
- •Оглавление
- •ОБЩИЕ СВЕДЕНИЯ
- •ЛАБОРАТОРНАЯ РАБОТА 1 ПОЛУЧЕНИЕ ПОРОШКОВ ЖЕЛЕЗА ВОССТАНОВЛЕНИЕМ ОТХОДОВ МЕТАЛЛООБРАБОТКИ ТВЕРДЫМ УГЛЕРОДОМ
- •ЛАБОРАТОРНАЯ РАБОТА 2 ПОЛУЧЕНИЕ ПОРОШКОВ МЕТАЛЛОВ МЕТОДОМ ЦЕМЕНТАЦИИ
- •ЛАБОРАТОРНАЯ РАБОТА 5 ОПРЕДЕЛЕНИЕ ПЛОТНОСТИ, ПОРИСТОСТИ СФОРМОВАННЫХ И СПЕЧЕННЫХ ПОРОШКОВЫХ МАТЕРИАЛОВ
- •ЛАБОРАТОРНАЯ РАБОТА 6 МЕТАЛЛОГРАФИЧЕСКОЕ ИССЛЕДОВАНИЕ СПЕЧЕННЫХ МАТЕРИАЛОВ
- •ЛАБОРАТОРНАЯ РАБОТА 7 ОПРЕДЕЛЕНИЕ ТВЕРДОСТИ СПЕЧЕННЫХ ПОРОШКОВЫХ МАТЕРИАЛОВ
- •ЛАБОРАТОРНАЯ РАБОТА 8 ОПРЕДЕЛЕНИЕ ЭФФЕКТИВНОЙ ГЛУБИНЫ УПРОЧНЕННОГО СЛОЯ
- •БИБЛИОГРАФИЧЕСКИЙ СПИСОК
- •ПРИЛОЖЕНИЕ

ЛАБОРАТОРНАЯ РАБОТА 2 ПОЛУЧЕНИЕ ПОРОШКОВ МЕТАЛЛОВ МЕТОДОМ ЦЕМЕНТАЦИИ
Цельработы
Получение порошка меди методом цементации путем перемешивания раствора с цементируемым порошком.
Задачиработы
Изучить теоретические основы получения порошков методом цементации; на примере технологии получения порошков меди определить влияние параметров процесса на механизм реакции цементации и свойства получаемых материалов; определить свойства полученных порошков.
Краткиетеоретическиесведения
Цементация – это электрохимический процесс, который часто называют контактным восстановлением, или внутренним электролизом (металл с более отрицательным потенциалом вытесняет из раствора металл с более положительным потенциалом, переходя при этом в раствор). Электрохимическую реакцию между металлом цементатором и ионами вытесняемого металла в общем виде можно записать следующим образом:
Z2Me1Z1+ + Z2M10 → Z2Me10 + Z1Me2Z2+
где Z1, Z2 – заряды ионов или валентности вытесняемого металла и металлацементатора.
Для прохождения подобной реакции слева направо вытесняющий металл должен иметь более отрицательный электродный потенциал (табл. 2.1).
По мере выделения Ме1 его концентрация в растворе уменьшается и, следовательно значение потенциала становится более отрицательным, а для цементирующего металла Ме2 – наоборот. Процесс вытеснения Ме1 из раствора будет протекать до установления равновесия, когда ϕМе1 = ϕМе2.
Из приведенных в табл. 2.1 данных видно, что некоторые металлы можно практически полностью выделить из раствора. Однако при этом необходимо учитывать, что в результате связывания металлических ионов в
Процессы порошковой металлургии. Метод. указания к лабораторным работам |
-21- |
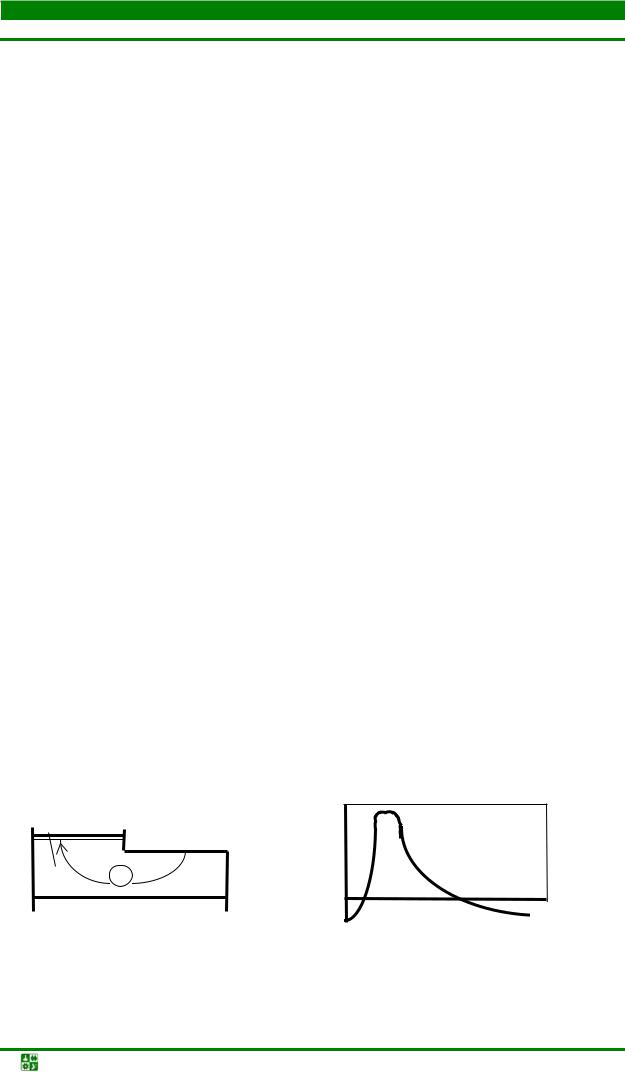
ЛАБ. РАБОТА 2 ПОЛУЧЕНИЕ ПОРОШКОВ МЕТАЛЛОВ МЕТОДОМ ЦЕМЕНТАЦИИ
Краткие теоретические сведения
комплексы понижается их концентрация в свободном виде и электродный потенциал осаждающегося металла сдвигается в отрицательную сторону.
Растворение и осаждение металла из раствора регулируется двумя противоположно действующими факторами: электролитической упругостью растворения и осмотическим давлением ионов раствора. Разность этих двух величин определяет значение и величину стандартного электродного потенциала.
Таблица 2.1
Стандартные электродные потенциалы и равновесные соотношения активностей катионов для некоторых пар двухвалентных металлов
Металл |
|
φо, В |
|
A MeZ1+ /A |
MeZ2+ |
||
Ме2 |
|
Ме1 |
Ме2 |
|
Ме1 |
||
|
|
1 |
2 |
||||
|
|
|
|
||||
Zn |
|
Cu |
–0,763 |
|
+0,320 |
1,0·10 −33 |
|
Fe |
|
Cu |
–0,440 |
|
+0,340 |
1,3·10 −27 |
|
Ni |
|
Cu |
–0,230 |
|
+0,340 |
2,0·10 −20 |
|
Zn |
|
Ni |
–0,763 |
|
+0,230 |
5,0·10 −19 |
|
Cu |
|
Hq |
+0,340 |
|
+0,798 |
1,6·10 −16 |
|
Zn |
|
Cd |
–0,796 |
|
–0,402 |
3,2·10 −13 |
|
Zn |
|
Fe |
–0,796 |
|
–0,440 |
8,0·10 −12 |
При погружении в раствор с ионами вытесняемого металла одни из участков металла-цементатора становятся катодами и на них идет выделение осаждаемого металла, а другие – анодами, где протекает процесс ионизации. Это связано с различием в уровнях энергии атомов, находящихся на поверхности металла-цементатора. Катодные участки возникают на местах поверхности с наиболее высоким электродным потенциалом. Так как катодные и анодные участки соединены, то электроны от анодных участков перетекают к катодным (рис. 2.1), а внешней цепью такого короткозамкнутого элемента служит электролит (раствор соли Ме1, в котором находится металлцементатор Ме2). После возникновения катодных участков на них продолжается преимущественное осаждение Ме1, так как это энергетически выгодней, поскольку не требует затрат энергии на образование зародышей новой фазы.
Me1Z1+ +z1e → Me1 |
|
V |
|
|
Me − z e → MeZ2+ |
||
|
|||
2 |
2 |
2 |
Me1 е |
Me |
|
|
2 |
|
а |
б |
t |
|
Рис. 2.1. Схема процесса цементации (а) и зависимость скорости цементации от времени (б)
Процессы порошковой металлургии. Метод. указания к лабораторным работам |
-22- |
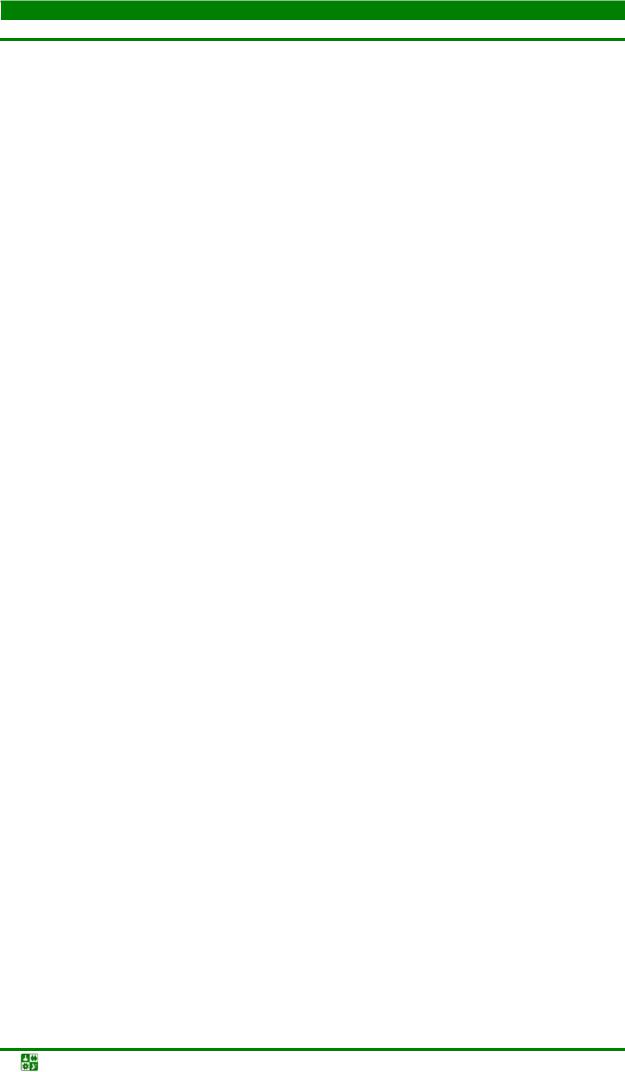
ЛАБ. РАБОТА 2 ПОЛУЧЕНИЕ ПОРОШКОВ МЕТАЛЛОВ МЕТОДОМ ЦЕМЕНТАЦИИ
Краткие теоретические сведения
Процесс цементации металла из его раствора определяется двумя последовательными процессами:
–доставкой ионов вытесняемого металла к катодной поверхности металла-цементатора через двойной и диффузионный слой;
–электрохимическим превращением на границе электрод-раствор, протекающим через несколько промежуточных стадий (дегидратация иона, его сорбция, разряд иона на металле-цементаторе с образованием атома металла и пр.).
Скорость реакции замещения зависит от разницы электродных потенциалов. Чем она больше, тем выше скорость цементации. Однако существует ряд других факторов, оказывающих влияние на результат реакции:
1. Цементирующий материал должен образовывать растворимое соединение с анионом, который связан с замещаемым металлом.
2. Металл-цементатор должен находиться в избытке. Это связано с тем, что реакция замещения проходит на поверхности и чем больше эта поверхность, тем скорее и полнее протекает реакция.
3. В процессе реакции поверхность металла-цементатора может покрываться выделяемым из раствора металлом, в следствие чего она становится инертной. Поэтому раствор должен циркулировать. В некоторых случаях раствор подвергают действию ультразвука.
4. Повышение температуры не только улучшает условия диффузии, но и снижает энергию активации реакции и процесс идет интенсивнее, переходя в диффузионную область.
Кроме основных реакций, в процессе цементации при определенных условиях наблюдается выделение водорода (разряд его ионов) и восстанов-
ление растворенного кислорода на катодных участках Ме2. Эти побочные процессы ведут к дополнительным затратам цементирующего металла и растворению выделенного металла.
Цементирующий металл часто используют в форме порошка (цинковая пыль, порошки железа или никеля), качество которого весьма сильно влияет на процесс. Присутствие в порошке более электроотрицательных примесей, хорошо растворимых в очищенном растворе, способствует реакции цементации. Примеси более электроположительных элементов затрудняют реакцию.
Аппаратурноеоформлениепроцесса
Внастоящее время процесс контактного восстановления осуществляется двумя способами: перемешиванием раствора с цементируемым порошком и просачиванием раствора через слой цементирующего порошка.
Воснову этих способов положен принцип полного противотока. Второй способ получения порошков в большей степени соответствует этому принципу. В этом случае наиболее концентрированный раствор взаимодействует с наиболее отработанной частью порошка и таким образом повышает-
Процессы порошковой металлургии. Метод. указания к лабораторным работам |
-23- |
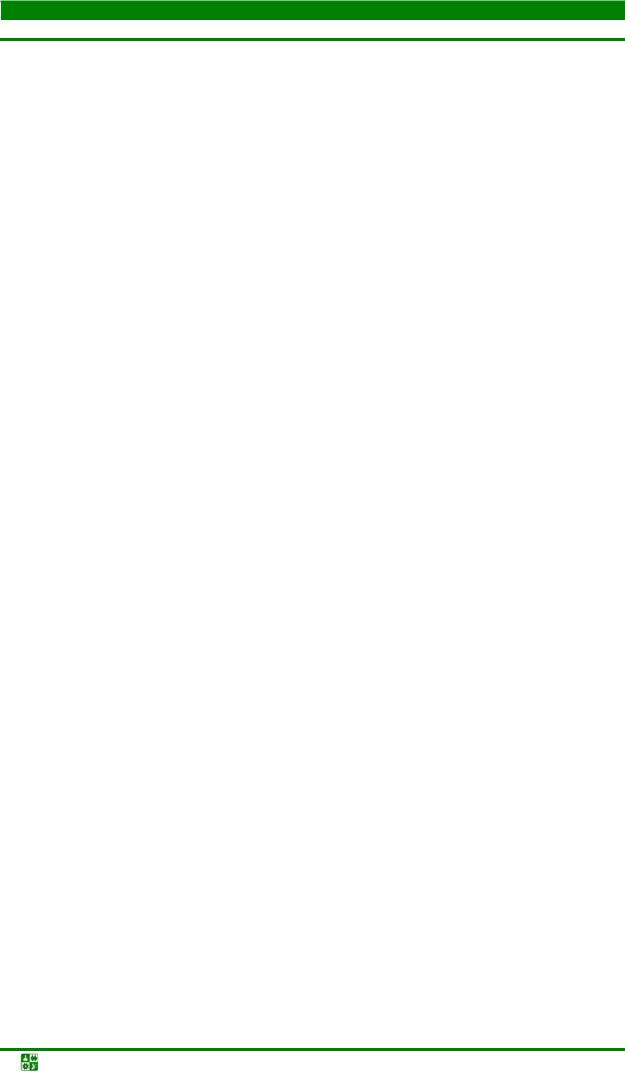
ЛАБ. РАБОТА 2 ПОЛУЧЕНИЕ ПОРОШКОВ МЕТАЛЛОВ МЕТОДОМ ЦЕМЕНТАЦИИ
Аппаратурное оформление процесса
ся степень использования цементатора. Однако при этом способе трудно добиться равномерного просачивания раствора через слой порошка: в отдельных местах образуются каналы с усиленной циркуляцией раствора, в других местах циркуляция слабая и цементатор реагирует не весь.
Способ перемешивания более доступен для механизации и автоматизации процессов. При осуществлении процесса по этому способу можно добиться частичного противотока, используя ряд последовательно включенных аппаратов. Свежий цементатор загружается в аппарат для окончательной очистки раствора.
Описаниелабораторнойустановки
1.Комплект химической лабораторной посуды.
2.Встряхиватель вибрационный WU-4.
3.Весы лабораторные SPU 202 OHAUS, 0,2–200 г, ±0,01–0,02 г.
4.Шкаф сушильный SNOL, Тmax = 200 оC.
Заданиенавыполнениелабораторнойработы
Получение порошка меди методом цементации с использованием способа перемешивания включает следующие операции:
–подготовку навесок металла-цементатора;
–подготовку раствора соли получаемого металла;
–смешивание реагентов и непосредственное проведение процесса;
–отделение полученного порошка, его отмывка.
Порядоквыполненияработы
1. Рассчитать количество цементируемого металла в соли (сернокислой меди), используемой для приготовления раствора.
2. Подготовить навески металла-цементатора и раствор соли получаемого металла. При подготовке навески соли цементируемого металла необходимо исходить из того, что содержание цементируемого металла в навеске соли должно быть не меньше пяти граммов. Количество металлацементатора (железа) необходимо брать с 50 %-м избытком от необходимого по стехиометрии на реакцию восстановления.
3. Изменяя условия получения порошка (температуру процесса, концентрацию раствора, количество цементатора и пр.), получить опытные образцы порошка металла. Для проведения процесса цементации водный раствор соли цементируемого металла с помещенным в него порошком металлацементатором установить на встряхиватель или на магнитную мешалку.
Процессы порошковой металлургии. Метод. указания к лабораторным работам |
-24- |
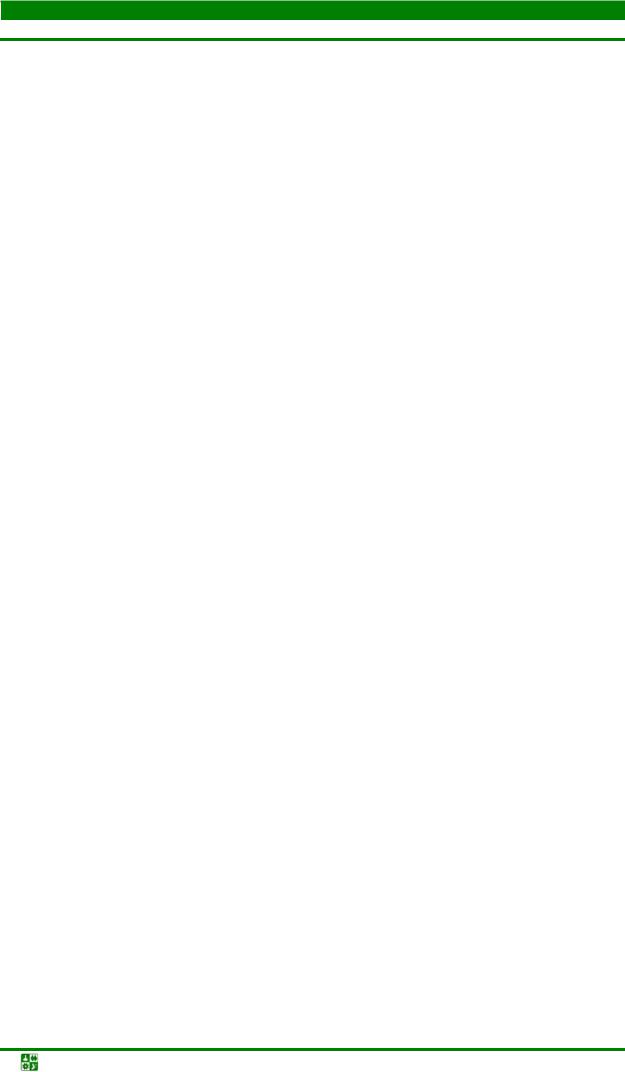
ЛАБ. РАБОТА 2 ПОЛУЧЕНИЕ ПОРОШКОВ МЕТАЛЛОВ МЕТОДОМ ЦЕМЕНТАЦИИ
Порядок выполнения работы
4.Установить оптимальный режим механоактивации процесса (скорость вращения встряхивателя или магнита мешалки). В течение всего процесса цементации визуально (по цвету раствора) фиксировать стадии процесса восстановления.
5.По окончании процесса цементации (примерно около двух часов), профильтровать раствор и провести кислотную отмывку полученного порошка от остатков металла цементатора. По окончании кислотной отмывки промыть порошок дистиллированной водой и обработать (последняя промывка) 4 %-м раствором хозяйственного мыла.
6.Раствор профильтровать, порошок высушить (в сушильном шкафу при температуре не выше 60 оС) и определить его массу.
7.Методом рентгеноструктурного анализа (РСА) провести полуколичественные определения состава образцов материала. Сопоставляя результаты РСА навесок порошка, полученного по различным методикам, определить оптимальные условия процесса цементации.
Требованиякотчету
1.Привести цель работы, краткие теоретические сведения, методику эксперимента, результаты анализа полученных порошков, сделать выводы.
2.Определить технологические свойства полученных порошков.
3.Полученные данные занести в таблицу.
4. Оформление отчета должно соответствовать СТО СФУ 4.2-07-2008.
Контрольныевопросыизадания
1.Что собой представляет процесс получения порошков методом цементации?
2.Какое условие с точки зрения электроотрицательности является необходимым для проведения процесса цементации?
3.Чем определяется значение и величина стандартного электродного потенциала?
4.Назовите два последовательных процесса цементации металла из его раствора.
5.Назовите факторы, оказывающие влияние на результат цементации.
Процессы порошковой металлургии. Метод. указания к лабораторным работам |
-25- |
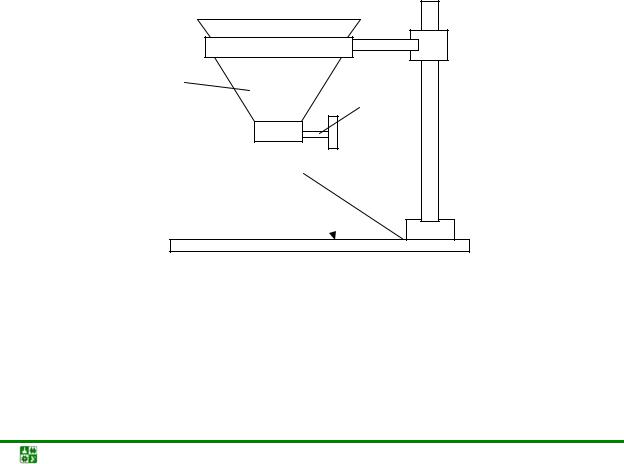
ЛАБОРАТОРНАЯ РАБОТА 3 ОПРЕДЕЛЕНИЕ ТЕХНОЛОГИЧЕСКИХ СВОЙСТВ
МЕТАЛЛИЧЕСКИХ ПОРОШКОВ
Цельработы
Освоение методики определения технологических свойств порошков (насыпной плотности, плотности утряски, текучести, угла естественного откоса).
Задачиработы
Определить основные технологические свойства металлического порошка, рассчитать пористость, относительную плотность порошка; определить уплотняемость и формуемость порошка.
Краткиетеоретическиесведения
Методика определения насыпной плотности и плотности утряски
Насыпная плотность – это масса единицы объема порошка при свободной насыпке, представляющая собой его объемную характеристику.
1
2
α
Рис. 3.1. Прибор для определения угла естественного откоса: 1 – воронка; 2 – шибер
Ее величина зависит от угла естественного откоса (рис. 3.1), определяющего плотность укладки его частиц при свободном заполнении ими какого-либо объема.
Процессы порошковой металлургии. Метод. указания к лабораторным работам |
-26- |
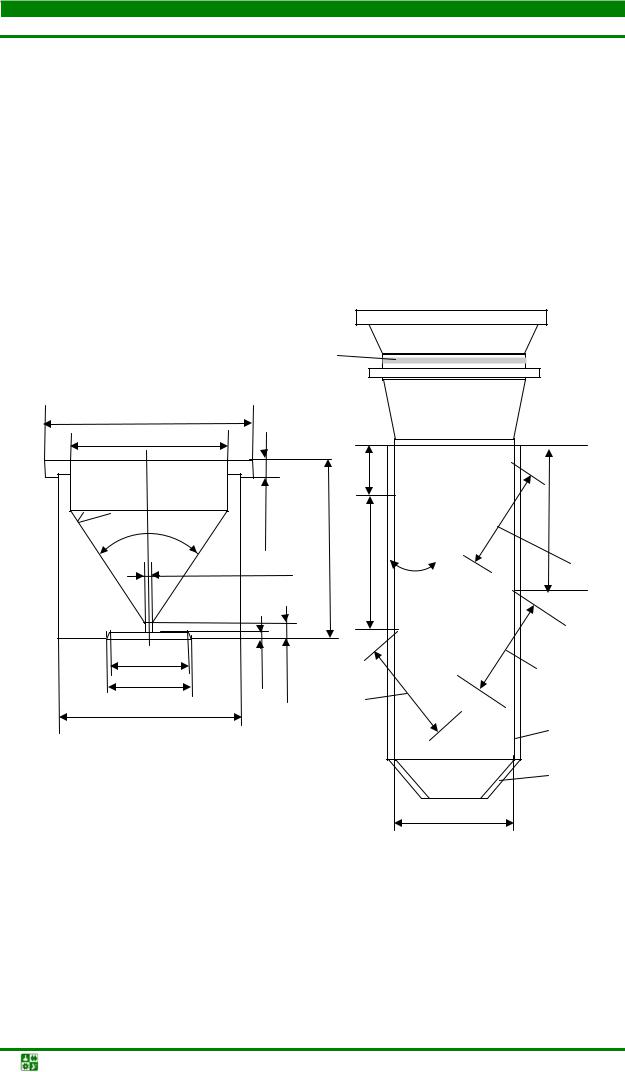
ЛАБ. РАБОТА 3 ОПРЕДЕЛЕНИЕ ТЕХНОЛОГИЧЕСКИХ СВОЙСТВ МЕТАЛЛИЧЕСКИХ ПОРОШКОВ
Краткие теоретические сведения
Она бывает тем больше, чем крупнее и правильнее форма частиц порошка и чем больше их пикнометрическая плотность. Существенное значение имеет также гранулометрический состав порошка, особенно наличие в нем тонкой фракции. С увеличением содержания тонкой фракции, как правило, насыпная плотность уменьшается.
Это связано с возрастанием поверхности трения. Однако при большой разнице в размерах мелких и более крупных частиц (примерно в 7–10 раз) насыпная плотность может возрасти из-за заполнения мелкими частицами промежутков между крупными.
Знание насыпной плотности необходимо прежде всего для расчета высоты матрицы пресс-формы при ее конструировании.
|
|
|
|
1 |
Ø65±0,5 |
|
|
|
|
Ø50,8±0,5 |
|
|
|
|
0,1 |
5±0,2 |
|
|
|
600±30´ |
|
|
60±0,5 |
|
|
|
+0,2 |
||
|
d2,5 |
|
|
|
|
илиd 5+0,2 |
|
||
Ø18±0,5 |
3,2±0,2 |
5,2±0,02 |
|
|
Ø20±0,5 |
|
|||
Ø55-0,5 |
|
|||
|
|
|
|
|
а |
|
|
|
|
25 |
|
|
50 |
65 |
50 |
|
|
|
25±20 |
|
50 |
40 |
|
|
2 |
|
3 |
|
40 |
|
б |
Рис. 3.2. Установки для определения насыпной плотности порошка: а – воронка; б – волюмометр; 1 – латунное сито; 2 – коробка из стекла; 3 – квадратная воронка
Для определения насыпной плотности по ГОСТ 19440-74 используют либо воронку (рис. 3.2), если порошок способен самостоятельно истекать через отверстие диаметром 5 мм, либо систему воронок с пластинками – во-
Процессы порошковой металлургии. Метод. указания к лабораторным работам |
-27- |
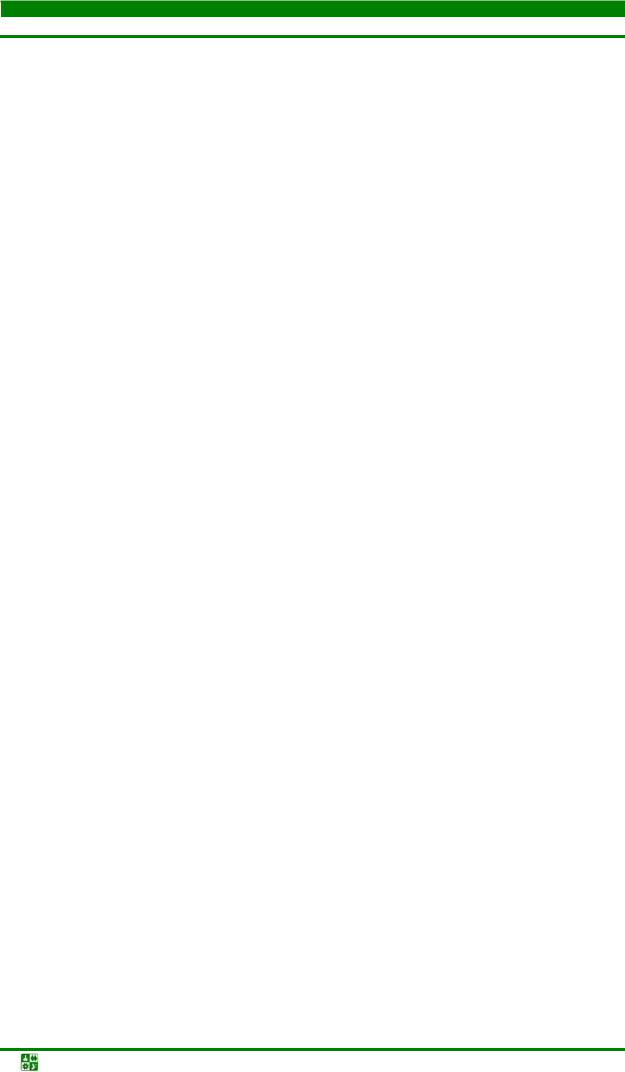
ЛАБ. РАБОТА 3 ОПРЕДЕЛЕНИЕ ТЕХНОЛОГИЧЕСКИХ СВОЙСТВ МЕТАЛЛИЧЕСКИХ ПОРОШКОВ
Краткие теоретические сведения
люмометр, представляющий собой прямоугольный сосуд с внутренними наклонными стеклянными полочками, по которым порошок ссыпается под действием силы тяжести.
Перед анализом проба порошка объемом около 100 см3 должна быть высушена при температуре около 110 оС до постоянной массы в сушильном шкафу с последующим охлаждением в эксикаторе до температуры окружающей среды.
В случае, когда порошок весьма мелкий или пирофорный, а также содержит добавки, не допускающие нагрева до указанной температуры, режим сушки должен оговариваться специально.
При анализе порошок ссыпают в мерный стаканчик объемом 25 см3. Избыточное количество порошка удаляют специальной пластиной из алюминия, повернутой ребром к верхнему торцу стаканчика. После этого стаканчик взвешивают на весах с погрешностью до 0,05 г.
Взвешивание проводят трижды и определяют среднее арифметическое от его результатов. Насыпную плотность рассчитывают по следующей формуле:
γнас = (G1 – G2) / V,
где G1, G2 – соответственно, масса пустого стакана и стакана с порошком, г; V1 – объем стакана, см3.
Величину, обратную насыпной плотности, называют насыпным объемом. Насыпной объем порошка всегда в несколько раз больше удельного объема компактного металла.
Понятие «плотность утряски» связано с наблюдаемым сокращением до 20–50 % объема, занимаемого свободно насыпанным порошком, при воздействии на него механических виброколебаний.
Отношение массы порошка к величине этого нового, уменьшенного объема и называется плотностью утряски.
По ГОСТ 25279-82 навеску порошка после просушки помещают в стеклянный мерный цилиндр объемом 100 или 25 см3, на который накладывают осевую вибрацию с частотой 100–300 ударов в минуту при амплитуде встряхивания около 3 мм. После прекращения изменения объема порошка в процессе встряхивания его фиксируют прямо в мерном цилиндре и известную массу порошка делят на величину объема, определяя значение плотности утряски:
γутр = G/V,
где G – масса порошка, г; V – объем, занимаемый навеской порошка массой G, после его утряски, см3.
Процессы порошковой металлургии. Метод. указания к лабораторным работам |
-28- |
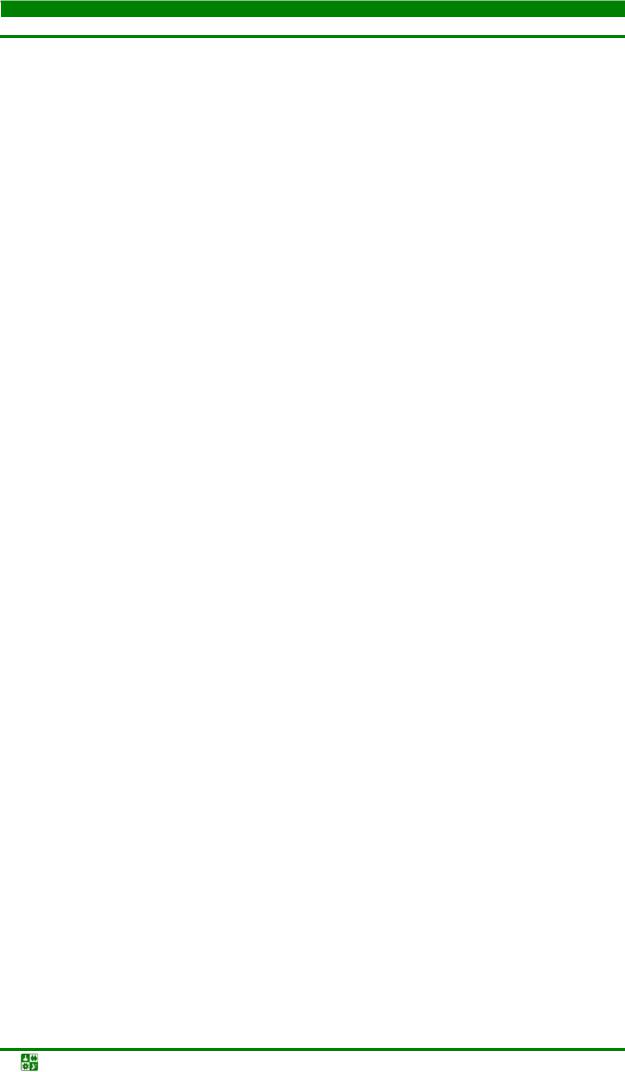
ЛАБ. РАБОТА 3 ОПРЕДЕЛЕНИЕ ТЕХНОЛОГИЧЕСКИХ СВОЙСТВ МЕТАЛЛИЧЕСКИХ ПОРОШКОВ
Краткие теоретические сведения
Максимальная плотность утряски достигается на порошках со сферической формой частиц при минимальной шероховатости их поверхности.
Величину, обратную плотности утряски, называют объемом утряски:
Vутр = 1/γутр, см3/г.
Зная насыпную плотность, пикнометрическую плотность, а также насыпной и пикнометрический объемы, можно определить еще несколько объемных характеристик вещества:
относительный объем:
β = Vнас / Vк = γк/γнас;
относительную плотность:
θ = γнас /γк = 1/β;
пористость:
П = ( Vнас – Vк )/Vнас = 1 – Vк / Vнас,
где γк – табличная плотность материала порошка или пикнометрическая плотность его частиц; Vк – удельный объем компактного металла, Vк = 1/γк.
Относительный объем показывает, во сколько раз насыпной объем порошка больше удельного объема металла его частиц. Относительная плотность характеризует долю объема, занимаемого в порошке частицами, а пористость – долю объема, занимаемого в порошке порами.
Насыпную плотность можно изменять, варьируя режимы получения порошка или прибегая к его дополнительной обработке.
Методика определения текучести порошка
Текучесть порошка характеризует его способность с определенной скоростью вытекать из отверстия, что очень важно для рациональной организации процесса автоматического прессования заготовок.
Текучесть порошка – сложная комплексная характеристика, зависящая от очень многих факторов (плотности и размера частиц, гранулометрического состава порошка, формы и состояния поверхности частиц и пр.); основным фактором является трение и сцепление частиц между собой, затрудняющее их взаимное перемещение.
Процессы порошковой металлургии. Метод. указания к лабораторным работам |
-29- |
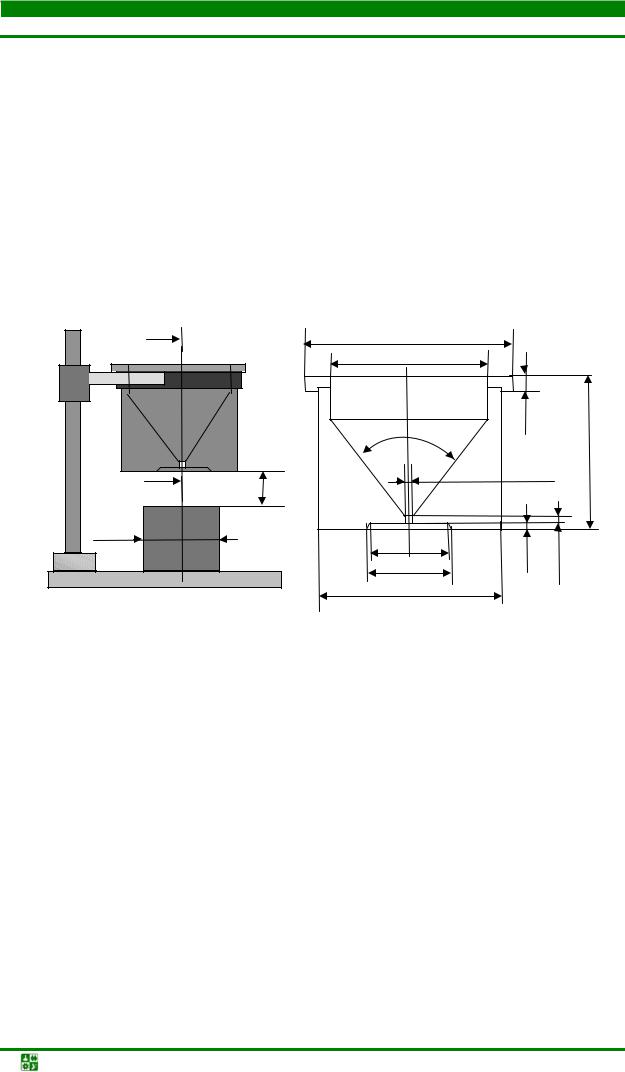
ЛАБ. РАБОТА 3 ОПРЕДЕЛЕНИЕ ТЕХНОЛОГИЧЕСКИХ СВОЙСТВ МЕТАЛЛИЧЕСКИХ ПОРОШКОВ
Краткие теоретические сведения
По ГОСТ 20899-75 текучесть выражается числом секунд, за которые 50 г порошка вытекают через калиброванное отверстие диаметром 2,5 мм конусной воронки (рис. 3.3).
Воронку укрепляют на штативе и устанавливают по уровню на горизонтальном основании, предохраненном от встряхиваний и вибраций.
Общую пробу порошка массой около 500 г просушивают и охлаждают в эксикаторе до комнатной температуры. Затем лабораторную пробу массой 50 г засыпают в воронку, выходное о тверстие которой закрывают пальцем. Открывают калиброванное отверстие воронки и одновременно включают секундомер.
А
А |
25 |
|
Ø28 |
А –А |
|
|
|
Ø65 |
|
|
|
Ø51 |
|
|
|
600±30´ |
5 |
|
|
|
|
60 |
|
|
d 2,54 |
||
Ø18 |
2 |
3,2 |
|
Ø20 |
|||
|
|
||
Ø55 |
|
|
Рис. 3.3. Воронка для определения текучести порошка
Как только последние частицы порошка выпадают из отверстия, секундомер останавливают. Текучесть порошка в секундах определяют по формуле
τ = К / t,
где t – продолжительность истечения лабораторной пробы порошка, с; К – корректирующий коэффициент воронки для определения текучести порошка.
Для расчета К сначала устанавливают клеймо воронки С: Через в о- ронку переливают отмеренные пипеткой 100 см3 дистиллированной воды, фиксируют необходимое для этого время в секундах; среднее из пяти измерений число секунд считают клеймом воронки, которое должно составлять 25±2 с. Если С станет меньше 23,0 с, то подобную воронку считают изношенной и непригодной для анализа. Корректирующий коэффициент равен величине 25,3, разделенной на клеймо воронки.
Процессы порошковой металлургии. Метод. указания к лабораторным работам |
-30- |
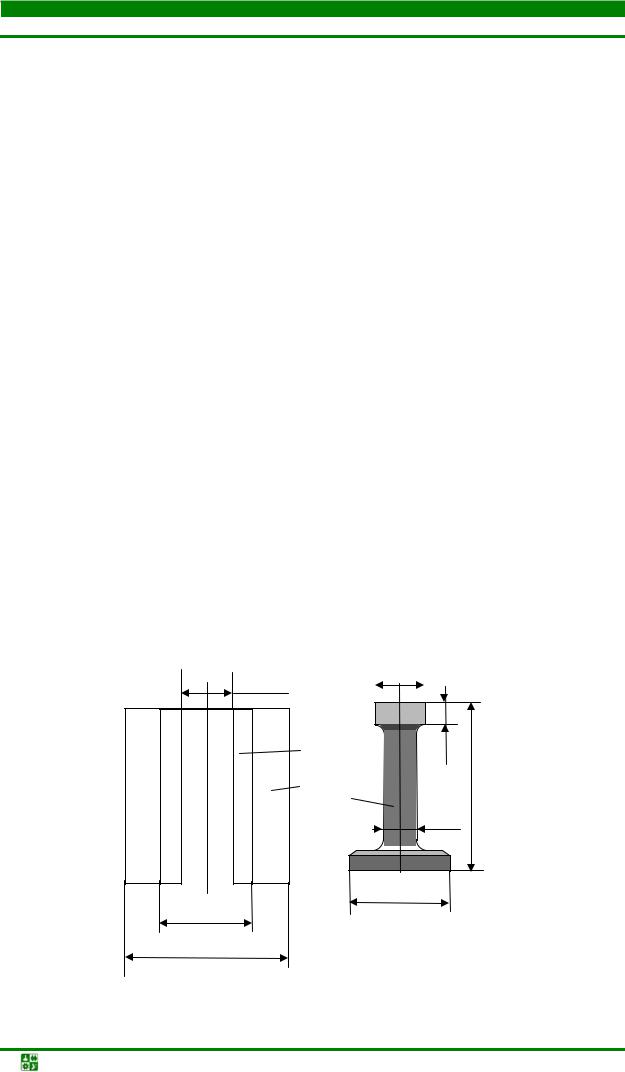
ЛАБ. РАБОТА 3 ОПРЕДЕЛЕНИЕ ТЕХНОЛОГИЧЕСКИХ СВОЙСТВ МЕТАЛЛИЧЕСКИХ ПОРОШКОВ
Краткие теоретические сведения
Испытание на текучесть проводят пять раз и берут среднее арифметическое значение.
Текучесть порошка обычно уменьшается при увеличении удельной поверхности и шероховатости частиц, так как при этом затрудняется относительное перемещение частиц. Окисление в большинстве случаев повышает текучесть порошка в связи с уменьшением коэффициента трения и сглаживания поверхности частиц. Значительно понижает текучесть порошка его влажность.
Уплотняемость, прессуемость и формуемость порошка
Уплотняемость металлического порошка – это его способность уменьшать занимаемый объем под воздействием давления или вибрации. По ГОСТ 25280-82 эта характеристика оценивается по плотности прессовок, изготовленных при давлении прессования 200, 400, 500, 600, 700 и 800 МПа в цилиндрической пресс-форме. Количество навески порошка вычисляют по формуле
m = 0,79d3γк,
где d – диаметр отверстия матрицы пресс-формы.
Перед засыпкой порошка стенки матрицы прессформы (рис. 3.4) смазывают раствором стеариновокислого цинка в летучей органической жидкости (100 г стеората цинка на 1000 см3 ацетона) и дают просохнуть смазке. Прессование проводят при постоянной скорости приложения нагрузки в течение не менее 15 с. При каждом давлении получают три прессовки и определяют их плотность. За результат измерения принимают среднее арифметическое из результатов трех испытаний, округленное до второго десятичного знака.
Ø11,3 Ø11,3
1
2 3
8
L
Ø10
Ø35
Ø26 Ø50
Рис. 3.4. Приспособление для определения уплотняемости порошка: 1 – матрица; 2 – обойма; 3 – пуансон
Процессы порошковой металлургии. Метод. указания к лабораторным работам |
-31- |
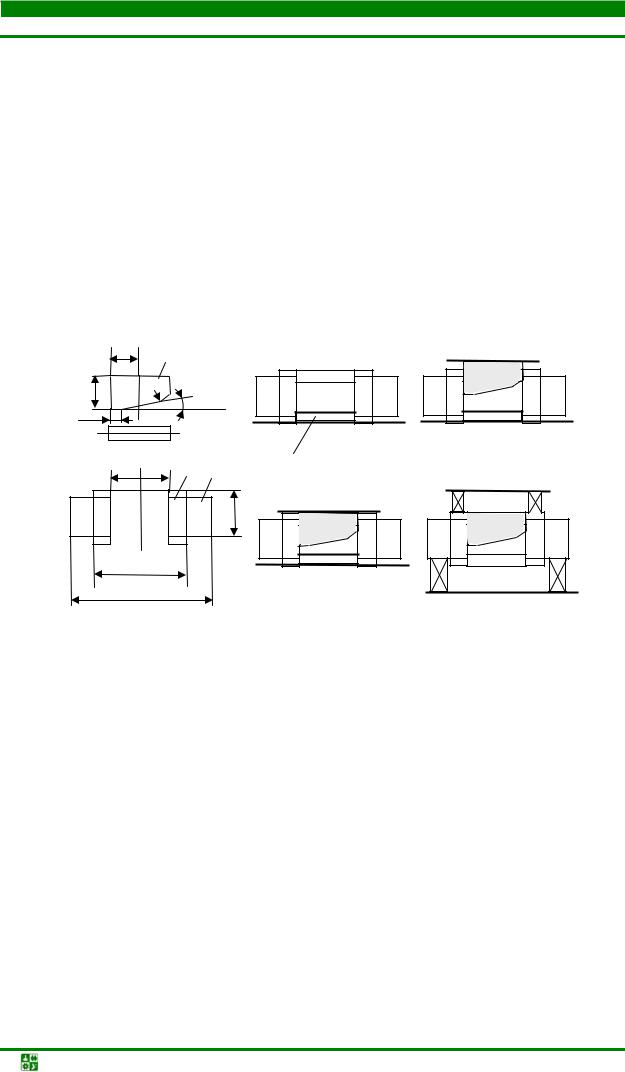
ЛАБ. РАБОТА 3 ОПРЕДЕЛЕНИЕ ТЕХНОЛОГИЧЕСКИХ СВОЙСТВ МЕТАЛЛИЧЕСКИХ ПОРОШКОВ
Краткие теоретические сведения
Прессуемость металлического порошка оценивает его способность образовывать под давлением тело, имеющее заданные размеры, форму и плотность. Эта характеристика дает качественную оценку свойств порошка, связанную с уплотняемостью и формуемостью.
Формуемость металлического порошка – это его способность сохранять приданную ему под воздействием давления форму в заданном интервале пористости (рис. 3.5). По ГОСТ 25280-82 эту характеристику порошка определяют при прессовании навески массой 2,5γк в разборной пресс-форме с последующим выставлением границ интервала пористости, при котором прессовка после извлечения из пресс – формы не осыпается и не имеет расслоения.
30
32 |
1 |
|
I |
II |
|
|
|||
|
|
|
|
|
R28 |
|
9030´ |
|
|
|
|
|
|
|
64 |
2 |
3 |
4 |
VI |
|
III |
|
||
|
|
|
|
|
|
|
44 |
|
|
Ø90 |
|
|
|
|
Ø140 |
|
|
|
|
а |
б |
Рис. 3.5. Приспособление для определения формуемости порошка (а) и схема получения образцов (б): 1 – верхний пуансон: 2 – матрица; 3 – разъемная обойма; 4 – нижний пуансон
Скорость приложения нагрузки идентична указанной выше для определения уплотняемости.
Прессование прекращают после соприкосновения верхней плиты пресса с верхним торцом матрицы.
Значения пористости, при которых прессовка не осыпается П1, и значение пористости, при котором она не имеет расслоений П2, определяют по графику (рис. 3.6), по оси абсцисс которого откладывается расстояние, соответствующее длине исследуемой части прессовки от ее торца меньшей высоты.
Минимальное и максимальное значение плотности, соответствующее плотностям П1 и П2, определяют по формулам
Процессы порошковой металлургии. Метод. указания к лабораторным работам |
-32- |
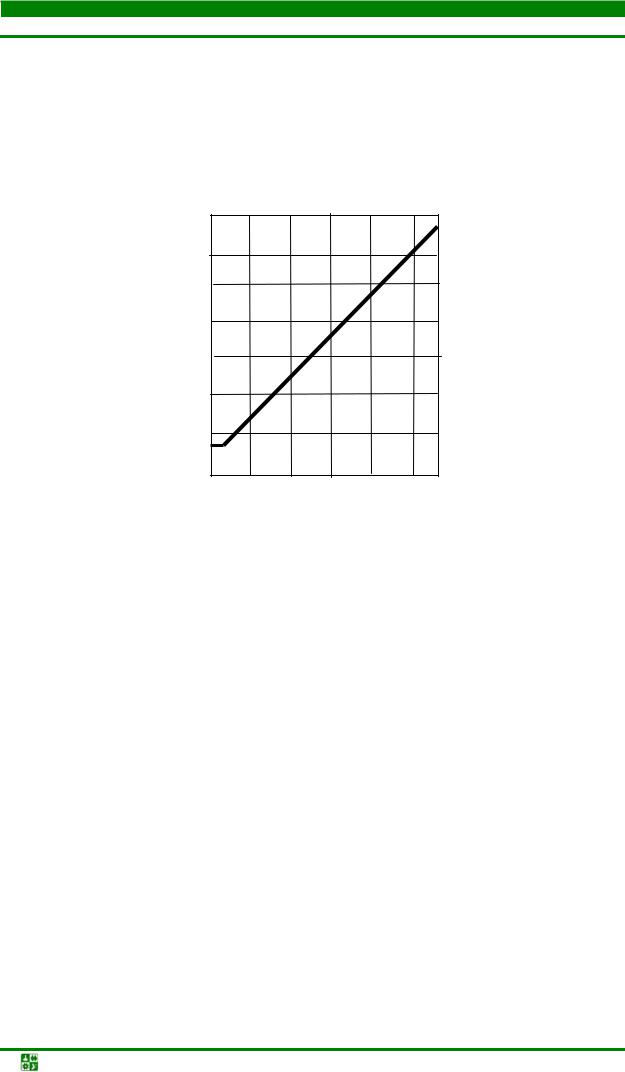
ЛАБ. РАБОТА 3 ОПРЕДЕЛЕНИЕ ТЕХНОЛОГИЧЕСКИХ СВОЙСТВ МЕТАЛЛИЧЕСКИХ ПОРОШКОВ
Краткие теоретические сведения
γ1 = γк(1 – П1),
γ2 = γк(1 – П2).
Вычисленные значения плотностей округляют до первого десятичного знака.
Пористость
0,8
0,7
0,6
0,5
0,4
0,3
0,2
0,1
10 |
20 |
30 |
40 |
50 |
Расстояние, мм
Рис. 3.6. Диаграмма для нахождения значений пористости
Формуемость качественно можно оценить по барабанной пробе – методу оценки устойчивости прессовок к истиранию. Брикеты диаметром 10 мми высотой 5 мм в количестве не менее 5 шт., спрессованные из исследуемого порошка при одном и том же давлении, после взвешивания обрабатывают во вращающемся барабане – сите с отверстиями размером 1,6 или 2 мм со скоростью вращения около 60 об/мин. Через 15 мин после начала испытаний образцы извлекают из барабана и определяют их вес. По разнице масс прессовок до и после обработки, отнесенной к начальной массе прессовок, оценивают сравнительную устойчивость кромок прессовок к разрушению.
Формуемость порошка в основном зависит от формы, размеров
исостояния поверхности частиц порошка. Хорошая прессуемость облегчает
иудешевляет процесс формования порошка, а хорошо формующиеся порош-
ки дают прочные неосыпающиеся формовки. Как правило, порошки с х о- рошей формуемостью обладают не очень хорошей прессуемостью и наоборот.
Процессы порошковой металлургии. Метод. указания к лабораторным работам |
-33- |
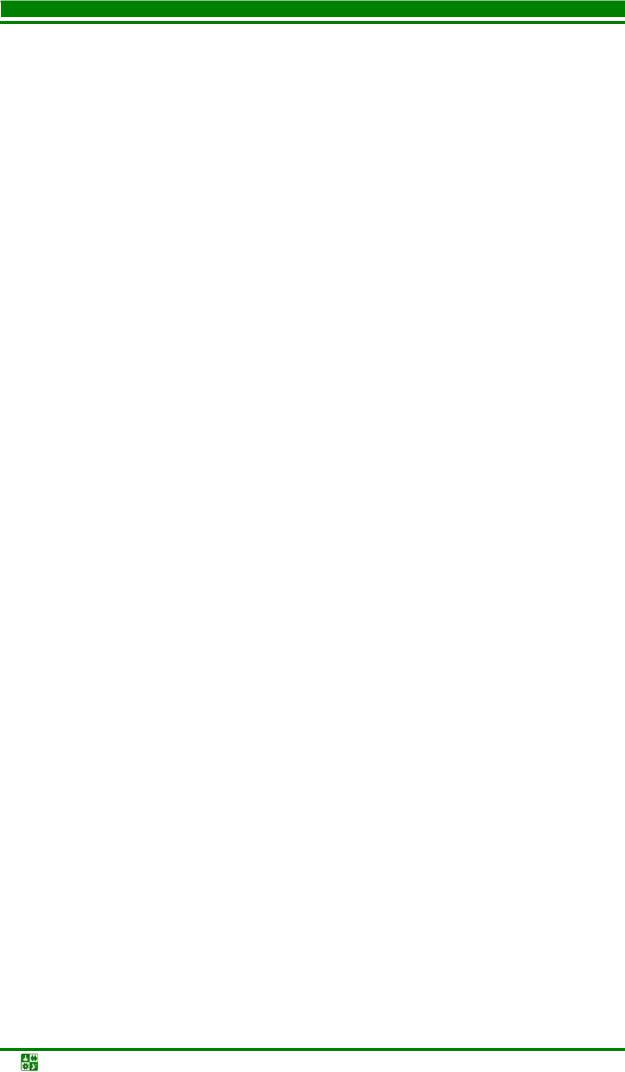
ЛАБ. РАБОТА 3 ОПРЕДЕЛЕНИЕ ТЕХНОЛОГИЧЕСКИХ СВОЙСТВ МЕТАЛЛИЧЕСКИХ ПОРОШКОВ
Описаниелабораторнойустановки
1.Комплект химической лабораторной посуды.
2.Воронка для определения текучести порошка (ГОСТ 20899-75).
3.Весы лабораторные SPU 202 OHAUS, 0,2–200 г, ±0,01–0,02 г.
4.Шкаф сушильный SNOL, Тmax = 200 оC.
5.Прессформы для определения прессуемости и формуемости порошка (ГОСТ 25280-82).
Заданиенавыполнениелабораторнойработы
1.Подготовить к анализу полученные порошки металлов.
2.Приготовленные партии порошка просушить в сушильном шкафу
при температуре (105±2) оС в течение одного часа.
3.Высушенные порошки поместить в эксикатор и дать им остыть до комнатной температуры в течение 15–20 мин.
4.Определить технологические свойства порошков: насыпную плотность, плотности утряски, текучесть, угол естественного откоса.
5.Рассчитать пористость, относительную плотность порошка.
6. Определить уплотняемость и формуемость порошка.
Требованиякотчету
В отчете должен быть изложен следующий материал:
1.Характеристика основных технологических свойств порошка.
2.Описание теоретических основ и методов определения насыпной плотности, плотности утряски, текучести, угла естественного откоса.
3.Результаты эксперимента в виде сводной таблицы.
4.Анализ и обсуждение полученных результатов измерений.
5.Оформление отчета должно соответствовать СТО СФУ 4.2-07-2008.
Контрольныевопросыизадания
1.Дайте определение насыпной плотности и плотности утряски.
2.Что такое текучесть порошка?
3.Дайте определение и расскажите, какова взаимосвязь следующих технологических характеристик: уплотняемости, прессуемости и формуемости порошка.
4.Каковы основные методы определения формуемости порошка?
5.Каким образом текучесть зависит от характеристик порошка?
Процессы порошковой металлургии. Метод. указания к лабораторным работам |
-34- |

ЛАБОРАТОРНАЯ РАБОТА 4 ОПРЕДЕЛЕНИЕ ГРАНУЛОМЕТРИЧЕСКОГО СОСТАВА ПОРОШКОВ СЕДИМЕНТАЦИОННЫМ МЕТОДОМ
Цельработы
Определение гранулометрического состава порошка.
Задачиработы
Изучение теоретических основ седиментации и методов седиментационного анализа; экспериментальное определение гранулометрического состава порошков методом весовой седиментации.
Краткиетеоретическиесведения
Частицы дисперсной фазы в грубодисперсных системах постепенно оседают под действием силы тяжести, если плотность частицы p больше плотности среды po, или всплывают, если p < po. Это явление называют седиментацией. Наблюдение за скоростью седиментации в суспензиях, т.е. в дисперсных системах, содержащих достаточно большие частицы и являющихся кинетически неустойчивыми, позволяет сравнительно легко и точно определять размер частиц. Соответствующая методика называется седиментаци-
онным анализом.
Рассмотрим, как оседает в жидкости отдельная частица. Оседание частицы происходит под действием силы тяжести f, которая с учетом силы Архимеда составляет
f = V(p – po)g,
где V – объем частицы; р – плотность частицы; po – плотность среды; g – ускорение свободного падения.
Оседанию противодействует сила сопротивления f”, пропорциональная скорости седиментации:
f’ = Bu,
где В – коэффициент трения между частицей и средой, зависящий от вязкости среды ŋ; u – скорость седиментации.
Процессы порошковой металлургии. Метод. указания к лабораторным работам |
-35- |
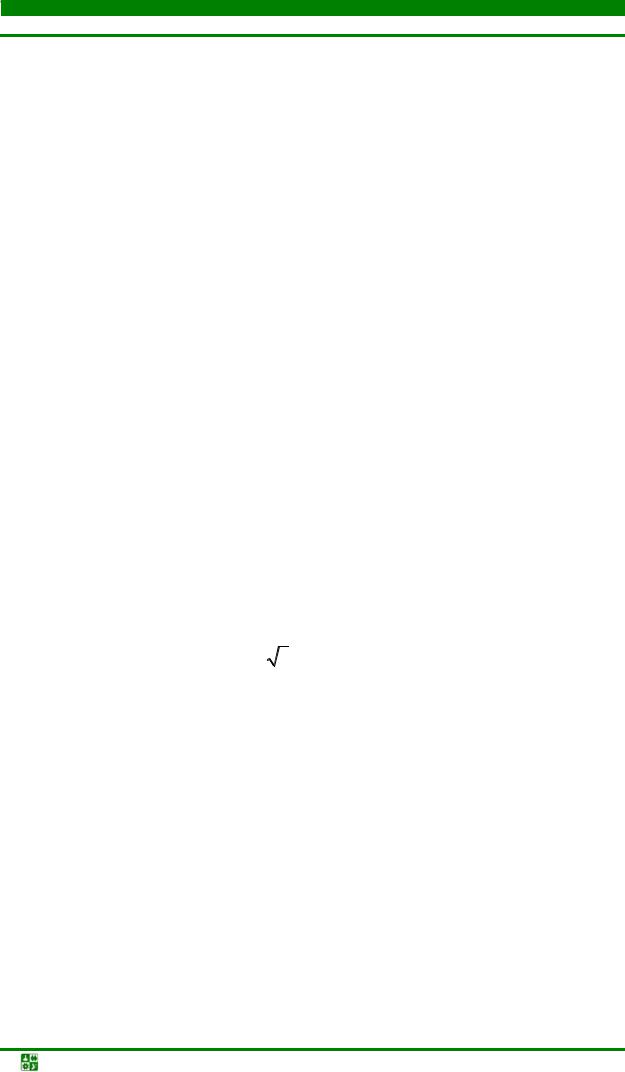
ЛАБ. Р. 4 ОПРЕДЕЛЕНИЕ ГРАНУЛОМЕТРИЧЕСКОГО СОСТАВА ПОРОШКОВ СЕДИМЕНТАЦИОННЫМ МЕТОДОМ
Краткие теоретические сведения
Вначале частица движется ускоренно, так как при малых скоростях сила тяжести превышает силу трения. По мере увеличения скорости движения сила трения возрастает и в некоторый момент уравновешивает силу тяжести, вследствие чего частица начинает двигаться с постоянной скоростью. При стационарном режиме оседания должно соблюдаться равенство
V(p – po)g = Bu. |
(4.1) |
Применительно к сферическим частицам это уравнение принимает
вид
3/4πr3(p – po)g = 6πη ru. |
(4.2) |
По уравнению (4.2) легко найти скорость седиментации:
u = 2r2/9η·(p – po)g. |
(4.3) |
Согласно уравнению (4.3) скорость седиментации прямо пропорциональна квадрату радиуса (или диаметра) частицы, обратно пропорциональна вязкости среды и зависит от разности р – ро: при р > ро частицы оседают, а при р < ро (например, суспензия парафина в воде) они всплывают, т.е. происходит так называемая обратная седиментация.
Используя уравнение (4.2), легко найти радиус частицы, зная скорость ее оседания и значения величин η, р и po:
r = |
9 |
ηu/2(p – po)g. |
(4.4) |
Уравнение (4.2) справедливо для водных суспензий, имеющих частицы размером от 0,1 до 100 мкм, так как для этих частиц время нарастания скорости оседания до постоянного значения настолько мало, что не оказывает влияния на результаты седиментационного анализа. Например, время достижения постоянной скорости оседания в воде частиц кварца с радиусом 1 мкм составляет 3,4·10-3 с, а частиц с радиусом 50 мкм – всего 1,7·10-6с. К частицам с радиусом больше 100 мкм, в обычных условиях оседающим ускоренно, и к частицам с радиусом меньше 0,1 мкм, содержащимся в кинетически устойчивых системах, уравнение (4.2) неприменимо. Поэтому обычный седиментационный анализ в этом случае непригоден.
Рассмотрим теперь седиментацию в дисперсных системах, состоящих из множества частиц. При этом примем, что частицы в таких суспензиях оседают совершенно независимо друг от друга. В монодисперсной системе от-
Процессы порошковой металлургии. Метод. указания к лабораторным работам |
-36- |
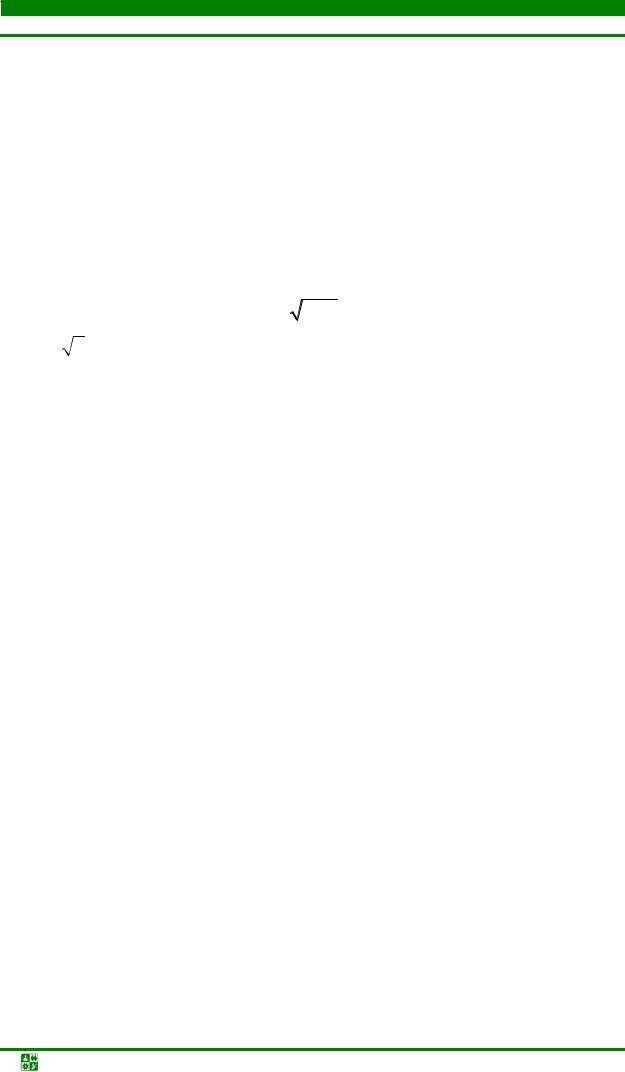
ЛАБ. Р. 4 ОПРЕДЕЛЕНИЕ ГРАНУЛОМЕТРИЧЕСКОГО СОСТАВА ПОРОШКОВ СЕДИМЕНТАЦИОННЫМ МЕТОДОМ
Краткие теоретические сведения
стаивание будет происходить равномерно, поскольку скорость оседания одинаковых по размеру частиц одинакова. Высота слоя осветленной жидкости Н в данном случае пропорциональна времени оседанияτ. Скорость движения границы раздела суспензии и прозрачной среды выражается уравнением
u = Н/τ, |
(4.5) |
а радиус частиц описывается выражением
r = k |
H / τ |
, |
(4.6) |
где k = 9 ηu/2(p – po)g .
На основе уравнения (4.6) можно рассчитать радиус частиц, используя результаты визуального наблюдения за их оседанием, например, с помощью микроскопа.
При отстаивании полидисперсной суспензии в отличие от монодисперсной четкая граница раздела суспензии и прозрачной среды не возникает, так как частицы, имеющие различные радиусы, проходят за одно и то же время различный путь. Поэтому седиментационный анализ полидисперсной системы сводится к определению скорости накопления вещества в осадке. Зависимость массы вещества m, выпавшего в осадок, от времениτ графич е- ски изображается в виде так называемой кривой седиментации, на основе которой получают необходимые данные для характеристики гранулометрического состава исследуемой системы.
По результатам, полученным при обработке кривой седиментации, обычно строится кривая распределения, характеризующая весовое содержание Q различных фракций в суспензии. Для этого строится диаграмма, на оси абсцисс которой откладываются значения радиусов частиц r, на оси ординат
– значения Q/Δr для каждой фракции. Пример такой диаграммы приведен на рис. 4.1. Очевидно, что Q/Δr· r = Q и весовое содержание каждой фракции выражается площадью соответствующего прямоугольника. Построив такие прямоугольники для всех фракций и соединив плавной линией средние точки их верхних сторон, получают кривую распределения.
Процессы порошковой металлургии. Метод. указания к лабораторным работам |
-37- |
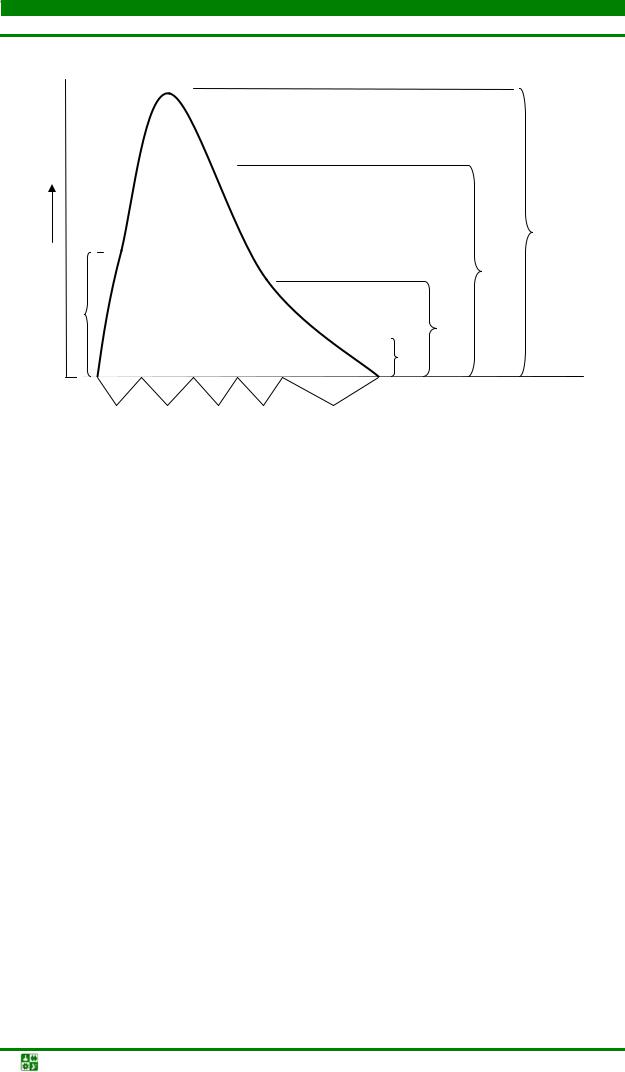
ЛАБ. Р. 4 ОПРЕДЕЛЕНИЕ ГРАНУЛОМЕТРИЧЕСКОГО СОСТАВА ПОРОШКОВ СЕДИМЕНТАЦИОННЫМ МЕТОДОМ
Краткие теоретические сведения
Q/Δr
Q5/Δr5
|
|
|
4 |
|
|
|
|
|
|
|
|
|
|
|
|
|
|
|
|
|
|
|
|
|
|
|
|
|
|
|
|
|
|
|
|
|
|
|
|
45 |
|
|
|
|
|
|
|
|
|
|
|
|
|
|
r |
|
|
|
|
|
|
|
|
|
|
|
|
/ |
|
|
|
|
|
|
|
|
|
|
|
|
|
4 |
|
|
|
|
|
|
|
|
|
|
|
|
|
|
Q |
|
|
|
|
|
|
|
|
|
|
|
|
34 |
|
|
|
|
|
|
|
|
|
|
|
|
|
||
|
|
|
|
|
|
|
|
|
|
|
|
|
/Δr |
|
|
|
|
|
|
|
|
|
|
|
|
3 |
|
|
|
|
|
|
3 |
|
|
|
|
|
|
|
Q |
|
|
|
|
|
|
|
|
|
|
|
|
|
|
|
5 |
|
|
|
|
|
|
|
|
|
|
|
|
|
|
|
|
|
|
|
|
|
|
|
23 |
|
|
|
|
|
|
|
|
2 |
|
|
|
|
|
/Δr |
|
|
|
|
|
|
|
|
|
1 |
|
2 |
|
||
|
|
|
|
|
|
|
|
|
|
/Δr |
|
Q |
|
|
|
|
|
|
|
|
1 |
|
|||||
|
|
|
|
|
|
|
|
|
|
|
|
||
|
|
|
|
|
|
|
|
|
Q |
|
|
|
|
|
|
|
|
|
|
|
|
|
1 |
|
|
|
|
|
|
|
|
|
|
|
|
|
|
|
|
|
|
r |
|
|
|
|
|
|
|
r1(max) |
|
|
|||
6(min) r5 |
r4 |
r3 |
r2 |
|
|
||||||||
|
r56 |
r45 |
r34 r23 |
r12 |
|
|
|
|
r |
Рис. 4.1. Кривая распределения частиц порошка по размерам
Фракция, отвечающая максимуму кривой распределения, называется преимущественной фракцией полидисперсной суспензии, так как частицы, составляющие эту фракцию, преобладают в системе (нарис. 4.1 эта фракция 4, содержащая частицы, радиус которых лежит в пределах от r4 до r5).
Кривые распределения являются важной характеристикой дисперсных систем. Чем уже интервал радиусов кривой распределения и чем выше ее максимум, тем суспензия ближе к монодисперсной. Наоборот, чем кривая более растянута и чем ниже максимум, тем суспензия более полидисперсная.
Следует отметить ряд условий, ограничивающих область применения седиментационного анализа. Во-первых, основное уравнение седиментационного анализа (4.2) пригодно только для расчета размера сферических частиц. Для частиц, отличающихся по форме от сферических, уравнение (4.2) позволяет определить только так называемый эффективный эквивалентный радиус, т.е. радиус воображаемых сферических частиц, обладающих той же плотностью и оседающих с той же скоростью, что и частицы суспензии. Вовторых, при седиментационном анализе с использованием уравнения (4.2) можно получить объективные результаты только в том случае, когда частицы не сольватированы. Понятно, что влияние солватации будет сказываться в тем большей степени, чем меньше размер частиц. Наконец, в-третьих, седиментационный анализ можно применять только тогда, когда частицы оседают раздельно друг от друга (когда концентрация суспензии не слишком велика) и когда они не образуют агрегатов.
Процессы порошковой металлургии. Метод. указания к лабораторным работам |
-38- |
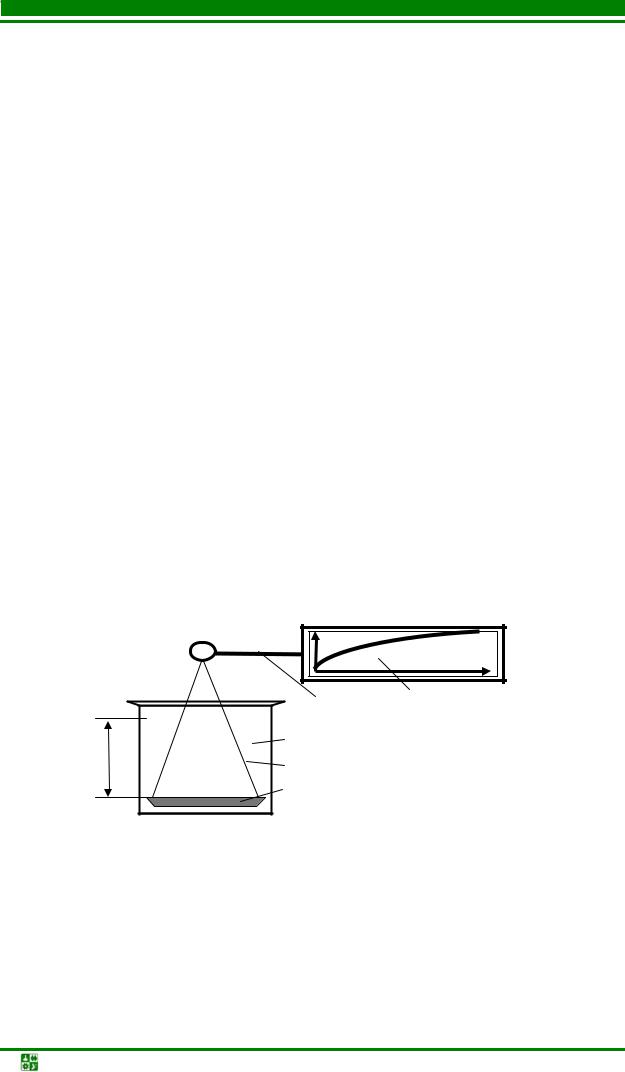
ЛАБ. Р. 4 ОПРЕДЕЛЕНИЕ ГРАНУЛОМЕТРИЧЕСКОГО СОСТАВА ПОРОШКОВ СЕДИМЕНТАЦИОННЫМ МЕТОДОМ
Описаниелабораторнойустановки
1. Комплект химической лабораторной посуды.
2. Весы лабораторные SPU 202 OHAUS, 0,2–200 г , ±0,01–0,02 г.
3. Секундомер.
Заданиенавыполнениелабораторнойработы
Проба порошка для исследований массой 50 г отбирается в соответствии с ГОСТ 9721-71. Для удаления крупных частиц проба просеивается через сито № 0040 с сеткой по ГОСТ 6613-73. Суспензия для седиментационного анализа приготавливается с концентрацией порошка не более 0,4 об. %.
Исследования проводятся методом весовой седиментации в соответствии с ГОСТ 22662-77. Суть его заключается в определении скорости накопления осадка на чашке весов. Схема устройства для проведения седиментационного анализа приведена на рис. 4.2.
Взвесь порошка в дисперсионной жидкости готовят в кювете 1 при перемешивании мешалкой в течение от 1 до 5 мин, не допуская образования пузырьков воздуха. По окончании перемешивания порошок должен быть равномерно распределен по высоте кюветы. После перемешивания мешалку извлекают из кюветы и погружают в кювету чашечку весов; продолжительность установки кюветы в гнездо прибора не должна превышать 15 с. Продолжительность оседания частиц регистрируют автоматически блоком 5 или с помощью секундомера.
|
4 |
5 |
|
|
|
h |
3 |
|
2 |
|
|
|
|
|
|
1 |
|
Рис. 4.2. Схема устройства для проведения седиментационного анализа: 1 – чашка весов; 2 – подвеска чашки весов; 3 – суспензия анализируемого порошка; 4 – коромысло весов; 5– блок регистрации и записи массы осадка
Процессы порошковой металлургии. Метод. указания к лабораторным работам |
-39- |
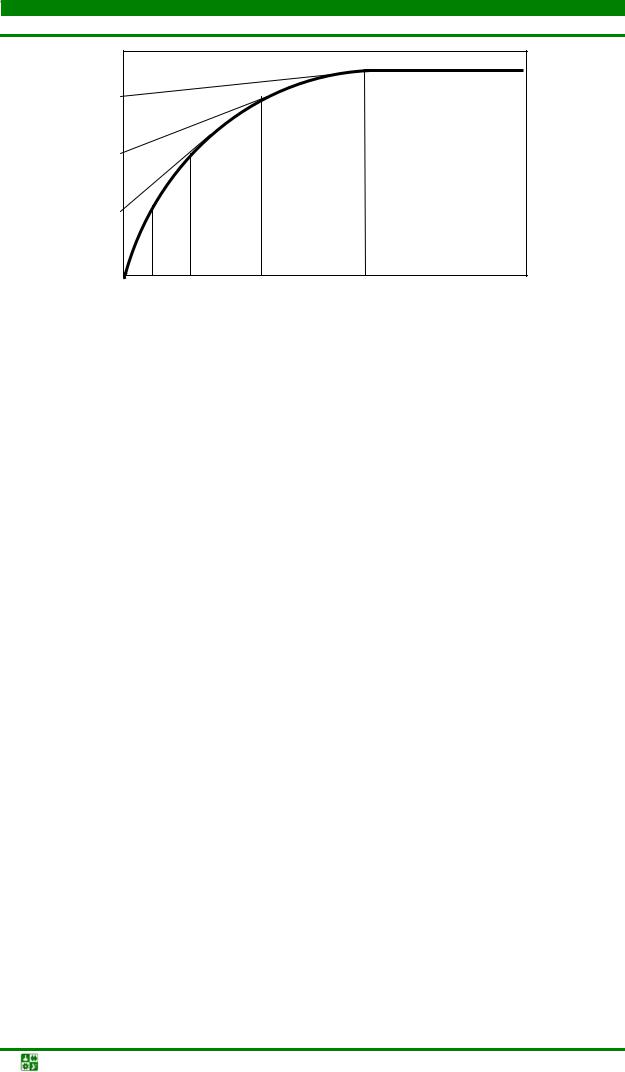
ЛАБ. Р. 4 ОПРЕДЕЛЕНИЕ ГРАНУЛОМЕТРИЧЕСКОГО СОСТАВА ПОРОШКОВ СЕДИМЕНТАЦИОННЫМ МЕТОДОМ |
|||||
|
Задание на выполнение лабораторной работы |
|
|||
m |
|
|
|
|
|
m3 |
|
|
|
|
|
m2 |
|
|
|
|
|
m1 |
|
|
|
|
|
0 |
τ1 |
τ2 |
τ3 |
τ4 |
τn |
|
d1 |
d2 |
d3 |
d4 |
dn |
|
Рис. 4.3. Схема обработки кривой седиментации |
|
При неавтоматической регистрации производят замеры массы осадка через 0,5, 1, 2, 3, 5, 7, 10, 15, 20, 25, 30, 45, 60, 70, 90, 120 мин и строят график зависимости массы осадка m от времени оседанияτ, то есть кривая седиментации m = f(τ) (рис. 4.3). Перегибы на седиментационной кривой не допускаются.
Для обработки результатов эксперимента по формуле (4.4) рассчи-
тываются соответствующие отмеренным промежуткам времени размеры частиц r и откладываются на оси абсцисс полученного графика. Затем произвольно задаются размерами, являющимися граничными значениями классов крупности частиц (фракций порошка). Число выбранных значений должно быть не менее пяти. Из этих точек восстанавливают перпендикуляры к оси абсцисс до пересечения с седиментационной кривой. В точках пересечения проводят касательные к кривой седиментации до пересечения с осью ординат. Горизонтальный участок кривой (плато) также продлевают до пересечения с осью ординат (точка m). Схема этих построений представлена на рис. 4.3.
Длина отрезка 0m пропорциональна массе всех частиц, осевших на измерительную чашечку, и соответствует 100 %. Длина отрезков 0 m1 m2 m3 и других на оси ординат является мерой доли соответствующих фракций порошка. Результаты графического анализа записываются в виде таблицы.
Порядоквыполненияработы
1.Отобрать пробу в соответствии с ГОСТ 9721-71.
2.По величине максимального размера частиц анализируемого порошка приближенно оценить по уравнению (4.4) вязкость жидкости, необходимой для исследования, и выбрать рабочую жидкость. Свойства некоторых дисперсионных жидкостей приведены в табл. 4.1.
Процессы порошковой металлургии. Метод. указания к лабораторным работам |
-40- |
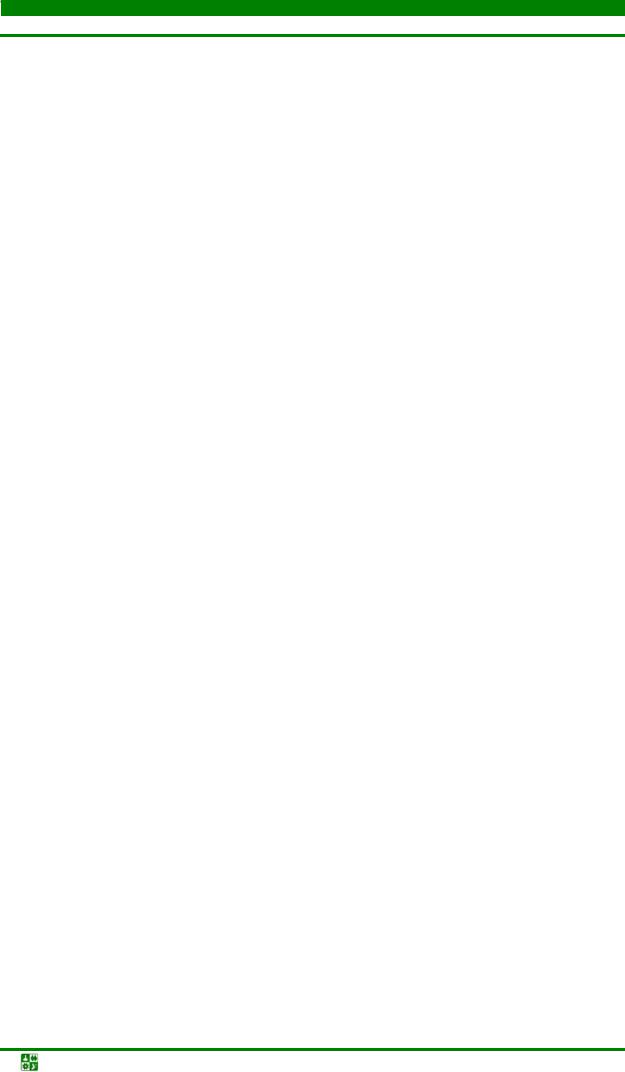
ЛАБ. Р. 4 ОПРЕДЕЛЕНИЕ ГРАНУЛОМЕТРИЧЕСКОГО СОСТАВА ПОРОШКОВ СЕДИМЕНТАЦИОННЫМ МЕТОДОМ
Порядок выполнения работы
Свойства некоторых дисперсионных жидкостей |
Таблица 4.1 |
||||
|
|
||||
|
Плотность, г/см3', |
Вязкость, с·П, |
|||
Вещество |
при температуре, °С |
при температуре, °С |
|||
|
20 |
25 |
20 |
|
25 |
Ацетон |
0,792 |
– |
0,325 |
|
0,308 |
Бензол |
0,879 |
0,875 |
0,649 |
|
0,604 |
Вода |
0,998 |
0,997 |
1,005 |
|
0,894 |
Спирт: |
|
|
|
|
|
бензиновый |
1,050 |
– |
5,800 |
|
5,050 |
изоамиловый |
0,816 |
– |
5,800 |
|
5,040 |
бутиловый |
0,808 |
0,806 |
2,950 |
|
2,510 |
метиловый |
0,795 |
0,791 |
0,598 |
|
0,547 |
этиловый |
0,789 |
0,785 |
1,200 |
|
1,096 |
Толуол |
0,864 |
0,859 |
0,585 |
|
0,550 |
Циклогексанон |
0,962 |
– |
68,000 |
|
52,000 |
Глицерин + 25 % воды |
1,061 |
– |
2,095 |
|
1,810 |
Глицерин |
1,262 |
– |
1 499,000 |
|
945,000 |
Четыреххлористый углерод |
1,593 |
1,584 |
0,969 |
|
0,906 |
3.Приготовить суспензию.
4.Установить стаканчик с суспензией на весы и провести контрольное взвешивание.
5.Повторно перемешать суспензию, установить на весы стаканчик,
опустить в стаканчик чашку весов.
6.Фиксируя время, провести замеры прибыли массы порошка на чаш-
ке весов.
7.По данным замеров массы осадка построить кривую седиментации.
8.На основании полученной кривой седиментации построить кривую распределения частиц порошка по размерам (гистограмму порошка).
Требованиякотчету
В отчете должен быть изложен следующий материал:
1.Характеристика физико-химических свойств порошка.
2.Описание теоретических основ и методов седиментационного анали-
за.
3.Результаты эксперимента в виде таблиц, графиков, гранулометрического состава порошка.
4.Анализ и обсуждение полученных результатов измерений.
5.Оформление отчета должно соответствовать СТО СФУ 4.2-07-2008.
Контрольныевопросыизадания
1.Дайте определение седиментации.
2.Как рассчитать скорость седиментации?
3.Суспензии с частицами какого размера пригодны для седиментаци-
онного анализа?
4.На чем основан выбор седиментационной жидкости?
5.Как влияет форма частиц на точность измерений?
Процессы порошковой металлургии. Метод. указания к лабораторным работам |
-41- |