
автоматизация / Пособе промышленные роботы / Глава 3
.pdf3.3. Промышленные роботы на операциях сборки
3.3.1. Общие сведения. Экономическое обоснование применения роботов при сборке
Сборочные и обрабатывающие центры возникли как результат развития технологического оборудования благодаря использованию программного управления, агрегатно-модульного принципа построения, робототехники. Транспортных и магазинных устройств.
Сборочные операции могут быть выполнены сборщиками вручную средствами технической гибкой автоматизации с применением промышленных роботов и специализированным технологическим оборудованием. В первом случае на лицо такие недостатки, как ограниченная производительность, утомляемость, некомплектность и т.д. Два других варианта отличаются друг от друга стоимостью оборудования, быстродействием, уровнем производственных затрат, длительность циклов морального старения оборудования и возможностью использования его при переходе на выпуск новых изделий, а также минимальным объёмом производства, обеспечивающим эффективность эксплуатации.
Специальное автоматическое оборудование проектируют и изготавливают для выполнения конкретных операций для выпуска определённого изделия. Эти машины представляют собой эффективное средство производства, позволяющее с высокой скоростью и минимальными дополнительными расходами выполнять операции сборки большого числа сборочных узлов. Однако такие машины практически невозможно переналадить для работы со сборочными узлами, отличающимися от тех, для производства которых они были разработаны. Поэтому, когда надобность в производстве данных конкретных сборочных узлов отпадает, отпадает и необходимость в использовании такого оборудования, т.е. происходит быстрое его моральное устаревание.
Средства технической гибкой автоматизации имеют меньшее быстродействие, чем специализированное автоматическое оборудование, поскольку они ориентированы на выполнение не одной конкретной операции, а целого класса сходных операций. Затраты на их приобретение обычно несколько выше по сравнению со специализированными автоматическими сборочными машинами, но длительность использования – больше, а эксплуатационные издержки – меньше. Минимальный объём производства, обеспечивающий эффективность их эксплуатации, тоже существенно меньше.
На рис. 3.9. приведено сравнение альтернативных технологий применительно к сборке. При этом ручная сборка рассматривается с применением транспортёров или специальных устройств подачи деталей; сборка специализированных средств автоматизации предполагает применение шаговых или непрерывных транспортёров; программируемая сборка с применением роботизированных комплексов (ячеек) – с использованием конвейеров, робокаров и (или) специальной оснастки.
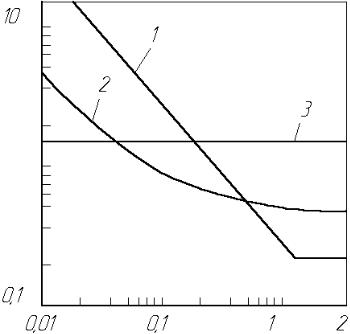
Совокупность сборочных ячеек с различной степенью механизации, автоматизации и гибкости (возможностью переналадки на выпуск различных изделий) образует сборочную производственную систему.
Рис. 3.9. Сравнение вариантов производственных сборочных процессов
Сборочная производственная система – совокупность механизмов и ма-
шин, которая, предотвращая повреждения исходных деталей и сборочных узлов, выполнят их перемещение, позиционирование и совмещение в определённой последовательности, приводя их взаимное расположение, кинематические отношения и физические свойства, возникающие в результате соединения в новый узел, к состоянию, регламентируемому сборочным чертежом или техническими условиями.
В таких системах в каждой из сборочных ячеек (сборочных постов) детали подаются к автоматическому рабочему органу или рабочему-оператору из магазинов, бункеров, питателей или в ёмкостной таре. Сборочные ячейки укомплектованы необходимым для выполнения сборки инструментом. Ячейки связаны между собой конвейером или иным транспортным устройством. Цикл сборки в ячейках может быть синхронным или асинхронным.
Программно-управляемая сборочная система – сборочная система, способная под воздействием управляющих программ собирать различные издеия, выпускаемые разными партиями.
Для создания такой система требуются довольно большие капиталовложения, но после её внедрения достигается существенное ускорение переналадки при переходе к выпуску нового изделия по сравнению со специализированными сборочными системами.
Производственные затраты при использовании программно-управляемой сборочной системы более стабильны, чем при неавтоматизированной сборке. Как правило, программно-управляемую автоматизированную сборочную систему можно успешно применять для средне- и мелкосерийного производства.
3.3.2. Обеспечение работы роботизированной сборочной линии при отказе робота
Роботизированная сборочная линия в общем случае представляет собой шаговой конвейер, вдоль которого размещены роботы, выполняющие последовательные операции сборки (рис. 3.10-а). Отказ любого робота приводит к остановке процесса сборки.
В настоящее время на производстве применяются следующие методы повышения надёжности работы линии:
1)Повышают надёжность работы роботов путём резервирования их элементов. Такие роботы называются редундантными. В соединение звеньев манипулятора вводят два привода вместо одного. При отказе одного привода второй обеспечивает работу манипулятора с пониженной механической нагрузкой на рабочем органе. Более распространено использование дублирующих звеньев манипулятора. В случае отказа одного из звеньев второе принимает на себя его нагрузку. Для того, чтобы робот продолжал работу при отказе одного звена, увеличивают число звеньев и степеней подвижности манипулятора. Этот метод усложняет конструкцию робота.
2)Между роботами размещают накопители, при отказе робота детали, поступающие с предыдущей операции, накапливаются в промежуточном накопителе и после восстановления робота поступают на последующую операцию. Чем больше емкость накопителя, тем больше времени может быть отведено на ремонт отказавшего робота. Этот метод требует значительной дополнительной площади для размещения сборочной линии.
3)Перераспределяют программы между оставшимися роботами при отказе одного из них. При этом необходимо выполнение следующих условий:
-кроме собственной программы каждый робот должен иметь программы соседних роботов;
-каждый робот должен иметь возможность доступа к комплектующим, которые используются предыдущим и последующим роботами;
-каждый робот должен получать информацию о состоянии остальных
роботов в линии.
При этом перераспределение программ работы роботов возможно кооперативным либо редунтандным методами.
При кооперативном методе функции отказавшего робота передаются предыдущему или последующему роботам, программы которых в свою очередь передаются другим роботам. При этом должен быть увеличен интервал подачи деталей на конвейер. Сборочная линия с кооперативным поведением агентов состоит из роботов r1, r2, …, rn, между которыми размещены накопители с комплектующими деталями для смежных роботов Р1, Р2, …, Р3 (рис. 3.10-б). При отказе любого робота rm его функции перераспределяются между соседними роботами. При этом возможны варианты передачи функций отказавшего робота к началу или концу линии.
При передаче программы отказавшего робота rm к началу линии робот rm-1 выполняет операции робота rm, робот rm-2 выполняет операции робота rm-1 и т.д. Ро-
бот r1 выполняет собственные операции и операции робота r2. При передаче функций отказавшего робота rm к концу линии его операции будет выполнять следующий робот rm+1, операции робота rm+1 будет выполнять робот rm+2 и т.д. последний робот rn будет выполнять собственную операцию и операцию робота rn-1. При использовании роботизированный автоматических линий с кооперативным поведением положение отказавшего робота в сборочной линии в целом не влияет на снижение производительности, которая падает в зависимости от времени отказа t, сек по линейной зависимости (рис. 3.11).
В сборочной линии с редундантным поведением роботов на конце линии вводится резервный робот rz (рис. 3.10-в). Промежуточные накопители Р1, Р2, …, Рn содержат комплектующие детали, необходимые для выполнения сборочных операций смежными роботами. При отказе робота rm его операции выполняет робот rm+1, операции робота rm+1 выполняет робот rm+2, а операции последнего робота rn выполняет резервный робот rz. Для этого каждому роботу необходимо иметь две программы: собственную программу и программы предыдущего робота. Резервный робот rz имеет программу только предыдущего робота rn. В отличие от кооперативного метода интервал подачи деталей на позиции сборки при отказе робота изменять не нужно, так как время операции сборки каждым роботом не изменяется. При использовании редундантного метода построения линий отказ одного робота не приводит к потере производительности сборки (рис. 3.12). Однако этот метод требует ввода резервного робота на конце линии.
а)
б)
в)
Рис. 3.10. Роботизированная сборочная линия: а – традиционная структура; б – с кооперативным поведением агентов; в – с редундантным поведением агентов
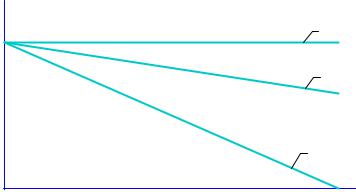
Q, äåò/÷àñ
3
2
1
t, ñåê
Рис. 3.11. Зависимость производительности Q сборочной линии от времени t отказа робота: 1 – традиционная сборочная линия; 2 - кооперативная сборочная линия; 3 – редундантная сборочная линия
Контрольные вопросы к главе 3
1.Какие требования предъявляются к промышленным роботам для погрузочноразгрузочных и транспортно-складских работ?
2.За счёт чего и как обеспечивается выполнение операций штабелирования роботом со стандартным шестиосным манипулятором?
3.Для чего применяются и из каких компонентов состоят портальные роботы балке?
4.Какие существуют разновидности и их кинематические схемы портальных роботов?
5.Какие особенности кинематических схем и конструкции имеют промышленные роботы для погрузочно-разгрузочных работ средней и тяжелой грузоподъемности?
6.Как применение промышленных роботов влияет на себестоимость процесса сборки?
7.Какие существуют варианты построения роботизированной сборочной линии с учётом возможной поломки одного из роботов?