
- •Оглавление
- •ОБЩИЕ СВЕДЕНИЯ
- •ЛАБОРАТОРНАЯ РАБОТА 1 ПОЛУЧЕНИЕ ПОРОШКОВ ЖЕЛЕЗА ВОССТАНОВЛЕНИЕМ ОТХОДОВ МЕТАЛЛООБРАБОТКИ ТВЕРДЫМ УГЛЕРОДОМ
- •ЛАБОРАТОРНАЯ РАБОТА 2 ПОЛУЧЕНИЕ ПОРОШКОВ МЕТАЛЛОВ МЕТОДОМ ЦЕМЕНТАЦИИ
- •ЛАБОРАТОРНАЯ РАБОТА 5 ОПРЕДЕЛЕНИЕ ПЛОТНОСТИ, ПОРИСТОСТИ СФОРМОВАННЫХ И СПЕЧЕННЫХ ПОРОШКОВЫХ МАТЕРИАЛОВ
- •ЛАБОРАТОРНАЯ РАБОТА 6 МЕТАЛЛОГРАФИЧЕСКОЕ ИССЛЕДОВАНИЕ СПЕЧЕННЫХ МАТЕРИАЛОВ
- •ЛАБОРАТОРНАЯ РАБОТА 7 ОПРЕДЕЛЕНИЕ ТВЕРДОСТИ СПЕЧЕННЫХ ПОРОШКОВЫХ МАТЕРИАЛОВ
- •ЛАБОРАТОРНАЯ РАБОТА 8 ОПРЕДЕЛЕНИЕ ЭФФЕКТИВНОЙ ГЛУБИНЫ УПРОЧНЕННОГО СЛОЯ
- •БИБЛИОГРАФИЧЕСКИЙ СПИСОК
- •ПРИЛОЖЕНИЕ

ЛАБОРАТОРНАЯ РАБОТА 1 ПОЛУЧЕНИЕ ПОРОШКОВ ЖЕЛЕЗА ВОССТАНОВЛЕНИЕМ ОТХОДОВ МЕТАЛЛООБРАБОТКИ ТВЕРДЫМ УГЛЕРОДОМ
Цельработы
Получение порошка железа методом восстановления оксидов железа углеродом.
Задачиработы
Освоить методику восстановления оксидов железа твердыми и газообразными восстановителями; проанализировать процесс восстановления и формирования структуры получаемых порошков; определить влияние технологических параметров на процесс восстановления и свойства получаемых материалов.
Краткиетеоретическиесведения
Доля производства порошков железа и сплавов на его основе составляет более 80 % мирового производства металлических порошков. Восстановление обеспечивает производство примерно половины всего потребляемого порошка.
Сырьем для порошковой металлургии служат оксиды железа или его хлористые соединения.
В соответствии с диаграммой состояния системы железо–кислород существуют три оксида железа:Fe2O3 – оксид железа, или гематит (30,06 % О2), Fe3O4 – магнетит (27,64 % О2) и FeO – оксид железа (22,27 % О2). Однако на диаграмме состояния Fe–O в данной области присутствует соединение с широкой областью гомогенности на основе FeO, обогащенное кислородом. Его название – вюстит, а общая формула FexO. При температуре ниже 572 оС вюстит неустойчив и распадается на α-железо и Fe3O4.
Наиболее распространенным сырьем являются окисленные руды железа, или прокатная окалина. В высокообогощенном рудном концентрате железо находится в виде гематита, магнетита, лимонита (HFeO2) и сидерита (FeCO3). Концентраты дороже прокатной окалины и уступают ей по содержанию железа, но содержат меньше серы и окиси марганца. Окалина, образующаяся при прокатке углеродистых сталей, содержит 70–75 % Fe, до 0,4 % C, а также окислы кремния и марганца (до 0,5 %), примеси серы и фосфора. Перспективным сырьем являются осадки, полученные из травильных раство-
Процессы порошковой металлургии. Метод. указания к лабораторным работам |
-13- |
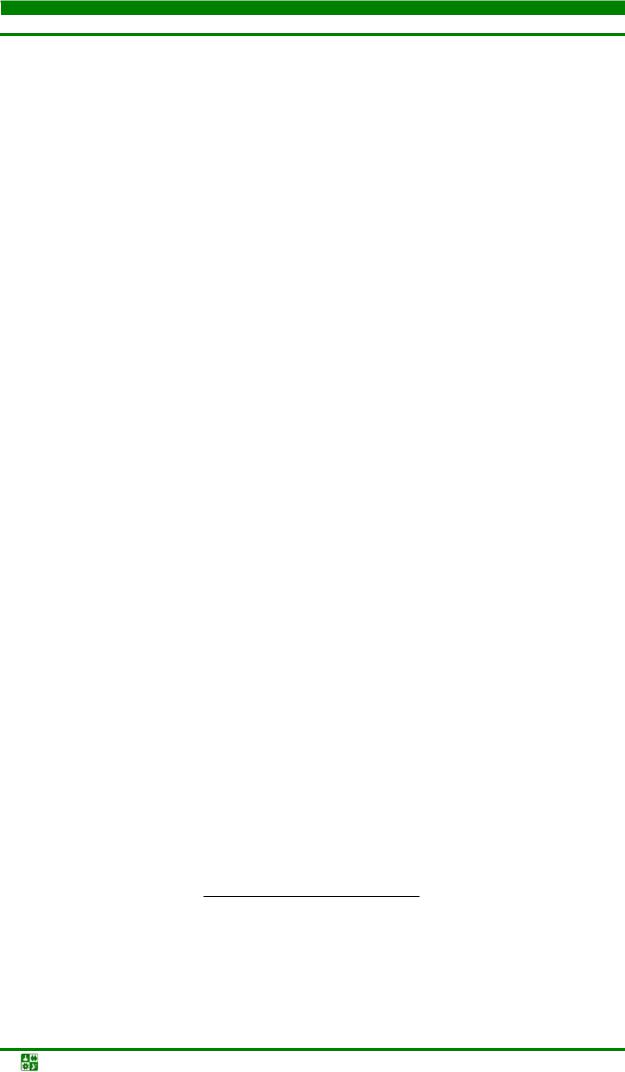
ЛАБ. Р. 1 ПОЛУЧЕНИЕ ПОРОШКОВ ЖЕЛЕЗА ВОССТАНОВЛЕНИЕМ ОТХОДОВ ОБРАБОТКИ МЕ ТВЕРДЫМ УГЛЕРОДОМ
Краткие теоретические сведения
ров. Процесс их выделения состоит в выпаривании сернокислого раствора железа, а затем в сушке образовавшегося осадка при температуре 600–800 оС.
Химически чистые оксиды железа в качестве сырья применяются крайне редко и только при получении каких-либо специальных материалов (например сплава системы W–Ni–Fe), так как подобные порошки дороги.
Восстановлениеоксидовжелеза твердымуглеродомиегооксидом
Реакция восстановления оксидов железа твердым углеродом протекает по следующему механизму:
3Fe2O3 |
+ C |
= 2Fe3O4 |
+ CO |
(1.1) |
|
6Fe2O3 |
+ C |
= 4Fe3O4 |
+ CO2 |
(1.2) |
|
xFe3O4 + C = 3FexO + CO |
(1.3) |
||||
2xFe3O4 + C = 6FexO + CO2 |
(1.4) |
||||
FexO + C = xFe + CO |
|
(1.5) |
|||
2FexO + C = 2xFe + CO2 |
(1.6) |
||||
Fe3O4 |
+ 4C |
= 3Fe + 4CO |
(1.7) |
||
Fe3O4 |
+ 2C |
= 3Fe + 2CO2 |
(1.8) |
Однако непосредственное взаимодействие твердых частиц железа с углеродом развивается слабо из-за малой поверхности взаимодействия частиц шихты. Практически восстановление оксидов железа обеспечивает СО, образующийся при окислении углерода.
Реакции, протекающие с участием газовой фазы, выглядят следующим образом:
3Fe2O3 + CO = 2Fe3O4 + CO2 + Q |
(1.9) |
xFe3O4 + CO = 3FexO + CO2 – Q |
(1.10) |
FexO + CO = xFe + CO2 + Q |
(1.11) |
Все приведенные реакции являются суммарными, идущими с образованием окислов углерода:
MeO + CO = Me + CO2
C + CO2 = 2CO
MeO + C = Me + CO
Механизм восстановления оксидов железа СО основывается на ад- сорбционно-автокаталитической теории. Основные элементарные акты гетерогенной топохимической реакции (т.е. реакции, сопровождающейся пре-
Процессы порошковой металлургии. Метод. указания к лабораторным работам |
-14- |
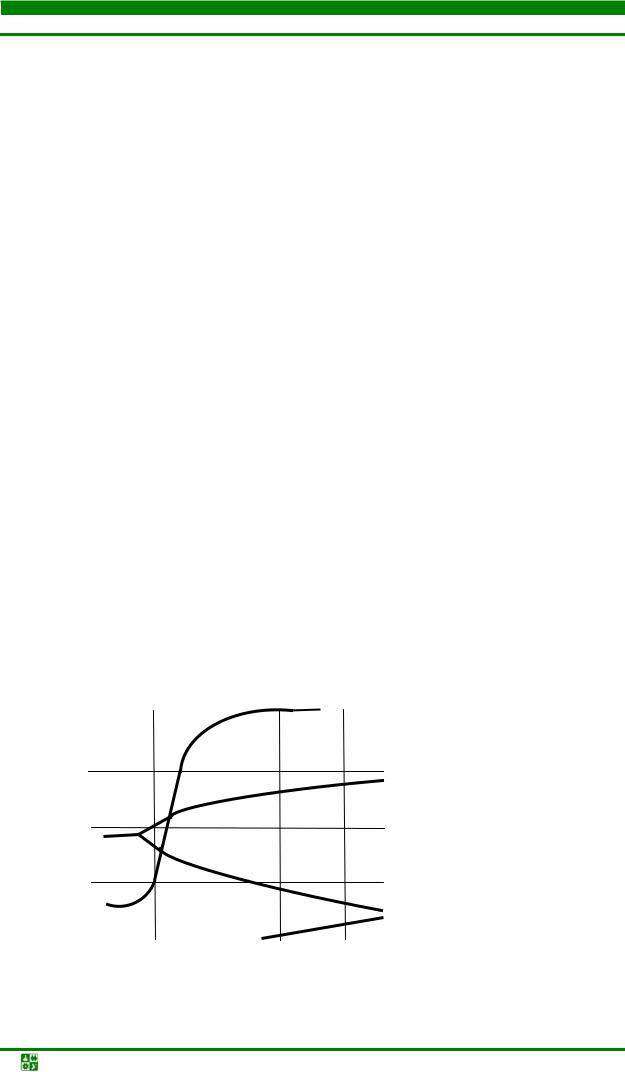
ЛАБ. Р. 1 ПОЛУЧЕНИЕ ПОРОШКОВ ЖЕЛЕЗА ВОССТАНОВЛЕНИЕМ ОТХОДОВ ОБРАБОТКИ МЕ ТВЕРДЫМ УГЛЕРОДОМ
Краткие теоретические сведения
вращениями в твердом состоянии, когда исходное твердое вещество с одной кристаллической решеткой исчезает и образуется твердый продукт с другой кристаллической решеткой) происходят в следующем порядке:
1)внешняя диффузия молекул CО к поверхности частицы оксида железа и их физическая адсорбция на ней;
2)активирование адсорбированных молекул СО вследствие воздействия на них силового поля кристаллической решетки оксида железа и их деформация, создание активных комплексов;
3)отрыв анионов кислорода от поверхности оксида железа на энерге-
тически наиболее выгодных (дефектных) местах с образованием СО2 и десорбированием этих молекул – газообразных продуктов реакции;
4)образование катионов железа при отнятии с поверхности его оксида аниона кислорода, частичный расход их на образование и достройку кристаллов металла с присоединением электронов, а также их диффузия в глубь решетки оксида железа и восстановление его высшей или промежуточной формы до соединения более низкой валентности. Одновременно происходит встречная диффузия ионов кислорода внутри решетки оксида железа к ее наружным поверхностям.
Процесс зарождения кристаллов новой фазы в результате кристаллохимической перестройки исходного оксида железа по мере пересыщения его ионами железа требует преодоления определенного энергетического барьера, что проявляется в замедлении процесса в его начальном периоде. Образование достаточного количества металлической фазы действует автокаталитически и процесс ускоряется. Когда внешняя диффузия газов, адсорбция восстановителя, десорбция газообразных продуктов реакции происходят с достаточной скоростью, что наблюдается при повышенных температурах, диффузия ионов через слой твердых продуктов реакции и внутри кристаллов оксида железа может лимитировать суммарную скорость всего процесса в целом.
Кривые равновесия реакций восстановления оксидов железа окислами углерода приведены на рис. 1.1.
СО, % |
|
|
|
|
|
|
|
СО2, % |
|
|
|
|
Р = 1 атм |
|
|
|
|
|
1) С + СО2 |
= 2СО |
|||
|
|
|
|
|
|
|
|
||||
90 |
|
|
|
|
|
|
|
10 |
2) FeO + CO = Fe + CO2 |
||
|
|
1 |
|
2 |
|
|
3) Fe3O4 |
+ CO = FeO + CO2 |
|||
|
|
|
|
|
|
|
|||||
|
|
|
|
|
|
|
4) Fe2O3 + CO = Fe3O4 + CO2 |
||||
|
|
|
|
|
|
|
|
|
|||
60 |
|
|
|
|
FeO (вюстит) |
|
40 |
|
|
|
|
|
|
|
|
|
|
|
|
|
|
||
30 |
|
|
|
|
|
3 |
|
70 |
|
|
|
|
|
|
|
|
4 |
|
|
|
|
|
|
|
|
|
|
|
|
|
|
|
|
|
|
400 |
600 |
800 |
1000 |
1200 |
Т, оС |
|
|
|
Рис. 1.1. Кривые равновесия реакций восстановления оксидов железа окислом углерода
Процессы порошковой металлургии. Метод. указания к лабораторным работам |
-15- |
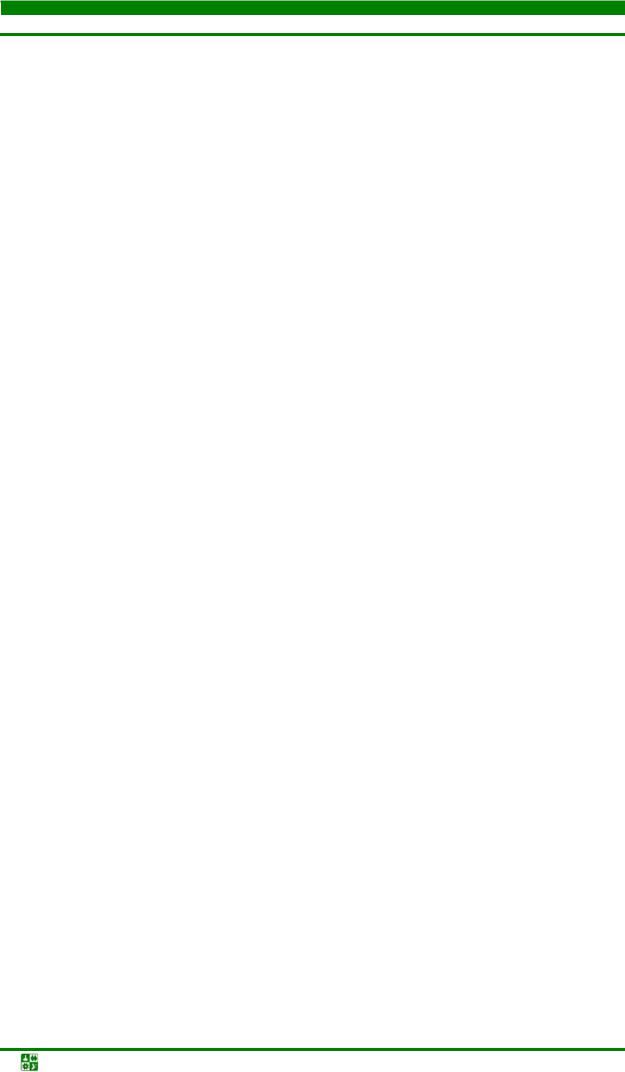
ЛАБ. Р. 1 ПОЛУЧЕНИЕ ПОРОШКОВ ЖЕЛЕЗА ВОССТАНОВЛЕНИЕМ ОТХОДОВ ОБРАБОТКИ МЕ ТВЕРДЫМ УГЛЕРОДОМ
Краткие теоретические сведения
Исходя из этих кривых можно сделать вывод, что производство железного порошка целесообразно вести при температурах не ниже 690 оС и концентрации СО в пределах от 60 до 100 %.
Основныетехнологическиеварианты полученияпорошковжелеза
Восстановление твердым углеродом
При получении порошков железа данным способом в качестве восстановителя используют молотый графит, кокс или термошлыб. В случае применения в качестве восстановителя термошлыба или кокса в состав шихты вводят известняк, который связывает серу в этих компонентах.
Окисленное сырье и восстановительную смесь засыпают кольцевыми слоями в тигли из карбида кремния таким образом, чтобы слой сырья располагался между слоями восстановителя. Примерный состав шихты в тигле составляет 60–69 % оксидного сырья, 25–33 % термошлыба или кокса, 6–7 % известняка. Подготовленный тигель загружают в печь и выдерживают при температуре 1 175–1 200 оС в течение 10–40 ч.
После выгрузки из печи контейнеры без крышек поступают на самообезуглероживающий отжиг при температуре 770–850 оС в течение 4–10 ч. Образовавшуюся губку извлекают из контейнера, подвергают дроблению, магнитной сепарации и рассеву на фракции.
Восстановление сажистым железом
Сажистое железо получают путем термокаталитического разложения углеводородных газов на поверхности или в порах железной губки при температуре 700–900 оС. Оптимальное содержание углерода в сажистом железе составляет от 20 до 50 %, наибольшая активность восстановителя наблюдается при 20–25 % углерода, а максимальная удельная поверхность (около 7 м2/г) при 50 % содержании углерода. Основная масса углерода в сажистом железе находится в свободном состоянии. Введение сажистого железа в восстанавливаемую шихту позволяет ускорить процесс восстановления и уменьшить температуру на 100 –200 оС. Это, в свою очередь, позволяет снизить (на 20–30 %) себестоимость продукции.
Комбинированное восстановление
Сущность этого метода состоит в одновременном действии на исходное окисное сырье твердого и газообразного восстановителя. Количество твердого восстановителя в шихте эквивалентно примерно 60 % содержания кислорода в окисном сырье, остальные 40 % кислорода удаляются действием газа-восстановителя, поступающего в печь.
Процессы порошковой металлургии. Метод. указания к лабораторным работам |
-16- |
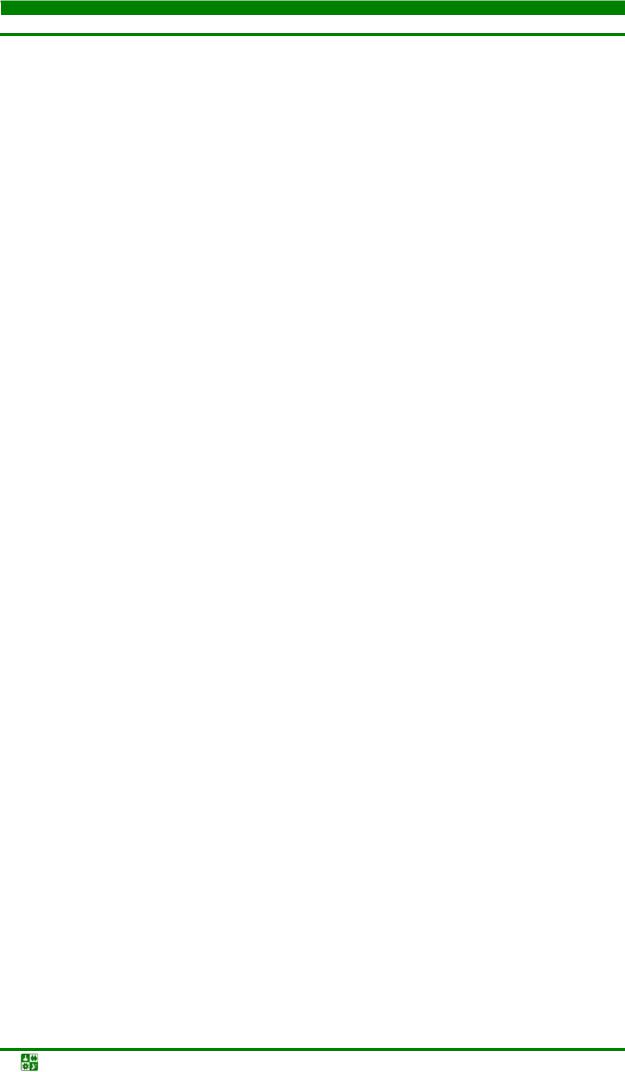
ЛАБ. Р. 1 ПОЛУЧЕНИЕ ПОРОШКОВ ЖЕЛЕЗА ВОССТАНОВЛЕНИЕМ ОТХОДОВ ОБРАБОТКИ МЕ ТВЕРДЫМ УГЛЕРОДОМ
Краткие теоретические сведения
Комбинированное восстановление позволяет получать порошок с пониженным содержанием углерода (менее 0,1 %). Кроме того, существенно ускоряется процесс восстановления.
Порцию шихтовых материалов помещают на противень из пористого железа, опускаемый в печь. Процесс восстановления ведут при температуре 1 100–11 50 оС в течение 6–8 ч. В печь по принципу противотока подают холодный или разогретый газ-восстановитель. После выбивки из поддона губчатое железо подвергают дроблению и размолу до крупности частиц менее 0,5 мм. После этого полученный порошок подвергают магнитной сепарации и рассеву на фракции.
Содовый способ
Сущность содового способа заключается в совмещении процесса восстановления и химического рафинирования железосодержащего сырья кальцинированной содой (Na2CO3). Процесс восстановления осуществляют при нагреве шихты из смеси оксида железа, углерода и соды до температуры выше 700 оС. Примеси, содержащиеся в шихте (кислородные соединения кальция, кремния, марганца, мышьяка, фосфора и пр.), образуют растворимые в воде и разбавленных кислотах соединения на основе натрия (Na2O Al2O3 2SiO2, Na2SiO3, Na3Po4 и пр.). Соду берут с четырех-, пятикратным избытком от необходимого на связывание примесей. Сода при восстановлении действует каталитически, ускоряя газификацию углерода и кристаллохимические превращения в восстанавливаемом материале.
Исходные компоненты шихты (железосодержащий материал с размерами частиц около 100 мкм – 80 %, нефтяной кокс – 10 % и соду – 10 %) смешивают в смесителе с шарами в течение 5–7 ч. При наличии операции окомкования соду в шихту вводят в виде водного раствора. Это позволяет равномерно распределить соду по объему материала.
Восстановление проводят в муфельной печи (температура– 950–1 000 оС, время восстановления – 11–12 ч), либо в конвейерной печи (температура – 1 050–1 100 оС, время восстановления – 5–6 ч). Полученный спек измельчают в молотковой дробилке и подвергают мокрому размолу в шаровой мельнице до размеров частиц около 200 мкм. Полученную пульпу обрабатывают водой и слабокислыми растворами в три этапа. После этого порошок обезвоживают, сушат и отжигают в атмосфере водорода (температура 1 100 оС, время отжига 6–7 ч). Отжиг проводят в муфельной печи. После отжига спекшуюся губку дробят, а полученный порошок рассеивают на фракции и упаковывают.
Восстановление оксидов железа водородом
Этот процесс происходит по трехступенчатой или двухступенчатой схеме, аналогичной схеме восстановления оксида углеродом. Механизм вос-
Процессы порошковой металлургии. Метод. указания к лабораторным работам |
-17- |
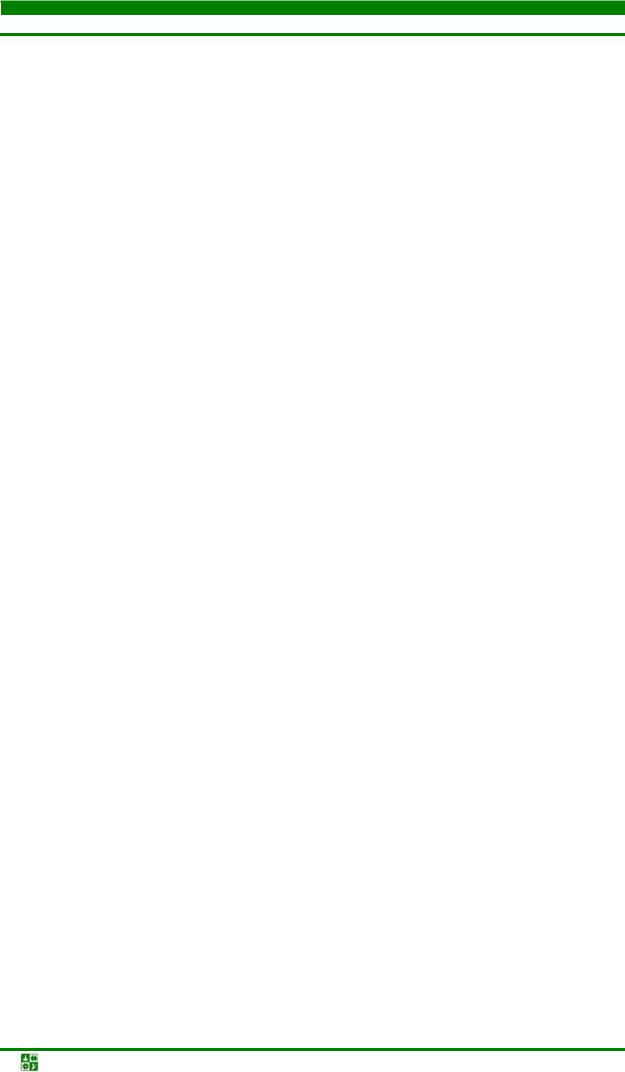
ЛАБ. Р. 1 ПОЛУЧЕНИЕ ПОРОШКОВ ЖЕЛЕЗА ВОССТАНОВЛЕНИЕМ ОТХОДОВ ОБРАБОТКИ МЕ ТВЕРДЫМ УГЛЕРОДОМ
Краткие теоретические сведения
становления базируется на адсорбционно-автокаталитической теории. Основные акты реакции сопровождаются превращениями в твердом состоянии, когда исходное твердое вещество с одной кристаллической решеткой исчезает и образуется твердый продукт с другой кристаллической решеткой.
На скорость процесса восстановления оксида железа водородом существенное влияние оказывает концентрация паров воды в реакционной зоне, так как ее увеличение препятствует развитию реакции из-за адсорбции молекул воды на поверхности частиц оксида. В зависимости от характера пористости и газопроницаемости шихты суммарный процесс может лимитироваться диффузией газов (как восстановителя, так и продуктов реакции) через слой образующегося металла и его исходного соединения.
В настоящее время на практике применяют три основные технологические схемы процесса восстановления оксидов железа водородом: восстановление в стационарном слое, восстановление во вращающейся печи, восстановление в кипящем слое.
Описаниелабораторнойустановки
1.Цилиндрический алундовый контейнер.
2.Лабораторная ступка.
3.Весы лабораторные SPU 202 OHAUS, 0,2–200 г, ±0,01–0,02 г.
4.Печь лабораторная муфельная SNOL 30/1300, Тmax = 1 300 оC.
5.Постоянный магнит.
Заданиенавыполнениелабораторнойработы
Методика подготовки шихты для восстановления оксидов железа включает следующие операции:
1)измельчение восстановителя (кокса) и окалины железа;
2)подготовку навесок восстановителя и восстанавливаемого соеди-
нения;
3) загрузку шихты в контейнер.
Для проведения процесса восстановления подготавливают смесь восстановителя (16–35 %) и известняка (в случае использования кокса или термошлыба).
Подготовленные шихтовые материалы загружают в тигель кольцевыми или горизонтальными слоями. Загрузка кольцевыми слоями является более технологичной. Контейнер, закрытый крышкой, помещают в печь и регу-
лятором температуры устанавливают температуру в печи в пределах от 1 150
до 1 200 оС.
Включают печь и после выхода ее на режим восстановления выдерживают тигель в печи в течение 7–15 ч. Затем открывают крышку контейнера
Процессы порошковой металлургии. Метод. указания к лабораторным работам |
-18- |
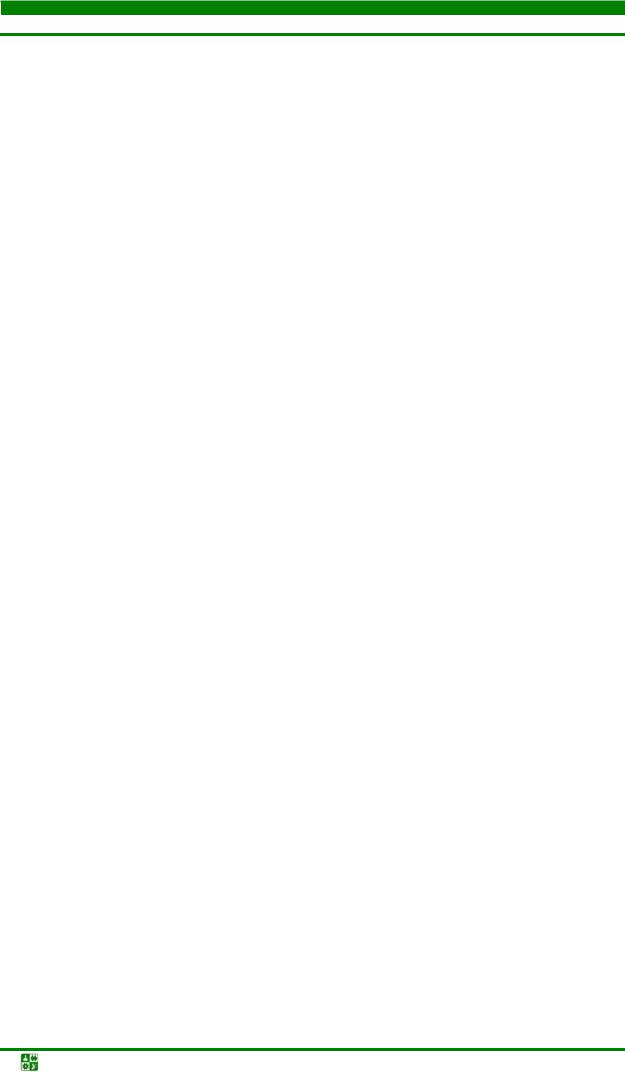
ЛАБ. Р. 1 ПОЛУЧЕНИЕ ПОРОШКОВ ЖЕЛЕЗА ВОССТАНОВЛЕНИЕМ ОТХОДОВ ОБРАБОТКИ МЕ ТВЕРДЫМ УГЛЕРОДОМ
Задание на выполнение лабораторной работы
и, снизив температуру в печи до 700–800 оС, проводят обезуглероживающий отжиг в течение 2–3 ч.
По окончании отжига извлекают контейнер, производят выгрузку материала, удаляют с его поверхности остатки восстановителя. Полученную железную губку измельчают, а порошок подвергают магнитной сепарации.
Проводят определение гранулометрического состава порошка и насыпной плотности. Методами рентгеноспектрального и рентгенофазового анализа устанавливают химический и фазовый состав материала.
Порядоквыполненияработы
1.Изучить особенности механизма восстановления оксидов железа твердыми и газообразными восстановителями.
2.Исходя из реакции восстановления оксида железа углеродом рассчитать количество компонентов реакции.
3.Определить насыпную плотность компонентов реакции (оксида же-
леза и восстановителя).
4.Исходя из насыпной плотности компонентов реакции и их количества (по стехиометрическому соотношению) рассчитать объемы компонентов.
5.При использовании в качестве восстановителя высокосернистого кокса, подготовить смесь восстановителя с известняком (80–82 % кокса, 18–20 % известняка).
6.Подготовить компоненты для засыпки в тигель кольцевыми слоя-
ми.
7.Исходя из рассчитанных объемов компонентов реакции рассчитать геометрические размеры слоев компонентов в цилиндрическом тигле.
8.Пользуясь результатами расчетов геометрических размеров слоев компонентов (главным образом – диаметром слоев), изготовить шаблоны (цилиндры) для засыпки компонентов шихты в тигель.
9.Установить шаблоны в тигель и провести засыпку компонентов шихты равными по высоте слоями. Аккуратно извлечь шаблоны из засыпки.
10.Закрыть тигель крышкой и установить его в печь.
Требованиякотчету
1.Привести цель и задачи работы, краткие теоретические сведения, методику эксперимента, описание структуры полученного материала.
2.Проанализировать влияние технологических факторов на свойства получаемого материала.
3.Оформление отчета должно соответствовать СТО СФУ 4.2-07-2008.
Процессы порошковой металлургии. Метод. указания к лабораторным работам |
-19- |
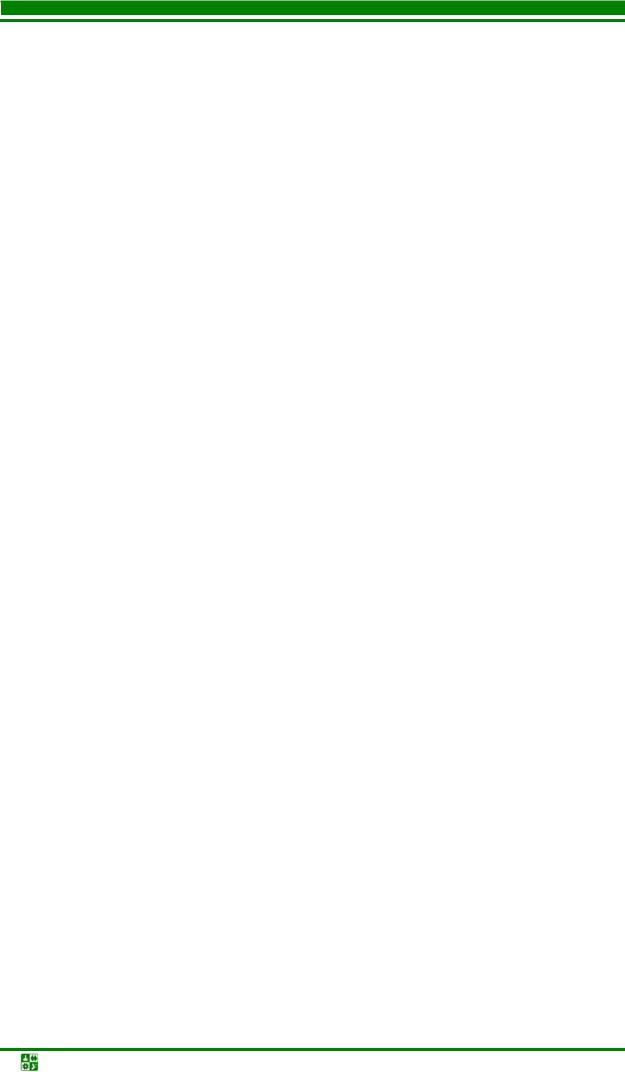
ЛАБ. Р. 1 ПОЛУЧЕНИЕ ПОРОШКОВ ЖЕЛЕЗА ВОССТАНОВЛЕНИЕМ ОТХОДОВ ОБРАБОТКИ МЕ ТВЕРДЫМ УГЛЕРОДОМ
Контрольныевопросыизадания
1.Назовите основные методы получения порошков железа.
2.Какое сырье является наиболее распространенным при получении порошка железа и почему?
3.Назовите основные типы восстановителей.
4.Назовите основные технологические параметры восстановления оксида железа углеродом.
5.Какова сущность содового способа получения железного порошка?
6.Каковы преимущества применения сажистого железа при восстановлении?
7.В чем заключается комбинированное восстановление? Каковы основные принципы и характеристики получаемого продукта?
Процессы порошковой металлургии. Метод. указания к лабораторным работам |
-20- |