
- •ОГЛАВЛЕНИЕ
- •ВВЕДЕНИЕ
- •2.5.3. Чугуны
- •ГЛАВА 3. ПРОИЗВОДСТВО МЕТАЛЛИЧЕСКИХ КОНСТРУКЦИОННЫХ МАТЕРИАЛОВ
- •ГЛАВА 4. СПОСОБЫ ФОРМООБРАЗОВАНИЯ ЗАГОТОВОК ДЕТАЛЕЙ МАШИН
- •ГЛАВА 5. ЛИТЕЙНОЕ ПРОИЗВОДСТВО – СПОСОБ ПЕРВИЧНОГО ФОРМООБРАЗОВАНИЯ ЗАГОТОВОК ИЗ ЖИДКОПОДВИЖНЫХ КОНСТРУКЦИОННЫХ МАТЕРИАЛОВ
- •5.3.3. Модельный комплект
- •5.3.5.1. Литье по выплавляемым моделям
- •5.3.5.3. Литье в кокиль
- •5.3.5.4. Литье под давлением
- •5.3.5.5. Центробежное литье
- •6.5.2.1. Прессование
- •6.5.2.2. Волочение
- •ГЛАВА 7. ТЕХНОЛОГИЯ ПОЛУЧЕНИЯ СВАРНЫХ И ПАЯНЫХ ЗАГОТОВОК
- •7.2.1. Электродуговая сварка
- •7.4. Пайка
- •ГЛАВА 8. КОМБИНИРОВАННЫЕ СПОСОБЫ ПОЛУЧЕНИЯ ЗАГОТОВОК
- •ГЛАВА 9. ПОЛУЧЕНИЕ ЗАГОТОВОК ДЕТАЛЕЙ МАШИН ИЗ НЕМЕТАЛЛИЧЕСКИХ И КОМПОЗИЦИОННЫХ МАТЕРИАЛОВ
- •9.1.3. Спекание
- •ГЛАВА 10. ТЕХНОЛОГИЧЕСКИЕ ПРОЦЕССЫ ОБРАБОТКИ ЗАГОТОВОК В СОВРЕМЕННОМ МАШИНОСТРОЕНИИ. ТЕОРЕТИЧЕСКИЕ И ТЕХНОЛОГИЧЕСКИЕ ОСНОВЫ МЕХАНИЧЕСКОЙ ОБРАБОТКИ
- •10.1.8. Смазывающе-охлаждающие технологические среды
- •10.9.1. Резьбонарезание
- •10.9.2. Зубонарезание
- •ГЛАВА 12. ТЕХНОЛОГИЧЕСКИЕ ПРОЦЕССЫ ФОРМИРОВАНИЯ ЗАДАННЫХ ФИЗИКО-МЕХАНИЧЕСКИХ И ЭКСПЛУАТАЦИОННЫХ СВОЙСТВ ПОВЕРХНОСТНЫХ СЛОЕВ
- •ГЛАВА 13. ОСНОВЫ СБОРОЧНЫХ РАБОТ И ТЕХНОЛОГИЧЕСКОЙ ПОДГОТОВКИ ПРОИЗВОДСТВА
- •ГЛАВА 14. ПРОБЛЕМЫ СОВРЕМЕННОГО МАШИНОСТРОИТЕЛЬНОГО ПРОИЗВОДСТВА И ОБЕСПЕЧЕНИЕ ЭКОЛОГИЧЕСКОЙ БЕЗОПАСНОСТИ ПРОИЗВОДСТВЕННЫХ ПРОЦЕССОВ
- •БИБЛИОГРАФИЧЕСКИЙ СПИСОК

ГЛАВА 4. СПОСОБЫ ФОРМООБРАЗОВАНИЯ ЗАГОТОВОК ДЕТАЛЕЙ МАШИН
Формообразование – основной этап придания конструкционному материалу требуемой геометрической формы детали согласно чертежу. Формообразующие технологические процессы можно классифицировать по агрегатному состоянию заготовок или деталей. В данной главе рассматривается формообразование из парообразного, жидкого и твердого состояний и условия получения при первичном формообразовании заготовок и деталей.
4.1. Формообразующиетехнологическиепроцессы
Формообразующие процессы по методу их исполнения принято подразделять на следующие:
•осаждение из парогазовой фазы, при котором конфигурация заготовки формируется в результате конденсации парообразных или газообразных химических элементов с образованием твердых осадков;
•литье, в процессе которого формообразование заготовки или детали осуществляется из жидкого материала путем заполнения им полости заданной формы и размеров с последующим затвердеванием;
•формование, заключающееся в получении заготовки или детали из порошкового или волокнистого материала путем заполнения полости заданной формы и размеров с последующим уплотнением;
•гальванопластика − процесс получения изделий из жидкого материала путем осаждения металла из раствора под действием электрического тока;
•обработка давлением, в процессе которой происходит изменение формы, размеров, шероховатости и свойств первичной заготовки (слитка, профиля) в результате пластической деформации и/или разделения изделия без образования стружки;
•механическая обработка резанием, в процессе которой происходит изменение формы, размеров, шероховатости путем деформирования и последующего отделения поверхностного слоя заготовки с образованием стружки;
•электрофизическая и электрохимическая обработка, заключаю-
щаяся в изменении формы, размеров, шероховатости поверхностей заготовки путем использования электрических разрядов, магнитострикционного эффекта, электронного или оптического излучения и растворения ее материала в электролите под действием электрического тока;
•сборка, в процессе которой происходит образование разъемных и неразъемных соединений составных частей заготовки или изделия путем навинчивания, сварки, пайки, клепки, склеивания и т. д.
Технология конструкционных материалов. Учебное пособие |
-94- |

ГЛАВА 4. СПОСОБЫ ФОРМООБРАЗОВАНИЯ ЗАГОТОВОК ДЕТАЛЕЙ МАШИН
4.2.Изделияипокрытия, получаемыеизматериалов
впарогазовойфазе
Изделия и покрытия, получаемые из материалов в парогазовой фазе, играют существенную роль в современной промышленности, и можно ожидать, что в будущем их применение значительно расширится. Это объясняется тем, что осаждение осадка из парогазовой фазы − универсальный и относительно экономичный метод получения покрытий, порошков и изделий путем контролируемого осаждения вещества в виде отдельных атомов или молекул.
Различают два вида осаждения:
•физическое осаждение, которое иногда называют вакуумно-конден- сационным напылением;
•химическое, или газофазное, осаждение.
Преимуществом физического осаждения является то, что заготовка находится при температуре окружающей среды. Для получения осадка в нужном месте температура изделия должна быть ниже температуры испаряемого вещества.
При химическом осаждении поверхность должна быть нагрета до более высокой температуры, чем газообразные соединения. В результате возможно термическое разложение летучего соединения и осаждение материала на поверхность заготовки.
Осаждение из парогазовой фазы можно рассматривать как ряд последовательных стадий: испарение, перенос, образование и рост кристаллитов.
Термическое испарение твердого тела или жидкого материала является простейшим способом получения паров для последующего осаждения. Скорость простого термического испарения можно повысить с помощью катодного распыления, т. е. путем бомбардировки поверхности мишени ионами с большой кинетической энергией. В результате атомы материала мишени переходят в парообразное состояние.
Другим способом испарения является химическое, при котором химически активный газ адсорбируется на поверхности исходного материала и реагирует с ним. Летучий продукт этой реакции десорбируется и его можно перенести в другие части системы, где он подвергается дополнительной очистке или вступает в реакцию, образуя осадок.
После того как исходный материал переведен в парообразное или газообразное состояние, его требуется транспортировать в то место, где нужно получить осадок.
При физическом осаждении сопротивление переносу незначительное, поскольку процесс осуществляется в высоком вакууме.
При химическом осаждении в замкнутых камерах скорость переноса источника осаждаемого материала до покрываемой поверхности зависит от температуры газа и скорости диффузии газообразных реагентов. Получаемые покрытия формируются из отдельных атомов. Следовательно, этим методом
Технология конструкционных материалов. Учебное пособие |
-95- |

ГЛАВА 4. СПОСОБЫ ФОРМООБРАЗОВАНИЯ ЗАГОТОВОК ДЕТАЛЕЙ МАШИН
4.2. Изделия и покрытия, получаемые из материалов в парогазовой фазе
можно получать изделия, плотность которых будет близка к теоретической. Однако причиной разрушения многих покрытий является неблагоприятное взаимное расположение кристаллитов, растущих из изолированных центров.
Заготовки и покрытия, получаемые химическим осаждением, обычно состоят из столбчатых кристаллитов, растущих от подложки к внешней поверхности. Отдельные кристаллиты могут быть весьма прочными, однако они плохо связаны друг с другом. При поперечной нагрузке такие осадки разрушаются при напряжениях существенно ниже предела прочности материала покрытия.
Физическое осаждение. Среди методов физического осаждения большое значение приобретает алюминирование пластмассовых и стальных изделий путем вакуумно-конденсационного напыления термически испаряемого алюминия. Этот технологический процесс широко используется в оптической технике для получения тонких пленок металлических и неметаллических материалов, способных изменять прохождение световых волн.
Химическое осаждение. Потребность авиационной техники в изделиях и покрытиях из тугоплавких материалов способствует развитию технологии химического осаждения, которая не только позволяет получать изделия сложной конфигурации, но и может стать эффективным способом соединения заготовок из тугоплавких металлов путем осаждения нужного материала в зазоре между соединяемыми элементами. Отсутствие в изделии шва и околошовной зоны с крупнозернистой структурой является основным преимуществом этого технологического процесса по сравнению со сваркой плавлением при прочих равных условиях. Известно применение никеля, образующегося при разложении карбонила никеля Ni(CO)4, для формирования нахлесточного соединения стальных и керамических элементов конструкции.
Ниобий, молибден, титан и вольфрам, которые нельзя осадить электрическим методом из водных растворов, легко осаждаются при водородном восстановлении соответствующих газообразных галогенидов. Формообразование волокон бора диаметром 75–200 мкм, применяемых в композитах, осуществляют путем восстановления треххлористого бора водородом. В результате химического осаждения бора на вольфрамовые нити диаметром 10–12 мкм образуются волокна, прочность которых во многом зависит от наличия локальных дефектов в виде крупных кристаллитов, инородных включений, трещин, пустот и др. Производительность промышленного процесса получения волокон с заданными свойствами возрастает с увеличением температуры процесса. Превышение температуры 13 000 °C приводит к образованию крупных кристаллитов, что заметно снижает их прочность. Для повышения термостойкости волокон на их поверхность химическим осаждением наносят слой карбидов кремния или бора толщиной 2–6 мкм.
После того как был открыт легко разлагающийся летучий карбонил никеля, возникла новая отрасль металлургии − газофазная металлургия. В
Технология конструкционных материалов. Учебное пособие |
-96- |

ГЛАВА 4. СПОСОБЫ ФОРМООБРАЗОВАНИЯ ЗАГОТОВОК ДЕТАЛЕЙ МАШИН
4.2. Изделия и покрытия, получаемые из материалов в парогазовой фазе
настоящее время в этой отрасли используются наряду с карбонильным методом и галогенидные процессы.
При химическом осаждении разложение карбонильных или других соединений проводят при низком давлении, в результате чего получают осадок высокой степени чистоты и равномерности. Суммарные реакции применительно к карбонилам [Me(CO)n] можно записать в следующем виде:
Me(CO)n → Me + nCO.
Для упрочнения деталей машин широко применяют поверхностное легирование, которое может осуществляться в газовой среде. Химико-терми- ческая обработка (ХТО) сводится к диффузионному насыщению поверхностного слоя заготовки неметаллами (C, N2, Si, B и др.) или металлами (Cr, Al, Zn и др.) в процессе выдержки при определенной температуре в активной газовой среде.
При ХТО одновременно протекают несколько процессов:
•образование в окружающей среде диффундирующего элемента в атомарном или ионизированном состоянии;
•адсорбция атомов (ионов) на поверхности изделия с образованием химических связей между ионами насыщающего элемента и основного металла (химосорбция);
•диффузия адсорбированных атомов в глубь обрабатываемой заготовки. Толщина диффузионного слоя зависит от температуры насыщения,
продолжительности процесса, характера образующегося твердого раствора (внедрения или замещения), атомно-кристаллического строения материала заготовки и концентрации диффундирующего элемента на поверхности. С повышением температуры, увеличением длительности процесса насыще-ния и концентрации диффундирующего элемента возрастает толщина легированного слоя.
Скорость диффузии атомов насыщающего элемента, образующего с металлом заготовки твердые растворы внедрения, значительно выше, чем при образовании твердого раствора замещения. Диффузия элементов протекает интенсивнее в решетке α-железа, чем в более плотно упакованной решетке γ-железа.
К ХТО в газовой фазе относят процессы цементации, нитроцементации, азотирования и диффузионного насыщения металлами (Al, Cr, Zn и др.) или смесями компонентов (Al и Si, Cr и Si, B и Al и др.).
При электроэрозионной и электрохимической обработке заготовок практически отсутствует силовое воздействие инструмента на заготовку, поэтому погрешности формы и размеров изделия ниже, чем при механической обработке резанием. Электрофизические и электрохимические процессы предназначены в основном для обработки изделий из очень твердых, вязких и хрупких материалов.
Технология конструкционных материалов. Учебное пособие |
-97- |

ГЛАВА 4. СПОСОБЫ ФОРМООБРАЗОВАНИЯ ЗАГОТОВОК ДЕТАЛЕЙ МАШИН
4.2. Изделия и покрытия, получаемые из материалов в парогазовой фазе
Наиболее широкое применение получила электроэрозионная обработка (ЭЭО), заключающаяся в изменении формы, размеров, шероховатости и свойств поверхностей заготовок в результате электрической эрозии. Под воздействием высоких температур в зоне разряда происходит нагрев, расплавление и частичное испарение металла. Процесс ЭЭО происходит в рабочей жидкости, которая заполняет пространство между электродами. При этом один электрод − заготовка, а другой − инструмент. Под воздейст-вием сил, возникающих в канале разряда, жидкий и парообразный металл выбрасывается из зоны разряда в рабочую жидкость и застывает в ней с образованием гранул диаметром 0,01–0,005 мм.
Электрохимическая обработка основана на законах электрохимии. По используемым процессам различают анодную и катодную обработку, а по технологическим возможностям − размерную и поверхностную. Анодномеханическая обработка основана на сочетании электротермических и электромеханических процессов. Обрабатываемую заготовку подключают к аноду, а инструмент − к катоду, в качестве которого используют металлические диски, ленту и проволоку. Обработку ведут в электролите, а заготовке и инструменту задают такие же движения, как и при обычных процессах механической обработки резанием.
4.3. Получениезаготовокизжидкойфазы методамилитьяисваркиплавлением
Получение заготовок из жидкого состояния предполагает, как правило, расплавление основного и/или присадочного материала, заполнение специально подготовленной формы или зазора между соединяемыми элементами и кристаллизацию жидкой металлической фазы.
При литье заготовок на процесс затвердевания и образования кристаллической структуры существенно влияет температура заливки металла в форму и скорость охлаждения отливки.
Низкие температуры заливки металла, как правило, приводят к образованию мелкозернистой структуры, высокие − к получению крупных кристаллитов в заготовках.
Низкие скорости охлаждения отливки способствуют получению крупных дендритно-равноосных кристаллитов. С увеличением скорости охлаждения появляются зоны столбчатых кристаллитов. При очень большой скорости охлаждения расплава получается сплошная мелкая столбчатая структура большой плотности, для которой характерны высокие механические свойства.
Особенностью отливок, изготовленных с кристаллизацией под давлением (жидкой штамповкой), является отсутствие прибылей и литниковых систем. При этом усадка заготовок определяется свойствами сплава, схемой прессования, давлением и временем выдержки отливки под нагрузкой. Увеличение давления и времени прессования способствует уменьшению величины усадки отливки.
При сварке плавлением в результате расплавления кромок соединяемых элементов и присадочного материала образуется сварочная ванна. Этот
Технология конструкционных материалов. Учебное пособие |
-98- |

ГЛАВА 4. СПОСОБЫ ФОРМООБРАЗОВАНИЯ ЗАГОТОВОК ДЕТАЛЕЙ МАШИН
4.3. Получение заготовок из жидкой фазы методами литья и сварки плавлением
процесс является разновидностью литья заготовок в металлическую форму, поэтому кристаллизация шва в значительной степени напоминает формирование отливок. Размеры столбчатых кристаллитов зависят от способа и режимов сварки. Увеличение длительности существования сварочной ванны при высоких температурах, например в случае электрошлаковой сварки, вызывает заметное увеличение размеров кристаллитов в зоне шва и в зоне термического влияния.
Сущность процесса наплавки заключается в получении поверхностных слоев нанесением расплавленного присадочного материала методом сварки. Проплавление основного металла, перемешивание основного и наплавленного металлов должны быть минимальными для сохранения механических свойств наплавляемого слоя.
4.4. Получениезаготовокпластическимдеформированием
Технологические процессы обработки давлением, механической обработки резанием, сварки давлением и порошковой металлургии в твердом состоянии применяют с целью получения и обработки заготовок. Для их осуществления необходимо приложение термической, механической энергии и их сочетаний, которые приводят к изменению структуры, свойств и размеров изделий.
Обработка давлением основана на пластической деформации заготовки без ее разрушения и нарушения сплошности. В процессе резания происходит разрушение заготовки с разделением ее на части. В традиционном понимании механической обработки (точение, фрезерование, сверление и др.) меньшая часть представляет собой стружку, бoльшая − обрабатываемую заготовку.
При разделительных технологических операциях обработки давлением, таких как вырубка, пробивка отверстий и разрезка на ножницах, разрушение заготовки сопровождается разделением ее на части, соизмеримые по размерам друг с другом.
Установить четкую грань между обработкой резанием и давлением достаточно сложно, поскольку для их осуществления необходима пластическая деформация заготовки. При этом в процессе резания заготовок и в условиях разделительных операций обработки давлением эти деформации всегда доведены до разрушения.
Сварка в твердом состоянии и изготовление заготовок методами порошковой металлургии обеспечивают получение требуемых свойств и заданной конфигурации изделий в результате образования межатомных или межмолекулярных связей на границе соединяемых элементов.
Термическая обработка заготовок, сопровождающая процессы горячей обработки давлением, сварки с использованием тепловой энергии и спекания порошков, оказывает существенное влияние на изменение их свойств.
В результате пластической деформации при получении заготовок и их обработке в твердом состоянии изменяются исходная структура и свойства материала. Кроме того, наличие механических надрезов, трещин, внутренних
Технология конструкционных материалов. Учебное пособие |
-99- |
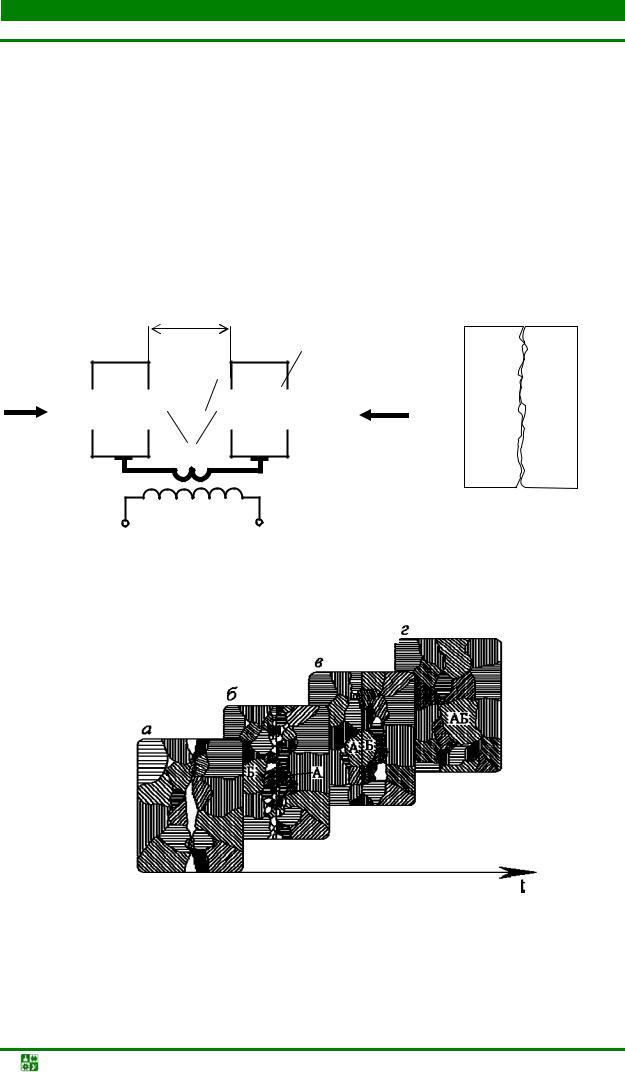
ГЛАВА 4. СПОСОБЫ ФОРМООБРАЗОВАНИЯ ЗАГОТОВОК ДЕТАЛЕЙ МАШИН
4.4. Получение заготовок пластическим деформированием
дефектов, сквозных отверстий, резких переходов от толстого сечения к тонкому приводит к неравномерному распределению напряжений.
Так как напряжения образуются в результате разных причин, различают временные напряжения, обусловленные действием внешней нагрузки и исчезающие после ее снятия, и остаточные напряжения, возникающие в заготовках после пластической деформации, при быстром нагреве или охлаждении в процессе сварки, обработки давлением и резанием вследствие неоднородного расширения (сжатия) различных слоев и зон изделия. Эти напряжения называют также тепловыми, или термическими.
Кроме того, вследствие неоднородного протекания фазовых превращений по объему заготовки возникают фазовые, или структурные,
напряжения.
2L
Rэл
R
Р |
|
|
Р |
|
|
|
|
Rзаг |
а |
б |
Рис. 4.1. Стыковая электроконтактная сварка сопротивлением: а – схема; б – физический контакт на стыке заготовок
г
в
б
a
t
Рис. 4.2. Процесс постепенного формирования сварного соединения однородных заготовок при сварке давлением (в твердом состоянии): а − пластическая деформация микронеровностей; б − поверхностная деформация; в − создание активных центров и диффузионные процессы в зоне сварки; г − образование общих зерен
Технология конструкционных материалов. Учебное пособие |
-100- |

ГЛАВА 4. СПОСОБЫ ФОРМООБРАЗОВАНИЯ ЗАГОТОВОК ДЕТАЛЕЙ МАШИН
4.4. Получение заготовок пластическим деформированием
При сварке на соединяемых поверхностях заготовок и в прилегающих объемах металла, как правило, протекают следующие процессы: пластическая деформация, диффузия, упрочнение, рекристаллизация, формирование и разрушение оксидных пленок и др. Скорость образования сварных соединений определяется кинетикой процессов образования физического контакта и химического взаимодействия в объеме соединяемых элементов. Физический контакт обеспечивается пластической деформацией микронеровностей на соединяемых поверхностях (рис. 4.1 и рис. 4.2).
Сглаживанию поверхностей могут способствовать процессы, не связанные с действием внешних сил. Скорость химического взаимодействия (образования связей) в основном зависит от скорости создания активных центров на сближаемых поверхностях и диффузионных процессов в зоне сварки (рис. 4.2, в).
В случае если длительность и температура процесса сварки в твердом состоянии достаточны для интенсивного развития диффузионных процессов, в зоне соединения образуются общие зерна или новые фазы. При сварке однородных элементов критерием окончания процесса может служить рекристаллизация, приводящая к образованию общих зерен в зоне контакта (рис. 4.2, г). Для получения соединений разнородных металлов необходимость развития или ограничения диффузии определяется свойствами образующихся фаз в зоне контакта.
4.5. Факторы, определяющиевыборметодаполучениязаготовки
Метод получения той или иной заготовки зависит от служебного назначения детали и требований, предъявляемых к ней, а также от ее конфигурации и размеров, марки материала, типа производства и других факторов.
Наиболее сложные по конфигурации заготовки можно изготавливать методами литья. Изделия, получаемые методом обработки давлением, должны быть более простыми по форме. Изготовление в поковках отверстий и полостей объемной штамповкой в ряде случаев затруднено, а использование напусков резко увеличивает объем последующей механической обработки.
Размеры заготовок, получаемых методами литья и обработки давлением, практически не ограничиваются. Нередко определяющим параметром в этом случае являются минимальные размеры (например, минимальная толщина стенок отливки, минимальная масса поковки). Объемной штамповкой и большинством специальных способов литья получают заготовки массой до нескольких десятков или сотен килограммов.
Форма и размеры заготовок, получаемых методами порошковой металлургии, ограничены как максимальными, так и минимальными размерами. В процессе конструирования деталей выбор марки материала определяется не только условиями ее функционирования, но и условиями изготовления в реальном производстве. В то же время технологические свойства материала существенно влияют на выбор метода и способа
Технология конструкционных материалов. Учебное пособие |
-101- |

ГЛАВА 4. СПОСОБЫ ФОРМООБРАЗОВАНИЯ ЗАГОТОВОК ДЕТАЛЕЙ МАШИН
4.5. Факторы, определяющие выбор метода получения заготовки
получения заготовок. Так, серый чугун имеет прекрасные литейные свойства, но обладает низкой деформированностью и плохой свариваемостью.
Заготовки из одного и того же материала, полученные методами литья, обработки давлением и сваркой, обладают различными свойствами. Так, литой металл характеризуется большим размером зерен, неоднородностью химического состава и механических свойств по сечению отливки, наличием остаточных напряжений и т. д.
После обработки давлением заготовки имеют мелкозернистую структуру и определенную направленность расположения волокон (неметаллических включений). После холодной обработки давлением возникает наклеп, поэтому холоднокатаный металл прочнее литого в 1,5−3 раза. Пластическая деформация металла приводит к анизотропии свойств: прочность вдоль волокон (неметаллических включений) примерно на 10−15 % выше, чем в поперечном направлении.
Сварка приводит к образованию неоднородных структур в сварном шве и в околошовной зоне. Неоднородность зависит от вида и режима сварки. Так, наиболее резкое отличие в свойствах сварного шва возникает при ручной сварке, а электрошлаковая и автоматическая дуговая сварка обеспечивает формирование наиболее качественных однородных швов.
Программа выпуска продукции, т. е. количество изделий, выпускаемых в течение определенного времени (обычно за год), является одним из важнейших факторов, определяющих выбор метода и способа производства заготовок.
В условиях единичного производства и для простых по конфигурации деталей часто заготовками являются профили (сортовой прокат, трубы и т. п.), получаемые в условиях металлургического производства. Стоимость механической обработки заготовок при изготовлении деталей в этом случае высока, однако такая заготовка может быть достаточно экономичной из-за низкой стоимости проката, почти полного отсутствия подготовительных операций и возможности автоматизации процесса механической обработки.
Технология конструкционных материалов. Учебное пособие |
-102- |

ГЛАВА 4. СПОСОБЫ ФОРМООБРАЗОВАНИЯ ЗАГОТОВОК ДЕТАЛЕЙ МАШИН
4.5. Факторы, определяющие выбор метода получения заготовки
а
Ø90
б
в
Ø65 |
Ø80 |
Ø86 |
117 |
228 |
150 |
|
||
|
|
594 |
Ø70 |
Ø85 |
Ø92 |
600
Ø90
600
Рис. 4.3. Вал ступенчатый: а − деталь; б − штампованная поковка; в − заготовка из горячекатаного проката
При крупносерийном и массовом производстве конструкции заготовок следует максимально приближать к конфигурациям деталей. Например, для изготовления ступенчатого вала из стали 45 (рис. 4.3) целесообразно применить поковку, получаемую объемной штамповкой.
Наиболее эффективными технологическими способами изготовления заготовок в крупносерийном и массовом производстве являются специальные виды прокатки (поперечно-винтовая, поперечно-клиновая, прокатка в винтовых калибрах), которые позволяют получить периодические профили. Применение таких заготовок дает возможность повысить коэффициент использования материала и производительность труда.
При конструировании деталей необходимо учитывать возможности предприятия, на котором предполагается их изготовление. Для этого необходимо располагать сведениями о типе и количестве имеющегося
Технология конструкционных материалов. Учебное пособие |
-103- |

ГЛАВА 4. СПОСОБЫ ФОРМООБРАЗОВАНИЯ ЗАГОТОВОК ДЕТАЛЕЙ МАШИН
4.5. Факторы, определяющие выбор метода получения заготовки
оборудования, производственных площадях, возможностях ремонтной базы, вспомогательных служб и т. д.
В соответствии с эскизом детали, полученной на основе расчетов, выбор метода изготовления заготовки осуществляется с учетом рассмотренных факторов, которые целесообразно располагать в порядке убывания их значимости. Анализируя степень влияния рассмотренных выше факторов, выбирают один или несколько методов, обеспечивающих получение заготовок требуемого качества.
Оптимальный метод изготовления заготовки определяют на основе анализа конструктивно-технологических признаков проектируемой детали, технико-экономических показателей способов и программы выпуска деталей. Затем конструируют заготовку с учетом оптимальной технологии ее изготовления.
Технология конструкционных материалов. Учебное пособие |
-104- |