
3479
.pdf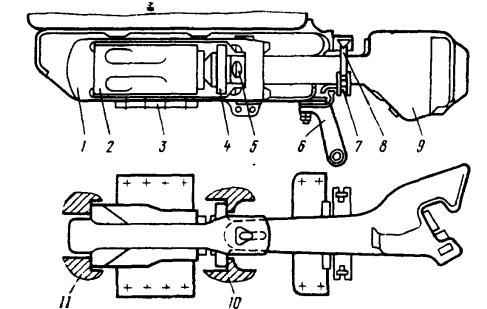
бруса шарниры, обеспечивающие взаимное перемещение сцепленных единиц, при котором корпуса автосцепок занимают наклонное положение.
Полужестким автосцепным устройством оборудуют пассажирские рефрижераторные, грузовые восьмиосные и некоторые другие вагоны. В таком автосцепном устройстве предусмотрен ограничитель вертикальных перемещений, который начинает действовать при смещении продольных осей сцепленных автосцепок в контуре зацепления по вертикали на расстояние около 100 мм.
Автосцепки нежесткого типа допускают относительное вертикальное перемещение сцепленных единиц, оставаясь при этом каждая в горизонтальном положении, но на разной высоте. На отечественном подвижном составе применяют нежесткие автосцепные устройства СА-3 и СА-Д, у которых допускаемая разность уровней осей автосцепок перед сцеплением 100 мм и 140 мм. Сцепление возможно, когда корпуса автосцепок смещены в горизонтальной плоскости один относительно другого не более, чем на 175 мм. Нежесткое автосцепное устройство состоит из автосцепки – корпус автосцепки с механизмом сцепления, привода для расцепления, центрирующего прибора с поглощающим аппаратом (рисунок 4.1).
Рисунок 4.1 – Автосцепное устройство: 1 – хомут; 2 – поглощающий аппарат; 3 – планка поддерживающая; 4 – плита упорная; 5 – клин; 6 – кронштейн; 7 – балка; 8 – подвеска; 9 – головка автосцепки; 10 – передний упор; 11 – задний упор
Корпус автосцепки (рисунок 4.2) представляет собой стальное пустотелое литье, в головной части которого помещен механизм автосцепки. Большой зуб 4 головной части корпуса и малый зуб 7 образуют вместе зев, из которого выступает рабочая часть замка 6 и замкодержателя 5. Контур зацепления имеет стандартные размеры, обеспечивающие взаимное сцепление автосцепок СА-З и СА-4. К головной части 3 корпуса примыкает пустотелый хвостовик 1 с отверстием 2 для клина, связывающего хвостовик с упряжным
31
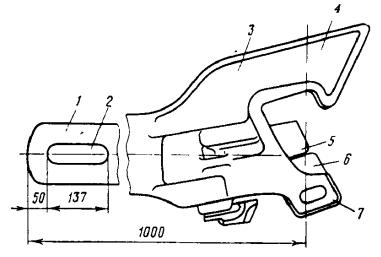
устройством. В головной части автосцепки в кармане размещен механизм сцепления, состоящий из замка с удерживающим от самопроизвольного расцепления замкодержателем, а также предохранителя, удерживающего замок от заглубления его внутрь кармана, и подъемник замка для расцепления автосцепки.
Рисунок 4.2 – Корпус автосцепки: 1 – подвеска; 2 – отверстие; 3 – головная часть; 4 – большой зуб; 5 – лапа замкодержателя; 6 – рабочая часть замка; 7– малый зуб
Во время сцепки локомотива с вагонами или другим локомотивом малый зуб одной автосцепки скользит по скошенной поверхности большого или малого зуба другой. Под действием нажатия или удара малые зубья входят в зевы автосцепок, замки при этом сначала вжимаются внутрь корпуса головок, а затем, как только малые зубья становятся на свои места, под действием собственного веса опускаются в нижнее положение, запирая автосцепки. Если автосцепки несколько смещены в стороны, они направляются для сцепки взаимно скошенными поверхностями зубьев.
Для возвращения автосцепки в центральное положение после боковых отклонений служит центрирующий прибор, состоящий из розетки 2 (рисунок 4.3) с прикрепленными к ней двумя маятниковыми подвесками 1 и опирающейся на них центрирующей балки 3. При боковом отклонении корпуса автосцепки, лежащего на этой балке, такое маятниковое подвешивание стремится вернуть корпус в среднее положение.
Чтобы расцепить автосцепку, достаточно повернуть рычаг расцепного привода, который, повернув подъемник, заставит его принудительно переместить замок внутрь кармана и оставаться там, пока не будут разведены автосцепки. В тех случаях, когда электровозом вагоны подталкиваются без их сцепки, нужно удерживать замок в расцепленном положении у одной из смежных автосцепок. Для этого рукоятку расцепного рычага поворачивают (как и при расцеплении), но не отпускают, а кладут рычаг плоской частью на горизонтальную полочку кронштейна, находящегося около рукоятки рычага. В этом положении расцепного рычага валик подъемника повернут до отказа и удерживается натяжением цепи.
32
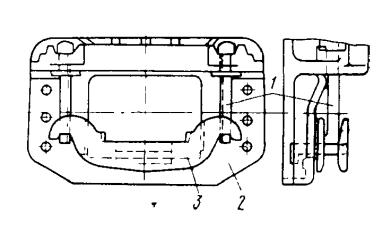
Рисунок 4.3 – Центрирующий прибор: 1 – подвеска; 2 – розетка; 3 – центрирующая балка
Продольные растягивающие и сжимающие усилия от корпуса автосцепки поглощающему аппарату передаются с помощью упряжного устройства (рисунок 4.1), которое состоит из хомута 1, клина 5, который связывает хомут с хвостовиком автосцепки, и упорной плиты 4. Поглощающий аппарат 2 с упорной плитой установлен между передними 10 и задними 11 упорами, закрепленными на продольных элементах рамы. Тяговые усилия от хвостовика автосцепки с помощью клина передаются хомуту, который, двигаясь вперед, сжимает поглощающий аппарат. От поглощающего аппарата через упорную плиту усилие передается хребтовой балке через передние упоры 10. Сжимающие и ударные силы от хвостовика автосцепки через упорную плиту передаются поглощающему аппарату и далее через задние упоры 11 хребтовой балке. Таким образом, поглощающий аппарат и при тяге, и при торможении всегда воспринимает сжимающие усилия.
Поглощающие аппараты служат для уменьшения продольных сил, передающихся на рамы локомотивов и вагонов при маневрах и в переходных режимах продольных колебаний поезда.
Основными характеристиками поглощающих аппаратов являются энергоемкость – количество кинетической энергии удара, воспринимаемое аппаратом при сжатии, соответствующем полному ходу (усилие при этом не должно превышать 2 МН), и коэффициент η необратимого поглощения энергии, равный отношению необратимо поглощенной энергии (механической энергии, преобразованной в другие виды энергии) к полной энергии, воспринятой аппаратом.
На грузовых локомотивах устанавливают пружинно-фрикционные аппараты Ш-1-ТМ. Корпус аппарата (рисунок 4.4) имеет внутреннюю поверхность в виде сужающегося шестигранника. К внутренним поверхностям корпуса примыкают три фрикционных клина 3, каждый из которых опирается на две грани. В собранном аппарате пружины 6 и 7 имеют предварительную затяжку, которая создается стяжным болтом 2, установленным между днищем корпуса и нажимным конусом 1. Скошенные поверхности нажимного конуса и нажимной шайбы 4 обуславливают образование сил распора, которые прижимают клинья к внутренней поверхности корпуса.
33
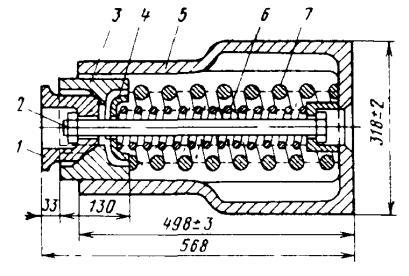
Рисунок 4.4 – Пружинно-фрикционный поглощающий аппарат Ш-1-ТМ:1 – нажимной конус; 2 – болт с гайкой; 3 – клинья; 4 – нажимная шайба; 5 – корпус; 6,7 – пружины
При сжатии аппарата нажимной конус и клинья перемещаются внутрь корпуса. Энергия, воспринимаемая аппаратом, затрачивается на упругую деформацию пружин и в большей степени рассеивается, т. е. из-за наличия сил трения (главным образом между корпусом и фрикционными клиньями) превращается в тепловую энергию. Энергоемкость аппарата Ш-1-ТМ составляет 40 – 50 кДж, ход аппарата 70 мм. Простота конструкции и малая стоимость определили широкое распространение пружиннофрикционных аппаратов. У пружинно-фрикционных аппаратов поглощающая способность при полном сжатии, т. е. при соприкосновении корпуса с упорной плитой, составляет 80–85 %; остальная часть подводимой энергии идет на сжатие пружин.
После снятия нагрузки с пружины клинья и нажимной конус возвращаются в исходное положение. Пружины снова раздвигают клинья, преодолевая их трение, что в значительной мере предохраняет поезд от сильных толчков. При текущем ремонте ТР автосцепку проверяют специальным комбинированным шаблоном с откидной скобой и при необходимости заменяют.
Контролируют состояние тягового хомута, клина, фрикционного аппарата, ударной розетки, маятниковой подвески и расцепного рычага. Для этого головку автосцепки снимают, осматривают хвостовик, хомут и клин. Тяговый хомут должен отвечать требованиям проверки шаблонами 920р-1 и 861р-м [6] (см. Приложение Б).
Хвостовик и клин проверяют магнитным дефектоскопом, убеждаются в отсутствии трещин. Трещины в частях автосцепного устройства не допускаются.
Для проверки действия механизма автосцепки лапу замкодержателя утапливают внутрь головы автосцепки и делают попытку втолкнуть рукой замок. Если он не уходит дальше после упора верхнего плеча предохранителя в противовес замкодержателя, предохранительное устройство от саморасцепа считается исправным.
С помощью специального приспособления проверяют высоту автосцепки над головкой рельса. При необходимости ее регулируют. После окончательной регулировки
34
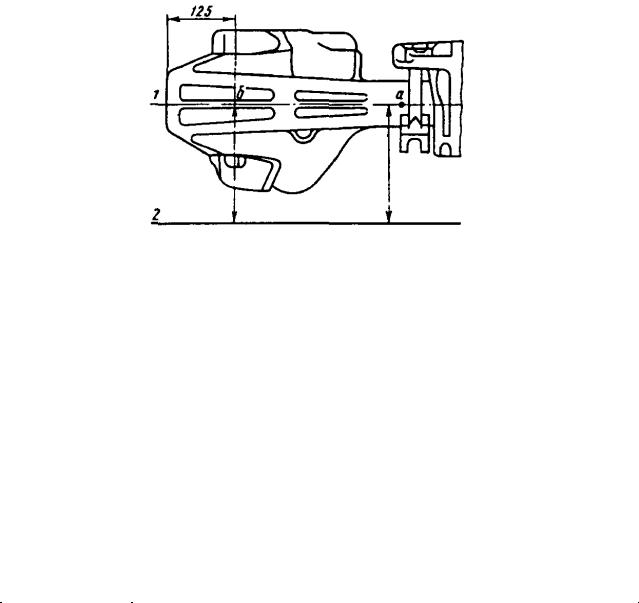
рессорного подвешивания замеряют высоту автосцепки над головками рельсов, определяют разность этих высот, и положение автосцепки относительно горизонтали. Горизонтальное положение автосцепки определяют на прямом и горизонтальном участке пути по разности расстояний до средней линии (литейного шва) у малого зуба и у входа хвостовика в ударную розетку (рисунок 4.5). По разности между замеренными расстояниями определяют отклонение от горизонтального положения автосцепки, которое должно быть не более 10 мм в случае ее провисания. Отклонение вверх не должно превышать 3 мм.
Рисунок 4.5 – Измерение высоты автосцепки над головками рельсов: 1 – продольная ось автосцепки; 2 – уровень головок рельсов
Порядок выполнения работы
1.Изучить конструкцию и особенности работы автосцепного устройства по содержанию лабораторной работы и на полигоне железнодорожного транспорта СамГУПС.
2.Произвести контрольные замеры и проверку действия механизма автосцепки (по указанию преподавателя).
3.Заполнить таблицу 4.1.
Таблица 4.1 – Результаты измерений
Наименование |
Единица |
Значение параметра при выпуске |
Примечание |
|
параметра |
измерения |
из СР (ТР-3) |
(эскиз) |
|
|
|
|
|
|
|
|
допустимое |
фактическое |
|
|
|
|
|
|
|
|
|
|
|
3.Изучить инструкцию по ремонту и обслуживанию автосцепного устройства подвижного состава железных дорог РФ [6].
4.Сделать заключение о пригодности автосцепного устройства к эксплуатации.
35
Содержание отчета
В отчете указать следующее: номер и название лаб. работы; дату проведения; цель работы; приборы и инструменты; эскиз автосцепного устройства; результаты контрольных замеров и проверки действия механизма автосцепки (таблица 4.1); выводы по работе.
Контрольные вопросы
1.Что называют автосцепным устройством? Его назначение и состав.
2.Классификация автосцепых устройств.
3.Устройство корпуса автосцепки, его назначение и механизм сцепления.
4.Для чего поверхности зубьев автосцепки выполняются скошенными?
5.Устройство и назначение центрирующего прибора.
6.Состав и назначение упряжного устройства.
7.Устройство и назначение тягового хомута.
8.Назначение передних и задних упоров продольных балок кузова.
9.Какими шаблонами проверяется состояние тягового хомута?
10.Какими шаблонами проверяется контур зацепления автосцепки?
11.Как проверяют действие механизма автосцепки?
12.Как проверяют высота автосцепки над головкой рельса?
13.Назначение поглощающего аппарата.
14.Какие усилия воспринимает поглощающий аппарат?
15.Устройство и принцип действия пружинно-фрикционного поглощающего аппарата Ш-1-ТМ.
16.Какая энергоемкость у поглощающего аппарата Ш-1-ТМ?
Лабораторная работа № 5
ТЯГОВЫЙ ПРИВОД I КЛАССА ОТЕЧЕСТВЕННЫХ ЭЛЕКТРОВОЗОВ
Цель работы: изучить конструкцию и особенности работы колесно-моторного блока отечественных грузовых электровозов, основы расчета упругого подвешивания тягового электрического двигателя (ТЭД) к раме тележки.
Оборудование, приборы и инструменты: кронциркуль; штангенциркуль; линейка.
36
Основные положения
1. Классификация тяговых приводов. Тяговой привод – это комплекс устройств, служащих для преобразования энергии какого-либо вида в работу по преодолению сопротивления движению. Все конструкции тяговых приводов, применяемых на отечественных и зарубежных локомотивах, по степени подрессоренности его элементов подразделяются на 3 класса.
Привод I класса характеризуется опорно-осевой полуподрессоренной подвеской ТЭД и редуктора. Хотя ТЭД имеет слабую виброзащищенность и большую неподрессоренную массу mнп = 6–8 т, данный привод применяется на всех отечественных серийных электровозах: ВЛ-15, 19, 22, 23, 8, 10, 60, 80, 82, 85 и др.
Привод II класса характеризует:
-установка тягового двигателя на подрессоренные части локомотива (раму тележки или кузова);
-наличие опорно-осевого полуподрессоренного редуктора с несущим корпусом. Характеризуется также соединением вала якоря двигателя (подрессоренная часть
привода) с валом шестерни редуктора (полуподрессоренная часть привода) через тяговую подвижную муфту, способную передавать тяговый момент при взаимных перемещениях валов по различным плоскостям. Неподрессоренная масса составляет mнп ≈ 4,5 т. Данный привод применяется на ЭР1, 2, 9, 22, 200; ЭТ2; ЧС1-8; ЭД-4М, 6М, 9М; ЭМ-2И-001;ЭП-1 и др.
Привод III класса характеризует:
-установка тягового двигателя и редуктора на подрессоренные части локомотива;
-соединение вала ведомого зубчатого колеса с колесной парой через тяговую подвижную муфту.
Здесь почти все элементы тягового привода подрессорены mнп ≈ 2 т и их воздействие на путь резко снижается. Применялся на опытных ВЛ-40, 81, 84.
Тяговый привод I класса. Колесно-моторный блок грузового электровоза является составной частью тягового привода (рисунок 5.1). Он осуществляет преобразование электрической энергии в механическую энергию поступательного движения и состоит:
-из тягового электродвигателя;
-2-х редукторов тяговой передачи;
-колесной пары.
Передачи тягового привода I класса называются жесткими, а II и III класса – гибкими.
Общий вид тягового привода I класса показан на рисунках 5.1–5.3.
37
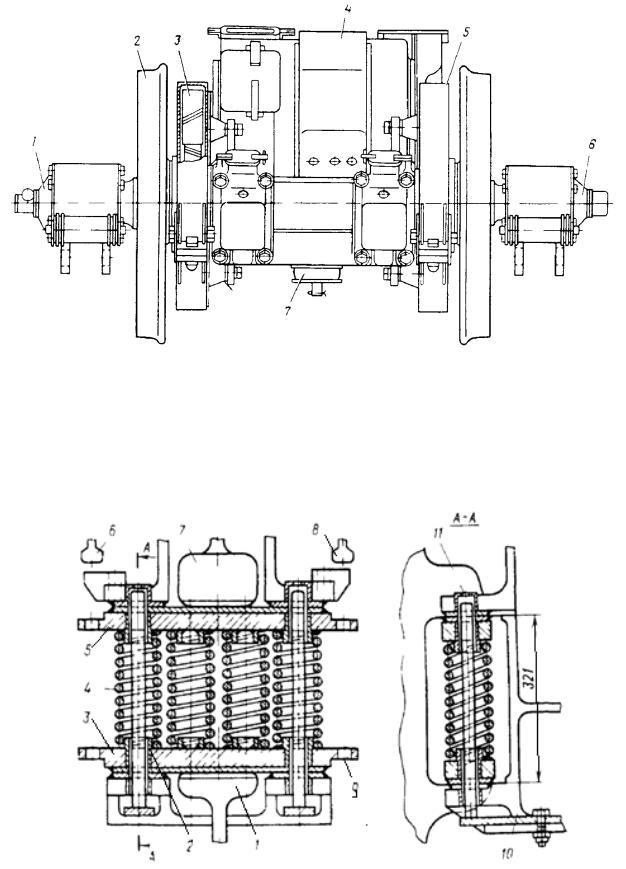
В этом случае применено опорно-осевое (трамвайное) подвешивание ТЭД, при котором тяговый двигатель одной стороной через моторно-осевые подшипники опирается на ось колесной пары, а другой – упруго на раму тележки.
Рисунок 5.1 – Колесно-моторный блок:
1,6 – буксы; 2 – колесная пара; 3 – зубчатая передача; 4 – ТЭД; 5 – кожух; 7 – подвеска ТЭД
Рисунок 5.2 – Траверсное опорно-осевое подвешивание тяговых двигателей
38
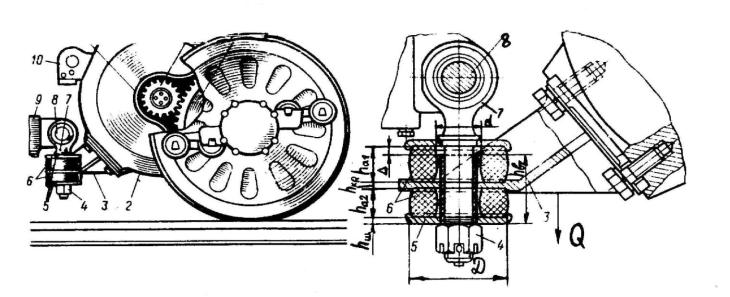
Рисунок 5.3 – Маятниковое подвешивание тяговых двигателей
Упругое подвешивание ТЭД к раме осуществляется:
-пружинным подвешиванием через траверсу, состоящую из верхней и нижней балок, между которыми размещены 4 пружины (ВЛ-19, 22, 23, 8, 60), рисунок 5.2;
-маятниковым подвешиванием (ВЛ-10; 80; 82), рисунок 5.3.
При траверсном подвешивании тяговый двигатель одним концом опирается через моторно-осевые подшипники на ось колесной пары, а вторым – двумя кронштейнами 1 и 7 (рисунок 5.2, а) через траверсу на раму 10 тележки. Траверса состоит из витых пружин 4, которые являются упругими элементами подвешивания, направляющих упоров 2 и стержней 11, опорных балок 3 и 5 с приваренными к ним накладками. Траверсу в сборе с предварительным натягом, который создается болтами, пропущенными через отверстия 9, устанавливают между двумя кронштейнами двигателя
1 и 7 и четырьмя кронштейнами рамы 10. На |
двигателе |
предусмотрены два |
предохранительных кронштейна 6 и 8, которыми |
в случае |
обрыва основных |
кронштейнов опирается двигатель. |
|
|
Натяг пружин выбирают таким, чтобы при установке траверсы не было зазора между верхней балкой 5 и кронштейнами рамы тележки, когда тяговый двигатель выступами опирается на траверсу. Предварительный натяг пружин должен исключить их деформацию от реакции тягового момента. Для этого необходимо, чтобы усилие начального натяга пружин было равно нагрузке двигателя, приходящейся на траверсу. Недостатком этой конструкции является износ направляющих стержней 11 в местах соприкосновения со втулками, верхней 3 и нижней 5 балок, а также износ трущихся поверхностей кронштейнов 1 и 7. На пружины 4 действуют примерно половина веса тягового двигателя и силы его реакции; рассчитывают их так, чтобы при наибольшей силе тяги между витками оставался зазор.
39
На отечественных грузовых электровозах для передачи вращающего момента применяют зубчатые передачи – двусторонние прямозубые с упругой связью (рисунок 5.2, б) и двусторонние жесткие косозубые (рисунок 5.2, в) с углом наклона зубьев 24 . Равенство статических нагрузок с правой и левой сторон двусторонней зубчатой передачи обеспечивается противоположным наклоном зубьев. Если по какойлибо причине в случае приложения нагрузки в зацепление вступит одна из сторон передачи, то появляющаяся осевая сила заставляет якорь перемещаться до тех пор, пока не войдут в зацепление зубчатые колеса другой стороны. Чтобы компенсировать неточность посадки зубчатых колес при монтаже двусторонней передачи с прямыми зубьями, применяют упругую связь между венцом 13 (см. рисунок 5.2, б) зубчатого колеса и его центром. Упругая связь позволяет также уменьшить динамические нагрузки, передаваемые через зубчатое зацепление на тяговый двигатель; при этом улучшаются условия работы двигателя и зубчатой передачи, повышаются их надежность и долговечность. Такое зубчатое колесо состоит из центра 17, венца 13, листовых (цилиндрических, резиновых) пружин с прокладками 18 в середине, боковых шайб 16 и заклепок 14. Состояние пакетов контролируется через отверстия 15 в шайбах 16, которые наложены с обеих сторон на центр и венец.
В настоящее время на электровозах траверсное подвешивание ТЭД к раме тележки вытесняется более технологичным и конструктивно простым маятниковым креплением на подвеске с упругими резиновыми шайбами, составляющими резинометаллический блок (РМБ), рисунок 5.3.
Узел опоры тягового двигателя на раму тележки предназначен для передачи веса и опорных реакций, создаваемых тяговым моментом двигателя на раму тележки. Данная нагрузка передается на подвеску кронштейном 3 коробчатого типа, прикрепленного к остову двигателя 2 болтами. Кронштейн 3 расположен между резиновыми шайбамиамортизаторами 6, которые зажаты с предварительным натягом корончатой гайкой 4 между двумя стальными упорными шайбами 5, надетыми на подвеску 7. При перекосе резиновых шайб кронштейном 3 в процессе движения подвижного состава данный блок выполняет функции шарового шарнира без поверхностного трения. Головка подвески 7 крепится к шкворневому брусу 9 с помощью плавающего валика 8. Валик проходит через втулки, запрессованные в проушинах бруса и в головке подвески. Внутреннее отверстие втулки, запрессованной в головке подвески и изготовленной из марганцовистой стали Г13П, имеет форму гиперболоида вращения, что позволяет подвеске перекатываться по валику при поперечных перемещениях ТЭД, обеспечивая соединению подвижность сферического шарнира. На случай обрыва подвески 7 в качестве дополнительной страховки служат специальные приливы 10 на остове двигателя 2 и приливы на шкворневом брусе рамы тележки. Эта конструкция подвески имеет технический ресурс, превышающий пробег до заводского ремонта электровоза.
Резиновые амортизаторы должны работать параллельно. Если действующая сила Q
превысит предварительный натяг, произойдет «раскрытие» амортизатора, т. е.
40