
автоматизация / Пособе промышленные роботы / Глава 2
.pdfПрограмматор предназначен для оперативного контроля, программирования и управления системой управления (СУР) и манипулятором. Программатор обеспечивает возможность ввода, коррекции, стирания программ, отдельных наборов. Программатор обеспечивает возможность ручного управления перемещением подвижных осей манипулятора, управления захватами.
Силовой узел располагается в нижней полости шкафа. Его назначением является преобразование сигналов управления в сигналы высокой мощности, обеспечивающие перемещение осей робота.
Силовой узел включает в себя:
-блоки питания;
-платы контроллеров сервоприводов осей А1…А6;
-блок логики.
Блоки питания предназначены для питания устройств, входящих в состав силового узла, системы управления, манипулятора:
-приводов основных осей;
-приводов осей кисти;
-реле, контакторов, блока управления микропроцессором, программатора;
-блок логики;
-датчиков абсолютного значения.
Платы контроллеров сервоприводов осей А1…А6 предназначены для управления работой двигателей манипулятора по определённому закону.
Блок логики предназначен для сбора, переработки, согласования и перераспределения сигналов связи, защиты, контроля, сигнализации между периферией, узлом управления и силовым узлом. Предназначен для самообследования системы управления роботом и сигнализации об ошибках работы.
2.2.2. Управление промышленным роботом. Характеристики движений
Решающую роль в определении характера движения играет выбранный вид управления. Всего различают три вида управления движением робота: цикловое, позиционное, контурное.
При цикловом управлении задается только последовательность движений, а положения подвижных частей задаются упорами или путевыми выключателями, примером такого робота может являться робот ПР-9 (рис. 2.32). Это сверхлёгкий робот, имеющий грузоподъёмность 0,2 кг, который используется в основном в качестве вспомогательного робота. В различных спецификациях он серийно выпускается отечественной промышленностью на нескольких заводах. Привод робота – пневматический, управление – цикловое, поэтому он прост, надёжен и дешёв. Но его возможности существенно ограничены: малое число команд в программе (не более 10), малые скорости перемещения (выдвижение руки – 0,3 м/с, подъём руки – 0,1 м/с). Максимальное линейное перемещение руки составляет 150 мм, пе-

ремещение при подъёме очень мало (30 мм). Диапазон угла поворота составляет 1200, это очень маленькая величина, но для обслуживания одной единицы оборудования – контактной сварочной машины этого вполне достаточно. Масса робота вместе с основанием составляет 70 кг. Большинство модификаций робота МП-9 имеет один штатный клещевой захват, рабочие элементы и их модификации изготавливаются на предприятии, на котором он работает. Программирование движений робота осуществляется на штекерной панели пульта управления. Положение точек позиционирования задаётся перестановкой упоров или якорей герконовых датчиков.
При осуществлении позиционного управления программируется последовательность выполнения и конечные точки движений. В современных роботах происходит движение одновременно нескольких осей, обеспечивающее перемещение острия инструмента из начальной точки в заданную за минимальное время. При этом характер движения острия инструмента между начальной и заданной точками не задается. Для обеспечения минимального времени позиционирования скорость движения осей выбирается обычно максимальной. В стандартной системе позиционирования предусматривается одновременное включение по всем осям с максимальными скоростями. Движение по всем осям выполняется независимо друг от друга и включает в себя в общем случае – разгон, движение с запрограммированной скоростью, торможение (рис. 2.33).
Рис. 2.32. Промышленный робот вспомогательного типа МП-9
Время позиционирования определяется временем движения одной оси, движение по которой из начальной точки в заданную занимает самый длительный промежуток времени. В то же время все оси, участвующие в движении в общем случае испытывают максимальные динамические нагрузки, связанные с разгоном до максимальной скорости и торможением.
Снижения динамических грузок на малоподвижные оси можно достичь, если в системе управления предусмотреть перемещение с максимальной скоростью

только той оси (ведущей), движение которой из начальной точки в заданную требует наибольшего времени по сравнению с другими осями. По остальным осям скорости снижаются до уровней, обеспечивающих выход в заданную точку одновременно с ведущей осью. При этом время позиционирования не увеличиваются, зато значительно снижаются динамические нагрузки на другие оси.
Рис. 2.33. Позиционное управление перемещением осей А1 и А2: 1-классическое; 2-перспективное
При реализации позиционного управления на практике в ряже случаев не требуется точного выхода рабочего инструмента в запрограммированную позицию например, при обводе инструмента препятствия по контуру. В этом случае остановка в конце движения приведет к излишним динамическим нагрузкам на оси и увеличению времени позиционирования. В современных системах управления предусмотрена возможность движения с плавным переходом от одной команды позиционного управления к другой. При этом, как только острие инструмента достигает области перехода, не дожидаясь окончания позиционирования, вводится следующая программа и включается её отработка. Остановка движения между командами не происходит, траектория движения инструмента не проходит через запрограммированную в предыдущей команде точку позиционирования
(рис. 2.34).
а) б)
Рис. 2.34. Траектория движения острия инструмента при позиционном управлении от точки 1 к точке 3 через точку 2:а) с остановкой в точке 2; б) с плавным переходом
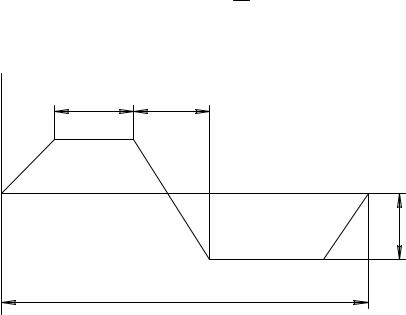
Область перехода при этом определяется машинными данными. Она не может быть больше половины пути позиционирования ведущей оси, если ведущая ось не достигает максимальной скорости. В случае если ось достигает максимальной скорости, область перехода не может быть больше участка торможения.
При контурном управлении программируется вся траектория движения и скорости перемещения по осям. В современных роботах возможно контурное управление с линейной и круговой интерполяцией, маятниковое движение.
При линейной интерполяции обеспечивается прямолинейное перемещение острия инструмента из исходной точки в запрограммированную. При этом ориентация инструмента может быть запрограммированная постоянная или переменная. При постоянной ориентации изменение ориентации происходит в начале движения, а последующее движение происходит без изменения ориентации инструмента в пространстве. При переменной ориентации изменение ориентации инструмента в пространстве происходит в стечение всего движения.
При круговой интерполяции острие инструмента описывает окружность по трем заданным точкам (начальная, промежуточная, конечная). При этом ориентация инструмента программируется и отрабатывается аналогично линейной интерполяции.
При включении маятниковой функции движение инструмента по траектории происходит качание инструмента. Это является необходимым для выполнения некоторых видов сварки, нанесения мастики или клея.
Параметры маятниковой функции (рис. 2.35): PA – амплитуда качания 0,1…99,9мм;
PL – период колебаний 0,1…999,9мм;
PF – фактор вибрации, характеризует форму колебаний (0…200).
PF = BA
При А = 0 - треугольные колебания PF = 0,
при PF = 200 - прямоугольные колебания.
ÀÂ
ÐÀ
ÐL
Рис. 2.35. Параметры маятниковой функции

Современные промышленные роботы работают в трёх видах системы координат, выбираемым пользователем:
-система координат робота;
-декартова система координат;
-система координат инструмента.
В системе координат робота положение острия инструмента и его перемещение в пространстве однозначно определяется положением осей робота. При этом острие инструмента движется вокруг соответствующей оси робота (рис. 2.36). Эта система координат применяется для управления положением отдельных частей манипулятора.
Рис. 2.36. Система координат робота
При движении робота в декартовой системе координат (рис. 2.37) задействованы все оси манипулятора. При этом положение острия инструмента движется по соответствующим осям декартовой системы координат, а ориентация инструмента остаётся постоянной. Изменение ориентации инструмента в пространстве задается в угловых координатах, при этом острие инструмента остаётся неподвижным. Такая система используется при программном задании положения инструмента.
Z
îñüZ
Y ü ñ î
+Ñ
+ |
 |
|
-
À
|
îñü Õ |
Y |
|
а) |
б) X |
||
|
Рис. 2.37. Движение инструмента робота в декартовой системе координат робота
Система координат инструмента тоже является декартовой, но при движении робота в декартовой системе координат инструмента точка начала координат совпадает с острием инструмента, ось ОХ совпадает с осью инструмента. При этом в движении участвуют все оси робота, обеспечивая перемещение острия параллельно осям координат, ориентация инструмента в пространстве не изменяется. При изменении ориентации инструмента в пространстве поворачивается и вся система координат. Использование системы координат инструмента позволяет использовать контурное управление, вводить программ методом обучения, корректировать положение инструмента в пространстве относительно данного (например, «вправо на 10 мм»).
2.2.3. Управление промышленными роботами в составе технологических линий
Для управления работой гибких производственных систем на базе роботов (несколько роботизированных технологических комплексов, роботизированная технологическая линия, роботизированный технологический участок и т.д.) необходимо оперативное получение информации о состоянии элементов системы, отдача исполнительных команд и перепрограммирование. Для этих целей предусмотрено объединение контроллеров всех исполнительной устройств единую локальную сеть.
Такая система построена следующим образом. Роботизированная технологическая линия разделяется на конечное число операций (рис. 2.38), на каждую из которых приходится определённое количество контроллеров роботов. Работа контроллеров каждой операции индицируется на терминале, где показываются этапы работы и выводимые ошибки в работе контроллеров. Работа всей линии индицируется на Главной вычислительной машине (ГВМ) через локальную сеть
Ethernet.
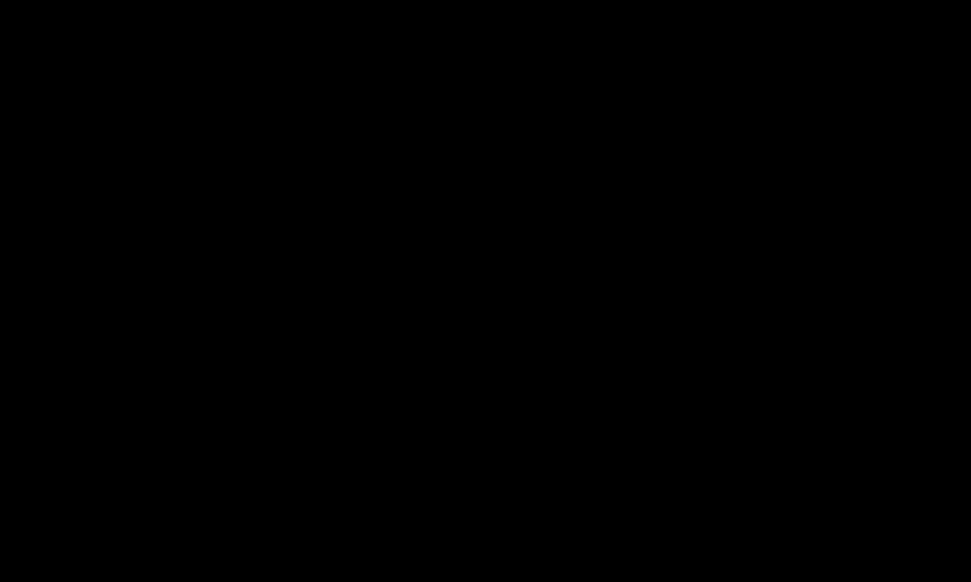
Рис. 2.38. Соединение контроллеров роботизированной технологической линии
Контрольные вопросы к главе 2
1.Из каких основных систем состоит промышленный робот и каково назначение каждой части?
2.Из каких основных частей состоит параллелограммный шестиосный манипулятор, как происходят его перемещения по этим осям?
3.Их каких основных частей состоит антропоморфный шестиосный манипулятор, как происходят его перемещения по этим осям?
4.Каково назначение и состав системы вывешивания промышленного робота ПР
601/60?
5.Из каких компонентов состоит и как работает система вывешивания шестиосного антропоморфного манипулятора промышленного робота?
6.Как устроена кисть промышленного робота серии «KUKA Famulus»?
7.Какие передаточные механизмы используются в современных промышленных роботах?
8.Как осуществляется регулирование направления и изменение скорости вращения серводвигателя по заданному закону у современных промышленных роботов?
9.При помощи каких технических решений увеличивают рабочую зону промыш-
ленных роботов?
10.Из каких узлов состоит управления промышленным роботом, какие компоненты включает в себя каждый узел?
11.Дайте определение циклового, позиционного и контурного управления промышленным роботом.
12.По какому закону изменяется скорость перемещения по оси подвижности при позиционном управлении, какие при этом возможны перемещения от точки к точке?
13.В каких системах координат рассчитывается перемещение рабочего инструмента промышленного робота?
14.Как осуществляется управление промышленными роботами в составе автоматических линий?