, сплавы имеют разные температурные кривые охлаждения (нагревания) и критические точки структурных и фазовых превращений. Превращения в сплавах происходят как при затвердевании жидкой фазы (первичная кристаллизация), так и в твердом состоянии (вторичная кристаллизация).
Первичная кристаллизация ограничена интервалом температур линий ликвидус (ABCD) и солидус (AHJECF). Вторичная кристаллизация вызвана полиморфными превращениями железа и изменением растворимости углерода в аустените и феррите.
Всистеме железо – углерод выделяют сплавы с превращениями: перитектическим
идоэвтектоидным (0,16…0,5 % С), доэвтектоидным (менее 0,8 % С); эвтектоидным (0,8 % С); заэвтектоидным (0,8…2,14 % С); доэвтектическим (2,14…4,3 % С), эвтектическим (4,3 % С), заэвтектическими (4,3…6,67 % С).
Изотермические превращения в системе железо − цементит:
- перитектическое превращение на линии HJB (1499 ºС), в сплавах с содержанием углерода 0,16…0,5 % имеет место превращение феррита высокотемпературного (Фв) в аустенит
Жв + Фн → Аj;
39
- эвтектическое превращение на линии ECF (1147 ºС) сопровождается кристаллизацией двух твердых фаз и образованием механической смеси ледебурита
Жс → АЕ + ЦI → ЛI;
который при температуре 727 ºС превращается в ледебурит ЛII, т. е. смесь
П+ ЦI → ЛII;
-эвтектоидное превращение на линии PSK (727 ºС) – результат распада твердого
раствора А0,8 на феррит и цементит
Аs → Фp + ЦII.
Все сплавы изучаемой системы отличаются по химическому составу и имеют свои критические точки структурных и фазовых превращений. Критические точки (и соответствующие им критические температуры) – это температуры, при которых изменяется агрегатное состояние или фазовый состав в металлах и сплавах при нагреве от температуры окружающей среды или при охлаждении от температуры выше линии ликвидус до обычной. Определяют их путем замера изменения теплофизических свойств: температуры (термический анализ), теплового расширения (дилатометрический анализ) и др. Методом термического анализа замеряют изменение температуры через заданный интервал времени, строят кривую охлаждения (нагрева), на которой фиксируются критические точки в виде площадок или перегибов. Значения критических точек нескольких сплавов с разной концентрацией компонентов определяют положение основных точек линий диаграммы состояния (ликвидус, солидус, эвтектических и эвтектоидных превращений и др.).
Взависимости от температуры и концентрации углерода железоуглеродистые сплавы имеют следующие структурные составляющие: жидкий раствор (Ж), феррит (Ф), аустенит (А), перлит (П), ледебурит (Л), цементит (Ц) и свободный углерод в виде графита (Гр).
Феррит – твердый раствор внедрения углерода в Feα. Различают высокотемпературный и низкотемпературный феррит. Феррит – мягкая пластичная фаза с НВ
800…1000, δ = 40 %.
Аустенит – твердый раствор внедрения углерода в Feγ. Аустенит пластичен, но тверже феррита (НВ 1600…2000) при температуре 20–25 ºС.
Цементит – карбид железа Fe3C, тверд (НВ 8000) и хрупок.
Вжелезоуглеродистых сплавах присутствуют фазы: цементит первичный, цементит вторичный, цементит третичный. Химические и физические свойства этих фаз одинаковы. Влияние на механические свойства сплавов оказывает различие в размерах, количестве и расположении этих выделений. Цементит первичный выделяется из жидкой фазы в виде крупных пластинчатых кристаллов. Цементит вторичный выделяется из аустенита и располагается в виде сетки вокруг зерен аустенита (при охлаждении – вокруг зерен перлита). Цементит третичный выделяется из феррита и в виде мелких включений располагается у границ ферритных зерен.
40