
330 / ЗаданКурсЖурналПолныйМПУСУ / 1СУшоколГлазури
.pdf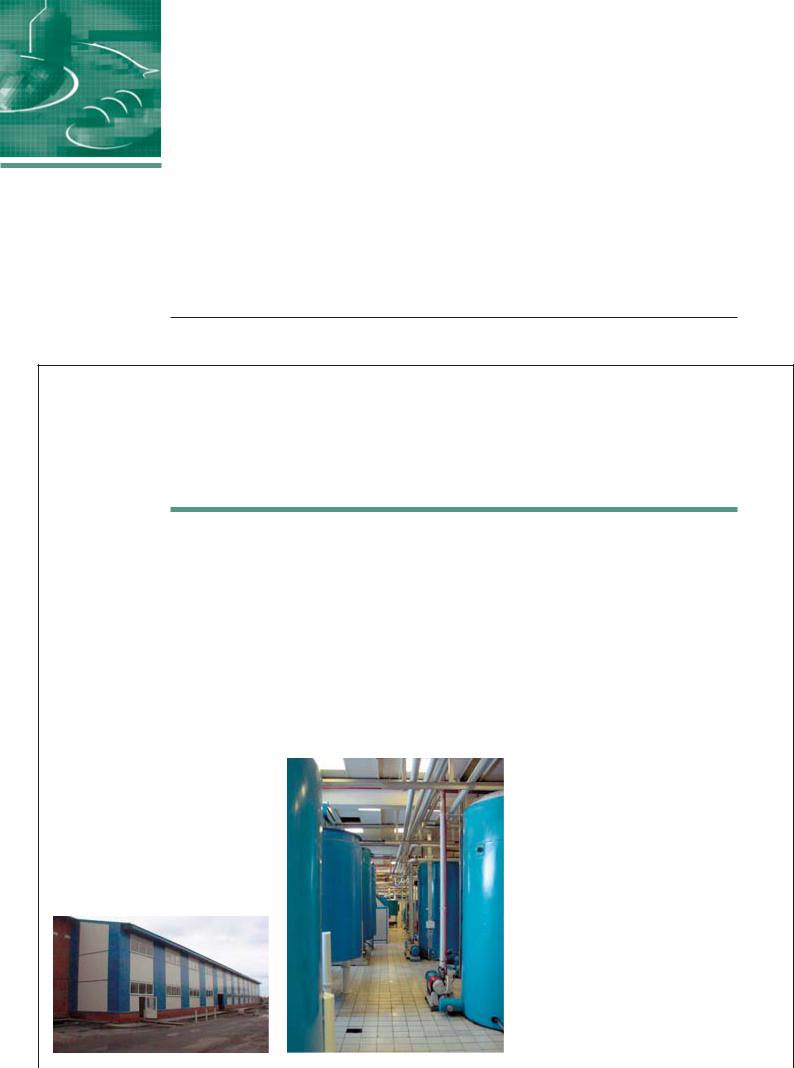
СИСТЕМНАЯ ИНТЕГРАЦИЯ ПИЩЕВАЯ ПРОМЫШЛЕННОСТЬ
Автоматизированная система управления технологическим процессом производства шоколадной глазури
Александр Лифанов
В статье рассказывается о модернизации АСУ ТП производства шоколадной глазури на Касимовской кондитерской фабрике с применением современных аппаратно# программных средств. В результате проведённой модернизации удалось стабилизировать вкусовые показатели и повысить качество выпускаемой продукции, увеличить производительность линии и её надёжность, автоматизировать ряд опасных
ирутинных операций, создать условия для дальнейшего наращивания
исовершенствования системы управления.
|
|
ВВЕДЕНИЕ |
|
кого уровня стабильности вкусовых по |
● 14 технологических установок с со |
||
|
|
С переходом к рыночной экономике |
|
казателей шоколадной глазури, произ |
ответствующими приводами, клапа |
||
|
|
российские производители все больше |
|
водимой на кондитерской фабрике. |
нами и трубопроводами; |
||
|
|
внимания уделяют не только объёмам |
|
|
● комплекс контрольно измеритель |
||
|
|
производства и ассортименту выпуска |
|
ОБЩАЯ ХАРАКТЕРИСТИКА |
ной аппаратуры (аналоговые датчи |
||
|
|
емых изделий, но и повышению каче |
|
ОБЪЕКТА И СИСТЕМЫ |
ки уровня, веса, тока, температуры, |
||
|
|
ства готовой продукции. Именно каче |
|
УПРАВЛЕНИЯ |
расхода, цифровые датчики протока, |
||
|
|
ство начинает играть главенствующую |
|
Линия производства шоколадной |
положения и др.); |
|
|
|
|
роль в продвижении продукции как на |
|
глазури была изготовлена в Голландии |
● управляющую часть, в которую вхо |
||
|
|
внутреннем, так и на внешнем рынках. |
|
и смонтирована на Касимовской кон |
дят |
исполнительные |
устройства, |
|
|
В этих условиях к системам автомати |
|
дитерской фабрике в 1994 году. С тех |
преобразователи, устройства плавно |
||
|
|
зации начинают предъявляться новые, |
|
пор линия производит 200 тонн шоко |
го |
пуска, модули распределённого |
|
|
|
более высокие требования. Выполнен |
|
ладных масс ежемесячно. |
сбора информации, контроллеры и |
||
|
|
ный компанией «Инфорум Пром» на |
|
Линия включает в себя (рис. 1): |
система визуализации. |
|
|
|
|
Касимовской кондитерской фабрике |
|
|
Технологический процесс производ |
||
|
|
|
|
||||
|
|
(ККФ) проект по модернизации систе |
|
|
ства глазури состоит из четырех основ |
||
|
|
мы управления линией производства |
|
|
ных этапов. Первый этап включает в се |
||
|
|
шоколадных глазурей преследовал цели |
|
|
бя операции дозирования различных |
||
|
|
увеличения точности измерения и ре |
|
|
(до 8 на каждую партию) ингредиентов |
||
|
|
гулирования технологических парамет |
|
|
и их перемешивания. Дозирование про |
||
|
|
ров, а также повышения надёжности |
|
|
изводится на весовой станции Wie |
||
|
|
функционирования технологического |
|
|
coMix, конструктивно состоящей из |
||
|
|
оборудования. Конечным результатом |
|
|
двух баков, вмещающих до 200 кг сырья |
||
|
|
модернизации стало обеспечение высо |
|
|
каждый. Верхний бак установлен на |
||
|
|
|
|
|
тензодатчиках и предназначен для взве |
||
|
|
|
|
|
|||
|
|
|
|
|
шивания одной дозы. Нижний бак яв |
||
|
|
|
|
|
ляется буферным и служит для ускоре |
||
|
|
|
|
|
ния процесса дозирования. Следующий |
||
|
|
|
|
|
бак (Н9) ёмкостью, соответствующей |
||
|
|
|
|
|
3000 кг продуктов, выполняет функции |
||
|
|
Производственный корпус |
|
|
накопительного бака и |
используется |
|
|
|
|
Цех измельчения |
для сбора всей партии ингредиентов пе |
|||
26 |
|
Касимовской кондитерской фабрики |
|
||||
|
|
ред дальнейшей обработкой. |
|||||
|
|
|
|
||||
|
|
|
|
|
|
|
|
|
|
www.cta.ru |
|
|
|
|
СТА 2/2003 |
© 2003, CTA Тел.: (095) 234 0635 Факс: (095) 232 1653 http://www.cta.ru

|
|
|
|
С И С Т Е М Н А Я И Н Т Е Г Р А Ц И Я /П И Щ Е В А Я П Р О М Ы Ш Л Е Н Н О С Т Ь |
|||||
|
|
|
|
Насос |
|
маслоКакао |
Нелауриновый жир |
Лауриновый жир Лецитин |
Стабилизаторы |
|
|
|
|
Насос с частотной регулировкой |
|||||
Лауриновый |
|
Какао |
Сухое |
Тейстчейнджер |
|
||||
Сахар |
Привод мешалки |
|
|
|
|
|
|||
жир |
порошок |
молоко |
|
|
|
|
|
||
Нелауриновый |
|
|
|
|
|
|
|
||
|
|
|
Клапан проходной с пневмоприводом |
|
|
|
|
||
жир |
F6 |
G6 |
H6 |
|
|
|
|
||
|
|
|
|
|
|
||||
Какао масло |
|
|
|
Клапан трехходовой с пневмоприводом |
|
|
|
|
|
Какао тертое |
|
|
|
Клапан с ручным приводом |
|
|
M8 |
|
|
WiecoMix |
|
|
|
Весовые датчики |
|
|
|
|
|
|
|
|
|
|
|
|
|
||
200 |
|
|
|
|
|
|
|
|
|
G8 |
|
|
|
|
|
|
|
|
|
WiecoМix |
|
RC 3000 |
|
W 155 |
Cao |
|
|
|
|
|
|
2000 |
|
|
|
|
|||
G9 |
H9 |
I9 |
J9 |
K9 |
K10 |
L9 |
|
M9 |
N9 |
|
|
||||||||
|
|
|
|||||||
|
|
|
Фильтрующий |
Пробоотборник |
|
|
|
|
На разливку |
|
|
|
элемент |
|
|
|
|
|
|
Условные обозначения: |
датчика уровня в промежуточном бач |
меной периферии, кабелей связи, сис |
|
||
F6 — бункер сахара песка; |
ке (для второй мельницы). Поскольку |
темы визуализации (рис. 2 б). |
|
||
G6 — бункер какао порошка; |
|
||||
помол связан с сильным нагревом, на |
|
|
|
|
|
H6 — бункер сухого молока; |
|
|
|
|
|
этом этапе тоже осуществляется кон |
МОДЕРНИЗАЦИЯ СИСТЕМЫ |
|
|||
G8 — основная весовая станция (до 200 кг); |
|
||||
троль температуры продукта в процес |
УПРАВЛЕНИЯ |
|
|
|
|
G9 — буферный бак (до 200 кг); |
|
|
|
||
H9 — накопительный бак (до 3000 кг); |
се обработки. |
Новый вариант АСУ ТП построен на |
|
||
I9 —рефайнер конш; |
Четвертый этап обработки подразу |
основе системы управления процесса |
|
||
J9 — накопительный бак (до 3000 кг); |
|
||||
мевает внесение различных добавок и |
ми SIMATIC PCS7 Compact фирмы |
|
|||
K9 — шариковая мельница WieneRoto W 155; |
|
||||
ароматизаторов, а также возможное |
Siemens, ядром которой является про |
|
|||
K10 — шариковая мельница Caotech Cao 2000; |
|
||||
конширование. Для дозирования доба |
мышленный компьютер SIMATIC RI |
|
|||
L9 — накопительный бак (до 3000 кг); |
|
||||
M8 — весовая станция добавок (до 200 кг); |
вок используется весовой бачок, под |
45 со встроенным модулем централь |
|
||
M9 — конширующий бак (до 5000 кг); |
вешенный на трех тензодатчиках фир |
ного процессора CPU 416 2DP в ис |
|
||
N9 — бак хранения (до 8000 кг). |
|
||||
мы Scaime. |
полнении SlotPLC. Связь процессор |
|
|||
|
|
||||
Рис. 1. Технологическая схема линии № 2 |
Система управления описанным тех |
ного модуля с компьютером реализова |
|
||
Касимовской кондитерской фабрики |
нологическим процессом изначально |
на по шине ISA, а с внешними устрой |
|
||
|
была построена на основе контроллера |
ствами — через коммуникационный |
|
||
Во время второго этапа обработки |
S5 115U фирмы Siemens (рис. 2 а), а |
контроллер |
по |
интерфейсу |
|
производится предварительное из |
для визуализации использовался пакет |
PROFIBUS DP. |
|
|
|
мельчение частиц ингредиентов круп |
Citect v.5.0. Связь контроллера и ком |
Промышленный компьютер с моду |
|
||
нее 75 мкм на рефайнер конше (маши |
пьютера была организована по прото |
лем CPU 416 2DP фактически выпол |
|
||
на для одновременного выполнения |
колу AS511 (9600 бит/с) через конвер |
няет функции контроллера, инженер |
|
||
операций измельчения и конширова |
тор RS 485/RS 232. |
ной и операторской станций. Он уста |
|
||
ния — длительного перемешивания |
Основными недостатками первона |
новлен в помещении операторной и |
|
||
подогретого шоколада с целью удале |
чальной версии системы были следую |
через сетевую карту и Ethernet связан с |
|
||
ния нежелательной влаги и летучих ве |
щие: |
компьютером верхнего уровня, кото |
|
||
ществ). Спецификой данного этапа яв |
● низкая скорость передачи по кана |
рый используется и как рабочее место |
|
||
ляется контроль температуры устрой |
лам связи, которая вызывала боль |
начальника производства, и как web |
|
||
ства одновременно с поддержанием за |
шие задержки между выдачей коман |
сервер для организации подключения |
|
||
данного тока главного двигателя. Авто |
ды оператором и её отработкой (до |
удалённых пользователей, например из |
|
||
матизация операций заливки и слива |
десятков секунд); |
московского офиса компании. Повто |
|
||
продукта из рефайнер конша позволи |
● моральное старение аппаратуры, ус |
ряя изображение, высвечиваемое на |
|
||
ла освободить оператора от рутинных |
ложнявшее процесс её обслуживания |
экране операторской станции, ком |
|
||
действий. |
и устранения аварийных ситуаций; |
пьютер верхнего уровня служит только |
|
||
На третьем этапе обработки выпол |
● сравнительно длинный цикл опроса |
для наблюдения за ходом технологиче |
|
||
няется основное измельчение в танде |
модулей контроллером, что при уве |
ского процесса |
и |
управляющими |
|
ме шариковых мельниц. Этот процесс |
личении скорости подачи сырья |
функциями не обладает. |
|
||
является критичным для качества ито |
приводило к ошибкам в дозировании |
По интерфейсу PROFIBUS DP мо |
|
||
гового продукта. Основным фактором, |
продуктов; |
дуль CPU 416 2DP связан со станция |
|
||
влияющим на результаты помола, яв |
● наличие большого количества руч |
ми распределённого ввода вывода |
|
||
ляется скорость подачи исходных про |
ных настроек. |
ЕТ200М, установленными в шкафах |
|
||
дуктов в мельницы. Регулировка ско |
В 2000 году было принято решение о |
управления на территории производст |
|
||
рости подачи осуществляется про |
модернизации системы управления |
венного помещения (рис. 3), а также с |
|
||
граммными PID контроллерами на ос |
линией производства шоколадной гла |
модулями распределённой периферии |
|
||
нове показаний расходомера End |
зури с переводом её на современное |
других линий и участков. Помимо |
27 |
||
ress+Hauser (для первой мельницы) и |
оборудование серии SIMATIC S7 и за |
станций ЕТ200М внутри шкафов раз |
|||
|
|
|
|
|
|
СТА 2/2003 |
|
|
|
www.cta.ru |
|
© 2003, CTA Тел.: (095) 234 0635 Факс: (095) 232 1653 http://www.cta.ru

С И С Т Е М Н А Я И Н Т Е Г Р А Ц И Я /П И Щ Е В А Я П Р О М Ы Ш Л Е Н Н О С Т Ь
|
а) |
|
|
|
|
|
|
|
|
|
|
|
|
|
|
Рабочее место |
|
|
|
|
|
|
|
б) |
|
|
|
|
|
|
|
|
начальника производства |
||
|
|
|
Операторская станция |
|
Операторская станция |
|
|
|
|
Web сервер |
|||||||
|
|
|
|
|
|
|
|
|
|
|
|
|
Сетевая карта |
OPC |
|
||
|
|
|
|
|
|
|
|
|
|
|
|
|
|
|
|||
|
|
|
|
|
|
|
|
|
|
|
|
PCI |
|
|
Ethernеt |
|
|
|
|
|
|
|
|
|
|
|
|
|
|
|
|
|
|
|
|
|
|
|
|
|
|
|
|
|
|
|
|
|
CPU 416 2DP |
|
|
||
|
|
|
|
|
|
|
|
|
|
|
|
|
SlotPLC |
|
HTTP |
||
|
|
|
|
|
|
|
|
|
|
|
|
ISA |
|
|
|
||
|
|
|
|
|
|
|
|
|
|
|
|
|
|
|
|
||
|
AS511 (9600 бит/с) |
|
|
|
|
|
|
|
|
|
|
|
|
|
|
||
|
|
|
|
Основная корзина контроллера S5 115U |
|
SIMATIC PCS7 Compact |
|
|
|
Удаленные |
|||||||
|
|
|
|
|
|
|
|
пользователи |
|||||||||
|
|
|
|
|
|
|
|
|
|
|
|
|
|
|
|
||
|
БП |
ЦПУ |
AI 16 |
AO 8 |
DI 32 DI 32 |
DI 32 |
PROFIBUS DP (12 Мбит/с) |
|
|
|
|
|
|||||
|
PS 951 |
S5 943 |
|
|
|
IM 306 |
|
|
|
|
|
||||||
|
|
|
|
|
|
|
|
|
|
|
|
|
|
|
|||
|
|
|
|
|
ET200M |
USiwarex |
|
|
|
|
|
|
|
|
|
||
|
|
|
|
|
|
|
AI 8 |
AI 8 |
DI 16 |
DI 16 |
AI 8 |
AI 8 |
|
|
|
||
|
|
|
|
|
Частотные |
|
|
|
|
|
|
|
|
|
|
|
|
|
|
|
|
|
преобразователи |
|
|
|
|
|
|
|
|
|
|
|
|
|
|
|
Датчики температуры |
|
|
|
|
|
|
|
|
Датчики температуры |
|
||||
|
|
|
Датчики уровня |
|
|
Тензодатчики |
|
|
|
|
|||||||
|
|
|
|
|
|
|
|
Датчики уровня |
|
||||||||
|
|
|
Расходомеры |
|
Корзина |
|
|
|
|
|
|
|
Расходомеры |
|
|||
|
|
|
|
|
|
|
|
|
|
|
|
|
|
||||
|
|
|
|
|
|
расширения |
ET200M |
DI 16 |
DI 16 |
DI 16 |
DI 16 |
DI 16 |
DI 16 |
AO 4 |
AO 4 |
|
|
|
|
|
|
|
|
IM 306 |
|
|
|||||||||
|
|
|
|
|
|
|
|
|
|
||||||||
|
DI 32 |
DI 32 |
DO 32 DO 32 |
DO 32 |
|
|
|
|
|
|
|
|
|
|
|
|
|
|
|
|
|
|
|
|
|
|
|
Концевые выключатели |
Частотные преобразователи |
||||||
|
|
|
|
|
|
|
|
|
|
|
|
|
|||||
|
|
|
|
|
Пускатели |
|
|
|
|
Датчики предельного уровня |
|
|
|||||
|
|
|
|
|
Частотные преобразователи |
|
|
|
Блок контакты автоматов защиты и пускателей |
|
|||||||
|
Концевые выключатели |
|
Пневмораспределители |
|
DI 16 |
DI 16 |
DO 16 DO 16 DO 16 DO 16 DO 16 DO 16 |
|
|
||||||||
|
Датчики предельного уровня |
|
ET200M |
|
|
||||||||||||
|
|
|
|
|
|
|
|
|
|
|
|
||||||
|
Блок контакты автоматов защиты и пускателей |
|
|
|
|
|
|
|
|
|
|
|
|||||
|
|
|
|
|
|
|
|
|
|
|
|
|
|||||
|
Условные обозначения: AI 16/8 — модуль аналогового ввода 16/8 ка |
|
|
|
|
|
|
|
|
|
|
|
|||||
|
нальный; AO 8/4 — модуль аналогового вывода 8/4 канальный; |
|
|
|
|
|
|
|
|
|
|
|
|||||
|
DI 32/16 — модуль дискретного ввода 32/16 канальный; DO 32/16 — |
|
|
|
Пускатели |
|
|
|
|
|
|||||||
|
модуль дискретного вывода 32/16 канальный; БП — блок питания; |
|
|
|
Частотные преобразователи |
|
|
||||||||||
|
ЦПУ — модуль центрального процессора; IM 306 — интерфейсный модуль. |
|
|
|
Пневмораспределители |
|
|
||||||||||
|
|
|
|
|
|
|
К модулям распределённой периферии |
|
|
|
|
||||||
|
Рис. 2. Конфигурация аппаратных средств системы управления: |
других линий и участков |
|
|
|
|
|
|
|||||||||
|
|
|
|
|
|
|
|
|
|
|
|
||||||
|
а) до модернизации; б) после модернизации |
|
|
|
|
|
|
|
|
|
|
|
|
||||
|
|
|
|
|
|
|
|
|
|
|
вам. Коммутационные возможности |
||||||
|
мещены интерфейсные реле, устройст |
выводами к модулям ввода вывода, а |
|
системы после модернизации отраже |
|||||||||||||
|
ва защитного отключения (УЗО), час |
силовыми — к клеммам, расположен |
|
ны в табл. 1. |
|
|
|
||||||||||
|
тотные |
преобразователи, |
устройства |
ным внизу шкафов. А уже с клемм вы |
|
Рабочее место оператора АСУ ТП |
|||||||||||
|
плавного пуска и другое оборудование |
полнена разводка непосредственно по |
|
(рис. 5) сформировано на базе промы |
|||||||||||||
|
(рис. 4), подключённое сигнальными |
датчикам и исполнительным устройст |
|
шленного |
компьютера Pentium II/ |
||||||||||||
|
|
|
|
|
|
|
|
|
|
|
333 MГц, функционирующего под уп |
||||||
|
|
|
|
|
|
|
|
|
|
|
равлением |
операционной |
системы |
||||
|
|
|
|
|
|
|
|
|
|
|
Microsoft Windows NT Workstation 4.0 с |
||||||
|
|
|
|
|
|
|
|
|
|
|
установленной системой визуализации |
||||||
|
|
|
|
|
|
|
|
|
|
|
Windows Control Center (версия 4.02). |
||||||
|
|
|
|
|
|
|
|
|
|
|
Отображение информации осуществ |
||||||
|
|
|
|
|
|
|
|
|
|
|
ляется на четырех мониторах с диаго |
||||||
|
|
|
|
|
|
|
|
|
|
|
налью 21 дюйм. |
|
|
||||
|
|
|
|
|
|
|
|
|
|
|
Система |
визуализации |
реализует |
||||
|
|
|
|
|
|
|
|
|
|
|
следующие функции: |
|
|||||
|
|
|
|
|
|
|
|
|
|
|
Таблица 1. Коммутационные возможности |
||||||
|
|
|
|
|
|
|
|
|
|
|
системы управления |
|
|
||||
|
|
|
|
|
|
|
|
|
|
|
Тип входа или выхода |
Количество |
|
||||
|
|
|
|
|
|
|
|
|
|
|
Цифровой вход |
|
160 |
|
|||
|
|
|
|
|
|
|
|
|
|
|
Цифровой выход |
|
96 |
|
|||
|
|
|
|
|
|
|
|
|
|
|
Аналоговый вход |
|
32+2 (для тензодатчиков) |
||||
28 |
Рис. 3. Сигнальная секция шкафа |
|
|
|
|
|
Аналоговый выход |
|
8 |
|
|||||||
управления |
|
|
|
Рис. 4. Силовая секция шкафа управления |
|
|
|
|
|||||||||
|
|
|
|
|
|
|
|
|
|
|
|
||||||
|
www.cta.ru |
|
|
|
|
|
|
|
|
|
|
|
|
|
|
СТА 2/2003 |
© 2003, CTA Тел.: (095) 234 0635 Факс: (095) 232 1653 http://www.cta.ru

С И С Т Е М Н А Я И Н Т Е Г Р А Ц И Я /П И Щ Е В А Я П Р О М Ы Ш Л Е Н Н О С Т Ь
● отображение технологических про |
оболочкой (управление доступом, жур |
тия. Кроме того, перемещение модуля |
|||
цессов, происходящих на производ |
налы тревог, перемещение по иерархии |
центрального процессора (наиболее |
|||
ственной линии (основная мнемо |
мнемосхем и т.п.). В средней части эк |
критичного узла системы) из произ |
|||
схема и мнемосхемы отдельных сек |
рана высвечивается мнемосхема вы |
водственного помещения в оператор |
|||
ций); |
|
бранной линии. Мнемосхемы выбира |
ную сделало более благоприятными ус |
||
● ручное |
управление устройствами |
ются независимо для каждого монито |
ловия для его эксплуатации, а исполь |
||
(переключение режимов управления |
ра. Серым цветом отображаются неак |
зование внутренней шины компьютера |
|||
«ручной/автомат» можно произво |
тивные устройства, зеленым – работа |
для связи с контроллером вместо |
|||
дить как посекционно, так и для от |
ющие, красным – аварийные. Уровни |
внешней шины позволило увеличить |
|||
дельного устройства); |
наполнения баков помимо цифровых |
поток данных для визуализации. |
|||
● управление циклами автоматических |
значений отображаются графически. С |
Модернизация системы управления |
|||
режимов; |
основной мнемосхемы линии можно |
от постановки задачи до получения от |
|||
● архивирование переменных (тренды |
переключиться на секционные мнемо |
ладочной версии заняла всего 5 недель. |
|||
сгруппированы посекционно); |
схемы, в окна уставок, трендов, рецеп |
|
|||
● индикация аварийных и информа |
тур, управления циклами. |
|
МОДЕРНИЗАЦИЯ |
||
ционных сообщений; |
В результате модернизации оборудо |
ТЕХНОЛОГИЧЕСКОГО |
|||
● разделение уровней доступа пользо |
вание системы управления было заме |
ПРОЦЕССА |
|||
вателей; |
|
нено более производительными и на |
Основной процесс приготовления |
||
● автоматическое формирование и пе |
дёжными |
устройствами |
серии |
шоколадных масс — измельчение — |
|
чать отчетов. |
SIMATIC S7. Это существенно расши |
выполняется на рефайнер коншах |
|||
Изображение на каждом мониторе |
рило как коммутационные, так и функ |
(рис. 7) и шариковых мельницах |
|||
рабочего места оператора разделено на |
циональные |
возможности |
системы, |
(рис. 8). |
|
три части (рис. 6). В верхней части на |
вследствие чего к ней через |
Шариковая мельница представляет |
|||
ходятся кнопки перехода между раз |
PROFIBUS DP и модули распределён |
собой цилиндр, заполненный шарика |
|||
личными |
линиями производства, а |
ной периферии были дополнительно |
ми. Через этот цилиндр снизу вверх |
||
также строка для информационных и |
подключены датчики и исполнитель |
прокачивается продукт. Насос, подаю |
|||
аварийных сообщений. В нижней час |
ные устройства ещё трёх линий и двух |
щий продукт, оборудован частотным |
|||
ти расположены кнопки управления |
вспомогательных участков |
предприя |
преобразователем. Воздействие соуда |
|
|
|
Рис. 5. Рабочее место оператора |
|
Рис. 7. Рефайнер&конш |
|
|
|
|
|
|
Рис. 6. Основная мнемосхема линии |
Рис. 8. Шариковая мельница |
29 |
|
|
|
|
|
СТА 2/2003 |
|
www.cta.ru |
© 2003, CTA Тел.: (095) 234 0635 Факс: (095) 232 1653 http://www.cta.ru
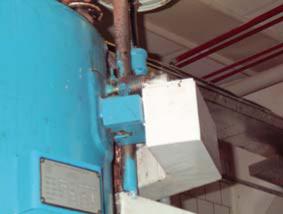
И Н Т Е Г Р А Ц И Я /П И Щ Е В А Я П Р О М Ы Ш Л Е Н Н О С Т Ь
|
|
ряющихся шариков приводит к из |
Таблица 2. Результаты тестового дозирования на модернизированной весовой станции WiecoMix |
|||||||||||||
|
|
мельчению частиц молока и сахара. |
|
|
|
|
|
|
|
|
|
|
|
|
|
|
|
|
|
|
|
Жир |
Какао |
|
Сухое молоко |
|
Сахар |
|
|||||
|
|
Основной задачей этого устройства яв |
|
|
|
|
|
|
||||||||
|
|
|
|
|
|
|
|
|
|
|
|
|
|
|
|
|
|
|
Номинальный вес дозы |
|
46,5 кг |
7,6 кг |
|
22,7 кг |
|
73,2 кг |
|
||||||
|
|
ляется получение на выходе продукта с |
|
|
|
|
||||||||||
|
|
|
|
|
|
|
|
|
|
|
|
|
|
|
|
|
|
|
определённой дисперсностью. |
Ошибка на 1 дозу |
абс. |
± 300 г |
± 170 г |
|
± 300 г |
|
± 580 г |
|
|||||
|
|
При прежней системе управления |
отн. |
±0,65% |
|
±2,3% |
|
±1,3% |
|
±0,8% |
|
|||||
|
|
|
|
|
|
|
|
|||||||||
|
|
стабильный помол получить не удава |
|
|
|
|
|
|
|
|
|
|
|
|
|
|
|
|
Ошибка на партию |
абс. |
± 660 г |
± 40 г |
|
± 10 г |
|
± 240 г |
|
||||||
|
|
лось. В результате длительных экспе |
|
|
|
|||||||||||
|
|
|
|
|
|
|
|
|
|
|
|
|
|
|||
|
|
(20 доз) |
|
отн. |
±0,07% |
|
±0,02% |
|
±0,002% |
|
±0,016% |
|
||||
|
|
риментов были отвергнуты идеи по |
|
|
|
|
|
|||||||||
|
|
|
|
|
|
|
|
|||||||||
|
|
|
|
|
|
|
|
|
|
|
|
|
|
|
|
|
|
|
стабилизации таких параметров, как |
Для этого на подающей трубе был ус |
на два тензодатчика Tedea Huntleigh |
||||||||||||
|
|
давление в подающей трубе, ток двига |
тановлен массовый расходомер Pro |
(серия 1260, тип — «балка изгиба»), |
||||||||||||
|
|
теля мельницы, усреднённый расход. |
mass 63I, основанный на принципе из |
выполненных из алюминия. Сигнал с |
||||||||||||
|
|
Единственно приемлемой оказалась |
мерения кориолисовых сил. Его пока |
них |
преобразовывался |
выносным |
||||||||||
|
|
идея стабилизации мгновенного рас |
зания были использованы в качестве |
нормирующим устройством в токовый |
||||||||||||
|
|
хода. |
сигнала обратной связи контура PID |
сигнал 4…20 мА, а затем обрабатывал |
||||||||||||
|
|
|
|
контроля |
скорости подачи. |
ся контроллером. К сожалению, сово |
||||||||||
|
|
|
|
|||||||||||||
|
|
|
|
В результате получены срав |
купность таких факторов, как неудач |
|||||||||||
|
|
|
|
нительно |
стабильные и |
но выбранные датчики, погрешности |
||||||||||
|
|
|
|
предсказуемые |
дисперсные |
преобразования и обработки сигна |
||||||||||
|
|
|
|
характеристики |
выходного |
лов, относительно длинный цикл оп |
||||||||||
|
|
|
|
продукта. |
|
|
|
|
роса контроллером, привела к недопу |
|||||||
|
|
|
|
Другим |
«узким |
местом» |
стимым для технологии ошибкам до |
|||||||||
|
|
|
|
технологического |
процесса |
зирования ±(1…1,5) кг на 50 кг про |
||||||||||
|
|
|
|
до модернизации была рабо |
дукта. |
|
|
|
|
|
|
|
||||
|
|
|
|
та основной весовой стан |
После модернизации обработка сиг |
|||||||||||
|
|
|
|
ции, которая не обеспечива |
налов |
тензодатчиков |
производится |
|||||||||
|
|
|
|
ла требуемую точность дози |
специально предназначенным для это |
|||||||||||
|
|
|
|
рования ингредиентов. |
го устройством Siwarex U (погрешность |
|||||||||||
|
|
|
|
Изначально бак основной |
не более 0,05%). Кроме того, была из |
|||||||||||
|
|
Рис. 9. Расположение тензодатчика весовой станции |
весовой станции |
опирался |
менена схема крепления бака: он был |
|||||||||||
|
|
|
|
|
|
|
|
|
подвешен на |
трех |
тензодатчиках |
|||||
|
|
|
|
|
|
|
|
|
||||||||
|
|
|
|
|
|
|
|
|
Hoettinger (серия Z6, тип – «балка из |
|||||||
|
|
|
|
|
|
|
|
|
гиба»), выполненных из стали. |
|||||||
|
|
|
|
|
|
|
|
|
Подобные проблемы не возникали |
|||||||
|
|
|
|
|
|
|
|
|
на весовой станции внесения добавок, |
|||||||
|
|
|
|
|
|
|
|
|
где изначально были установлены три |
|||||||
|
|
|
|
|
|
|
|
|
тензодатчика |
Scaime |
модели F60X |
|||||
|
|
|
|
|
|
|
|
|
(рис. 9). Каждый из этих датчиков име |
|||||||
|
|
|
|
|
|
|
|
|
ет диапазон измерения до 100 кг, харак |
|||||||
|
|
|
|
|
|
|
|
|
теризуется значением комбинирован |
|||||||
|
|
|
|
|
|
|
|
|
ной погрешности не более 0,033% и |
|||||||
|
|
|
|
|
|
|
|
|
выполнен из нержавеющей стали. За |
|||||||
|
|
|
|
|
|
|
|
|
всё время эксплуатации тензодатчики |
|||||||
|
|
|
|
|
|
|
|
|
F60X показали себя достаточно ста |
|||||||
|
|
|
|
|
|
|
|
|
бильными и точными, поэтому в ходе |
|||||||
|
|
|
|
|
|
|
|
|
модернизации обработка формируе |
|||||||
|
|
|
|
|
|
|
|
|
мых ими сигналов тоже была передана |
|||||||
|
|
|
|
|
|
|
|
|
устройству Siwarex U, но сами датчики |
|||||||
|
|
|
|
|
|
|
|
|
при этом не заменялись. |
|
|
|||||
|
|
|
|
|
|
|
|
|
Проведённые мероприятия позволи |
|||||||
|
|
|
|
|
|
|
|
|
ли достичь точности дозирования, ука |
|||||||
|
|
|
|
|
|
|
|
|
занной в табл. 2. При этом формирова |
|||||||
|
|
|
|
|
|
|
|
|
ние одной дозы длится 7 минут с уче |
|||||||
|
|
|
|
|
|
|
|
|
том вымешивания и сброса, то есть од |
|||||||
|
|
|
|
|
|
|
|
|
на партия (20 доз) обрабатывается |
|||||||
|
|
|
|
|
|
|
|
|
2,5 часа. |
|
|
|
|
|
||
|
|
|
|
|
|
|
|
|
Такие результаты были |
достигнуты |
||||||
|
|
|
|
|
|
|
|
|
во многом благодаря применению кор |
|||||||
|
|
|
|
|
|
|
|
|
ректировочных расчётов: после закры |
|||||||
|
|
|
|
|
|
|
|
|
тия клапана определяется вес реально |
|||||||
30 |
|
|
|
|
|
|
|
|
отдозированного продукта, и если этот |
|||||||
|
|
|
|
|
|
|
|
вес превышает заданный, то в следую |
||||||||
|
|
|
|
|
|
|
|
|||||||||
|
|
|
|
|
|
|
|
|
|
|
|
|
|
|
|
|
|
|
www.cta.ru |
|
|
|
|
|
|
|
|
|
|
|
|
СТА 2/2003 |
© 2003, CTA Тел.: (095) 234 0635 Факс: (095) 232 1653 http://www.cta.ru
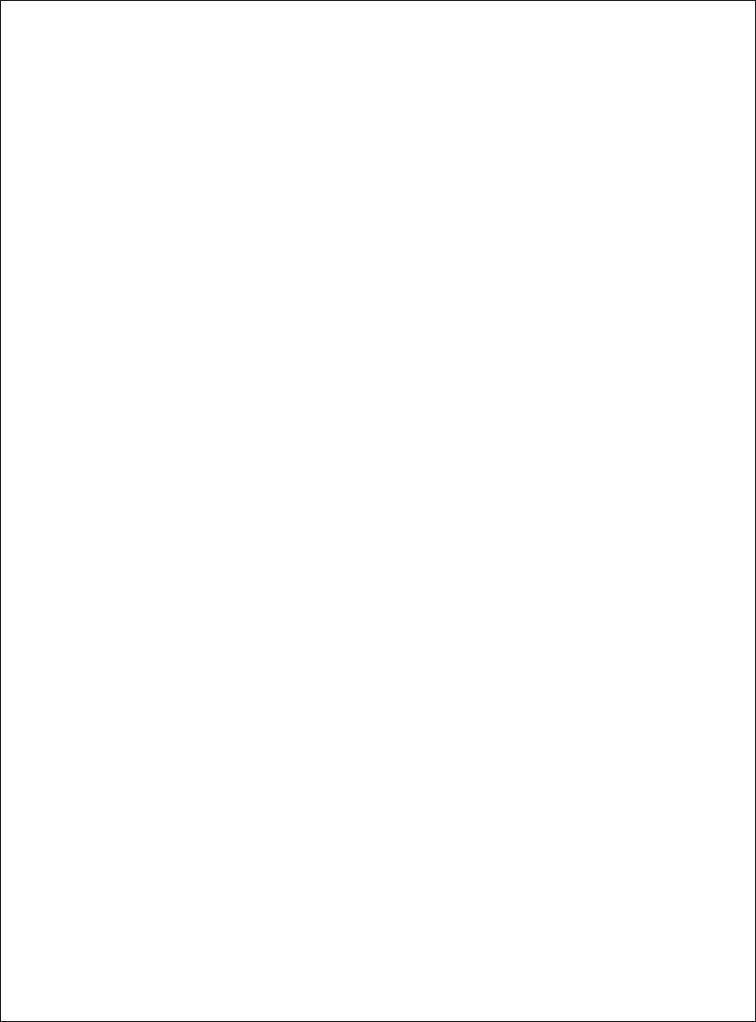
С И С Т Е М Н А Я И Н Т Е Г Р А Ц И Я /П И Щ Е В А Я П Р О М Ы Ш Л Е Н Н О С Т Ь
щий раз клапан будет закрыт на неко торое расчётное время раньше, что позволит приблизить вес новой дозы к заданному. При расчёте текущей по правки учитываются величины кор рекции предыдущих доз данной пар тии.
Помимо этого на достигнутые ре зультаты положительно повлияло ис пользование двухступенчатого дозиро вания продукта: когда до предельного веса дозы продукта остаётся менее 10 кг, при помощи частотного преобра зователя понижается скорость враще ния шнека или насоса, подающего продукт, что позволяет точнее отсечь дозу.
ЗАКЛЮЧЕНИЕ
Данный проект стал одним из пер вых промышленных применений сис темы SIMATIC PCS7 Compact, пред назначенной для управления как не прерывными технологическими про цессами, так и сложными сборочными производствами. Представленная сис тема базируется на устройствах серии S7, обеспечивает работу с периферией любых производителей, совместимой с интерфейсом PROFIBUS DP, и обла дает широкими возможностями к рас ширению.
Использованные аппаратные реше ния позволили добиться высокой точ ности измерений (до модернизации передозировки составляли десятки ки лограммов на партию) и чёткой работы оборудования. Реализация расширен ной диагностики неисправностей со кратила время поиска их причин в два три раза. Применение для программи рования контроллера языков высокого уровня дало возможность:
1)провести разработку всего описан ного программного комплекса в те чение 5 недель;
2)упростить все виды работ с про граммным обеспечением;
3)поручить обслуживание рядовым ин женерам службы КИП.
В целом модернизация системы ав томатизации позволила не только улучшить качество выпускаемой про дукции, но и достичь повышения про изводительности линии. При этом уда лось освободить работников линии от выполнения ряда рутинных и небезо пасных операций. ●
Автор – сотрудник ЗАО «Инфорум Пром»
Телефон: (095) 796 9072
СТА 2/2003
31
www.cta.ru
© 2003, CTA Тел.: (095) 234 0635 Факс: (095) 232 1653 http://www.cta.ru