
3479
.pdfобразуется зазор между стальной и резиновой верхними шайбами подвески. При изменении направления нагрузки образуется зазор между стальной нижней шайбой и гайкой, и проходит снятие нагрузки с гайки. Таким образом, на гайку действуют переменные силы, которые при наличии зазоров в резьбе вызывают ее износ. В результате резьбовое соединение может потерять несущую способность. Чтобы не допустить «раскрытие» амортизаторов, необходимо при сборке РМБ и монтаже создать предварительный натяг , определяемый действующей в эксплуатации максимальной нагрузкой Qmax.
2. Расчет траверсного подвешивания ТЭД
Для создания максимальной величины предварительного натяга усилие затяжки определяется из условия исключения деформации пружин от максимальной нагрузки Qmax. Максимальная нагрузка возникает, когда реакция на тяговый момент направлена вниз и действует совместно с весом двигателя. Для создания необходимой величины предварительного натяга усилие затяжки принимается равным:
Р3 = Qmax= Рд/2 + RТ . |
(5.1) |
Реакция на подвеске от действия тягового момента можно определить из уравнения равновесия моментов сил, действующих на двигатель в режиме тяги:
RТ = FТ·DK/2LД, |
(5.2) |
где LД = 1,2 м – расстояние от оси колесной пары до оси шарнира подвески двигателя. Расчетная сила тяги принимается максимальной из условия ограничения по
сцеплению. В момент трогания при скорости V = 0: - для электровозов постоянного тока
FТ = 0,34 Рсц., |
(5.3) |
- для электровозов переменного тока
FТ = 0,36 Рсц, |
(5.4) |
где Рсц – нагрузка от оси колесной пары на рельсы.
Для отечественных электровозов нагрузка на рельсы имеет величину в пределах Рсц = 210…250 кН. Сила затяжки РЗ зависит от жесткости пружин и определяется величиной затяжки ∆:
РЗ = Жэкв · ∆, |
(5.5) |
где Жэкв = 4Жпр – эквивалентная жесткость комплекта параллельно работающих пружин.
41
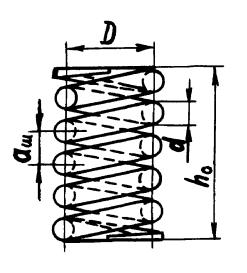
Рисунок 5.4 – Цилиндрическая винтовая пружина
Жесткость цилиндрической винтовой пружины (рисунок 5.4) определяется по
формуле |
|
Жпр = Р/∆ = G·d4/8D3n, |
(5.6) |
где G = 75÷85 ГПа (75÷85 кН/мм2) – модуль упругости при сдвиге; n = nо – 1,5 – число рабочих витков; nо – общее число витков; d – диаметр прутка, м; D – средний диаметр, м.
На полигоне железнодорожного транспорта СамГУПС с траверсным подвешиванием тягового электродвигателя представлен грузовой электровоз ВЛ-60 с двигателем НБ-412К массой 4,85 т.
3. Расчет маятникового подвешивания ТЭД
Резиновые шайбы выполняются высотой в свободном состоянии h0 = 0,06÷0,09 м, а размеры сечения шайб определяются из условий прочности. Допустимое напряжение резины составляет [σ] = (3÷5) МПа.
Осевая жесткость резиновой шайбы определяется по формуле, Н/м:
Ж ш |
SE |
, |
(5.7) |
||
|
|
||||
H H |
|||||
|
|
|
|||
где S – площадь нагружения, м2; |
|
|
|
|
|
Е – статический модуль упругости, Н/м2; |
|
|
|||
Н – высота резиновой шайбы, м; |
|
|
|
|
|
Н – деформация сжатия, м (при деформации до 20 % принимается |
Н = 0). |
||||
При динамической нагрузке модули упругости ЕД и GД выше, чем при статической: |
|||||
EД к Д Е ; |
GД кД G |
(5.8) |
|||
|
42 |
|
При производстве маятниковых подвесок применяют морозостойкие резины, физико-механические характеристики которых приведены в таблице 5.1.
Максимальная нагрузка Qmax определяется по формулам (5.1)–(5.4).
Сила затяжки РЗ зависит от жесткости амортизаторов и определяется величиной затяжки :
РЗ = Жэкв . |
(5.9) |
Чтобы вероятность раскрытия амортизаторов не превышала 3 %, необходимо устанавливать в один блок амортизаторы одинаковой жесткости и обеспечивать необходимый предварительный натяг.
Таблица 5.1 – Физико-механические характеристики морозостойких резин
Механические характеристики |
Значения показателей резины марки |
|||
|
|
|
||
7-1847 |
7-2959 |
7-2462 |
||
|
||||
|
|
|
|
|
Твердость по Шору А, ед. |
42,5 |
52,5 |
67,5 |
|
Модуль упругости, МПа |
1,7 |
2,3 |
5,7 |
|
Модуль упругости при сдвиге, МПа |
0,48 |
0,67 |
1,5 |
|
Коэффициент Пуассона |
0,492 |
0,487 |
0,482 |
|
Сопротивление разрыву, МПа |
18,0 |
18,0 |
7,5 |
|
Относительное удлинение при разрыве, % |
675 |
550 |
325 |
|
Температурный интервал работоспособности, С |
–50…+80 |
–50…+80 |
–50…+80 |
|
|
|
|
|
Известно, что наибольший срок службы резины имеет место при степени деформации не более 20÷25 %, а предельная степень сжатия свободной резины составляет 40÷45 %. На полигоне железнодорожного транспорта СамГУПС с маятниковым подвешиванием тягового электродвигателя представлен грузовой электровоз ВЛ-10 с двигателем ТЛ-2К массой 4,7 т.
Порядок выполнения работы
1.Траверсное подвешивание ТЭД
1.1.Изучить устройство и особенности работы траверсной подвески по содержанию методических указаний и на полигоне железнодорожного транспорта СамГУПС на примере грузового электровоза ВЛ-60.
1.2.Произвести контрольные замеры полной высоты траверсного пружинного блока и толщины составных элементов.
1.3.Выполнить расчет предварительного натяга металлических цилиндрических винтовых пружин траверсной подвески и сравнение с замерами.
2.Маятниковое подвешивание ТЭД
2.1. Изучить устройство и особенности работы маятниковой подвески по содержанию методических указаний и на полигоне железнодорожного транспорта СамГУПС на примере грузового электровоза ВЛ-10.
43
2.2.Произвести контрольные замеры полной высоты резинометаллического блока (РМБ) маятниковой подвески и толщины составных элементов.
2.3.Выполнить расчет предварительного натяга резиновых пружин и сравнение с
замерами.
Содержание отчета
В отчете указать следующее: номер и название лаб. работы; дату проведения; цель работы; приборы и инструменты; эскиз траверсной и маятниковой подвески ТЭД; результаты контрольных замеров; результаты расчета предварительного натяга металлических и резиновых пружин; сравнение с контрольными замерами; выводы по работе.
Контрольные вопросы
1.Что такое тяговый привод, его классификация?
2.Устройство тягового привода I класса.
3.Назовите виды зубчатых передач.
4.Устройство зубчатых колес.
5.Почему тяговая передача привода I класса называется «жесткой»?
6.Как подвешен редуктор в тяговом приводе I класса?
7.Поясните особенности устройства траверсной подвески ТЭД.
8.Поясните особенности устройства маятниковой подвески ТЭД.
9.Для чего производится начальный натяг пружин подвески ТЭД?
10.Чем определяется начальный натяг пружин подвески ТЭД?
11.Что повышает надежность и долговечность ТЭД и зубчатых передач?
12.Какие функции выполняет узел маятниковой подвески ТЭД?
Лабораторная работа № 6
МОТОРНО-ОСЕВЫЕ ПОДШИПНИКИ СКОЛЬЖЕНИЯ
Цель работы: изучить конструкцию и принцип действия моторно-осевого подшипника (МОП) скольжения с фитильной системой смазки.
Оборудование, приборы и инструменты: образец МОП скольжения с фитильной системой смазки, веерный набор щупов для измерения износа вкладышей МОП.
Основные положения
В тяговых приводах I класса, т. е. при опорно-осевом подвешивании, тяговый электродвигатель имеет три опорные точки. Он опирается на специальные опорные шейки средней части оси колесной пары двумя опорно-осевыми подшипниками. Третья
44

опора – это упругое подвешивание к раме тележки через пружинный комплект металлических или резиновых амортизаторов. Подшипники вала тягового двигателя и ось колесной пары размещаются в одном корпусе, что гарантирует неизменность межцентрового расстояния зубчатой передачи.
Моторно-осевые подшипники скольжения тяговых приводов I класса имеют следующие системы смазки: фитильную, польстерную, циркуляционную и с постоянным уровнем смазки, рисунок 6.1, а, б, в, г.
Первые МОП имели фитильную систему смазку шеек оси колесной пары (рисунок 6.1, а). В состав МОП скольжения входят два вкладыша из свинцовистой бронзы ОЦС 4-4-17. Один вкладыш 10 (верхний) вставляется в расточку корпуса тягового электродвигателя 8, второй 12 (нижний) в шапку (крышку) 3, прикрепленную к корпусу болтами 7. Для предотвращения проворачивания вкладышей предусмотрена шпонка 9, закрепленная в остове электродвигателя 8. Нижний вкладыш 12 имеет прямоугольное окно для подвода смазки к шейке оси.
в)
а)
г)
б)
Рисунок 6.1 – Схемы моторно-осевых подшипников скольжения, имеющие системы смазки: а – фитильную; б – польстерную; в – с постоянным уровнем смазки; г – циркуляционную
Смазка шеек осуществляется контактным способом с помощью набивки из полушерстяной пряжи. Масло заливается в масляную ванну в шапке 3 через верхнюю масленку в крышке. Набивка укладывается до заливки масла в определенной
45
последовательности. Сначала непосредственно на шейку вдоль стенки полости шапки укладывается войлочная прокладка 11, которая предохраняет набивку от истирания и затягивания в подшипник. Затем размещают заблаговременно пропитанные осевым маслом пять мотков полушерстяной пряжи 6: четыре – вдоль прокладки, а пятый сложенный вчетверо на дно масляной ванны, прижимая расправленные по дну концы первых четырех мотков. Набивка, прижатая пружинной планкой 5, равномерно распределяет масло по всему окну во вкладыше 12. Сверху набивки укладывают слой хлопчатобумажной путанки, пропитанной в масле 1.
Для смазки трущихся поверхностей используется осевое масло. Уровень смазки в подшипнике проверяется наклонным щупом через нижнюю масленку. Его высота должна быть 45÷90 мм.
Значительное число повреждений МОП происходит из-за неудовлетворительной подачи смазки в рабочую зону, что потребовало их усовершенствования. Появились моторно-осевые подшипники скольжения, имеющие польстерную, с постоянным уровнем системы смазки и циркуляционную (рисунок 6.1, б, в, г).
На электровозах удельные нагрузки на вкладыши МОП благодаря симметрии зубчатой передачи значительно ниже, чем у тепловозов, поэтому на них с успехом применяются МОП с постоянным уровнем смазки (рисунок 6.1, в). В шапках МОП с постоянным уровнем смазки имеются две камеры 18 и 19. Уровень смазки в камере 19, в которой находится шерстяная набивка, зависит от высоты ниппеля, соединяющего данную камеру ее с камерой 18, представляющей собой запасный резервуар объемом 4 л. Работает эта система следующим образом: как только уровень масла в камере 19 понизится настолько, что она не будет касаться ниппеля, воздух, находящийся в ней, начнет поступать в камеру 18. Разрежение в последней уменьшится и масло будет поступать через канал 20 в камеру 19 до тех пор, пока не закроет ниппель, в результате чего прекратится доступ воздуха в камеру 18. Пополнение смазки и поддержание ее постоянного уровня в камере 19 будут продолжаться до тех пор, пока она не израсходуется в запасной камере. Заправка смазки в МОП с постоянным уровнем осуществляется под давлением 0,35МПа через специальный шланг с наконечником, вставляемым в коническое отверстие 20. После заправки обеспечивается пробег электровоза не менее 1000 км.
На тепловозах |
с электродвигателями |
ЭД118Б |
примененяются МОП с |
циркуляционной системой смазки (рисунок 6.1, г). |
В одной общей шапке, привинченной |
к остову электродвигателя восемью болтами М36, размещены, кроме вкладышей, два польстера, по устройству аналогичные выше описанным, маслосборник 17 вместимостью 35 л и шестеренчатый насос, приводимый в действие от разъемного зубчатого колеса, установленного на колесной паре (в сечении не показаны). Производительность насоса 8 см3 за один оборот колесной пары. Смазка от него по специальным каналам подается в правую и левую верхние камеры 16, в них установлены польстеры, с помощью которых смазка через окна во вкладышах поступает
46

непосредственно в зону трения. Отработанная в подшипниках смазка, а также излишки ее в камере 16 по специальным каналам и через окно В сливаются непосредственно в маслосборник 17. Польстеры обеспечивают смазку МОП при трогании тепловоза с места и при малых скоростях движения, а также играют роль дублирующей системы смазки в случае выхода из строя шестеренчатого насоса.
При возможности применяют вкладыши с заливкой баббитом марки Б83. На рисунке 6.2 приведен чертеж комплекта вкладышей с баббитовой заливкой – З (баббит).
Рисунок 6.2 – Вкладыши с баббитовой заливкой
Известно, что в условиях обильного смазывания интенсивность износа вкладышей в 5 раз ниже, чем при фитильной, и в 2 раза ниже, чем при польстерной системах смазки.
Ремонт МОП состоит в основном в замене изношенных вкладышей. Максимальный износ вкладышей установлен техническими нормативами и составляет 2,5–3,5 мм в зависимости от вида локомотива. Для электровоза ВЛ-10 максимальный износ составляет 3,0 мм. Замеряется износ вкладышей МОП специальным веерным набором плоских щупов-калибров, через измерительные отверстия в корпусе ТЭД.
При текущем ремонте ТР-2, ТР-3 износ вкладышей не должен превышать установленных нормативами пределов, таблица 6.1.
47
Таблица 6.1– Предельный износ вкладышей МОП, мм
Материал |
ТР-2 |
ТР-3 |
|
|
|
Бронза |
0,6 1,8 |
0,6 1,5 |
|
|
|
Сталь с баббитом |
0,45 1,8 |
0,6 1,8 |
|
|
|
Внастоящее время в ремонтных локомотивных депо и на пунктах технического обслуживания локомотивов для заправки смазкой МОП применяются автоматизированные установки.
Врамках лабораторной работы дополнительно выполняется заправка смазкой образца МОП с циркуляционной системой смазки (рисунок 6.1,в) при помощи установки УКЗП – 03, разработанной в диссертационной работе доцента кафедры Булатова А.А.
Заправка производится в точном соответствии с Инструкцией по использованию маслозаправочной установки (см. Приложение В). Окончание заправки фиксируется визуально, как уровень масла закроет ниппель. При этом следует контролировать давление на манометрах установки: компрессора Рк ≤ 0,3 МПа (3 атм); пневмолинии Рпн = 0,2÷0,3 МПа (2÷3 атм); вакуумной камеры Рвк – в зеленой зоне.
Порядок выполнения работы
1.Изучить конструкции и особенности работы МОП по содержанию методических указаний и по экспонату в учебной лаборатории.
2.Произвести контрольные замеры величины износа вкладышей МОП электровоза ВЛ-10 на полигоне железнодорожного транспорта СамГУПС.
3.При заправке МОП смазкой произвести замеры давлений на указанных технологических манометрах.
Содержание отчета
В отчете указать следующее: номер и название лаб. работы; дату проведения; цель работы; приборы и инструменты; эскиз заданного МОП; результаты контрольных замеров; выводы по работе.
Контрольные вопросы
1.Что такое МОП, назначение, виды?
2.Устройство МОП с фитильной системой смазки.
4.Какова должна быть высота уровня смазки в МОП?
5.Что в основном заменяется в МОП при ремонте?
6.Назначение и устройство вкладышей МОП.
7.Как и чем измеряется износ вкладышей МОП?
8.Нормативные пределы износа вкладышей МОП.
9.Порядок заправки МОП смазкой.
48
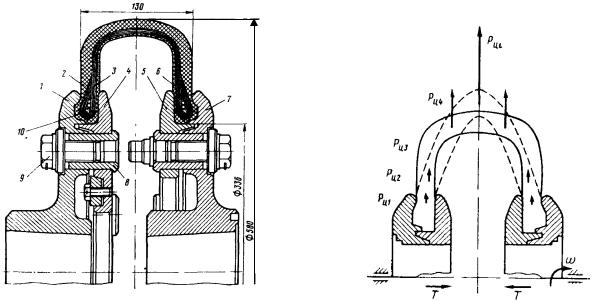
Лабораторная работа № 7
РЕЗИНОКОРДНАЯ МУФТА
Цель работы: изучить конструкцию, особенности работы и технологию ремонта резинокордной муфты.
Оборудование, приборы и инструменты: кронциркуль; линейка.
Основные положения
В настоящее время в тяговом приводе моторвагонных электропоездов ЭР2, ЭР22, ЭР9П, ЭД4М широко применяют эластичную муфту с торообразным резинокордным элементом (рисунок 7.1). Резинокордная муфта служит не только соединительным звеном между валом тягового двигателя и редуктором, но и является упругим элементом, компенсирующим разницу в перемещениях валов двигатели и редуктора, а также снижает динамические нагрузки в приводе, возникающие в моменты трогания и торможения. Она состоит из ведущего 1 и ведомого 7 фланцев, напрессованных на конические хвостовики валов якоря электродвигателя и осевого редуктора, разрезных колец 4 и 5, разгружающих от поперечных срезающих сил втулок 8, от поперечных срезывающих сил, болтов 9, с помощью которых к фланцам крепится неразрезной резинокордный упругий элемент, состоящий из каркаса 3, двух металлических колец 10, наружного 2 и внутреннего 6 защитных резиновых покрытий. При этом предусмотрено специальное центрирующее клиновое кольцо 11 с болтами 12.
Рисунок 7.1 – Резинокордная муфта Рисунок 7.2 – Схема, поясняющая возникновение осевых сил, действующих на фланцы муфты и вала
49
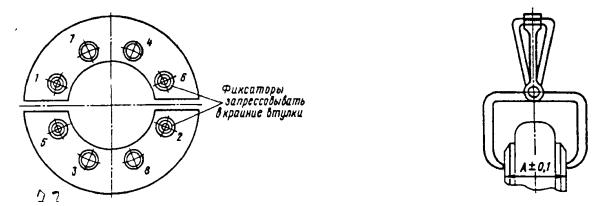
Каркас оболочки выполнен из перекрещивающихся под углом 45° десяти слоев пропитанного синтетической резиной капронового корда, края которого для обеспечения надежного его крепления в бортовых частях упругого элемента завернуты вокруг металлических колец. Кордный каркас защищен от механических повреждений слоем резины снаружи толщиной 9÷12 мм и внутри – 1,5÷2 мм. Резиновые покрытия (протекторы) способствуют также повышению устойчивости каркаса – основной несущей части резинокордного элемента при передаче вращающего момента. В муфте нет подвижных соединений с поверхностным трением, она не требует постоянного ухода и смазки. Резинокордная муфта упруго передает вращающий момент с вала двигателя на вал шестерни. Помимо скручивающего момента она испытывает растягивающие усилия от центробежной силы при ее вращении.
Недостатки муфты – высокая радиальная жесткость и значительные осевые силы Т, возникающие при высоких частотах вращения. Их появление объясняется тем, что под воздействием центробежных сил Рцi оболочка муфты (рисунок 7.2) деформируется таким образом, что его боковые поверхности принимают коническую форму (штриховые линии).
После ремонта тягового привода для сборки муфты устанавливают на фланец шестерни резинокордный элемент. Полукольца в сборе заводят в резинокордный элемент, пригодный по нормативам для эксплуатации (без трещин, расслоений и разрывов), а концы втулок – в отверстия фланца. В определенной последовательности, показанной цифрами на рисунке 7.3, производят затяжку болтов тарированным ключом с моментом 255÷274 Н·м. Заводят два полукольца со стороны тягового двигателя в резинокордный элемент и крайними втулками устанавливают на фиксаторы. Затем подкатывают колесную пару с редуктором под тележку и крепят серповидную или прямую подвеску к кронштейну рамы. Соединяют полумуфты редуктора и тягового электродвигателя. Подняв корпус редуктора до совпадения осей вала двигателя и вала шестерни, упругую оболочку сжимают и закрепляют болтами. Завершив сборку, проверяют кронциркулем (рисунок 7.4) размер А по фланцам муфты, который должен быть 158÷170 мм для электропоездов ЭР1, ЭР2 и ЭР9 и 169÷178 мм для электропоездов ЭР22.
|
|
|
|
Рисунок 7.3 – Схема установки фиксаторов |
Рисунок 7.4 – Кронциркуль для контроля |
||
и последовательность затяжки болтов |
размера А по фланцам упругой муфты |
||
эластичной муфты электропоезда ЭР2 |
|
||
|
|
|
50 |