
автоматизация / Пособе промышленные роботы / Глава 5
.pdfГлава 5 РОБОТЫ ДЛЯ КОНТАКТНОЙ ТОЧЕЧНОЙ СВАРКИ
Одной из динамично развивающихся областей применения промышленных роботов является контактная точечная сварка в автомобилестроении.
Необходимость применения роботов для контактной точечной сварки обусловлена следующими объективными причинами:
1. Переход мирового производителя на использование оцинкованного листового материала, что требует:
1.1.Периодической зачистки электродов после простановки определённого количества сварных точек;
1.2.Осуществления двухстороннего токоподвода к свариваемым деталям;
1.3.Проведения 100% активного контроля качества контактной точечной сварки.
2.Расширение модельного ряда кузовов автомобилей.
3.Повышение точности сборки и сварки деталей кузова.
4.Снижение доли ручного труда на производстве.
По области применения роботы для контактной точечной сварки занимают место после универсальных подвесных сварочных машин и перед узкоспециализированными многоэлектродными сварочными агрегатами, экономически выгодными только для массового производства одной модели изделия в течение многих лет. В автомобилестроении раньше, чем в других областях машиностроения начали применяться роботизированные линии и гибкие (автоматически переналаживаемые) производственные системы на основе роботов для контактной точечной сварки. Такие системы позволяют автоматизировать не только сварочные, но и сборочные, транспортные, складские и другие операции, что обеспечивает комплексную автоматизацию и роботизацию производства и его автоматический переход на сварку различных моделей изделия в зависимости от порядка поступления заказов.
5.1. История внедрения роботов на ОАО «АВТОВАЗ»
Отечественным предприятием автомобилестроения, на котором использование роботов получило наибольшее развитие, является ОАО «АВТОВАЗ».
Первые роботы «Джулия» в количестве 10 штук появились в 1978 году при запуске в производство автомобиля «Нива». Роботы имели гидравлический привод и шесть степеней свободы. Они использовались для точечной сварки боковин и в прессовом производстве, для разгрузки штампов от деталей. В середине 90-х эти роботы были демонтированы из-за медленного перемещения по осям.
При постановке в производство ВАЗ 2105-2107 на линии доварки кузова использовалось 25 роботов КАВАСАКИ (Япония) с пятью и шестью степенями подвижности.
В 1986 году при запуске в производство ВАЗ 2108, 2109, 21099 было смонтировано 50 роботов «Юнимейт» (США) и 30 роботов «Бета» (ПТО ВАЗ), используемых для точечной сварки и в металлургическом производстве.
В1993-95 г.г. при запуске модели ВАЗ 2110 было смонтировано 230 роботов СУР-101 (производство ПТО) с манипуляторами ПР601/60 и ПР161/60 (по лицензии фирмы «Кука», ФРГ). Роботы имеют различную комплектацию и используются при точечной, дуговой сварке, нанесении мастики и клея, на погрузочных работах. Робот ПР-601/60 грузоподъемностью 600 Н несет сварочные клещи с прямолинейным ходом электродов или радиальные со встроенным трансформатором, имеет шесть управляемых осей и обеспечивает позиционирование клещей с точностью ±1,2 мм. «Рука» робота поворачивается вокруг вертикальной оси стойки основания на 320°. Границы рабочей зоны его 1100…2700 мм от вертикальной оси стойки и до 3000 мм по вертикали от площадки крепления. В пределах рабочей зоны могут быть запрограммированы до 1000 точек позиционирования клещей. Робот ПР-161/60 перемещается по порталу, несет одноэлектродный сварочный пистолет, предназначенный для сварки изделия, расположенного на омедненном кондукторе. Сварочное усилие, развиваемое пистолетом, составляет 5 кН. Площадь рабочей зоны под порталом 6х2,5 м. Емкость программы – 1000 точек. Точность позиционирования ±1 мм. В качестве источника сварочного тока используется выпрямитель, один полюс которого присоединяется к пистолету, а другой — к кондуктору, на котором располагается свариваемое изделие. Роботы снабжаются пультом ручного управления, с помощью которого может быть выполнено программирование обучением.
В1997 году в НТЦ было установлено 4 робота СУР 101 с манипуляторами ПР 161/60, на которых крепились лазеры для резки металла.
В1998 году 80 роботов СУР 101 были заменены на более современные ро-
боты KR-1.
В2002 году при производстве автомобиля Нива-Шевроле используется 30 роботов с контроллером KRС-1 для точечной сварки.
При проектировании нового семейства КАЛИНА заложено 320 роботов с контроллерами KRС-2, роботы будут использованы вместо транспорта для перегрузке детали с одной операции на другую, для точечной сварки, электродуговой сварке, и для приклейке потолков на конвейере.
5.2.Классификация промышленных роботов для контактной свар-
ки
Всоответствии с ГОСТ 26054-85 «Роботы промышленные для контактной сварки. Общие технические условия» ПР для контактной точечной сварки классифицируются:
1. По способу установки на рабочем месте: напольные (рис. 5.1-а), подвесные настенного исполнения (рис. 5.1-б) и подвесные потолочного исполнения (рис. 5.1-
в).
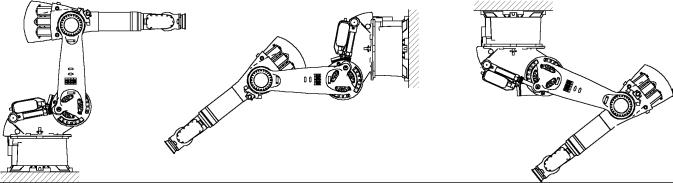
а) б) в)
Рис. 5.1. Классификация ПР для контактной сварки по способу установки на рабочем месте
2. По месту размещения источника сварочного тока:
-со встроенным в исполнительное устройство промышленного робота источником сварочного тока;
-со встроенным в рабочий орган промышленного робота источником сварочного тока;
-с отдельным (вне исполнительного устройства и манипулятора про-
мышленного робота) источником сварочного тока.
На рис. 5.2 представлен манипулятор промышленного робота КR 125/3 (KUKA) с закрепленными на кисти сварочными клещами со встроенным трансформатором. Такая компоновка (рис. 5.3) состоит из контроллера 1, манипулятора 2 с закрепленными на нем клещами 3 и сварочным трансформатором 4 и имеет следующие преимущества: снижается индуктивность сварочного контура, установочная мощность, отсутствуют гибкие токоподводы, усложняющие конструкцию сварочного контура и требующие постоянной замены вследствие разрушения от электродинамических рывков. Недостаток: увеличивается масса сварочных клещей, что приводит к снижению скорости линейных перемещений, увеличивает нагрузку на оси и снижает точность позиционирования и ресурс работы манипулятора.
При использовании трансформатора, встроенного в сварочные клещи, можно применять роботы широкого назначения без ограничения их манипуляционных возможностей со стороны токоподводов вторичного контура, так как тяжёлые и жёсткие кабели вторичного контура заменены лёгкими и гибкими кабелями малого сечения первичного контура. Полное сопротивление вторичного контура существенно снижается, что позволяет значительно уменьшить габаритные размеры и массу трансформатора. Клещи со встроенным трансформатором, крепящиеся на руке робота, имеют следующие конструктивные особенности:
-малый вылет электродов и габариты вторичного контура (иначе приходится увеличивать индуктивное сопротивление и масса трансформатора);
-центр тяжести клещей должен по возможности находиться максимально близко к кисти робота (иначе увеличивается нагрузка на кисть робота);
-улучшенный теплоотвод за счёт разделения контуров охлаждения для трансформатора и электрода (ПВ клещей для роботизированной сварки может составлять порядка 50%);
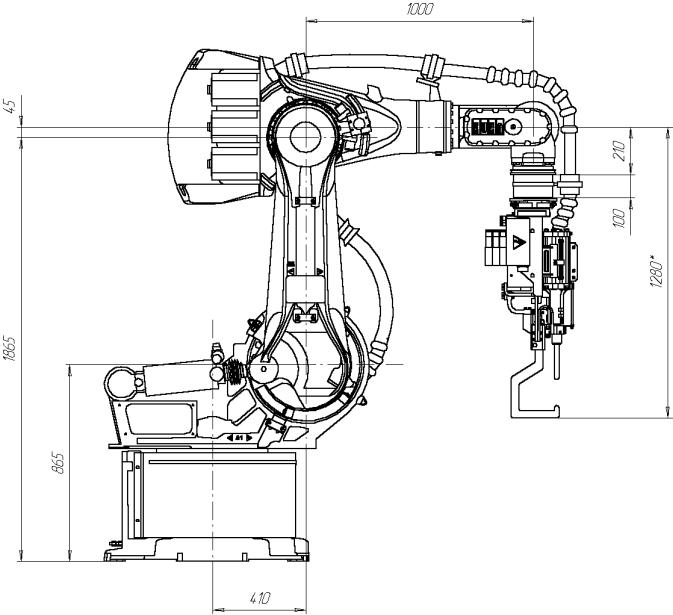
-масса клещей составляет порядка 50 кг для тонколистовых деталей и в отдельных случаях 120 кг для деталей средних толщин;
-сварочные клещи имеют значительные габариты и массу при малом вылете электродов, что делает их маломанёвренными, ими удобно работать только на фронтальных и хорошо доступных сварных соединениях.
Рис. 5.2. Манипулятор KR125/3 (KUKA) для контактной сварки со встроенным в исполнительное устройство сварочными клещами
На рис. 5.4. представлен промышленный робот с отдельным (вне исполнительного устройства и манипулятора) источником сварочного тока. На управляемом от контроллера 1 манипуляторе 2 закреплены сварочные клещи 3, которые соединены со сварочным трансформатором 4 посредством гибких токоподводов 5. Такая схема имеет очевидные преимущества: сварочные клещи такого робота не содержат трансформатора, вследствие чего снижается их масса, что приводит к снижению нагрузок на оси, повышению точности позиционирования и скорости
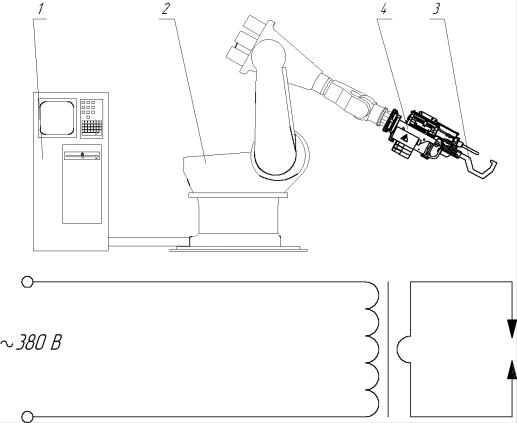
линейных перемещений. Недостаток: увеличение габаритов сварочного контура и установочной мощности силового оборудования.
Рис. 5.3. ПР для контактной сварки со встроенным в исполнительное устройство источником сварочного тока
Размещения источника сварочного тока вне манипулятора робота характерна для универсальных роботов, предназначенных для широкого круга технических и транспортных работ. Чтобы трансформатор не ограничивал рабочую зону робота, кабели должны быть достаточной длины. Однако с их удлинением повышается сопротивление вторичного контура и его нагрев при работе. Для уменьшения сопротивления токоподвода и его нагрева сечение токоподвода увеличивают (иногда до площади 250 мм2). Такие токоподводы плохо изгибаются и создают дополнительную нагрузку на механизм ориентирующих перемещений (кисть) робота. Рабочая зона робота загромождается кабелями, а манипуляционные возможности робота и доступ к внутренним полостям изделия ограничены. Кроме этого, при сварке возникают значительные электродинамические нагрузки, которые разрушают токоподвод, а так же передаются на кисть. Возникающие этом повторные знакопеременные нагрузки на кисть приводят ускоренному износу её механизмов и росту погрешности воспроизведения программы. Возникающие при перемещении манипулятора повторяющиеся изгибы и скручивания токоподводов в сумме с действием электродинамических сил приводит к их быстрому разрушению. Срок его службы обычно составляет не более двух недель (реже - двух месяцев) при двухсменной работе.

Рис. 5.4. ПР для контактной сварки с отдельным источником сварочного тока
Таким образом установлено, что использование робота для контактной сварки со встроенным в клещи источником сварочного тока и робота с отдельным источником сварочного тока имеют свои явные недостатки. Компромиссным решением является использование робота со встроенным в рабочий орган источником сварочного тока. При установке трансформатора на одном из звеньев робота (обычно это основание руки) длина токоведущих элементов вторичного контура значительно (в 2,5…3 раза) уменьшается, но при этом возрастают нагрузки на манипулятор. Поэтому трансформатор устанавливают вблизи места крепления основания руки на коромысле (рис. 5.5) или используют трансформатор в качестве противовеса (рис. 5.5), если в данном типе манипулятора предусмотрено вывешивание оси А3.
При размещении трансформатора на одном из звеньев робота уменьшается длина вторичного контура и, следовательно, габаритные размеры трансформатора, снимаются ограничения на манипуляционные возможности робота, связанные с кабелями, соединяющими клещи с трансформатором, увеличивается срок службы токоподводов, уменьшается дестабилизирующее влияние кабелей вторичного контура на погрешность позиционирования.

Рис. 5.5. ПР для контактной сварки со встроенным в манипулятор источником сварочного тока
В настоящий момент на предприятиях автомобилестроения начинает применяться следующая схема построения робота для контактной сварки без сварочных клещей (рис. 5.6): на работающем от контроллера 1 манипуляторе 2 закреплено захватное устройство 3, робот позиционирует деталь относительно стационарной сварочной машины 4. Такая схема имеет следующие преимущества, характерные для первых двух компоновок: максимальное уменьшение перемещаемых масс, что приводит к увеличению ресурса работы робота, скорости линейных перемещений и
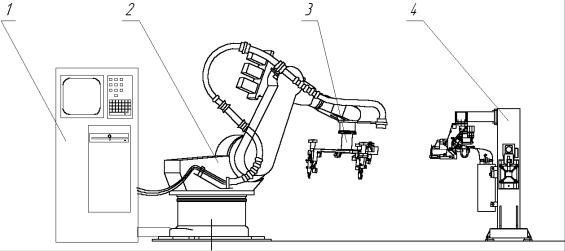
точности позиционирования, снижение габаритов сварочного контура и установочной мощности оборудования, возможность сварки деталей больших толщин, т.к. не ограничена мощность и масса сварочной машины. Однако применимость такой компоновки ограничена следующими её недостатками: затруднена возможность одновременной обварки более двух деталей, в ряде случаев масса свариваемых деталей может оказаться больше массы сварочной машины. Вот почему при сварке крупногабаритных деталей, например, при простановке точек на кузове автомобиля, применяются роботы со встроенными в манипулятор сварочными клещами (первые две компоновки).
На современных предприятиях автомобилестроения находит применение робот, манипулятор которого оснащён комплексным рабочим инструментом, состоящим из сварочных клещей и захватного устройства. Такая спаренная конструкция рабочего инструмента робота позволяет при помощи одного манипулятора производить простановку сварных точек в соответствии с заданной программой, и после этого переместить деталь далее по технологической цепочке. Преимуществами такого подхода является: снижение числа установленных на автоматической линии роботов, продление цикла работы одного робота (увеличение коэффициента загрузки робота на автоматической линии).
Рис. 5.6. Использование для контактной сварки робота без клещей
Конструкция сварочного инструмента для роботизированной контактной точечной сварки зависит от способа подвода тока и может быть с двухсторонним или односторонним подводом сварочного тока. К сварочному инструменту с двухсторонним подводом тока относятся все виды сварочных клещей. К сварочному инструменту с односторонним подводом тока относятся полуклещи и сварочные пистолеты (цилиндры).
Основными типами клещей для роботизированной сварки являются клещи с радиальным ходом электродов (Х-образные) и клещи осевым ходом электродов (С- образные), отличающиеся различными вариантами крепления на фланце кисти робота (рис. 5.7).
а) б)
Рис. 5.7. Сварочные клещи для крепления на кисти робота:
а – С-образные; б – Х-образные прямые и повернутые 1 – клещи; 2 – фланец для крепления рабочего инструмента; 3 – кисть руки
Изделие и сварочнй робот должны быть защищены от повреждения в случае прихватывания электродов к металлу изделия. Даже при оптимальном выборе режима сварки такое прихватывапние не исключено и происходит с периодичностью приблизительно одно прихватывание на 150 тыс. сварных точек. Для защиты от поломок при прихватывании в клещи встраивают датчики: иходного положения электродов, раскрытия (разведения электродов) на рабочий ход, сжатия электродов. При наличии таких датчиков контролируется весь цикл работы механизма клещей. Если электроды не расходятся после сварки очередной точки, например в результате прихватывания электродов, операция сварки изделия прерывается и начинает работать программа вращения роботом вокруг оси электродов. При этом происходит отрыв электрода от изделия.
5.3. Построение РТК и автоматических линий для контактной сварки
Роботизированный технологический комплекс (РТК) — это совокупность единиц технологического оборудования, промышленного робота и средств оснащения, автономно функционирующая и осуществляющая многократные циклы. Роботизированные технологические комплексы, предназначенные для работы в ГПС, должны иметь автоматизированную переналадку и возможность встраивания в систему. В качестве технологического оборудования в РТК может быть использован промышленный робот. Средствами оснащения РТК могут быть устройства накопления, ориентации, поштучной выдачи объектов производства (деталей, заготовок) и другие устройства, обеспечивающие функционирование РТК.
Роботы со встроенными в манипулятор сварочными клещами (рис. 5.2…5.5) используются в составе гибких производственных систем (гибкая автоматизированная линия, гибкий автоматизированный участок, роботизированный технологический комплекс) в нескольких вариациях. Простейший РТК для контактной сварки (рис. 5.8) состоит из манипулятора 1 с закрепленными на нем сварочными клещами, поворотного стола с технологической оснасткой 2, оператора 3 и огорожен оградой 10. Работа такого комплекса определяется циклограммой (рис. 5.9): оператор 3 берет из контейнеров 4 заготовки и укладывает их в установленной последовательности на поворотный стол 2, производя фиксирование прижимами; после завершения укладки заготовок и их фиксации оператор отступает к пульту управления 5 и нажимает кнопки двурукого включения. При этом если оператор находится в зоне поворота стола 2, то на систему управления поступит сигнал «человек в зоне разворота» от датчика давления (установлен в полу) или от объёмного датчика, и система не разрешит дальнейшую работу РТК.
РТК такого типа применяются для сварки листовых конструкций небольших габаритных размеров с малым числом сварных точек (20…50), если такт производства и конструкция изделия позволяют выполнить сварку всех точек на одном рабочем месте.
После нажатия кнопок двурукого включения происходит разворот стола 2 на 1800. При этом манипулятор 1 робота отрабатывает заданную программу сварки, диктуемую шкафом управления 6 и силовым шкафом 7. В это время со второй половины поворотного стола 2 оператор 3 снимает сваренную деталь и укладывает её в контейнер-накопитель 8, после чего производит укладку заготовок на поворотный стол, отступает к пульту 5 и нажимает кнопки двурукого включения, поступает сигнал «конец укладки деталей». После отработки заданной программы сварки манипулятор позиционирует сварочные клещи на концевой выключатель 9, поступает сигнал «конец сварки». В случае если в систему управления РТК поступило оба сигнала «конец сварки» и «конец укладки деталей», а так же нет сигнала «человек в зоне разворота», то происходит разворот стола 2 на 1800, и цикл работы РТК начинается снова. Восстановление рабочей поверхности сварочных электродов происходит автоматически на зачистной машинке 11 после определённого числа циклов работы РТК.